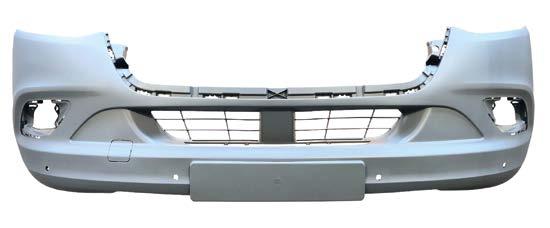
11 minute read
HIGHLIGHT OF THE MONTH
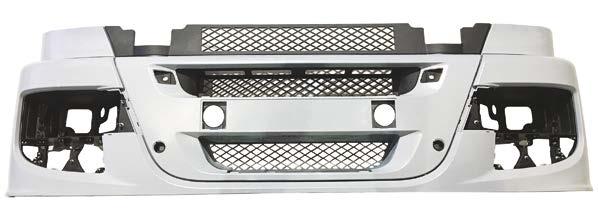
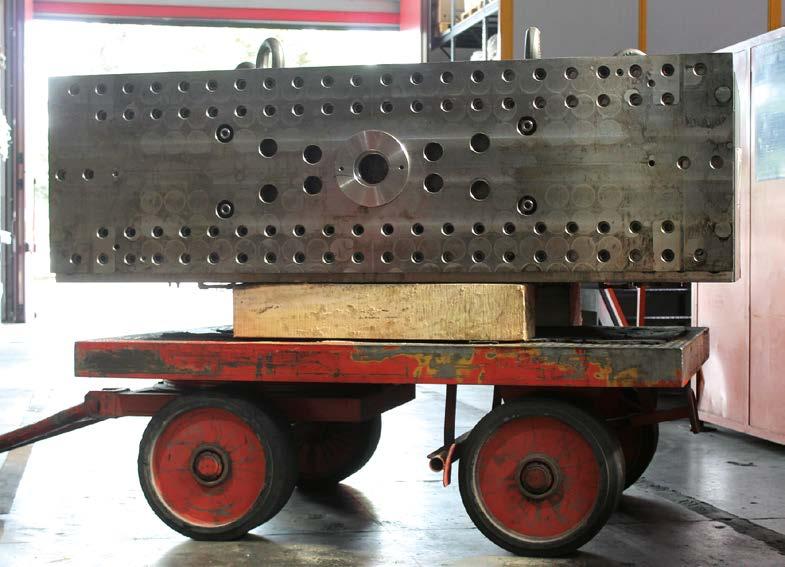

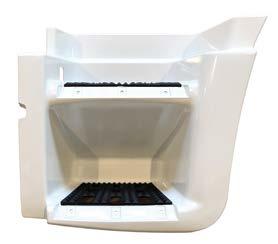
Paraurti realizzati da Poliplast Srl di Albiate (Monza e Brianza).
