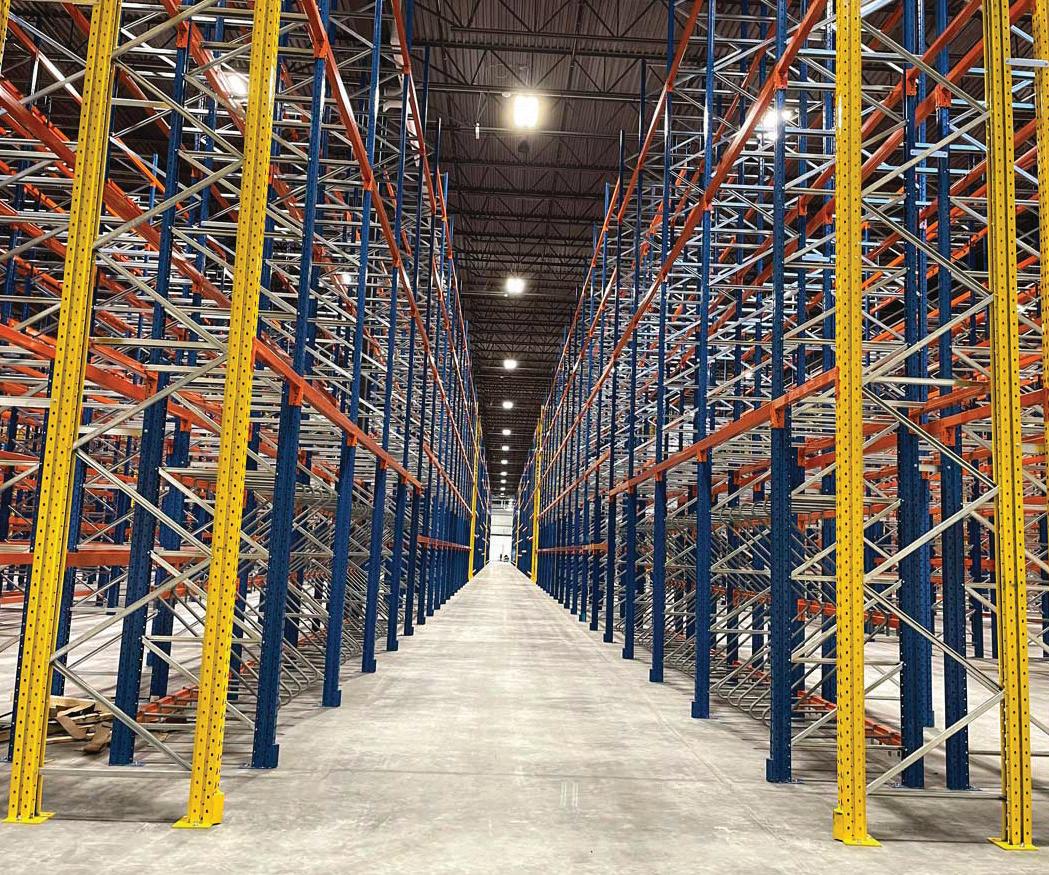
4 minute read
SMOOTH RUNNINGS
hazardous waste, there is more scrutiny when processing oil-based products. It’s essential to use licensed waste management companies to collect and dispose of used lubricants due to the growing customer interest in sustainability and the strict regulatory guidelines and associated fines.
For bearings and lubricant purchasers, align the application with the material. As demonstrated above, each material provides a different level of load applications, temperature tolerances and durability that can impact its overall performance.
Additional best practices include development of a lubrication program and having a proper storage system. For a lubrication program, identifying each component’s unique needs is paramount. These can include types of greases versus oils, along with how often bearings are lubricated. In addition, ensuring that training is included in the program is critical so that correct procedures are followed for maintenance, usage and inspection. All of this contributes to equipment longevity and employee safety. Too much or too little lubrication can impact friction levels, which can cause excess wear and tear or accumulation of dirt and debris, leading to higher temperatures.
