
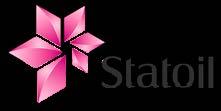
Underwater technology will have a massive impact in the years ahead. Vast resources require reliable underwater technology to be developed. About 71% of the surface is covered by ocean and Subsea wells stand for only 10 % of the world’s oil and gas production. To compete with onshore oil & gas we must keep costs down and use remotely operated installations which will be the future for the oil and gas industry. Subsea wells will be the preferred solution for most offshore developments if we can keep the cost level down, increase recovery, operability of well interventions preferable year around, and improve reliability.
It’s up to all of us in the subsea business to demonstrate that subsea installations are the preferred solution in terms of safety, environment, capex/opex and reservoir drainage. In many cases, we will most likely experience a mix of subsea or unmanned wellhead platform and unmanned production platform or existing manned platform.
We know that the oceans are the future of major priority areas like fish farms, mineral extraction on the ocean floor and wave, wind and tidal power stations. In all these areas, we have great business opportunities using the best available technology, searching across the various industries operating in the ocean room.
The Underwater Technology Foundation is a non-commercial entity. Any surplus from the conference is allocated to grants for educational purposes. The overall objective of the foundation is to promote increased knowledge of the subsea sector. This is something the foundation will achieve through UTC which also features an exhibition open to everyone interested in learning more about subsea, and with a high level technical programme.
FREE WIFI TO UTC DELEGATES:
Wifi: UTC 2017
Password: underwater
CONFERENCE PROCEEDINGS:
Presentations will be available for delegates at www.utc.no, after the conference (will be published during week 26/27).
Password: utc2017
TRANSPORTATION TO THE AIRPORT
Airport shuttle after the conference: There will be buses to Bergen Airport Flesland immediately after the conference, 22 June at 15:45 from Grieghallen.
Taxi: Security at the entrance can help calling for taxi Bus: The bus station is only a 4 minute walk from Grieghallen
HELP DESK
Please contact technical organizer Possibility AS if you have any questions. The Help Desk is located at the entrance
TECHNICAL ORGANISER Possibility AS
Kanalveien 11
NO-5068 Bergen Norway
E-mail: utc@possibility.no
CONTACT PERSONS:
USEFUL PHONE NUMBERS
Medical emergency: (+47)113
Police: (+47)112
Fire: (+47)110
Bergen Taxi: (+47) 07000
Norgestaxi: (+47) 08000
LUNCH AND REFRESHMENTS
You find coffee and refreshments buffets in the Exhibition from morning to the afternoon. Lunch will also be served in the Exhibition.
ALLERGIES
All buffets have allergen listings. Please contact the waiters if any questions.
UTF commends the Program Committee for their efforts in putting together a highly topical program that we are very proud of and much looking forward to learn from. The cooperation in this great group of subsea professionals motivates us to further develop the conference to be the preferred international arena for discussions for the future underwater technologies and system solutions. With great challenges ahead, it is important that individuals from major subsea operators from all over the world gather together with suppliers and service providers to share initiatives, developments and solutions. We will provide the collaborative environment for you all to thrive.
As in 2016, the UTC Day Zero seminar will be arranged at USF Verftet hosted in collaboration with our valued partners DNB and GCE Subsea. The theme this year is Subsea Market Insight, and provides us with insights and updates on investors strategies and assessments, capital market influence and adapting to achieve competitiveness. The Icebreaker event will take place at the same venue later in the evening. Join us for an informal networking event at this unique culture arena. Meet fellow delegates, exhibitors and speakers, while enjoying tasty tapas and drinks at Bergen’s largest terrace by the sea. The focus this evening is to network in relaxed surroundings before the conference proceedings start Wednesday morning.
Since last year the UTF has been strengthened and we are very pleased that both Subsea 7 and GCE Subsea have joined the foundation
UTF and GCE Subsea have solid cooperation on common objectives. UTF was a strong contributor to the establishment of this Norway’s subsea cluster -now a Global Centres of Expertise. The UTC conference is one of the most important projects for the partners. Now UTF and GCE Subsea have joined forces to strengthen UTC and will as equal partners further develop UTC as the world’s most important Underwater Technology Conference Many thanks to our sponsors, exhibitors, speakers and attendees who are making this conference a great success! We look forward to a rewarding conference and welcome you to Bergen in June!
On behalf of UTF
Tor Willgohs Knudsen Chairman of the Board, UTFREGISTRATION, HOTEL RESERVATIONS AND ACCOUNTING:
Lene Vikre, Registration and Accounting Manager
E-mail: lene.vikre@possibility.no
Phone: +47 916 94 214
UTC EXHIBITION:
Ståle Eiken, Exhibition Manager
E-mail: stale.eiken@possibility.no
Phone: +47 928 05 779
CONFERENCE MANAGER:
Irmelin Grønevik, Project Manager UTC
E-mail: irmelin.gronevik@possibility.no
Phone: +47 922 37 093
SPEAKER CONTACT:
Stina Boge, Project Manager
E-mail: stina.boge@possibility.no
Phone: +47 919 13 845
Organised by: Underwater Technology Foundation
Editor / Project Management: Irmelin Grønevik, Possibility AS
Layout: Lasse Hellen, Bembell AS
Print: A7 Print AS
On behalf of the Underwater Technology Conference Program Committee, our sponsors and exhibitors, it is my privilege and great pleasure to once again welcome you all to UTC.
The subsea industry is slowly recovering from the most severe downturn in the hydrocarbon energy era, and most participants in this business have shaken off the denial, absorbed the consequences and is now looking ahead at how a sustainable future can be secured for subsea oil and gas industry.
The recovery of the hydrocarbon energy market is fragile and influenced by many factors outside our control – however, it is more important than ever that we all make every possible effort to shape our subsea future. On this realization, the UTC Program Committee have decided to challenge all of us to present ideas, experiences, technological innovations, business models and execution models at this year’s conference.
Terje
The Minister will attend UTC June 21st and we are looking forward to his opening speech and his visit to the UTC Exhibition, where he will meet both global operators and suppliers, as well as smaller technology providers and newcomers to the subsea industry.
The response from the subsea community has as always been impressive and proves once again that we are a lean, innovative and strong industry with an incredible drive – all proven by the very impressive line-up of speakers and presenters at this year’s conference – from all over the world and representation from all stake holders in the subsea industry.
I proudly welcome you to UTC 2017, Bergen, Norway.
Nils Arne SølvikChair UTC 2017 Program Committee
President Processing
OneSubsea – A Schlumberger Company
The Underwater Technology Foundation is a non-commercial entity established in 1980 when several large oil-related companies joined forces to arrange the first Underwater Technology Conference in Bergen. At that time, the subsea industry was in its infancy, and the foundation was the first in the world to put on a conference with sole focus on this sector.
Ever since the first UTC, the conference has been a regular event in Bergen. For the first 30 years, it was held biennially, but from 2010 onwards, it became an annual event. In addition to the large Norwegian oil and gas operators and suppliers, the proportion of international representatives is high. The conference attracts between 700 and 1000 participants annually. Hence, this June event in Bergen is an international meeting point for the world’s leading subsea technology companies. New technology is presented and challenges are discussed. UTF hosts and organizes the conference together with GCE Subsea.
of the subsea sector in the Bergen region. This is something the foundation will achieve through conferences such as UTC, which features an exhibition open to everyone interested in learning more about subsea. In addition, the foundation will hold exhibitions and meetings, and will contribute to research and training at university level.
GRANT
To fulfil the latter, the foundation offers a grant available to applicants in need of financial support for a subsea related research or training project. The foundation would like to see more applicants for the grant, and encourages anyone with a relevant project to apply.
In 2017, the Foundation welcomes two new members, GCE Subsea and Subsea 7. The Foundation now consists of Aker Solutions, City of Bergen, CMR, DNV GL, GCE Subsea, NUI, OneSubsea, Sparebanken Vest, Statoil, Subsea 7 and TechnipFMC.
UTF Board:
Tor Willgohs Knudsen, Statoil – Chairman of the Board
Hans Erik Berge, DNV GL
Jarle Daae, Aker Solutions
Jon A. Sværen, OneSubsea Stig Instanes, TechnipFMC
Marie B. Holstad, Christian Michelsen Research
Owe Hagesæther, GCE Subsea (observer)
FROM ITS DEEP UNDERSTANDING OF THE SUBSEA RESERVOIR TO TECHNICAL PRODUCT EXPERTISE, ONESUBSEA IS FULLY ENGAGED IN THE ENTIRE E&P JOURNEY.
Contributed by OneSubsea, a Schlumberger company
Offering a step change in reservoir recovery for the subsea oil and gas industry, OneSubsea provides integration and optimization solutions for the entire production system over the life of the field. OneSubsea combines in-house subsurface and production assurance knowledge with field-proven technology and equipment to deliver solutions that can help customers achieve first oil faster, accelerate production, and increase recovery to maximize the financial return on investment.
The key to optimizing field production is early engagement, whereby one can anticipate challenges, model scenarios and ultimately improve decisions. Through collaboration in this initial phase, OneSubsea experts work together with customers to generate complete subsea development options and enhance equipment architecture design for the life of the field. OneSubsea integrates comprehensive reservoir simulations with detailed well in-network models that incorporate artificial lift options, ESPs, gas lift, and multiphase pumps and recommend a number of solutions to help eliminate future operational issues and avoid the need for costly change orders later in the process.
Through its unique OneSubsea Pore to Process* optimization approach, the company brings together a team of experts from key focus areas to not only design the required equipment but also consider all related field dependencies that could impact equipment life and resulting field operability. Through efficient communication and accelerated execution, this approach reduces risk and uncertainty for our customers so they can achieve their project targets.
OPTIMIZE LIFE-OF- FIELD OPERABILITY
Whether for a new greenfield or mature brownfield, OneSubsea provides services to ensure that the equipment is operating at peak performance and that potential risks are identified and minimized. Through its FRIEND* remote surveillance and diagnostic system, OneSubsea provides 24/7 real-time condition monitoring, providing valuable diagnostic information to customers on the operational performance of their subsea hardware.
As part of the Subsea Services Alliance with Helix Energy Solutions and Schlumberger, OneSubsea is focused on increasing the operating envelope of today’s subsea intervention technology.
By combining its in-depth reservoir analysis and modeling capabilities with decades of subsea engineering experience, OneSubsea can help optimize capex and generate a fully integrated subsea field architecture solution that is designed with the reservoir behavior dynamics and fluid flow characteristics in mind.
Selecting the right equipment can minimize risk and reduce capex, ensuring that the production, recovery, and financial performance goals of the subsea assets are achieved. Additionally, OneSubsea optimizes opex through its detailed assessment of the subsea field performance throughout its lifecycle.
To learn more, visit us at booth number 3
*Mark of Schlumberger
Whether it’s the innovative engineering that goes into designing an efficient field, or the proven technologies that ensure you get the most value out of it, GE Oil & Gas has been helping shape the subsea landscape for over 30 years. And we’re fully committed — with ultra-reliable subsea infrastructure, powerful new digital optimization tools, and a collaborative commercial approach — to helping you shape the future.
Visit us at booth 65.
Discover
and power from control system power. This would remove the need for ROV support vessels. Initial trials of such a system have been ongoing and this summer Oceaneering is contracted to provide an ROV for the e-ROV project as part of a trial. With this kind of future in mind, Statoil is starting to design projects with fiber infrastructure already installed, Ramberg says.
“If we shift to take responsibility for supplier-led solutions – the performance of it – then we make more in depth decisions about what kind of hardware we deliver and be able to optimize and analyze it, for maintenance in a life of field scenario and in a very efficient way,” Sølvik says.
They’ll also have to digitize, he says. “When you tie a change in business model in with digitalization and surveillance, condition-based monitoring, production optimization, production management… you will need to have a platform to achieve these things. You need a digital twin. We need digital responsibility of all our kit.”
Pressure on the industry will also come in the form of carbon emissions reductions, Sølvik says. “It is going to grow in force.” To achieve climate targets set by the 2015 Paris agreement, CO2 emissions need to go down dramatically, impacting sales and how firms operate.
AHEAD OF THE UNDERWATER TECHNOLOGY CONFERENCE (UTC) IN BERGEN THIS JUNE, ELAINE MASLIN SPOKE WITH PROGRAM CHAIRMAN NILS ARNE SØLVIK AND STATOIL’S CHIEF ENGINEER SUBSEA TECHNOLOGY & OPERATIONS, RUNE MODE RAMBERG, ABOUT SOME OF THE TOPICS LIKELY TO COME UP.
While there are signs oil and gas investment might be on the rise, the subsea industry still faces multiple challenges – not least retaining its focus on simplification and cost reduction, facing growing emissions reduction targets and ensuring that there’s a sustainable business going forward.
One answer to all of these challenges could be technology. Subsea production, all-electric and remote operations could help reduce costs and carbon emissions. On the other hand, business and contracting models need to change to achieve and sustain the cost reductions and simplification the industry has been striving toward.
“When the oil price comes back up and projects start to get sanctioned, will we then go back to the normal oil industry capacity frenzy and cost escalation,” asks Nils Arne Sølvik, chair UTC 2017 program committee/president, OneSubsea processing systems. “What do we do now to avoid that? One of the things we are focusing on is all-electric, which could be, I think, an important cost reduction technology. We just need to make sure that when interest picks up that we stay focused on benefiting from these technologies, otherwise we will go backwards and we will be back on the cost wagon.”
Rune Mode Ramberg, chief engineer subsea technology and operations, Statoil, who is also on the UTC program committee, adds: “The current challenge is a lot about simplifying the system. Going all-electric is a way to remove hydraulics and simplify the system.”
This push, as well as a growing emphasis on CO2 reduction, reducing chemical leakages, enabling flexible systems, and allelectric becoming more competitive, is driving momentum in this space. He says there will be much more development and much more installation of all-electric in a couple of years.
All-electric also feeds into the digitalization space, enabling more information to be sourced from the seafloor.
“The first parts of the system are already out there working,” Ramberg says. “Electric actuators are available and in operation. Åsgard subsea compression is an electric system.” Statoil is planning a DCFO (direct current fiber-optic) combined cable for power and controls for its Johan Castberg floating production development (OE: August 2016), providing power to valves and communication. “DCFO technology is an important step going forward, in digital and electrification. I believe in simplicity, I believe simple solutions will survive,” Ramberg says. The next step is high voltage power distribution, he adds.
Subsea field remote operation is another strong topic at UTC. Statoil is playing in this space, too. The firm has an e-ROV concept that envisions a remotely operated vehicle (ROV) stationed in the field and operated from shore, with fiber-optic communications
But, the future of the industry is not just about technology. Could contracting models shift from procurement practices that drive price and capacity heat to more performance-based contracts, asks Sølvik.
“The traditional set-up is high-quality, installed and delivered on time,” he says. “The contractor has a focus on executing project delivery and hardware and then lets the operator run it. If it is a performance-based structure, the contractor knows they have to live with what they deliver. If they don’t deliver high-quality, there is risk to their reputation and the next job and you hit the value stream and cash flow.
“Instead, the end client could look at how much oil we get out and then pay for the production. Or maybe the focus could be on performance, in terms of availability requirements,” Sølvik says. Indeed, in the offshore renewables market, contractors have increasingly been taking equity stakes in projects, as well as acting as lead contractors, aligning the project’s performance with their own goals. TechnipFMC’s SVP in Norway has noted that the company is considering doing something similar in the oil business. Indeed, floating production system providers already also work on production-based contracts. The airline industry has also been through such a change, going from having their own huge internal engineering teams, to their jet engines now being owned and maintained by the likes of GE, points out Sølvik. “We might need such a shift as well. Contractors will have to take greater responsibility,” he says.
“That will have an impact on oil consumption, but gas will still need to grow,” Sølvik says. “And the focus on gas is important for us, and means using technology that can reduce emissions. I think subsea has a major role to play in that picture. The efficiency budget for a platform-based development with old fashioned artificial lift methods is much worse than a complete subsea tieback to infrastructure or to shore. Using modern artificial lift methods –boosting, compression, downhole boosting – that’s much more efficient than a traditional water injection system or gas-lift system. Those are also topics that will be important.”
Written by Elaine Maslin, Editor, OE First published in OEAt a time when the oil and gas industry is intensely focused on lowering CAPEX and OPEX costs, Subsea 7 is developing a number of related technologies to enable subsea field architecture for production via very long-tie-backs, typically over 50km for oil-dominated flowlines.
The company aims to achieve a situation where remote fields can be tied-back to existing subsea facilities over longer distances than is currently possible, and more economically than with FPSO or platform-based alternatives.
To do this, it is currently identifying design drivers to define the optimal distances for passive insulated, actively heated and cold flow transport pipelines for thermal management, along with their smart combination with subsea pumping.
