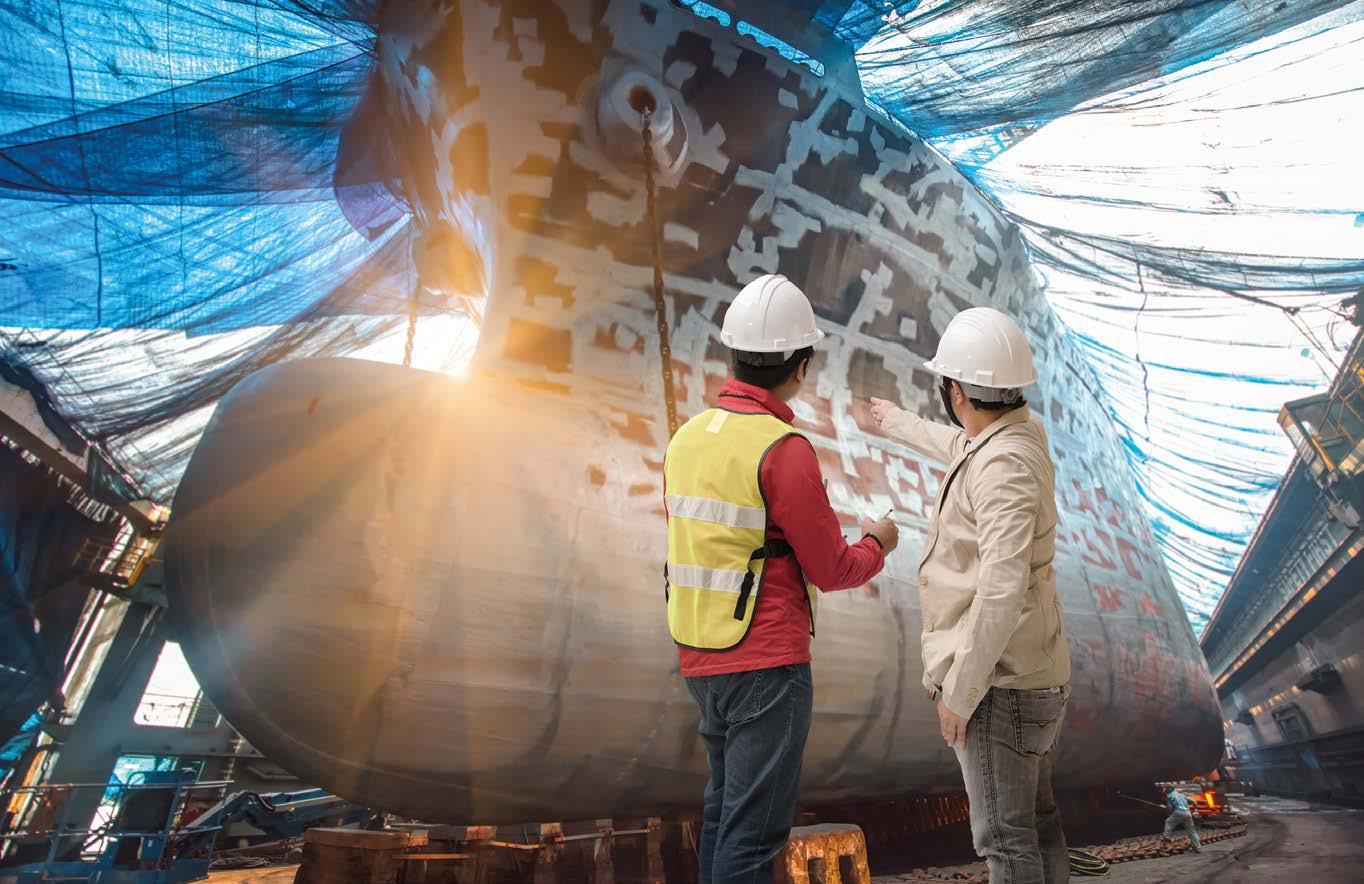
6 minute read
INSPECTION LOGBOOK
Massimo Cornago
NACE International Certified Coating Inspector, NACE CIP PEER Reviewer cornago@ipcm.it
Following the previous article, “Inspection of Steel Surface Preparation, Part 3”, we will now discuss other surface preparation systems and their related inspections to be carried out during the works themselves, analysing the abrasive blast cleaning process and its related inspection method based on the appropriate standards.
