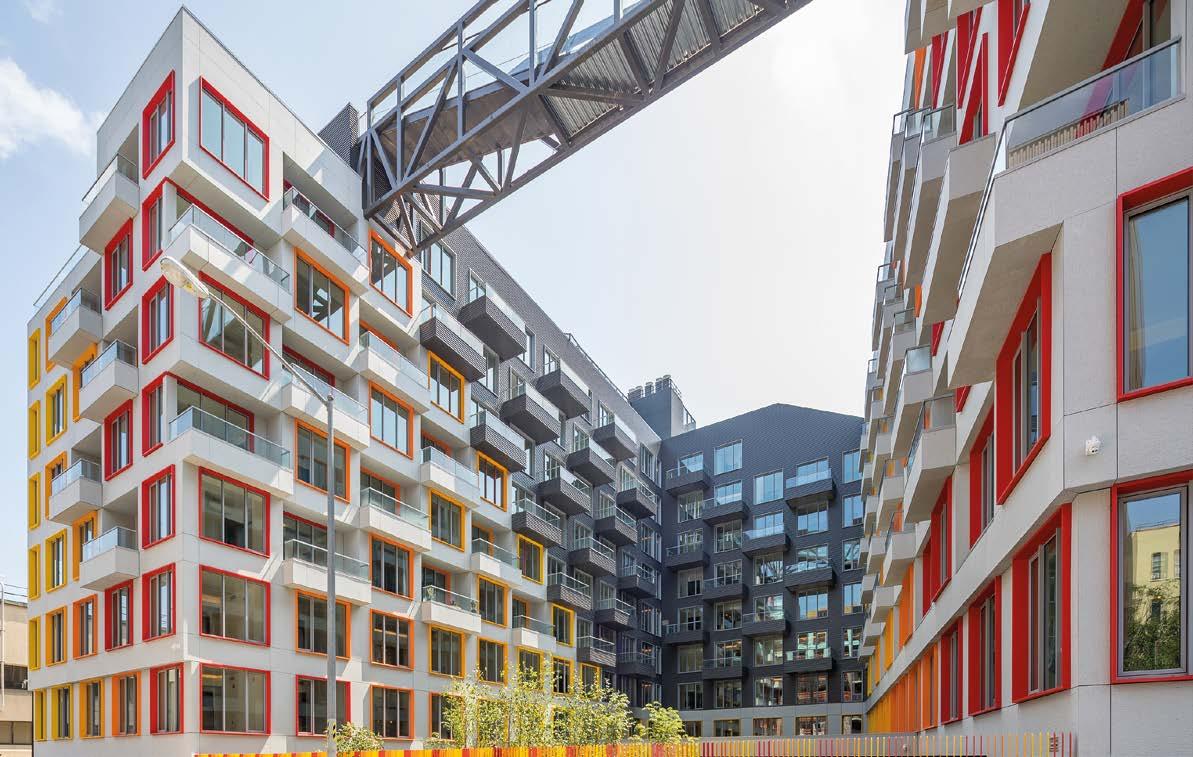
15 minute read
SUSTAINABILITY
Powdura ECO Powder Coatings: from Plastic to Powder
The Sherwin-Williams scientists developed a new process which converts plastic waste into a durable, high-performing polyester resin that contains 25% pre-consumer recycled plastic (rPET).
