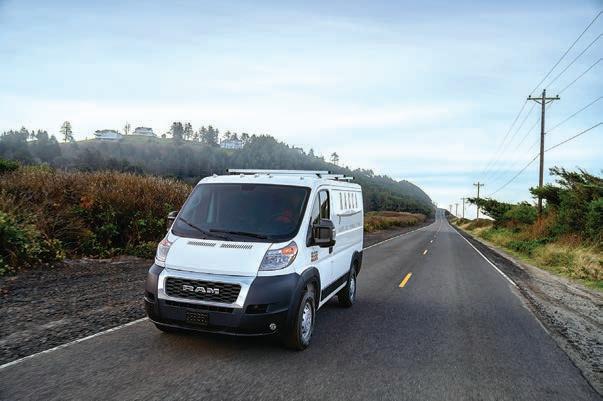
22 minute read
PROMATDX
BUILDING BEYOND COVID-19
DIGITAL EVENT PROMATDX FOCUSES ON RESILIENCY, INNOVATION
The venue may have been digital, but that didn’t stop over 17,000 supply chain professionals from attending ProMatDX, MHI’s annual manufacturing and material handling show. The online event, held April 12-16, saw attendees learn about supply chain equipment and technology innovations.
Among the keynote discussions was Beyond COVID-19, a panel focusing on lessons from the pandemic and building resiliency.
Panelist Carmela Hinderaker, senior director of business continuity and customer support at C&S Wholesale Grocers, said that resiliency for her organization meant ensuring stores receive their orders within a window of 12 to 24 hours. For fellow panelist David Lusk, director, FedEx Global Security Operations Center, resiliency equals elasticity and the ability to flex capacity or the network. Rick McDonald, senior vice-president and chief product supply officer at Clorox, saw resiliency as preparation for unexpected events, responding quickly, then moving from disruption to a stable state.
To prepare for a crisis, McDonald said that Clorox runs efficiently at all times to model future capacity requirements. The company focuses on supplier relationship management as well as operating on a continuous improvement model.
Lusk emphasized FedEx’s teambuilding, not only across the business but also industry segments. Teambuilding pays off when challenges arise. The company’s COVID-19 response was informed by past events, such as the 2009 H1N1 outbreak, he noted.
“All of that work has gone on the front end before you need it, and that’s critical,” Lusk said.
TECHNOLOGY FOCUS
Each year, MHI presents the results of its industry report. This year, moderators John Paxton, CEO of MHI and Thomas Boykin, supply chain specialist leader at Deloitte, led a panel through the report’s main points. Panelists included Randy V. Bradley, associate professor of information systems and supply chain management, Haslam College of Business, The University of Tennessee; and Annette Danek-Akey, executive vice-president of supply chain at Penguin Random House.
One survey focus was technology and among those surveyed, 83 per cent believe digital will become the predominant model within five years; 22 per cent believe that model has already arrived.
The report outlined how much companies have adopted leading technologies, or when they planned to, tracking 11 technologies based on how they impact supply chains. The report found that 57 per cent of companies surveyed use cloud computing and storage, while 44 per cent have adopted inventory and network optimization. Sensors and automatic ID came in third with 42 per cent, followed by robotics and automation at 38 per cent. Overall, 30 per cent of organizations have adopted predictive analytics, while IoT weighed in with 27 per cent. Next up was AI (16 per cent), then AV and drones (21 per cent).
The report highlights skills that professionals will need over the next five years to work with digital supply chains. Project management and leadership ranked the highest, with 41 per cent citing it as most important. That was followed by strategic thinking and problem solving, at 40 per cent. Supply chain management (degrees and certifications) came in at 32 per cent, while 31 per cent cited analytics, modelling and visualization. Bradley said he was encouraged by the report’s findings that 49 per cent are still increasing technology investment. But he warned that investing too early can also be as detrimental.
The panel discussed developing business cases for technology adoption. Danek-Akey recommended highlighting core competencies that technology enables. Also, look within your own area when developing a business case. “If you want to talk about e-commerce investment, go to the person who is in charge of your e-commerce platform, or in charge of that P&L, and ask them, ‘what do you need from me to be able to create your business case and grow?’” she said.