FOCUS ON TECHNOLOGY
SPECIAL ISSUE ON ACE & OFF ROAD VEHICLES
L’intuitiva programmazione in self-learning dei robot semplifica la gestione della produzione per la consegna in real time di ricambi automotive
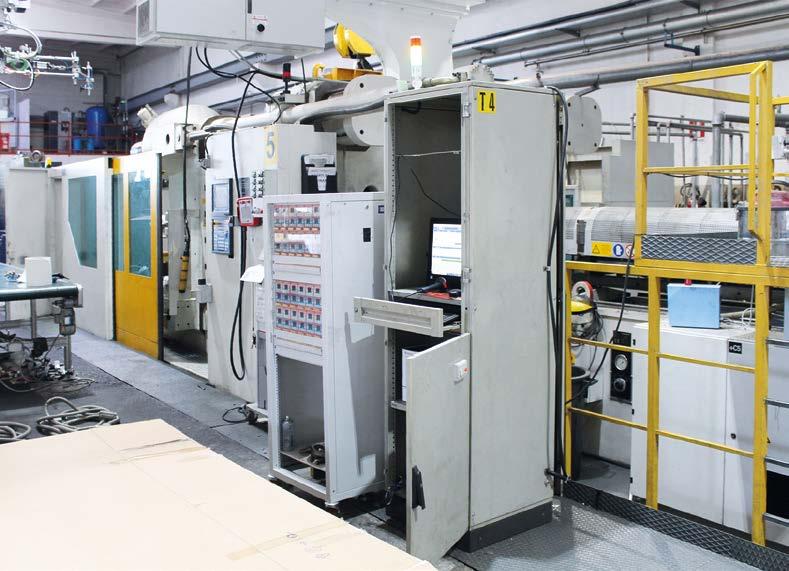
Monica Fumagalli ipcm®
Poliplast, azienda storica del settore della ricambistica in plastica per veicoli commerciali e industriali, ha attrezzato le sue stazioni robotizzate di flammatura e verniciatura con 3 robot Lesta in grado di garantire applicazioni in tempi rapidi e con prestazioni ottimali, un aspetto strategico nei sistemi produttivi scanditi dalle continue necessità di ripristino delle scorte a magazzino delle aziende attive nell’aftermarket.
In un settore caratterizzato da enormi quantità di articoli e da una domanda altalenante e intermittente come quello dell’aftermarket, la gestione attenta delle scorte è fondamentale e deriva dall’ottimizzazione del flusso produttivo attraverso gli strumenti impiantistici e informatici atti a semplificare ogni fase del processo per rispondere in modo rapido e flessibile alle richieste di consegna in realtime dei clienti. Poliplast Srl di Albiate (Monza e Brianza) è un’azienda storica del settore, attiva da oltre 50 anni nell’aftermarket automotive. “Produciamo ricambi per la carrozzeria in plastica di veicoli commerciali e industriali dal 1969” – esordisce Alessandro Pozzoli, responsabile di produzione e rappresentante della terza generazione della famiglia alla guida dell’azienda. “I primi prodotti realizzati erano paraurti in metallo. Successivamente l’attività si è convertita alla lavorazione di un materiale più malleabile come il poliuretano, anche se caratterizzato da un processo produttivo ancora complicato rispetto a quello attuale, che prevede lo stampaggio a iniezione del polipropilene”. Oggi l’azienda monzese offre un catalogo di ricambi molto ampio, che spazia dai paraurti ai cantonali, dalle griglie alle modanature, dalle calandre alle traverse, dai retrovisori ai parafanghi fino ai deflettori e alla fanaleria. “Abbiamo 6 linee produttive di diverse dimensioni che ci permettono di produrre dai componenti più piccoli di pochi cm fino ai paraurti da 2 m dei veicoli industriali”. Gli investimenti in nuove tecnologie produttive caratterizzano continuamente la storia di questa azienda, da sempre impegnata nel perseguimento della qualità della propria produzione e della sostenibilità ambientale. “Allo scopo di migliorare la gestione del flusso produttivo, l’ergonomia delle macchine, la qualità del prodotto finito e, non da ultimo, l’impatto ambientale delle nostre lavorazioni, da circa un anno stiamo collaborando con la società Lesta Srl di Dairago (Milano) specializzata nella progettazione e produzione di sistemi automatizzati per la verniciatura di plastica, metallo e legno e dei software di programmazione relativi”.
La gestione a ripristino delle scorte
In Poliplast l’intero ciclo produttivo si svolge internamente. “Il processo di sviluppo di un nuovo prodotto parte dal reverse engineering, che permette di riprodurre fedelmente la geometria 3D del campione tramite la scansione dello stesso. Il disegno
© ipcm
© ipcm
Per lo stampaggio dei suoi ricambi automotive, Poliplast utilizza stampi di peso variabile da 1000 kg a 30 ton.
