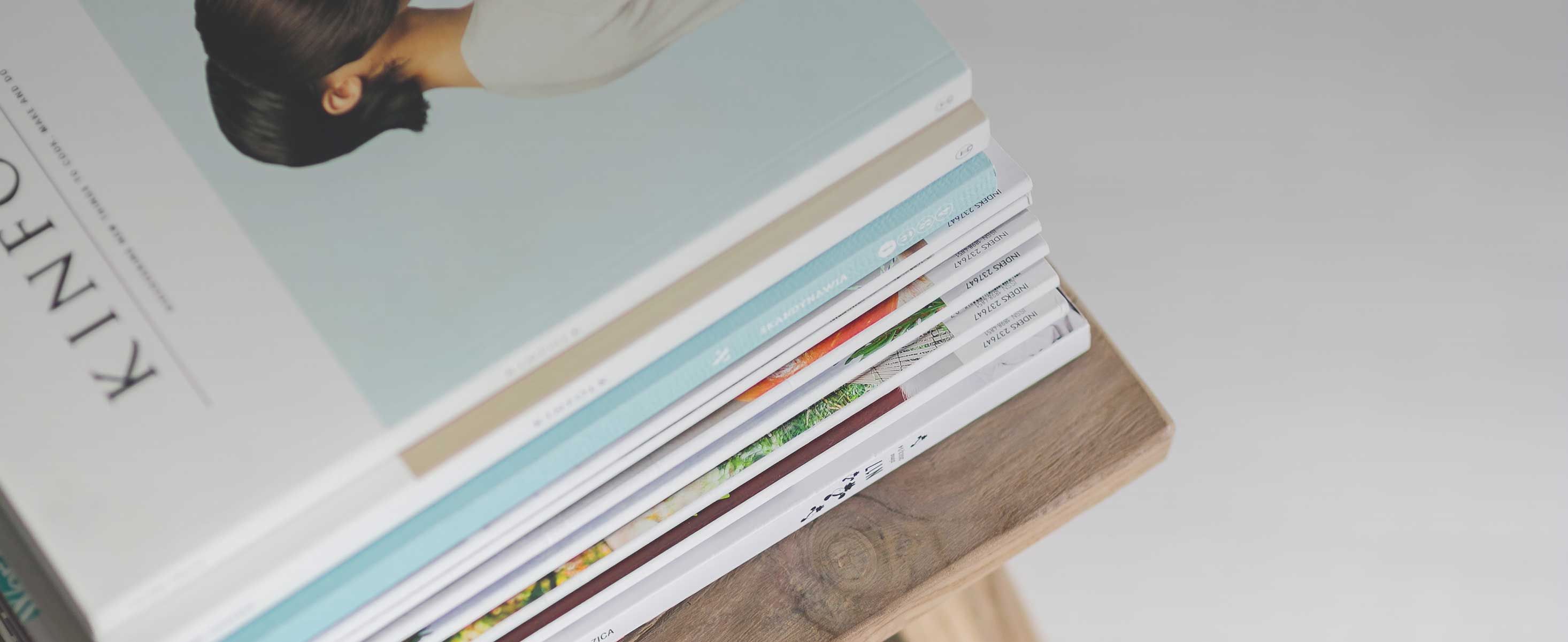
5 minute read
SUPPLY CHAIN RESILIENCY
BY MARIETE F. PACHECO
SAFETY’S NEW NORMAL
HOW PPE PROCUREMENT HAS EVOLVED SINCE THE PANDEMIC BEGAN
Mariete F. Pacheco, MBA, PMP is managing director at FRW Services Ltd.
It has been a unique and challenging time for nearly all industries these last two years. During this time, businesses have had to pivot their operations, with many needing to add new personal protective equipment (PPE) to their EHS toolkit to keep employees safe.
The greatest investment an organization can make is in keeping employees safe and certainly this has been demonstrated time and time again during the pandemic. Initially, the highest COVID-19 case counts came from food processing plants and warehouses; both of which are designed for maximum efficiency and product safety, not employee wellbeing. These first major outbreaks resulted in many operations having to be shut down due to employees being unable to safely operate the business.
During the onset of the pandemic, the focus was on securing PPE as quickly as possible. Quantity over quality was the rule. This led to poor quality, unregulated products flooding the market caused by a surge in non-traditional PPE manufacturers beginning production to meet explosive demand.
