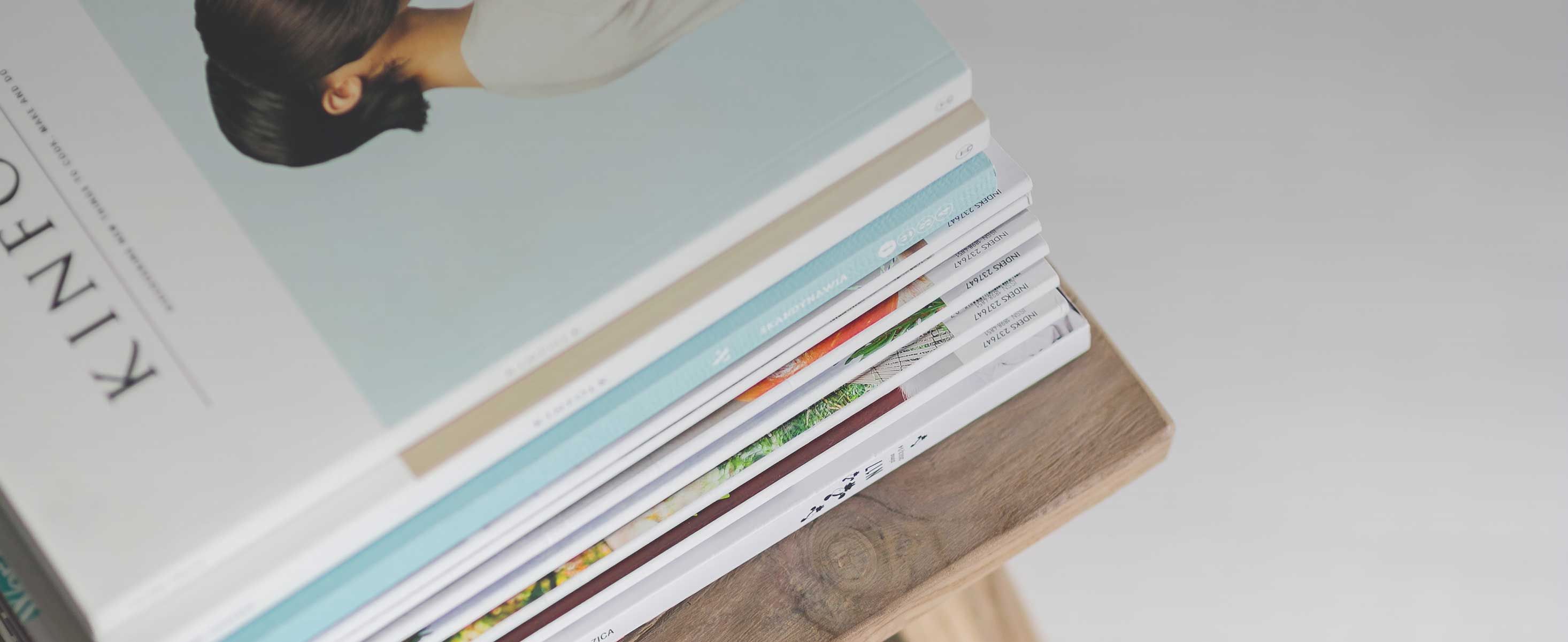
3 minute read
SUPPLY ASSURANCE LESSONS FROM SECURING SUPPLY DURING THE COVID-19 PANDEMIC
For anybody in supply chain, the past three years have been interesting, difficult, exciting, and challenging. We had to adapt to a changing landscape, adopt new methods, and ensure that data was updated and realistic. Data to make tactical and strategic decisions must be updated to reflect the environment, which has been very dynamic.
