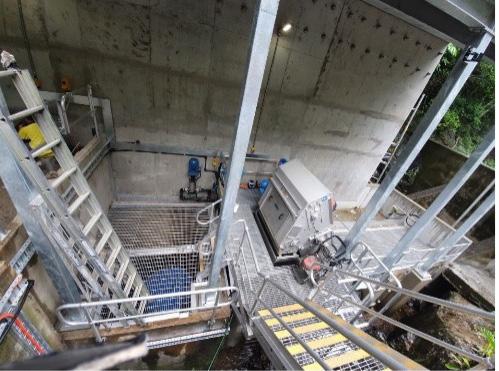
6 minute read
Crystal Cascades Intake Upgrade Project
Travers Boland Northern Australia Water Market Leader, GHD Pty Ltd
Peter Thoren Principal Engineer Design & Delivery, Cairns Regional Council
The Crystal Cascades Intake is the primary water supply point for Cairns and feeds the Freshwater water treatment plant. To improve water quality and address safety issues that had been identified at the intake site Cairns Regional Council (CRC) commissioned GHD to collaborate on the Crystal Cascades Intake Upgrade Project.
The solution created by the team centred on four considerations: careful material selection to ensure feasible delivery to a difficult site with minimal disruption to the environment; structure performance to protect Council crews against potential rock fall events; a temporary bypass strategy to enable uninterrupted water supply to the community while constructions crews worked; and site flooding enhancements to assist with future flood recovery at the site. The water quality of the Cairns community was improved with the provision of new mechanical belt screens, while the safety of the CRC operators and maintenance teams was increased with a site structure that combined the strength and durability of concrete with the absorbing properties of sand and soil via anchoring to the native rock. The collaborative approach was invaluable as the experience and knowledge of Council operators and maintenance teams ensured that the solutions aligned with potential events and future needs of CRC and the Cairns community.
The Crystal Cascades Intake Upgrade project was a collaborative project between Cairns Regional Council (CRC), GHD and NQEF to deliver: 1.) improved water quality through the provision of new mechanical belt screens to the
Crystal Cascades Intake; and 2.) increased safety for Council operators and maintenance crews from potential falling rock debris. The area is prone to falling rocks that can cause damage to traditional structures.
To address these two criteria, the entire project team worked collaboratively to develop an optimal outcome. The experience of operators and maintenance crews regarding past events and future needs was particularly beneficial to the project.
The team resolved five key issues: 1. screen type to achieve desired water quality 2. structural performance of the new facility 3. access and materials selection 4. facility improvements based on lessons from past flood events 5. temporary bypassing to accommodate construction
Screen type to achieve desired water quality.
The designers, operators and management team undertook a collaborative multi-criteria analysis (MCA) with weighting by pairwise comparison on a comprehensive range of mechanical screening technologies. The technology assessment included the screen’s ability to achieve the desired water quality, appropriateness to retrofit within the confines of the existing raw water channels and ability to traverse the access track for either installation or future maintenance. The team determined that a double pass band screen (or belt screen) was the appropriate choice for the Crystal Cascades facility.
A fault tree analysis of the complete screening facility was undertaken to ensure appropriate levels of redundancy and to understand constraints within the proposed system.
