
5 minute read
INSPECTION LOGBOOK
Coating Inspections – Basic Inspection Practice
Massimo Cornago
NACE International Certifi ed Coating Inspector, NACE CIP PEER Reviewer
cornago@ipcm.it
In our previous articles, we have had the opportunity to analyse all the documents that an inspector should prepare before, during, and after a coating job based on customer procedures. In general, the inspections that must be carried out in the course of a coating project are numerous and complex, as are the equipment required, the tools to be used, and the regulations to be applied and, above all, assessed and understood in detail. These will be described thoroughly in further articles that will be published in the next issues of this magazine. We will now start with an introductory summary aimed at familiarising with the basic procedures for site inspections (e.g. on materials), for preliminary inspections, and for the fi nal tests performed on the paints and coatings applied (e.g. DFT, adhesion, hardness, etc.). These procedures are used with both metal (carbon steel, stainless steel, special alloys, etc.) and cement-based substrates, although diff erent surface types call for diff erent preparation and passive protection application systems. For better understanding, we will segment these processes as follows: 1 – preliminary inspection responsibilities; 2 – surface preparation inspection (for both metal and cement-based materials); 3 – paint mixing, dilution, and application activities’ inspection; 4 – fi nal post-application inspection.
The following recommendations are aimed at guaranteeing the minimum acceptable quality level for basic inspections. In any case, as already mentioned in previous articles, it is extremely important that project specifi cations and their related documents, such as the Quality Control Plan (QCP), are used as guidelines for any special inspection requirement and for the defi nition of the inspector’s responsibilities. At the risk of being boring, we would also like to repeat that “the latest reviews, the latest issues” of international standards should always be indicated and specifi ed.
1. Preliminary inspection responsibilities
The Coating Inspector (CI) has specifi c responsibilities during the phase that precedes the coating operations (pre-job activities), including perfectly understanding the client’s specifi cations and all the associated documents relevant to the project, namely as follows: • Project drawings, photo and video documents, and fl oor plans; • Reference documents, such as industry and legal standards, pictorial standards, and municipal, state, and government regulations; • Work plans, quality control plans, time schedules, coating analyses, manufacturers’ technical data sheets (TDS), application instructions, and material safety data sheets (MSDS); • Order changes and addenda; • Reports (data logbook). With such a high amount of papers, it is extremely important for the CI to adopt a proper approach based on their special training – let us remember that we are talking about highly specialised professionals, with technical-inspection knowledge of the highest level. Such approach includes as follows:
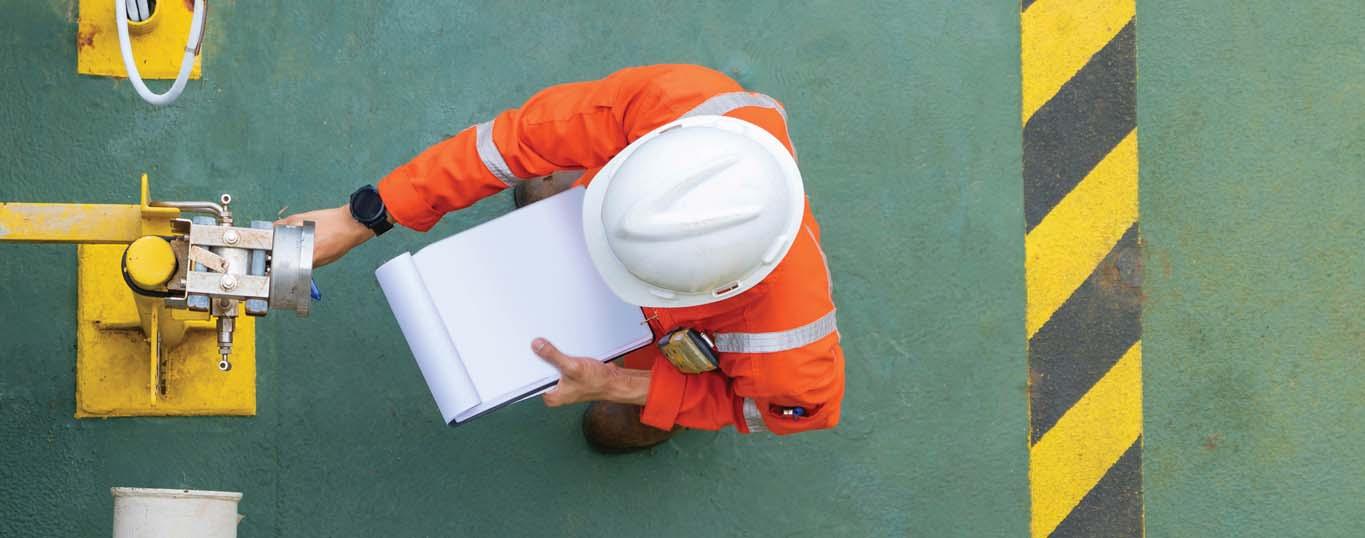
