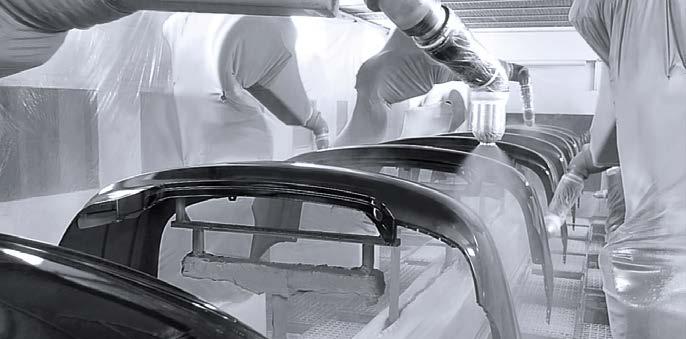
4 minute read
HIGHLIGHT OF THE MONTH
Aluminium and Plastic Paints: Diverse Industrial Needs, a Single Quality Requirement
Edited by Sames Kremlin
Pioltello (Milan), Italy marie-anne.guilldou@sames-kremlin.com
Cars, motorbikes, bicycles, smartphones, laptops, coffee machines... So many products whose aluminium and plastic painted parts present a great diversity of shapes, sizes, colours, layers to be applied and quantities to be processed. Sames Kremlin meets these needs with a wide range of solutions. What they have in common is the quality of the result. When it comes to paints and application quality, one industrial sector is the most demanding: the automotive industry. It is with this sector that Sames Kremlin has acquired its credentials over the decades by developing a whole range of solutions. They allow the application of powder or liquid paints, solvent or water-based, for series of all sizes and for all types of parts: aluminium bodies of top-of-the-range models, wheel rims, tailgate elements, bumpers, interior plastics of the dashboard or the trim, etc. Aluminium and conductive plastic parts are suitable for the ultimate application technique: electrostatic spraying. The principle is to electrically charge the paint droplets or powder grains and direct them towards the part to be treated, which is earthed. The paint is deposited in a perfectly uniform layer, without forming aggregates. It covers the entire part, including the back side and hardto-reach areas.
Avoiding touch-ups, not wasting paint
“The quality of the finish is such that touchups are minor or even unnecessary; the manufacturer saves a lot of time”, explains Marie-Anne Guilldou, EMEA Marketing Coordinator at Sames Kremlin. “The proportion of sprayed paint that reaches the part, which we call the transfer rate, rises to 80% for liquid paint compared to 60% for pneumatic application, while recycling rate approaches 100% for powder applications (and zero VOCs!). The result is product savings that accelerate the return on investment.” Sames Kremlin is deploying solutions for major global players in the aluminium wheel industry. If these are painted in a single coat, powder coating is chosen for its profitability and productivity. “We combine electrostatic spraying with a bell rotating at tens of thousands of revolutions per minute: it improves the dispersion of the powder grains, and therefore the quality of application.” Sames Kremlin is the only player in the market to offer this solution, called Inobell. A rotating bell has the same productivity as 2 to 3 automatic guns from the competition.
© Sames Kremlin © Sames Kremlin Automotive bumpers: the ultimate in high standards
For smaller volumes and/or multi-tone rims, liquid paint is the best choice: it allows much faster colour changes. Here again, electrostatic spraying and a rotating bell are combined in the Nanobell 803, launched in 2021, which succeeds the famous PPH 308. The automotive sector is just as demanding
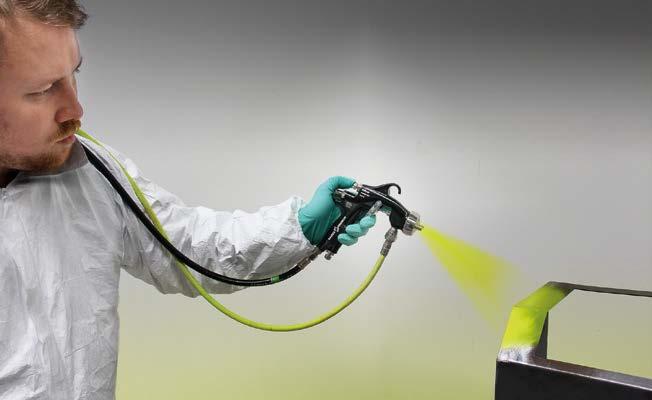
The automotive industry is one of the sectors that is increasingly demanding application quality.
for plastic parts. An extreme case: bumpers, painted at the manufacturer’s, which must have exactly the same colour as the bodywork painted on the manufacturer’s line. The slightest deviation in colour is rejected. “We use another electrostatic rotating bell, the PPH 707”, says Marie-Anne Guilldou. “In addition, we offer a paint circulation system, PaintCare, which avoids shearing: this could break or destructure the pigments, and would alter the colour.” PPH707 bells are also used by manufacturers of plastic tailgate components. Here too, the quality of the automotive finish is required.
