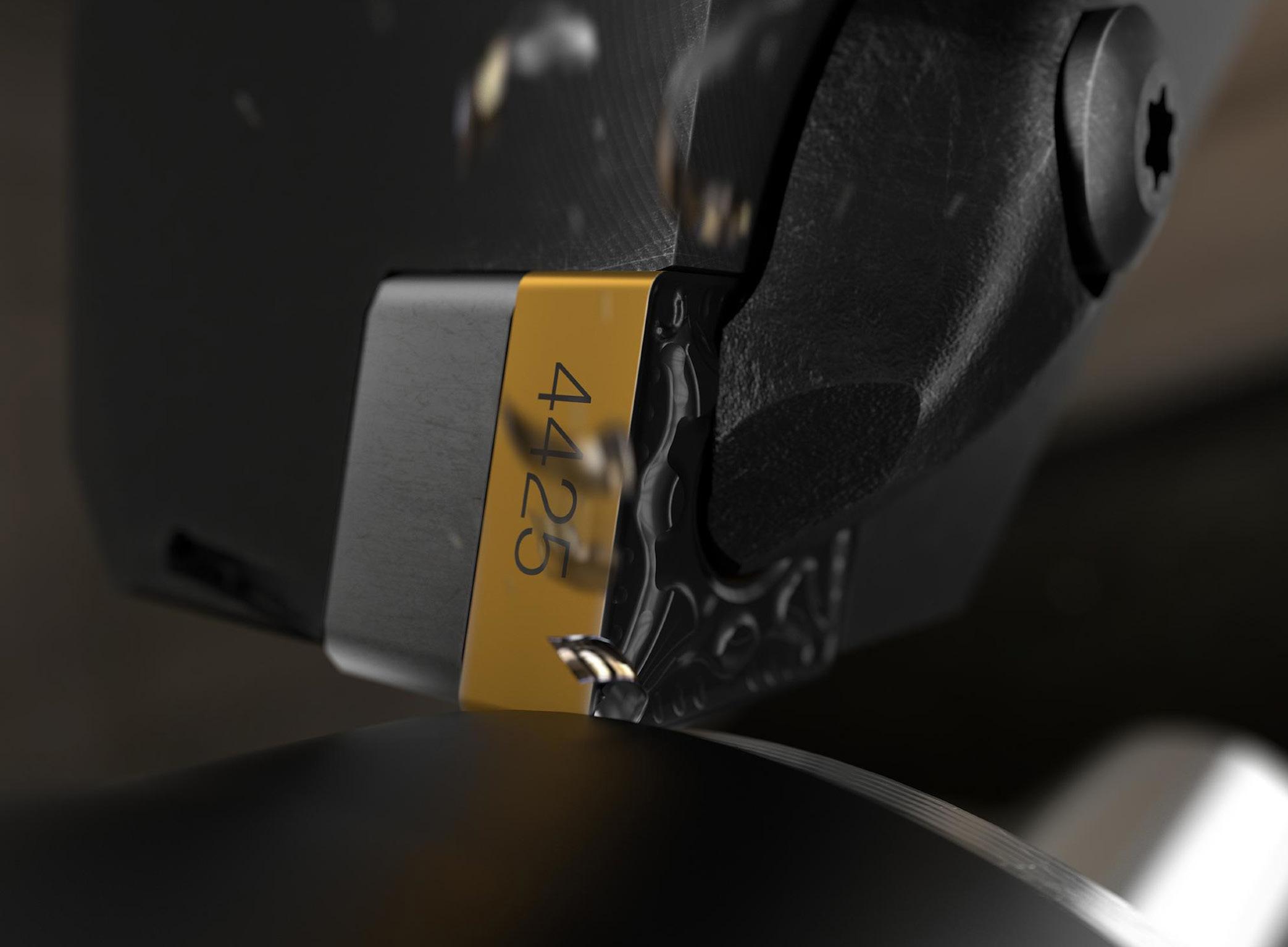
31 minute read
Fixing what isn’t broke Why manufacturers should embrace a new generation of tooling solutions Materials are Key to Meeting the Growth in Demand for Li-ion Batteries
BY SANDVIK COROMANT
Fixing what isn’t broke
Advertisement
Why manufacturers should embrace a new generation of tooling solutions
The father of modern political philosophy, Machiavelli, said that, “Whosoever desires constant success must change his conduct with the times.” We are surely living in unprecedented times with the ongoing effects of COVID-19 on industry. Here, Rolf Olofsson, Product Manager at Sandvik Coromant, the global leader in metal cutting tools explains why now is the time for machine shops to embrace a new generation tooling solutions to tackle steel ISO P turning challenges and make their production more efficient and productive.
For manufacturers, stepping away from the established way of doing things — whether it’s a production process, method of communication, or a trusted machine or tool — invites risk. No wonder it so tempting to fall back on the old adage of “if it ain’t broke, don’t fix it.” Could a new tool or digitalized process create more disruptions than it’s worth?
Yet, there is more onus than ever on manufacturers to change with the times — whether they are dealing with mass or batch production scenarios. Research by Pinsent Masons, the German law firm, has identified three main drivers for change.
First, its survey of 100 German manufacturers and German students found that disruptive Industry 4.0 technologies, like artificial intelligence (AI) and intelligent automation, are “sparking a fresh industrial revolution”. Second, the green agenda is driving manufacturers more quickly towards low carbon business models. Third, Pinsent Masons found “that macroeconomic pressures such as Brexit, and now COVID-19, will cause global supply chains to fragment.”
How can manufacturers overcome this trio of obstacles without losing sight of the two main challenges: increasing output and reducing costs? And, how can they do so while machining one of most common and complex ISO P (steel) work piece materials? The answer lies is next generation tools — even if the last generation of tools ain’t broke.
The right stuff First, let’s look at the two ultimate goals for manufacturers to achieve profitable steel turning, increasing output and reducing costs. Manufacturers should drive down the appropriate production costs for their specific situation. The situation will depend on whether they are dealing with mass or batch production, and is more unpredictable in the COVID-19 era where manufacturers are facing changeable high-or low-demand scenarios, and must adapt accordingly. Manufacturers must always strive towards maximizing their machining output that, according to Sandvik Coromant’s findings, can reduce the overall cost per component by 15%. To properly maintain a higher machine output, it’s also
necessary to increase metal removal rates, and reducing scrap and component rejections to manufacture more steel components in a shorter time.
Central to all of this is the manufacturer’s choice of tool, specifically their choice of insert. That’s why Sandvik Coromant recommends choosing steel turning insert grades that can deliver most predictable and consistent performance.
Stay in shape Sandvik Coromant added two high performing carbide insert grades to its existing range, GC4415 and GC4425. The inserts’ designations refer to P15 and P25, the demands that different working conditions impose on machining parameters — cutting data, surface finish, depth of cut, machined or rough surfaces, continuous or interrupted cuts.