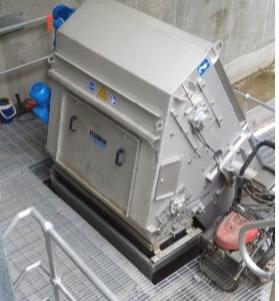
Careful observation of the existing facility to ensure structural performance of the new facility
Providing the facility with a shelter that offers operation

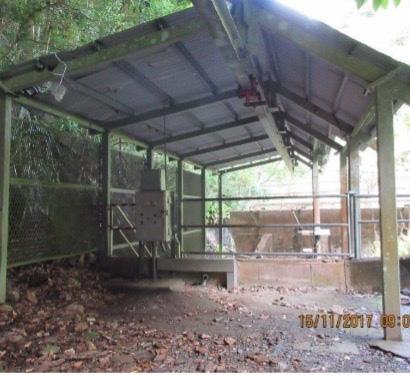
Final Facility
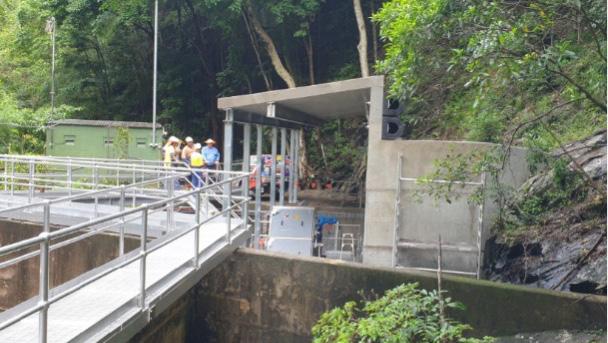
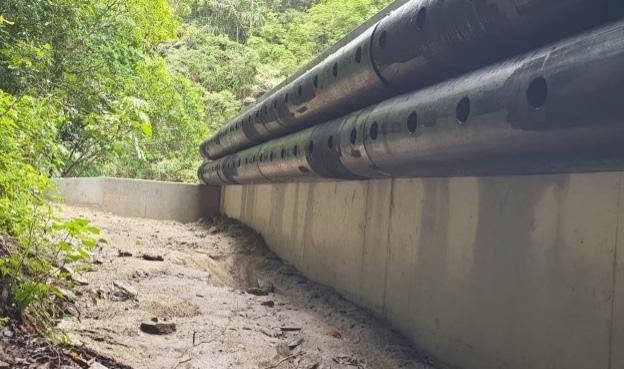
and maintenance crews with improved protection against potential rock fall events was a fundamental objective of the facility improvement. Steel and netting rockfall solutions were assessed but determined to be unsuitable.
Although a steel structure would have been the easiest solution to construct in an access confined site, the existing expanded mesh and steel portal structure was compromised on numerous previous occasions.
Dense vegetation (additional organic debris that requires removal), increased maintenance, and further exposure of Council staff to rockfalls eliminated netting style rockfall protection systems as a suitable option.
After numerous iterations, the team settled on a bespoke solution. The structure combines the strength and durability of concrete anchored into the native rock with the absorbing properties of sand and rubber fenders behind the wall.
Access and material selection
Careful selection of materials was essential to ensure feasible access to the difficult site and limit impact on the pristine environment.
The access path to the site is: a) visited by hundreds of tourists every day. Maintaining
safe pedestrian movement throughout the access track was non-negotiable. The entire team also developed methodologies and safety systems that allowed this tourist attraction to remain open to the public. b) narrow. The track was built for light vehicle access and in places is less than 2.5m wide. c) steep. The track’s heavily broomed concrete finish is greater than 35 degrees in places. d) sharp corners. In some locations corners are greater than 90 degrees with valve pits and other obstructions such as rocks, trees, and guard rails.

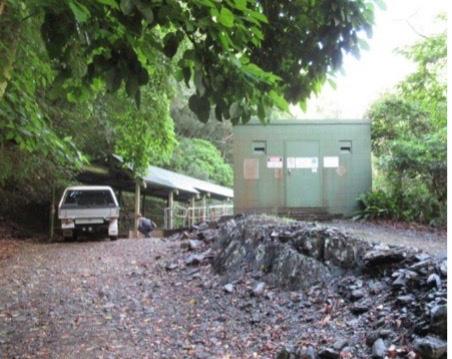

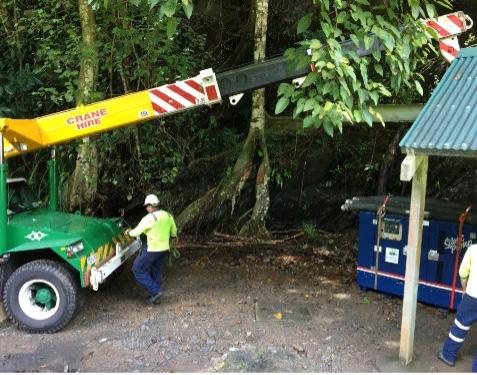
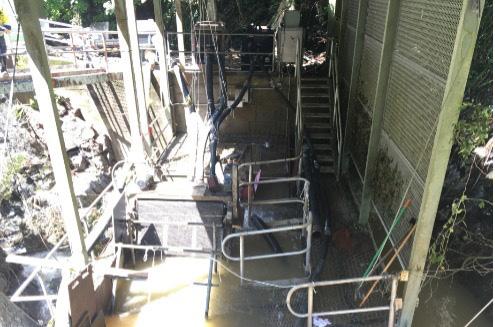
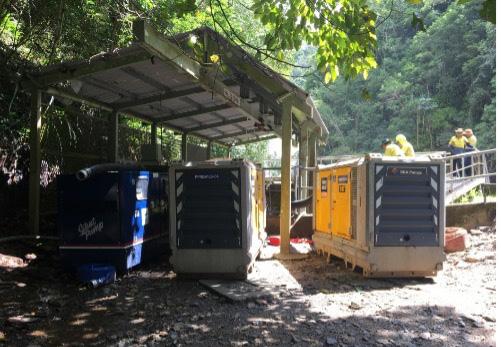
e) long. Access to site is via concrete paved track approximately 2 km from the
Crystal Cascades main car park.