WOMEN LEAD THE WAY
Another panel focused on women in supply chain, with panelists discussing steps to achieve success. Panelist Megan Smith, CEO of Symbia Logistics, stressed an integrated supply chain – a notion that’s critical due to the pandemic and recent technological advances.
Ensure your systems are communicating properly and that complicated integrations are seamless, Smith stressed. Don’t overlook simple integrations. Ensure there’s a strategy in place and someone who keeps stakeholders aligned.
Fellow panelist Erin Donnelly, supply chain development director at Home Depot, offered advice on prioritization. Understand where the starting point is, Donnelly advised, including analyzing the industry, competitors and other factors.
Skillful mentoring is essential to leadership, said fellow panelist Chaneta Sullivan, Esq., director, safety, quality and compliance, Chick-fil-A supply. Sullivan noted it’s equally as important to influence the team you’re on, as the team you lead, since that can make it easier to get things done.
“When your team wins, you win,” she added. “That’s helped me when I’ve led in that way.”
The winners of the 2021 MHI Innovation Awards were also announced during the online conference. This year, ThruWave, Inc. won Best New Product for its ThruWave X2 mmWave Imaging System. The Best IT Innovation award went to 4Front Engineered Solutions for 4SIGHT Connect Digital Gate. Packsize International LLC took home Best Innovation of an Existing Product with their Packsize X7 Automated In-line Packaging and Fulfillment Solution. SP
Fleet Management
24
Road test Driving the Ram ProMaster.
26
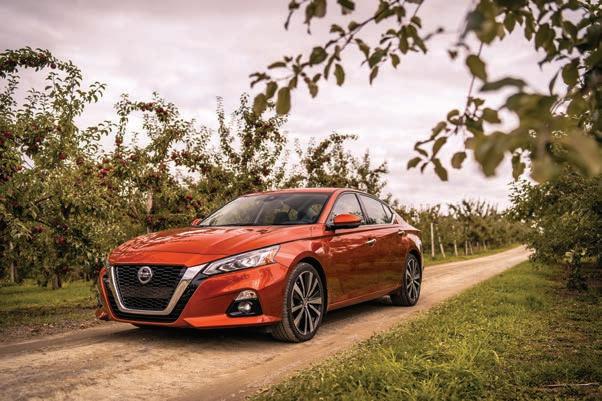
26
Mid-sized roundup What’s new in midsized vehicles.
28
In with the new Do’s and don’ts of vehicle replacement.
29
Gathering data Trends in the telematics world.
Fleet Management is a special section of Supply Professional magazine. It is an important resource for Canadian supply professionals who recommend, select and manage fleet vendors and service providers. EDITORIAL INQUIRIES: Michael Power, 416-441-2085 x110, michael@supplypro.ca ADVERTISING INQUIRIES: Alex Papanou, 416-441-2085 x101, apapanou@iqbusinessmedia.com
Designed to meet demand
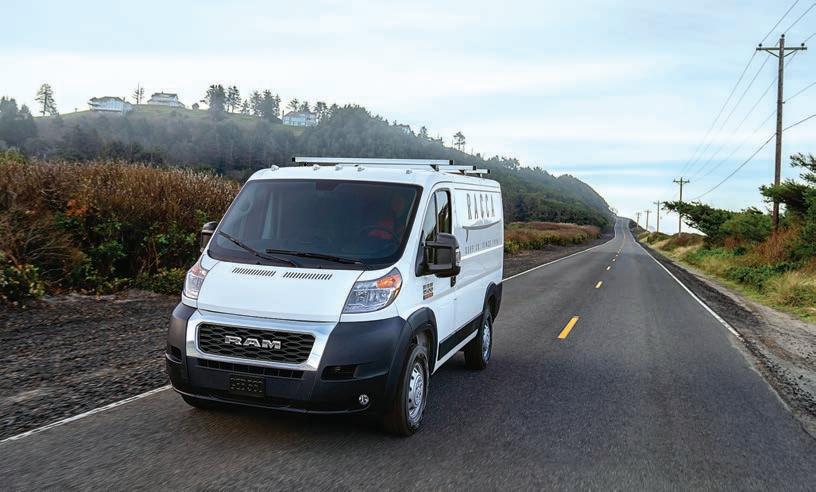
The 2021 Ram ProMaster
In the commercial van market, the ProMaster by Ram is unique with its front-wheel-drive (FWD) system. With its transversely mounted front engine it offers reduced overall weight and complexity by locating all components beneath the cab. This also means that the chassis cab model has a completely clean deck back of the cab. This benefits upfitters in countless ways – all of which improve aftermarket design and offer cost savings.
