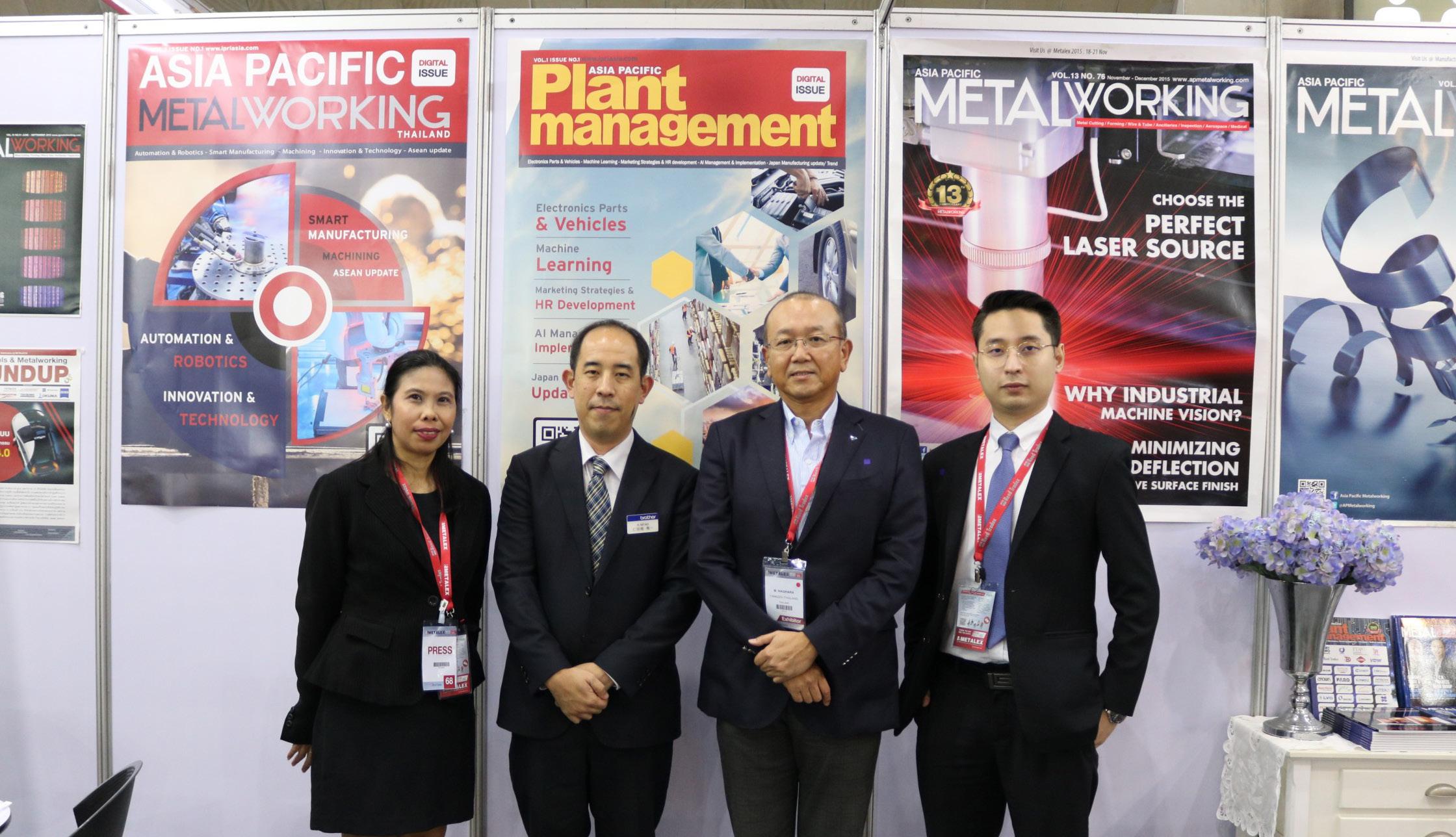
6 minute read
ExEcutivE talk
ExEcutivE talk intErviEw BY suratHan parapornpisut
Second from the left, Ryoichi Roy Nitao, General Manager, Brother Commercial Thailand In the middle, Masashi Hagihara, President, Asean Regional Headquarters Yamazen Thailand
Advertisement
BROTHER THAILAND & YAMAZEN TALK WITH APM ON TRENDS AT METALEX 2020
The Covid-19 pandemic has had a significant effect on the events industry in Thailand. At the same time, it has given the country an opportunity to innovate. Metalex 2020, the leading Machine Tools & Metalworking Exhibition in ASEAN, and the first hybrid meeting solution for an industry exhibition in Thailand that opened 18 November, offered a blend of offline and online activities. The show presented several booths featuring latest innovative technologies in machine tools and metalworking. For this edition of Asia Pacific Plant Management, PM has held exclusive interviews with Metalex 2020 exhibitors to gain an insight into the latest trends that are to shape the industry in 2021.