The two new carbide inserts from Sandvik Coromant can meet these parameters. While GC4425 delivers improved wear resistance, heat resistance and toughness, GC4415 is designed to complement GC4425 where enhanced performance and better heat resistance is needed.
Both contain the second generation Inveio® coating technology. What makes Inveio unique can be examined at the microscopic level: the material’s surface has a uni-directional crystal orientation. Each crystal lines-up towards the cutting edge, creating a strong barrier that improves crater and flank wear resistance. Heat is also lead away from the cutting zone more quickly, which keeps the cutting edge in shape for longer time in cut.
So, GC4415 and GC4425 can machine a larger number of pieces within a mass and batch production set-up. Each insert contributes towards extended tool life, eliminating sudden breakages and reducing reworking and scrap.
With the ability to machine more components one set-up, the new insert grades can reduce the production interruptions caused due to frequent insert changes and time spent in finding the right insert for each application or material — both factors are considered to be the biggest time killers in modern production.
Coolant can further improve the insert performance, deliver even better performance in all aspects and play a crucial role in reducing overall production cost. Under coolant controls the heat in the cutting zone, which leads to improved tool life and predictable machining. This makes it possible for operators to increase the cutting speed or feed, which allows for a greater productivity increase and maximized output.
In addition, precision coolant with pre-directed nozzles focused directly at the cutting zone, which is a good way to achieve chip control. That is why, if correctly applied, coolant will maximize output, increase process security and improve cutting tool performance and component quality. These are all important cornerstones in successful machining.
We’ve examined how factors like choice of tool and the use of coolant can yield tangible machining benefits — but what could manufacturing gain by applying a new methodology to their steel turning operations?
Sandvik Coromant’s specialists asked themselves this question, and the result was a new ethos that we call PrimeTurningTM, designed as a good choice for mass production or components needing frequent set-ups and tool changes.
In particular, if turning is a bottleneck operation, then companies suffer a restriction on the number of components produced per run. Therefore, manufacturers need to reconsider their turning process in order to get maximum output from their modern machine tools, which are currently being underutilized.
This is where the PrimeTurning can support, offering flexibility to do turning in all-directions. With it, machine shops can realise a multi-fold productivity increase without compromising process security and tool life. This way of turning is found to be much more efficient and productive compared to conventional turning.
Positive change GC4415 and GC4425 have already proven advantageous since they were launched to market, earlier this year.
In one case, a manufacturer in general engineering, pitted the GC4415 insert against a competing insert, and put to work in machining an AISI/SAE CMC 02.1 steel workpiece with a Brinell hardness of 220 HB.
As the workpiece was subjected to axial external turning and light roughing, the customer was able to run the GC4415 at a higher cutting speed (vc) of 300 m/min (984 ft/min) and feed rate (fn) of 0.33 mm/rev (0.013 inch/rev) compared with a competitor’s insert, which ran at a vc of 250 m/min (820 ft/min) and fn of 0.25 mm/rev (0.009 inch/rev). The competitor’s insert machined 200 pieces (pcs) per edge before breaking down, whereas GC4415 machined 256 pcs before only shown signs of risk of breaking down.
By switching to GC4415 and increasing the cutting data, the customer was able to achieve a productivity of 210% and reduce costs by 53%.
As this example shows, manufacturers can indeed prove Machiavelli’s assertion that, “whosoever desires constant success must change his conduct with the times.”
BY Frost & Sullivan
Materials are Key to Meeting
the Growth in Demand for Li-ion Batteries

Having chalked up lacklustre growth in 2019, global electric vehicle sales registered a sharp surge (+35% YoY) in 2020, defying the pandemic, ensuing containment measures and supply disruptions. In sharp contrast to the plummeting sales of conventional ICE vehicles, down by 14%, global EV sales volumes were estimated at nearly 3.1 million units in 2020. EVs represented nearly a tenth of total vehicle sales in Europe in 2020.
EVs: A Dramatic Rise despite the Pandemic Among a multitude of factors, government grants and incentives for zero-emission vehicles or EVs, especially in Europe, coupled with increasingly stringent regulations and legislations pertaining to CO2 emissions, competitive product offerings, continue to underpin the rise in EV sales.
Materials as Means to Achieve Common Ends As demand gathers momentum and several global-scale battery facilities come online, the production costs and hence the average battery price are expected to register further declines, thereby inching closer to the coveted tipping point of US$ 100/KWh (where the price gap between ICE vehicles and EVs disappears).
Accordingly, the quest toward packing in high energy densities to facilitate maximum possible driving ranges, while focusing on pushing the overall battery costs downward, continues to be the key factor driving development, adoption, and widescale use of specific battery materials.
The subsequent sections highlight the key trends that are expected to shape the demand for specific Li-ion battery materials over the remainder of the decade. Cathode Materials Cathode materials make up 30% to 45% of the overall battery materials cost, depending on the type of composition under consideration. The need for longer-range EVs and decoupling battery costs from the ever-volatile cobalt prices have been prompting manufacturers to increasingly shift toward highernickel compositions.
With rapid advancements in cell chemistry and ever-agile supply, especially in China, NCM-based cathodes are expected to remain the mainstay in the global market over the midterm. Furthermore, to improve energy density and raw material supply security, NCM-based Li-ion battery manufacturers (in collaboration with OEMs and cathode material suppliers) have been developing advanced battery chemistries composed of fewer proportions of cobalt and higher quan-tities of the relatively more abundant nickel. Thus, there is a swift shift from NCM 1-1-1 (comprising one part each of nickel, cobalt, and manganese) toward NCM 5-3-2, NCM 6-2-2, and NCM 8-1-1.
However, it is important to note that such a move away from cobalt and toward nickel-rich cathodes also entails a shift in demand toward higher-purity lithium, higher-quality electrolytes, and the replacement of lithium carbonate with lithium hydroxide.
Anode Materials While there have been rapid shifts in cathode chemistries, graphite continues to be the material of choice for Li-ion battery anodes. While silicon anodes and lithium metal-based anodes are being developed as promising alternatives to graphite anodes, graphite continues to be the single largest component in prevailing batteries, owing to its consistency, lower electrochemical reactivity, and structural stability.
Furthermore, within the graphite space, synthetic graphite is increasingly becoming the material of choice, especially for EV batteries, owing to its higher purity and stability than natural graphite.
While pure-silicon anodes are not expected to be commercialized in the near term, especially for EV applications, the incorporation of a small portion of silicon-based alternatives in the anode composition is expected to gather momentum over the next five years.
Electrolytes As solid-state electrolytes continue to remain at the development stage, especially in the case of EV applications, liquid electrolytes are likely to remain indispensable to Li-ion batteries during the forecast period. Although electrolytes account for a comparatively small share in the overall battery pack cost (5% to 8%), the overall performance and functioning of the battery largely depends on the efficient functioning of the electrolyte.
