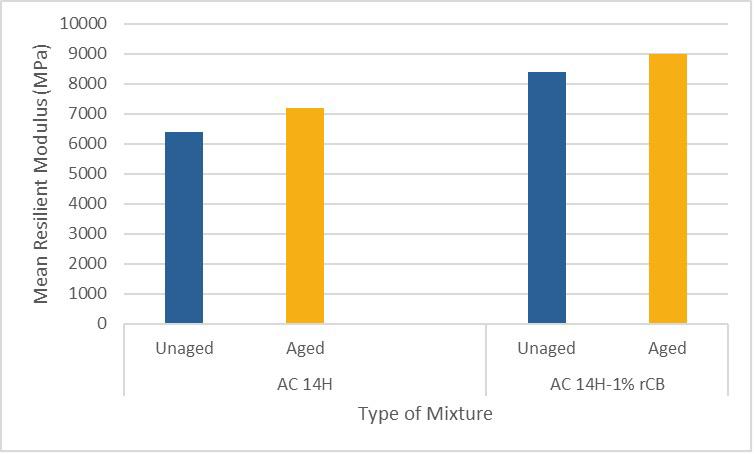
7 minute read
Enhanced Properties and Performance of Asphalt Mixtures Incorporating Recovered Black from Repurposed Passenger Vehicle Tyres
ENHANCED PROPERTIES AND PERFORMANCE OF ASPHALT MIXTURES INCORPORATING RECOVERED CARBON BLACK FROM REPURPOSED PASSENGER VEHICLE TYRES
June Njogu PhD Candidate, School of Civil & Environmental Engineering, Queensland University of Technology
David Simmons General Manager, Austek Asphalt Production
Chaminda Gallage Associate Professor, School of Civil & Environmental Engineering, Queensland University of Technology
Waste tyres, including passenger car tyres, create significant environmental issues when they reach the end of their life and are disposed into landfills.
Tyre recycling is one of the solutions to these environmental issues; however, only certain tyre types, such as truck tyres, are preferred by most recycling techniques. Two local Queensland companies have in combination discovered a unique process to break down the waste tyre into usable products via a process known as thermal desorption. The thermal desorption process to extract fuel from tyres is an innovative technique to recycle all types of tyres, including and especially passenger car tyres. The Recovered Carbon Black (rCB) is a by-product of this process. Due to its limited usage, it is immediately accumulated after production and research is therefore needed to investigate possible applications to make the recycling process even more sustainable and environmentally friendly.
The rCB can be used as a mineral filler in asphalt mixtures, to replace a portion of fine aggregates, resulting in increased sustainability and performance of pavements.
Background
Every year more than 56 million tyres reach their end of life in Australia. More than 60% are landfilled, stockpiled, illegally dumped, or ‘lost’, adding to a global contaminated waste problem. Queensland generated approximately 12 million equivalent passenger units of end-of-life tyres during 2015–16, of which only 14% were recycled (Randell report, 2017). As tyres are built to last, they are not naturally degradable or easy to treat and therefore if not managed properly, end-of-life tyres can create economic, health and environmental issues.
The different recycling methods include re-treading, reclaiming, combustion, grinding, and pyrolysis, each with its advantages, disadvantages and different end products being obtained. Pyrolysis involves thermal degradation of the waste tyre in the absence of oxygen. The recycling method enables truck, passenger, motorcycle, forklift, bicycle tyres etc to be utilised, and valuable end products such as tyre oil and syngas to be generated. After the oil and ash removal process from tyre pyrolysis, a high-purity commercial carbon black is obtained.
The Product
Carbonphalt® (Austek’s registered trade name) is Austek’s proprietary dense grade asphalt mix design incorporating rCB as a filler material, for enhanced performance properties while providing environmentally friendly and sustainable benefits. The tyres used in these mixes are exclusively sourced from local Queensland council waste facilities and sources.
The recovery process used by Queensland tyre recycler, Pearl Global,sees every component within the tyres, recycled and reused. The shredded rubber tyres go through a series of heating chambers, the steel is removed, the fibres are taken out and the rCB is left. The thermal desorption technology adopted by Pearl Global produces rCB with a carbon content of approximately 80%. This offers a sustainable alternative that can replicate, to a reasonable degree, the properties of virgin carbon black.
Working in conjunction with Pearl Global, Austek Asphalt production have developed systems to allow the incorporation of both rCB and tyre derived fuel oil into their production of asphalt mixes. The rCB is added to the pugmill with the heated aggregates and hot bitumen to produce rCB modified asphalt mixes. While the tyre derived fuel oil is used to replace diesel that dries the aggregates in the mixing drum. By so doing, 10 passenger vehicle tyres are reused in every tonne of rCB modified asphalt produced by Austek.
