
9 minute read
ART WITHIN SURFACES
Graco’s Winning Team to Celebrate the Best Cyclists in the World
Wim Belmans from Graco actively collaborated with street artist Thomas Daem, employing two Cordless 390 Classic units, to paint the portraits of famous cyclists along the road of the 2021 UCI Road World Championships.
Wim Belmans, District Manager CED of Graco, has cooperated with the art collective Puncheur for a special street art project on the famous Flander’s cycling roads. Aiming to honour the greatest cyclists in history, they employed two Cordless 390 Classic units to paint the faces of the athletes along the trail of the 2021 UCI Road World Championships, which took place in Belgium from 18th to 26th September 2021. The original idea came to the Belgian graphic designer Thomas Daem for Tom Boonen’s last year as a professional cyclist in 2017. The artist and his dad created some basic stencils with spare cardboard from the grocery store and painted the face of Boonen on the road. Since then, Daem made several other portraits, such as the ones of Peter Sagan, Frank Vandenbroucke, Johan Museeuw, Bradley Wiggins and Wout van Aert, becoming very renowned in the world of cycling and street art. For the 2021 UCI Road World Championships, he and the street-art collective Puncheur searched for better equipment and finally chose Graco airless machine to lift his art to a higher level. Belmans became immediately fascinated with the projects, and after some initial tests they both discovered that Graco cordless 390 classic units made their work faster and easier. In total, the team painted 16 portraits of 3.75 m x 2.55 m in just three days, working tirelessly from 09:20 am until past midnight. “Graco as a partner is very proud to cooperate in this very unique sports event and is even more proud that the lightweight and compact design of the new battery-powered sprayer, which was on top of that highly portable, turned out to be the ideal help for this paint jobs,” commented Belmans.
For further information: www.graco.com
© Graco © Graco
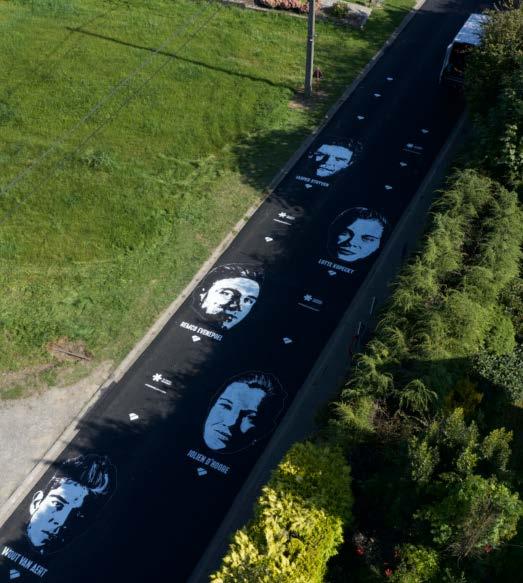
© Sud-Ouest Laquage
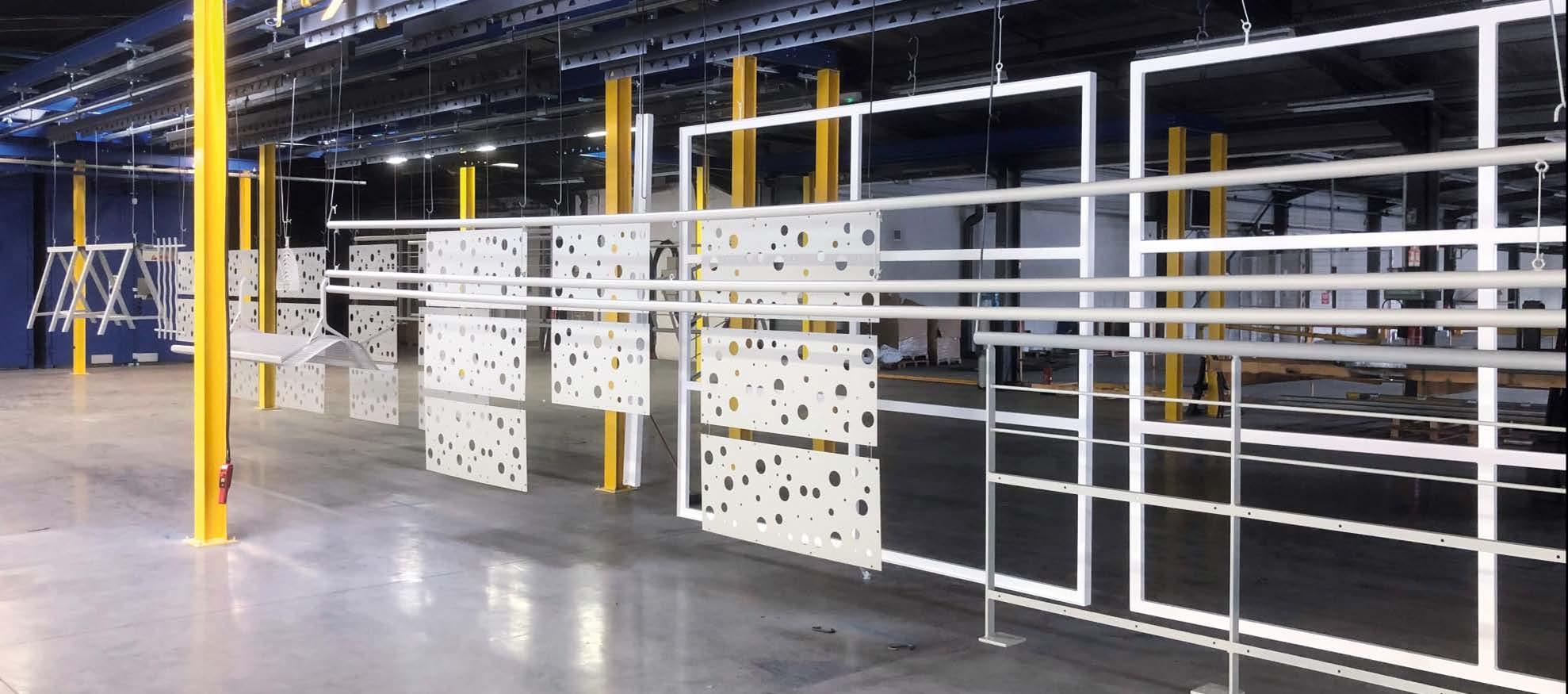
Some of the products powder-coated by Sud-Ouest Laquage (Barbezieux, France).
