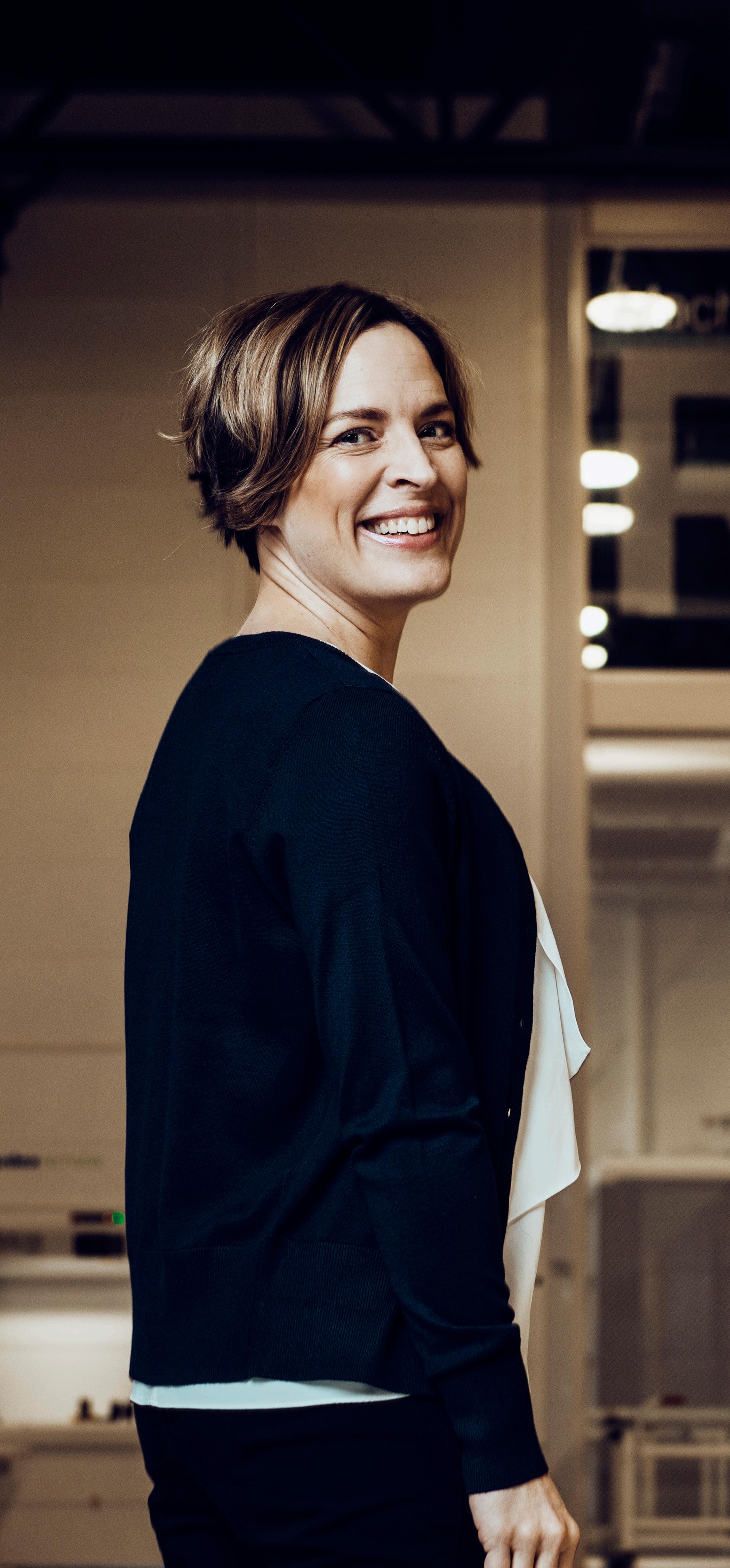
4 minute read
Sandvik
by Vivian Chen
Helen Blomqvist
Advertisement
President of Sandvik Coromant
With the COVID-19 pandemic, Our first priority is to safeguard our people, operations and customers from adverse impacts, putting people first is always our main concern. As we continue to navigate the pandemic, and with our global network of facilities, people and customers facing varied situations, Sandvik Coromant is carefully following guidance and taking the precautionary measures provided by health authorities and local governments.