Active heating technologies are currently based on topsides power distribution, which by default limits the length of the flowline that can be heated. Subsea 7 is combining subsea electrical power distribution with its existing highly efficient Electrically Heat Traced Flowline (EHTF) technology to greatly extend the range of active flowline heating.
EHTF is based on a thermally-enhanced Pipe-in-Pipe (PIP) design which requires lower power requirements than Direct Electrical Heating (DEH).
To maintain a constant fluid temperature at every location along a flowline requires a remediation of potential “cold spots”. Given the higher U-values of connections, structures or line-ends, when compared with the PIP flowline, this can result in overheating which compromises the power efficiency of the system.
For long-distance tie-backs, Subsea 7 has addressed the issue of cold-spot management through added insulation, local increases of heating power and the innovative re-design of key components, including the “Thermally Efficient Ring Arrangement” (TERA), which complies mechanically with reeling conditions while mitigating heat losses.
It has also extended the reach of EHTF tie-backs by developing efficient subsea electrical distribution systems, based on reliable, low-maintenance components, which supply the EHTF heating elements at regular locations along a flowline.
This system greatly extends the length of heated flowlines and offers greater operational flexibility and reliability, while also allowing power outputs to be adapted to changing heating requirements via simple switching controls.
As tie-back distances increase beyond the capability of active heating systems, flow assurance strategy moves from “maintaining the temperature above hydrate formation temperature” to “transporting under ambient temperature conditions”. The latter is denoted “Cold Flow”.
This Cold Flow Technology (CFT) approach requires Subsea Processing (SSP) facilities near the field and is especially valuable for long distance subsea developments without infrastructure, like in the Arctic. One potential strategy for achieving a safe cold flow condition in the development of large marginal fields is based on utilising a large-scale subsea cooler which bring down the temperature to that of ambient sea water. This new subsea processing function denoted Wax Control Unit (WCU) is based on mainly proven technologies.
Subsea 7 is defining the optimum distances for favourable Cold Flow Systems (CFS’s) when compared with actively heated flowlines.
Subsea 7 is currently assessing the boundaries of applicability for CFS’s for various tie-back distances and host platform alternatives, but the concept enables longer tie-backs at a lower cost than with FPSO or platform-based processing solutions.
Pre-assembled pipeline Bundles are another extremely effective technology for extending subsea infrastructure lifespans and reducing field development costs, since they can incorporate hot water circulated close to the production pipe within the Bundle cross-section.
Subsea 7 is currently assessing the efficiency of circulated hot water in longer and multiple Bundles, with its longest installation to date being a 27km Bundle.
The company is also developing direct bundle-to-bundle connector systems that improve the economics for longer tie-backs, and, with hot water systems, these have the added technical advantage of heating the bundle-to-bundle interconnecting spools.
These technologies enable the prospect of total subsea production facilities with no requirement for manned platforms, transforming the economics of field development in areas lacking existing infrastructure or beyond helicopter reach.
This enhanced subsea capability will allow the future development of brownfield and remote reservoirs which have previously been regarded as uneconomic prospects using traditional platform-based technologies.
UTF PROMOTES YOUNG TALENT, AND THROUGH AN ABSTRACTS COMPETITION FOR STUDENTS AT MASTER OR PHD LEVEL IN THE FIELD OF SUBSEA TECHNOLOGY, THE COMMITTEE HAVE SELECTED THREE STUDENT PRESENTATIONS TO BE INCLUDED IN THE TECHNICAL PROGRAM.
Please welcome the students and attend the student presentations Thursday morning. The UTC delegates get the opportunity to see what the new generation of subsea technologist are focusing on, which methods they use to achieve optimized usage, lower cost, and how they face design challenges and more complex operational environments.
Attendance at the UTC conference gives the student the possibility to meet technologists from most of the major operators and suppliers in the international subsea community. As a speaker at UTC, the student will get invaluable exposure to future employers and an international network in the industry.
The featured students receive complimentary conference fee, flight fares and hotel accommodation for the duration of the conference, sponsored by the Underwater Technology Foundation.
The Underwater Technology Foundation sponsors all subsea students with delegate passes to the conference. Students can apply to get free attendance at the conference proceedings and lunches.
Read more about UTF´s focus on students and the promotion of subsea knowledge at www.utf.no.
THE MARKET INSIGHT SEMINAR ON DAY ZERO WAS INTRODUCED AT UTC 2016, AND WILL AGAIN OFFER A NICE WARM-UP TO THE MAIN CONFERENCE IN GRIEGHALLEN, BERGEN. THE SUBSEA MARKET INSIGHT SEMINAR IN 2017 IS HOSTED IN COLLABORATION WITH VALUED PARTNERS GCE SUBSEA AND DNB
The program for Day Zero, June 20th, will be focused on providing an insight into the Subsea Market, and is divided into three main themes:
• Market Analysis
• Industry Outlook
• Investors and Entrepreneurship
UTCs core asset is the high quality technical program. Still, in the current market climate, a deeper insight into both market and investors is of interest to both engineers, economists and academics. We would like them to meet and share their thoughts for the future. These critical issues deserve more extensive attention than what we are able to include in the format of the main conference program. This year’s seminar will take place at USF Verftet, where the Icebreaker will be arranged in the evening.
Torbjørn Kjus, chief oil analyst at DNB Bank in Norway, is today recognized as one of the world’s leading oil industry commentators, and is one of the key note speakers at the Subsea Market Insight seminar.
Mr. Kjus was one of the first oil price contrarians and has since 2011 provided regular updates to the US Treasury Department in Washington DC on oil prices and the global oil market. He argued early in 2012 that international oil prices would stabilise and even drop as the US shale oil industry would be a game changer for the global oil market. He has 15 years of experience in the oil industry and is a well-known name in this space. He provides regular updates of the oil market to the Norwegian Ministry of Petroleum and is frequently interviewed/quoted in media. Prior to joining DNB, his previous role includes more than 5 years as an oil market analyst and oil trader at Norsk Hydro in Oslo and BP in London.
13:30 – 14:00
REGISTRATION AND COFFEE
14:00 – 14:05
Welcome by Carl Andreas Holm, Boston Consulting Group
Market Analysis
Key factors impacting oil prices the next 5 years
14:05 – 15:00
Torbjørn Kjus, Oil Analyst, DNB Markets
The subsea market- outlook and uncertainty
15:00 – 15:20
Eirik Reiso, Partner and Subsea Expert, Rystad Energy
15:20 – 15:40
Coffee break
Industry Outlook
The Outlook for the oil & gas industry in 2017 - Short-term agility, long-term resilience
15:40 – 16:00
Kjell Eriksson, Regional Manager Oil & Gas, DNV GL
Energy perspectives 2017
16:00 – 16:20
Elisabeth Aarrestad, Vice President Analysis, Statoil
Boosting our Innovation Era
16:20 – 16:40
Thomas Sunde, VP Technology, Subsea 7
Aker Solutions’ perspective on the industry outlook
16:40 – 17:00
- cost reductions, sustainability and efficiency improvements
David Clark, Executive Vice President Services, Aker Solutions
17:00 – 17:20
Coffee break
Investors and Entrepreneurship
Entrepreneurship to the NXT level
17:20 – 17:35
17:35 – 17:50
17:50 – 18:10
18:10 – 18:30
Erlend Waaler, Relations Manager - Startups and Growth Companies, DNB ASA
A journey through subsea entrepreneurship
Mark Bokenfohr, CEO, WiSub
Growth Investments in the Oil & Gas Industry
Rune Jensen, Senior Partner, Energy Ventures
Venturing to Shape the Future of Energy
Kristin Aamodt, Managing Director Statoil Technology Invest, Statoil
18:30 – 18:35
Closing remarks
19:30 – 22:00
Icebreaker
08:30 – 09:30
Badge pick-up and coffee
Welcome
09:30 – 09:40
UTC Program Committee Chairman Nils Arne Sølvik and Conference Moderator Simon Davies, Statoil
Opening speech
09:40 – 10:00
10:00 – 10:20
10:20 – 10:40
10:40 – 11:00
11:00 – 11:45
Terje Søviknes, Minister of Petroleum & Energy
Deepwater and the Future of Energy
Robert Patterson, Executive Vice President Engineering, Shell
Subsea, a margin business going forward?
Torger Rød, Senior Vice President Project Development, Statoil
Good projects are more than look for lower breakeven
Cristina Pinho, Executive Manager Subsea Engineering, Petrobras
Coffee break and exhibition
Panel discussion:
Introduction by Tore Halvorsen, EVP and Senior Advisor, TechnipFMC
• Knut Nyborg, Head of Front End, Aker Solutions
11:45 – 13:00
• Rod Larsson, CEO, Oceaneering
• Robert Patterson , EVP Engineering, Shell
• Cristina Pinho, Executive Manager Subsea Engineering, Petrobras
• Torger Rød, SVP Project Development, Statoil
• Nils Arne Sølvik, President Processing, OneSubsea
Moderator: Simon Davies
13:00 – 14:30
Lunch and exhibition
PARALLEL SESSIONS, TRACK 1 - 3
14:30 – 16:00
– SEE DETAILED PROGRAM, PAGE 18-19
16:00 – 16:30
Coffee break and exhibition
PARALLEL SESSIONS, TRACK 1 - 3
08:00 – 09:00
Morning coffee and refreshments in exhibition hall
Students @Klokkeklang
Session leader: Marie B Holstad, CMR and Terje Clausen, Subsea 7
Possibilities and Implications by Designing an Aluminium Integrated Template Structure
08:30 – 08:50
Henrik Nesheim and Kjell Petter Løkling Lunde, Master students Subsea Technology, NTNU
Wax Control for Long Distance Tie-back of Subsea Production Systems
08:50 – 09:10
09:10 – 09:30
Yury Novoseltsev, PHD Candidate & Engineer, NTNU/ Subsea 7
Formation of gas hydrates monitored with dielectric spectroscopy
Kjetil Haukalid, PHD Candidate, University of Bergen/ CMR
PARALLEL SESSIONS, TRACK 1 - 3
09:30 – 11:00
– SEE DETAILED PROGRAM, PAGE 18-19
11:00 – 11:30
Coffee break and exhibition
Plenary session @Peer Gynt
Is Subsea Services Ready for a Digital Future?
11:30 – 12:00
12:00 – 12:30
12:30 – 14:00
Rod Larson, CEO, Oceaneering
New Era of Partnering
Stuart Fitzgerald, VP Technology & Strategy, Subsea 7
Lunch and exhibition
PARALLEL SESSIONS, TRACK 1 - 3
14:00 – 15:30
– SEE DETAILED PROGRAM, PAGE 18-19
16:30 – 18:00
– SEE DETAILED PROGRAM, PAGE 18-19
19:30 – Conference Dinner
15:45 – 16:00 Summary and closing
Field Development/ System Solutions
Session leaders Johan Mikkelsen, Perestroika and Tom Eddy Johansen, TechnipFMC
14:30 – 15:00
Ormen Lange Late Life Recovery
– Moving in the Right Direction
Anthony Protheroe-Winters, Norske Shell
Subsea Power, Controls And Umbilicals
Session leaders Merethe Paasche, Oceaneering and Jarle Daae, UTF/Aker Solutions
Challenges with combined power and control umbilicals
Steinar Midttveit, Statoil
Surf, SPS and Marine Operations
Session leaders Tim Crome, TechnipFMC and Tonje Dahl, ClampOn
Rigid riser repair at 1250 msw, a world first André Midtun, and Pål Magne Hisdal, Connector Subsea Solutions
15:00 – 15:30
Modular Compact Pump Systemt
Pierre-Jean Bibet, Total E&P and Aslaug Melbø, GE Oil & Gas
15:30 – 16:00
Technical challenges in design and application of EHT PiP for development of a long subsea tieback field development
Alireza Forooghi, VNG Norge
16:00 – 16:30
Coffee break and exhibition
Managing surge conditions in subsea gas compression with electrical actuator
Kristin Moe Elgsaas, GE Oil & Gas
Multipurpose Workover Control System: Experience and Lessons After 4 years in Operation
Christian Bøhmer, Aker Solutions
Application of Large Diameter Steel Lazy Wave Risers for Production Systems in Deepwater Norway Rohit Shankaran, 2H Offshore Engineering Ltd
Open PLET system – radical simplification to the installation of pipeline end terminations (PLET) for large size export pipelines Mohammed Hasan Ali, GE Oil & Gas
Track
Field Development/ System Solutions
Session leaders Johan Mikkelsen, Perestroika and Rolf Røssland, NUI
09:30 – 10:00
Strategies, methods and tools for development of subsea fields
Karl-Petter Løken, Lundin Norway
10:00 – 10:30
How subsea tiebacks may be enabled by use of alternative and fit-forpurpose technology
Tim Nallipogu, Woodside
10:30 – 11:00
Remote ROV Piloting – Using innovative technology to reduce costs
Arve Iversen, Oceaneering AS
Track 2@Klokkeklang
Asset Management/ Increased Recovery/ Life of Field Solutions
Session leaders Per Christian Eriksen, Aker Solutions and Tom Eddy Johansen, TechnipFMC
High Boosting a Satellite Field with Record Step-Out Distance
Mike Clarke, Murphy Oil and Arill Småland Hagland, OneSubsea
Tordis Subsea Separation: Operational Experience Nikola Lazarevic, Statoil
SPRINGS®: New Subsea Seawater
Treatment Qualified after Offshore Tests
Stephane Aanres, Saipem
11:00 – 11:30
11:30 – 12:30
12:30 – 14:00
Asset Management/ Increased
Recovery/ Life of Field Solutions
Session leaders Rune M Ramberg, Statoil and Mads Hjelmeland, OneSubsea
16:30 – 17:00 Åsgard Subsea Compression – from qualified to proven technology
Lars Brenne and Svend Tarald Kibsgaard, Statoil
Subsea Power, Controls And Umbilicals
Sessions leaders Bård Espelid, DNV GL and Knut Rognve, ABB
Fail-Safe Functionality on Subsea Trees without Utilization of Mechanical Spring
Cartsen Mahler, OneSubsea and Markus Glaser, University of Aalen
17:00 – 17:30
Shell Draugen Infill: Optimizing late life production with Subsea Boosting
Tatiana Marie Hoeydal, Norske Shell
Subsea Installation Session leaders Martin Dove, BP and Per Christian Eriksen, Aker Solutions
Aasta Hansteen Deepwater Development: Enabling New Frontiers Through New Technology
Kristian Grjotheim, Aker Solutions
Subsea All-Electric Initiative: Status & Way forward Daniel Abicht, Statoil
17:30 – 18:00
Qualification and Development of the World´s First High Pressure Subsea
Boosting System for the Jack and St. Malo Field Development
Øyvind Reimers, OneSubsea
Extending life of brown fields and enabling new standards
Tore Erntsen, Proserv
Installation of world’s first subsea high pressure Thermoplastic Composite Pipe for spool application on Alder Jan van der Graaf, Airborne Oil And Gas
Dynamic modelling for deepwater installation of subsea equipment
Vahid Abdolkarimi, TechnipFMC
14:00 – 14:30
Coffee break and exhibition
Plenary session @Peer Gynt, more information at page 17
Lunch and exhibition
Track 1@Peer Gynt
Field Development/ System Solutions
Session leaders Terje Clausen, Subsea 7 and Aslaug Melbø, GE Oil&Gas
Moho Field development – challenges and achievements. Possible challenges with such field developments when shaping the new subsea future
Joel Cazaux, Total
14:30 – 15:00
Integrated satellite tieback for marginal fields
Dag Jostein Klever, TechnipFMC
15:00 – 15:30
Designing Subsea Production Systems for Efficient Field Startup
Cedric Chidiac, Onesubsea
Track 2@Klokkeklang
Asset Management/ Increased Recovery/ Life of Field Solutions
Session leaders Jarle Daae, UTF/Aker Solutions and Marie B Holstad, CMR
Using Engineering Simulations to create Digital Twins for IoT-Based Predictive Maintenance
Tomas Jakobsen, EDR & Medeso AS
Omnirise Boosting System - Barrierfluid less and With Integrated Variable Speed: Reduces Cost and Increases
Reliability
Alexander Fuglesang, Fuglesangs Subsea As
The Sonsub HyDrone: a resident intervention ROV
Giovanni Massari and Francesco Cavallini, Saipem
Track 3@Troldtog
Subsea Power, Controls And Umbilicals
Session leaders Bård Espelid, DNV GL and Roger Walls, ExxonMobil
Future oriented distribution of power and communication
Bjørn Rasch, Siemens Subsea
A new technology for flexible power distribution to subsea machinery Bjørn Simen Ljønes, Benestad Solutions
Subsea power distribution – Key enabler for next generation subsea production Knut Rognve, ABB
Track 3@Troldtog
Surf, SPS and Marine Operations
Session leaders Tim Crome, TechnipFMC and Martin Dove, BP
Adoption of the Shell Flow Induced Vibration (FIV) Intermediate Screening methodology on OLLLR project Frank Smith, Norske Shell
Light Module Handling Systems on Roll & Pitch Compensated vessels Asmund Sætre, Axtech
Dynamically positioned highresolution subsea laser: - cost effective offshore survey operations, including contactless metrology, reverse engineering and IMR tasks David Rattray, DeepOcean
of our best ideas will never see the light of day.