The FWD setup also keeps the cargo-load floor height and step-in height low. This trait alone is one that is much appreciated by an operator getting in and out of the van all day. Another advantage to the FWD system is traction. It’s always better to pull than push in slippery situations like snow. Improved traction comes from having the powertrain weight on top of the front wheels. The overall result of this design for ProMaster is a purpose-built, highly customizable van body that is unique among its competition. It’s designed to meet the demands of commercial customers and upfitters.
Euro roots ProMaster has been selling in Canada for the past five years, however it’s worth noting that it’s a cousin of the Fiat Ducato van. The ProMaster we now have in Canada is descended from this van. Mind you, this is a common thread among the other van providers. Mercedes-Benz’s Sprinter and Ford’s Transit both originated in Europe. The key difference is that most of the old-world vans are diesel powered while the Canadian version of the ProMaster uses the 3.6L Pentastar V6 gas engine as its standard powerplant (280hp and 260lbs-ft of torque). It is paired with a six-speed automatic transmission. Of note for 2021, the diesel option is no longer available. The Pentastar V6 is now the sole powertrain.
Competition in this livery segment is brisk; and while vans don’t change much year to year, each manufacturer keeps looking for customer advantages. Frankly, it makes sense. If you wonder about the value of this market to the manufacturers, consider that the commercial van market in North America can consume as many as 325,000 units a year.
The ProMaster is built on three different wheelbase lengths – 118, 136 and 159 inches. The cargo van body comes with either a low or high roof. As for the gross weight vehicle rating, it’s offered as 1500, 2500 and 3500 series vehicles. In all, the ProMaster can be ordered in any one of 18 different configurations. This includes a Chassis Cab Cutaway on the 3500-series version. In addition to the cargo van models, ProMaster can also be ordered as a passenger window van.
ProMaster has certain best-inclass features, including standard V-6 horsepower; turning diameter; standard interior cargo height; load-floor height; cargo width between wheel wells; and maximum cargo width.
For 2021 there are also a few new standard features such as Crosswind Assist, which helps the driver stay on course in windy conditions. A range of new safety options are available this year, including blind-spot monitoring with rear cross-path detection, forward collision warning with emergency brake assist and ambient/ courtesy lights.
Class-exclusive digital rear-view mirror is available to replace the traditional rear-view mirror with a 9.2-inch-wide LCD monitor. A new factory-installed trailer hitch option was new in 2020 – but is worth mentioning. It increases the max tow rating to 6,800lbs.
Lastly, (late availability this year) is a monitoring system called Ram Telematics, which will interest fleet managers. Mopar offers an electronic vehicle tracking system as well. A new standard item on ProMaster now is a speed limiter. This is activated by the dealer and can be set at 100, 105, 110 or 120km/h.
The ProMaster is becoming popular with upfitters, either as a chassis cab with clean frame rails or as a van body suited to institutional purposes. To that end, Ram is offering prep packages targeted at specific vocations, for instance, ambulances. They also offer the same prep for recreational vehicle builders. Also available from the factory is an interior cargo shelf group. This option requires the cargo partition installed. FM/SP
We’re in the business of driving yours forward.
Behind every thriving business is a team you can count on.
The all-new TUCSON brings capability, reliability and impressive fuel economy to you, your company and everyone that drives it forward.