While conventional formulation ensures electrochemical stability and high ionic conductivity and guards the aluminum current collector against corrosion, the use of high-voltage cathode materials to enhance the energy density of the battery results in the rapid degradation of conventional organic solvents-based electrolytes. This, in turn, significantly reduces the battery cell life. Accordingly, additives that enhance the safety and performance and improve electrolyte properties are increasingly being used in conjunction with organic solvents and lithium salts.
Separators Separators play a vital role in ensuring efficient performance and safety in a Li-ion battery. Separators prevent short-circuits (and subsequent fire hazards) in advanced Li-ion batteries, characterized by increasingly high energy densities. While these components effectively prevent direct contact between cathode and the anode, they continue to allow the transport of ions through pores on the substrate.
The ever-increasing energy densities in batteries and the swift move toward low-cobalt-containing cathode chemistries necessitate battery separators to play an all-the-more important role in ensuring safety and optimum cell performance. Furthermore, as against dry separators that dominated the market in the past, wet technology-based separators are expected to continue witnessing increasing preference, owing to several advantages such as the ability to be manufactured as thinner separators, with uniform distribution of pores and higher safety and stability.
Binders Binders or binding compounds are polymeric materials that bind the active materials to each other and to the conducting compounds/additives as well as the collector plates, thereby ensuring the integrity (and life-span) of the electrode throughout the battery life cycle.
Binders account for a mere 2% to 3% of overall battery mass. While a variety of materials such as PVP, PTFE, PVA, PAA, have been (and are being) developed, two of the most well-established materials for electrode binders continue to be PVDF-NMP and SBR/CMC. The segment continues to be characterised by developments focusing primarily towards addressing the need for a solventfree, environment-friendly, process based on aqueous slurries as against conventionally used organic solvent (NMP) based binders in case of cathodes. Whereas the development of solutions for anodes composed of silicon-composites along with graphite are expected to offer sizeable growth opportunities.
Adhesives & Sealants Adhesives and sealants play a vital role in ensuring the structural integrity of the battery pack and its components, contributing to the overall strength and stiffness of the battery pack, conducting heat away from the pack components, isolating the battery components from dust, fluids, vibrations and mechanical shock.
Also, in the wake of growing sustainability concerns as well as the need for cost-effective alternatives, there is a growing focus on developing solutions for serviceable battery packs wherein the packs can be repaired and resealed without causing a surface failure. Furthermore, tightening thermal management-related regulations are expected to drive the demand for thermal interface gap-filling adhesives.
Frost & Sullivan’s study on Li-ion Battery Materials quantifies the consumption of key materials for lithium-ion batteries, focuses on gauging the level of impact that the market developments such as advancements in battery chemistries and technologies, upsurge in electric vehicle sales, evolving regulatory scenario, and the increasing shift in consumer preferences towards electric vehicles are expected to have on the demand for individual materials over the seven-year period, 2020-2027.
For more information : https://ww2.frost.com/frost-perspectives/materials-are-key-to-meeting-the-growth-in-demand-for-li-ion-batteries/
BY World Economic Forum
The Automobile industry needs to steer in this direction for future success
The automotive industry needs to become digitalised.
Manufacturers will enjoy increased efficiency and productivity by embracing Industry 4.0. This was a start; the aim was to produce a variety of all-electric trucks and SUVs. However, the pandemic should have served as a greater wake-up call for the industry than so far seems the case.
Automotive manufacturers and downstream suppliers need to implement change management strategies.
Automotive companies have spent the best part of a century investing billions into their enterprise systems. It’s now time they kept pace with the digital revolution of Industry 4.0. What’s more, this is critical to their survival.
Original equipment manufacturers (OEMs), and tier 1 manufacturers in particular, must begin to acknowledge the responsibility they have in supporting their downstream suppliers in becoming Industry 4.0 proficient.
The digital transformation of today requires a complete culture shift, involving automakers and auto suppliers investing in change-management strategies that realign the entire supply chain.
In January 2020, General Motors announced it was investing $2.2 billion into its Detroit-Hamtramck assembly plant, since renamed Factory ZERO (zero crashes, zero emissions and zero congestion). The raw computational power and foundational technologies supporting Industry 4.0 include artificial intelligence and Big Data, the Internet of Things (IoT), cloud computing, augmented and virtual reality, advanced robotics, 3D printing and cybersecurity.
Manufacturers that go down this path enjoy increased efficiency and productivity, improved product quality and processes, operating cost reductions, greater supply chain visibility, accelerated innovation and speed to market of new products, services and technologies.
Embracing this tech also revolutionises the role labor plays in the economy.
No pain, no gain Creatively destructing a company in the face of new realities can be painful. But it is entirely necessary, and especially so considering the shorter lifecycles of today’s technologies as they grow even more sophisticated, complex and exponential.
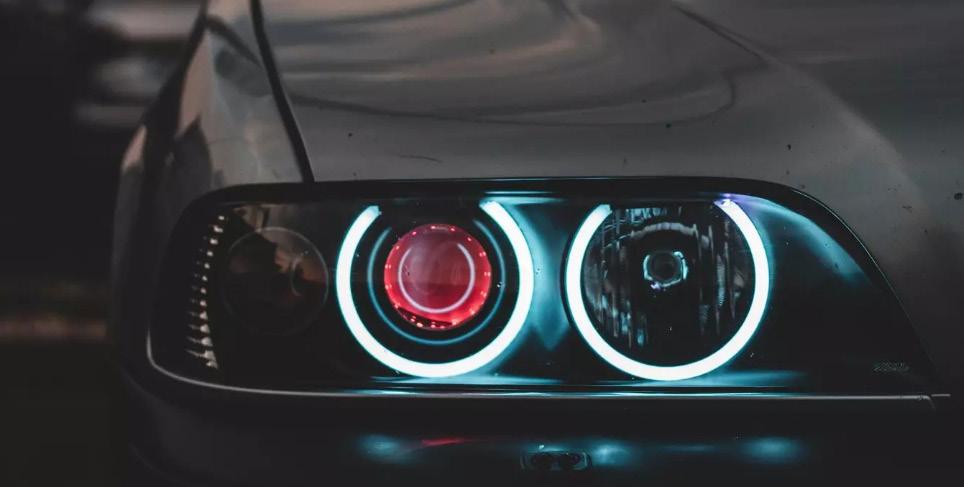
History proves the long-term benefits of adopting new technologies and processes, and those benefits far outweigh their initial barriers. Change management strategies that automotive manufacturers and downstream suppliers can implement include small, option-like bets and modest investments with the potential for large payoffs.
Change needs to trickle through though, and not be an avalanche of inputs. In this way, people and systems will prove able to absorb new technologies gradually and accept new ways of doing things without being overwhelmed by complexity. Once a company realises returns on their investments, it can incrementally integrate further technologies and processes.
3D printers for automotive suppliers One example of this approach working successfully is Automation Alley’s Project DIAMOnD, which has seen 300 3D printers distributed to manufacturers across Oakland and Macomb Counties – a Southeast Michigan region filled with automotive suppliers of all sizes and levels of sophistication.