The issue of plastic waste polluting our oceans is well documented and reported to be around 12 million tonnes of pollution each year - this is the equivalent of > 700 billion plastic water bottles1 . Why is this happening? Plastic is cheap, strong, lightweight and malleable making it ideal for single-use plastic containers, which have been widely adopted as a convenient way to package and carry food and drinks. Once the contents are consumed the container is discarded as waste that eventually makes its way, via the waste cycle, into the oceans. Many polymers are difficult or expensive to recycle, however the scientists at The Sherwin-Williams Company have found a way to repurpose the polymer used to manufacture plastic water bottles and convert it into a powder coating. Powder coatings are amongst the most sustainable coatings available as they contain no VOCs and have utilisation rates >95%. ‘Using pre-consumer PET waste that would normally go to landfill and recycling it into a functional coating that is used to protect products from corrosion, extending their service life, makes perfect sense’ explained Aliette Brochier, Product Director of The Sherwin-Williams Company. ‘Not only does this support the circular economy by recycling waste material, but it further reduces the environmental footprint of powder coatings by capturing the good carbon contained in the waste PET’, she went on to explain. ‘PET
1 “Plastic Waste Inputs from Land into The Ocean”, Science, Feb. 2015, Vol. 347, Issue 6223, pg. 768-771. (polyethylene terephthalate) contains the same monomers (building blocks of polymers) as the resins used in the binders of powder coatings. The novel process the scientists developed to capture and stitch these monomers directly into the backbone of the Powdura ECO powder coating resin not only reduces the environmental footprint of the coating by 20%, as demonstrated in life cycle analyses, but the resulting coating has the same protective, decorative and functional properties as a product made from virgin resin’. The Sherwin-Williams scientists put Powdura ECO through its paces, probing the performance with an exhaustive array of mechanical, environmental and chemical tests against a class-leading control with the results in the table below exceeding expectations. As the recycled material is polymerised into the resin backbone this gives a wide degree of formulation flexibility with Powdura ECO being offered in a full range of colors, gloss levels, effect and textured finishes. The incorporation of recycled PET, the equivalent of 35 plastic bottles per kg, into Powdura Eco translates into quantifiable environmental benefits, creating a competitive advantage for manufacturers looking to achieve corporate sustainability targets, differentiate their products in the market-place or meet the requirements of third-party certifications such as LEED, BREEAM, GREENGUARD and GBB.
For further information: https://industrial.sherwin.eu
TEST PROPERTY
Smoothness Rating @ 2.0 mils Impact (Direct/Reverse) Conical Mandrel Bend Pencil Hardness Crosshatch Adhesion Re-coat Adhesion Chemical Resistance (100% MEK)
Humidity Resistance (500 hrs.)
Salt Spray Resistance (500 hrs.)
Powdura ECO’s tests results.
TEST METHOD
PCI #20 ASTM D2794 ASTM D522 ASTM D3363 ASTM D3359 ASTM D3359 PCI #8
ASTM D2247
ASTM B117
POWDURA ECO
≥6
160/160 in. lbs. 1/8” No Cracking ≥2H
100% (5B) 100% (5B) Pass Blister Rating: 10, no blisters Rust Rating: 10, no rust Avg. creep from scribe = <1.0 mm Blister Rating = 10, no blisters Rust Rating = 10, no rust 60° Gloss Retention = ≥85% - ∆E = ≤1.0
© VanceFox.com
The Rheingold building at 10 Montieth Street, Brooklyn, NY (top photo), and a house in Martis Camp, Truckee, CA. Located midway between historic Truckee, California and North Lake Tahoe, Martis Camp is a 2,177-acre private, luxury community. Loverde Builders.
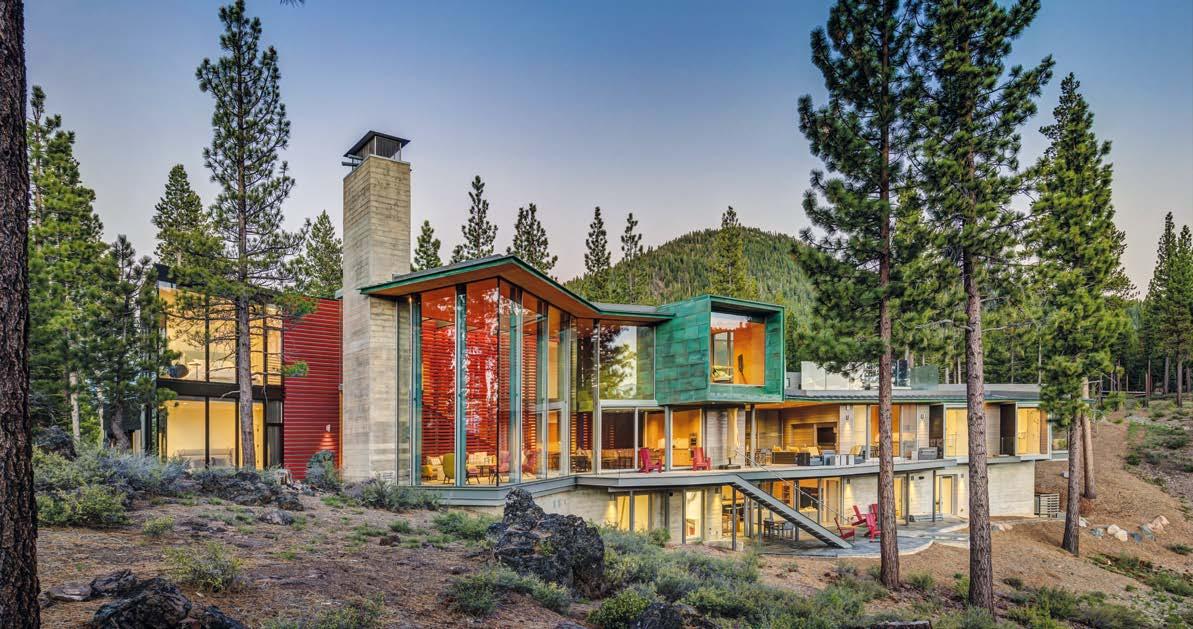
FOCUS ON TECHNOLOGY
SPECIAL ISSUE ON ARCHITECTURE & DESIGN
A FOX System for In-Line Pre-Anodising and a C-Expert Booth: Alural’s Future-Proof Technical Choices
Alessia Venturi ipcm®
Flash oxidation as an additional pre-treatment step for aluminium profiles to ensure even longer outdoor durability has been a topic of debate for some ten years now. Another debated aspect is the difficulty of coating such profiles’ increasingly complex shapes, which prove that their developers take little account of the technical peculiarities of finishing operations when designing new parts. In this article, we show how Alural, one of the largest aluminium coating contractors in the world, has tackled (and solved) these technical issues with the cooperation of its plant engineering partner SAT.