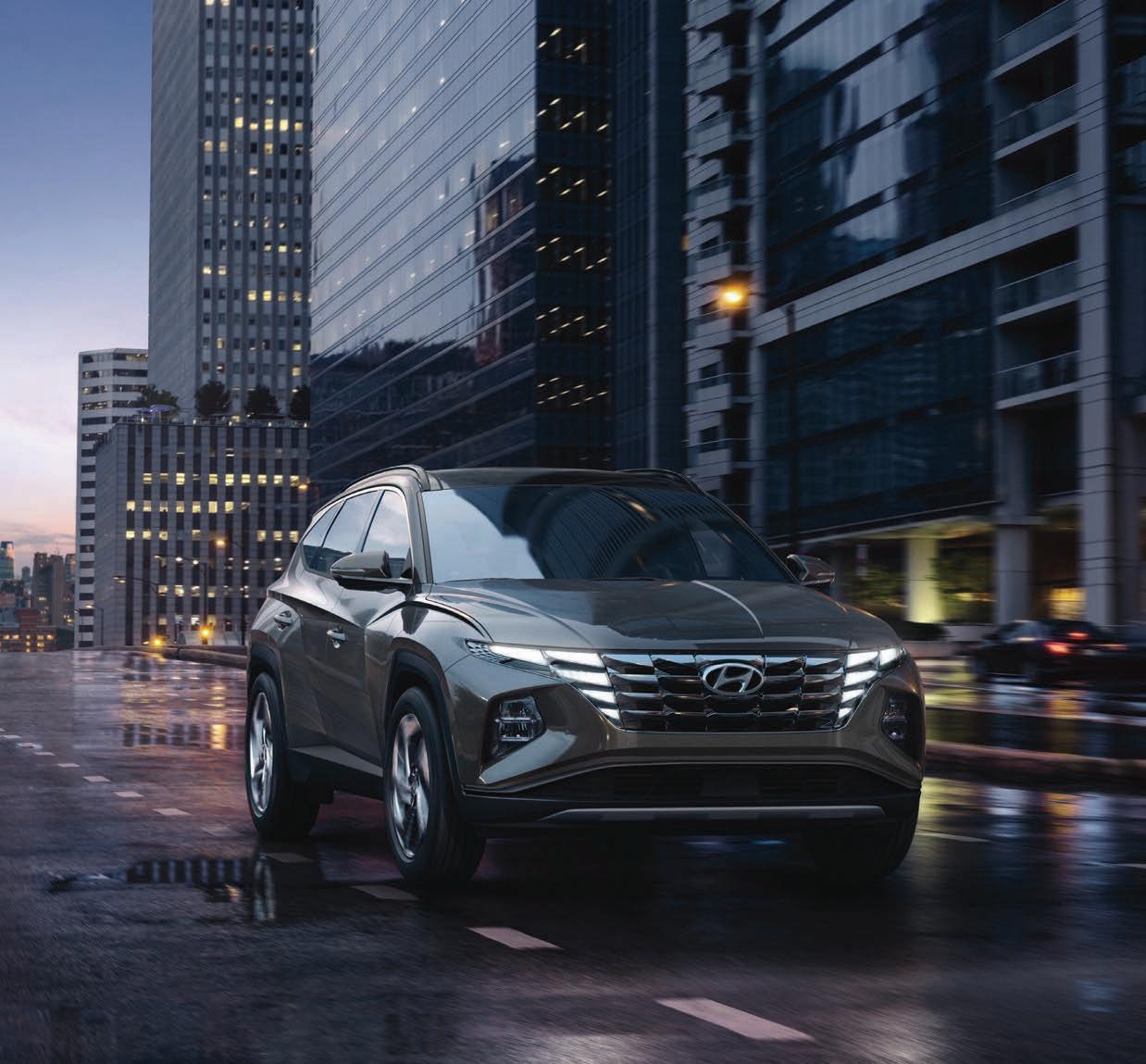
Kevin Forodi
Senior Manager, Fleet Sales CPO and Remarketing kforodi@hyundaicanada.com (905) 948-6701
Zohair Ahmed
Manager, Commercial and Government Fleet Sales zahmed@hyundaicanada.com (905) 948-6822
Julian Cheng
Fleet Analyst jcheng@hyundaicanada.com (905) 948-6764
Neil O'Donnell
Remarketing and Fleet Analyst nodonnell@hyundaicanada.com (905) 948-6891
hyundaicanada.com
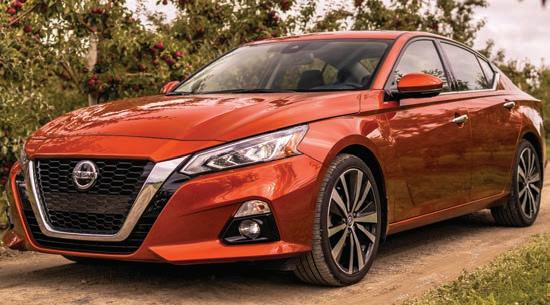
Nissan Altima
If the lack of available all-wheel drive is what causes some buyers to shy away from mainstream sedans, then the Nissan Altima is worthy of attention. Equipped with standard all-wheel drive in Canada, the Altima uses its 2.5-litre four-cylinder engine to power all four wheels with 182hp and 178lbs-ft of torque while still achieving a fuel efficiency of 9.4 litres per 100km in the city and 6.7 on the highway. With a starting price of $29,498 in the entry-level SE grade, the Altima offers a cost-effective way to add mid-size vehicles with all-wheel drive to Canadian fleets.