Motorbikes and bicycles: liquid paint on high-profile parts
Sames Kremlin also deploys application equipment at motorbike and bicycle manufacturers. Powder coating is preferred for the less visible aluminium parts. Liquid paint, which is unbeatable in terms of visual results, is used for parts that are important to buyers: rims, mudguards, forks, fuel tanks, etc. If the manufacturer processes large volumes, he can equip himself with a robotic system and rotating bells for powder (Inobell) or liquid (Nanobell 803). If the parts to be painted are non-conductive, for example car interiors or the shells of smartphones and laptops, it is necessary to return to pneumatic spraying. But without compromising on the quality of the finish. Sames Kremlin offers an automatic gun, the A35, and a manual one, the FPro. “It is the only one on the market with vortex technology that disperses the paint into finer, more homogeneous droplets. The result is a flawless application...” Electrostatic spraying is still relevant, however, if the plastic parts have a complex shape that would involve time-consuming and costly rework. After applying a conductive layer, for example with an A35 pneumatic gun, the Nanobell 803 rotating bell and an automated or even robotic system can be used. This is particularly the case for the shells of high-end coffee machines.
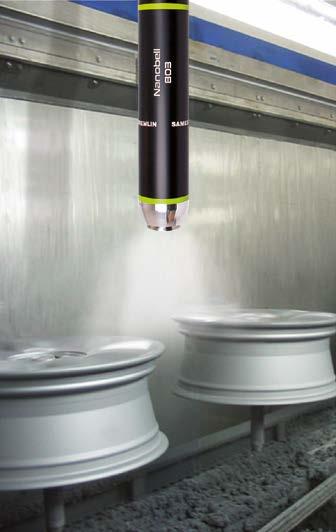
© Sames Kremlin
A liquid coating application with the Nanobell 803 rotating bell.
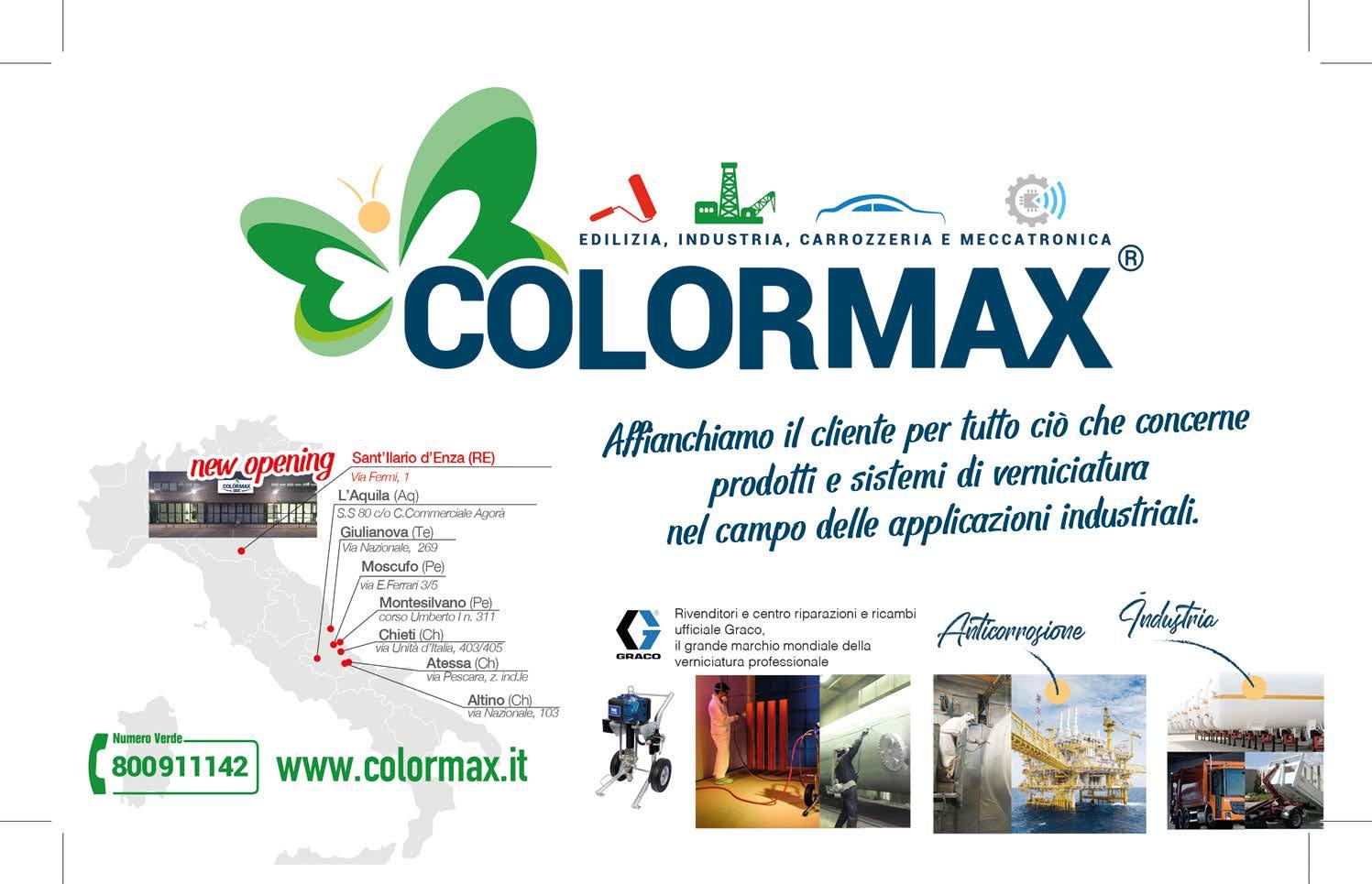