With 2 production sites, 350 employees, and a production capacity of 9,250,000 m2 of painted material and 660,000 m2 of anodised metal, Alural is one of the largest aluminium finishing contractors in the world. Active in several European countries, it offers a complete service to extruding and plant engineering firms: powder coating with various types of pre-treatment processes, wood-effect finishes, and anodising, but also storage, order management, packaging, and logistics. Whereas high quality, high specialisation, and excellent service are the mission of this company with 35 years’ experience in the aluminium treatment market, continuous technological innovation is what has made Alural a leader in its field. It continuously invests in new production and process technologies and in new plants, while at the same time exchanging information and knowledge both within its Group – it was acquired by Reynaers Aluminium in 2011 – and within the associations to which it belongs.
© ipcm
The latest SAT vertical coating line installed at Alural at the beginning of 2021.
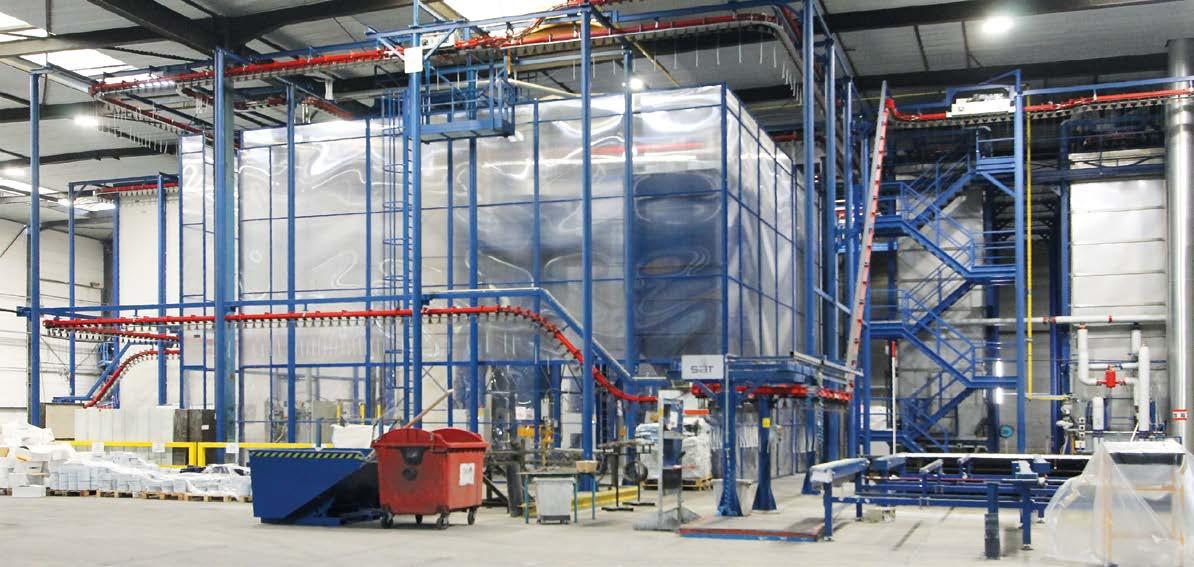
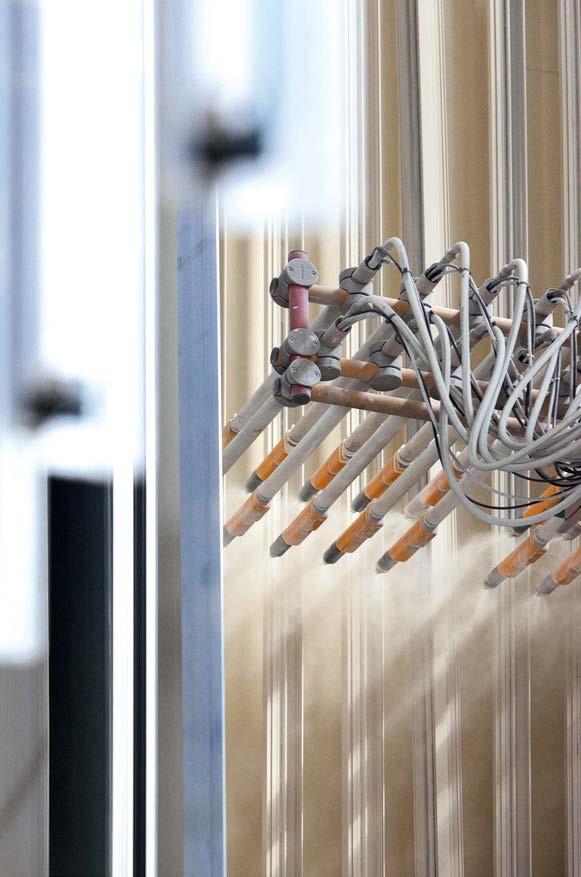
©Alural ©Alural
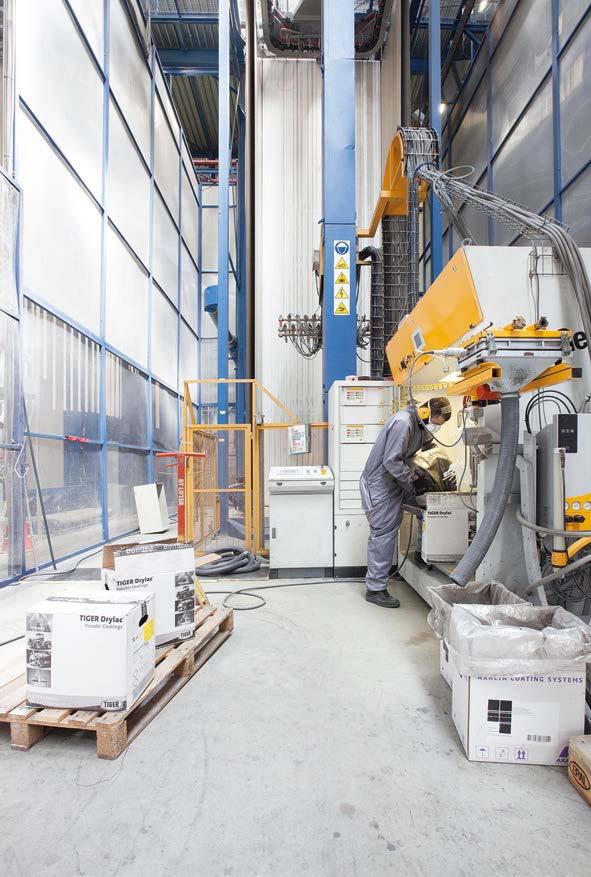
SAT’s new generation application booth called C-Expert for its peculiar C-shape. The gun arrangement has remained the same as the one of the V-shape, given its proven efficiency. It allows spraying on both sides of a profile at the same time.
Company history
The industrial history of Alural began 35 years ago in Boom (Belgium) as a small contract coating firm. Today, it has two production sites, in Lummen and Tisselt-Willebroek. In these two factories, Alural provides its customers with totally finished products, managing batches of any size thanks to its impressive equipment, which