FOCUS ON TECHNOLOGY
The Key Role of Multi-Metal Pre-Treatment in Improving Powder Coating Adhesion and Quality
Monica Fumagalli ipcm®
The integration of a 5-stage automatic multi-metal pre-treatment tunnel in its powder coating department has enabled Sud-Ouest Laquage to improve paint adhesion on steel and aluminium substrates and, thanks to the faster production process, deliver high-quality products within just a few days, thus optimising its ability to penetrate markets other than its own.
For more than twenty years, the art of transforming metal has been one of the specialisations of Charente Pliage, a company based in Montboyer (France) machining and painting aluminium, stainless steel, galvanised steel, and other components, be they mass produced or made to measure for the architectural sector. The continuous search for solutions capable of preempting the needs of the market and reducing process times, without of course losing sight of product quality, led this French company to create a new production unit dedicated exclusively to powder coating small and large products. Charente Pliage thus founded Sud-Ouest Laquage in 2021. It set it up with a shot blasting cabin, a metallisation cabin, a powder coating booth, and two curing ovens, all supplied by Industrie-Systèmes (Bouches du Rhône, France), which has been offering turnkey painting products and equipment since 1985.
“Although our company is young,” states Mickaël Matignon, Associate General Manager at Sud-Ouest Laquage, “our team has many years of experience in powder coating. Thanks to this know-how, we are already receiving more and more requests from both our local market, that is, the southwestern region of France, and the national market. This is why we decided to speed up our preparation phase prior to painting by integrating an automatic pre-treatment tunnel, and once again we turned to our trusted supplier, Industrie-Systèmes.” Since 2010, Industrie-Systèmes has been working in partnership with Eurotherm Spa, an Italian company specialising in the design, manufacture, and installation of liquid and powder coating lines, whose commercial activities conducted in France were managed by the former.
