
4 minute read
WPU – the Danish company ready to rock the world of plastic waste
It all started with a good idea, some half-finished drawings, and no money three years ago for the Danish company Waste Plastic Upcycling (WPU).
At least, that’s how the chairman of the board Niels Stielund jokingly begins the story about the early beginnings of WPU. Now, the company is on the verge of starting production and entering the market for handling end-of-life plastic waste.
Advertisement
“I was introduced to a great idea but also a project that was out of money, and I and a couple of investors bought it because we believed it had potential,” he says.
They succeeded and today the great idea is still alive and kicking. On 22nd April last year, WPU was listed on Euronext Growth in Oslo, and the first of three planned factories in Denmark is built and will be operational in Q2 2023.
“Now, we have a fully functioning system where we can upcycle end-of-life plastic waste into an oil product and full range naphtha,”
Niels Stielund states with a smile.
The product can be used to produce new plastic or as an additive for diesel and petrol or jet fuel.
Batch Technology Is Key
In the last couple of months, WPU has hired dozens of new employees, but in the beginning, the team consisted only of a small core of people. Niels Bagge joined early on as CEO, and he’s played a key part in bringing WPU forward and developing a technology that sets the company apart from other actors in the market.
He explains how WPU uses pyrolysis to give new life to plastic that would otherwise end up in a landfill or an incinerator with a negative impact on the environment and climate.
However, the use of pyrolysis isn’t the main reason for the great interest in WPU:
“We’ve developed a batch technology, and batch pyrolysis processes are far easier to construct and operate compared to other pyrolysis processes,”
Niels Bagge says.
Extremely tolerant to various types and grades of waste plastic Indiscriminate intake of polluted waste plastic No sorting of waste plastic before processing needed Robust and flexible w/o risk of total breakdown of production
Impressive Numbers
The first factory is ready to receive 42,000 tonnes (93,000,000 US pounds) of plastic waste yearly. When all three Danish factories are built in 2026, they’ll be able to process almost 160.000 tonnes each year.

At that point, the expectation is annual net sales of 97 million USD and an annual result of 80,5 million USD.
WHAT MAKES WPU STAND OUT IN THE MARKET?
Niels Stielund (NS): First and foremost, I must point out our batch technology as something that separates us from our competitors. Also worth emphasizing are the circular production process and the possibility of making a profit on the sale of excess heating.
WHAT CAN YOU TELL US ABOUT WPU’S BATCH TECHNOLOGY?
Niels Bagge (NB): We developed the technology in close cooperation with The Technical University of Denmark, and it has shown itself to be robust and flexible.
With our technology we can process the plastic in big, messy batches with different kinds of materials like steel bands, without worrying if it is dirty or wet.
Most pyrolysis processes are continuously fed and are not able to take batches. Usually, the plastic needs to be cleaned, shredded, and sorted, and that’s a process that require a lot of resources. However, our technology enables us to bypass that whole process.
HOW DO YOU DO THAT?
NS: you can compare it to a huge washing machine. Just like you have programs for different kinds of clothes, so do we for different kinds of plastic.
That way, we can process plastic waste from a hospital in one pyrolysis reactor while the one next to it processes a completely different type of plastic waste.
WHAT MAKES YOU SO CERTAIN THAT THE TECHNOLOGY WILL WORK?
NB: For six months, we had a production in a test facility. We even sold the product to a German company. So not only did we prove that the technology works, but the test-product was of such a high quality that we had no problem selling it.
COULD YOU ELABORATE ON THE CIRCULAR PROCESS?
NS: Our system hardly uses any external energy to run the pyrolysis process even though it’s quite energy intensive. When the process begins, gas is released from the plastic, and we use that gas for our burners. When we ignite a cold reactor, we use a bit of oil from the production the day before. It makes us independent of fluctuating energy prices as the only electricity we need is for our pumps and the coffee machine in the kitchen.
