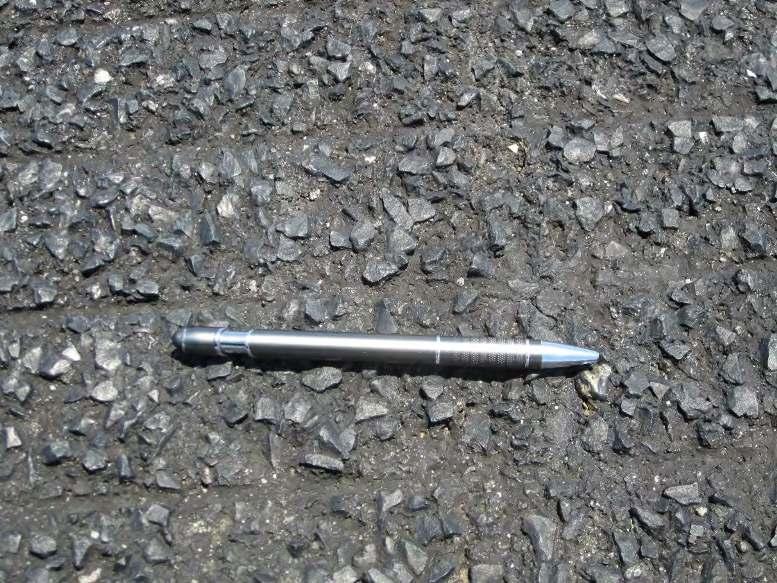
12 minute read
Emerald Airport Runway - Central Highlands Regional Council
EMERALD AIRPORT RUNWAY, REHABILITATION AND OVERLAY PROJECT - CENTRAL HIGHLANDS REGIONAL COUNCIL
Kerry Hayes Mayor of Central Highlands
The rehabilitation of a Central Queensland airport runway with ungrooved stone mastic asphalt is an award winning Australian-first project that became a valuable casestudy in innovation and collaborative management.
Emerald Airport is the 34th largest airport in Australia. Owned and operated by the Central Highlands Regional Council, this airport on the edge of outback Queensland, transports approximately 208,000 passengers per year and services the main business hub of Emerald and the Bowen Basin coal region.
The Queensland Government’s planning policy regards Emerald Airport as a strategic airport with a pivotal role in facilitating the state’s economic growth.
The airport provides for a broad range of industries such as agriculture, business, tourism, recreation, health services (including the Royal Flying Doctor Service and Angel Flight) and regular passenger transport
flights serviced by Qantas and Virgin Australia.
Emerald Airport is a securitycontrolled airport overseen by the Department of Home Affairs. It is also a certified airport, meaning that it must comply with all aviation safety requirements, similar to much larger airports.
Airport infrastructure investment could be described as ‘lumpy’; extended periods of routine maintenance are displaced by short periods of significant investment.
The Emerald Airport Runway – Rehabilitation and Overlay Project was commissioned after visual condition inspections, deflection testing, ground investigations, preliminary geometry review and technical analysis outcomes found the runway was several years past requiring attention.
The usual average runway life span is approximately 12 to 15 years. The historic 20 to 30-year life span is rare now because of the refinement of materials and stricter aviation safety regulations.
Built on black and reactive clay soils, the runway had deteriorated in several ways: oxidisation and deformations, wearing course and grooving erosion. It was uncommon to move from one groove floor to the next without encountering a height change.
Early rehabilitation efforts focused on the runway ends that showed significant failures.

The ridges between these grooves should be at least half (or more) of the pen’s height.

Turning node deformation. The runway had given way under the weight of slow-moving aircraft turning and lining up for take-off. During construction, machines were at risk of being bogged once the asphalt layer was stripped off as a result of uncontrolled moisture ingress.
Crown on the northern side of the runway (darker colour indicates higher areas).
This project formed part of a larger works program managed by the airport and the same project team. 24-hour works for several months resulted.

A number of approaches were generated as part of an investigation aimed at ensuring that the works would address shortcomings in the runway. Although this process delivered technically acceptable solutions, council was concerned that the traditional approach may not deliver great value for money.
A peer review of runway condition reports led Dr. Greg White of the University of the Sunshine Coast to conclude that the problems were widespread across the entire runway. An approach was needed to resolve the failures and future-proof the runway within council’s budget.
The runway project also had to be a 24-hour operation that did not disrupt aviation while it maintained continuous safety, security and operational compliance.