An established team of suppliers
Sud-Ouest Laquage worked with Industrie-Systèmes to design and install its powder coating line from the outset. “We knew the reputation that Industrie-Systèmes had acquired in France thanks to its professionalism and in-depth experience in the supply of turnkey plants,” says Emmanuel Lafon, General Manager at Sud-Ouest Laquage. “Its collaboration with Italian company Eurotherm has given it an even more international profile and enabled it to consolidate its business beyond France. We visited the Eurotherm factory in Volpiano (Italy) to see the results of their solutions for ourselves. We were immediately convinced of the need to continue working with them in order to improve our paint adhesion and product quality levels and thus fully meet the demands of our partners – which, after only a few months since the start of our activity, are becoming not only more numerous, but also highly varied in terms of industries.” The latest addition to this partnership was Aertech, specialising in supplying technical solutions for industrial coating and surface treatment departments, which provided the chemicals for the pre-treatment process. Aertech is the sister company of the Chemtec Italian company which has been producing and distributing chemical products for the metal surface and water treatment for the coating industry since 2010.
© Industrie-Systèmes

The exterior of the pre-treatment tunnel, the powder coating booth, and the curing oven.
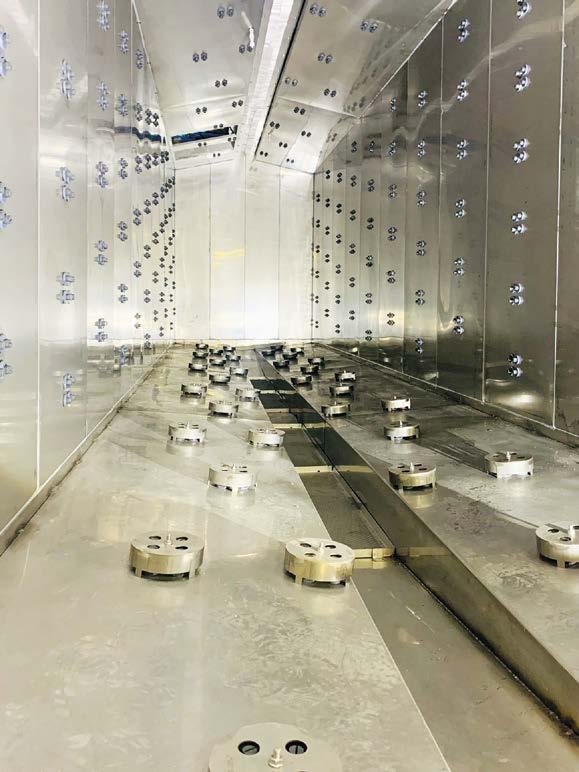
© Industrie-Systèmes
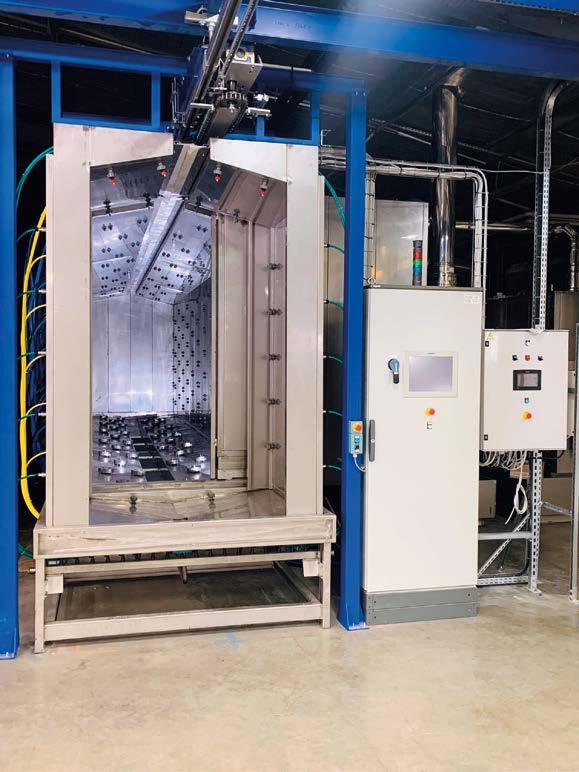
The 5-stage pre-treatment tunnel, the latest system to be integrated into the coating department.
