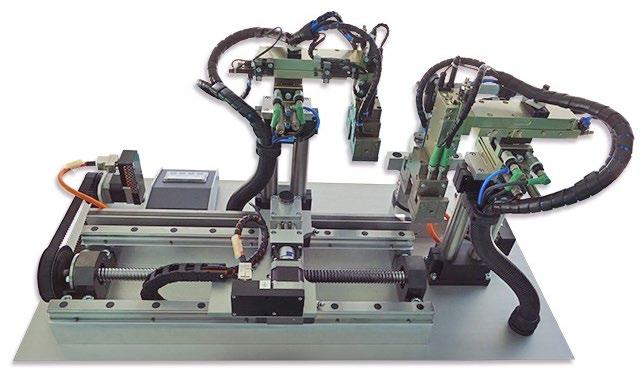
5 minute read
Link by link: The benefits of seeing the full chain
LINK BY LINK: THE BENEFITS OF SEEING THE FULL CHAIN
Design engineering and industrial automation need to work hand in hand to maximise efficiency and reliability – and decisions regarding pulleys, chains and sprockets are critical to making this happen. Here, Marcus Schneck, CEO of norelem, looks at why seeing the full chain around these products is invaluable…
Engineering relies on cause and effect. A chain of action and reaction, where desired aims lead directly to desired outcomes. In this chain, every link is crucial – every link needs to play its part, which is why decisions about tensioning solutions, pulleys, sprockets and roller chains are so vital.
These are standard components: products within belt or chain drives that most engineers would be forgiven for paying little attention to. However, even the smallest solution plays a big role, from the reliability and efficiency of these drives to simplifying and speeding up industrial automation. Because even the simplest sprocket is one link in a wider chain of cause and effect that delivers productivity and potential. So, let’s begin by looking at the core links in this chain.
Getting it right: Components and considerations
For every chain drive or belt, it’s important to get the basics right. Which means designing custom tensioning solutions that are right for each specific application, with particular consideration given to seemingly the simplest components – such as sprockets and tensioning pulleys.
These components within chain-driven machinery are subjected to extremes of temperature, friction, vibration and corrosion, all of which can hamper performance and long-term reliability. So, it’s critical when designing this machinery to factor in the forces and environments surrounding them. Making the right decision on the sizes, types and forms of tensioning solutions can be the key to minimising vibration and extending equipment lifespan and productivity.
Tensioning devices from norelem, for example, comprise chain tensioners, sprocket sets and tension pulleys that can be adapted for individual needs. Built around a clamping element, each unit provides cushioning, support, tensioning and dampening through multifunctional spring bodies composed of highly elastic and dimensionally stable natural rubber. This effectively safeguards against tearoff and the need for maintenance, while delivering high chemical resistance – a ready-to-install solution with long-term benefits, thanks to customisability and multi-component thinking.
For heavier-duty chain drives, even stronger solutions are required – such as duplex or triplex roller chains and steel sprockets. These are commonly used to drive heavyweight equipment in challenging applications, such as packaging, materials handling or agriculture, delivering power transmission under uniform, non-uniform or impulse conditions.
Whether it’s pulley systems or chains, we need to retain this focus on power transmission, without slippage or failure. When designing a solution, this should remain at the forefront, as well as the need to mitigate the risk of corrosion or wear. The smoother a chain drive’s operation, after all, the more efficient it remains now and in the long term.
Linking it together: Ancillaries and support
Designing an effective, efficient chain drive solution goes beyond thinking about sprockets, pulleys and chains. We need to factor in the ancillary products and support that link everything together.
Firstly, in choosing ancillary products, it’s important to look at the bigger picture of your chain drive solution: its operational requirements and loads, its environment, and longer-term plans for expansion or adaptation. Answering these will lead to more intelligent and effective choices for the standard components that will complete your solution.
Again, there’s a wide range of these available in THE BIg gREEN BOOK from norelem, from toothed belts and stepper motors to tension levers, roller elements and guide rails. Making the most of this, however, depends on our second consideration: support.