Not because they are bad, but because they come to life at great depths.
Statoil was born in Norway in 1972 and is today the worlds largest offshore operator. Half of our production comes from our 500 subsea wells. Though Oslo is located hundreds of kilometers from the North Sea, the region is leading the way with innovative thinking within subsea technology. One of these innovators, our subsea engineer William, challenges the impossible every dayat great depths. Knowing that no one might ever see his best ideas.
Learn more at Statoil.com/stories
Statoil. The Power of Possible
June 21st, 14:30-15:00, Track 1@Peer Gynt Ormen Lange Late Life RecoveryMoving in the Right Direction
Anthony Protheroe-Winters, Senior Concept Engineer, Norske Shell
Mr Arne Dahle, Mr Anthony Protheroe-Winters, Mr Anders Svensen, Ms Claire Richardson-Dissel
In 2014, the Ormen Lange Infield Compression (OLIC) project was stopped and recycled back to the feasibility stage due to increasing costs making the project uneconomic. The project was subsequently renamed as Ormen Lange Late Life Recovery (OLLLR) with focus on identifying cost effective concepts that could deliver an economically viable development. The OLLLR opportunity was reframed and passed the project initiation gate (DG1) in February 2016.
OLLLR aims to commercially unlock additional reserves from the Ormen Lange gas field by reducing wellhead pressure on the Ormen Lange subsea wells. The additional volumes can become accessible by lowering landing pressure at Nyhamna, minimizing pressure drop subsea-toplant and/or installing compressors offshore.
In the pursuit of cost effective solutions, the project has adopted a structured approach embedding Shell’s PT2020 mindset in the ways of working from the start with a strong focus on Competitive scoping (CS), supply chain transformation (SCT) and technology & innovation (T&I). The project team has engaged extensively with JV partners and suppliers to evaluate various innovative technologies including subsea separation, subsea compression and subsea VSD, in order to inform concept decisions and develop a technology qualification plan for the project.
Significant progress has been made since the project was recycled. This presentation will discuss some of the key success factors
to date and address challenges to overcome and opportunities that exist to make OLLLR a successful project.
June 21st, 15:00-15:30, Track 1@Peer Gynt
Modular Compact Pump System
Pierre-Jean Bibet, Rotating Machinery Department, Expert in Pumping systems, Total E&P Hans Kristian Sundt, Product Management Subsea Manifolds, Connections, Power & Processing. GE Oil & Gas
The Modular Compact Pump (MCP) is an entirely new subsea pump architecture which does not exist in the industry today. As opposed to conventional pumps, where the motor is connected to the pump with a rotating shaft, the MCP motor is integrated on the impeller itself which is spinning on a static shaft.
The modular approach with stages/groups of stages running independently enables:
- no barrier fluid … process lubricated bearings w/ limited bearing load
- very high boost … distribution of the axial thrust without need of balance piston
- scalable … 320 bar dP @ 60% GVF in a 6MW pump only 6m long
- robust rotor-dynamics … no long rotating shaft that leads to rotor-dynamic limitations
- robust and wider operating envelope … low rotor inertia enables rapid response to fluctuations
- high life cycle efficiency … operates near best efficiency with varying stage rpm
These benefits change the architecture of subsea boosting systems enabling low cost installations with very high pressure boosting capability. This in turn can allow more fields to apply subsea boosting and increase oil recovery, The MCP is under development and a 3 x 125 kw pump is being tested in Q2/Q3 ‘17”.
Total will provide the Operator perspectives on the technology and associated benefits. GE
will present an overview of the concept as well as the key outcomes from testing of a 3-stage prototype.
June 21st, 15:30-16:00, Track 1@Peer Gynt
Technical challenges in design and application of EHT PiP for development of a long subsea tieback field development
Alireza Forooghi, Lead Flow Assurance Engineer, VNG Norge AS Pil and Bue oil and gas discoveries are situated in PL 586 (Blocks 6406/11 and 12) on the southern part of the Halten Terrace in Norwegian Sea. Three different development options are envisaged and studied in the conceptual study phase, including two subsea tieback options to Njord (Statoil operated semi-sub) and Draugen (Shell operated GBS) production facilities located 32 and 65 km away from Pil and Bue fields respectively and an alternative standalone development option, a FPSO, located close by to the subsea templates. Pil reservoir oil is waxy and has a high pour point temperature which makes this development a challenge over such long distances towards the host facilities.
EHT PiP is selected as a technically robust flowline option for the subsea tieback options to Njord which is the selected concept for development of Pil and Bue oil fields. This paper aims to review technical challenges in relation to the design and implementation of this new technology over such long distances in harsh offshore environments and present how it will go through an extensive qualification and testing program leading to a breakthrough in its applications for development of high pour point waxy oil fields in deep waters. The paper also reviews pros and cons of EHT PiP technology in comparison with other active heating alternatives such as DEH single flowline wet insulated and DEH PiP
June 21st, 14:30-15:00, Track 2@Klokkeklang
Challenges with combined power and control umbilicals
Steinar Midttveit, Leading Engineer Electrical Technology, Statoil
This presentation will focus on an incident that occurred on the Gullfaks Subsea Compression (GSC) combined power and control umbilical in 2015. The GSC project comprises two subsea wet gas compressors, each 5 MW. Supply of compressor power, LV power, FO communications, barrier fluid and MEG lines were combined in one common power and control umbilical between the Gullfaks C platform and the compressor station. The complete system, including the 16 km power and control umbilical (PCU) was installed during spring/summer 2015.
Shortly after start-up of the compressors (within 1 month), pressure was lost on some of the fluid lines. Leakages have been identified on 3 of the 7 super duplex steel tubes in the umbilical. The failure mechanism is corrosion related to influence from the power circuits (AC corrosion). This paper will describe the incident, fault finding methods, root cause and results from subsequent analyses and tests. This phenomenon is new to the umbilical industry and the design and manufacture of power and control umbilical do not take this failure mode sufficiently into account today. Analyses and tests have showed that very high corrosion rates can be seen under certain conditions in combined power and control umbilicals. In addition to analyses and test results, possible mitigation actions will be discussed.
June 21st, 15:00-15:30,
Track 2@Klokkeklang
Managing surge conditions in subsea gas compression with electrical actuator
Kristin Moe Elgsaas, Senior Product Manager, Subsea Power & Processing, and Terje Undheim, Product Engineering Manager, GE Oil & Gas
The successful move to subsea compression is a significant milestone for the whole industry. An important part of making this move, was ensuring auxiliary systems to the compressor were adapted to the seabed environment and the required robustness for subsea operation.
A key challenge in compression systems is surge conditions, where flows reverse and cause the compressor to break down. To prevent this, an anti-surge loop is used to circulate flow from the outlet to the inlet when required.
GE has developed the electrical linear AntiSurge Actuator (ASA) specifically to ensure the integrity of this safety-critical system. Unique features of the ASA include ultra-fast operation and the ability to continuously modulate. To enable both modes of operation, the actuator relies on both mechanical and electrical energy. The Anti-Surge Actuator has been through extensive qualification and currently has more than a year of operational experience. The qualified technology building blocks have a number of application areas within the oil & gas industry.
The presentation will provide an introduction to different types of electric actuators, and a technical description of the electric Anti-Surge Actuator.
It will give an overview of the qualification program, and share key lessons based on experience to date including a view of the use of electrical versus mechanical energy in safety critical systems. Finally, the presentation will look at how the Anti-Surge Actuator is integrated into the compression system to provide continuous and reliable protection.
June 21st, 15:30-16:00, Track 2@Klokkeklang
Multipurpose Workover Control System: Experience and Lessons After 4 years in Operation
Christian Bøhmer, Director PLM Workover System &Tooling, Aker Solutions
Jon Lund Larsen, Chief Engineer, Aker Solutions
Traditional workover control systems (WOCS) have been designed and built for specific fields or specific tools. In 2011-2012, Aker Solutions developed a multipurpose workover control system that allows for one control system to be utilized on multiple rigs, performing workover operations on multiple fields. The system is set up to operate tree and tubing hanger tooling, as well as landing strings and open water workover system. This WOCS implements an optimized interface for easy integration of 3rd party XT communication equipment allowing streamlined cross vendor cross field operations.
Compared to a traditional workover control system, this system gives the operators a great flexibility to utilize the same workover control system for a range of different operations on different fields and rigs without any major rework. All systems are built upon a common platform of hardware and software, and the standardized SCADA system can easily be reconfigured for a new application. A dedicated software and support team allows quick mobilization planning and response times are significantly reduced.
Standardization has also allowed creation of a workover control system simulator, giving better onshore training of offshore personnel and testing of procedures before going offshore. This has also allowed building one collective crew to operate a multitude of similar control systems across fields.
Aker Solutions have now delivered 13 multiWOCS™ systems. This presentation will focus on experience and lessons after 4 years in operation, and will also include some case studies of actual savings achieved, especially on mobilization/demobilization cost.
June 21st, 16:30-17:00, Track 2@Klokkeklang
Carsten Mahler, Research Engineer, OneSubsea Professor Dr. Markus Glaser, Volker PhielipeitSpiess, Stefan Schlünß, Stefan Marx, Robert Schreck, Martin Reinhart
Key learning outcome:
Traditional subsea production control systems are based on fixed-mounted actuators which operate Christmas tree valves. Safety functionality is provided by utilizing spring packages. When cutting power to the dedicated tree-SCM the spring pushes the valve back to the fail-safe position. Major shortcomings of this solution are the high power demand to operate the valves (as the spring has to be loaded), the size of such a tree and the loss of communication and therefore also loss of sensor readings in case
of a shutdown.
The new modular All-Electric concept, proposed in this paper, is based on rotary actuators that operate manual valves. Energy for the fail-safe operation is no longer stored mechanically but chemically in a dedicated centralized battery.
The new concept eliminates all above described disadvantages. Especially by reducing the tree footprint and the ability to downsize the power distribution system, cost saving with regards to the overall subsea production system costs (CAPEX and OPEX) can be achieved.
As a battery based fail-safe system is novel to the industry, four partners formed a jointindustry project team and successfully applied for three years of co-funding from the German government to evaluate the described concept.
Each of the partners brings in expertise from its core business (University of Aalen: Research in functional safety – OneSubsea: EPC for Subsea Production Systems – Wittenstein: Supplier for electric actuation systems – SubCtech: Supplier of high-tech marine battery systems) to develop a subsea actuation system that suits all regulatory requirements.
June 21st, 17:00-17:30, Track 2@Klokkeklang
Subsea All-Electric Initiative: Status & Way forward
Daniel Abicht, Leading Advisor Subsea Control Systems, Statoil
Inge Helge Knutsen
Statoil has launched an All-Electric Subsea (AES) initiative to prove the feasibility of new flexible, cost efficient subsea production system (SPS) to meet future demands. While most of the main technology elements are available and proven in use, full market and operator acceptance seems to be a challenge.
Targeting a system approach and examining the impact on all elements of a subsea development, i.e. topside, umbilical, SPS, and downhole will ensure proper reflection allelectric solution benefits. Thus, in co-operation with the supply chain, the strategy for the AES initiative is to identify all electric concepts in order to establish cost effective solutions and strive for standardisation of products and interfaces.
This contribution will look at the experiences gained with existing all electric installations such as Åsgard Subsea Compression which have been enabling for the initiative, explain the fundamental features of the subsea all-electric technology. Furthermore, it will address the potential of this technology for operation in production control systems. It will also enlighten the status of the all-electric initiative with respect to associated technology maturity along with a description of the activities required to close these gaps.
June 21st, 17:30-18:00, Track 2@Klokkeklang
Extending life of brown fields and enabling new standards
Tore Erntsen, VP Subsea R&D, Proserv When a subsea development is conceived many aspects and assumptions have to be taken into account before securing investment and approvals. At the onset of the system implementation no provision has generally been put in place to address obsolescence, reliability and the ability to extend operational life and/or enhance the development performance.
One Statoil asset in the north-sea wanted to refurbish subsea control modules where the
OEM stated obsolescence. Statoil challenged the statement by bringing a third party company onboard to refurbish the modules. By breaking out from “mainstream” and challenging the market Statoil managed to upgrade and utilize existing asset instead of scrapping. The conclusion and solution from this project will be presented, both technically and financially this is a strong concept. Challenging tasks are integration of the new equipment into existing infrastructure without adding substantial downtime and cost to the asset, by combining new standards and existing specifications we showed that this is a viable solution. The extended system generally provides the benefits of modern technology such as remote diagnostic support on an increased performance system. Interfacing to the existing topside equipment like DCS will also be discussed and different solutions be presented. The North Sea has a large number of aging assets set within an extensive infrastructure built up over the years. Several different steps can be used to achieve system upgrade, changing minor parts and test up to a full refurbishment cycle with SEM change-out.
June 21st, 14:30-15:00, Track 3@Troldtog Rigid riser repair at 1250 msw, a world first André Midtun, Senior Project Manager / Pål Magne Hisdal, Sales Manager, Connector Subsea Solutions “Even highly complex deepwater operations can be broken down to a sequence of actuated rotations and translations; the challenge is to manage risk and reliability”
2 off 4” risers in a hybrid riser tower, offshore Angola were damaged during installation. This paper will describe the methods and equipment developed to cut the damaged section out and replace with flexible spools to re-instate riser integrity.
Connector Subsea Solutions in Bergen, Norway was in 2015 contracted to develop a riser repair spread for a major E&P company operating in deep water offshore Angola. An extensive toolkit was designed, built and tested to enable cutting of riser, jack out the riser to get access to the end, remove coating, deburr and machine the pipe end, hang off connection tooling and connector, align install and activate connector, pressure test, mill out buoyancy in a tight space and install securing aids to arrest dynamics and reduce potential fatigue damage. The tooling was designed lightweight to allow ROV handling subsea, as crane deployment into the tight space on the riser tower would cause significant risk of damage by accidental transfer of large forces from the crane wire. Reliability, fail-safe design and risk management were all important design aspects. Testing was extensive, including subsea testing with ROV operations. The design of the support clamp that secures the new spools included more than 2000 hours of advanced nonlinear Finite Element Analysis encompassing elastic-perfectly plastic analysis cases.
June 21st, 15:00-15:30, Track 3@Troldtog Application of Large Diameter Steel
Lazy Wave Risers for Production Systems in Deepwater Norway
Rohit Shankaran, Senior Engineer, 2H Offshore Ali Anaturk, Hugh Howells, Marcelo Lopes
In the current market, innovative low cost solutions are necessary for development of new fields and late life recovery from existing fields. Steel Lazy Wave Risers (SLWRs) provide low cost alternatives to flexible risers and offer flexibility during design and late life for Floating Production Systems (FPS) in deepwater North Sea. While flexible risers are limited to a maximum of 16” inner diameter, steel risers are qualified for outer diameter pipe of up to 24”, which can help reduce the number of risers tiedback to the FPS and lowering development costs.
Deepwater fields in the North Sea greater than ~400m water depth have traditionally been developed using flexible risers. SLWR configuration, a variation of the steel catenary riser (SCR) with added buoyancy near the touchdown, have recently been deployed in the GoM and Brazil for deepwater applications.
Due to simplicity of design, good track record, qualified supplier, fabrication and installation methods for SCRs, SLWRs have become a logical extension for more severe environments and vessel motions. Harsh North Sea environments result in high FPS motions. Buoyancy installed on SLWR, helps decouple vessel motions at the riser touchdown, which results in improved strength and fatigue performance.
Development of a 24in SLWR for North Sea application in 850m water depth is discussed. The effect of wall thickness, hang-off location, departure angle and buoyancy distribution on design is evaluated and the resulting riser arrangement described. The advantages and disadvantages of SLWR’s North Sea applications are assessed and costs for flexibles and SLWR’s compared.
June 21st, 15:30-16:00, Track 3@Troldtog
Open PLET system – radical simplification to the installation of pipeline end terminations (PLET) for large size export pipelines Hasan Mohammed Ali, Product Manager, Manifolds and Connection System, GE Oil & Gas
A few key learnings in installing large bore export pipeline end terminations (PLET) can be listed as follows:
-Difficulty to handle the PLET structure onboard the installation vessel and larger deck space needed
-Size envelope restrictions on the PLET structure while passing through the tensioners and pipe lay-vessel stinger
-Personnel safety and vessel time to integrate large PLET to the pipeline on-board the vessel
To cope with these challenges, An Open PLET system with lift & shift method has been deployed on few live projects with the following demonstrated benefits:
-Significantly less space required on the vessel
-Simplified pipe laying operation due to exclusion of PLET structure on-board the vessel
-Use of the standard GE connection system
-The PLET Structure can be installed on seabed on a ‘convenience basis’ as weather allows and wet stored until integration with pipeline
-Design offers simplicity and robustness to enhance reliability and safety
-Associated cost savings
A recent successful deployment was on Ichthys
42” gas export trunk line PLET connection. Further improvement of the concept has been made to further optimize cost of final PLET integration on the seabed. In contrast to the original system, in this method the PLET Skid is landed out directly over the pipeline and skid will be well captured within the pipeline
thereby eliminating any need of pipeline shifting operation.