Un dettaglio del reparto di stampaggio.
ottenuto sarà la base per la fase di progettazione dello stampo”. La gestione della produzione è organizzata settimanalmente. “Riordiniamo il magazzino sulla base degli ordinativi degli ultimi 2 mesi. È un settore complesso caratterizzato da una domanda altalenante che riusciamo a gestire grazie ad una costante ottimizzazione dei processi produttivi. Un aspetto imprescindibile del nostro settore è infatti la velocità di consegna e, di conseguenza, la rapidità nel ripristino delle scorte a magazzino, ottimizzato dal controllo in tempo reale dell’intero flusso produttivo, a partire dall’approvvigionamento della materia prima e dei componenti necessari alle lavorazioni dei nostri prodotti”. La struttura produttiva
Durante la fase di programmazione settimanale, l’obiettivo principale è quello organizzare la sequenza di produzione cercando di limitare il più possibile i tempi di setup tra una lavorazione e l’altra, così da riuscire a ripristinare le scorte con maggiore rapidità e flessibilità. Il reparto produttivo di Albiate è attrezzato con 4 presse ad iniezione di diverse dimensioni, con forza di chiusura corrispondente a 14.000, 18.000, 20.000 e 23.000 ton e in grado di supportare stampi di peso variabile da 1000 kg a 30 ton. “Per non compromettere l’efficacia dell’operazione di stampaggio –
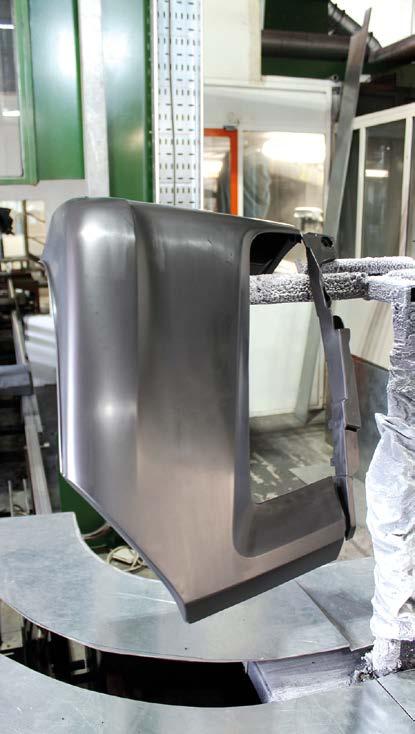
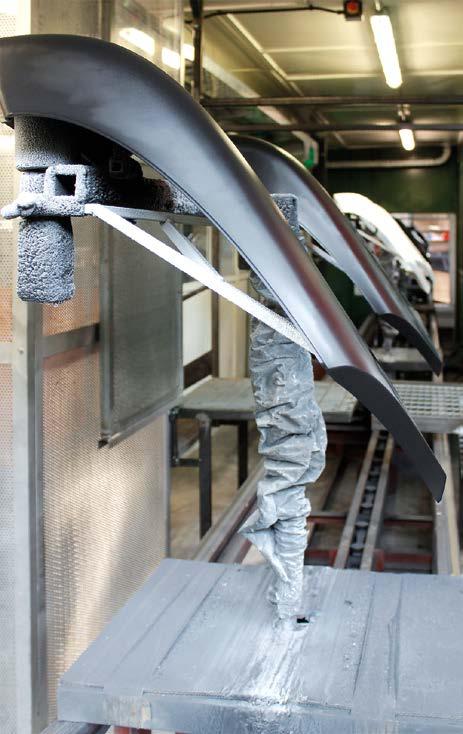


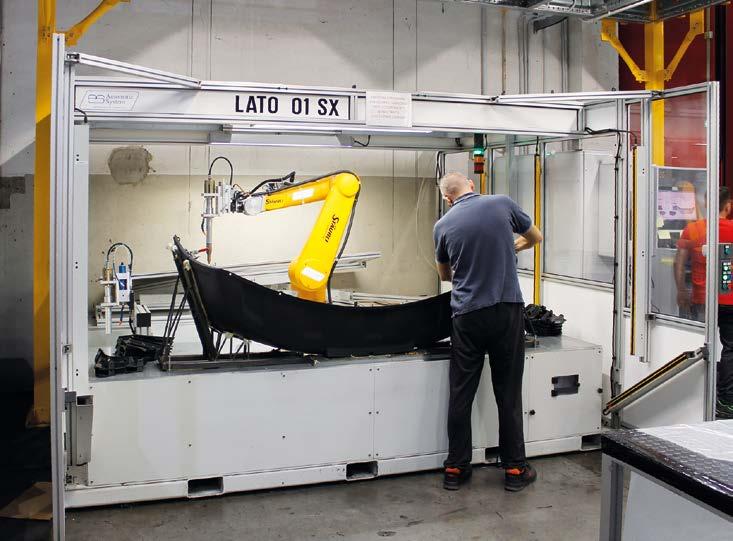
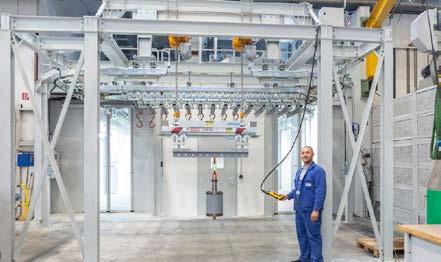
© ipcm