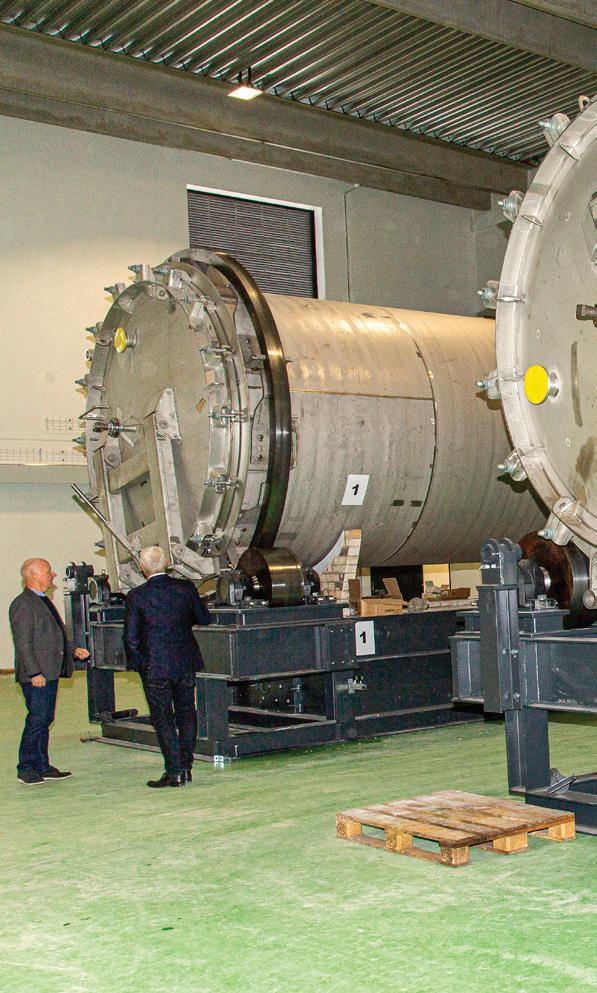
WHAT IS THE ENVIRONMENTAL IMPACT?
NB: We are ISCC+-certified and we only process end-oflife plastic that no longer can be mechanically recycled, so it is either landfill, incineration, or pyrolysis. When our three factories in Denmark are up and running, they will reduce CO2 emissions by more than 68.000 tonnes a year compared with incineration.
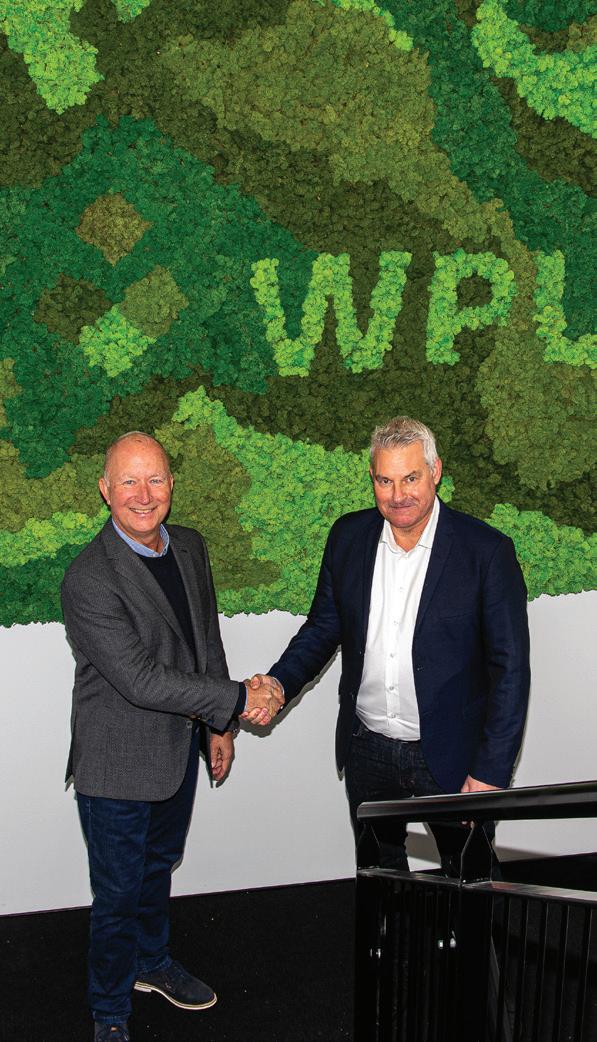
HOW CAN YOU TAKE ADVANTAGE OF THE EXCESS HEATING?
NB: Our plan is to turn it into an alternative revenue stream as we move forward. Excess heating from our first factory will be led to the local district heating plant that can distribute it to the local community. And we are already in talks with local companies that are very interested in paying for our excess heat to use it in their own production.
DO YOU SEE ANY RISKS THAT CAN AFFECT YOUR BUSINESS MODEL?
NS: Our previous test production has made us quite confident in our business model. Moreover, we have secured deals when it comes to feedstock and offtake. Vitol, one of the largest independent traders of energy and commodities, will buy all the product from our initial three Danish factories for the next five years. So, all in all, I think we can allow ourselves to be positive about the future.