
3 minute read
Reaching boiling point
A new 5MW Steam Boiler means increased efficiency for an Auckland food manufacturer.
After 23 years, it was time for an Auckland food manufacturer to invest in a new steam boiler. Producing beef products from beef extract and beef bone extract, exporting to Korea, Australia and America, it was important for the new machinery to be reliable, economical, and able to keep up with increasing production demands – responsible for heating a water tank for cleaning chambers and heating the cooker used for boiling.
Increased efficiency
Engaging the expertise of Tubman Heating, the 5MW 90% efficient Unical Trypass 12 Steam Boiler, equipped with a gas-fired CIB modulating burner, was installed. It was suggested by the Tubman team that an economiser also be specified to recover the flue gas’ heat and use it to pre-heat the feedwater – further increasing the efficiency to 95%. The plant can also increase its demand in the future as the new boiler can provide up to 1,600kg/hr more than the current steam usage.
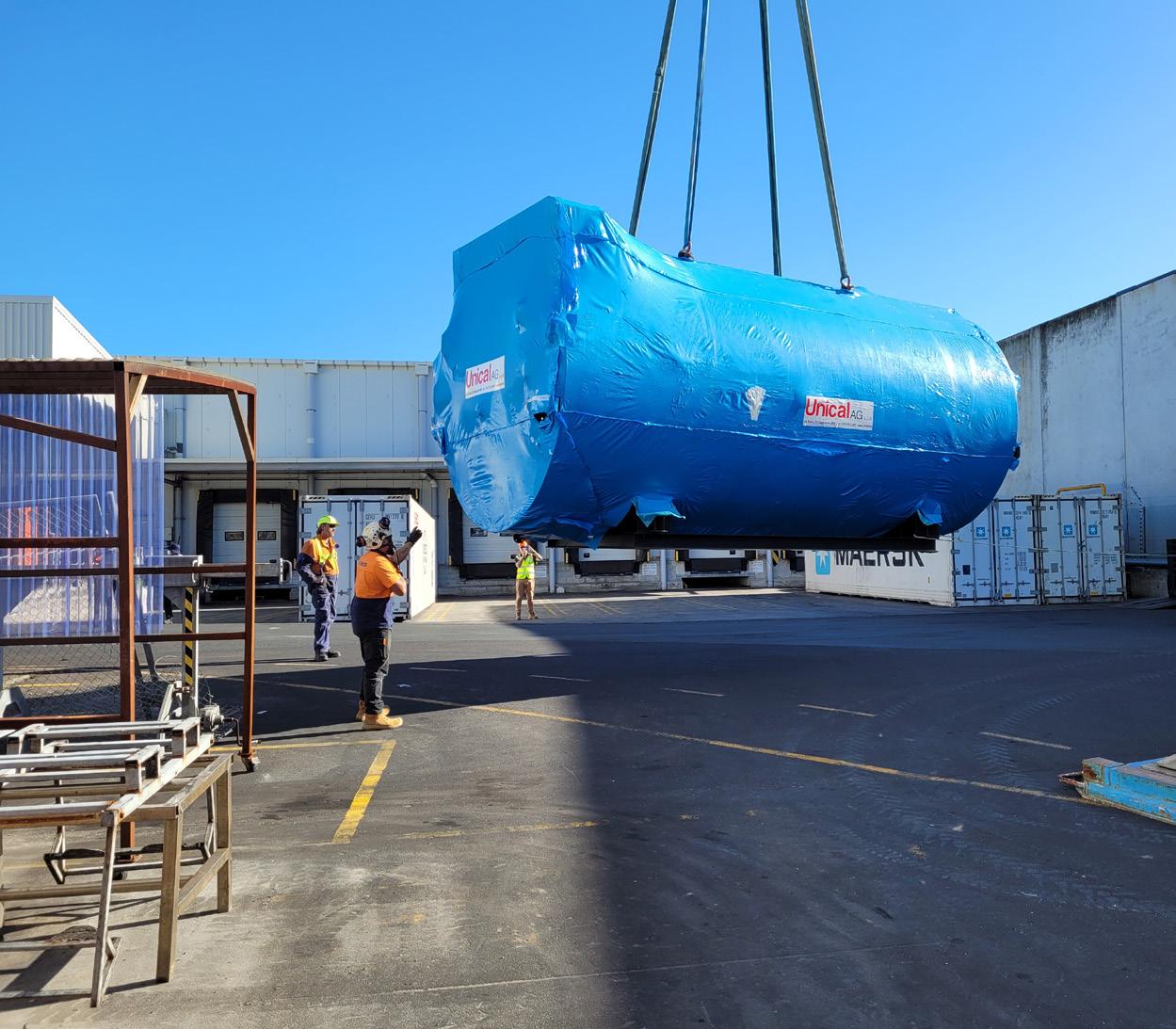
“The previous boiler was rated at 4MW,” says David Teesdale, Tubman Heating Sales and Design Engineer. “The new boiler is 5MW and allows for future expansion to the site – the expansion is proposed over the next few years to increase the production.”
“The previous boiler was rated at 4MW,” says David Teesdale, Tubman Heating Sales and Design Engineer. “The new boiler is 5MW and allows for future expansion to the site – the expansion is proposed over the next few years to increase the production.”
