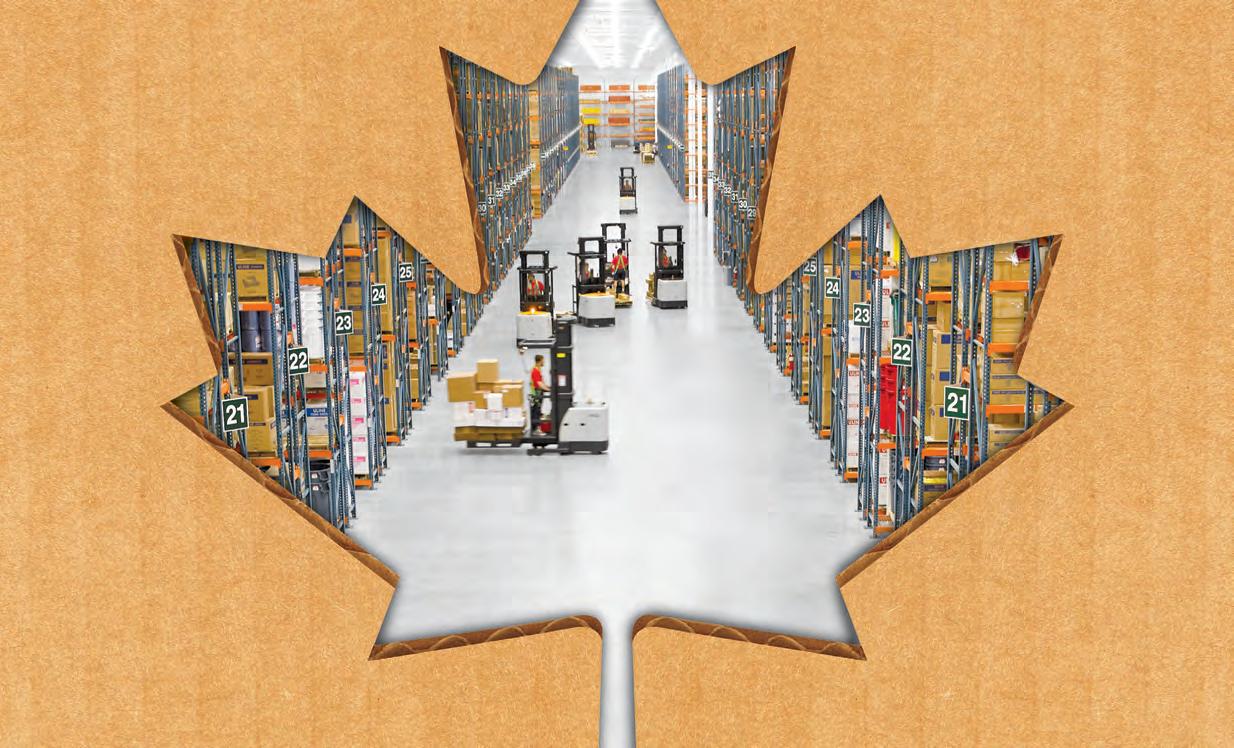
4 minute read
KEEPING COOL TECHNOLOGY AND THE RISE OF E-COMMERCE ARE SHAPING THE COLD CHAIN
The instability and disruption of the past few years has kicked off several supply chain trends. The COVID-19 pandemic, the rise of e-commerce, and other events have changed what goods we buy, along with how we get them. This is reflected in the increasing need for or cold chain services. Cold chain – supply chain and logistics services designed for low-temperature goods – continues to change due to shifts in the consumer and technological landscape.
Demand for cold chain solutions has increased due to a changing retail environment, among other reasons, says Michael Keck, senior director, business development, at DHL Supply Chain. Consumers now want omni-channel solutions, and buy goods in ways that best suit their lifestyles. The rise of e-grocery options has meant smaller, more frequent orders, like when consumers order a single recipe ingredient they forgot when shopping.
“As the omnichannel trend grows, so too does the need for temperature-controlled warehousing specifi- cally for additional fulfilment centres,” say Keck. “Some of DHL’s innovations use the new and emerging technologies in temperature monitoring, building out chain change storage in warehouses or conveyance technology like totes that will control the temperature up until the delivery to the customer.”
The company has also invested in robotics and advanced digitization in its cold chain, including collaborative robots to manage the dynamics of demand such as offsetting labour challenges during peak seasons, then ramping down during slower months, Keck notes. DHL also improves package visibility through MySupplyChain.com, its digitization platform.
“We use advanced sensors in our facilities to monitor the temperature throughout the warehouse,” Keck says. “Our solution can detect warm spots and control the response to cool those warm spots without kicking in the entire cooling system, thus reducing costs and maintaining the exact requirements for the products.”