Project DIAMOnD has created the largest independent and distributed 3D-printing network in the world operating on a blockchain technology platform to address the urgent need to move companies to Industry 4.0.
One of the firms involved, Rochester Hills, Michigan-based Air & Liquid Systems – a tier 2 automotive supplier with 40 employees and an annual revenue of $20 million – is using its 3D printer to print a part that was previously made of stainless steel and cost $100. It now costs them only $1 to make out of carbon fiber.
Their printer is placed near the engineers to make them more curious about what else they can create, shifting the way they think about production and their business. For the company CEO, Jim Miller, it was exciting to see the culture change of integrating into manufacturing new technology that positions the organization for gains on its journey to Industry 4.0.
Similarly, Josh Tucker of Shelby Township Michigan-based Tucker Induction System, was surprised by how quickly his company was able to produce 3D-printed parts that proved to withstand tension, heat, and other forces seen in real-world scenarios.
The company is a Tier 3 automotive supplier with 17 employees and an annual revenue of $3 million. They are now 3D printing some parts that were previously produced using subtractive manufacturing methods and also using 3D printing to develop completely new solutions. “This technology is not just for prototyping. You can actually print parts and put them out in the field,” Tucker said. Investment in digital technologies to upgrade or enhance legacy systems, like the 3D printing examples above, are not only good for increased efficiency and cost reductions, but also for supply chain resilience.
Supply chain benefits We have seen how trade disputes, COVID-19 and other unforeseen circumstances have caused supply bottlenecks for auto manufacturers in the areas of rare earth materials, semiconductors and personal protective equipment. It has reversed some of globalisation’s gains, while hastening the insourcing of production.
It will take years for the US to reconstruct a domestic ecosystem of suppliers and a network of skilled workers hollowed out during the trend to offshore production. The hope is that rapid advancements in technology will shift some manufacturing back to the US and create a multitude of well-paying local jobs.
The implications for the world economy are also enormous. According to ING, 3D printing alone is projected to reduce global trade flows by 40% by 2040.
Domesticate or diversify? A recent article in The Economist suggests that the “way to make supply chains more resilient is not to domesticate them, which concentrates risk and forfeits economies of scale, but to diversify them.” This is especially true in the case of auto companies that are obliged to build in the countries where they sell their production. That said, this view may hint at some blind spots regarding the degree to which natural disasters, diseases and trade wars have disrupted supplies chains.
What is indisputable is the urgency for manufacturers to embrace the emerging technologies their competitors have already deployed in factories.
The pandemic has provided forward-thinking business leaders with the ammunition they may have needed to create change from within, in response to extenuating circumstances imposed from without.
Indeed, many enterprises have vaulted their digital transformation forward five years in the matter of 14 months during the pandemic crisis — a silver lining that was just aspirational at the end of 2019. For its part, the auto industry and its largest suppliers need to lead their broader supply chain to a sustained transformation to Industry 4.0, despite the fact that the pandemic – and the urgency it wrought – is starting to ebb.
For More Information : https://www.weforum.org/agenda/2021/06/the-automobile-industry-needs-to-steer-inthis-direction-for-future-success/
BY SCHUNK
Desktop Metal Qualifies
4140 Low-Alloy Steel for High-Volume Additive Manufacturing of End-Use Parts With the Production System




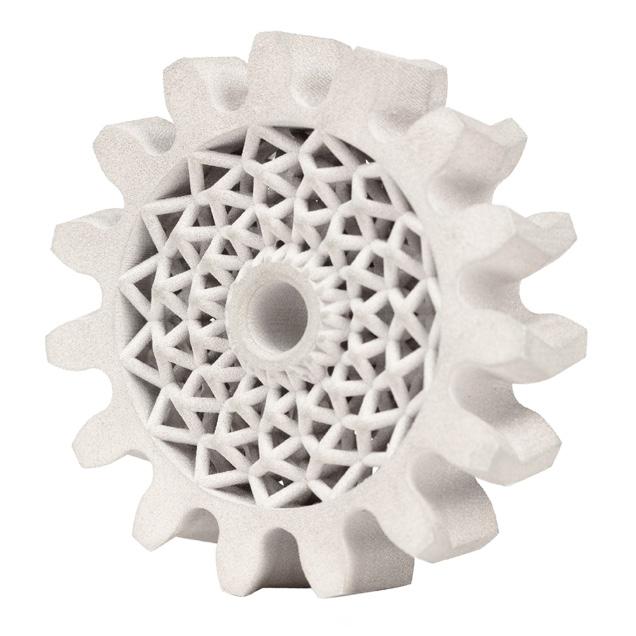

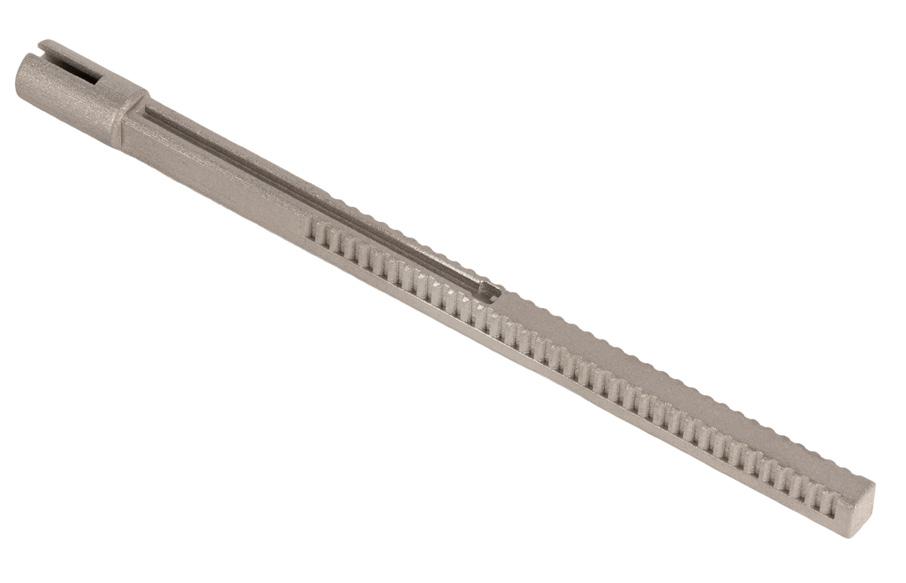
The First Company to Qualify 4140 via Metal Binder Jetting for the Mass Production of Strong Steel Parts That Withstand High Impacts, Temperatures and Mechanical Stresses
Desktop Metal (NYSE: DM), a leader in mass production additive manufacturing (AM) solutions, today announced it has qualified the use of 4140 low-alloy steel for the Production SystemTM platform, which leverages patentpending Single Pass JettingTM (SPJ) technology designed to achieve the fastest build speeds in the metal additive manufacturing industry. Desktop Metal is the first and only company to qualify 4140 low-alloy steel for use with metal binder jetting systems, enabling its use in mass production end-use part applications.
