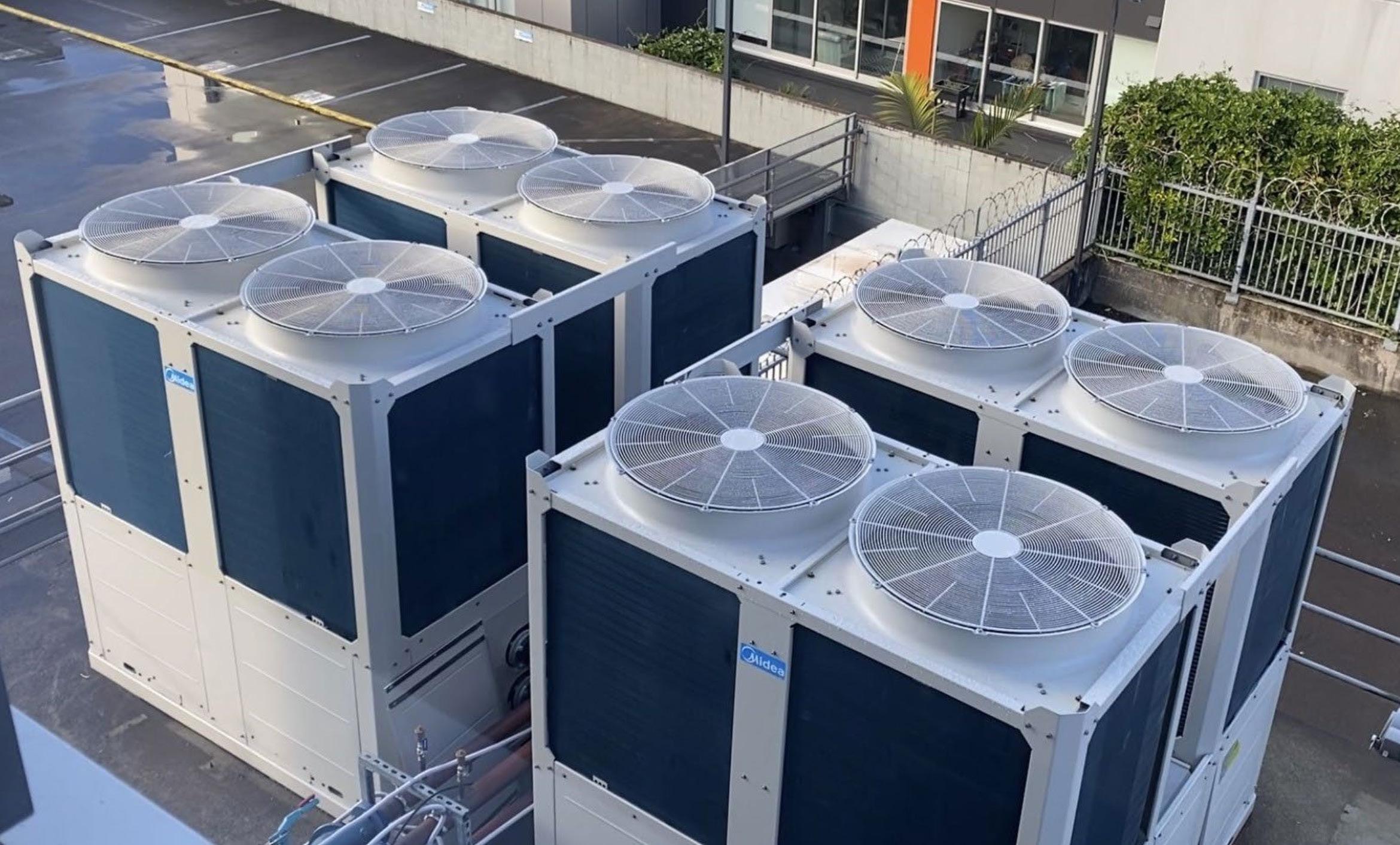
3 minute read
Argus Engineering revitalises the HVAC system at a Grafton office building
After 16 years of operation, this central Auckland office complex’s air conditioning system needed an overhaul
Comprising an underground carpark and three levels of open office area, each floor totalling approximately 1,000sqm, the office building along Khyber Pass Road was completed and put into use in 2007.
“After that, due to change of owner and tenant requirements, there were minor changes to the internal layout, but overall it has maintained the nature of an office building,” says Henry Fan, technical director at Argus Engineering. “Since 2021, due to the impact of Covid-19, the ground and first floors have been vacant – while the second floor has been in operation as the owner’s office.”
The existing system
Operating via a two-pipe fan coil unit (FCU), the existing air conditioning system’s air-cooled chiller on the roof of the diesel generator room behind the main building provided chilled water at a temperature of 6-12ºC, with the total cooling capacity 332.2kW.
“The chilled water is sent to the FCUs distributed on each floor through the piping system. In winter, heating was provided by an electric heater installed on each FCU. The indoor air conditioning temperature was set at 23ºC and the BMS automatically selected the cooling and heating modes,” explains Henry.
After more than 16 years of operation, the existing air conditioning system had the following problems:
• The air-cooled chillers were leaking refrigerant due to ageing and corrosion of pipelines, resulting in a gradual loss of cooling capacity.
• Heating in winter used inefficient and backward electric heaters, which consumed considerable electricity.
• The automatic control system was ageing and partially malfunctioning. Users were unable to read data and use relevant settings, which affected both indoor comfort and the economical operation of the air conditioning system.
Equipment procurement and installation
“According to the ordering parameter requirement provided by the services consultant, we decided to select two air-to-water modular heat pump units manufactured by Midea, which have both heating and cooling functions,” says Henry.

Comparison of electricity bill
One or Argus Engineering’s business partners, Yans Homes, completed the plant room renovation, including:
• Removal of the existing scrapped air-cooled chiller units and pipelines;
• Installation of new air-cooled Midea air-cooled chiller units and pipelines;
• Power supply wiring of the new units;
• Installation and wiring of BMS sensors;
• Installation and wiring of the BMS gateway;
• Pipework insulation;
• Pipework flushing and pressure testing;
• T&C.
The plant room renovation started in early June 2023 and ended in late July, before entering the T&C stage. With the upgrading and transformation of the air conditioning system – especially with the changes in heating methods – it was also imperative to upgrade the BMS to adapt. Direct Control, who is maintaining the existing BMS in the building, completed the upgrade work.
To verify the energy saving outcome for heating mode, three months of electricity charges were compared between 2022 and 2023 as below, demonstrating a significant difference.