This panicked production, although well intentioned, drove prices to never-before-seen levels and further exacerbated the shortage. The result was stockpiling for some organizations while others went without any product at all. As organizations adapted to the onslaught, subsequent coronavirus waves combined with learning from government and industry experts. The result was greater knowledge both in terms of business needs but also regarding PPE standards. From ASTM for disposable surgical masks to NIOSH for N95 respirators, PPE standards had become commonplace beyond medical environments. Procurement professionals were now becoming authorities in PPE and had developed partnerships with reputable suppliers.
INVENTORY MANAGEMENT
As COVID-19 waves ebb and flow, it will be paramount for organizations to optimize PPE usage from a risk management perspective to mitigate inventory risk from obsolescence or shortages. Procurement must manage a fine balance between how much to order and how much to use.
Since most PPE has expiry dates, it is critical to invest in inventory management practices to ensure stock is rotated. This can help to avoid exposure to non-conforming or poor performing products (for example, expired N95 respirators have lower filtration protection and no longer fit as tightly due to the loss of elastic integrity). Considerations may include dual sourcing, prioritizing product by job task, investing in reusable PPE or partnering with domestic manufacturers.
Diversifying the supplier base with multiple providers reduces the risk that comes with not having inventory. As well, having backup suppliers may also help support cost management strategies. A common best practice is optimizing PPE use in healthcare. This is done by aligning the risk profile of employees with the PPE available. For example, in higher risk environments, N95 respirators are used in conjunction with other products such as gloves, goggles or face shields, whereas lower risk environments may only see the use of standard disposable surgical masks. The greater the risk, the greater the protection coverage.
Lastly, to combat the need for additional storage space for large stockpiles of PPE, more organizations are looking to make the shift from disposable to reusable PPE. This can include N95 respirators, which have interchangeable filter cartridges, face shields and goggles that can be wiped down or sanitized between uses or the laundering of garments such as gowns and gloves.
The challenges with re-usable PPE include more complex supply chains, additional product complexity, and the need for additional services such as the laundering of products. These services often need to be outsourced. This not only offers a consistent supply of PPE but also provides a sustainably focused solution which many organizations are searching for, as corporate sustainable reports become more pervasive.
This year, organizations continue to face ongoing supply chain challenges, from long lead times to raw materials shortages. PPE procurement is no longer at the crisis level we saw in 2020. However, there remains rolling shortages. These have thankfully been offset by countless new domestic manufacturers across Canada and much of North America.
The ongoing need, regardless of the industry, continues to be the procurement of masks. This is due
to the respiratory nature of the virus’s transmission and the generally high protection and price point that masks offer compared to alternatives such as face shields. These benefits, combined with less severe flu and cold seasons the last two years, may result in greater acceptance and usage beyond the COVID-19-era. This is especially true in environments where physical distancing may be a concern, such as warehouses or production lines in manufacturing facilities.
The number of cases of these illnesses, along with the spread of other common respiratory illnesses, has decreased dramatically to record-low levels compared to the most recent 2017-2019 seasons, according to the Government of Canada, Centers for Disease Control in the United States and the World Health Organization. The secondary benefit of mask use in reducing absenteeism due to almost non-exist airborne illness during the fall and winter has generated interest from some organizations. These organizations are investigating masks as standard issue during select times of the year, which may keep PPE demand levels higher than pre-pandemic levels.
A NEW NORMAL?
Looking forward to the “new normal,” what will EHS professionals be faced with? More of the same? Changes to their standard operating procedures? New standard operating procedures?
It depends. If the last two years has taught us any lessons,
it has been to expect the unexpected. More important, it has taught us how vital it is to keep employees safe as they are the core to any operations, whether in construction, manufacturing, or warehousing.
COVID-19 protocols for many industries, including food processing plants, manufacturing and construction sites, focused almost exclusively on increasing their PPE usage and enhanced personal hygiene measures, such as hand sanitizer availability, to counter virus spread to keep employees safe and their operations running. Organizations are required to demonstrate they maintain an acceptable standard of employee safety. The last two years have left a long-lasting impact on how organizations approach this, especially as it relates to PPE usage. SP