
2 minute read
Small Enterprise with a Big Reach
The parasols of Pathein combine tradition with innovation and prove a hit in the hot season
By KYAW HSU MON / PATHEIN, Ayeyarwady Region
The hot season has well and truly arrived, and while many are sweating it out as a result, it’s good news for makers of the famed Patheinhtee (Pathein parasol), who are reaping the benefits of high demand from shadeseekers.
The parasols of Pathein, the capital city of Ayeyarwady Region, are an internationally recognized part of Myanmar’s iconography. It is an industry, made up primarily of smallscale workshops, that has been turning out the colorful creations for more than 100 years.
U Thein Oo, owner of the Nay Nat Thar Pathein Htee workshop in Pathein, said demand this summer, as in years past, has risen significantly. At his homebased factory, employees can produce 250 parasols per day, and the enterprise has been selling out its stock nearly every day as temperatures have climbed. Prior to the summer season, his workers produced less than 200 parasols per day.
“We’re distributing to all cities nationwide, especially in Mandalay, Bago and Mawlamyine,” he said.
Using a division of labor process, each step in the production of Pathein parasols is assigned to an individual. Most parts, except for the wooden finials that are set atop the parasols’ canopies, are handmade.
U Thein Oo said that in the past, the parasols’ canopies were made from paper, but over the years the Pathein craftsmen have flexed their creative muscles, and now produce parasols with canopies of cotton, silk and satin as well, wall hangings or lampshades. in attractive floral-pattern designs.

In the production process, the parasol’s main shaft is made of a wood known as ma u shwe war . The ribs and stretchers are made from a type of bamboo called taragu, which grows around Pathein city.
“All parts of the parasol are from around the Pathein area, except silk and cotton canopies, which are bought from Yangon,” U Thein Oo said.
“There are three sizes we’re producing right now: The biggest one is for garden use, and two [smaller] sizes are for ladies’ use,” he said.
U Thein Oo’s business employs 15 workers, some of whom operate rudimentary machinery used for some of the woodwork.
U Maung Kyi, a craftsman in the workshop, said that he earns just 8 kyat (less than 1 US cent) for each wooden finial that he produces. In an average day, he says, he makes about 100 finials.
Workers bind the main shaft, ribs and stretchers together, and stretch the parasol’s canopy across this frame.
In the last steps, the cloth is dyed and coated with tayae (natural fruit juices) to help the canopy maintain its vibrant coloring. Workers varnish and polish the wood before leaving the parasols to dry in the sun. The painting of designs on the cloth serves as the final touch on a Pathein parasol.
After attaching the canopy to the wooden frame, the parasol undergoes strength testing to ensure its durability.
“In the past, we used a paper that was made in Shan State. Now, we’ve created new silk and cotton canopies. We dye them to be colorful and then glue them to make them stronger and more attractive to customers,” he said.
These re-envisioned Pathein parasols have helped fuel sales among local buyers, who are largely women. Pathein parasols are also highly sought after by the growing number foreign visitors, who purchase them as souvenirs, or for interior decoration as
“We’re distributing at 2,000 kyat [$2] for a large ladies’ use parasol as a wholesale price, but in retail shops, prices are almost double,” U Thein Oo said. The production cost of a parasol is 1,000 to 1,200 kyat, depending on the size.
Although Pathein parasols have traditionally been known for their practical purpose and as a fashion accessory, they are increasingly deployed to serve decorative purposes in home interiors, gardens, hotels and restaurants.
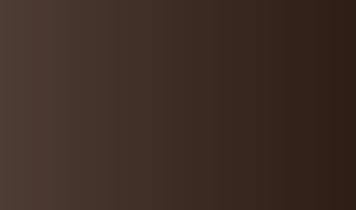