When the pandemic started, no one would have guessed the impact it would have on the supply chain. I remember first hearing about COVID-19, and back then, many people (including myself) thought it would be contained outside of Canada, yet that assumption proved false. Driving into work one day, I realized that the traffic was considerably less. To me, it was the start of the challenges in supply chain. Supermarkets were another indicator on how our lives would change. Shelves were empty, there were long line ups at the check outs and shoppers bought in bulk. Disinfectants were nowhere to be found and third parties sold it at outrageous prices. The rule of supply and demand was now in force, with more demand than supply, which meant higher prices.
Manufacturing Challenges
The first challenge within manufacturing was attempting to get a supply of personal protective equipment (PPE). Regular sources were out of stock, and we had to source and qualify other suppliers quickly. This process was no longer as simple as ordering catalogue items from a website. Another key topic was raw materials and component replenishment. Suppliers started changing their commit dates on purchase orders due to labour shortages since employees that tested positive for COVID-19 were off from work. Certain jurisdictions had restrictions on whether employees could be in certain areas, to mitigate the spread of the virus and, of course, lockdowns were enacted in different regions that affected the ability to get materials.
No one wanted to declare Force Majeure due to COVID. This condition did reside in most terms & conditions. There were delays, but they were just delays, and sooner or later goods would arrive. Most parties understood that. Consumers could witness the impact of delays by driving past an automotive dealer and seeing the empty lots which, prior to the pandemic, were well stocked.
Assumptions had to be validated throughout the supply chain. Distributors, due to supply constraints from manufacturers, no longer maintained a certain level of inventory, therefore revising their terms and conditions of sale. Normally, companies are allowed certain rescheduling or cancellation privileges, but under the “COVID Umbrella” those conditions were amended. Rescheduling privileges were either eliminated or reduced and some items were upgraded to be non-cancellable. A widely used industry term to describe this is non-cancellable, non-returnable (NCNR).
In logistics, door-to-door lead times increased and then there was the shortage of shipping containers, congestion at ports, transport truck driver shortages, instability of vessel sailing times, rail yard congestion, and so on. Container and truck loads were stuck in congested yards awaiting clearance. Price increases also had an impact on product costs. Companies had to ensure goods were moving and provide a clear delivery date to sales staff, who could communicate with customers. Planning had to update transit times since the current ones in the system were not relevant, thus painting a false picture. A vicious lead time syndrome had started, and in some cases changed weekly.
Data integrity within an organizations’ ERP platform has always been the foundation in providing information and used in planning and other decisions. During the pandemic, it was paramount to ensure critical items on the Item Master in the ERP platform were updated to reflect current conditions. Regarding suppliers, it was important to ensure these Item Master attributes were updated: replenishment lead time, rescheduling and cancellation privileges, and supplier-to- destination transit time. If the supplier was classified as sole source, other items like changes in an organization’s policy surrounding safety stock had to be looked at. This had to be updated in the ERP platform and procurement would put more surveillance on the supplier to limit disruption.
SUB-TIER SUPPLIERS
The other important element of ensuring sustaining supply is understanding the sub-tier supplier portfolio. If your supplier is providing a product, where do their materials come from? One example is procuring an item built to your drawings and specifications. To understand the impact, drill down to the sub tiers of your primary suppliers. There is a benefit when a supplier is classified as high risk if those new suppliers were developed and validated during the on-boarding process. Sometimes, the results were better replenishment lead time and sometimes even better pricing. Although the champion of ensuring supply assurance and cost containment was supply chain, results came from collaboration with cross-functional teams like engineering, operations, sales, finance, and program management.
Supply chain professionals recently faced another issue: the invasion of Ukraine. When this situation occurred in February 2022, some commodity pricing immediately started to increase due to the situation’s uncertainty.When governments imposed sanctions, organizations had to understand what materials came from Russia and the impact those sanctions would have on supply chains.
Working in supply chain means being adaptable and building contingencies to ensure supply assurance and cost controls. As stated, the data integrity in the ERP platform is paramount in providing accurate information. As the COVID-19 emergency retreated and lead times decreased, these attributes also had to be updated in the ERP Item Master. SP
BY MICHAEL POWER