Ungrooved stone mastic asphalt (SMA) was identified as a solution. No other airport in Australia had used this product on a runway giving rise to initial industry scepticism.
Rather than blanket corrections, a combination of deep excavations, rock mattresses and shape-correcting were applied and subsequently covered with a SMA wearing course.
One cost-effective solution was to add a wider non-loadbearing asphalt apron around
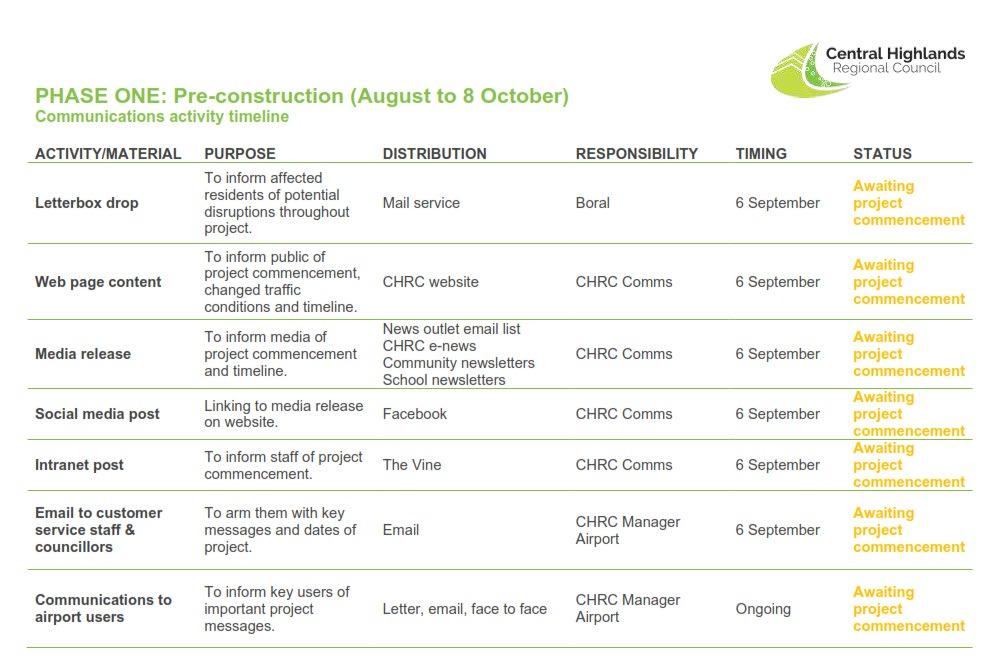
Part of the high-level project communication plan prior to works starting. The above draft was prepared prior to the project go-ahead given by airport management.
Asphalt pavers paving the first run of the runway strip in a specially constructed mud-mix. No rolling or wetting was required. Note the joint heater (not in use) carried by this machine for asphalt work, should joint temperature fall faster than desired.

areas where the runway and turning nodes have an ingress of moisture. This was an alternative to excavating the base and sub-base because the clay soils performed well under load tests while dry.
In addition, legacy issues resulted in a wandering crown. It was decided that, to the extent possible, this matter would be addressed by a combination of localised profiling and a corrective layer. SMA production and construction is more expensive than dense graded asphalt (DGA). A detailed life cycle cost analysis using international data showed that, because of SMA’s higher binder content, rejuvenations would need to be less frequent and courser aggregate should last five to ten years longer than a DGA runway. Consequently, despite higher upfront capital investment, the whole-of-life cost is expected to be lower. SMA is well established as having a greater anticipated service life as evidenced by research from the United States, previous trials at Cairns International Airport aprons (Jamieson & White 2018) and Sydney International Airport taxiways.
SMA has an annual depreciation rate that is 25% lower than DGA based on an expected four-years longer service life associated with the SMA. Considering the cost, it was also evident that if the SMA service life is only one-year longer than DGA, then annual depreciation is still lower for SMA than DGA.
Considering the challenges and risks, the council needed to ensure that the contractor could demonstrate measurably on site and deliver on the brief prior to commencing the SMA-based works.
Council requested submissions for both SMA and DGA treatments. That way should production or construction not meet expectations the work could go ahead in DGA. The wearing course’s laying down was planned to provide the opportunity to gain more time for information gathering from the SMA test strips, especially the development of friction, before authorising SMA construction.
Council was assisted by local firm George Bourne and Associates throughout the project’s development and procurement phase. During delivery, they were joined by a number of other expert firms such as GHD and Boral to deliver this Australianfirst project.
