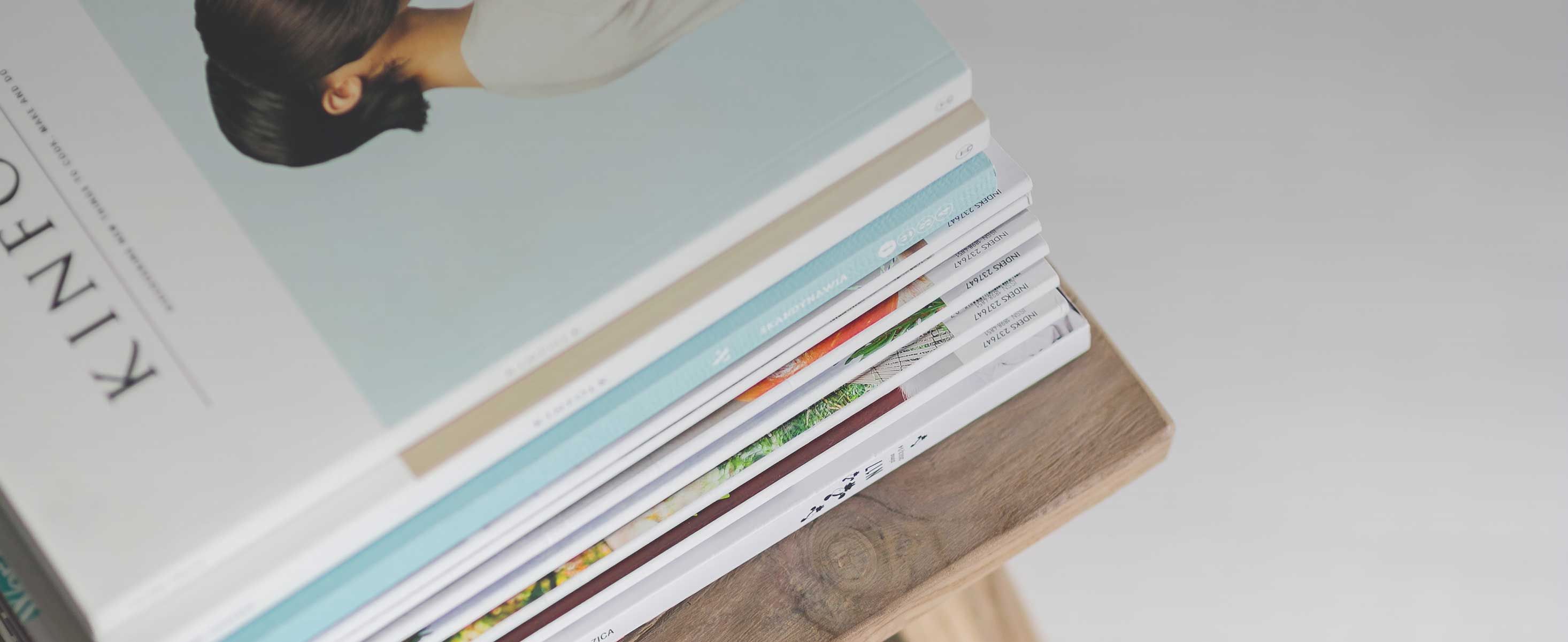
4 minute read
Troubleshooting
Victam LatAm, which took place from at Sao Paulo from October 3-5, allowed us to get in front of a large group of feed millers and address their questions specially in the Credo Online Milling section on troubleshooting.
Some of the questions reviewed below were asked and noteworthy to be mentioned.
1. Moisture control out of the dryer, how to manage the exhaust air? First let’s review the fact that time, temperature and airflow are the three major controlling factors. So, airflow in the dryer needs to be even so the drying effect is even. Exhausting air is how the moisture is removed. Doing this efficiently is a key factor and today’s modern advanced dryers can measure the wet bulb and dry bulb temperatures, the relative humidity and other factors which allow for computer control of the amount of air exhausted over all the possible conditions. Basically, the goal is to have as much water in the exhaust air as possible but not have this moisture drop out like rain in the ductwork.