Design details will be presented to elaborate the Open PLET and how this has positively impacted the install-ability of Large-bore export pipelines in challenging deep-water projects.
June 21st, 16:30-17:00, Track 1@Peer Gynt
– from qualified to proven technology Lars Brenne, Specialist Rotating Equipment / Svend Tarald Kibsgaard, Principal Researcher Rotating Equipment, Statoil
The presentation is describing operational experiences with the Åsgard subsea compressor technology towards TR7 approval. Relevant subjects are; actual machine load/utilization, machine performance and impact of the subsea environment.
A large step towards higher recoveries from gas fields was made in 2015. The first Åsgard subsea compressor was put in operation mid 2015 after a technology development period of 20 years. The technology basis is based on an all-electric compressor concept with a high total efficiency meeting future low carbon requirements. The subsea compressors have been utilized at the maximum capacity during normal production, accelerating and increasing production rates from the Midgard and Mikkel reservoirs. The compressor performance, including rotordynamic behaviour subsea, has proven to be similar with experiences gained from the test pit environment at K-lab.
After qualifying the compressor technology at K-lab in submerged condition in 2014 the first subsea compressor reached 10 000 operating hours in December 2016. The compressor technology thus meets Statoil TRL7 requirements, the step from qualified to proven technology.
June 21st, 17:00-17:30, Track 1@Peer Gynt Shell Draugen Infill: Optimizing late life production with Subsea Boosting Tatiana Marie Hoeydal, Subsea Systems Team Lead, Norske Shell
The Draugen field, operated by Shell Norway in the North Sea, started the oil production in 1993. It has a concrete mono-column platform with integrated topsides located in 250 m water depth with a number of subsea wells. In recent years Shell Norway has executed series of projects extending the life of field to 2023 and beyond. The presentation will discuss Draugen Infill, one of these lifetime extension projects . This includes the addition of a subsea boosting pump station, four subsea wells, one manifold, and number of flowlines and umbilicals plus all supporting topsides facilities including pump control systems.
Execution of the project has been both challenging and exciting and a number of technological solutions had to be found to adapt the changing project strategy. The presentation will provide insights into the successes and lessons learned of the project; its contribution to extend the late life of the field; and operational experiences of optimizing recovery with Subsea Boosting Pump.
June 21st, 17:30-18:00, Track 1@Peer Gynt
Qualification and Development of the World´s First High Pressure Subsea
Boosting System for the Jack and St. Malo Field Development
Mads Hjelmeland, Global Sales Director Subsea Processing, OneSubsea
Øyvind Reimers, Dan Broussard, Chris Hey
The Jack and St. Malo fields were developed in a deepwater Gulf of Mexico (GoM) setting by Chevron and co-owners and commenced production in 2014. The Jack and St. Malo fields were developed with subsea completions flowing back to the Walker Ridge Regional Platform, the largest, by displacement, semi-submersible floating production unit in the GoM.
The Lower Tertiary trend in the GoM poses a number of challenges for flowing reservoir fluid from the sand face to surface facility. The key challenges are related to low permeability, high pressures, high temperatures, as well as water and well depths.
The naturally high pressures driving Jack and St. Malo fields during the early stages of development will decrease over time. To compensate, and maintain production levels, it was decided to deploy three powerful subsea pumping systems on the seabed to boost fluids from the wells to the host platform. While a number of subsea boosting systems have been deployed previously, the Jack and St. Malo fields required technology qualification in order to meet design requirements in terms of water depth, pressure rating and shaft power.
This paper will describe the technology qualification program of the world’s first high pressure seabed boosting system, as well as the subsequent delivery project and deployment of three subsea boosting systems in the Jack and St. Malo fields. An overview of the drivers for selecting this technology will be provided, as well as insight into early operational experience from the field.
June 21st, 16:30-17:00, Track 3@Troldtog
Aasta Hansteen Deepwater
Development: Enabling New Frontiers Through New Technology
Kristian Grjotheim, Head of Installation and Well Intervention Services, Aker Solutions
Christian Bøhmer, Lead Engineer AHA WOS, Statoil
Morten Johansen, Project Manager AHA, Statoil
Brynjar Vist, Specialist Engineer Workover Systems, Aker Solutions
Jonas Åkerlund, Lead Engineer Workover Systems, Aker Solutions
Erik Tømte, Manager, Innovation Practices, Aker Solutions
Ann-Kristin Takle
Statoil’s Aasta Hansteen subsea project is a major deep water gas development located north of the Arctic Circle and 190 miles from shore, west of the city of Bodø in Norway. The development is a new deep water frontier in Norwegian water and it is characterized by its remote location and harsh environment.
This presentation will focus on the key challenges identified by Statoil prior to the
investment decision of Aasta Hansteen, and how these where solved though new technology and system solutions, including:
• New template design optimized for rapid installation in harsh weather
• Guideline less system for deepwater installation of manifold, XTs and LRP/EDP
• Rigid lock down system on WH to reduce fatigue
• New optimized deepwater open water workover system
The presentation will also discuss some of the fundamental challenges related to operation of riserbased completion and workover systems from dynamically positioned (DP) semisubmersible rigs in deep water and harsh environment, including:
• Personnel safety on rig-floor
• HSE for riser based weak links, especially important for high gas oil ratio applications
• Challenges with achieving sufficient strength and fatigue capacity for workover riser systems
• Risk of lost rig time in harsh
This presentation is jointly developed by technology experts from Aker Solutions (SPS provider) and Statoil (Operator on the Aasta Hansteen field), and will include key lessons from the Aasta Hansteen project, with focus on how to successfully introduce new technology in a delivery project.
June 21st, 17:00-17:30, Track 3@Troldtog
Installation of world’s first subsea high pressure Thermoplastic Composite Pipe for spool application on Alder
Jan van der Graaf, Business Development Manager, and Martin van Onna, Chief Commercial Officer, Airborne Oil and Gas
This presentation will cover the successful design, qualification and installation of a Thermoplastic Composite Pipe in a subsea spool application on Chevron’s high pressure Alder field in the North Sea. The Thermoplastic Composite Pipe has been established for some years as a viable alternative to steel and flexible pipe in subsea applications, with various intervention type of applications building track record in the field. Up until now however, no TCP has been installed yet subsea for a permanent application: the Alder TCP Spool is the world’s first. The presentation will discuss the TCP specific benefits that lead to a significant total installed cost reduction for subsea spools; these benefits include the lack of corrosion, flexibility, the smooth bore in combination with external pressure resistance, and more. It will include an overview of the design, its methodology and results for all loadcases. The presentation will also cover the testing and qualification process it has gone through which has been executed in accordance with the new recommended practice for TCP, DNV RP F119. This includes the TCP as well as the ancillaries such as end-fittings. What will be clear is the accuracy with which TCP behaviour can be predicted. Finally, the presentation will cover the development of offshore handling and subsea installation procedures, as well as the installation itself, completed in September 2016. The presentation will conclude with an evaluation of what TCP can do to reduce the total installed cost in subsea applications.
June 21st, 17:30-18:00, Track 3@Troldtog
Vahid Abdolkarimi, Chief Engineer, TechnipFMC Deployment and installation of the subsea equipment includes risk of impact loads on the deployed subsea structure and its foundation. Any uncalculated installation load could be considered as a risk to the functionality of the subsea equipment and its sensitive instruments.
This study presents a comprehensive dynamic analysis to calculate the impact forces and correlated displacements of components during a landing operation. This analysis method investigates the interactions between the vessel, cable/wire rope, landed structure, foundation and the seabed soil.
This study combines modern dynamic analysis approach with structural analysis to develop a comprehensive methodology that can predict behavior of each component and its effect on the landing system.
Despite of the efforts to conduct a controlled landing during the installation, the magnitude of the impact load is a function of dynamic characteristics of the involved tools and equipment which makes it difficult to calculate.
DNV-RP-H103 provides a simplified and conservative methodology to calculate dynamic and static forces on the lifting tools, cable, and landing subsea equipment and seabed soil. This analysis methodology investigates the interactions between the vessel, cable/wire rope, landed structure, foundation and the seabed soil. Mass, velocity, and stiffness of each component from the dynamic system have significant effect on the dynamic response of the whole system as well as the internal interaction between its components. This study combines modern dynamic analysis approach with structural finite element analysis to develop a comprehensive methodology that can predict behavior of each component within a landing structure dynamic system.
Developing and applying solutions that reduce cost, enhance production and extend field life.
We take pride in our project management, engineering and execution. Collaboration with our clients and suppliers is key to joint success. The result is more cost efficient, faster and smarter solutions. Read more on subsea7.com Visit
June 22nd, 09:30-10:00, Track 1@Peer Gynt Strategies, methods and tools for development of subsea fields
Karl-Petter Løken, Project Development Manager, Lundin Norway
This presentation describes methodology used by Lundin Norway to be able to do concept selection for a subsea deep-water field development. The specific challenge addressed is how to proceed when the number of wells, production profiles and well targets are extremely uncertain.
The starting point (“DG1”) when going from reservoir appraisal to a full Field Concept Development phase is usually the definition of the maximum number of wells and the production profile. The challenge facing the industry today is that these input data are more uncertain than before.
The methodology that we have used is to define a field development case by first choosing a development strategy. Then a reservoir case, a drilling sequence and a field layout supporting these choices can be defined. Since each strategy can be fulfilled in many ways a large number of development cases are identified initially.
Furthermore a specific field layout can be achieved in many ways depending on choice of subsea technologies.
The next step is to identify the most attractive cases. A key screening factor is field development flexibility. Agreement on flexibility requirements is extremely important. The presentation includes a discussion of various flexibilities and the benefits identified.
The most important factor is the people involved and their attitude and competence. Therefore a key success factor is early engagement of a broad range of suppliers/engineering houses. They can be challenged with an open scope giving freedom to propose solutions.
This presentation discusses experiences and pros and cons for the chosen approach.
the GEP; the background and drivers of the development, including the challenges related to a long subsea tieback to a brownfield host. The main focus will be on key parameters on how the development could be enabled by use of fitfor-purpose technology in a challenging global industry environment.
June 22nd, 10:30-11:00, Track 1@Peer Gynt
Remote ROV Piloting – Using innovative technology to reduce costs
Arve Iversen, Rov Operations Manager, Oceaneering
The presentation is a collaboration between Oceaneering, Statoil and Telenor Maritime describing a joint project where the three companies have worked together to find new and innovative ways reducing operating cost.
In 2016 Oceaneering introduced “Remote Piloting and Automated Control Technology” (RPACT) as a cost saving initiative and established a Mission Support Center at the Forus headquarter capable of remotely controlling a Work class ROV with associated tooling. This way reducing the need for expertise personnel on site offshore.
At the same time, Telenor Maritime has been rolling out their offshore 4G LTE broadband network on all Statoil operated fields in the North Sea, providing a necessary data communication channel.
To show the maturity of the technology, a demonstration was held on December 6th 2016, remotely piloting a work class Magnum ROV onboard the drilling rig Songa Endurance located at the Troll field. Oceaneering proving the ROV and remote control technology and expertise, Telenor Maritime providing the 4G LTE data technology and Statoil facilitating with a suited offshore operation for the demo.
A number of representative ROV tasks were done during the demonstration. All tasks executed according to plan without any assistance from offshore personnel. Statoil Management and Statoil key personnel from the Troll project organization witnessing the demo live in the Mission Support Center and at Statoil’s Bergen office.
development of smaller discoveries are associated with higher subsurface risk as the appraisal cost can be hard to justify.
To unlock the resource potential in small discoveries, the cost and risk of developing small discoveries must be reduced substantially. Based on an analysis of undeveloped small discoveries on the NCS, a target development cost securing profitability has been established. The target cost forms the basis for a design to cost approach developing an integrated solution for subsea satellite wells.
This presentation describes both the design approach and the low cost satellite solution.
The low cost satellite has been developed as a complete integrated EPCI offering, providing the flexibility and ability to fully draw the benefits of optimizing interfaces between traditional SPS and SURF scope of work, and optimizing the installation, pre-commissioning and commissioning activities. A description of how the low cost satellite solution impacts the risk and cost of drilling and completing the well will also be discussed.
The solution is prepared for re-use, with a design life allowing sequential development of two or more discoveries with the same equipment. The presentation will discuss how this can open up for alternative contracting strategies, contributing to lowering risk exposure for satellite developments and unlocking resource potential in undeveloped discoveries.
June 22nd, 15:00-15:30,
June 22nd, 09:30-10:00, Track 2@Klokkeklang High Boosting a Satellite Field with Record Step-Out Distance
Mike Clarke, Project Manager, Murphy Oil / Arill Småland Hagland, Senior Systems Engineer, OneSubsea
Subsea boosting was implemented in the Gulf of Mexico’s Dalmatian field, which saw its first oil in 2014, to increase recovery. In today’s challenging market situation and increased focus on cost reduction, a great effort has been put in place to enable this project to materialize, ranging from contracting strategy and application of fit-for-purpose technology. It is the first project in the industry in which an alternative business model will enable the delivery and installation of a deepwater subsea boosting system. Furthermore, the Dalmatian project will represent the longest deepwater multiphase boosting step-out distance applying high-voltage motor technology.
June 22nd, 10:30-11:00, Track 2@Klokkeklang
SPRINGS®: New Subsea Seawater
Treatment Qualified after Offshore Tests
Stephane Anres, R&D Project Manager, Saipem SPRINGS® (Subsea PRocess and INjection Gear for Seawater) is a subsea technology for the treatment of seawater prior to injection into the wells.
The main function of such a system is to remove sulfates from the seawater injection stream before they reach the reservoir, where severe scaling is likely to result if they mix with its often-high concentrations of barium or calcium.
Alexander Fuglesang, CEO, Fuglesang Subsea AS Subsea boosting and injection systems can offer 10%-30% increased recovery from existing fields. at a minimal impact to the environment.
However, cost of installation and unplanned maintenance as well as the need for hundreds of tons of topside electric equipment and hydraulic barrier-fluid systems to support the pumps, are limiting widespread implementation.
FSubsea’s has recently qualified the worlds first Barrier Fluid-less and most autonomous subsea pump, Omnirise miniBooster, using advanced magnetic coupling technology and seawater lubricated bearings. This is the first subsea pump intended for permanent applications that can be called environmentally “green”. This means no chemicals can be released into the sea, controlled or un-controlled.
1@Peer
Cedric Chidiac, Product Champion, OneSubsea
The scope of the contract calls for the supply and installation of a subsea multiphase boosting system including topside and subsea controls as well as a 35-km integrated power and control umbilical. The execution model enables a turnkey integrated project from design through supply, installation, and commissioning. This fit-forpurpose subsea boosting technology will improve the operator’s ultimate recovery through a costeffective, record tieback. This paper will address the technology and alternative business model used to make this project economically viable in today’s volatile and challenging market.
Total, Saipem and Veolia have been working together for 10 years to come up with robust solutions featuring the use of membranes to treat seawater on the deep offshore sea bed. This paper presents the development work performed on SPRINGS® including the offshore tests performed in Congo in 2014. The objectives of these tests were to measure the rate of fouling and the performance of the membranes under in situ subsea conditions. These tests have confirmed the viability of the SPRINGS® concept. They have been performed with a Subsea Test Unit (STU), a small scale subsea module deployed from the floating production unit.
SPRINGS® is a cost effective solution for water injection when developing remote satellite fields in deepwater.
June 22nd, 14:00-14:30, Track 2@Klokkeklang
Using Engineering Simulations to create Digital Twins for IoT-Based Predictive Maintenance
The company was in December 2016 awarded 14 MNOK from Demo2000 to scale the Omnirise Boosting System technology to 1.5 MW and 6000rpm and test a full scale system in the ocean. This time adding integrated variablespeed functionality, obliterating the need for large topside electric Variable Speed Drives. The enabling and disruptive technology is called Hydromag Drive Unit (“HDU”, US Patents: 14973960 & 14218640).
The four main components in the HDU are a pressure-compensated fixed- (low) speed electrical induction motor, a hydrodynamic torque converter, a high performance permanent magnetic coupling and an embedded control and cooling system.