Considered one of the most versatile low-alloy steels, 4140 is characterized by its toughness, high tensile strength, and abrasion and impact resistance. It is a critical all-purpose and heat-treatable steel used extensively in a variety of automotive, oil and gas, and industrial applications, such as gears, downhole tool components, couplings, spindles, bolts and nuts, and many other mechanical parts.
“4140 has been a challenging material for metal binder jetting because of its low alloyed content, tight carbon control requirements, and low ignition energy, which together require advanced binder chemistry, as well as extensive printing and sintering optimization and atmospheric controls for safe processing,” said Jonah Myerberg, co-founder and CTO of Desktop Metal. “We are excited to be the first to qualify 4140 for metal binder jetting to enable this versatile material for the AM industry. With the speed of the Production System, businesses can now use binder jetting to print complex 4140 parts at competitive costs while maintaining the strength and mechanical properties of traditionally manufactured alternatives. This is a game-changing
solution for manufacturers who have been tied to timeconsuming and expensive machining and conventional tool-based manufacturing processes.”
4140 Low-Alloy Steel - Key Applications Desktop Metal’s materials science team has validated that 4140 low-alloy steel printed on Production System technology and sintered by Desktop Metal meets MPIF 35 standards for structural powder metallurgy parts set by the Metal Powder Industries Federation. 4140 parts printed on the Production System platform not only eliminate the use of tooling and minimize material waste, but also represent a significant decrease in production time and part cost compared to conventional manufacturing methods.
Power Steering Joint This joint is used for power transfer between an electric power steering motor and the steering shaft in an automobile. 4140 provides excellent strength and hardness, which is essential for the spline teeth that connect this part to the rest of its assembly. While production using a conventional press and sinter process would require an expensive mold, the Production System P-50 enables production with no tooling, reducing lead times and enabling more flexible design for quantities up to 1.2 million per year at a fully burdened part cost as low as $2.45.
Herringbone Gear Herringbone gears, which are found in a variety of industrial machinery applications, benefit from the excellent hardness of 4140 low-alloy steel and can be lightweighted using complex lattice designs made possible by additive manufacturing, reducing material cost and reducing wear on external components, such as motors and bearings. This part can be mass produced on the Production System P-50 in quantities up to 200,000 per year with 120 parts nested in each build.
Linear Pneumatic Piston Linear pneumatic pistons are used to convert air pressure into rotary motion through a rack and pinion with 4140 providing the toughness and wear resistance required for this application. These parts are traditionally assembled from multiple components due to the geometry and cost limitations of conventional manufacturing processes. The Production System P-50 enables production of up to 690,000 parts per year at a cost as low as $0.28 per cubic centimeter of sintered 4140 low-alloy steel.
Lever Drive Lever drives are often used in machine design to linearly adjust the location of components in a machine. Binder jetting easily facilitates features such as the precise grooves critical for locating the correct position of external components. While producing a mid-volume run of 10,000 parts would not be cost-effective with conventional manufacturing given the upfront tooling costs or the labor costs associated with machining, the Production System P-50 can print the required quantities in a day with sintered parts ready in less than a week.
