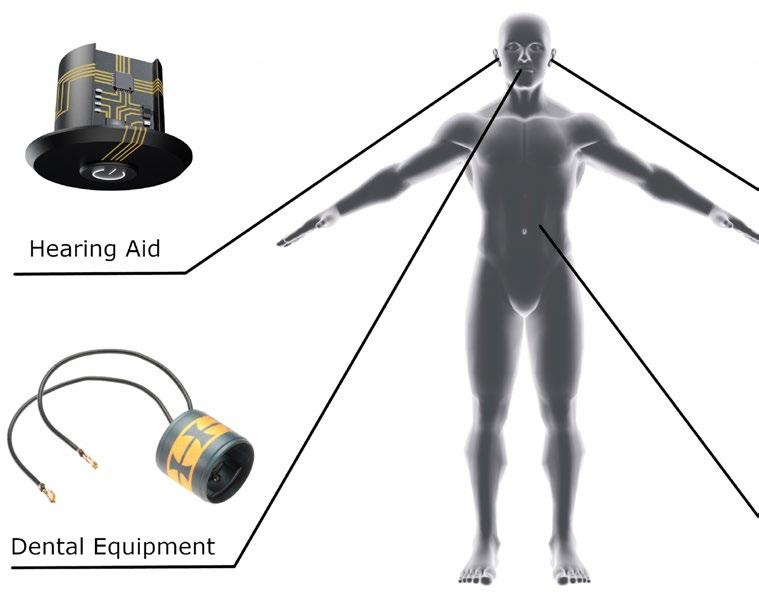
6 minute read
3D-MID – MINIMIZED SENSING HIGH-TECH WITHIN THE PATIENT
When it comes to miniaturization, the ideal partner is the leading 3D-MID supplier HARTING. The company is located in the innovative heart of the Swiss watch industry in Biel, which is also a growing hub for medical device technologies. This location was chosen with care, because in this region people have grown up in a world of micromechanics - generation after generation.
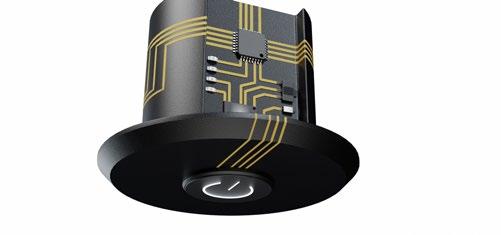

Japanese corporation Yaskawa coined the term “mechatronics” in 1969 by combining “mechanical” and “electronics”. since then, steady developments in technology—notably at drives systems and wireless connectivity—have significantly expanded its usage.
today, medical devices are a major focus of mechatronics. one of its breakthrough innovations are Mechatronic integrated Devices (3D-MiD). it’s a technology that allows higher density integration of electronic components into the smallest possible space.
3D-MiD or 3D-circuits, has the potential to transform medical industry as we know it. as medical devices such as hearing aids and dental instruments become smaller and smaller, the manufacture of their most important elements - traditionally printed circuit boards (PcB’s with wires and other electrical parts) require much more delicacy and precision.
High-end miniaturization is facilitated by 3D-circuits: a fantastic combination of mechanical and electronic integration.
this article breaks down everything you need to know about 3D-MiD technology, its many benefits, and its applications in the medical device industry.
All About 3D-MID Technology
HartinG’s 3D-circuits technology makes it possible to combine mechanical and electronic functions into a single component to fit into the smallest spaces.
the electronic circuit can be built into the device itself, making it more compact and functionally dense. By using injectionmolded circuit boards, the number of process steps, assembly times, and parts can all be drastically cut down.
3D-MiD technology has become incredibly useful in many industries, especially so in the world of medical devices, where it drives miniaturization.
How 3D-MID Technology works
Device designers can go above and beyond the limits of traditional manufacturing with the help of 3D-circuits. the sky’s the limit when electrical and mechanical functions can be unified in a single threedimensional component.
these components are constructed using very malleable bits of plastic through injection molding. this process makes it possible to create anything with precise measurements according to the requirements laid down by final customer usage.
injection molding is perfect for mass production of products with complex geometries and in miniature sizes, such as the components of high-end medical devices. a process called laser direct structuring (lDs), developed by lPKF laser & Electronics in 1996, can then draw the needed electrical trace layout to these components, which will be made conductive in a subsequent chemical plating process. as HartinG unifies all these process steps under one roof, customers benefit from quality “Made in switzerland”.
By integrating functions and the three-dimensional routing of circuit tracks, the design space for the electronics of hearing aids can be optimally utilised.