Kia Sorento

Kia’s mid-size Sorento enters a new generation for the 2021 model year while remaining one of the most affordable ways to get into a mid-size three-row SUV with a starting price of $33,995. Two engines are offered, each a 2.5-litre four-cylinder; the entry-level version makes 191hp and 181lbs-ft of torque while using 10.1 litres per 100km in city driving and 9.2 on the highway, while the upgraded turbocharged engine generates 281hp and 311lbs-ft while consuming 11.1 and 8.4 litres respectively. An all-wheel drive version of the hybrid Sorento is expected to go on sale in Canada late in 2021.
Mitsubishi Outlander PHEV
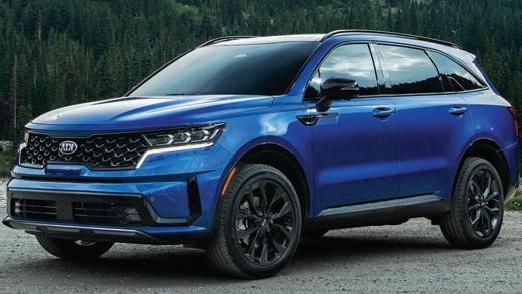
The Mitsubishi Outlander PHEV checks a lot of the right boxes for fleets. With a starting price of $44,198, it qualifies for partial incentives from both the federal iZEV program and existing provincial EV rebate programs. Its 2.4-litre four-cylinder engine combines with twin electric motors to generate a total system output of 221hp while using a combined average of 3.2 litres-equivalent per 100km and offering an electric-only range of 39km. All-wheel drive is standard, plus this is one of the few plug-in hybrids that works at a Level 3 charger for quick battery top-ups on the go, and it’s offered with a 10-year, 160,000km limited powertrain and battery warranty.
Mercedes-Benz GLE
City runners, highway haulers Mid-size fleet options for 2021
The proliferation of electrified options in today’s automotive market is giving fleet managers more choice than ever – and introducing more factors to consider in making those selections. Between fuel efficiency, all-wheel drive capability and price range, it’s easier than ever to customize fleets to best meet the tailored needs of both drivers and owners. Here’s a closer look at eight of the best mid-size options for fleets on the market in Canada today, from city-friendly runabouts to highway haulers and everything in between.

Fleets with a need for luxury vehicles will want to consider the MercedesBenz GLE, a mid-size SUV that come as either a simplified entry model or a to-the-nines grade. The latter is the GLE 350 and is a suitably premium vehicle, priced from $69,900 and fitted with a 2.0-litre turbocharged four-cylinder engine that produces 255hp and 273lbs-ft of torque while burning 12.4 litres per 100km in city driving and 9.0 on the highway. The GLE 450, priced from $77,500, upgrades the engine to a 3.0-litre turbocharged inline-six-cylinder engine fitted with the EQ Boost mild hybrid system, which makes 362hp and 369lbs-ft while consuming 11.4 litres per 100km and 9.2 on the highway.
Subaru Outback
There’s nothing else on the market quite like the Subaru Outback. Its dimensions give it a feel that’s an ideal compromise between a wagon and an SUV, and standard all-wheel drive, 22cm of ground clearance, and off-road chops make it a great choice for more rugged applications. Starting from $31,195, the Outback is offered with two engine options. The entry-level engine, a 2.5-litre with four horizontally opposed cylinders, makes 182hp and 176lbs-ft of torque and averages 9.0 litres per 100km in city driving and 7.1 on the highway. The upgraded engine is a 2.4-litre turbocharged horizontally opposed four-cylinder that’s good for 260hp and 277lbs-ft of torque, and it averages 10.1 and 7.9 litres per 100km respectively in the top two grades.