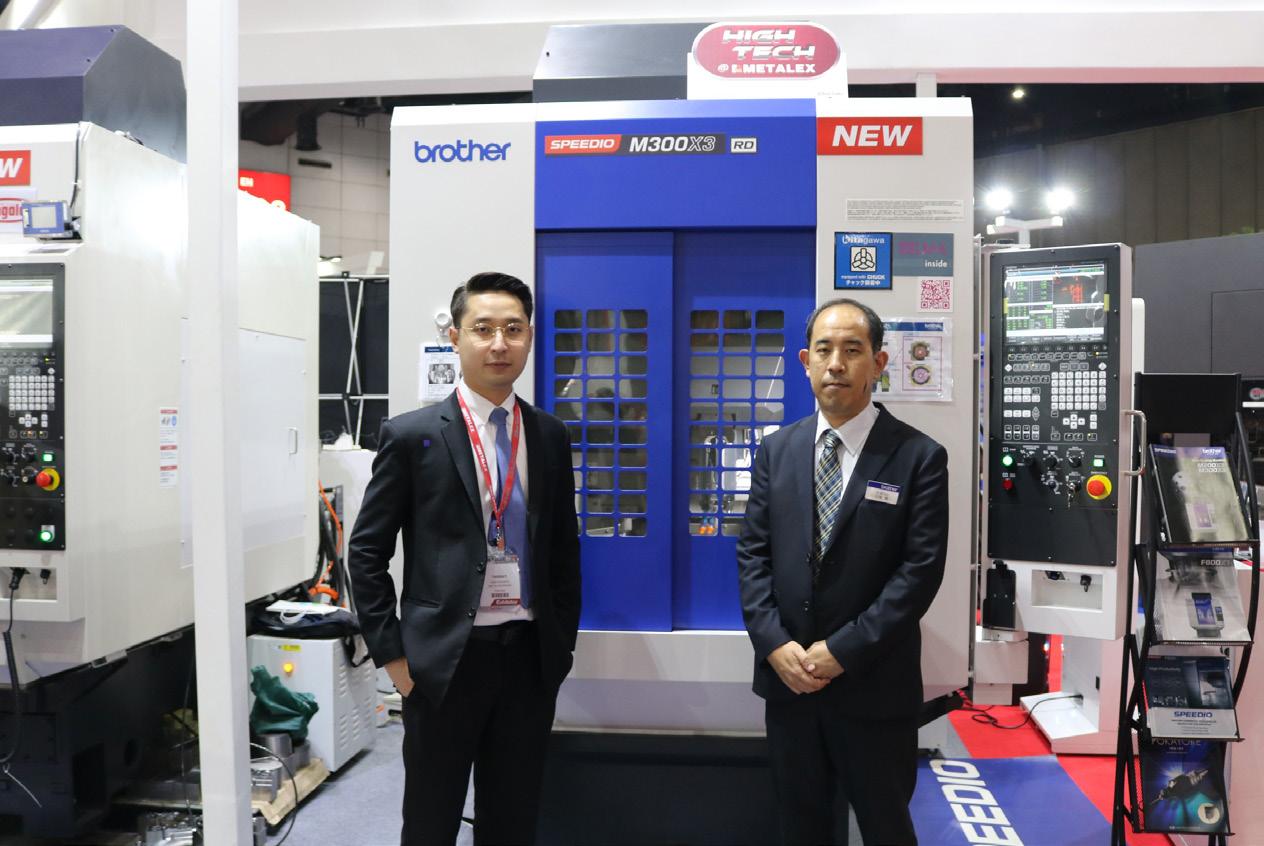
Ryoichi Roy Nitao, General Manager, Brother Commercial Thailand
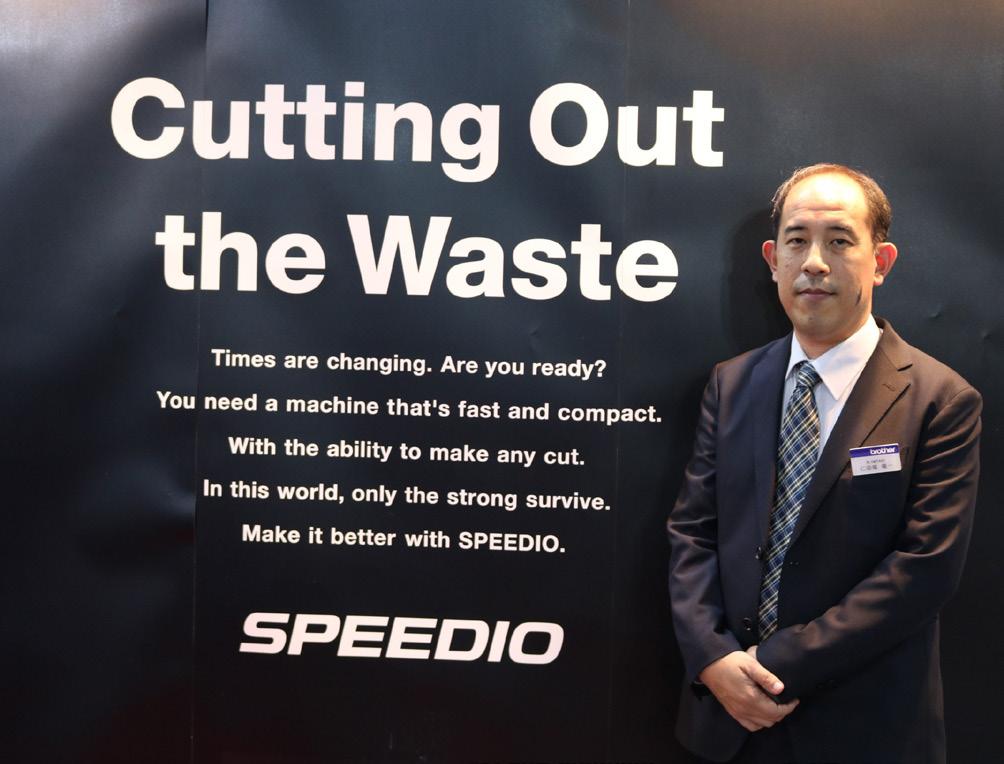
First of all, I would like to thank AP Metalworking and AP Plant Management for this opportunity to share with readers. Brother Thailand is primarily focused on machining tools for this year at Metalex 2020.
For Brother group, our main products are manufacturing of machining tools, printers, sewing machines and a variety of other printing products. For machine tools, our main focus is supplying machinery to the automotive and industrial part manufacturing industries. We primarily market the machines for aluminum die-cast and other metal parts. Supplying machinery for general machining in Job shops are also another key component of our business as for machine tools our focus is more onto the smaller and medium sized parts for the Thai market. Our office in Thailand oversees the Asian region business, namely Vietnam, Malaysia, Singapore, Indonesia, the Philippines and India.