The Production System - the World’s Fastest Way to 3D Print Metal Parts At-Scale
Created by the inventors of binder jetting and single-pass inkjet technology, the Production System is an industrial manufacturing platform powered by Desktop Metal’s SPJ technology. It is designed to achieve speeds up to 100 times those of legacy powder bed fusion additive manufacturing technologies and enable production quantities of up to millions of parts per year at costs competitive with conventional mass production techniques.
The Production System platform consists of two printer models: the P-1, a solution for process development and serial production applications, and the P-50, a large form factor mass production solution for end-use parts, scheduled to begin commercial shipments in the second half of 2021. The Production System combines Desktop Metal engineered binders with an open material platform, allowing customers to produce high-performance parts using the same low-cost metal powders used in the Metal Injection Molding (MIM) industry. An inert processing environment enables compatibility with a variety of materials, including 4140 low-alloy steel as well as other high-performance alloys and even reactive metals, such as aluminum and titanium. To learn more about the Production System, visit: www.desktopmetal.com/products/production.
Today, the Production System platform materials library includes 17-4 PH stainless steel, 316L stainless steel and 4140 low-alloy steel, each of which have been qualified by Desktop Metal. The platform also supports several customer qualified materials, including silver and gold, and Desktop Metal plans to add additional metals to its portfolio, including tool steels, stainless steels, superalloys, copper, and more. To learn more about 4140 and the Production System materials portfolio, visit: www.desktopmetal.com/materials.
ExOne Metal 3D Printing
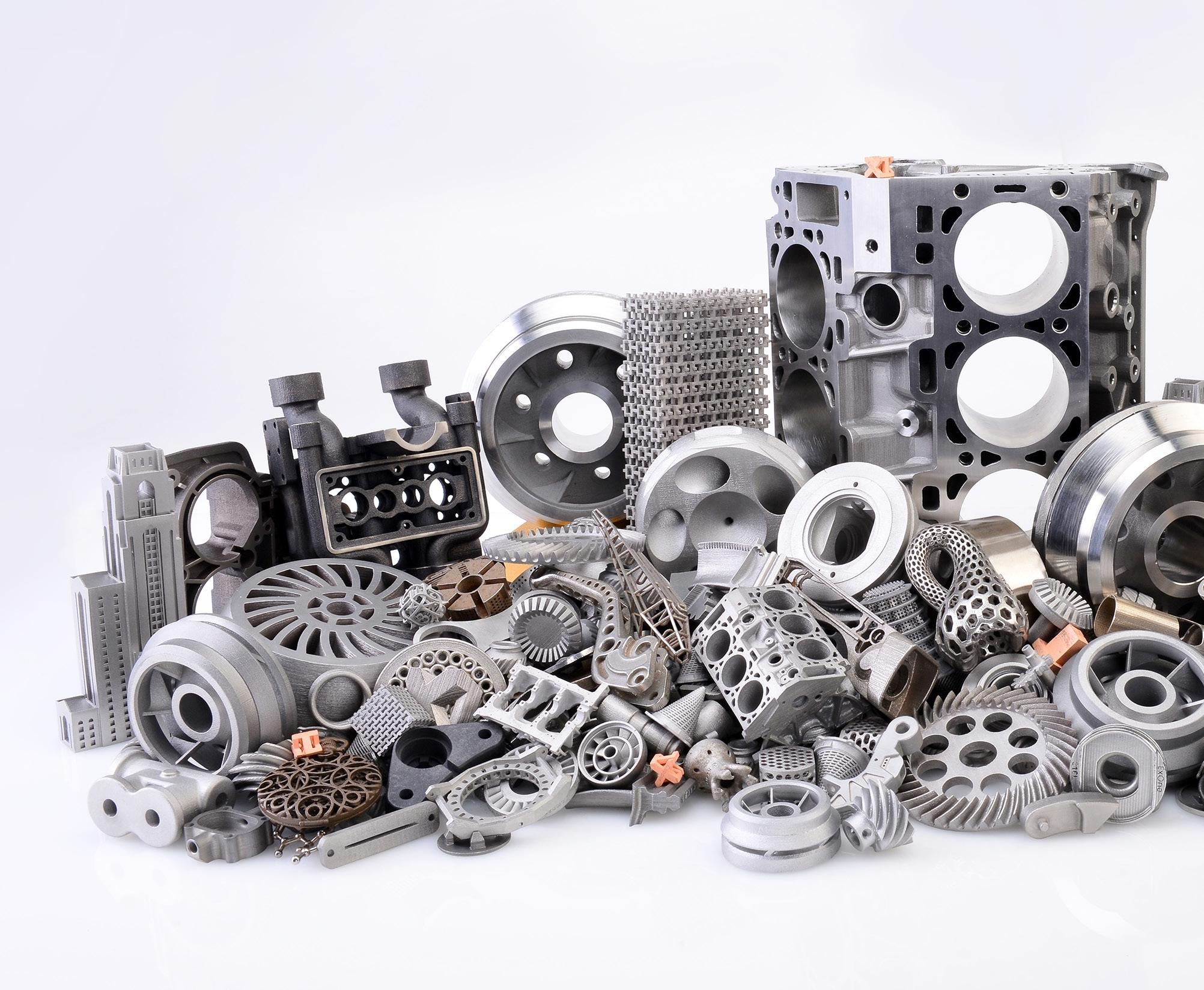
Adoption Center Surpasses 2 Million Parts, Adds New Systems for Stainless Steel Part Production
Two new X1 25Pro® binder jet printers now support dedicated production of 17-4PH and 316L stainless steel parts for industrial customers and service bureaus
ExOne will continue offering the company’s most popular and affordable 3D printed metal – now named X1 Metal 420i™ – available in a dozen custom finishes and durable enough for use in plastic injection molding and other tooling applications
The newly renovated Adoption Center operates 24-7 with 28 metal 3D printers and about a dozen furnaces, including a high-capacity Elnik batch furnace and a continuous furnace The ExOne Company (Nasdaq:XONE) (“ExOne” or the “Company”), the global leader in industrial sand and metal 3D printers using binder jetting technology, today announced it has surpassed delivery of 2 million metal parts to customers worldwide and has added two X1 25Pro metal printers for dedicated production of stainless steel parts.
The mission of the ExOne Adoption Center is to allow customers to try metal binder jet 3D printing for their designs before they decide to buy an ExOne printing system for their own production.
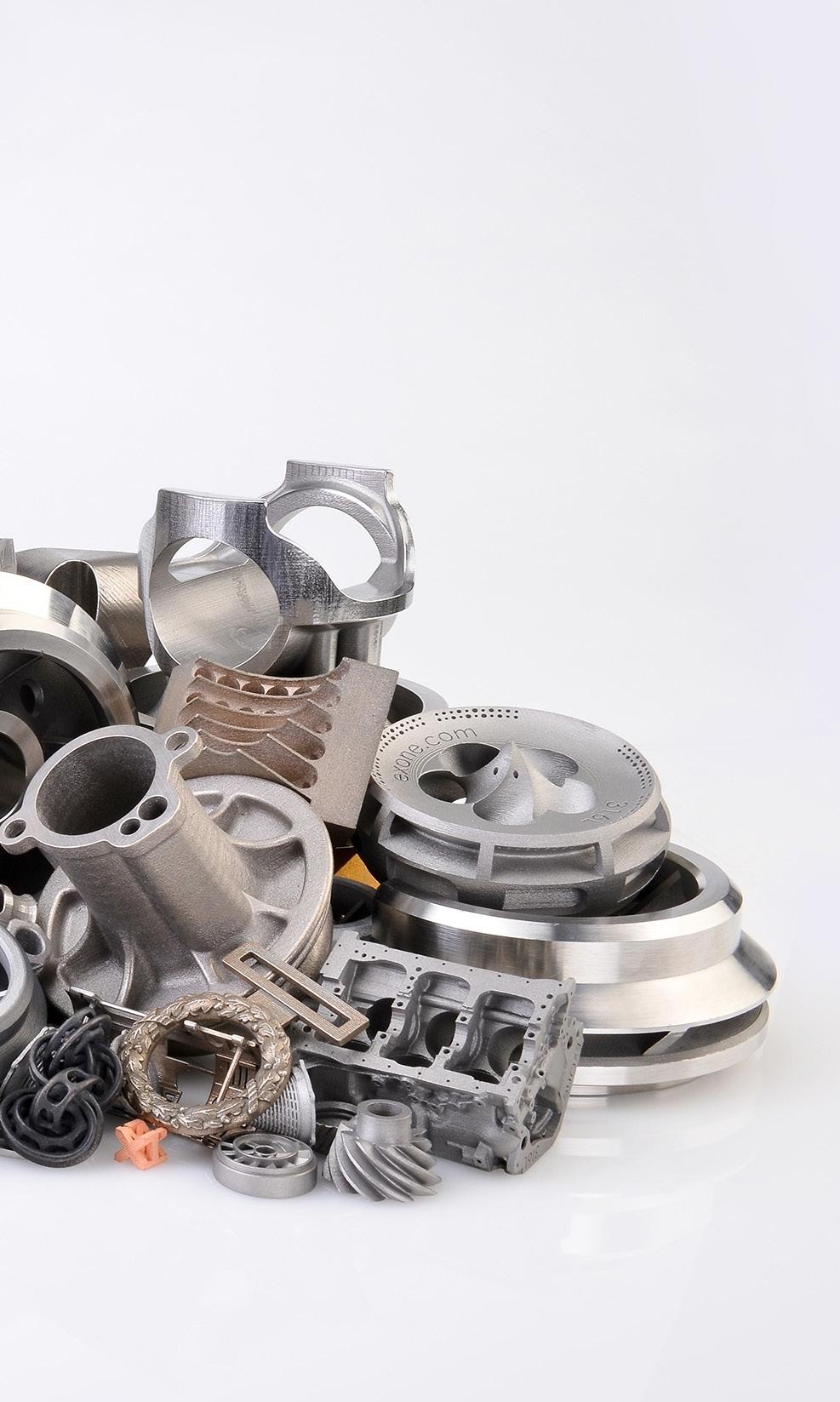
Located outside of Pittsburgh, ExOne’s Metal 3D Printing Adoption Center produces parts 24-7 on more than two dozen metal 3D printers for industrial customers and ondemand manufacturing service bureaus such as Shapeways, Sculpteo, Xometry, and more.
ExOne’s metal 3D production facility has been in continuous operation since 2005 and has now produced more than 2 million parts in a wide range of metals, with production of single-alloy metals picking up following the launch of the company’s patented Triple Advanced Compaction Technology (ACT).