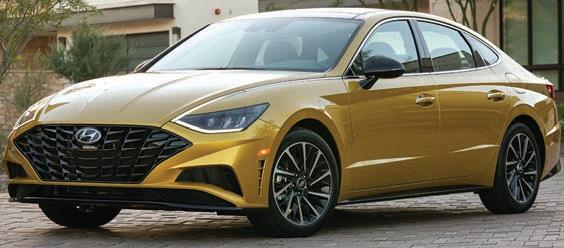
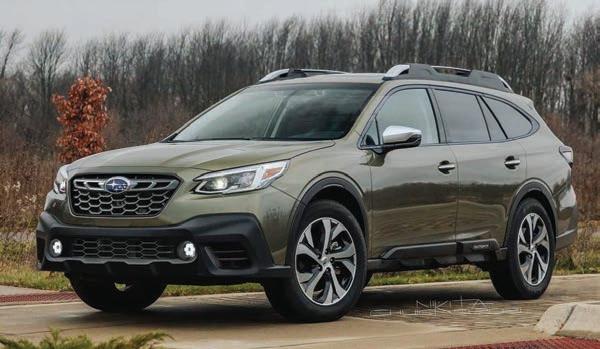
Hyundai Sonata
If what you really need is wheels and you can take ground clearance, allwheel drive and cargo capacity out of the equation, don’t let the market’s heavy lean toward SUVs distract you from the humble mid-size sedan. The Hyundai Sonata comes in both gaspowered and conventional hybrid configurations, and its dramatic styling and unique lighting treatment ensure it comes across as anything but boring. In the gas version (from $27,149), two engine options are offered with the entry-level 2.5-litre four-cylinder producing 191hp and 181lbs-ft of torque while consuming 8.8 litres of fuel per 100km in city driving and 6.4 litres on the highway. Opt for the hybrid (from $40,199) and those figures drop to 5.3 and 4.6 respectively from its 2.0-litre fourcylinder engine and electric motor with a combined system output of 192hp and 271lbs-ft.
Ford Mustang Mach-e
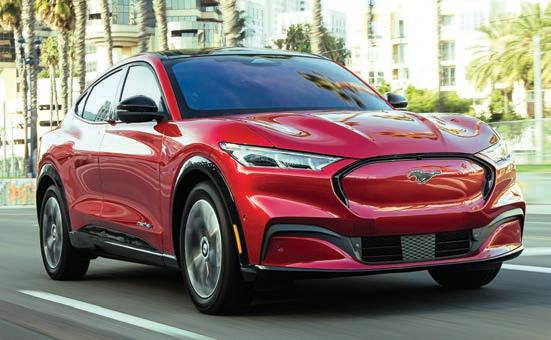
An EV’s efficiency depends heavily on its weight, which is why there aren’t yet a lot of reasonably priced battery electric vehicles much larger than subcompact. Ford has therefore filled a market gap with its new Mustang Mach-e, which with an overall length of 4,724mm falls firmly into mid-size territory. Although it doesn’t qualify for the federal government’s iZEV rebates with a starting price of $50,495, it does qualify for rebates in Quebec and BC in its lower-priced configurations. Offered with both standard and extended range batteries and in rear- or electric all-wheel drive, and a maximum range in the latter of 435km, the Mustang Mach-e hits the market ready to electrify a variety of applications.
Toyota Venza
Toyota’s mid-size Venza returns to the company’s line-up after a fouryear hiatus, and this time it comes equipped with standard hybrid drive. Not only does this mean that hybrid fuel efficiency is available at every price point, including in the base model priced at $38,490, but electric all-wheel drive is also standard equipment since the electric motor powers the rear axle. Combined with the Venza’s 2.5-litre four-cylinder engine, it has a total system output of 219hp while averaging 5.9 litres per 100km in city driving and 6.4 on the highway, figures that are remarkably low for any SUV of this size that doesn’t require a plug.