includes three vertical coating lines, two horizontal lines, a painting system for small parts, a sublimation plant for wood-effect finishes, and an anodic oxidation line. Alural also represents the perfect link between system houses (such as Reynaers, Schüco, and AluK to name but a few) and manufacturers, guaranteeing extreme product customisation and perfect coating quality in compliance with the most stringent European standards (Qualicoat and Qualanod) and covered by an insurance policy, as well as reliability, precision, and punctual deliveries. For the producers of other components, such as shutters, awnings, doors and gates, greenhouses, and bioclimatic pergolas, Alural is a partner capable of providing customised logistical solutions in addition to finishing services. “Since its takeover by Reynaers Aluminium in 2011, Alural has grown faster and faster,” starts off Philip Hilven, the Sales and Commercial Manager of Alural NV. “We are no longer strictly dependent on market demands because our parent company supplies us with material every day, accounting for 60% of our workflow. In order to meet demand, our plants operate in three shifts. Our main market is Belgium, followed by the Netherlands, Great Britain, and for some time now
also France, which is gaining increasingly more importance. This is why our most recent investment was the construction of a new automated high-bay warehouse with 4,100 pallet spaces. Until today, logistics has been a limitation for our activities: we lose at least one day in transport alone. With this warehouse, we will be able to offer warehousing and on-demand order picking services and to limit transport to deliveries alone, while expanding our area of influence to half of Germany on the one hand and to Bordeaux in France on the other hand.”