In addition to the usual concerns, risks and considerations, the fact that the runway must be returned to serviceable condition (complete with working lights and paint markings) at short notice was front of mind. Prior to Boral coming onsite, every night’s work was planned in detail.
Start and end times of every trade, team and action was mapped months in advance. For

Corrector plus SMA layer thickness. This gives an indication of the relative original high vs low spots.
Test patches about to be constructed.
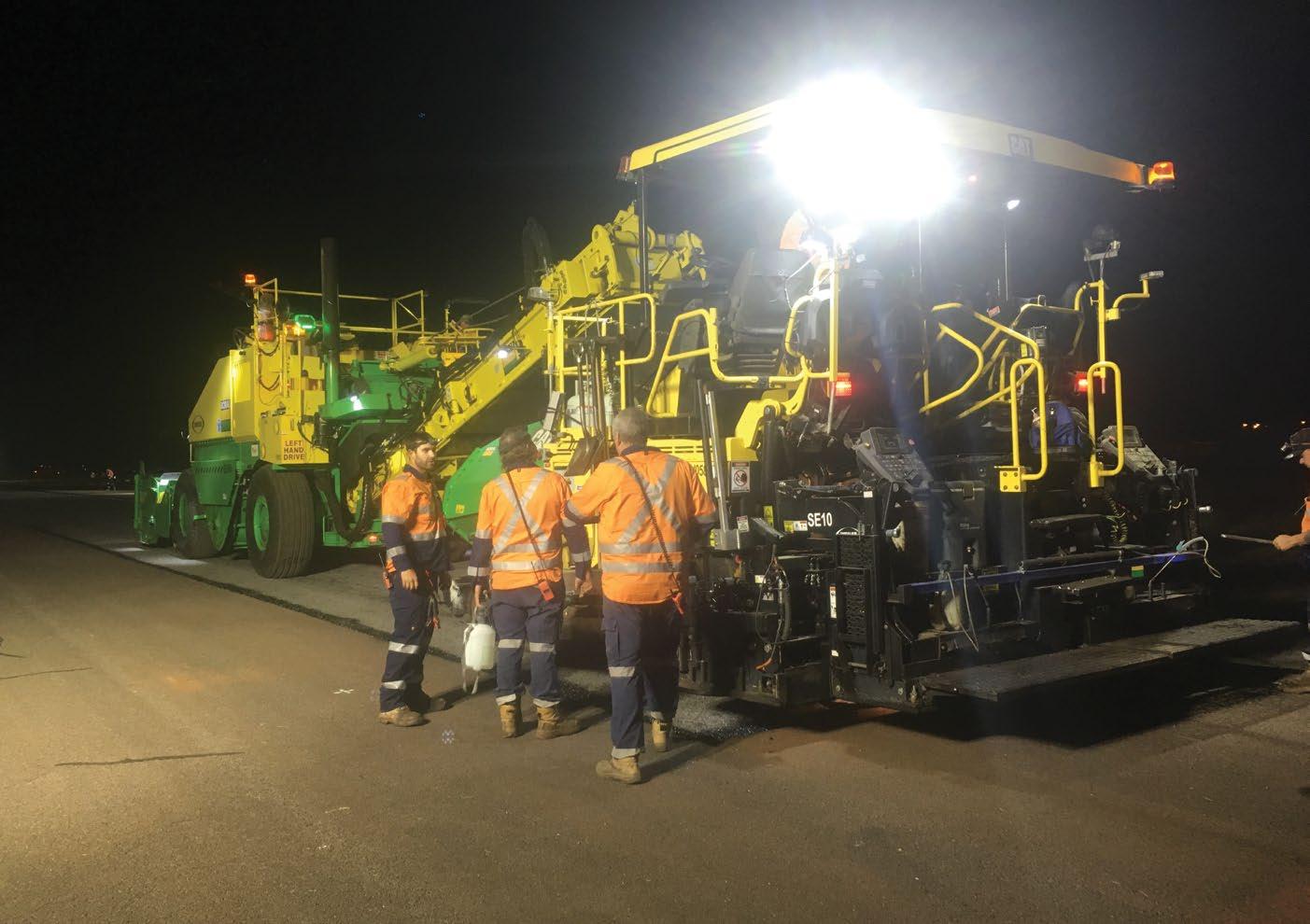
instance, excavations could not be done before enough asphalt was ready to fill the excavation (mitigating the risk of plant break-down).