Da sinistra in alto in senso orario:
Un paraurti in plastica dopo la fase di stampaggio.
Il magazzino dei semilavorati.
L’assemblaggio a ultrasuoni nella stazione robotizzata.
© ipcm
Dettaglio del trasportatore rovesciato.
spiega Pozzoli – ciascuna macchina deve avere una forza di chiusura sufficiente a mantenere chiuso lo stampo per contrastare la pressione della plastica che si svilupperà al suo interno”. Dopo lo stampaggio, i pezzi che non devono subire ulteriori lavorazioni sono scaricati dalle macchine e inviati al magazzino. Nel caso in cui, invece, i componenti debbano essere inviati ai reparti di assemblaggio e verniciatura, questi sono stoccati nel magazzino dei semilavorati per poi essere prelevati successivamente. L’assemblaggio ad ultrasuoni dei componenti avviene in 3 stazioni, due manuali e una robotizzata. I particolari che dovranno essere verniciati, ove richiesto, sono prima mascherati per proteggere le aree che non devono essere verniciate, e poi caricati sul trasportatore rovesciato che li conduce alle 3 stazioni robotizzate - una per la flammatura e
© ipcm
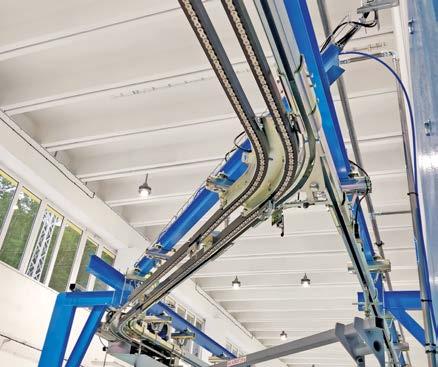

Un componente in attesa di entrare nella stazione di flammatura.
le altre due destinate alla verniciatura – e nel forno tradizionale ad aria calda per l’asciugatura. “In genere la flammatura e la verniciatura avvengono come ultima fase, per evitare di compromettere la qualità del rivestimento a causa delle continue movimentazioni, prima dell’imballaggio e dello stoccaggio finale” – prosegue Pozzoli.