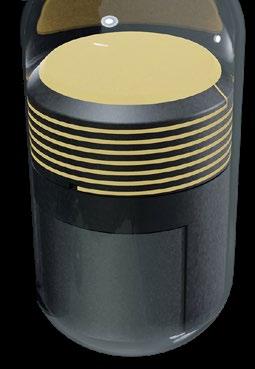
This is a substitution for an endoscope. You basically swallow it like a pill which makes way more comfortable than an endoscope.
With 3D-MiD technology, there are virtually no limitations for designers. this opens up a world of possibilities and potentially huge savings for manufacturers and consumers alike. By combining mechanical and electrical hardware, the design and creation of electronic devices with very complex functions become easier and much more affordable.
Because of its adaptability, mechatronics can be used in an ever-expanding variety of medical applications, ranging from bed positioning systems to robotic surgical equipment.
3D-MID Technology in the Medical Field
in the last few years, 3D printing has accelerated many advancements in the world of medicine, with millions of people benefiting from components and devices created with ease. and now, 3D-MiD is poised to change the face of medicine forever. this technology takes all these advancements one giant step further by using mechatronics to create devices with an even wider range of electronic functions that fit in the smallest of spaces.
Mechatronics allows for the extreme downsizing or miniaturizing of medical applications, enabling examination, sensing, and monitoring from within the patient. With such technology, medical devices can be designed to be much less invasive, leading to a significant improvement in patient care. With its many years of experience - HartinG started its activities in this field in 2003 – the team is familiar with the requirements of the medical market. the numerous series production projects confirm this. taking large medical machines and devices and putting them into a more compact package is a big part of what 3D-circuits brings to the table. it offers significant improvements to changing how medical devices are used today.
one of the most important benefits of this technology is that it makes these advances possible without sacrificing quality. You may think that shrinking a medical device down would make it less powerful or effective, but with 3D-MiD, that isn’t the case at all.

HARTING has realised a microphone carrier in 3D-MID design that precisely aligns the microphones of the hearing aid and at the same time integrates the electrical contact. By implementing a 3D-MID ring switch in the dental instrument, HARTING was able to significantly improve the ergonomics and weight of the instrument while simultaneously reducing the assembly effort.

in fact, as 3D-circuits continues to grow in popularity, it will only get better, opening up new options for even smaller and more effective medical devices, from hearing aids and implants to surgical and dental instruments.
The Benefits and Uses of 3D-MID Technology
Miniaturization is one of the most critical trends in healthcare that affects how mechatronics technology is used. the development of ever-smaller instruments, devices, and equipment enables less invasive treatment methods, allowing faster recovery times and muchimproved patient care.
these micro actuators and miniature sensors also propel the development of small mechatronics systems for the following applications:
• Handheld diagnostics for use at the point of care, including ultrasound and blood testing
• scientific instruments for flow cytometry, Dna identification, pathogen detection, and Dna sequencing
• Medical imaging using small, precise modules for lens control and laser tuning • implantable devices that can be dynamically adjusted in-place
• Mobile miniature robots
• Micropumps and auto-injectors for drug delivery products
there has also been a shift toward placing a greater emphasis on the convenience and aesthetics of medical technology as well as the level of comfort experienced by a patient. this is because more treatments are shifting from hospitals to outpatient settings, and today’s discerning customers now expect a more positive experience as a patient.
redesign efforts for medical equipment aim to make them easier and more convenient for patients to use and manage in the long run.
Even conventional hydraulics are being phased out and replaced with mechatronics as the method of choice for controlling motion. Mechatronics systems are much simpler to operate, create less noise, weigh less, and are more compact. some of the value-added benefits that medical organizations can gain from using mechatronics in place of more conventional manufacturing methods:
• the miniaturization of medical devices • Development of low-cost disposable gadgets, which has become a pressing requirement • Device portability • High levels of accuracy and precision • improved performance in all aspects • Design freedom • Weight reduction • simplification of products
Conclusion
the most important developments in mechatronics lead to new technologies that will shape the healthcare of the future so that devices are safer, more portable, and, most importantly, painless. HartinG’s 3D-circuits technology is changing how medical devices are made, especially complex equipment with integrated electronics that must fit into increasingly miniscule spaces.