The quantity and time that an amount of asphalt should be ready was planned based on the size of excavation. Because SMA has a short shelf-life, the exact time that the geofabric team started building the mattress was specified so that the paver could start and complete the pavement run prior to the SMA being drained of binder.
Electrical crews had to remove runway lights and re-install them after works and civil crews had to bring the strip width up to compliance (levels, slopes and grade changes managed to within .10%).
Council also established a consensus-based, multidisciplinary self-managed project team to plan details and manage the project. This team also reviewed the live test data (onsite NATA lab), autopsies (shifts past) and planning for shifts (shifts future). Live test reports confirmed that the methodologies and scope were communicated to the project team by an independent engineer present during the night construction.
As the main contractor, Boral provided an onsite senior manager to interact with airport management, the project, and head office on matters identified. Throughout the works, airport staff were onsite with an independent engineer’s oversight, verifying that the methodology was followed throughout the entire project.
Airport staff also conducted works and compliance inspections every morning from around 4.00 am, ensuring that crews could fix issues of concern before day operations commenced.
The night staff had access to offsite resources at any time during the night. Any person could stop works if uncomfortable with an element of the project; this would trigger an ‘all-stop’ with the project team meeting onsite to resolve issues. Although used sparingly, this did result in a few potentially unfortunate situations being avoided; matters that would have been unknown to day staff.
The project involved the relocation of a unique asphalt plant on to the site. The size of this plant was specified to not be too large. Although cost-effective, large plants deliver minimum amounts of asphalt that would have impacted negatively on the shelf-life of the SMA considering the placement specifications.
A quality control regime was set up and stockpiles managed with the local Shepton Quarry. An onsite NATA accredited laboratory allowed real-time testing of production samples and core testing only minutes after being laid and compacted giving feedback to the production and construction teams on mix, binder and roller passes. When read with results from nuke testing, void measurements and continuous level surveying looped back to the GPS controlled machines.

Airport management set specific targets for skid resistance. The project met these on the first morning. This shows quality in specification, design, production, and construction. The above relate to the entire project at completion. Low friction numbers are mostly isolated to the moisture protection flanks and turning nodes.
Isolated bitumen rich areas prior to construction methodologies being amended in a data driven manner.
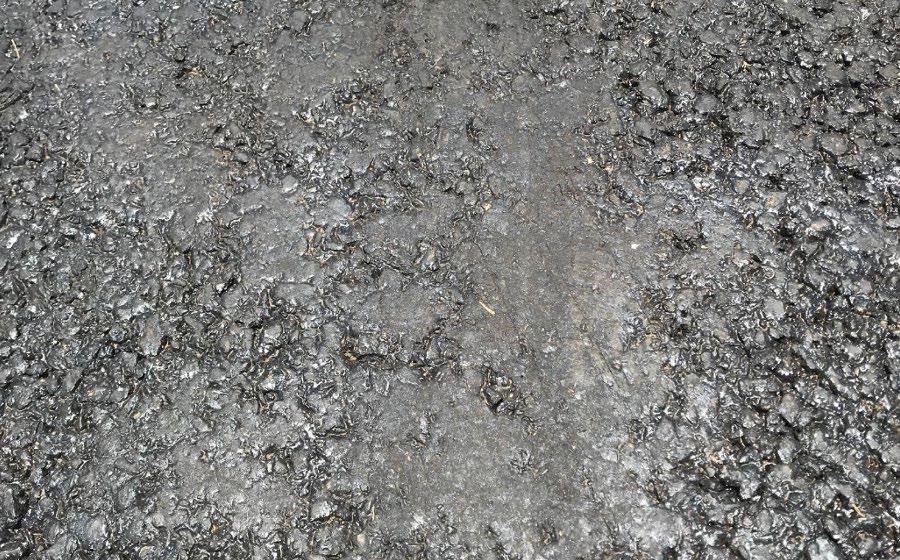
Several innovative steps, methods and processes were created throughout the project including:
• Senior leadership from each contractor was appointed to a project governance group before commencement.
Airport management used this opportunity to ensure there weren’t any misunderstandings for the project’s duration. This group proved invaluable as a forum to strategically discuss allocating additional and different resources separate from the management team that focused on operational and technical issues. • Bespoke flanking mixes with different soil types were made and incorporated with asphalt pavers in the strip (dirt area next to the runway) with numerous tests completed onsite.
• Excavations did not commence until asphalt had been produced and loaded in case of a plant or shute break down. No excavation could be started if the plant and materials were not within reach to fill it again.