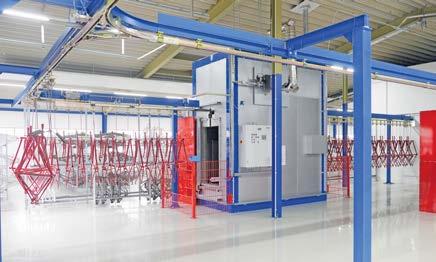
L’investimento nei robot ad auto-apprendimento Lesta
l robot di flammatura e verniciatura e la nuova centrale vernici rappresentano uno degli investimenti più recenti di Poliplast. “La scelta è stata motivata dalla necessità di sostituire i robot che avevamo in precedenza, ancora funzionanti ma ormai datati, con sistemi di ultima generazione in grado di semplificare il lavoro dei nostri operatori perché più leggeri e maneggevoli e, soprattutto, intuitivi”.
Abbiamo installato 3 robot della serie Lesta LEBOT MV A6, uno per la flammatura e gli altri 2 per la verniciatura” – interviene Luca Ghidoni, tecnico commerciale di Lesta. “Si tratta di robot antropomorfi a 6 assi in autoapprendimento con capacità al polso pari a 4 kg, ripetibilità di ± 3 mm e velocità massima pari a 1000 mm/s. Si tratta di dispositivi in grado di registrare in tempo reale i movimenti dei propri assi e di riprodurli in maniera automatica. Il braccio è realizzato in alluminio in modo da offrire una maggiore facilità di utilizzo grazie alle caratteristiche di leggerezza e robustezza di questo materiale. I suoi movimenti sono bilanciati da un sistema idraulico ad aria compressa che garantisce all’operatore la minore frizione possibile e restituisce un utilizzo fluido e non vincolato. La peculiarità di questo robot è la sua flessibilità e versatilità di collocazione nelle diverse stazioni operative e la sua possibilità di applicare vernici sia liquide, come in questo caso, sia in polvere sui materiali più diversi”. Programmare la fase applicativa in modo facile e intuitivo

Dopo la flammatura, la fase applicativa prevede l’applicazione di uno smalto, nella maggior parte dei casi bianco. Oltre al bianco, le altre tinte utilizzate sono il nero e sette diverse tipologie di grigi. “I 2 robot lavorano in contemporanea e verniciano lo stesso componente – precisa Pozzoli - perché trattandosi di articoli con superfici non uniformi avevamo la