A single plant engineering partner to ensure business continuity
“In order to make a profit, a contractor with our current structure has to run its plants 24/7,” explains Hilven. “We cannot afford to rely on suppliers who do not deliver powder coatings or chemicals on time, for example, just as we cannot have the slightest technical problem that cannot be solved quickly and remotely: if one of our finishing lines stops for two hours, we send our operators home to avoid losses. This is the reason why Alural’s owners chose to rely on a single partner for our vertical coating systems, in order to work more smoothly and easily and to readily replace spare parts if necessary. Italian company SAT was selected for this role: all the three lines operating in Alural’s factories, one in Tisselt and the other two in Lummen, were designed and installed, and subsequently revamped in the case of the two oldest ones, by this Verona-based firm.” Indeed, over the last two years, SAT has carried out three major interventions on Alural’s vertical coating lines: in 2020, the Tisselt plant was almost completely revamped, with the exception of the conveyor, and the two application booths were replaced with newer V-Shape ones. In 2021, SAT installed a new vertical system in Lummen, which included the C-Expert application booth launched by the company in March this year. Also in 2021, SAT integrated the alreadyexisting vertical plant in Lummen with a FOX system for in-line pre-anodising processes.
C-Expert: the innovative features of the last system installed
The latest vertical coating line installed at Alural has two innovative elements: a new type of ovens for drying and curing, with some technical features
© ipcm
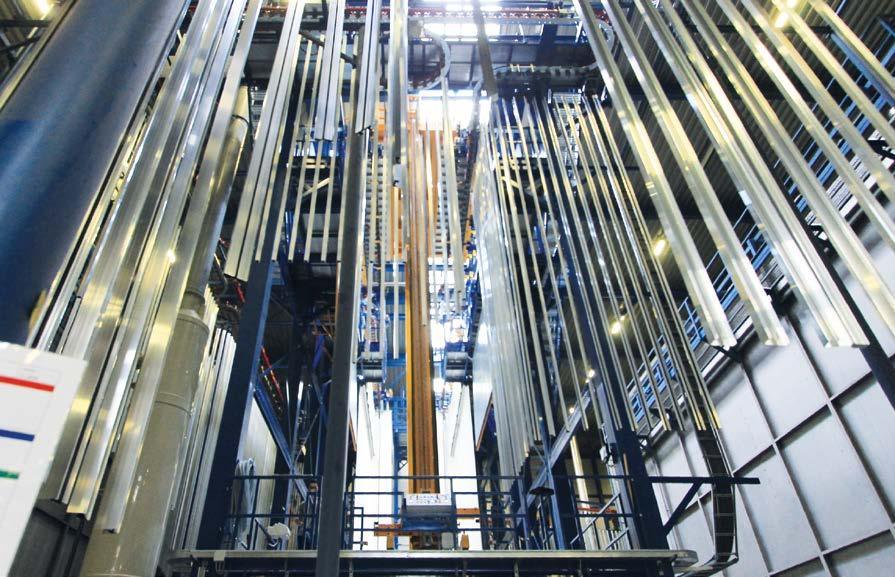
The second major intervention carried out by Alural in cooperation with SAT earlier in 2021 was the addition of a FOX (Flash OXidation) system to the existing vertical line at the Lummen factory.
© ipcm © ipcm
The crane lowers the aluminium profiles in the flash oxidation tank.
Back in 2015 Alural’s plant had already been prearranged by SAT for the integration of the FOX system and its necessary electrical wiring.