There is a balance to identifying correct lubrication levels and frequency. A well-organized and labelled storage system is critical in ensuring the correct lubricants are used, especially when bulk lubricants are packaged in similar formats, confusing users that don’t reviewing the labelling carefully.
Organization and labelling can also help inventory management, as properly labelled inventory can be easily identified and accounted for instead of ordering unnecessary inventory due to poor storage practices. Adequate storage space is key in a lubrication program. This can include criteria such as indoor versus outdoor space or covered versus uncovered spaces. These can help maintain lubricant performance due to temperature changes, water exposure or contact with light.
The bearing and lubrication industry is not immune to the global supply chain issues started by the COVID-19 pandemic. Like others, the industry faced raw material and labor shortages, since early on they were directed to produce more urgently needed products like PPE or other healthcare and medical devices. These shortages, coupled with escalating freight costs, drove not only massive price increases but exasperated the situation as organizations would order more than they needed to hedge against any future supply chain issues. This caused a demand cycle that outpaced supply.
There are possible alternatives to mitigate supply chain challenges, including researching substitutions. Pivoting between different suppliers or products offers flexibility to smooth out price swings as well as mitigating product shortages, which is critical in many JIT industries like automotive.
Bearings and lubricants have progressed in performance and material structure, in part due to performance requirements and changing customer expectations, as well as partially due to long-term supply chain concerns. Although a relatively simple component of a much larger system, the bearing and its associated lubricants remain vital to many industries, from energy to automotive to warehousing and most everything in between. They will continue to adapt as market demands shift and new technologies arise. SP
BY NOELLE STAPINSKY
SMART MOVES
ROBOTICS AND AUTOMATION HELPS BOOST LABOUR AND MAINTAIN A RELIABLE THROUGHPUT
Automation has been a key part of logistics for decades—albeit early adopters have mainly been Fortune 500 companies. In the past few years, however, there have been advancements in robotic and automation technology, which has lowered investment costs, making it a more attractive option for any size of operation. Is it the race toward Industry 4.0? Or has this uptick been a result of the pandemic? Industry experts say that it’s a bit of both.
Regardless of an operation’s size, labour has always been an issue and the pandemic has accentuated it more. Not only is there a manual labour shortage, but the reliability of the workforce that might be attainable is also a big uncertainty for many companies.
“There has been a spike in interest as a result of the pandemic, but I think it created a realization, for a lot of companies, about the vulnerabilities that they have and problems they were aware of before COVID in terms of processes that were entirely manual,” says Ryan Weaver, vice-president, Commercial at Robotiq.
Markus Schmidt, president of Swisslog, agrees. “Not knowing if your workers are going to come to work, during a pandemic or not, has been a nightmare for everyone in the supply chain, not to mention labour costs keep rising,” he says. “The more you can automate, the more independent you become of those conditions. The other issue is that supply and demand is out of control.”
Certainly, customer demand and experience expectations have drastically changed.
“When Amazon started offering Prime delivery, that was a huge accelerant to all the automation that’s being adopted. They started to use the fulfillment experience as a weapon rather than just reducing costs. And that’s driven a lot of innovation and pushed everyone forward,” says Leif Jentoft, co-founder and chief strategy officer at RightHand Robotics. “In the past five years there has been an explosion in goods-to-pickers systems like AutoStore or OPEX for auto storage and retrieval. This is interesting because you can increase the storage density, increase the facility throughput, and scale your businesses, even in the face of labour shortages. But what we’re seeing is that’s still not enough for companies to deliver a customer experience or meet demands. What people are looking for now is the next step in the process, which is picking and placing, and that’s where we live.”
ARTIFICIAL INTELLIGENCE
RightHand Robotics’ RightPick platform is a turnkey modular solution that uses artificial intelligence (AI) to learn as it picks products. “We focused on the piece level. It’s not cases or pallets, but individual items that have variations from one piece to the next. Like picking up your sunglasses and then your phone or