June 22nd, 10:00-10:30, Track 2@Klokkeklang
Tordis Subsea Separation: Operational Experience
Nikola Lazarevic, Senior Engineer Subsea Operations, Statoil
June 22nd,
How subsea tiebacks may be enabled by use of alternative and fit-forpurpose technology
Tim Nallipogu, Subsea Pumping System Lead, Woodside Energy
Greater Enfield, formerly known as Laverda, is located in the Carnarvon Basin, approximately 60km north-west of Exmouth, Western Australia, in water depths of approximately 850m.
Several technical challenges had to be tackled for the Greater Enfield Project (GEP), as the tie-back distance to the Floating Production Storage and Offloading (FPSO) is ~32km, introducing flow assurance, as well as overall production assurance challenges. This resulted in the requirement for several means of artificial lift/pressure support of which subsea pumps at high differential pressures were a key enabler. Moreover, the oil accumulations will be tie-back to an existing brownfield FPSO, and hence modifications to existing facilities are required. This presentation will provide an overview of
The three presenters will work together and present the project, and lessons learned, from their perspectives as end user and technology providers respectively.
June 22nd, 14:00-14:30,
Track 1@Peer Gynt
Moho Field development – challenges and achievements. Possible challenges with such field developments when shaping the new subsea future
Joel Cazaux, SPS Manager Moho, Total
June 22nd, 14:30-15:00,
Track 1@Peer Gynt
Integrated Satellite Tieback for Marginal Fields
Dag Jostein Klever, Project Manager Offshore Integrated Services, TechnipFMC
Several small discoveries on the Norwegian Continental Shelf remain undeveloped, even when close to existing infrastructure. Satellite well developments on the NCS have historically high unit costs compared to wells drilled from templates. In addition to relative high cost,
Starting up a subsea production system for large offshore developments is a time consuming task which may take multiple hours and/or days. The startup is particularly inefficient during an unplanned shutdown, where the operator may have a threshold time of few hours to fix the problem and startup the production system, before having to preserve the field. This paper provides the necessary workflow to evaluate and design systems and operational procedures needed for efficient field startup.
At the center of the workflow, a dynamic integrated model is used to accurately assess and effectively adjust scheduled startup time of the SPS. The integrated model evaluates and captures the full dynamic response of a large field startup by integrating a reservoir model to a transient network model. The overall workflow incorporates equipment, field design, control systems and simulation to create a complete system capable of handling quick efficient field startups throughout the field life. This is an industry first application where a full reservoir model has been integrated with a full dynamic network model which allows for startup evaluation and adjustment to be performed at different points throughout the field life. After evaluating multiple field designs and control systems, the integrated model shows that using all electric controls combined with the right field layout enables a 30 well subsea field to startup in less than 5 hours throughout the field life. The startup procedures were in accordance with network and equipment constraints as well as with flow assurance problems and mitigation requirements.
The key learning outcome of the presentation is to share operational experience and lessons learned from Tordis subsea separation during the first ten years of the lifetime.
The oilfield is located at water depth of 200 meters in block 34/7 in the Tampen area of the Norwegian Sea and is routed to Gullfaks C platform about 12 kilometers away. Due to increased water cut and the need for reduction of well-head pressure, FMC Technology delivered a SSBI (Subsea separation, boosting and injection) station in 2007. The facility was the first “full-scale” subsea separation facility in the world, which contributed to increased oil recovery from the field from 49 to 55% (adding 33 MBOE of oil reserves).
The main point of the presentation is to summarize and present technical experience including various operational challenges during the lifetime. Particular focus will be provided on reliability of the facility’s main components such as subsea separator, multiphase- and water injection pumps, desanding system and control system in general. In addition, the presentation will include field-experience from IMRoperations for replacement of Desanding unit, Multiphase Pump (MPP) and HV-power jumper in 2016.
Tomas
Jakobsen,Managing Director, EDR & Medeso AS
The project is inspired by the growing demand for efficient and strategic utilization of IoT-generated data in industrial product maintenance and development processes. Today, the use of intelligent sensors that measure mechanical, thermal or vibrational loads in industrial applications, vehicles and equipment is increasing and constitutes the technological foundation for the so called Intelligent Maintenance Systems (IMS). However, the major prevailing technological limitation of the existing IMS solutions is the inability of the systems to detect and act on early warning signs of the future malfunction problems. The technology of today is thus based on the reactive approach.
This project has proposed a novel approach to intelligent equipment maintenance based on the integration of IoT and automated engineering simulations. The cooperating parties have combined their simulation expertise, data research expertise, component design expertise and IoT platform competence to create a prototype of a unique IoT tool that utilizes sensor-generated IoT data to both predict future equipment maintenance needs, and improve the product development processes. The equipment maintenance need can be based on e.g. fatigue, wear or erosion calculations using high fidelity Finite Element Method (FEM) or Computational Fluid Dynamics (CFD) simulations. It is also evaluated how Reduced Order Modeling (ROMs) can be utilized to create a simulator that is running in real-time. The implementation of the IoT solution is based on commercially available platforms such as ANSYS Workbench (ANSYS, u.d.)® and Microsoft Azure®.
The system only requires connection to communications and a power source to function seamlessly on the seabed for several years without intervention. It is estimated to save more than 150 MNOK per project, remove 80% of topside space required, and increase reliability substantially, compared with similar systems.
June 22nd, 15:00-15:30, Track 2@Klokkeklang
The Sonsub Hydrone: a Modular, Subsea Resident Intervention System
Giovanni Massari, Project Manager, Saipem
Nowadays three factors call for a new methods to support Life Of Field in complex subsea scenarios:
1. the need to guarantee the sustainability of the present and future offshore fields where the challenging environmental conditions (e.g. under the ice) or the level of novelty of involved subsea equipment (e.g. subsea processing) lead to an increased operational complexity
2. the need to efficiently manage operational risks minimizing system downtime and environmental impact
3. the need to substantially reduce costs of IMR campaigns conventionally carried out with work Class ROVs operated by dedicated support vessels
Sonsub proposes a new comprehensive approach to field integrity management, HyDrone, that represents a transition of paradigm between the old, reactive, IMR approach to a new, preventive, autonomous solution to daily integrity issues.
HyDrone is a Modular, Subsea Resident Intervention Platform, directly integrated within the subsea field and capable to work subsea for
long time without MSV support. This modular platform is an evolution of work class ROVs, designed to allow reliable remote interventions on complex or inaccessible subsea infrastructures, also integrating AUV functionalities and additional innovative features. A possible HyDrone integration to a real subsea field is presented so to illustrate system benefits in term of augmented Life Of Field capabilities and consequent cost / risk reduction.
June 22nd, 09:30-10:00, Track 3@Troldtog
Future oriented distribution of power and communication
Bjørn Rasch, Head of Concept Group and FEED, Subsea Systems, Siemens
The growing number of electrical actuators, process and storage systems, complex instruments and new types of instrumentation require more power, higher communication throughput and lower and more predictable latency than existing control & communication systems.
These new types of subsea control systems require new ways of distributing auxiliary power with a more effective subsea communication network. Siemens has developed and qualified a generic and flexible subsea low power distribution system. Combined with a subsea state of the art wet mate connectors and field proven and qualified static or dynamic subsea cables from NEXANS, this forms a cost-effective and standardized power and communication hub for upgrade projects, (field extensions), and for future field developments.
The solution is a complete system which utilizes use of qualified components from topside or onshore to subsea connection.
The subsea remote I/O unit in the ACFO hub is based on open Ethernet communication with standardized communication protocols. Protocol conversion and intelligent I/O modules allows backwards compatibility.
The power conversion module in the ACFO hub is based on AC transmission and the power can be distributed at various voltage levels. Each power consumer can separately be interrupted and isolated from the main power bus. Each power outlet has separate diagnostics and monitoring.
This ACFO concept ensures high flexibility and selectivity for the distribution of power and communication by using qualified and field proven system components.
June 22nd, 10:00-10:30, Track 3@Troldtog
A new technology for flexible power distribution to subsea machinery
Bjørn Simen Ljønes, Manager Products, Benestad Solutions
Learning points:
– The principles of electrical power connectors to subsea rotating machinery
– Insight in the ongoing development project for a new connector
– The cost and system impact of a smaller wet mate connector
The next years will see an increased use of subsea pumping and compression, due to the demand for increased recovery from existing oil and gas fields. Field proven subsea multiphase pumps are
available from multiple vendors, but there has been little progress in streamlining the system around the pump itself. One area is the power connectors.
In order to really improve the cost picture of any subsea components, it is necessary to reduce size, complexity and weight. Heavy components require heavy infrastructure and heavy tooling –ultimately the total price tag inflates.
At Benestad we are now developing a power connection system that dramatically reduces weight and size of a high power wet-mate connector system by 90%, envision the impact on the surrounding “yellow steel” and tooling. This technology has multiple patents by now, and the presentation will walk you through the experience we now have in the R&D project. The principle of the connector is a two stage mating, 1) the mechanical alignment and locking, and then 2) the electrical connection. This has the advantage that the electrical parts are never exposed to seawater, and is also not subject to rough handling by ROV’s
In sum this new and novel connection system will dramatically reduce the operator’s capital and operational expenses.
June 22nd, 10:30-11:00, Track 3@Troldtog
Subsea power distribution – Key enabler for next generation Subsea Production
Knut Rongve, Project Portfolio Owner Advanced Electrification and Subsea Systems, ABB Subsea power distribution feasibility studies began mid 1980’s and the first subsea transformer was delivered around 1998 from ABB.
ABB is currently running a Joint Industry project together with Statoil, Chevron and Total to develop technologies for subsea power transmission, distribution and conversion at greater distances, in deeper waters, and in harsher environments. The project started up in 2013 and is targeting a 3000-hour shallowwater system test in 2018, including the qualification of pressure tolerant medium voltage switchgear, medium voltage drives, as well as supporting controls and auxiliary supplies. The target environment is water depths up to 3000 meters, transmission distances up to 600 km, and power levels up to 100 MW
This presentation will show the progress on the technology developments for high/medium voltage subsea power distribution main building blocks, i.e subsea switchgear, subsea VSD and control system. The organization of the technology project and how ABB utilize the know-how of industrial experience to ensure reliable subsea power components will be presented. The project is based on open dialogue with the project partners on the technology proposition and a shared interest in long-term growth.
Main topics for the presentation will be :
– History for subsea power components
– Subsea power building blocks under qualification in the Joint Industry Project
– Organization of the project and how ABB’s industrial experience is used to ensure reliable subsea power components
– Update on the project status and achievements and expected challenges in the remaining work.
June 22nd, 14:00-14:30, Track 3@Troldtog
Frank Smith, Hardware Team Lead, Norske Shell The Ormen Lange Late life Recovery Project was seeking greater insight to the engineering limits and life associated with Flow Induced Vibration as a recognised threat from unconstrained flow across the existing subsea template. The screening methodology was capable of assessing a range of concept engineering options within a relatively short timeframe, which was an important requirement for the Front End loading on the Project.
The adoption of the Shell FIV Intermediate screening methodology on the Project was verified against past operational experience and the recent industry FIV JIP high quality data from a 6” laboratory test facility (managed by Xodus Group and TNO).
The OLLLR project successfully demonstrated the use of the novel Shell Intermediate screening approach based on a Frequency Domain analysis for multiple flow cases using competent FEA engineers and not CFD specialists. Ultimately, the simplified methodology generated fatigue life estimates of equipment in several days and not the weeks normally associated with a more comprehensive and complex CFD + Structural analysis.
The insight offered greater value to the Project decision making and helped focus attention on those engineering areas for further attention in the next project phase.
Juan Pontaza, Bostjan Bezensek, Cliff Ho, Frank Smith (Shell International E&P Inc. USA, Shell UK E&P Ltd UK, A/S Norske Shell NO)
June 22nd, 14:30-15:00, Track 3@Troldtog
Light Module Handling Systems on Roll & Pitch Compensated vessels Åsmund Sætre, Sales and Business Development Manager, Axtech
Over the years, have subsea lifting operations become very advanced but also very expensive. However, the market dropped and cutting cost became the new main challenge. Like many others, AXTech accepted the challenge and we would now like to share what we found, and how the largest cost factors in subsea lifting operations can be addressed by new technology and methods.
Most module handling systems require large modifications to the vessel, causing expensive mobilization and installation. We believe it is possible to make small versatile module handling systems that can quickly be installed on almost any existing offshore vessel and able to handle 90% of the modules in the North Sea. The result of our work is AXTech’s new Light Module Handling System, which can be installed in a few days with little or no modifications on almost any vessel.
Heave compensated winches are essential in module handling. But what if the vessel also was “heave compensated”? AXTech are in cooperation with MRPC developing a concept for module handling from small vessels with synchronized active roll and pitch control of the
entire vessel. By combining LMHS and MRPC we believe we can make a significant impact on the cost level of most subsea lifting operations. We would like to present the theory behind these topics and compare it with the experiences we have made so far including the test results after building a full-scale prototype, which has been extensively tested this winter.
June 22nd, 15:00-15:30, Track 3@Troldtog
Dynamically positioned highresolution subsea laser: - cost effective offshore survey operations, including contactless metrology, reverse engineering and IMR tasks.
David Rattray, Senior Project Surveyor Mark Lawrence, MD ADUS,Deepocean
Jostein Valen, Director Survey and Inspection, Deepocean
The problem: To meet the challenges of energy security, an increasing number of offshore renewables projects and power sharing interconnectors are being installed across Europe and beyond. The main arteries delivering the power to shore are the export cables which are protected from damage through means of burial.
The growth in power cable installation has led to increasingly deeper burial requirements in increasingly challenging soil conditions and currently available burial tools were not up to the task leading to exposed cable and increased risk. The Race Bank wind farm is one such project, demanding cable burial of 3m across an area of vastly differing soil conditions and seabed topography. To rise to this challenge, DeepOcean developed the T3200, a 170te tracked mechanical trencher capable of creating trenches up to 3.5m deep in sands, clay and weak rock up to 40MPA. Delivering the trenching power required to create such deep trenches in tough ground conditions presents numerous technical challenges leading to the development of new trenching tools and operating techniques. This paper discusses the challenges faced in developing T3200 and how they were overcome.
22ND JUNE @KLOKKEKLANG
08:30 - 08:50
Possibilities and Implications by Designing an Aluminium Integrated Template Structure.
Henrik Nesheim, Kjell Petter Løkling Lunde, Master students Subsea Technology, NTNU Steel has historically been the governing material for use in subsea structures. This project looks into the possibilities for using aluminium rather than steel in subsea structures.
A four well-slots integrated template structure installed on the Norwegian continental shelf is used as a design case. The use of aluminium represents a lighter structure (approximately 25 to 45% lighter than steel) with a great potential in reducing life cycle cost. The aluminium alloys 5083 and 6082 are the only ones approved for structural seawater applications by the NORSOK M- 121 standard. However, material properties has to be fully understood in order to utilize aluminium in a subsea environment. Especially with respect to corrosion behaviour, mechanical properties and joining methods.
In order to establish a better understanding of the material properties of aluminium a literature review has been conducted. A short historical review of aluminium used as construction material in subsea structures has been done to identify achievements in the use of aluminium subsea. Design loads for an integrated template structure has been identified from appropriate NORSOK standards for trawling and drilling loads.
The utilization of aluminium in subsea structures looks very promising for the integrated template structure, although there are some challenges with respect to corrosion and joining methods, a new design aimed to solve these challenges will be presented. A cost comparison between steel and aluminium (taking into account fabrication and installation costs) has been done to identify the total project cost implications by using aluminium instead of steel. The installation cost is reduced as the necessary crane capacity to perform the installation is reduced.
08:50 - 09:10
Wax Control for Long Distance Tieback of Subsea Production Systems
Yury Novoseltsev, PHD Candidate & Engineer, NTNU/ Subsea 7, Sigbjørn Daasvatn, Strategic Technology Manager, Subsea 7, Daniel Karunakaran, Technical Authority, Subsea 7 Some fields produce well streams containing high amount of paraffinic components. Part of these paraffinic components can deposit as solid waxes form at pipe wall when temperatures are gradually reduced during fluid transport using long distance pipelines. Without control, growing wax deposits can block a pipe entirely. Several concepts for control technics are present at market: wall heating, pigging, wax inhibitors, heat pulse method, etc. Another approach is to remove the wax from well stream, and then transport dewaxed fluid at ambient temperatures. This paper describes overview of complete field development system (from well to entrance of export pipeline) with focus on subsea WCU (Wax Control Unit) - a structure installed at the seabed to perform removal of wax from a pre-conditioned well stream. WCU is new equipment and the steps for the ongoing qualification process are also presented.
WCU will enable subsea transport of waxy petroleum fluids from field to shore at ambient temperatures. This type of flow is termed “cold flow”. It features no or very limited wax build-up at pipeline wall due to equality of bulk temperature and pipe wall temperature.
WCU as a part of subsea field development system will allow access to fields in Arctic as an alternative to heated pipelines or application of FPSO or platform based solutions.