Our main product highlight for the METALEX exhibition this year can be summarized into four products. We have made a leaflet this year to introduce products that we showcase. Our multi-tasking machine M300X3 is our main product for this year. Features for this machine includes the capability of not only do machining but also rotates the workpiece in other and has the capacity to conduct turning applications as well. Secondly, as a fully automated proposal, we have the BV7-870 loading system which is exclusive to our S300X2, S500X2 and M200X3 machines. Third the F600X1, which is a highly robust 30 taper machine aimed for cutting the more challenging materials. Finally, the S300X2, is the most compact machine for factory floor space-saving that we have in a product line-up right now. As for our business strategy for 2021, our focus is to strengthen our distributors and trading companies and technical expertise. In light of the Covid-19 situation, we may have to focus more online seminars for promotion tools, and this applies not only to our machine tools but to our other product divisions as well. For Brother, our mission is to provide machining tools for mass productivity. In the past, customers would just look for larger machinery. For Brother, our focus is to select the machine that’s more suitable for customer’s production needs.
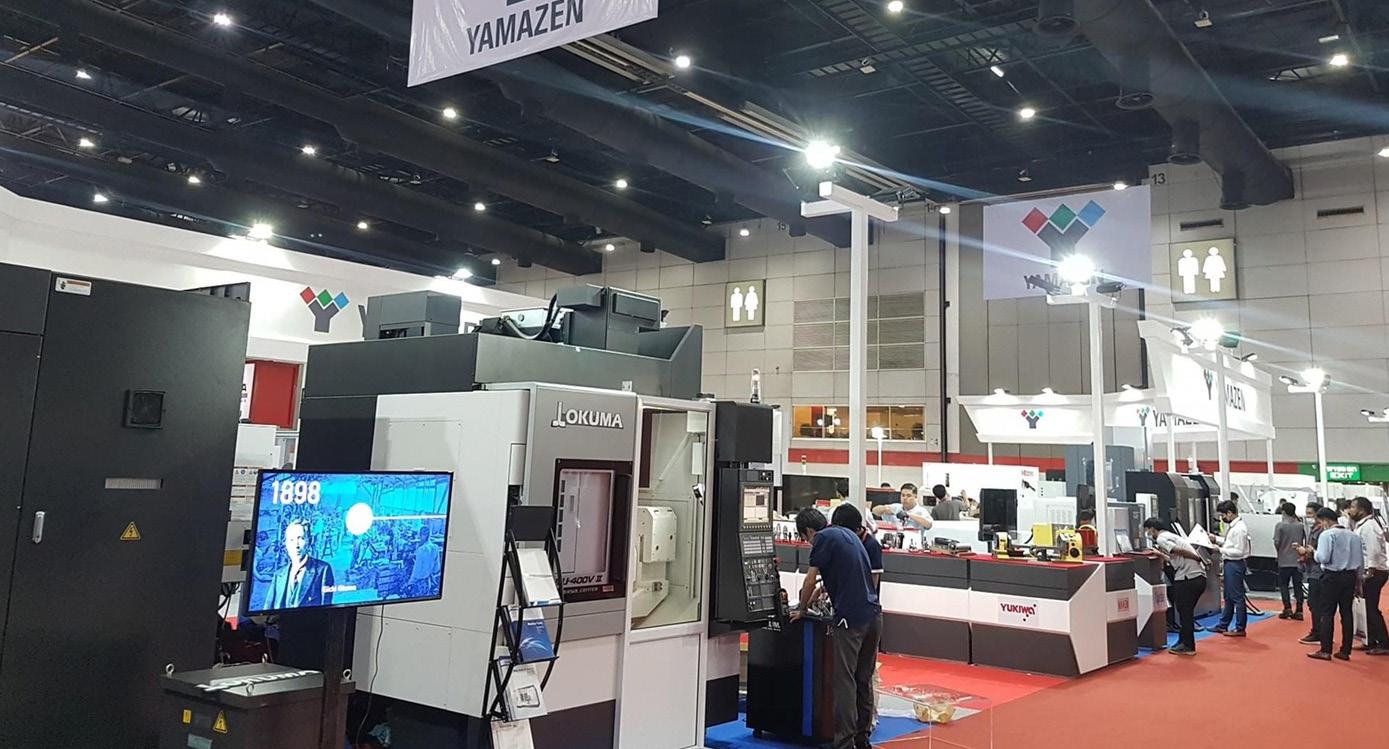
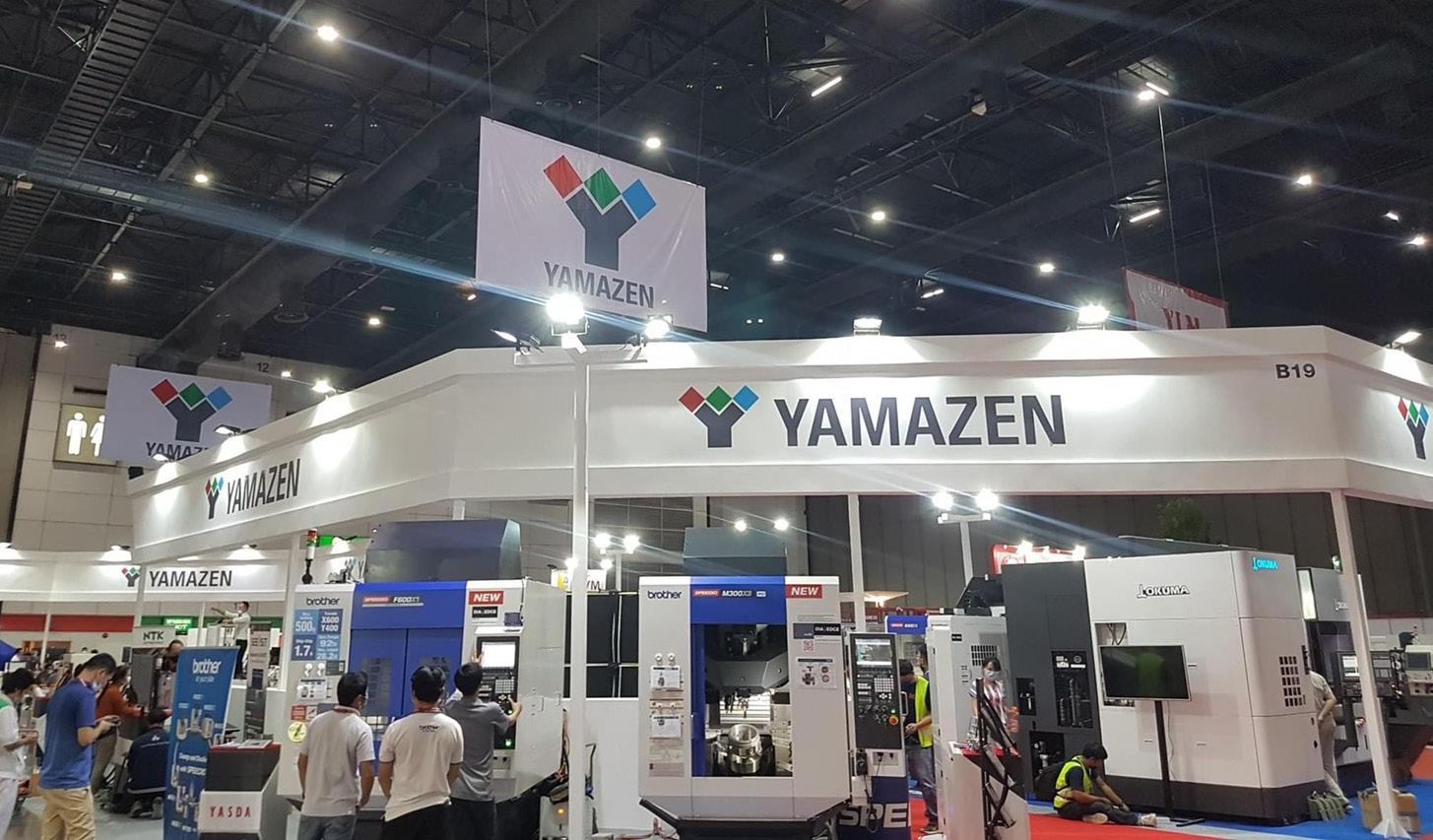
Masashi Hagihara, President, Asean Regional Headquarters Yamazen Thailand
Yamazen has been in Thailand for more than thirty years. Due to Covid-19, Yamazen has also been inevitably been affected. “We have to follow the market and the end user such as factories. If the factories cannot perform their business, we cannot perform our business as well.”