Analysis of blasting abrasives (SSPC AB-1)
The Inspector should verify that the blasting abrasive meets all requirements of the job specifications. This includes verifying that it is capable of providing the specified surface profile. The SSPC AB-1 standard defines the requirements for assessing both mineral and slag abrasives and it summarises the various tests that can be used to determine their general physical and chemical properties. These properties include: • Specific Gravity • Hardness • Weight change on ignition • Water soluble contaminants • Crystalline silica content • Oil content • Particle size distribution.
As fully described in the standard, the blasting abrasive should be tested for water-soluble ionic contamination, in compliance with ASTM D 4940 (standard test method for conductimetric analysis of water-soluble ionic contamination of blast cleaning abrasives). In this test, a slurry is made with abrasive particles and pure water and then filtered; the filtrate is tested for acid/basic contaminants and soluble salts (checking its pH and conductivity, respectively). The acceptable pH value is between 5 and 8. After settling and before filtration, the liquid should also be inspected visually for oil and dirty or fines. The test is usually conducted periodically at the discretion of the Inspector. It is good practice to retain a small sample from each batch of abrasive.
Inspection of abrasive blasting equipment
The inspection focusses on three main important aspects: “Hoses, coupling, and nozzles”, “Oil or water in compressed air (ASTM D 4285)”, and “Verification of blasting pressure”.
Hoses, coupling, and nozzles The Inspector should check blasting hoses, couplings, and nozzles for deterioration and verify that blast hoses have safety wires. Hoses should be as short a length and as large a diameter as practical to minimise loss of blasting pressure, internal friction, or particular restriction. To increase productivity, blast nozzles should be replaced when their throat diameters are eroded to the next larger size.
Testing for oil or water in compressed air (ASTM D 4285) Oil and water in the compressed air may affect the degree of cleanliness of the coating. The Inspector should check to ensure that water traps and dryers for air compressors are present and operational. The Inspector should use the “blotter test”, in compliance with ASTM D 4285, to determine the presence of oil or water contamination of compressed air used for abrasive blast cleaning. Blotter testing is normally conducted daily, after the compressor has reached the operative temperature. Any indication of oil discoloration and water contamination on the collector is cause for rejection of the compressed air. The normal procedure is summarised as follows: • Place a white blotter, or another similar absorbent material (such as filter paper) on a rigid backing within 610 mm (24 inches) of the air discharge point centred in the air stream of a blast equipment.