09:10-09:30
Formation of gas hydrates monitored with dielectric spectroscopy Kjetil Haukalid, PHD Candidate, University of Bergen/ CMR
To develop and increase the use of less expensive hydrate treatment strategies, there is need for measurement technology that is able to monitor formation of gas hydrates for realistic pressure and temperature conditions. This paper demonstrates how dielectric spectroscopy can be used to study formation of gas hydrate deposits and formation of gas hydrates in the bulk phase. Dielectric spectroscopy is measurement of the material property permittivity as function of frequency of the electric field. The permittivity of gas hydrates differs from the permittivity of oil, gas and water. Dielectric spectroscopy can therefore be used to monitor formation of gas hydrates.
Operational experiences and lab-scale studies have revealed that the mechanisms of hydrate plug formation depend on the fluid system, and in particular the volume fractions of oil, gas and water. This paper presents broad-band permittivity measurements on formation of gas hydrate deposits/layers and on hydrate formation in water-in-oil emulsions. By mounting the permittivity sensors flush with the inner pipe wall, formation of thin hydrate deposits can be detected. The hydrate fraction in the deposits can be estimated from the permittivity measurements. By comparing the measurements with finite element simulations, the thickness of the layers can be estimated. The measurements on water-in-oil emulsions show how the permittivity measurements can be used to monitor hydrate formation and dissociation in the bulk phase. Hydrate agglomeration due to capillary bridging between the hydrate particles can be detected from a characteristic change in the measured permittivity spectra.
The Subsea SAS: Topside Extension Concept
Paula Doyle, Subsea Technology, ABB Gunnar Johan, Subsea Technology, ABB
The subsea industry has overcome great technical challenges as it approaches the realization of the subsea factory, with advances in subsea processing and power distribution filling the factory toolbox. However, there still remain issues to be overcome in terms of cost, simplicity and standardization.
To realize the vision of the subsea factory, every effort needs to be made to simplify, industrialize and standardize. A key element of the subsea factory is the control system. As the subsea applications get more complex, the demands on the control system increase. High availability, real-time performance and safety are key functional requirements that subsea control systems will need to deliver. In addition, standardized, open interfaces and communication protocols coupled with a foundation of industrialized products are two of the system requirements that need to be fulfilled in order to deliver a cost-effective manageable solution that leverages the best of what is existing in today’s topside automation environment.
The extension of the existing topside safety and automation system into the subsea domain fulfills these requirements and introduces benefits such as engineering efficiency, interoperability and synchronized lifecycle management that will enable operators to achieve their goals of simplicity, industrialization and standardization. This presentation presents the concept of the topside SAS extension in terms of specific applications in subsea processing and production. The overall concept and the specific examples illustrate the benefits of the extension in terms of reduced interfaces, engineering effort and improved lifecycle management.
Control system for subsea factory
Dr. Gunleiv Skofteland, Leading Researcher Automation, Statoil
Egil Dino Hansen, Principle Engineer SubseaT.&Ops, Statoil
Daniel Abicht, Leading Advisor Subsea Control Systems, Statoil
An important part of Statoil’s vision of the Subsea Factory is a cost efficient subsea control system. Subsea processing including separation, boosting, subsea compression set strong demands to the control system to handle fast closed-loop control, safety functions as well as conditioning monitoring of the subsea equipment.
Experience from the Åsgard subsea compression project will be presented. The subsea compressor station has been in successful operation since August 2015. Based on the experience from Åsgard and other subsea processing installations we have identified potential for further improvements to the design of control systems for future subsea applications.
This contribution proposes a ‘Next generation subsea control system’ aiming to be simpler, safer and more reliable. The goal is to reduce cost in all project phases including engineering, construction, testing, commissioning and
operation. Standardisation of interfaces, hardware and software, is essential to make the solution cost effective. Ethernet communication on fiber optics using open industrial standards form the basis for the control functions, and ‘Black channel’ functionality on Ethernet is proposed for safety functions. The logic solvers for safety and controls can be placed topside communicating by Ethernet with Remote IO’s placed subsea. Performance calculations show that this architecture will achieve a bandwidth that fulfills our requirements for closed-loop control including the demanding task of compressor anti-surge control and safe shut down.
The same control architecture could be applied for production control of subsea wells. Especially, in combination with AllElectric Subsea solutions great potential of the investigated control system architecture is anticipated.
OneSubsea Subsea Modular Injection System: A Flexible Lowcost Intervention Solution for an Increasingly Variable Market.
Robert Large, Engineering Manager, New Technology Development, OneSubsea In today’s challenging environment, operators are working hard to maximise operational efficiency. One trend evident in the intervention arena is an increased interest in accessing broader scopes of service support to lessen the commercial risk of procuring high CAPEX field dedicated equipment. In response, service providers are being challenged to develop innovative offerings that are flexible enough to meet the needs of a diverse market, whilst also remaining efficient enough to deliver the required commercial benefit. This paper discusses the development of a new to market OneSubsea innovation, intended to provide a cost efficient means of subsea hydraulic well access.
The desire to accommodate a broad range of operational objectives, environmental conditions, customer preferences and regulatory requirements, cumulatively drive a strong need for flexibility. The need to accommodate rapid mobilisation without the requirement for inefficient equipment inventory then in turn drives a need for heavy standardisation.
Accepting that standardisation and functional flexibility can introduce competing design influences, this presents an exciting challenge. OneSubsea has taken several innovative steps in the development of the Subsea Modular Injection System ‘SMIS’ to meet this challenge.
The OneSubsea SMIS utilises a subsea barrier package, optimised topside deployment system and open water coiled tubing riser system supported by an innovative fatigue management system.
The presented development process and resulting new technology highlight how project specific sensitivities can be identified and mitigated, how complex functional requirements demand a structured development process and how a welldefined safety philosophy is key to delivering a robust low-cost intervention solution.
New single subsea production well design gives well cost reduction and production acceleration
Harald Strand, CTO, Neodrill Conventional subsea single production well design require the well to be drilled and completed with the drilling vessel before flow lines pull-in, connection of umbilical’s, etc. may be undertaken with another specialized vessel. This will cause time delay between well completion and production start-up, sometimes amounting to several weeks.
By pre-rig installing a single well foundation with integrated conductor, this costly time delay can be reduced, and facilitate instant production.
The well foundation is used as integrator between drilling, SPS (Subsea Production System) and SURF installation operations, enabling parts of the well construction and SPS/SURF installation to be undertaken prior to the rig arriving at the location. This new, pre-installed well foundation with integrated conductor will fix the exact well location and can therefore be used as a ‘hub’ to perform pre-rig well construction, such as:
- Flow Base/Lower X-mas Tree installation
- Flow line pull-in (the well foundation is a strong pull-in anchor!)
- Umbilical hook-up
- Control module installation
- Corrosion Protection System
- Protective structure installation (integration with well foundation)
The pre-installation of the production system will enable the rig to put the well on production prior to leaving location. Thus the need for killing the well, risking production losses caused by high skin factors, is avoided. Further, safer well construction; higher well load capacities; including accidental loads / fatigue, will be attained as well as risk mitigation as the Conductor is pre-installed and tested before rig arrival.
Henrik Alfredsson, CFD Lead Engineer, Aker Solutions
Julien Rolland, Flow Assurance Lead, Total E&P For deep water oil developments wet insulation is typically used to insulate equipment with complex geometries to ensure that the production system stays above hydrate formation temperatures during production shut down. Thermal performance of the subsea assets as such plays a vital role in the operational philosophy of the field and historically cool down testing (CDT) has been an integral part of project execution to verify the insulation design. In order to meet the Kaombo extreme thermal requirements, Aker Solutions with Total E&P contribution have perfected and qualified numerical Computational Fluid Dynamics (CFD) methods able to fully predict the thermal performance of various insulated subsea components without the need for future testing. In this paper Aker Solutions will together with Total E&P present how CFD simulations can be used to completely remove CDTs from future projects. This will reduce execution cost and schedule risk especially
important for small to medium sized brown field developments. Reference will be made to Kaombo project cool down tests performed on horizontal and vertical tie-in systems along with christmas tree and manifold showing how high accuracy simulations today, when done right, are able to predict test outcome to within one degree accuracy. Test data will be revealed and compared to CFD predictions providing the governing parameters important for predictively sizing the insulation system without the need for future cool down testing.
Novel methods for automated condition monitoring of valves and actuators
Ben Mooney-coomes, Subsea Controls Engineer, BP Big data methods are widely endorsed as catalysts for performance improvement in the oil and gas industry over the coming decade. Over
half of the super-majors explicitly outline digital data analysis as an area of focused investment in publicly available 2016 technology reports.
The digitalization of condition based monitoring is one area anticipated to benefit from modern data analysis techniques which have potential to impart measurable gains in safety, productivity and environmental performance. This technical paper/presentation describes the engineering and deployment of a novel cloud-based valve condition monitoring app which fully embodies this industry push for digitalization.
The ‘Valve Signature Tool’ is a web based analysis package providing quantitative information on the condition of subsea linear actuators and gate valves to onshore engineers.
Developed in partnership between BP and the software company Intelligent Plant, the methods described in this technical paper/presentation overcome a number of technical and process hurdles to make condition monitoring of valves accessible and easy.
Hydraulic closure signatures are uniquely accurate for condition monitoring of valves because they are fundamentally linked to the force-balance equation describing the valve
and actuator themselves. Therefore differences in successive closure signatures accurately represent changes in the balance of forces in the valve and actuator.
This paper/presentation explains innovative methods for automating the condition monitoring of valves and actuators including: (1) Decoupling’ the process bore pressure effects on closing valve signatures, (2) Remote assisted diagnosis of degradation and (3) Instating a virtual control module flow-meter using only existing equipment setups.
The Underwater Technology Foundation (UTF) Subsea Award is designed to recognize the many outstanding achievements within the subsea industry.
The award can be given to a person or a group of people that have contributed to knowledge and understanding in subsea technology through new products, services and/or processes.
On the basis of UTF position in the industry, UTF will credit the individuals behind new breakthroughs and innovation. Furthermore, we will share the story of the winner, not only with you, but also through our partner Offshore Engineer, to a wider audience outside the UTC conference halls.
The objective is to tell everyone with a brilliant idea what it takes to succeed and what all the work resulted in for the industry. The jury has been appointed by the UTF board and consists of prominent individuals from valuable UTF partners.
The first UTF Subsea Award was awarded Tracerco for their Discovery™ at UTC 2015. The jury recognized Discovery’s™ innovative technology, the large global potential, the fact the technology is field proven with excellent results and that it contributes to both operators, IMR companies and suppliers.
Paul Featonby, Technology Manager and Tim Hough, Discovery Technology Lead, both at Tracerco, are recognized for the technology and project execution.
The winner of the second UTF Subsea Award 2016 was OneSubsea® Multiphase Compressor. Bernt Helge Torkildsen and Simon Kalgraff, OneSubsea, and Jarle Ottar Hella and Caroline Bøe, Statoil was recognized for their significant contributions to the OneSubsea’s Multiphase compressor technology.
The third UTF SUBSEA AWARD will be presented at UTC, June 21st
THE JURY:
Bjørn Søgård, Segment Director, Business Development, Subsea and Floaters, DNV GL
Elaine Maslin, Editor, Offshore Engineer Magazine
Mads Hjelmeland, Global Sales Director – Processing Systems, OneSubsea
Karl Ludvig Heskestad, SPEI
Stig Instanes, TechnipFMC
Gisle Nondal, GCE Subsea
NILS ARNE SØLVIK (CHAIR)
Chair UTC 2017 Program Committee/ President Processing, OneSubsea
Nils Arne graduated as a Master of Science in Electrical Power Engineering from the Norwegian Institute of Technology (NTH) in 1991. He started his career as a Consultant with Norwegian Contractors in the area of the large concrete platforms, such as Sleipner, Draugen, Troll A and Heidrun. In 1994 he joined ABB as a Technical Trainee and after several periods with different ABB companies he joined ABB Corporate Research and became involved in subsea processing and power distribution development programs. In 1997 he joined ABB Offshore Technology AS as Project Manager and later Department Manager before he went on to become Sales Manager, Subsea Processing for ABB Offshore Systems Inc. in Houston from 2001. In 2003 he joined Framo Engineering AS and now holds the position President, Processing Systems Division, OneSubsea.
MATHIAS
Deputy Chair UTC 2017 Program Committee/ SURF & Technical Delivery Manager, A/S Norske Shell
Mathias Owe holds a Master of Management from the Norwegian School of Management and an MSc in Mechanical Engineering/Oil Production from the Norwegian Institute of Technology. He has 30 years of international experience from the oil and gas industry and has been Project Manager for large and complex Subsea EPC(I) development projects. He has led opportunities/projects through all its phases from Project Pre-qualification, Technology qualifications, Studies, FEED, Tender, Execution, Installation, Start-up and Service in Operation. Mathias has held positions as Project Manager for Ormen Lange Infield Compression Project and Ormen Lange Subsea Compression Pilot Project, and has been Technical Manager for Ormen Lange Subsea Systems. His previous work also include ABB Vetco Gray & GE Vetco Gray as Project Manager for the subsea development
Vice President Technology Strategy, Aker Solutions
Per Christian holds 12 years’ experience in the industry and has been part of Aker Solutions organization since 2002. He has been part of the full value chain in subsea ranging from studies, tenders, projects and services. More specifically he has been in Angola for the Dalia project, and further he built up the Global Lifecycle Services Support department as a support entity for the regional onshore and offshore operations. Currently he is heading the Technology Strategy in Aker Solutions’ Subsea area, setting the technology direction for the Aker Solutions subsea products in the years to come. Per Christian graduated as Master of Science in Petroleum Engineering from the Norwegian University of Science and Technology in 2002.
MARTIN DOVE
Project Director, BP
Martin Dove holds the position of Project Director in the GOO Subsea Production team, and is based in BPs Sunbury offices. Martin has responsibility for ensuring that subsea operational experience input is provided to the BP projects organisation ‘GPO’, assuring subsea operational readiness and start-up efficiency on major subsea projects and facilitating the common process implementation for smaller subsea projects across the Regions. Martin joined BP in 1988, working most recently as the Subsea Production Operations Manager in Norway. Prior to this Martin has worked as the Subsea Team Leader for Greater Plutonio in Angola where he set up the subsea operations organisation and led the team through start-up into operations. Earlier in his career Martin has undertaken subsea and facilities roles in Azerbaijan, Aberdeen, Sullom Voe, Southern North Sea and Grangemouth. Martin has an M.Eng from London University in Mechanical and Electrical Engineering.
TONJE DAHL
Marketing & Communications Manager, ClampOn
Tonje has been with ClampOn since 1997 and has been a vital part of the company’s marketing strategies and activities. She graduated from the University of Stavanger with a bachelor degree in business administration, with a specialization in export marketing. Tonje has been a volunteer on the Board of SPE Bergen Section for several years and has previously held the position as Chairman of the section. Over the years, she has gained extensive knowledge of instrumentation, and subsea instrumentation in particular.
MARIE BUEIE HOLSTAD
Department Manager Measurement Science, Christian Michelsen Research(CMR)
Marie graduated as Dr. Scient in industrial instrumentation from the University of Bergen in 2004. She started working as a development phycisist for Tracerco, supplier of measurement systems and diagnostics services for subsea and topside offshore industries. Marie has been working for Christian Michelsen Research AS for the last 7 years, mainly focusing on measurement technology R&D for the oil and gas sector, including subsea measurement concepts and studies . Marie currently heads the CMR Measurement Science Department.
BÅRD ESPELID
Head of Department, DNV GL
Bård Espelid holds a M.Sc. in electrochemistry from the Norwegian Institute of Technology (NTNU). He has been working for DNV GL within materials technology and integrity management the last 32 years. Today he holds a position as business development leader within “Subsea and Wells”. In DNV GL he also execute the role as customer service manager for some prioritized customers. The last years Espelid has been especially involved in DNV GL services related to re-certification of well control equipment. Bård Espelid is an active member of different national and international corrosion societies.
TOM EDDY JOHANSEN
Senior Chief Engineer, TechnipFMC
Tom Eddy has been working in the subsea business since he graduated in 1982 and with FMC Technologies for more than 25 years. He is educated mechanical engineer and has a degree in marine/offshore engineering. Tom Eddy has worked in most of the product lines within the subsea business and in the last 15 years as engineering manager and chief engineer in several major international subsea development projects for various customers. His current position is manager for subsea production system at Forsys Subsea in Paris. Forsys is a joint venture between FMC Technologies and Technip.
Product Manager Subsea Boosting & Compression, GE Oil & Gas
Hans Kristian graduated from the Norwegian University of Science and Technology in 2000 with a Master of Science in Chemical Engineering. He has more than 10 years of experience within technology development and sales in the oil and gas industry. He started his career as a topside process engineer and has since followed new products from the initial idea, through the development and finally to the market. In 2008 he left dry land and joined the subsea community. Hans Kristian currently works with GE Oil & Gas as Product Manager for Subsea Processing.