There’s also growth in temperature-controlled logistics in the life sciences sector and healthcare, says DHL Supply Chain’s VP of lifesciences & healthcare, David Kopstein, as next-generation Rx/biologics is all cold chain. This supply chain is visible, as organizations make their ESG commitments a greater priority.
“The pandemic has also driven the transformation of more safety stock needed, more local production, and hence more warehousing need for I2M(inbound to manufacturing) and finished goods capacity,” Kopstein says.
Digital Future
Artificial intelligence (AI) and the Internet of Things (IoT) can also track data and predict outcomes, among other functions, he adds. For example, generation sensors help to rescue exceptions, while AI can simulate different coldchain pack-outs and materials to increase efficiency and support sustainable solutions.
Early and frequent planning with partners helps to ensure cold chain visibility, build resiliency, and ensure business continuity while meeting growth needs, Kopstein says.
As well, it pays to adapt to today’s environment rather than standing still, Keck recommends. “Select your partner that has expertise, depth of resources, and the ability to implement to achieve your objectives,” he notes. “Delays will most certainly cause your supply chain capability to be far behind your business’s needs.”
E-commerce activity has remained high, even though people are able to shop more in person now, says Douglas Kent, executive vice-president, strategies and alliances, at the Association for Supply Chain Management (ASCM). Track and trace capabilities are especially important for temperature-controlled products, to know where they are as they move through the cold chain, Kent says. Advances in temperature-control technology have proven especially useful for products like pharmaceuticals that must arrive at clinics, pharmacies, and hospitals at specific temperatures. Otherwise, the products can’t be used.
“Always keep an eye on the technology,” Kent says. “See what you can do to become more efficient, more secure in the cold chain environment. By secure, I mean both the protection of the quality of goods but also counterfeit goods entering the market. So, keep ahead of those technologies.“
Part of the problem, Kent notes, is organizations sometimes get interested in technologies that don’t align with the talent and training they have. Companies that adopt new technology must ensure they have staff trained in its use to integrate it into their operating model.
“Oftentimes, I think what we see is chasing technology for efficiency and effectiveness reasons, and we forget that we have to grow the talent to be able to do that and in order to make the best use of that technology and the best ROI on those investments,” Kent says.
Recent challenges associated with e-commerce pushed Missis- sauga, Ontario-based Amplify Logistics to focus on cold chain services, says Matthew Zarzycki, the company’s chief operating officer. That means more consumers are looking to buy local, organic goods. There has also been growth in the use of technology to increase visibility, Zarzycki says. Whether it’s visibility into trailers or temperature, having more than one data source can help relay more information to customers, faster, about their goods.
Zarzycki also recommends continually researching new technology to see what’s available, what you can potentially utilize, and how it can affect business.
I divide the trailer into three segments have a dry, two different reefer zones, or I can have three different reefer zones?’ That’s something that I’ve seen far more merging into the marketplace.” largely due to older infrastructure that needs replacing with more efficient and right-sized cold chain solutions, says DHL’s Keck. This issue is compounded by increased demand as well as products like fresh pet food needing cold chain. onto products on trailers since there’s nowhere else to put it, says Zarzycki of Amplify Logistics. The company’s solution has been to focus on rapid, agile deployment – a smaller space closer to the end-market often works better than a large distribution centre further away.
“DHL’s real estate solutions team has at their command the ability to build to suit facilities that directly meet the clients’ needs in location, size, and purpose,” he says.
“I don’t want to build a giant 400,000 square foot warehouse out in Milton (Ontario), he says. “I’d rather have a 50,000 square foot warehouse in downtown Toronto. Why? Because then I can rapidly deploy direct to the customer, right to the store, bypass the DC and get that product to the customer a lot quicker.” SP
SPACE MATTERS
While not a new technology, more customers also now require dual- and multi-temperature trailers, Zarzycki says: “Traditionally, you’d have a single temp across the whole reefer; now customers are looking for more of those technology solutions,” he says. “‘Hey, can 23_003274_Supply_Professional_JUN_CN
Space constraints in warehousing and distribution centres remain a challenge in cold chain. That’s
There’s often a two per cent or less vacancy rate in many key industrial campus markets, says Kopstein, also of DHL. Add to that long infrastructure build-out timeframes due to supply chain challenges on chiller parts like compressors and finding adequate cold chain space, and the situation can be challenging.
“However, building out larger/ more multi-client facilities will help to meet the demand,” he says.
A lack of warehouse capacity has meant that some organizations hold
BY MICHAEL POWER