Now featured on all ExOne production metal printers, Triple ACT uses an exclusive method of dispensing, spreading and compacting ultra-fine metal powders during binder jet 3D printing – delivering metal parts with industry-leading density, accuracy, and repeatability.
Two new X1 25Pro printers featuring Triple ACT have now been installed in the ExOne Adoption Center and are dedi cated to running two stainless steel materials for customers: 17-4PH and 316L. The 25Pro is designed for high-volume production and has a build area of 400 x 250 x 250 mm (15.75 x 9.84 x 9.84 in), enabling it to 3D print a wide range of part sizes.
ExOne also offers X1 Metal 316i™, an easier-to-machine matrix material that is 60% 316 stainless steel 40% infiltrated with bronze. This material also offers enhanced corrosion resistance properties.
A unique feature of ExOne’s binder jetting technology is the ability to 3D print metal parts with a specific level of porosity, which is helpful for filtration, tooling, and other applications.
ExOne and Shapeways will be hosting a webinar today at 10 a.m. ET about 3D printing 316L and X1 Metal 420i for consumer and industrial parts using ExOne’s exclusive approach to binder jet 3D printing.
What is Binder Jet 3D Printing? Widely regarded as the fastest method of metal 3D printing for high-volume output, binder jetting is highly similar to paper printing. An industrial inkjet printhead selectively deposits a binder into a bed of powder particles creating a solid part one thin layer at a time. Binder jetting can create 3D objects in metal, sand, ceramic or other powders. When printing metals, the final part must be sintered in a furnace to fuse the particles together into a high-density solid object.
ExOne has qualified more than 20 metal, ceramic, and composite materials for its binder jetting process. More than half of those materials are single-alloy metals, such as 17-4PH, 316L, 304L, M2 Tool Steel, Inconel 718, and more. Most recently, ExOne announced that 6061 aluminum is now a Customer-Qualified material, and titanium is now fast-tracked for qualification in partnership with a global medical device firm.
To have your part metal 3D printed with ExOne technology, contact one of our service bureau partners or visit www.exone.com/quickship for more information.
For More Information : https://www.exone.com/
BY Universal Robots
Universal Robots Handpicks Systems Integrators
to Deploy ActiNav Next-Generation Machine Loading

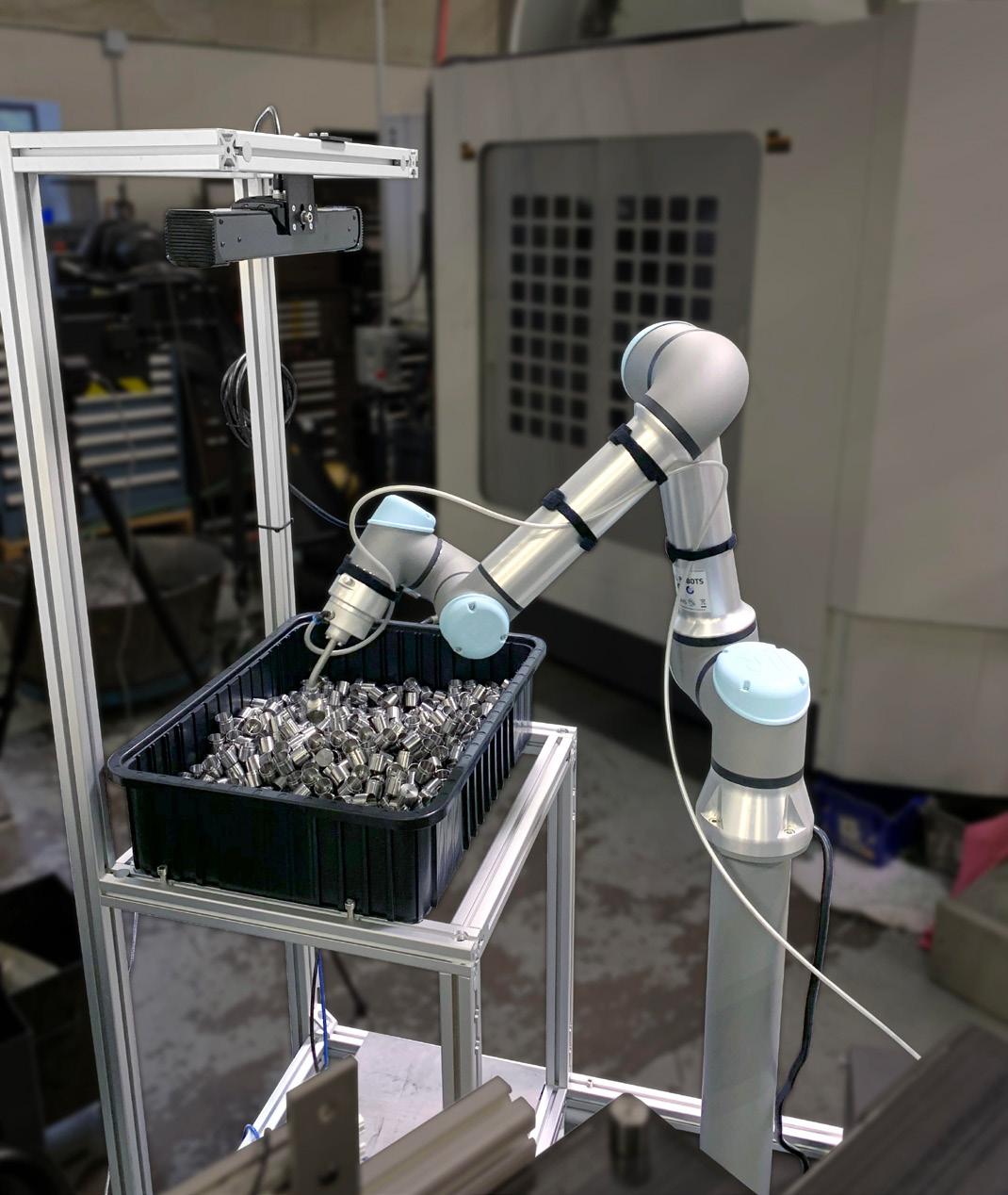
To better address demand for its popular ActiNav flexible machine loading system, Universal Robots announces the following integrators as ActiNav Solutions Providers to assist end users in ActiNav deployments.
Today, solutions for unstructured picking and placing of parts into machines are solely focused on the vision aspect, often requiring additional programming to bridge the gap from “pick” to “place” – especially if the “place” is not just dropping into a box but accurately inserting parts into fixtures for further processing.
ActiNav changes all that, combining real-time autonomous motion control, Universal Robots cobots, vision and sensor systems in one seamless Application Kit that solves the random bin picking challenge in machine tending applications. To help manufacturers integrate ActiNav into machining cells, UR has vetted and selected a limited group of systems integrators across the U.S. to deploy the next-generation machine loading solution.