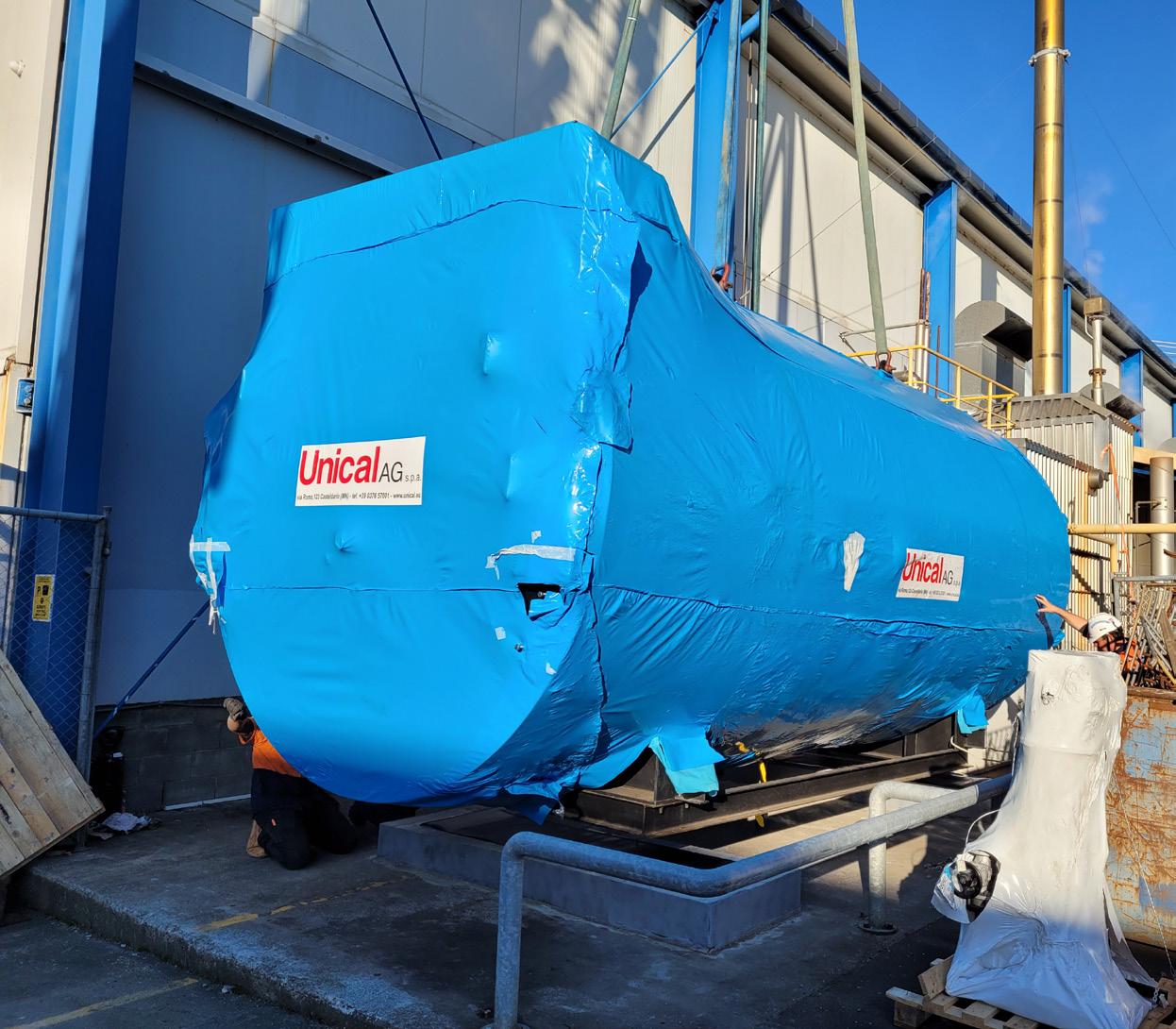
The increased efficiency, up 15% from the old boiler’s 80% efficiency, results in reduced gas usage and saves 315,000m3 of CO2 per year – a reduction of 600,000 tonnes of CO2, the equivalent of 17,130 cars per year.
Also adding to the efficiency of the boiler system is the CIB R525A fully modulating low NOx burner, which maintains a consistent supply of energy according to the steam demand. An automatic blowdown valve was also installed and integrated to the Prolec control panel to optimise the TDS (total dissolved solids) levels of the boiler and lengthen the lifespan of the boiler.
Installation logistics
A vital component in the manufacturer’s production, this project needed to be completed within one week during the company’s annual shutdown. Together with the assistance of NZ Cranes, Tubman Heating’s Auckland projects and service team worked collaboratively to off-load and install the machinery, weighing in at 21 tonnes – and due to this increased size and weight, additional concrete pads were designed and constructed to bear the new load.
As the existing 4MW boiler was still operational and supplying steam to the factory, the changeover week was planned so that the existing boiler could be decommissioned, and the existing control panel relocated to the new boiler which was installed beside the 4MW.
“When sizing a boiler for a new process or replacement, it is important to accurately calculate the existing steam load of the boiler,” explains David. “Over years, the steam load can vary with production lines no longer in use or new lines added. Any plans for future expansion added to the existing steam load gives a good picture of the existing and future steam load.” www.tubman.co.nz