We are a global company with production and distribution facilities all over the world. We are able to reallocate products between our production units to support the service of customer orders. We continuously assess inventory demand, raw material requirements, production capacity and logistics to assess and manage risks.
As many of us work remotely and from home, we’ve taken a digital-first approach in customer interactions and internal meetings. This includes using our Sandvik Coromant Center for live machining demos when customers cannot visit us in person, so that we can still deliver our expertise while we’re physically apart.
In the Digital Era, As a company, we recognize the value of digital tools and our responsibility to share this knowledge with our customers. Whether companies want to reduce their number of scrapped components, shorten set times or efficiently plan for machine tool maintenance, digital services can help reduce costs, increase productivity and aid better planning.
To support our customers, we’ve developed a robust, and growing, number of digital services. For example, our CoroPlus® software allows data is
to be gathered at both the machine level and tool level, which means that industrial tools can become ‘smart’. This allows tools to be adapted and adjusted at any time for more efficient use and to prevent production stoppages.
In addition, Sandvik Coromant has partnered with several industry players to support our digital acceleration. Last year, we announced the start of a unique venture with Microsoft to drive forward the development and digitalization of the manufacturing industry. Combining Sandvik Coromant’s expertise in machining with technical solutions from Microsoft, the collaboration will seek to link up parts of the production chain to create solutions for the next generation of manufacturing. The contract also includes an acceleration of the internal digitalization network for Sandvik Coromant.
Our facility in Gimo, Sweden also demonstrates our commitment to digital solutions. In 2019, Gimo was announced as a ‘Lighthouse facility’ by the World Economic Forum. It shares this title with just 68 other facilities around the world. Achieving Lighthouse status indicates our commitment to implementing Industry 4.0 technologies, and positions Sandvik Coromant as an exemplary manufacturer that can inspire the industry.
Sandvik Coromant adding value across customer’s value chain
We have been supporting and solving customers problems since 1942, and are present in 150 markets, with around 7,600 employees. As time has passed, our focuses have shifted and the value we deliver aligns with the challenges the industry faces today.
The greatest opportunity digitalization brings is the added value that we can provide to our customers, from design and planning, all the way to manufacturing and analysis. Helen Blomqvist

President of Sandvik Coromant
ourselves. We’re here to make it easier for our cus tomers to find the right tools, to buy them and to get support.
We will be launching several new products throughout the year in South East Asia and Oceania. In April 2021, we will be launching CoroPlus® Machining Insights, which is a cloud-based machining analytics software that can help customers increase overall equipment effectiveness (OEE) and other important parameters in a manufacturing facility. We’ll also launch CoroPlus® Process Control in South East Asia this year, which is a sensor-based real time monitoring system that monitors machining in real-time and acts according to programmed protocols if specific issues occur, for example by stopping the machine or replacing a worn cutting tool.
Together with other products for launch include CoroPlus® Tool Library Cloud, a software that can help reduce time spent making initial operations planning and programming. These solutions are applicable for all industries and we cannot wait to share them with our customers.
Ultimately, one of the best ways to share knowledge and gain value is to collaborate with others. We do this constantly, both globally and locally, with partner companies, institutes, schools, universities and customers. By working together, we drive continuous improvement and progress and, at the same time, meet the manufacturing challenges of today and the future.
It opens up new business opportunities for us as we can broaden our offering. We’ve always focused on the manufacturing part, but now we’re finding ways to serve our customers throughout their value chain. The data, the software and the technology are there. Our job is to identify how we can provide the most value in a profitable way for both our customers and