
7 minute read
PLANT DOCUMENTATION 4.0 – AN ESSENTIAL ENABLER FOR INDUSTRY 4.0
Specialist articles on Industry 4.0 generally emphasize the aspect of technical feasibility of the consistent, intelligent networking of machines, processes and personnel: What gateways, protocols and platforms will be needed to interlink machines from different manufacturers? What legal requirements have to be observed? How can security be designed to avoid hacker attacks?
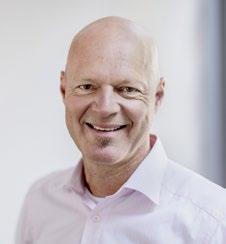
We are living in a time of perpetual change. This is also reflected in industrial production. Manufacturing processes are continually adapted and optimized; products are increasingly being individually manufactured. This is not new, because in the past, too, production plants were in a state of perpetual change: failed components were replaced, software patches and updates were installed, process optimization programs were developed, and much more. Nevertheless, this trend is gaining speed and processes are becoming more dynamic.
Fig: 3 - LiveDOK makes distributed documentation of large-scale plants digitally available to engineers and plant operators: all relevant documents and drawings are presented in a structured way on one unified, intuitive user interface – regardless of their format and medium. Plant data can be administered, searched and corrected in real time – from planning to operation, anytime, anywhere. (Copyright: Rösberg)
Christian Stolz, Account Manager Plant Solutions at RÖSBERG Engineering: “As well as maintenance, many other areas benefit from digital documentation: troubleshooting, large-scale revisions, project-related documentation, loop checks and the management of assets, the integration of package units, and know-how transfer. And when it comes to audits, it certainly pays off to have up-to-date, legally compliant documentation to hand.” (Copyright: Rösberg)
ProDOK is the I&C-CAE system for the planning and operational support of process control equipment in process plants. ProDOK enables rational, consistent project planning and consistent documentation, ensuring an integrated planning process that follows unified rules. (Copyright: Rösberg)
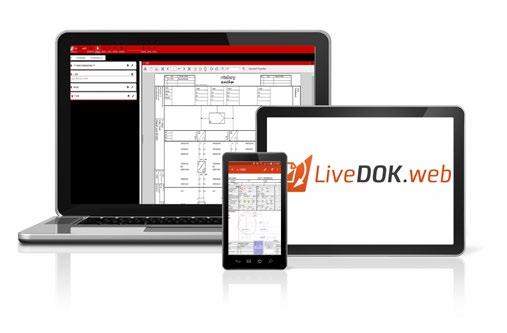
Reliable documentation of as-built status
As-built documentation – meaning documentation that reflects the actual state of a new plant – has always been required for commissioning, but in fact the time and resources involved in preparing the relevant documents is always immense. And controlling the delivered documents, to make sure they really do tally with plant reality, is always very time-consuming – thus quality control process is generally confined to some random checks. Thus often enough, plant documentation does not even correspond to plant reality at the start – and even if it does correspond initially, the task of keeping the status of this documentation up to date is anything but trivial. The bigger and more complex the plant, the greater this challenge appears. It may even sound a little schizophrenic to be talking about digital twins on the one hand, whereas in many places a daily struggle is still going on to master plant documentation with the aid of paper documents, excel lists and complex file structures. However, this is exactly where Plant Documentation 4.0 can make a vital contribution, especially if a system is also able to simplify the management of changes.
Current status of all built-in components – and much more
In sectors such as petrochemicals, chemicals, logistics, manufacturing, in power plants, plant construction or the pharmaceutical industry, production processes are generally complex, and plants often assume gigantic proportions. Thus these sectors of industry have had to rely on digital documentation for a long time now to keep track of the asbuilt status of their plants and manage the relevant interrelated processes. So it is not surprising that a company like Rösberg e ngineering from Karlsruhe – already active in these sectors for decades – developed digital solutions many years ago in order to keep an overview of the flood of information in these types of plants. Christian Stolz, Account Manager Plant Solutions at RÖSBeRg engineering comments: “With our I&C-CAe system ProDOK we primarily document the planning and construction of plants. However, it is also important to know the current status and components built in during the operational phase. Our software tool LiveDOK (Fig. 3) helps with the administration and documentation of changes. A main focus of the tool is on simply find documentation updates and enabling the changes to be made available to everyone quickly and easily.”
Various use cases benefit from Plant Documentation 4.0
When envisaging Plant Documentation
4.0 probably the first aspect to be considered is the advantages for maintenance. Here, of course, it is extremely useful to know the current state of the plant and be able to easily document the changes. “To do this, maintenance crews can simply enter the change on a tablet with a stylus (Fig. 4), and it is saved together with the information about who made the change, when, and explanation if necessary”, says Stolz. “Workflows built into the system then ensure that the original documentation is reviewed regularly and thus stays clear and up-to-date.”
In addition to maintenance, many other areas benefit from digital documentation (Fig. 5). These include e.g., troubleshooting, large-scale revisions, project-related documentation, loop checks and the management of assets, the integration of package units, and know-how transfer. And when it comes to audits, it certainly pays off to have upto-date, legally compliant documentation at hand at all times.
Troubleshooting, large-scale revisions and loop checks
When something goes wrong, every minute counts. In a situation of this kind valuable time is lost if the current documentation status of the plant first has to be assembled – in the worst case, inability to react fast enough may result in damage or danger to people and the environment. In large-scale revisions, too, time is usually tight. Numerous employees need to be coordinated and very many changes made to the documentation simultaneously. This makes it all the more important to ensure that everyone involved in the process has access to the current documentation at all times. Similarly, loop checks also involve the coordination of large numbers of employees and the structured execution of various tasks.