necessità di rivestire tutte le zone interne ed esterne del pezzo: per questo lo spindle del trasportatore fa ruotare il manufatto nel passaggio tra un robot e l’altro. Uno degli aspetti maggiormente apprezzati dai nostri operatori è la facilità di programmazione del sistema robotizzato: l’operatore afferra il joystick e segue i contorni del pezzo con il supporto di un altro operatore che gestisce la sequenza di movimento dal PLC di controllo. La semplicità dell’operazione è subito descritta: si avvia con il tasto “start”, l’operatore esegue il movimento che il robot dovrà ripetere e, quando si seleziona il tasto di “fine apprendimento”, il
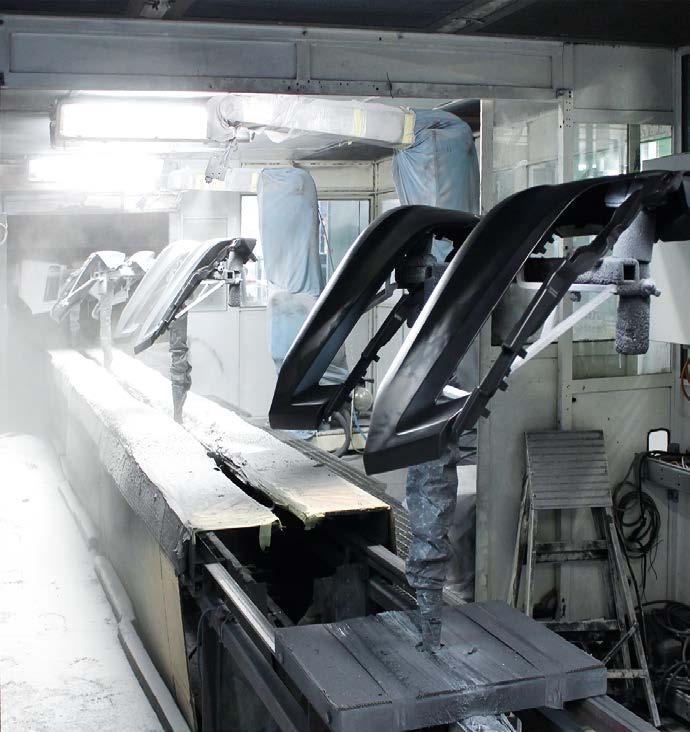
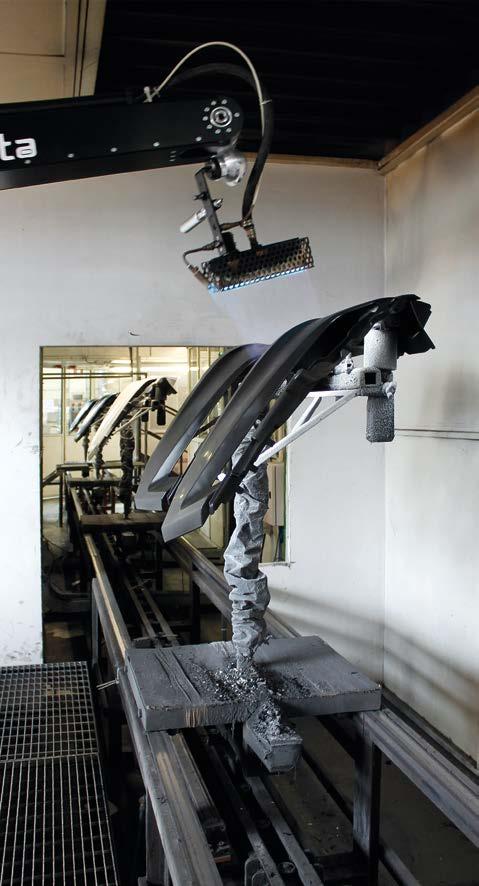
I robot Lesta durante l’applicazione dello smalto.
© ipcm
Il robot per la flammatura.
© ipcm © ipcm
Il componente in uscita dal forno di asciugatura.
programma viene automaticamente registrato e salvato. Resta poi solo da verificare se il programma così concepito è adeguato o se c’è qualcosa da modificare”.
L’ottimizzazione dei consumi in ottica sostenibile
La partnership con Lesta è stata motivata sia dalla necessità di sostituzione e aggiornamento delle macchine ormai datate sia in ottica ecosostenibile. “Poliplast – conclude Pozzoli – ha da tempo un post-combustore che riduce le emissioni in atmosfera al minimo, nel rispetto delle normative ambientali. Con l’introduzione della batteria di robot Lesta, è stato possibile ottimizzare al massimo il consumo di vernice, riducendo gli sprechi e, di conseguenza, l’attività del post-combustore. L’integrazione dei dispositivi Lesta migliorerà ulteriormente la nostra capacità di monitoraggio dei consumi e ci servirà anche per ottenere una valutazione più corretta delle tempistiche di lavorazione e dei costi operativi di verniciatura, in modo da poter programmare i nostri cicli produttivi con maggior sicurezza e precisione e gestire le scorte a magazzino in modo ancora più efficace”.