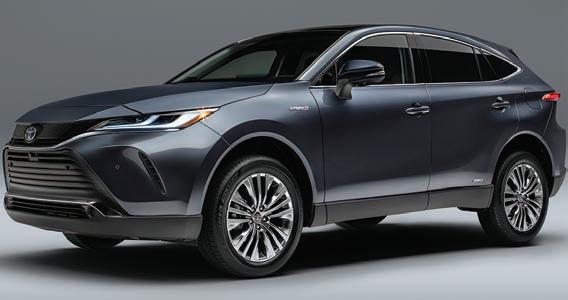
In with the new
Taking an informed approach to delayed fleet replacement 1.
Fleet professionals understand optimum replacement and how to work towards the lowest total cost of ownership (TCO). It is intuitive that capital costs (depreciation) decrease when they are spread out over longer periods and operating costs increase as a vehicle gets older, is less fuel efficient and requires more maintenance.
When possible, vehicles should be replaced when the TCO is at its lowest, usually just before a spike in operating (maintenance) costs.
Many organizations use technology to calculate optimum replacement points for various equipment classes and the yearly budget. Optimal replacement can only happen if an organization can dedicate sufficient budget for fleet. Best-laid replacement plans fail the first year that funding is not forthcoming. In a perfect world, fleet professionals would adhere to optimum lifecycles and minimize TCO over multi-year plans.
The pandemic means a far from perfect world. Budgets have been redirected to purchase of PPE, increased cleaning, workplace modifications, enhanced technology to allow work from home and other changes. These funds must come from somewhere and the fleet replacement budget is an attractive target. Decision-makers often see delaying fleet replacement as an “easy out,” as the impacts may not be known for years. Diverting fleet replacement funds to a higher operational priority may be inevitable.
Although delayed replacement is not new, it is exacerbated by the COVID-19 crisis. I recently spoke with a fleet manager who is living this reality. After a devastating fire, followed by floods, his fleet replacement funding was zero in two of the past five years. He is now facing another year of no funding. The organization may not have other viable options. But they are digging a hole by delaying fleet replacement without a workable plan for longer-term fleet renewal. There’s no ideal solution. Fleet professions must act counter to best practice to meet priority goals. When delayed replacement is inevitable, fleet managers should take these steps:
Understand the budget reduction.
In large organizations, it can take time to communicate information. Budget cuts rumours may hit the fleet office before official announcements. Fleet managers must understand the decision and reduction to capital and/or operating funds. They should be ready to perform “what if” analysis and offer alternatives. Ideally, the fleet manager is involved in the budget process and can ensure the impacts of any reductions are known.
Evaluate short- and long-term
costs and impacts. Cutting replacement funding has immediate and longer-term consequences. The fleet manager should evaluate the immediate impact on operating costs and service delivery. Keeping vehicles longer means that fuel and maintenance costs will rise. Maintenance needs may exceed shop capacity and outsourcing may increase. More operating funds may be needed to the fuel or outsourced maintenance cost centres.
If funds are not available for these increased requirements, downtime will increase. This can compromise key services delivery – it may take longer to plough roads, collect garbage or repair bridges. Downtime can mean lost productivity as crews wait for a vehicle. This operational degradation is difficult to quantify but should factor into the delayed replacement decision.
Educate decision-makers on
these impacts. Fleet professionals must quantify these impacts and educate decision-makers. They must paint a picture that short-term impacts grow exponentially over time. Every year that replacement funding is insufficient, the hole gets deeper and more difficult to make up. Decision-makers need to be reminded that withholding $2 million in funding may result in an increase to total fleet spend of twice that over 15 years. Fleet managers should use models to demonstrate these impacts.
Explore less costly alternatives.
Knowing that delays to fleet replacement postpone these expenditures, organizations should ask tough questions about whether a program or service can be discontinued to achieve savings. Can garbage service be every two weeks, instead of weekly, or can recreational facility hours be reduced? Either would mean reduced services but translate into savings.
Before suggesting service level reductions, fleet professionals must be certain their house is in order. A fleet utilization review may reveal units that are lightly used and can be remarketed or pooled. The use of rentals, employee-owned vehicles and public transit may help alleviate fleet replacement costs.