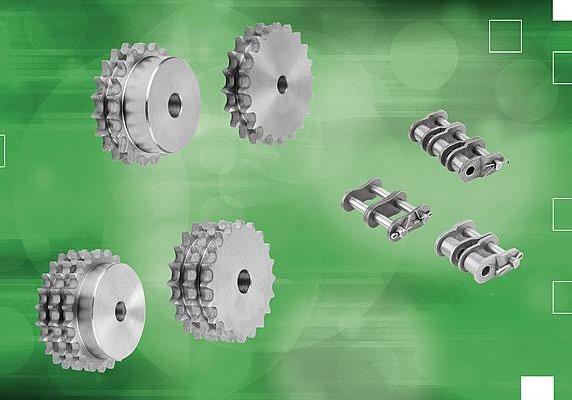
This means having access to accurate CAD information, drawings and product datasheets – data which should be core to any design solution. Minimising time, cost and wastage also means securing rapid access to components, efficient delivery and clear communication. All things that, from experience, we at norelem know are integral to the success of any project – to keep the chain moving.
Setting it in motion: Simplifying industrial automation
Keeping projects and equipment moving is one thing – but considering the full chain of components and support in design solutions has another, potentially more impactful, benefit: streamlining and speeding up industrial automation.
Automated production lines are the gold standard of efficiency and cost savings but adopting them can be daunting. Yet it doesn’t need to be. As the global workforce begins to embrace automation, with 72% of workers viewing it as a technology that can actively help them do their jobs better, there’s a clear opportunity to make adoption easier.
Take, for example, a pick-and-place machine. These machines work using a combination of motors, linear and rotary guides and positioning units, and a measuring unit and handling system. They can all be created, quickly and flexibly, using standard components – controlled through a stepper motor, a combination of toothed belt drive and ball screw drive can convey components horizontally, while the addition of an electrical positioning table can feed components across the vertical axis. Pneumatic handling modules fitted with parallel gripper and rotary modules can be used to pick up and pass components, while position indicators and magnetic strips and sensors ensure precision measurement.
The key to this example is the speed and simplicity of creating automated machinery using readily available and quick-to-source standard components, made possible by the use of detailed CAD data to aid in design and manufacture. given the typical lead time of a traditional pick-and-place machine is up to three months, designing, installing and commissioning these systems can cut that time to as little as two to four weeks.
Considering the full chain of tension solutions, from pulleys and belts to sprocket sets and steel chains, while also considering the requirements and operating conditions of those solutions, is a major way to design in efficiency and reliability. Working link by link, taking a logical approach at the outset, can cut lead times and deliver immediate and long-term benefits. A clear example of cause and effect.
To learn more about norelem and its range of over 60,000 components, and order your copy of THE BIg gREEN BOOK, visit www.norelem.co.uk
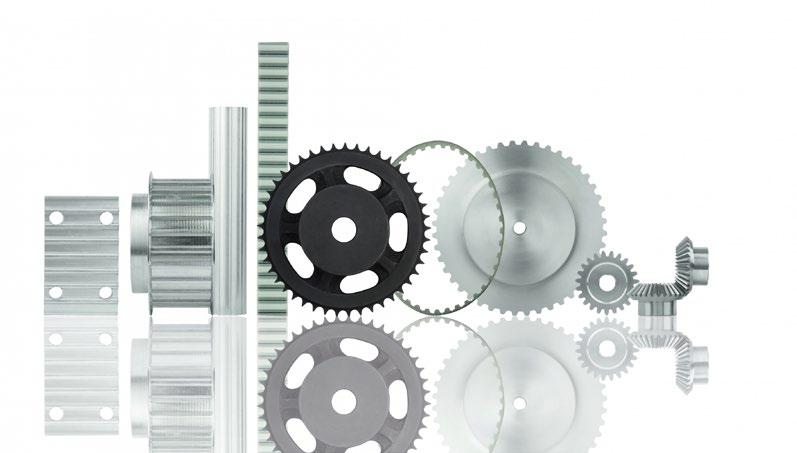