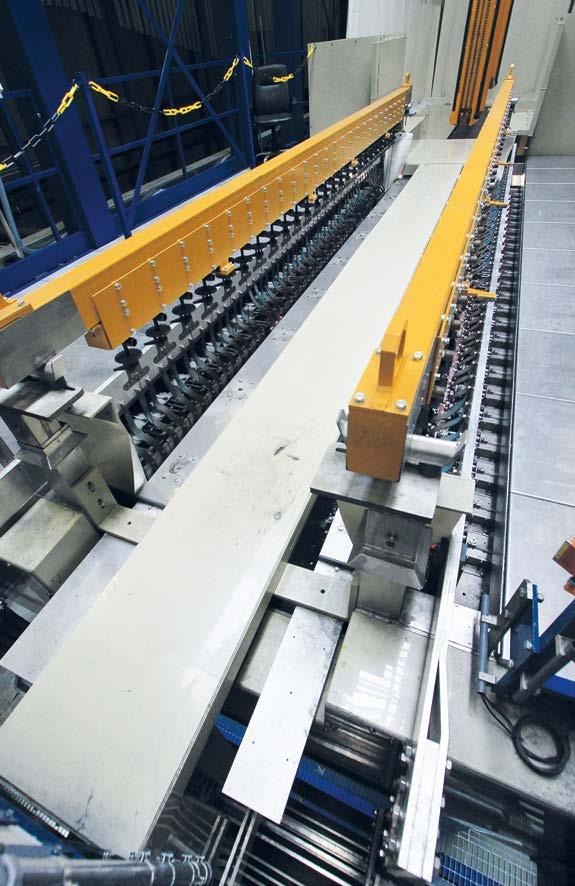
and a general set-up that make them energy efficient and simplify maintenance, and SAT’s new generation application booth, launched earlier this year and called C-Expert. “Compared to our V-Shape booths, the shape and structure of the C-Expert ones is slightly different (C-shaped), while the gun arrangement has remained the same, given its proven efficiency. It allows spraying on both sides of a profile at the same time, creating a powder cloud that helps increase transfer efficiency,” explains Alberto Formenti from SAT. “The C-Expert machine was conceived in our test laboratory in Verona, where we carry out numerous tests to improve our existing products and develop new technologies. This booth has been designed for those customers, mainly contractors, which paint a high number of different profiles with very complex geometries, as it is able to maintain a constant painting configuration for each difficult-to-coat profile.” “The biggest problem with plant engineering companies’ R&D departments is that they do not take into account the difficulty of coating the geometries of the profiles they develop,” states Philip Hilven. “The coating phase, with all its critical aspects and peculiarities, is not considered at all during design. This results in the development of very large profiles with difficult-to-reach bends and grooves. A second problem that undermines the quality and consistency of the powder coating operation is the insulation of profiles: the insulation strip between different components partially hinders paint adhesion. However, with the new line we commissioned from SAT, which features
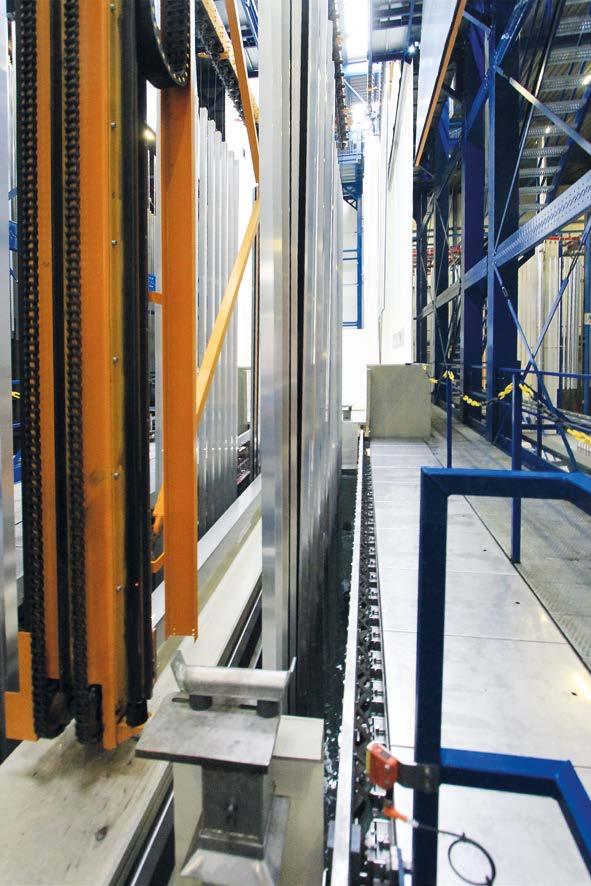
electrostatic optimisation features, and in particular thanks to the C-Expert booth, these two critical aspects are 100% under control. The new drying and curing ovens’ concept is also very satisfactory because it enables us to recover residual heat to pre-heat the powder and thus avoid using an IR oven, which, on the other hand, we are still using on the Tisselt line. Revolving doors also contribute to greater energy efficiency and therefore cost savings.” As far as pre-treatment is concerned, the new Lummen coating line features a traditional reverse cascade tunnel with a “French” cycle, i.e. alkaline degreasing and acid etching. “Demand from the French market is growing, and therefore we have chosen to offer the alkaline+acid pre-treatment cycle as a standard to meet the Qualimarine certification requirements,” indicates Hilven.