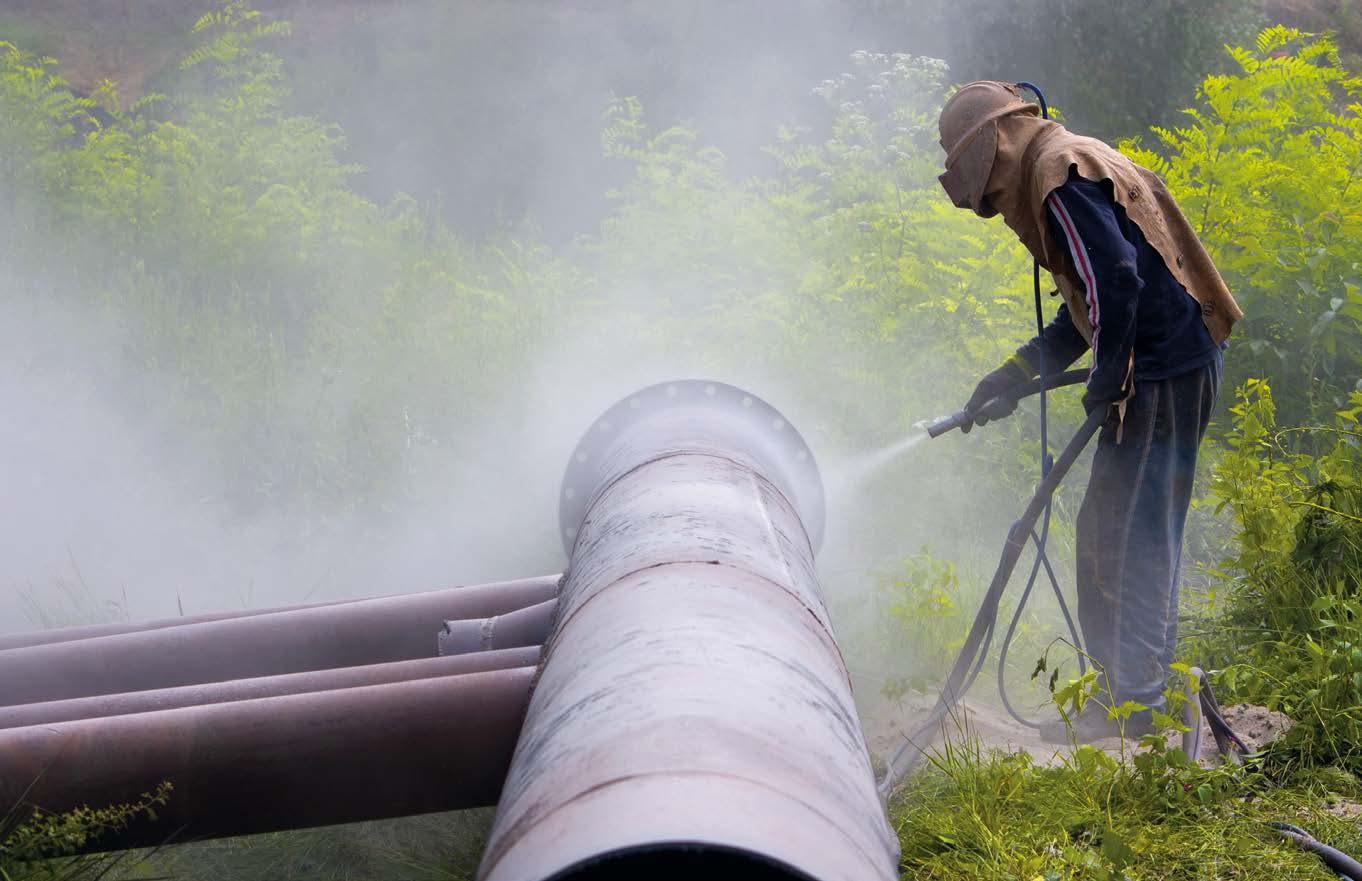
• Allow the air stream to impact onto the collector for a minimum time of 1 minute. • Visually examine the collector for the presence of oil or moisture. Any indication of either is sufficient cause for rejection of the compressed air stream. To avoid false indications, the Inspector should do as follows: - Allow compressed air to reach operating conditions before testing. - Fasten the collector material to a rigid backing and avoid personal contact with the air stream. - Locate the collector as close to the use point of the air stream as possible and downstream of the in-line oil and water separators.
Verification of blasting pressure Any change in the blasting pressure may affect the depth of the anchor pattern. Whenever a change in blasting pressure is suspected, the Inspector should measure the internal blast hose pressure at the nozzle. The test is conducted with an air pressure gauge attached to a hypodermic needle, inserted through the blast nozzle just below the reading dial. The gauge can also be used to determine any pressure drops in air hoses. The normal procedure can be summarised as follow: • Start up the blast cleaning equipment, so that all blast nozzles are operational. • Insert the gauge needle through the blast hose as close to the nozzle as possible and slanted toward it at a 45 degrees angle to minimise needle damage or clogging. • Read the blast cleaning air pressure directly from the gauge dial. • Repeat the test periodically, as required by the project specifications or any time new events occur that could change the pressure value.
Testing for surface cleanliness
The Inspector should verify that the specified kevel of surface cleanliness is attained. SSPC (Society for Protective Coatings) and NACE International (National Association of Corrosion Engineers) have developed joint written standards that are used to verify the degree of surface cleanliness by abrasive blast cleaning methods. Incidentally, SSPC and NACE International have recently merged to create AMPP, the Association for Materials Protection and Performance. These standards, i.e. NACE1/SSPC-SP5, NACE2/SSPC-SP10, NACE3/SSPCSP6, and NACE4/SSPC-SP7, are descriptions of the various degrees of surface cleanliness. We will analyse these standards in detail in our next article, “Inspection of Steel Surface Preparation, Part 5”. In addition, SSPC has developed visual standards called SSPC-Vis1, a book containing colour prints illustrating the various degrees of abrasive blast cleaning over various rust grades of structural steel. It is intended to supplement the written description.