“For Thailand and Vietnam, the situation is still well under control. For other countries in the region Covid-19 remains a pervasive problem. Clearly, Covid-19 situation is beyond our control. However, Yamazen has sought to online tools such as webinars for communicating with suppliers and end-users. We wait for it to end. Once pandemic is over, customers will be busy and we will have to prepare so that we are busy as well.
spEcial articlE BY scHunk
Digital twins for everything/ everyone

Open Source is the magic word that should move digitalization of industrial processes forward : The foundation of the technology association “Industrial Digital Twin Association”, the two associations VDMA (German Engineering Association) and ZVEI (German Electrical and Electronic Manufacturer’s Association) should pave the way to a real mass start towards industry 4.0. This project is supported by 18 companies from mechanical and electrical engineering, and one of the participants is SCHUNK, the specialist for gripping systems and clamping technology. It has already gained extensive expertise in the generation digital images of their components. The aim of the association is to combine parallel developments of the digital twin, and to further develop it jointly as an open source solution.
In order to simplify conception, design, and commissioning of automated systems, SCHUNK already pushes digitalization of engineering for several years forward. In conventional engineering processes, mechanics, electrics and software programming run off successively, however, the world of digital simulation combines all three disciplines on one surface, and therefore opens the possibility of parallelizing all activities. This speeds up everything, reduces complexity and communication problems, increases flexibility and saves costs, also because possible errors are detected and eliminated at an earlier stage. Changes can be applied within no time at all and their feasibility verified. Comparable follow-up projects can therefore be implemented much faster than was previously possible.
A complete digital 24 V program for high-speed assembly is already available
Digital twins of SCHUNK components are already available in a wide variety of software solutions. As a part of an OEM partnership with Siemens PLM Software, the competence leader for gripping systems and clamping technology offers an attractive starter kit, the Mechat ronics Concept Designer™, which includes a library of digital twins as well as introductory training courses and individual support for users. Designers, programmers, and project developers can test the simulation software for six months in the full version free of charge. SCHUNK has already created its 24 V mechatronics program for high-performance assembly completely as a library of digital twins. The complete gripping system program will follow successively. In the field of tool management, digitalization also creates the ideal conditions for simulations, collision analysis and store floor management. Therefore, SCHUNK provides the data for the TENDO, TRIBOS, and SINO toolholder series in accordance to standard DIN 4000 as digital twins.
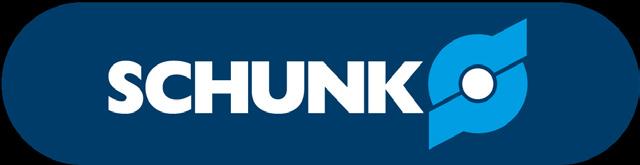
The open source strategy has wide-ranging effects
“While the solutions which are available on the market have provided access to the technology of digital twins exclusively within individual ecosystems, the digital twin for industry 4.0 will now be established as an international standard,” explains Timo Gessmann, Chief Technology Officer (CTO) at SCHUNK. “The new user organization and the associated cooperation offer a great opportunity to significantly accelerating digitalization of the industry in the upcoming years, because availability of digital components and security of investment in new technologies will increase.” The two associations VDMA and ZVEI as well as Asentics, Bosch, Bosch Rexroth, Danfoss, Endress+Hauser, Festo, Homag, KUKA, Lenze, Pepperl+Fuchs, Phoenix Contact, SAP, Schneider Electric, SCHUNK, Siemens, Turck, Volkswagen and Wittenstein participate in the network.