• A new understanding was formed of the range for lime content in SMA for airports. • A new understanding was formed regarding the thickness that asphalt can be paved and how its qualities (and compaction) change due its thickness.
• Development of friction from various types of asphalt surfaces (test strips paved ahead of project commencement and friction tested periodically onsite to understand how friction changes over time) was completed in conjunction with engineering students from the
University of the Sunshine Coast.
• A lot-system to control the quality of aggregate was introduced by the project team at Shepton Quarry. This meant that a specific patch on the runway could be traced back in constituent parts to the production batch, the load from the quarry and the individual stockpile enabling the project to reduce variability that would have only become apparent during testing
The Emerald climate, which can have a range of temperature from below 10 to 40°C+; has prolonged periods of drought (with clay shrinkage); and significant wet events (resulting in expansions), presents one of the least runway-friendly environments in Australia.
This project was used as a pilot to demonstrate that ungrooved SMA is a viable alternative to grooved DGA for runway surfacing in Australia.
SMA is not perfect; inexperienced contractors can easily cause many negative outcomes. Of these, airport management highlighted friction loss as a particular aviation safety risk.
To address this, two patches (SMA and DGA) were established on the Emerald Airport cross runway to act as test beds to signoff on mixes, production, and construction methodologies.
SMA skid resistance compliance was achieved immediately following construction; a
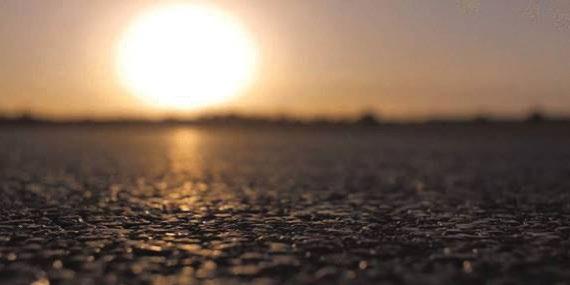
The morning light shows freshly laid SMA.

Work crews await the outcome of a runway serviceability inspection.
significant advantage over grooved DGA, which usually does not achieve compliance until grooves are sawn some four to eight weeks later.
Exhaustive testing showed superior performance of SMA. It would take the DGA patches months to reach the friction levels of four-hour-old SMA (and improving).
The project incorporated much more than delivering an SMA runway. It also included taxiways, aprons, and a complete excavation, reconstruction and extension of the general aviation apron.
SMA looks and reacts differently to DGA. As an example, the seeming movement of individual stones in the top layer of green SMA when agitated raised concerns at first with airport staff, but conventional and unconventional testing showed this not to be an issue.
Localised fatty spots were observed occasionally at the start of paver runs and dealt with when construction procedures were amended (including keeping mixes longer in shuttle buggies rather than in pavers). This proves that, although comparable, experience with road SMA is not directly transferable to airports and will stand Boral in good stead in future.
The superiority of SMA over DGA has been independently tested and verified along with financial benefits due to longer periods between the need for intervention and rehabilitation. This less intensive intervention is expected to deliver significant financial savings to the council and therefore the community.
Engineering and financial performance (measured and academically reported) makes this project worthy of consideration for all airports and airfields in Australia.
For more technical analysis on the project, we urge anyone to seek out Dr. Greg White and Hayden Dutney’s paper to be presented at the 11th International Conference, on the Bearing Capacity of Roads, Railways and Airfields, Trondheim, Norway, 28 - 30 June 2022. (www.ntnu.no/bcrra/).
The paper has been accepted-inprinciple, based on a previously submitted and peer-reviewed abstract. It is titled Stone Mastic Asphalt as an Ungrooved Runway Surface: Case Study on Emerald Airport.
Boral also host a special project page on its website: www. boral.com.au/projects/emeraldairport-upgrade and a similar YouTube video at Emerald Airport Resurfacing Project - YouTube
The project has won several awards, including the AAPA Outstanding Project Award for projects of its size as well as the IPWEAQ Innovation Award.
ABOUT THE AUTHOR
Born and bred in the Central Highlands, Mayor Kerry Hayes has owned and operated the Emerald Land and Cattle Company for more than 30 years and been active in the region’s local government since 1997. His drive and passion is to promote and enhance the Central Highlands to its full potential.
As Chair of the Central Highlands Development Corporation, Cr Hayes firmly believes investment in quality infrastructure will ensure the region sustains its reputation and attraction as one of Australia’s most progressive regional agricultural and mining resource hubs.