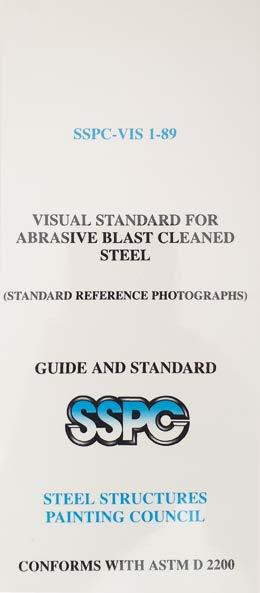

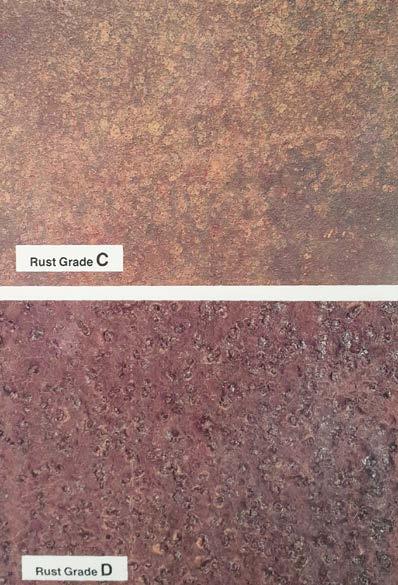
The SSPC-Vis1 book contains colour prints illustrating the various degrees of abrasive blast cleaning over various rust grades of structural steel.
While published visual standards have proven to be extremely helpful, it is rare that the appearance of the surface condition exactly matches those in the standards. As an alternative to using published visual standards to verify the degree of surface cleanliness, a section of the structure may be selected and cleaned in the presence of a blaster and the Inspector. The cleanliness is then discussed and agreed upon and the field standard preserved as a reference. This is referred to as a jobsite standard.
SSPC-Vis1 The visual standard (it includes sets of standard photographs illustrating the four levels of blast cleaned steel), is used to assist in determining if blast cleaned steel surfaces meet the written cleanliness standard. The procedure is as follows: • Determine the initial condition, or grade, of the steel to be cleaned by comparing it to the four photos representing different conditions: - Rust Grade A: steel surface completely covered with adherent mill scale, little or no visible rust. - Rust Grade B: steel surface covered with both mill scale and rust. - Rust Grade C: steel surface completely covered with rust, little or no pitting visible. - Rust Grade D: steel surface completely covered with rust, pitting visible.
• Immediately prior to painting, turn to the section of SSPC-Vis 1 representing the rust grade level determined in Step 1 and select the photo that represents the specified level of cleaning: - SSPC-SP7 Brush-off blast cleaning - SSPC-SP6 Commercial blast cleaning - SSPC-SP10 Near-white blast cleaning - SSPC-SP5 White metal blast cleaning.
Thus, if a Rust Grade B steel is to be cleaned to SSPC-SP10, use the photo designated “B-P10” and visually compare it to the cleaned steel to help determine whether it meets the written standard. Note that variations from the photo may occur in texture, shade, colour, tone, the amount of mill scale or pitting, or the abrasive used.
In the next article, we will discuss other standards. ‹

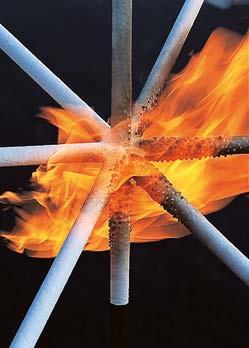
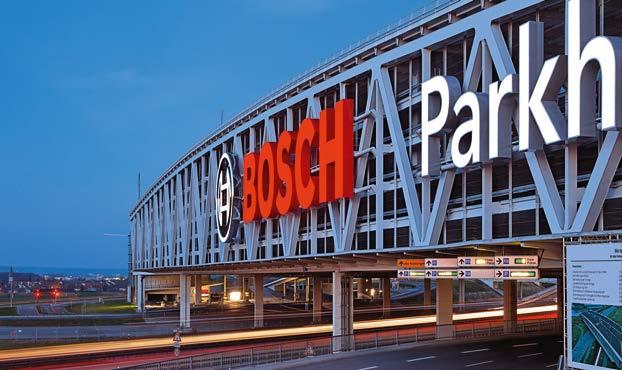