In-line pre-anodising: a trump card for meeting market challenges
The second major intervention carried out by Alural in cooperation with SAT earlier in 2021 was the addition of a FOX (Flash OXidation) system to the existing vertical line at the Lummen factory, which was installed by SAT itself in 2015. “The demand from some markets for flash anodising as an additional pre-treatment step to increase the outdoor resistance of aluminium profiles is growing at such a rate that I predict that, within five-years years, pre-anodising will be prevalent in the coating market,” says Philip Hilven. “Before we integrated the Lummen line with the FOX system for in-line pre-anodising, our anodising plant was practically only devoted to this process. This saturated its capacity and caused us to lose up to five days on delivery times. Not to mention the fact that we had to turn down requests for anodised or electrocoloured profiles, which have been increasing in the powder coating market lately.” “Why do I believe that pre-anodising will be strategic in ten years at the most? Firstly, because of the quality degree of primary aluminium, which is not always constant enough to guarantee the outdoor resistance level required by our customers. Secondly, because of the widespread use of recycled aluminium, which should certainly be safeguarded but which calls for greater care during extrusion. Unfortunately, unlike the quality of aluminium, the quality of extrusions is something we cannot measure. This is why we guarantee a minimum standard of 2 g/m2 of etching with traditional pre-treatment, but we prefer to focus on pre-anodising as a quality strategy. Now, thanks to our in-line pre-anodising system, we can offer this additional processing at a lower cost and within the cycle time of a normal painting process.”
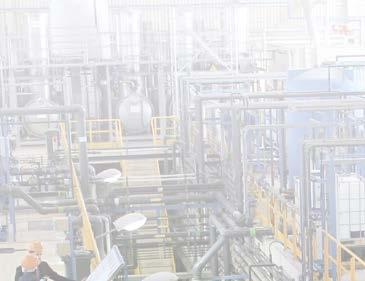
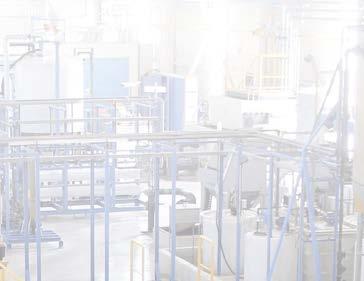


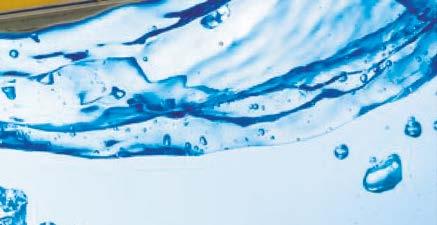
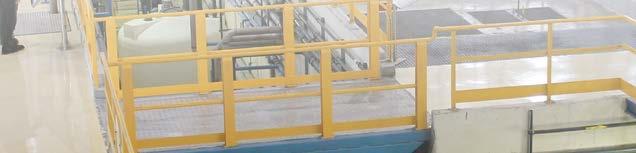
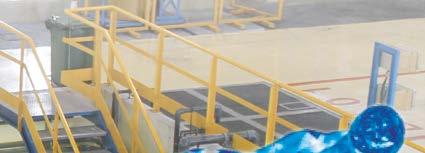
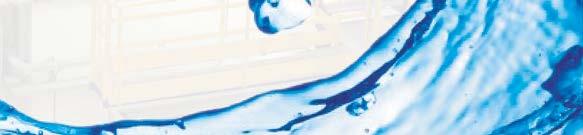
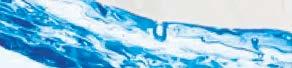
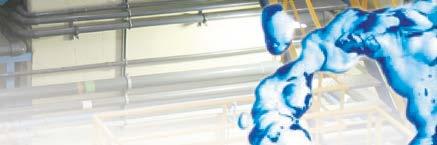
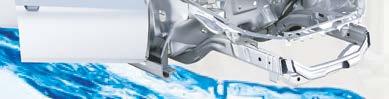
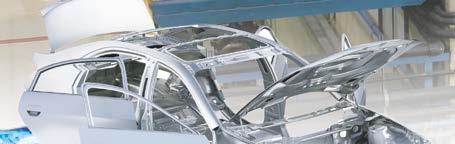
© ipcm © ipcm
The transport system of the FOX system transfers the profile from the monorail conveyor to the crane that lowers them into the flash oxidation tank. From the left Alessia Venturi, Philip Hilven of Alural and Alberto Formenti of SAT.