“Our collaboration with Industrie-Systèmes and the team of companies working with it” - continues Lafon - proved to be a winning choice: they understood what we needed and supported us very carefully through every stage of the development and installation of our 5-stage pretreatment tunnel.”
The flexibility of the new pre-treatment tunnel
One of Sud-Ouest Laquage’s most pressing needs was to find a pre-treatment solution that would be effective for different types of materials and components. “We process parts characterised by different dimensions, materials, and shapes. We carry out metallising or shot blasting treatments on products that need extra corrosion protection. However, for the other components, we were also looking for a solution that would ensure greater resistance to weathering and corrosion and excellent powder adhesion. Our plants are capable of treating products up to 4 m long, which we powder-coat in a large booth: the problem was to find a pre-treatment system that would not only be effective on any metal substrate, but would also provide optimal powder adhesion results. We therefore worked with Industrie-Systèmes to develop a pretreatment tunnel capable of meeting all these requirements.” “The concept of this tunnel is unique,” states Mathieu Breton, General Manager of Industrie-Systèmes, “because it allows carrying out two different pre-treatment processes in the same chamber, depending on the type of material to be treated. In the case of steel and galvanised steel, we perform a phosphodegreasing or alkaline degreasing stage, followed by three rinses, including two with mains water, and one with osmosis water and nanometric conversion. In the case of aluminium, on the other hand, acid pickling is carried out first to remove the oxides that remain on the workpieces’ surfaces after welding and annealing, followed by three rinses, including two with mains water and one with
© Industrie-Systèmes
The inside of the pre-treatment chamber, where components of different materials can be cleaned.
© Industrie-Systèmes
The feeding system of the pre-treatment tunnel.
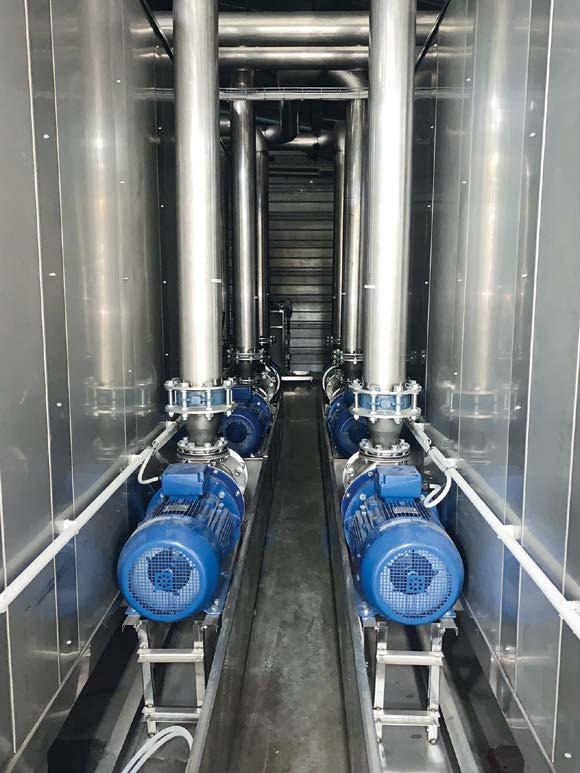
osmosis water, and nanometric conversion.” “The chemical products are formulated and manufactured by Chemtec in Italy and distributed by Aertech in France” - says Carlo Giudetti, CEO of Chemtec. “This double pre-treatment cycle guarantees the highest quality level for each type of metal. The formulations have been developed specifically for single-chamber tunnels, which always represent particular applications due to the high contamination rate of the rinsing tanks. The passivation applied to each surface is the latest innovation available in the pre-treatment industry: the PRONORTEC process developed by Chemtec is the only nanotechnological conversion that exploits the chemical features of organic phosphorus compounds. It is totally free of heavy metals, does not require rinsing, has a very long life and very simple