GLOBAL SOLUTIONS FOR WATER TREATMENT
with a complete service that includes system design manufacturing installation technical support chemicals
SPRAY BOOTHS WATER SLUDGE REMOVAL RESIN DEMINERALIZATION SYSTEMS REMEDIATION OF CONTAMINATED SITES BIOLOGICAL SYSTEMS BATCH TREATMENTS PHYSICAL-CHEMICAL SYSTEMS ADSORPTION FILTRATION REVERSE OSMOSIS MEMBRANE SYSTEMS EVAPORATORS BIOGAS BIOMASS SYSTEMS OIL SEPARATORS DESANDERS DESALINATION SYSTEMS PYROCHAR OTHER SYSTEMS CHEMICALS
INNOVATIONS: PRESENT&FUTURE
SPECIAL ISSUE ON ACE & OFF ROAD VEHICLES
VIANT – Una nuova e innovativa tecnologia per la protezione dalla corrosione
A cura di Chemetall,
Giussano, Italia cristiano.laurita@basf.com
Rivestimento di conversione e primer in una sola mano: VIANT è la nuova soluzione sviluppata dalla divisione Coatings di BASF per aumentare la qualità della verniciatura e ridurre l’impatto ambientale delle aziende che scelgono di integrarla nei propri processi produttivi. Può essere impiegata in vari settori, compreso quello di macchine agricole e da costruzione (ACE).
In una situazione economica altalenante, incerta e attualmente sfavorevole per l’industria manifatturiera in generale e per il settore dei trattamenti superficiali in particolare – poiché la verniciatura è una delle operazioni più energivore del sistema produttivo – trovare soluzioni in grado di ridurre i consumi energetici è fondamentale. Chemetall, un esperto di riferimento per il pretrattamento delle superfici metalliche, ha introdotto VIANT, un nuovo processo che combina rivestimento di conversione e primer in una sola mano per proteggere l’acciaio dalla corrosione in vari settori, come ad esempio l’agricoltura, l’edilizia e il movimento terra (ACE). Questa soluzione è facile da usare e fornisce un’affidabile protezione dalla corrosione per bordi e superfici interne. Non richiede alta tensione, apparecchiature speciali o una temperatura costante durante le fasi del processo di verniciatura. Al contrario, VIANT può accorciare il processo, permette di risparmiare risorse, e riduce i costi di gestione. Vediamo come.
Processo a risparmio energetico e sicuro per l’ambiente
La nuova tecnologia di verniciatura può offrire vantaggi decisivi: in cima alla lista ci sono il possibile risparmio sui costi di corrente elettrica e processi semplificati in varie aree, che possono essere ottenuti combinando pretrattamento e primer in un bagno di immersione in cui non è richiesto né il raffreddamento né il riscaldamento. Di conseguenza, nemmeno il controllo costante della temperatura del bagno è necessario. Il film può essere applicato direttamente sulla superficie dell’acciaio. Il film di liquido di rivestimento si forma grazie alla liberazione di ioni dalla superficie del metallo piuttosto che all’applicazione attiva dell’elettricità. Grazie all’ampio intervallo di temperature di esercizio e di una circolazione del bagno molto bassa, il processo è molto stabile ed è necessaria meno elettricità per alimentare le più piccole pompe di circolazione. Inoltre, è possibile disattivare la circolazione del bagno tra i turni senza danneggiare il prodotto chimica di rivestimento. Oltre al risparmio di elettricità, acqua e prodotti chimici, si può ridurre anche la quantità di acque reflue da trattare. Tutto ciò è possibile grazie all’assenza di una fase di conversione dedicata. Il processo VIANT è caratterizzato da un migliore equilibrio ambientale rispetto alle tecnologie convenzionali.
© Chemetall Utile a molti settori
Oltre che per l’industria ACE, dove il rivestimento di superfici interne con lo stesso spessore e lo stesso livello di protezione dell’esterno è un possibile vantaggio, VIANT può essere adatto a molti settori in cui i metalli devono essere protetti, come per esempio nelle seguenti industrie: produzione di elettrodomestici, componenti automobilistici, pezzi di

VIANT è il nuovo processo sviluppato da Chemetall: combina rivestimento di conversione e primer in un solo strato per la protezione dalla corrosione dell'acciaio in vari settori (foto di apertura). VIANT combina pretrattamento e verniciatura in un bagno a immersione dove il raffreddamento o il riscaldamento non sono richiesti, quindi anche controllo costante della temperatura del bagno non è più necessario.