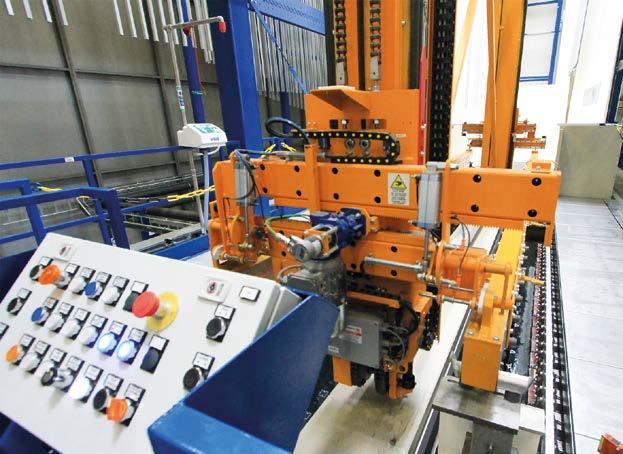
In 2015, Alural’s plant had already been prearranged for the integration of the FOX system. This is why the implementation of such an important technical improvement was a “little miracle” and everything worked perfectly, also thanks to Alural’s in-depth knowledge of anodising processes. “We are talking about the installation of a very large system, with complex components, special requirements such as a deep installation pit for the anodising tank, complex electrical wiring, and a complex handling unit,” adds Alberto Formenti. “This project came eleven years after the installation of our first FOX plant, in Vietnam: the experience gained during this time has enabled SAT to improve the system and achieve even greater performance in terms of line speed. Some components have been completely redesigned with respect to the original FOX system in order to avoid the occurrence of certain critical problems; the chemical pre-treatment cycle prior to the flash anodising phase has been improved to ensure the application of a minimum thickness of 4 microns of oxide in a uniform and constant manner, as required by current regulations. Clearly, this is a top-level technology, which requires a major investment not only in the system itself but also in the factory (appropriate foundations, deep pit, etc.).” The future of aluminium coating
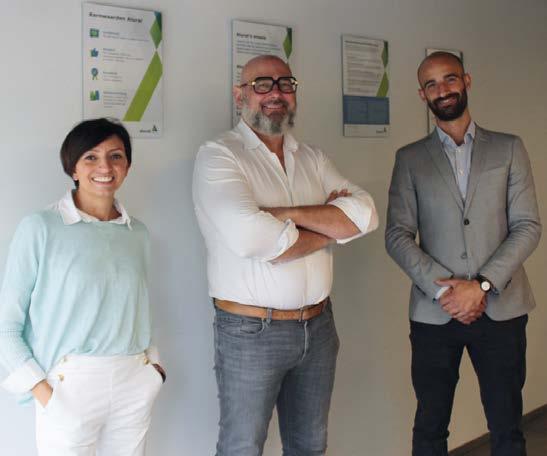
“At Alural, we believe that an excellent pre-treatment process and the application of Qualicoat certified powders, combined with premiumquality raw materials and extrusions, are the only way to guarantee an outdoor durability of 20-25 years, as required by northern European markets,” says Hilven. “This is why we never apply Qualicoat 3 powders: although they guarantee the same resistance degree as Qualicoat 2 ones, they are too expensive, present mechanical issues, and are available in only a few colours. We chose to propose, or rather impose, pre-oxidation as a winning technology and a guarantee of quality. Numerous company are already interested in our FOX system. Many of them are asking to come and see this frankly impressive line. Thanks to the latest investments made with SAT, Alural can respond much more quickly to market demands than any other contractor on the market and with far greater volumes: we have a production capacity of 35,000 m2/day and we can produce pre-oxidised coatings in almost the same cycle time as traditional coatings. The market is rewarding us with a boom in orders: we have already exceeded our 2021 forecasts by 30%.” This is very good news – for the entire European aluminium market.