2. Accuracy in coating products? Great question as there are many different styles of coating systems. The key here is to have control on both the product to be coated and the liquid flow rates. The method of application varies, so percent of liquid added specially in the very low volumes takes special to coat each and every piece. Batch system where both dry and liquids are weighed and blended together with adjustable spray system to match the volume of liquid added. Continuous systems would include weight belts or loss in weight systems to determine the dry flow back up with adjustable pumps and liquid delivery systems to match the percent to be applied.
3. How to correct off spec kibble or pellet size and appearance? This question can be answered in a number of ways as multiple causes can result is uneven product sizes or rough appearance. Finer dry raw material grind can increase product uniformity and eliminate some of the rough appearance effect. Added moisture and steam in the process greatly effects the final product shape and appearance. Lower moisture reduces expansion and yields larger cell structure in the product. More water approximately 25 to 28 percent M yields the most even looking expanded well shaped product. Higher or in the low 30 percent range expansion is harder to develop due the water restricting friction development. Moving into possible hardware issues instead of operational reasons the initial point to check is the extruder wear. Excessive wear allows pressure changes behind the die as product can flow backwards between the screws and sleeves. This effect is called surging and you end up with uneven product sizes. The fix is to renew the gap between screws and sleeves. Die hole location can have an effect as holes not evenly spaced can cause increased or decreased flow in areas yielding uneven product appearance.
These were a few of the questions and very typical of the type of discussions in our Online milling Classes for both pet and aquatic feed production. Feel free to send any issues you wish discussed at joek@ perendale.com
Previously on Troubleshooting...
1. Density
An examination of product density and its relationship with moisture levels, heating, cooling feeder screw rate and automation.
2. Non-uniform and rough appearance
A guide to understanding the science involved in improving the art of making products of all the same size.
3. Extrusion dies
This article takes a look at aspects of the process including high, medium and low shear as well the adjustments required when producing feed for small mammals.
4. Dryers
The dryer is without a doubt one of the machines in the system which greatly impacts the bottom line.
5. The extruder barrel - Part 1
Forming extruders are used for some select products – thus this part of the discussion centres on single and twin designs.
6. Cook in the extruder barrel – part 2
As discussed last month, the extruder barrel has a number of functions, but the main goal is to finalise the cook, yield the desired shape with the density target.
7. Coating
The coating process has a few areas of importance, with this edition of ‘Troubleshooting’ exploring the most important of these.
8. Expanded cat food
Dry expanded cat food production is similar to dog food production, but there are some differences, with this edition exploring a choice selection of these.
9. Extrusion during operation
This month we discuss steam input into the conditioner. During the water addition process, the steam is usually in the two-bar range.
Innovations this month November 2023
This month’s Production Showcase section features equipment and ingredients that will help in the production of petfood, taking you right from the recipe book, right up until until your product is ready to leave your factory door.
If you would like your product or service to appear on this page in a future edition of International Petfood magazine, then please contact us at editorial@perendale.co.uk
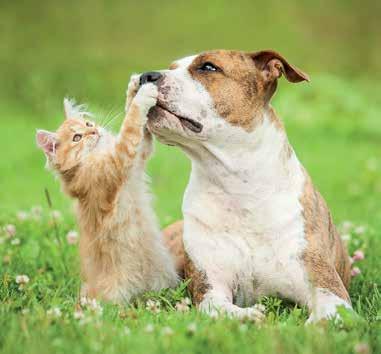
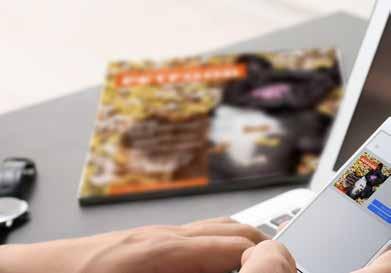
Expanders by Ottevanger
Ottevanger offers a range of expanders which improve the quality of finished feed as well as more efficient production process flow. The Ottevanger Contivar expanders have a reliable and sturdy design and are equipped with a unique Active Disk system (AD-system) in order to control exact product output and assure the quality of the product. The AD-system is easy to control and it is easy to exchange wear parts. The robust and simple design of the Ottevanger Contivar guarantees years of trouble free and economical production.
• Eliminate heat sensitive bacteria (salmonella)
• Addition of higher fats and liquids inclusions
• Gelatinisation of available starches
• Improved end product durability and strength
• Increased output of pellet mill
• Reduces wear costs of pellet mill
• Improved water stability for fish feed http://mypetfood.info/cZnT