Managing assets and package units
Digital documentation is also beneficial for effective asset management –for instance, when a manufacturer discontinues an asset, making it necessary to know how many of the relevant components are built into the plant and where; or when compiling an overview of components that will no longer receive support in the near future. Only a company managing its assets effectively can keep production running reliably. Another aspect that necessitates digital documentation is the trend in the process industry towards integrating Package Units, meaning the distribution of large plants into smaller units. This raises the question of how the documentation that is delivered together with a functional unit can most easily be transferred into the already-existing plant documentation.
Project-related documentation and know-how transfer
When engaging in extensive plant retrofit or extensions, or for inspection purposes, many project-related documents also have to be immediately available as and when required. If these documents only exist in paper form, or are only available from different sources and in assorted file formats, compiling them is effort-intensive and not overly efficient. Another advantage of consistent digital documentation is that know-how can be preserved, because the knowledge no longer exists solely in the minds of experienced employees. This substantially facilitates knowledge transfer to new employees.
“In all these and many other use cases, LiveDOK has been proving its worth for decades now” Stolz says, and adds: “With digitalization the focus was on the PC, but with Industry 4.0 the focus is on the Internet. This also applies, so to speak, to Plant Documentation 4.0. We have been creating digital documentation for a long time now, but we have consistently developed our concepts further, for instance regarding cloud enablement, in order to stay with the pulse of the times. Thus our customers get a tried and tested product that uses today’s state-of-the-art technologies to fulfill the technical and legal requirements of tomorrow.” In the use cases described above, the documentation tool enables documents to be found fast, provides a realistic overview of the components built into the plant while helping to keep documentation up-to-date, ensures standardization in documentation in line with current legal requirements, gives all disciplines involved in a project access to the documentation without media discontinuity, and ensures that everyone in the team is working with the same documents. https://livedok.roesberg.com/ https://prodok.roesberg.com/ https://roesberg.com/
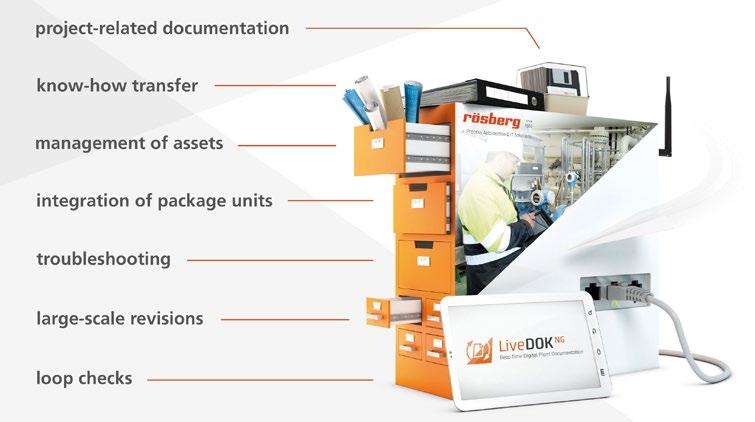
Getting started is easier than you think Companies who wish to consistently implement Industry 4.0 cannot do so without digital, cloud capable plant documentation, especially where large plants are concerned. Nevertheless, many companies are still put off by the initial effort and expense of digitalizing their documentation at all in the first place. Here the process automation experts can reassure them – numerous projects carried out in the past have shown that getting started is much easier than users generally fear. “And not only that – very often digitalization opens up many optimization opportunities, so the effort pays off much faster than many people think”, says Stolz, speaking from his own experience.
PEPPERL+FUCHS IS EXPANDING ITS IO-LINK PORTFOLIO WITH A UHF RFID READER
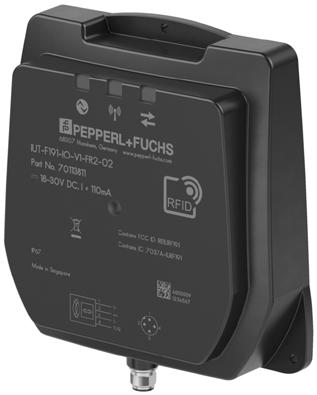
With the IUT-F191-IO-V1, Pepperl+Fuchs is filling a gap in its portfolio and enabling customers to easily access UHF RFID.
In recent years, IO-Link has become a well-established interface on the market and its use is increasingly widespread. One reason for its popularity is the standardized interface, which enables customers to integrate a number of different sensors easily and in a uniform way. Additional advantages of IO-Link include quick installation and easy replacement in the field. The existing HF RFID portfolio (13.56 MHz) for IO-Link is now being expanded to include a UHF reader.
The IUT-F191-IO-V1 fills the gap between HF and RFID and the UHF systems already available from Pepperl+Fuchs. The IUT-F191-IO-V1 is used in situations where the detection range of HF systems is no longer sufficient or where customers prefer a UHF solution for other reasons, for example because a UHF solution is already in use and should be used consistently. In many applications, read/write distances of approx. 1 m are completely sufficient. Furthermore, the IO-Link interface enables easy, costeffective integration into any existing IO-Link networks, quick commissioning, and interchangeability. The easy Mode - already familiar from the well-known HF RFID read/write devices with IO-Link - reduces the programming effort for the user and enables easy access to UHF RFID applications. In expert Mode, advanced setting options are also available.
Applications include intralogistics, for example, where materials provided to machines need to be identified before further processing to avoid errors and therefore disruptions to the production process, and products must have continuous traceability throughout the entire manufacturing process.
Potential applications also include on conveyor lines or automated storage systems, where IO-Link is often already used to connect further sensor technology and components.
www.pepperl-fuchs.com