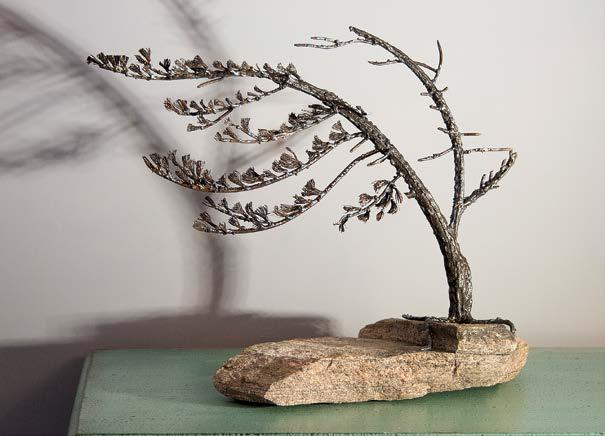
2 minute read
INTEGRITY PASSION
CONTINUED FROM PREVIOUS PAGE with stickers related to her local union and trade, revealing Courtney’s pride in being a skilled trades worker.
Courtney mostly works with carbon steel, stainless steel and occasionally copper – and a wide array of tools. First, she cuts the metal, often into intricate shapes, using a plasma cutter.
To heat or bend thin metal, she grabs her oxygen acetylene torch. To bend thicker round or square stock metal, such as railway spikes, she heats them in her small forge and hammers it out when red-hot. To fuse two pieces of metal together, she reaches for one of three types of specialty welding machines. After she has layered and welded metal pieces to meet her overall vision, she wields an angle grinder to cut, sand down or grind off excess metal, as well as to polish.
Courtney’s process differs depending on the piece. Today she’s building a swaying tree, a commissioned work, using epoxy to mount its round- bar tree trunk to a rock base. (The bars she uses for the piece comes in different diameters – ½ inch, ¾ inch, 5⁄8 inch and so on.) As Courtney gets close to her vision for the trunk and branches, she adjusts by grinding, bending and shaping the material. To achieve the look of bark, she layers weld metal onto the trunk. Rope-like wire sling left over from construction rigging serves as the pine needles. Some projects, like a recent koi fish carbon- and stainless-steel sculpture, require a 3D wire frame outline onto which the various metal pieces are placed, held together by welds.
For her koi fish sculpture, Courtney used carbon steel for one fish and stainless steel for the other. A recently completed piece (below) depicts a windswept tree.
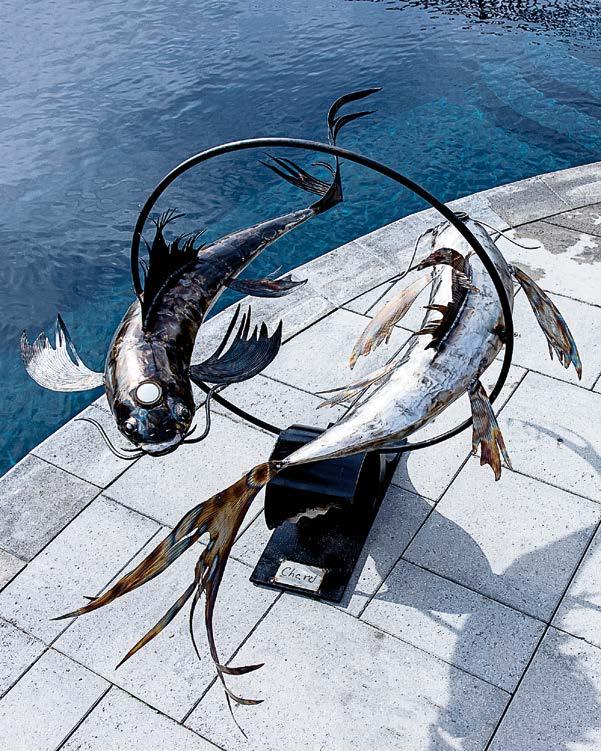
Now it’s time for the finishes. Courtney eschews paint in favour of more natural patinas and oils. For the pair of koi fish, motor oil helped achieve a darker colour on the carbon steel of one fish in contrast to the lighter stainless steel of the second; the sculpture represents yin and yang, she says. Vinegar, salt and hydrogen peroxide help rust metal and a blowtorch creates spectacular blue and purple effects on stainless steel.
The final step is oil or a clear coat to preserve the finish. Courtney can complete a small piece in a weekend. Larger, more intricate sculptures take weeks or months.
When asked to describe her personal style, Courtney lets out a warm laugh and admits she doesn’t know. “I’m a chameleon. I don’t have any one particular style. When I work on a client’s piece, I’m a conduit for their visions.”
She may not hew to a particular look, but she has honed a singular philosophy around making art.
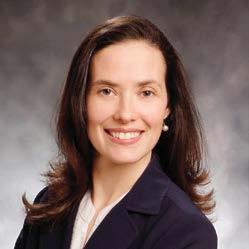
“Try to listen to your inner voice – it’s not easy, because the world is flashy and loud, and often values convenience over creativity,” she says. “Be quiet and still, and you may learn the path for you.”
Find Courtney on Instagram at Courtney Chard Cre8tive Welding