ERIK SVERRE JENSSEN
Field Development Manager, Lundin Norway
Erik Sverre Jenssen started his career in Saga Petroleum in 1983, after having completed his petroleum engineering studies at the Norwegian Technical-Natural Science University (NTNU) the same year. He then moved to Norsk Hydro, where he was offshore installation manager for Oseberg Field Centre, and held the position as SVP for Southern North Sea Asset Area, including the redevelopment of Heimdal and the development of the Grane field. He was president in Aker Geo (Aker Solutions) before he came to Lundin Norway in 2011 as Chief Operation Officer. He has over 33 years of experience related to operations and development of North Sea Assets.
KARL LUDVIG HESKESTAD
Director North Sea Region, SPE
Karl Ludvig Heskestad is the SPE Director for North Sea Region, and Senior Reservoir Engineer at Aker BP within Business Development. Heskestad holds a Master in Petroleum Engineering from the Norwegian University of Science and Technology in Trondheim and a Master in Energy Management from BI Norwegian Business School in Oslo.
OWE HAGESÆTHER
Chief Executive Officer, GCE Subsea
Owe Hagesæther has more than 25 years of varied experience from Technology Management, Change and Project Management, Top Management and Board positions, International Networking, Marketing, Sales and Business Development. He has his experience from industries such as Oil & Gas and Energy, Banking & Finance, IT & Telecom, Management Consulting and Maritime Technology. Hagesæther is an entrepreneur and former Founding Partner of Nordic Integrator Group. He holds an MSc in Computer Science from University of Bergen and an MBA in Strategic Management from Norwegian School of Economics.
250.000 unique users weekly on tu.no 100.000 unique users weekly on digi.no
managers
ROLF RØSSLAND
Managing Director, NUI
Rolf Røssland has been Managing Director for NUI AS since 2014. NUI is a Company that provides the subsea industry with a great diversity of products and services, ranging from advanced research, hyperbaric contingency and performance testing to engineering, training, consultancy services and pressure/equipment testing. Rolf Røssland has nearly 40 years’ experience from the offshore industry, mainly within Diving, Underwater Operations, Safety Training and HSEQ. He has held several positions such as Diver, Diving supervisor, Consultant, HSEQ Director and Managing Director. Having an operational background the main-focus has been, and still are, to participate in the Industries work to perform safe and effective operations. He is a frequently speaker and a member of the UTC Council and the Program Committee for The Bergen International Diving Conference.
MERETHE BERGE PAASCHE
Marketing & Communications Manager, Oceaneering
Merethe Berge Paasche is the Marketing & Communications Manager for Oceaneering AS with responsibility for maintaining and development of growth strategy, brand development, customer relationship management and value-based sales management. Merethe graduated from the Norwegian School of Information Technology (NITH) in 1992. She has over 15 years experience in the oil and gas industry, within completion, drilling and subsea services. The last 6 years she has held management roles in Oceaneering within Marketing and Business Development. Prior to joining Oceaneering, she was employed by Baker Hughes and Odfjell Well Services.
JOHAN KR. MIKKELSEN
Chief Technology Officer, Perestroika AS
Johan Kr Mikkelsen has 40 years experience from Norsk Hydro and Statoil. He entered the oil and gas industry at the Mongstad refinery in 1974 as process engineer and a couple of years later as Production Manager at the refinery. In 1983 he moved on as Production Director for Oseberg field and in 1992 as SVP for Norsk Hydro drilling. In 2000 he continued as SVP for Oseberg asset and in 2003 as SVP for the Troll asset. In 2005 he became Country manager for Norsk Hydro Canada before he moved on as Peregrino Project Director and later Production Director for the field in Brasil. In 2012 he returned to Norway as VP for the Statoil Subsea Improvement Project until early 2014 when he retired from Statoil. At present he is the Chief Technology Officer with Perestroika AS. He holds a Master degree from NTH from 1973 in Industrial Chemistry and a Master degree in Chemical Engeneering from University of Wisconsin, USA in 1979.
RUNE MODE RAMBERG
Chief Engineer Subsea Technology & Operations, Statoil
Rune has 25 years’ experience within the oil and gas industry. He experience includes: research, early phase development, project execution and field operations. He worked 4 years in Houston with Chevron on Jack St. Malo and as Technology Manager for Statoil Houston office. In the position as Chief Engineer in Subsea Technology and Operations, he is heading the professional network of 400 subsea engineers in Statoil. Ramberg holds a M.S degree and a Ph.D from the Norwegian University of Science and Technology. He has worked for Statoil since 1997. In his spare time he is riding bikes and coaching soccer.
TERJE CLAUSEN
Business Development Director, Subsea 7
Terje holds a MSc in Marine Technology from the Norwegian Institute of Technology (NTNU), specializing in Marine Hydrodynamics and Marine Operations. He has over 20 years experience within the offshore industry, within marine operations, pipelines, mooring, deepwater risers systems and field development. The last 10 years he has held several management roles in Subsea 7 within Technology & Business Development. He was previously employed by Aker, DNV, Global Maritime and Brown & Root.
TIM CROME
Technical Manager, Global Front End, TechnipFMC
Tim Crome has worked in the offshore pipeline / subsea industry since graduation from Imperial College, London, in 1980. For more than 30 years his work and home has been in Norway. He joined Technip in 1997, was Engineering Manager for the Oslo office from 2001 until 2007, Director for Sales and Business Development for Norway until the end of 2014 and is now VP Subsea Mediterranean. Prior to joining Technip he worked for JPKenny, DNV and Norsk Hydro.
PER ARNE NILSEN
Head of Subsea Department, Total S.A France
Per Arne has for many years held Senior Management positions internationally (Norway, US, Canada, UK, Singapore, Australia, France). He has been employed by several Oil & Gas operators globally, with roles spanning from asset management, via project management and delivery management to R&D/Technology management. Specialties: International negotiations, project execution management, change management, professional leader with multicultural skills and experience. Professional in Subsea technologies.
MADS HJELMELAND
Global Sales Director – Processing Systems, OneSubsea
Mads Hjelmeland holds an MSc in Marine Technology with the Norwegian University of Science and Technology, and currently holds the position as Global Sales Director, Subsea Processing, in OneSubsea. The responsibilities include managing early engagement and market initiatives, as well as strategic business & technology development efforts, within the subsea processing domain. Prior to joining OneSubsea in 2014, Mads worked with Murphy Oil in Malaysia where he held the position as Manager of Subsea Projects, which included development planning and execution of projects across Murphy’s Malaysian deepwater portfolio. Before he joined Murphy Mads worked with OneSubsea, where he held a variety of positions in Norway, the Middle East, and Asia. His work scope focused on subsea processing technologies, with particular emphasis on subsea boosting- and wet gas compression technologies.
JARLE DAAE
Chairman of the Board, Underwater Technology Foundation
Jarle Daae holds more than 18 years of experience in the industry and has been part of Aker Solutions since 1998. He started within the Specialist Services in Aker Solutions and has 10 years of experience from Riser, Umbilical and Pipeline design and verification and has held several roles within the development of the Asset Integrity Management (AIM) Services in Aker Solutions. Currently he is heading the Integrity Engineering department in Aker Solutions AIM and is responsible for developing Subsea Inspection and Integrity capabilities. Jarle is a Naval Architect & Offshore Engineering from the University of Strathclyde in Glasgow and has been a member of the Board for the Underwater Technology Foundation (Host of the UTC) since 2011.
KNUT RONGVE
Project Portfolio Owner, ABB
Knut graduated as Master of Science in Electrical Power Engineering from the Norwegian University of Science and Technology (NTNU) in 2003. He joined ABB in 2006 as Project Engineer for Oil, Gas and Petrochemicals in Norway. He has held various technical and management positions within the organization. Knut is currently leading ABB’s Subsea Growth Initiative and the overall activities within subsea, including Global Product Manager for Subsea, on behalf of the ABB BU OGC
TORKILD REINERTSEN
Ph.D, Managing Director, Reinertsen AS
Responsible for the oil&gas activity in the family owned company, Reinertsen AS for more than 30 years. Reinertsen is an Engineering and EPC contractor working within Subsea and Process Facilities.
RICK KOPPS
Subsea Specialist, Chevron
ROGER WALLS
UK Joint Interest, Exxon Mobil
GCE Subsea is an industry driven initiative for strengthening and internationalisation of businesses, research and education. We represent the world’s most complete cluster for subsea life-of-field solutions. Our goal is to increase the cluster’s competitiveness and global market share, and take a leading position in sustainable utilisation of ocean resources.
All organisations established in Norway providing products or services to the subsea industry, or intend to do so, can become members of GCE Subsea. Partners are companies viewed as particularly important for the development of the cluster, as well as R&D and education institutions and governmental organisations.
GCE Subsea’s combination of companies, specialised service providers, research and development (R&D) environments and development agencies make the cluster a global knowledge hub. The cluster develops and supplies innovative products and services to install, operate and maintain subsea oil and gas production systems (subsea life-of-field). The cluster’s resource base consists of industry companies, R&D and higher education institutions, joint innovation support resources and joint test facilities and R&D infrastructure.
The cluster’s key players are located within half an hour’s drive from the city centre of Bergen. The close proximity between businesses, R&D environments and support agencies enables good mobility, communication and knowledge sharing.
GCE Subsea companies operate globally and serve primarily clients on the Norwegian/British continental shelf, in the Gulf of Mexico, Brazil, Asia, Australia and West Africa.
We own and operate Subsea Index, a bi-lingual matchmaking tool in English and Portuguese. The intent of the database is to create business opportunities by providing accessible and searchable high quality, business relevant data about companies and organisations related to the subsea industry.
Subsea Index is open for registration for all companies and organisations delivering products and services in the worldwide subsea industry. Use the database to find your partner in business, R&D, education and training.
GCE Subsea is one of three Global Centres of Expertise in Norway and a part of the Norwegian Innovation Clusters government supported cluster programme. The programme aims to trigger and enhance collaborative development activities in clusters. The goal is to increase the cluster dynamics and attractiveness, the individual company’s innovativeness and competitiveness.
The programme is organized by Innovation Norway, and supported by Siva (The Industrial Development Corporation of Norway) and the Norwegian Research Council.
The GCE status is the highest level in the Norwegian Innovation Clusters programme
GCESUBSEA.NO
SUT is a worldwide, multi-disciplinary, learned society that brings together organisations and individuals with a common interest in underwater technology, ocean science and offshore engineering. SUT was founded in 1966 and has members from more than 40 countries, including engineers, scientists, other professionals and students working in these areas.
The organisation has comprehensive expertise within its area of activity, whereby it influences the development of new techniques to further explore and exploit the world’s oceanic resources, such as through annual prize-giving ceremonies.
Today the association is established in London with branches in Bergen, Aberdeen, Houston, Rio de Janeiro, Perth, Melbourne, Kuala Lumpur and Lagos, where they carry out learned courses and programmes for members and others who are interested in subsea technology and their wide range of other ocean-related activities. The latest branch, SUT Norway (Bergen) was established in 2009.
SUT Norway is a non-profit organisation, to be developed through networking and interaction between individuals and companies working professionally with underwater technology. Its objective is to facilitate the exchange of knowledge and information, e.g. by arranging courses and seminars with agendas relevant to subsea activities.
Society of Petroleum Engineers (SPE) is a professional association whose 100,000-plus members worldwide are engaged in energy resources development and production. Local sections of the SPE are established around E&P communities all over the world.
SPE Bergen Section is one of five sections in Norway. We host a variety of activities and events, focusing on networking and knowledge.
SPE Bergen hosts regular member meetings, the annual SPE Sailing with the Statsraad Lehmkuhl in late spring, SPE Bergen Lutefisk in early winter and the SPE Bergen YP.lnk hosted by our YP program. Our largest event during the year is the annual SPE Bergen One Day Seminar in April. This international E&P conference and exhibition attracts some 500 participants and approximately 45 exhibiting E&P companies.
SPE recognizes the importance of those who one day will be leaders of the E&P industry. Along with many SPE sections, the SPE Bergen Section has developed a Young Professionals (YP) programme, to support and assist those in the industry with fewer than ten years of experience.
SPE also offers student memberships. The SPE Bergen Student Chapter counts several hundred members and is the most important link between students and the petroleum industry in the Bergen area. The SPE Bergen Section is proud to support and sponsor one of the world’s largest and most vibrant SPE student chapters. The chapter hosts its own events, and students also participate on regular section events.
WWW.SYSLA.NO
AKER BP
Aker BP is a fully-fledged E&P company with exploration, development and production activities on the Norwegian Continental Shelf (NCS).
Measured in production, Aker BP is one of the largest independent oil companies in Europe.
Aker BP has a balanced portfolio and is the operator of the Valhall, Ula, Ivar Aasen, Alvheim and Skarv field hubs. The company is headquartered at Fornebu outside Oslo and has offices in Stavanger, Trondheim, Harstad and Sandnessjøen.
At the end of 2016, the company had 1,371 employees.
Aker BP ASA is jointly owned by Aker ASA (40%), BP (30%) and other shareholders (30%).
LUNDIN
Lundin Petroleum is one of Europe’s leading independent oil and gas exploration and production companies with operations focused on Norway.
STATOIL
Statoil is an international energy company with operations in 36 countries. Building on more than 40 years of experience from oil and gas production on the Norwegian continental shelf, we are committed to accommodating the world’s energy needs in a responsible manner, applying technology and creating innovative business solutions. We are headquartered in Stavanger, Norway with approximately 23,000 employees worldwide, and are listed on the New York and Oslo stock exchanges.
WINTERSHALL
Wintershall is one of the major oil and gas companies on the Norwegian Continental Shelf, with a daily production of over 80,000 barrels of oil equivalents. The company has a portfolio of around 60 licenses, and is the operator of the production platform Brage and the subsea field Vega.
In addition to being partner in several large development projects, Wintershall is developing the subsea fields Maria and Skarfjell. The Maria Field in the Norwegian Sea has a planned start-up in the first half of 2018, whilst the plan for development and operation of Skarfjell will be submitted to the authorities in the beginning of the year.
4C
4C Solutions AS (4CS) is an EPC supplier of subsea and surface products mainly for the offshore industry. The 4CS main office is located at Randaberg just outside Stavanger.
The main 4C Solution product range is EPC deliveries of:
• Pipeline and subsea repair systems and components • Diverless tie-in systems for bolted flanges
• Subsea Structures; such as PLEMs, PLETs, SSIVs manifolds and spools • Pig launchers and receivers
• Running tools, installation aids and subsea/ROV tooling • Inline, hot-tap and retrofit tees Partner Companies are:
• DesignBanken AS, Stavanger • Randaberg Industrier AS, Randaberg
• Malm Orstad AS, Voll, Jæren • Isotek Oil & Gas Ltd, Leeds, UK
For over 50 years, ABB has offered products, systems and services across the entire hydrocarbon value chain. We provide an integrated approach for automation and electrical needs that reduces cost, keeps projects on schedule and minimizes risk. We have a proven track record for reliable operations, optimized safety and system availability.
Aker Solutions is a global provider of products, systems and services to the oil and gas industry. Its engineering, design and technology bring discoveries into production and maximize recovery with a focus on sustainability and limiting the environmental impact. The company employs approximately 14,000 people in about 20 countries. Go to http:// akersolutions.com for more information on our business, people and values.
Blue logic is in possession of technical expertise that has designed qualified and produced Hot Stabs since 2000. The founders and technical responsible, had the same job done under the brand Ifokus Engineering. We have spent the first 6 years of the Blue Logic start up to take Hydraulic, Electrical, and Mechanical Interfaces to a new level in terms of industrialisation and standardisation. We have optimised the design to improve all aspects to make them even more fabrication friendly in order to cut cost. In summary we have a long track record in design, qualification of Subsea equipment designed for permanent and intervention use.
Castrol Energy Lubricants provide a full range of subsea control fluids, lubricant solutions and specialist chemicals to the global Oil & Gas Industry.
We are a one stop shop for all offshore lubrication issues – Subsea Production, Surface Production & Drilling.
C-Kore is a fast-growing, innovative UK company passionate about making life easier for subsea engineers by bringing fast, modern and reliable testing techniques to the offshore industry.
Their C-Kore subsea measurement tools save customers money while providing fast and accurate data, measuring insulation resistance (IR) and confirming the integrity of subsea cables.
For too long down-hole testing, fault-finding and installation tasks have relied on error-prone manual measurement, using down-lines of dubious condition or burdensome platform-led testing. C-Kore eliminates these problems, allowing testing to be completed much faster by automating the entire testing process, saving days of vessel time.
