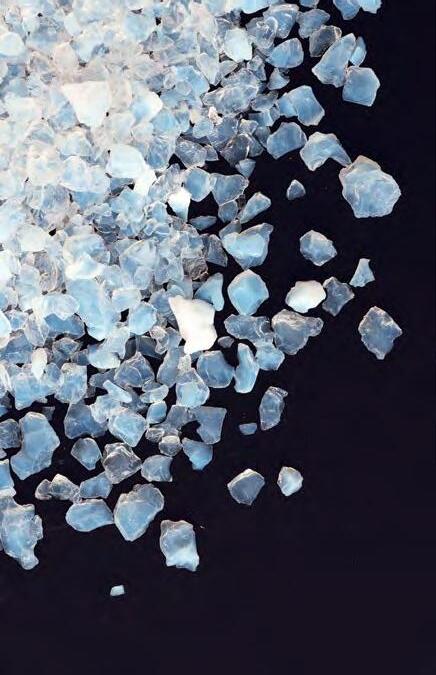
5 minute read
The Silicosis Crisis
By Ted Sherritt, ISFA President
Over the past few months, a lot has happened in the slab quarrying, manufacturing, distribution and countertop fabrication industry. From Cal/OSHA’s Emergency Temporary Standard that came into effect December 29, 2023, which mandates no dry cutting, grinding, or polishing; the use of powered air-purifying respirators (PARPs); and employee medical testing, to Australia’s engineered stone ban set for July 2024, there is a lot of talk about silica safety. To be sure, these developments will have profound impacts on the decorative surface industry as we know it today.
The overarching issue at the heart of these changes is the exploding number of stone workers developing silicosis because of respirable crystalline silica (RCS) in fabrication shops and on job sites worldwide. Silicosis is one of the oldest industrial diseases documented — first identified in the 15th century. When RCS gets lodged in the lungs, it results in scarring that significantly reduces the ability to breathe. There’s no cure; advanced cases are debilitating and can result in death. As employers of workers who are exposed to RCS, it’s imperative that we keep this issue top of mind and do our best to stay informed about silicosis and do whatever we can to mitigate it.
Because silicosis is 100% preventable, we must all work diligently toward eliminating this disease within our industry. If we don’t, we’re facing far-reaching disruptions that will negatively impact each and every one of us.
The traditional course of silicosis development occurs due to exposure to RCS over a long period. But with the exponential growth in market share of hard surfaces like granite, quartz, porcelain and sintered materials — particularly in the kitchen countertop segment — we’re seeing a substantial increase in this disease.
Over the last two decades, the demand for premium countertop surfaces has been fueled by significant increases in the home equity value as a result of the housing bubble, low interest rates providing affordable renovation budgets, the influence of home improvement television, the significant reduction in the material costs, improvements in manufacturing and installation processes, as well as other factors. In the end, hard surface countertops have elevated to heightened demand from homeowners.
In order to meet this increased demand, there has been a massive boom in the number and type of fabrication facilities throughout the world. The countertop industry has many different kinds of fabrication companies, from highly automated large-scale operations to 2-5 person shops. Some of these fabrication companies comply fully with safety regulations, some are trying hard to get compliant and some are operating unaware of the governmental requirements in their area. And some are disregarding these requirements altogether — operating in clear violation of the local laws and regulations and putting profits ahead of worker safety. Each of these companies needs different support and enforcement methods to ensure worker safety.
The shops that are not complying with government regulations that require a safe work environment for their employees are a result of:
1. The owner’s engineering and administrative controls are ineffective.
2. The owner is not informed about their legal responsibility to their employees.
3. The owner intentionally ignores the law to increase profits by not protecting their employees.
The first group needs to continue to apply engineering and administrative controls to further reduce RCS in the workplace. These shops are actively making improvements that will effectively control the level of RCS and will create safe work environments for their employees. Many ISFA supplier partners have products and information that can help you develop methods to control the RCS dust. If you fall into this category, you are not alone. Please reach out to your supplier and take advantage of their resources.
The second group needs to prioritize informing themselves of their legal requirements around air quality and worker safety and then work diligently to comply with the legislation in their area. For the uninformed, education and awareness campaigns must be established to get these owners to follow the law. ISFA and the Natural Stone Institute are working together to provide training and certification for employers and employees working in the stone industry to eliminate this knowledge gap. Ignorance of the requirements is not a defense for noncompliance.
The third group is a liability to us all. Government regulations must encompass the authority to stop these businesses from operating at all. Many of these fabrication shops have been using techniques that include dry cutting, grinding and polishing without engineering and management controls to suppress the RCS dust. In these environments, the level of RCS exceeds the permissible exposure limit (PEL) and action level (AL) many times over. It’s hazardous to employee health — even those who work adjacent to the shop floor can be impacted. Shops that operate dry — without regard for the OSHA-required level of air quality — are among the most significant contributing factors to the rise in silicosis cases in recent years.
The entire industry, including quarriers, manufacturers, fabricators, installers, regulators, trade associations and others, must work together to support responsible operators and business owners while eliminating the “bad actors” that are focusing the regulatory spotlight on our industry for the wrong reason. If we all work together, we can keep our workers safe while our businesses continue to thrive.
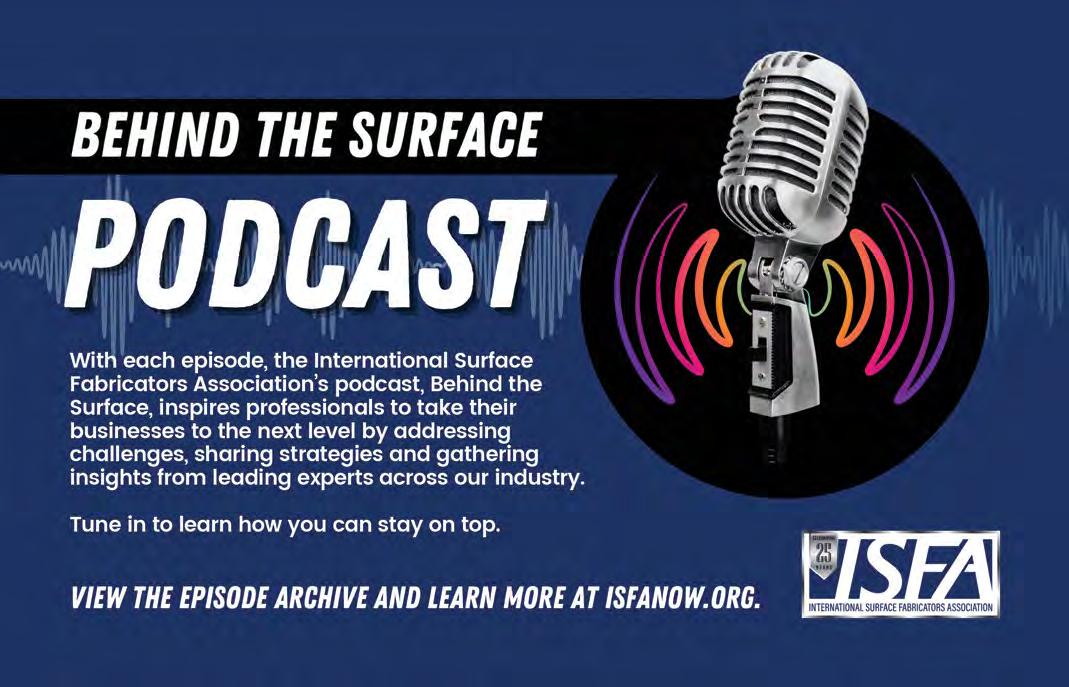