The select systems integrators are: Eckhart Inc. (Michigan), Integro Technologies Corp. (North Carolina), Southwestern Production Technology Solutions (Texas), and Cross Company (North Carolina). Additional integrators in the U.S. and Canada are expected to be approved as ActiNav Solution Providers before the end of Q2, 2021.
“Our selection process focused on integrators with expertise in both vision and robotics, delivering superior value, and on time/on budget projects for customers,” says Bryan Bird, Regional Sales Director for Universal Robots’ North America division.
The selected systems integrators have all been provisioned with in-house demo units, enabling them to quickly develop proofs of concepts for customers in their region. “Integrating ActiNav into a machining cell is where the expertise of the right systems integrator really shines,” says Bird. “Our integrators will be able to quickly handle all peripheral requirements such as integration with safety sensors, machine interfaces, end-of-arm tooling and other components that all need to work together.”
Eckhart Inc. was the first company to become an ActiNav Solutions Provider. “We look forward to delivering increased machine uptime, quality and efficiency to manufacturers in our region,” says Sheldon Coney, director of robotics at Eckhart Inc. “In many ways, ActiNav will set a new level of operational expectations regarding the future of intelligent systems.”
Launched in April 2020, ActiNav has been deployed with numerous manufacturers across North America, who were seeking a simple solution to a complex problem. One of them is Flywheel Supply in Iowa. “The only way that made sense for us to put a robot on a machine tending application was to be able to do randomized bin picking,” explains Zach Northway, co-owner and lead project engineer at Flywheel Supply. “The cycle times on the machine are so short that if an operator has to stand there and line parts up in an organized fashion for a robot to pick them in a traditional sense, it would defeat the entire purpose of using the robot to begin with, because your operator is still standing there.”
In Flywheel’s ActiNav application, the UR5 cobot picks parts from a deep bin and places them in the jaws of a machine that indexes to multiple stations to perform tasks such as drilling, chamfering, and internal and external threading. Ultimately, the ActiNav system will process as many as 1,500 different part numbers, so it must be quickly programmable to pick parts of different shapes, sizes, and weights. “The biggest advantage to ActiNav is that it can take randomization of parts being dumped in a bin, and as the bin gets low, a person can just come by and dump some more into the bin and it will keep picking parts,” says Northway. “It doesn’t have to be reset, recalibrated—anything. It notices the bin amount changed and it keeps on going.”
For More Information : https://www.universal-robots.com/
BY Thailand Automotive Institute.
Toyota speeds up carbon-zero target for factories to 2035
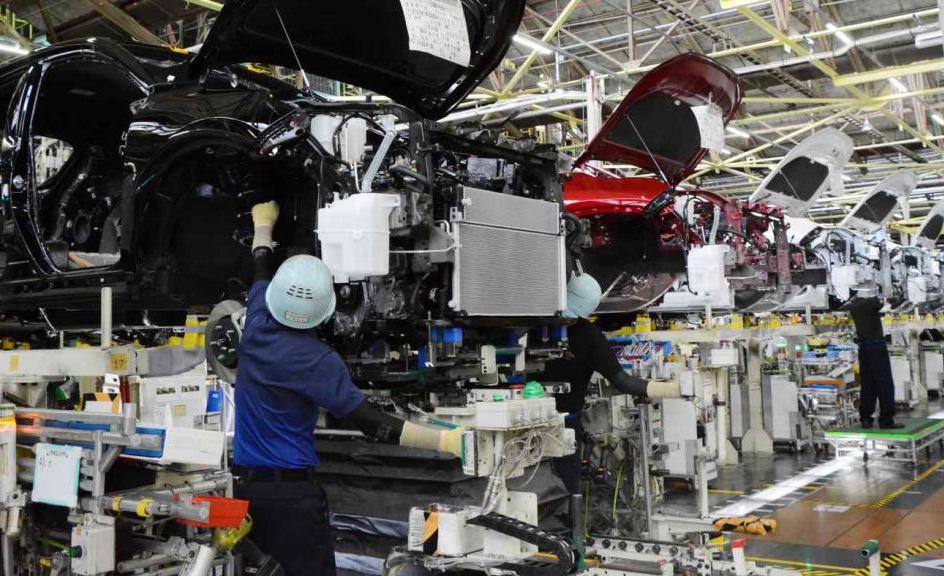
NAGOYA, Japan -- Toyota Motor has moved up its target year for attaining net-zero carbon emissions among group factories to 2035 from the previous deadline of 2050, the company said Friday.
The Japanese automaker will achieve this goal by adopting new technology in coating and casting processes, it said. The company will also step up its use of renewable energy.
“Achieving carbon neutrality through production processes will come to be the natural approach,” Masamichi Okada, Toyota’s chief production officer, told reporters in an online briefing Friday.
Okada said Toyota’s plant automation will increasingly take its inspiration from an old technology called karakuri. The concept was used to put mechanical dolls in motion with weights and gears. Now karakuri will be tapped to move equipment without consuming power.
The presentation showed a simple karakuri-based conveyance system that dropped off material at a production line.
“It is an example of an ultimate carbon-neutral piece of equipment,” Okada said. Given the situation, cutting carbon emissions within the entire supply chain, and not just at factories or through vehicle electrification, has become a pressing issue.
Toyota plans to sell 8 million electrified vehicles by the end of the decade, or nearly quadruple the current volume. By midcentury, the automaker aims to cut average carbon emissions by new vehicles globally by 90% compared with 2010.
The supply chain is making headway in decarbonization as well. Toyota has asked first-level suppliers of critical parts to cut carbon dioxide emissions this year by 3% compared with 2020. Outside of Japan, Germany’s Daimler plans to achieve carbon neutrality for its entire supply chain in 2039.
Looking at the global automotive landscape, the makers of luxury vehicles are taking the lead in cutting carbon.
Volkswagen seeks to halve the per-unit carbon emissions by vehicles under its eponymous brand by 2025 compared to 2015. The German automaker will have nearly all its European plants source the entirely of their electricity from renewable energy by 2023.
Volkswagen will apply that standard to all factories worldwide, excluding China, by 2030. For the Volkswagen brand, two factories have already attained net-zero emissions. Group company Porsche has achieved carbon neutrality in German plants.
BMW seeks to achieve net-zero carbon emissions at every plant under its umbrella this year. Per unit carbon dioxide emission during production will be reduced by 80% by the end of the decade compared with 2019. Mercedes-Benz plans to achieve net-zero emissions at global factories by next year.
Toyota will also purchase carbon credits from other companies.
Including group companies, Toyota factories emitted 5.68 million tons of carbon dioxide in 2019. However, Toyota plants account for just 2% of carbon footprint attributable to the entire life cycle of the automobiles, including raw material procurement, production, vehicle operation and disposal. Among Japanese companies, Nissan Motor will pursue carbon neutrality at all business activities, including factories, by the year 2050. The automaker has yet to disclose goals for each operational fields, such as production.