• Being self-responsible and getting to know all the surfaces that are going to be coated (weather they are simple metal bulkheads for containers, external surfaces of large tanks, parts required in a refi nery, or complex components for oil platforms), by both reading documents and physically going on site. • Familiarising with the specifi c properties of the individual coatings that will be used, their characteristics, and their application methods, as reported in the technical data sheets of each product. • Attending the pre-job meeting (PJM) and discussing any issues so that all the parties involved clearly understand the meaning of project specifi cations and job requests. During this meeting, the client should also offi cially clarify the CI’s degree of authority during all project phases. • Knowing the potential safety risks related to all project phases. To this end, before starting work, CIs should clarify their position regarding their own responsibilities and those of other parties involved. They must also be prepared to recognise any safety risks and take reasonable steps to minimise them wherever possible. Moreover, CIs should make sure that they are not involved in the monitoring of activities outside their responsibility and that they do not make any decisions that could aff ect other professionals. • Checking that all safety-related warning signs are correctly positioned and easily visible to all workers, that entry tests are safe, and that adequate work permits are issued. • Verifying and inspecting all the equipment that is going to be used both in the surface preparation phase and in the paint mixing and application ones, as well as in other operations to be examined from time to time, while also constantly monitoring environmental conditions.
2. Surface preparation inspection
Before the surface preparation phase starts, the inspector should check and report the initial surface conditions and verify that all the necessary preparatory work has been completed, including steel preparation if required. After surface preparation, the CI must verify that the cleanliness level and the surface profi le obtained comply with requirements. This is
© Adobe Stock
done through both control tests checking the cleanliness level of the compressed air used by the compressor and tests assessing the presence of any surface contamination. In the next article, we will describe in detail the surface preparation methods required for metal and concrete, which are very diff erent.
The CI should monitor the mixing and diluting steps as follows: • Checking and reporting all batch numbers; • Making sure that the material used complies with specifi cations; • Reporting mixing times and temperatures; • Checking that the mixed coating is homogeneous and that the paint manufacturer’ instructions are followed exactly as regards product addition, mixing, dilution, and stirring speed; • Verifying that the products’ pot lives are not exceeded; • Making sure that appropriate precautions are taken to prevent any contamination of the mixed materials. During the application of the coatings (primer, intermediate, and top coat layers), the CI should act as follows: • Monitoring environmental conditions and verifying that they fall within the parameters required by the specifi cations; • Observing applicators at work; • Checking that the applied paint fi lm is smooth, homogeneous, defectfree, and within the required thickness range (DFT). In the next articles, we will also explain in detail the CI’s responsibilities and tools during these three work phases.
4. Final post-application inspection
After application, the CI must measure the thickness of the applied fi lm (DFT) to make sure it falls within the parameters required by the project’s technical specifi cations, as well as performing a continuity test (or Holiday test), an adhesion test, a cure test, and other checks. Finally, the CI must verify that waste disposal takes place as required by current regulations. ‹