GHD (designer), CRC (client), and NQEF (contractor) worked collaboratively to manage these risks with bespoke project equipment, including modified narrow bed vehicles to transfer concrete and other equipment to the site. This negated the need to batch concrete on-site, improved quality, and reduced environmental risks.
Facility improvements based on lessons from past flood events.
The site is susceptible to turbulent flood waters, as was evident during the design phase where a significant rainfall event caused damage and debris buildup at the site. As a result, the GHD and CRC teams were able to determine that: a) flood water impact handrails at all angles at Crystal Cascades, therefore collapsible handrails are not practical. Furthermore, replacement costs did not warrant inclusion. b) if required a 15t mobile crane could get to the site. A 20t crane was not able to traverse the constrained access track. c) diesel pumps are a short-term solution, but do not keep up with “normal” demands.
They could only be set up at the carpark, not at the weir, therefore would clash with the proposed construction works. Refuelling also risks spills and release in a pristine environment.
Enhancements incorporated into the design to assist with future flood recovery events, included: a) improved drainage around the screens for simplified clean-up. b) penstocks to allow flushing of sands/grit/gravel deposited upstream of the screen during a flood event without entering the channel. c) elevation of platforms from existing levels. d) CCTV monitoring of screens.
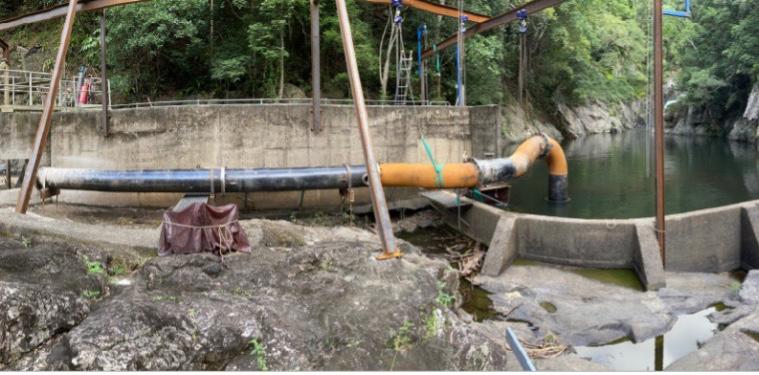

Temporary bypassing
Establishing a bypass strategy that allowed the construction crews ample time to perform the works was a fundamental requirement of the project. Key to the bypass strategy was to: a) ensure that an uninterrupted supply of water (700-900L/s) was provided to the Freshwater
Water Treatment Plant. b) prevent air from entering the raw water main due to the risk of water transients and impedance on downstream flow control valves. c) negate the use of mechanical equipment wherever possible to limit the risk of fuel spills to a sensitive environment and tourist attraction. Additionally, past flood events had identified that diesel pumps could not be set up at the weir due to their weight and limited crane access to the site.
GHD developed a nonmechanical syphon solution. Working collaboratively with NQEF and CRC operations, the entire team implemented a system that was screened, stable, cost efficient, environmentally friendly, and low maintenance in its operation.
The ultimate test – another flood!
Shortly after completion, the facility was stress tested by a flood event of a similar magnitude to previous years. The facility was largely unaffected and was brought back on-line quicker than ever before.
Acknowledgements
Keith Shephard (GHD), Arthur Ahiladellis (GHD), John Gammie (NQEF), Jonathan Ward (CRC), John Bishop (CRC)