Case Study
In July of 2021, Austek in collaboration with the City of Logan and Tyre Stewardship Australia conducted a sideby-side comparison trial of the innovative Carbonphalt® asphalt mix by resurfacing a section of pavement on Miller Road, Logan Village. The project stretched over 410m in length in both carriageways. The first 200m was paved using conventional TMR AC14H C320 mix, and the remaining was paved with Austek’s Carbonphalt® mix, incorporating 1% of rCB.
The test method was designed to directly compare and highlight the differences in performance and benefits between Carbonphalt® and the conventional Queensland Department of Transport and Main Roads (DTMR) asphalt mix. The project was also aimed to provide a continual specimen for examination, where the longevity and field performance of the two asphalt mixes could be monitored over an extended period.
The Outcome
Figure 1. depicts the resilient modulus values obtained for unaged and aged specimens of AC14H-320 and Carbonphalt® (AC14H – 1% rCB) mixtures at 25°C.
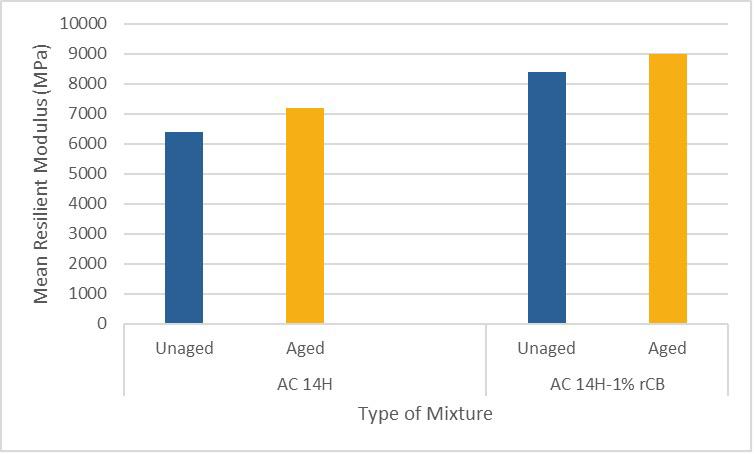
Figure 2. The calculated strain at 1,000,000 cycles for the AC14H and AC14H – 1% rCB mixes

The Australian Road Research Board (ARRB) were engaged to conduct the sampling at the job site, and the laboratory performance testing. All the 100mm cylindrical test specimens for the resilient modulus tests and fatigue beam specimens were prepared using the gyratory and slab compaction methods respectively, achieving the target air void content of 5±0.5%.
To simulate the field ageing of asphalt, some compacted specimens (for both mixture types), were conditioned at 85°C for 120 hours in accordance with AASHTO R30.
In general, both mixtures showed a similar trend with aged mixtures having slightly higher resilient modulus compared to the unaged mixtures. (As the asphalt hardens or becomes stiffer, the strain is reduced thus leading to an increase in Resilient Modulus).
The resilient modulus of the Carbonphalt® (AC14H-1% RCB) is 25 % - 31% higher than for the AC14H mix in the unaged and aged samples respectively.
Further, fatigue performance of Carbonphalt® AC14H – 1% rCB mix increases with ageing while there’s a reduction in performance in the AC14H mix.
Figure 2 shows that as expected, the performance of AC14H reduces with long-term ageing. As the stiffness increases, the fatigue life reduces and therefore a lower strain level of 137 µƐ at 1,000,000 cycles. Interestingly, the fatigue life of the AC14H-1% rCB mix shows a longer fatigue life in the aged mix. Given the vagaries of fatigue testing, even with the voids and temperature controlled to +/- 0.5% and +/- 0.5˚C, there could be some subtility in the voids and temperature influencing the results and therefore further investigation is needed.
The improved performance 1% rCB modified mixtures could be due to the difference in structure and morphology of rCB compared to lime, with rCB causing a more locked up aggregate skeleton. The chemical composition of rCB could also influence the bitumen, improving the adhesive bond between aggregate and bitumen.
Market Penetration and cradle to grave reconomy.
The introduction of rCB to the asphalt products has not only produced a massive step forward in finding an end use for problematic passenger car tyres but has proven that the performance of the asphalt produced is delivering higher modulus, higher Kn strength, improved resistance to moisture susceptibility, better compaction in the field and superior safety attributes via colour retention Combining rCB and the tyre derived fuel oil from Pearl Global’s unique world first processes, Austek Asphalt production is reducing its carbon footprint by 42kg/ Tonne of Co-E2 in every tonne of asphalt produced. This equates to 10 passenger vehicle tyres being repurposed in every tonne of asphalt produced delivering a true circular economy.
To date, over 25,000 Tonnes of Carbonphalt® has been successfully delivered to over 7 local supporting councils in Southeast Queensland.