application and is able to guarantee the same coat adhesion and corrosion resistance levels as the ones guaranteed by microcrystalline zinc phosphating”. “The possibility of choosing between these two processes,” notes Mr. Matignon, “ensures we always achieve the best level of metal preparation prior to coating, in terms of both mechanical strength and anti-corrosion resistance.” The tunnel has been designed to minimise the risk of contamination of liquids during rinsing. “In addition, to avoid contamination of the pre-treatment chamber due to the performance of different processes, we have equipped the plant with a zero-liquid discharge water treatment system that filters the different chemicals used during the cycles, purifies the liquid, and sends clean water back to the machine.” Thanks to this special system, entirely designed and supplied by Aertech, it is no longer necessary to drain water from the rinsing tanks to ensure the high quality of the processes: water consumption corresponds to the actual use of the system without drains or wastewater. The 5-stage pre-treatment is followed by the drying phase and the
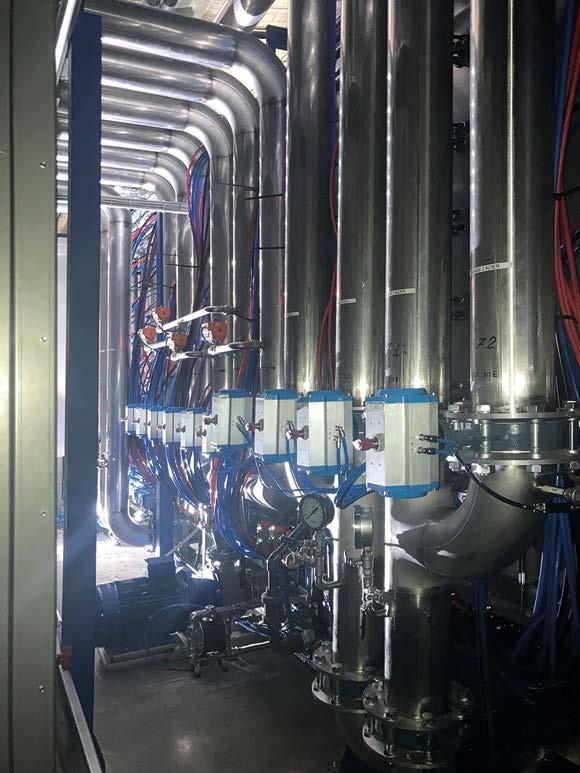
© Industrie-Systèmes
Electric recirculation pumps.
Some special workpieces painted by Sud-Ouest Laquage.

© Sud-Ouest Laquage
application of powder primers and coats, in which Sud-Ouest Laquage specialises. After curing, the coated products undergo a quality control and then they are ready for packaging and delivery or collection by customers.
Conclusions
“Thanks to this investment,” says Mr. Lafon, “and to the quality of service provided by the team made up of Industrie-Systèmes, Eurotherm, and Aertech, Sud-Ouest Laquage now has the opportunity to increase its production capacity and respond more promptly to requests not only from the architectural sector, with which we were started out thanks to the reputation of Charente Pliage, but also from other industries, such as furniture and carpentry, without limitations on the materials treated and with the certainty of offering a high quality service. Moreover, we have improved the working conditions of our operators by making them less burdensome, thanks to the elimination of sanding operations before painting, now replaced by chemical pre-treatment. Finally, thanks to the water recovery and recirculation system, we have even minimised our running costs. The latest plant innovations by Eurotherm and Industrie-Systèmes combined with the technological development in the surface treatment of Chemtec and in the water treatment of Aertech guarantee us to achieve excellent results in terms of coat adhesion and corrosion resistance without using technologies with a strong environmental impact, creating wastewater rich in toxic substances, and discharging polluted water, by minimizing energy and water consumption. Technological innovations now guarantee the coating industry to achieve the objectives of the green and circular economy”.