Connector Subsea Solutions is the leading specialist provider of complete Deepwater Pipeline Repair Systems worldwide. Our range of solutions are developed from ground up for remote operations, and are characterized by: Lightweight and Small footprint Innovative- Simple Operation, Robust and Reliable, Unique Track Record from Deepwater Repair Operations
The solutions cover both horizontal and vertical repairs, using both Repair-Connectors and Boltless Repair clamps. Our collaboration with Hydratight ensures that the most reliable and field proven equipment available is used throughout.
DeepOcean is an integrated provider of safe, high quality, innovative services and technologies for the subsea industry. Demonstrating an extensive track record, DeepOcean offers a breadth of subsea services, including Survey and Seabed-mapping, Subsea Installation (SURF), Seabed Intervention, Inspection, Maintenance and Repair (IMR), and Decommissioning for the oil & gas, renewable and power transmission industries.
DeepOcean delivers innovative engineering solutions and turnkey project management for complex offshore operations. The company is a leading IMR Contractor and trenching operator in the Greater North Sea and has a global presence with ten offices in Norway, UK, the Netherlands, Brazil, Mexico, Ghana, and Dubai.
A German/Norway based company with a focus on developing and manufacturing turnkey customised data acquisition and telemetry solutions for marine monitoring applications. Our customers are well-known international research institutes, navies and companies in the renewable energy, construction and offshore oil & gas sectors.
DNV GL is the technical advisor to the oil and gas industry. We bring a broader view to complex business and technology risks in global and local markets. Providing a neutral ground for industry cooperation, we create and share knowledge with our customers, setting standards for technology development and implementation. From project initiation to decommissioning, our independent experts enable companies to make the right choices for a safer, smarter and greener future. Our advanced testing capabilities, technical expertise and standards help customers apply technology safely, efficiently and cost effectively. Our Global network of experts and test facilities comprises laboratories and test sites in Norway (Bergen and Høvik), UK, Netherlands, Singapore and USA.
EAB is your specialist on Subsea tie-in and infrastructure from wellhead to point of export – and a part of OneSubsea. EAB delivers: Subsea connection systems, Equipment for installation and commissioning, Subsea intervention and tiein tooling, Subsea tie-in structures like PLEM’s, TEE’s, Riser Bases, Manifolds and UTA’s, FEED studies and Subsea engineering in general
Our solutions are based on standard products and executions, or are tailor made towards customer requirements. EAB has advanced engineering resources specialized on Subsea engineering, a network of experienced sub-suppliers and access to extensive test facilities. EAB’s main shareholder is OneSubsea Processing as. EAB has been in business since 1952
FORCE Technology Norway is a leading technological consultancy company, built on years of experience with development and problem solving. Our history dates back to 1977, with the fo+undation of CorrOcean in Trondheim, before it was diverged to become part of the Danish company FORCE Technology in 2003 as FORCE Technology Norway.
Globally, we represent approximately 1’300 employees, serving customers in more than 60 countries. In Norway, with around 200 employees, we specialise within: Corrosion & materials, Asset integrity management, Inspection & testing, Structural engineering, Structural monitoring, Training & certification
GCE Subsea is an industry driven initiative for strengthening and internationalization of businesses, research and education. We represent the world’s most complete cluster for subsea life-of-field solutions. Our goal is to increase the cluster’s competitiveness and global market share, and take a leading position in sustainable utilization of ocean resources. In order to achieve these goals, we focus on: Develop competence and attract talents and investors, Develop subsea solutions beyond oil and gas, Stimulate technology development, Create new entrepreneurs and grow businesses, Succeed in the global market, Improve work and production processes. More than 120 companies and organizations form the foundation of the GCE Subsea cluster.
•
Co-exhibitors / Entrepreneur companies
Moonshine Solutions
GE Oil & Gas is inventing the next industrial era in the oil and gas sector. In our labs and factories, and in the field, we constantly push the boundaries of technology to solve today’s toughest operational & commercial challenges. We have the skills, knowledge and technical expertise to bring together the physical and digital worlds to fuel the future. Follow GE Oil & Gas on Twitter @GE_OilandGas or visit us at www.geoilandgas.com
Innova AS is a leading supplier of services, equipment and solutions to the international underwater industry. Our business idea is to combine our operational experiences and engineering skills with quality products from own portfolio and respected suppliers of equipment to the underwater industry. Highly qualified personnel, modern design tools and an established network of reliable subcontractors, makes Innova a trusted partner for mechanical design, control system applications, data collection and hydraulic products and services.
Metas AS is a spin off company from the Institute of Marine Research in Bergen, Norway and have since started in 2009 developed new and innovative leak detection systems for the oil and gas industry aswell as subsea observation platforms for scientific equipment, and recently introduced its technology to the fish farming industry. As part of developing the Ocean Observatory in Lofoten-Vesterålen (LoVe) back in 2013, Metas have developed a unique tool, X-LRT® for retrieval and redeployment of sensor platforms connected to a cabled network in order to reduce cost for maintenance. The Sensor Platforms, also developed by Metas could aswell include docking station for AUV`s / mobile subsea sensor vehicles. The X-LRT tool development has been sponsored by Statoil and successfully field tested in June 2017.
SEALMAKER™ is a differentially activated sealant system that transforms from liquid to flexible solid within a leak path when exposed to the dynamic force of high shear rate through a convergent flow profile. Namtvedt Sealmaker is expanding from operating only on the Norwegian Continental shelf. We are now performing operations in UK sector and in Danish sector. Started on a 3 years frame contract with BG in India. We have a daughter company in in Brazil, and first job for Petrobras is under our belt. Our specialists have also executed repairs in the Far East.
Nexans Norway AS is a leading supplier of power, telecommunications, installations and heating cables in Norway, and is among the world’s leading manufacturers of offshore control cables and high-voltage submarine cables. The company’s head office is in Oslo, and it has manufacturing plants at Rognan, Langhus and Halden. The company has nearly 1,550 employees and is a part of the Nexans Group which has an industrial presence in 40 countries and commercial activities worldwide. Nexans employs close to 26,000 people and is listed on the Paris stock exchange. More information on www. nexans.no.
Induction Bending and Heat Treatment of pipes and profiles.
Outer diameter: ø12 mm to ø457,2 mm (18”)
Wall thickness: 1,2 mm to 100 mm
Stainless steel qualities such as duplex, super duplex, 6Mo, Super austenite, Inconel, TP 312/TP 316. High-alloyed carbon qualities such as AISI 4130, 13Cr, F6NM, F22, and carbon qualities such as API 5L X52-X65/ DNV360-450.Clad pipe, aluminium, copper and brass.
Since 1975, Offshore Engineer (OE) has been the monthly go-to source for engineering and technology news and features. Each issue contains news briefs, analysis and data, sector and segment forecasts, project updates, technology reviews and case studies, and industry profiles. For more information, please visit: www.oedigital.com
OneSubsea® delivers integrated solutions, products, systems and services for the subsea oil and gas market. The company offers a step change in reservoir recovery for the subsea oil and gas industry through integration and optimization of the entire production system over the life of the field.
PLM Technology AS is a certified reseller of Product Lifecycle Management (PLM) solutions from Dassault Systèmes and deliver expertise in design, engineering, simulation and manufacturing. We provides the 3DEXPERIENCE® platform that includes dedicated solutions for the Marine, Offshore & Subsea industry. This solution support the entire lifecycle of a product from concept, through design, engineering, production and installation, to service and disposal and includes several well-known software products such as : CATIA for Mechanical and systems design, DELMIA for manufacturing and assembly simulations and SIMULIA ABAQUS that are used by the major classification societies, EPC Contractors and major suppliers to marine industries for advanced Multiphysics, linear and nonlinear analysis.
RadøyGruppen AS have since 1969 been a solid partner in construction. We fabricate complex Subsea Production Systems including steel structures, completing assets ready for our Client`s needs.
We acknowledge our Client`s requirements through our management system combined with the principles of our effective project execution model. We add competent and dedicated staff to meet our Client`s requirements.
We expand our capacities at new sites enabling us to deliver even larger projects. Investing in our Client`s needs are investments in our own future, and the opportunity to deliver projects with value creation through Norwegian quality.
The Society of Petroleum Engineers (SPE) is a not-for-profit professional association whose members are engaged in energy resources, development, and production. SPE serves more than 110,000 members in 141 countries worldwide.
SPE is a key resource for technical knowledge related to the oil and gas exploration and production industry and provides services through its publications, events, training courses, and online resources.
The SPE Bergen Section monthly meetings
SUBSEA 7
Subsea 7 is a world-leading seabed-to-surface engineering, construction and services contractor to the offshore energy industry. We provide cost-effective technical solutions to enable the delivery of complex projects in all water depths and challenging environments. Our vision is to be acknowledged by our clients, our people and our shareholders as the leading strategic partner in our market.
We focus on segments of the subsea market where we can differentiate ourselves by delivering high-quality services built around our core strengths of engineering and end-to-end project management.
Our extensive experience in deepwater Subsea, Umbilical, Riser and Flowline (SURF) and Life-of-Field projects has made us the preferred contractor and trusted partner for national and international energy companies.
SubseaDesign AS is an engineering, design and fabrication company providing high tech. level of equipment and services for the oil and gas industry.
SD offers a variety of special products including SeAlign™ misalignment connectors, ROV operable for all water depth. SD was in 2016 awarded the contract for delivery of 72 off SeAlign connectors 8’’ – 18’’ to Statoil on the J. Sverdrup project, including Frame Agreement. SD has also delivered connection systems ROV operable for Statoil Tordis Field. Other connection products are Collet Connector from small 4’’ to larger 18 ¾’’ 10k Wellhead Connector.
In conjunction with Wellhead Fatigue during drilling, SD has delivered more than 30 systems of WLR (Wellhead Load Relief) to various fields operated by Statoil, Suncor, ExxonMobil and Wintershall. Hydraulic connectors with high CV factors are available up 15k.
The Society for Underwater Technology (SUT) is a multidisciplinary learned society that brings together organisations and individuals with a common interest in underwater technology, ocean science and offshore engineering. SUT was founded in 1966 and has members from more than 40 countries, including engineers, scientists, other professionals and students working in these areas.
Sysla.no is a business news site that covers the ocean industries (oil/gas, maritime and aquaculture) and renewable energy. Sysla has approximately 30 000 unique readers each day, mostly readers who work directly or indirectly in the industries sysla.no cover.
We’ve learned a lot in 175 years. We like to share it. Building on 175 years of technological and engineering excellence, our employees in more than 20 countries are now driving development to help solve the world’s energy needs safely and sustainably.
Teknisk Ukeblad is Norway’s leading technology and business magazine and is published with 18 issues each year.
Teknisk Produksjon (TP) is a provider of machining and fabrication services, including NDT and pressure testing, to the mechanical industry, including the oil and gas area. TP has, among other types of products, manufactured compact flanges for subsea use for 30 years.
TP Connectors (TPC) was established in April 2016 and supplies a product range of compact flanges and clamp connectors. The staff at TPC has long experience with these types of products from other companies.
TP Asker Subsea, acquired by TP October 2016, has designed and manufactured different subsea products for more than 25 years. The most important product areas have been subsea valves and connectors (the Asker stab).
By using advanced polymer material technology, Trelleborg’s offshore operation provides high integrity solutions for the harshest and most demanding offshore environments. Trelleborg’s offshore operation in Norway have 120 years of experience with development and production of rubber-based products and solutions. Our core products are corrosion protection, thermal insulation, passive and active fire protection solutions. Rubber is also an excellent construction material, which dampens vibration and absorbs shocks. From our factory in Norway we deliver tailored solutions and standard components for customers worldwide.
Westcon Subsea is a provider of high quality fabrication, maintenance and testing of subsea equipment and tools. Focusing on innovative technology to solve our customer needs, makes Westcon Subsea a preferred partner for developing and delivering cost efficient subsea equipment.
Westcon Subsea is part of the Westcon Group, and can provide all services from our Yard facilities from South to North in Norway.
WiSub is a subsea solutions company developing and delivering wetmate pinless connection systems to transfer power and data safely and reliably underwater. The team leverages decades of experience in subsea equipment design and operations to deliver relevant, client-focused products and systems.
Leveraging patents within non-contact data and power transfer, WiSub’s innovative and flexible solutions provide greater freedom to subsea equipment designers and operators, evolving traditional complex mechanical systems using solid-state electronics.
WiSub’s mission is to design and deliver advanced subsea connection systems to reduce clients’ costs and increase operations reliability and uptime, realising the vision of “No Pins, No Pain”.
DIGITIZE YOUR ASSETS, VISUALIZE YOUR FIELD, COLLABORATE WITH YOUR TEAM
Field Activity Planner enables a digital working environment for your organization for visual field development, digital planning and cost management. Field Activity Planner serves as a collaboration platform between experts, disciplines and companies involved in the life of field perspective.
Allowing you to REDUCE COST in the design process for the whole value chain by quickly finding the best solution in the design phase and by shortening the total project lead time is just one of the many benefits. Learn more at www.fieldap.com
In a challenging market it is increasingly important for operators, suppliers and service providers to meet and share ideas, initiatives, developments and solutions. The UTC Exhibition will be a vibrant and important arena for subsea updates and information. At UTC you will meet executives, managers, engineers and other strategic and planning personnel related to the subsea field of the petroleum industry. Students are also especially invited to the UTC exhibition. The exhibition will be open for other professionals, not participating at the conference, at these hours:
Wednesday 21 June: 10:30 – 16:00
Thursday 22 June: 09:00 – 14:30
Guests have to register at the entrance, no entrance fee will apply. Guests will be given the opportunity to buy lunch tickets at registration.
We encourage all exhibitors to invite their business partners to visit the UTC Exhibition.
The OneSubsea portfolio of standardized designs supports streamlined processes, documentation, and manufacturing to deliver integrated production systems that enable achieving first oil as soon as 24 months after contract award.
Customized to your field architecture, these capital-e cient solutions help you maximize recovery from new fields to transform deepwater economics across the life of the asset.
Each issue contains news briefs, analysis and data, sector and segment market forecasts, project updates, technology reviews and case studies, and industry profiles.
OE’s mission is to seek out the latest technologies, from leading edge subsea processing to equipment and methodologies that will save time and cost and increase efficiency. We lead in our coverage of new improved oil recovery techniques, subsea and topside robotics, and the latest well intervention techniques.
OE is a leader in its coverage of the burgeoning decommissioning industry, covering, in-depth, the latest technologies, concepts and vessels, as well as the environmental research that will underpin future decisions in this market.
Similarly, OE regularly focuses on offshore renewables, with our July issue dedicated to the topics, profiling the latest advances in offshore wind and ocean renewable technologies across the world.
We’re also embracing the new digital era, with regular features on operator efforts towards digitalization and a quarterly focus dedicated to automation. Each month, we also shine a light on a different region of the world, keeping readers abreast of the latest developments in everywhere from Alaska to Vietnam.
OE also produces bespoke sector and region reports. For the past three years, OE has compiled annual reports on the globally leading Norwegian Subsea sector, as well as the innovative Dutch offshore marine industry, and keeping readers up to date on efforts to reform Mexico’s energy sector.
In Q1 each year, OE partners with GCE Subsea to shed light on the latest Norwegian led subsea innovations. Every March, OE releases its Mexico report, featuring Q&As with industry experts that have long-established connections to the oil and gas industry (CGG, Weatherford, and TGS). In Q3, OE also produces the Dutch offshore review.
OE also has a strong events portfolio to encourage the spread of industry lessons learned. For 23 years, the magazine has organized the annual Petroleum and Exhibition Conference of Mexico (PECOM) in Villahermosa, Tabasco – the oil capital of Mexico - which attracts more than 6000 delegates from over 1200 companies, drawn from more than 40 countries. The conference program included industry leaders from federal and local government entities.
Each August, OE hosts the annual Deepwater Intervention Forum (now in its 13th year) and the Global FPSO Forum (now in its 7th year), highlighting technological advancements, case studies, regulatory updates, and important lessons learned from both sectors.
OE delivers a range of focused newsletters and webinars. And in July 2016, OE released a brand-new, leading edge digital edition platform that allows readers to read OE on the go – with no app required.
As well as supporting leading events such as the Underwater Technology Conference, in Bergen, OE has a long-standing partnership with SPE Offshore Europe. This year, we will again produce the official show daily for the show.
At OE’s core is a drive to showcase the challenges and achievements of the offshore upstream industry. We’ve done it for 42 years and we hope to do it for many more years yet.
The Underwater Technology Foundation (UTF) is a non-commercial entity established in 1980 when several large oil-related companies joined forces to arrange the Underwater Technology Conference in Bergen. The foundation’s goal is to promote increased knowledge of the subsea sector. This is achieved by hosting the conference and giving contributions to research and training at university level. UTF offers a grant available to applicants in need of financial support for a subsea related research or training project. The foundation would like to see more applicants for the grant, and encourages anyone with a relevant project to apply.