Implement wisely. Even after explaining the economics of fleet and exploring alternatives, some organizations will reduce replacement funding. Fleet managers must then plan and execute, making the best decisions under the circumstances. Using a points system that accounts for vehicle age, mileage or hours, maintenance spend and condition can help to minimize long-term impact. Abandoning the multi-year replacement plan is not the answer. Changes are needed to plan to reflect the new reality. Once adjustments are made to the multiyear replacement plan, decision-makers should be told of cost impacts and the risks associated with further reductions.
Fleet managers will be asked to delay fleet replacement in tough times. They must ensure decisionmakers understand the impacts and have alternatives to delayed replacement. After the final decision to reduce fleet budgets, they must make informed decisions that minimize impacts. FM/S
Kate Vigneau, CAFM, is director (fleet and Canada) at Matrix Consulting Group, Ltd. (US) and MCG Consulting Solutions (Canada).
An essential fleet tool
1. Choosing the right telematics
Roger Constantin is a fleet management expert. Reach him at roger.constantin@ conseilsrc.com.
Today, managing your vehicle assets is all about data. Data will give you all the details that you need to make the right choices about your fleet. It’s a data driven approach; the principal focus with such an approach is to base your decisions on facts. As you might have heard, the devil is in the details.
One way to get the data you need is to use vehicle telematics. This tool will be able to get you the information you need to: Right-size your fleet Track driver behaviours
Achieve your preventive maintenance goals
Reduce greenhouse gas (GHG) emissions Support your lifecycle analysis
Rightsizing your fleet The definition of rightsizing your fleet includes the following components: having the right number and right kind of vehicles, having them at the right location, as well as at the right time.
While you can make this analysis without a telematics tool, you will not be able to get the same calibre of information, especially at the right time.
That analysis will also confirm if you have enough vehicles, if you need more or, as in most cases, whether your fleet has too many vehicles. As mentioned, you can achieve this analysis without telematics. But by using such technology, you will be able to illustrate, with scientific facts, a clear picture of the state of your fleet.
Once that’s done, you are still just at the beginning of the process. You will be challenged by the end users of the vehicles. My advice is to take the time to prepare top management, including your own boss, and present to them a blueprint of the continuous improvement approach and how telematics fits in.
Driver behaviour Driver behaviour is all about how users utilize vehicle assets. Without telematics, you will have little data to produce a scoreboard for each driver. You will not be able to measure speed, idling time, harsh braking, fast starts or anything else.
With a scoreboard, each driver will have a monthly report that can be compared to the group in which you driver belongs. If you have more than one driver per vehicle, you will be able to identify each driver’s performance.
In my experience, I can confirm that without telematics, it is impossible to reduce excessive speed from users. You might even face legal actions that could have a major impact on your organization.
If you have some problematic drivers, you can access the right data to take action directly with them. You will be able to present facts regarding their driving behaviour.
With telematics, you will be able to get more specific details when an accident occurs. You will be able to demonstrate to your insurer that you’ve taken steps to get control of your vehicle. In fact, you will be able to provide an input into your risk management policy.
Finally, telematics will offer you the possibility to geofence your vehicle, so you will make sure that the vehicle stays within a specific territory.
OEM versus service providers Now let’s discuss telematics products. We should distinguish between two major options. First, most OEMs have their own tool, including all the support a fleet would need, such as a dashboard to track your fleet asset and produce driver scoreboards. The main advantage with their products is the integrity of the data.
The other option is to use tools developed by a third party or service provider. Their products are developed like the OEM to have the same features, but they need an agreement to include them in their solution. Some OEMs have preferred services providers.
Your decision on which of those two options to select will also be influenced by the type of fleet you are managing. For example, do you have only cars or heavy vehicles?
Preventive maintenance With telematics, you will be able to reach your maintenance program goals by using the input of the data, especially for heavy vehicles or specialized equipment. Telematics will send alerts on when mechanical components require maintenance, so there will be heads up.
Reduce greenhouse gas With telematics, you can get the idling time of your asset. Some telematics providers differentiate good idling from bad idling. This is included in the scoreboard. There is a lot to save.
Lifecycle analysis Almost all the data that you will received can be converted in cost. You can then use it in your lifecycle analysis. Finally, with the arrival of electric vehicles (EVs), you will need to be aware of the driver’s behavior; telematics should give you the needed data. FM/SP