
5 minute read
Five Reasons To Start Using Cartridge-Based Adhesives
By Louise Scott
Time, Time, Time.
Let’s look at a day in the life of a stone fabricator. The fabricator’s first job of the day is to glue up some mitered edges for an upcoming installation. The process begins with the fabricator opening a can of adhesive. They take out a large scoop onto their mixing board, making sure there is more than enough to complete the job with one mix. After inspecting the color of the countertop to be assembled, they slowly add pigments, mix it all together and inspect the match. They realize more pigment is required, add more and mix again, repeating until the color is finally close enough. They add their activator and give one final mix. Next, taking their palette knife they begin applying adhesive to the edge, trying to keep the adhesive application even, while moving quickly to transfer all the adhesive needed from their board to the countertop edge. It’s a race against time to get all the adhesive applied and then position the slabs into place and clamped before the adhesive sets; the adhesive is curing whether they’re ready or not. After assembly, our fabricator is left with their mixing board of excess adhesive, adhesive dripping on the floor, and adhesive squeeze-out to clean off the surface before it sets.
Now imagine that first fabricator is a new employee. The time to train and get good at mixing pigments and learning the technique for mixing and applying adhesive is significantly longer than training a new employee on a cartridge.
If that same fabricator used a tube of premixed adhesive, their first job would be to pull up the color match app and find the correct adhesive to use. Then they head over to the shelf and grab the cartridge and a new mixing tip, pop it on, give it a purge, and begin laying a bead. Laying down the perfect amount of adhesive in seconds, they’re able to stop and assemble as they work as the adhesive that’s still in the cartridge won’t cure until they need it. And because they were able to use exactly what they needed, there is little waste material on the floor, and only a tiny bit left in the mixing tip to be thrown away. The cap is replaced on the cartridge, ready to be used again for the next job. Using cartridges instead of bulk means shorter onboarding of new staff and the ability to use subcontracted labor if required.
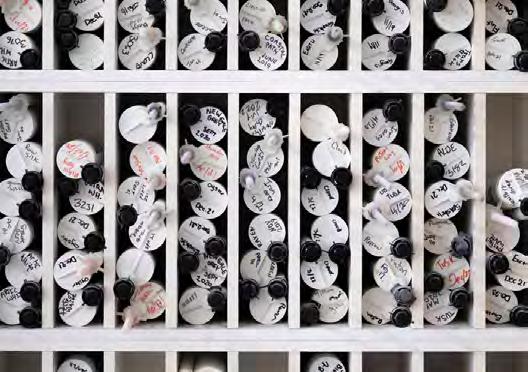
Ready to use color matched adhesives.
Consistent, Repeatable Results.
Cartridge-based adhesives create standardization in the fabrication process. They ensure the perfect mix of adhesive and hardener, and perfect color matches. Mixing tips eliminate air pockets that are often introduced with hand mixing. With more time to fix and assemble, removing color matching from the equation, and no air pockets, every fabricator can produce the same quality of work quickly and easily.
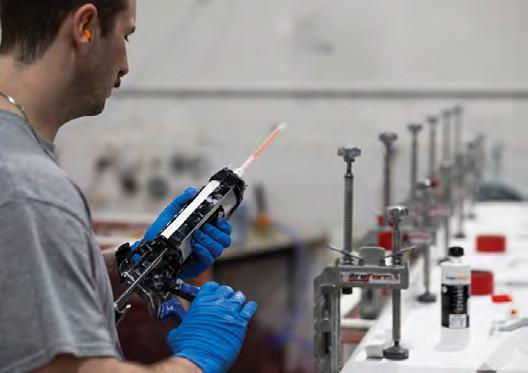
Quick purge and you’re ready to apply.
Industry surfacing trends have moved to clean whites, grays, neutrals and blacks. Gone are the days of surfaces with various colors and large pieces of quartz to help hide seams. Unfortunately seams are harder to hide, and customers have higher expectations. An adhesive with the correct color and transparency is a must.
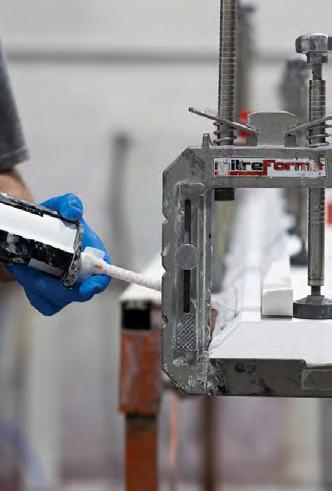
Apply color matched adhesive.
Health, Safety and the Environment.
Cartridge-based adhesives use the latest Methyl Methacrylate (MMA) technology, and they come with the GREENGUARD Gold certification which means they are free from styrene, isocyanates and other harsh chemicals. They are safer for employees and safer for customers in the environment where the countertops are installed. Because the fabricators aren’t mixing chemicals right under their nose and there is less chance of spills, cartridges reduce unsafe exposure.
In addition, cartridge-based adhesives have minimal waste. As the adhesive is dispensed, the pistons in the cartridge clean the inner walls of the tube, meaning every bit of product is removed from the cartridge and usable for installation. When the cartridge is empty, it is ready for disposal.
Technology Has Changed.
Some fabricators believe that MMA adhesives are good for solid surface, but not strong enough for quartz or stone. This is not the case. Today’s cartridgebased MMAs can tackle the toughest tasks, they are strong and durable, and they have been stringently tested.
Interior trends are seeing countertop materials being applied vertically to walls and fireplaces and large waterfall edges. The results are dramatic and exquisite. New challenges require MMA adhesives to offer advanced properties of greater shear strength and reduced sag on application.
Demand for outdoor installations has also forced adhesives to adapt to weathering conditions and ultraviolet exposure. Integra Adhesives is one such manufacturer offering adhesives like Surface Bonder Zero and Rapid designed specifically not to drip, making it perfect for vertical or angled applications. Surface Bonder Ultra, developed for higher strength bonding on ceramics, is weatherproof for outdoor kitchen applications.
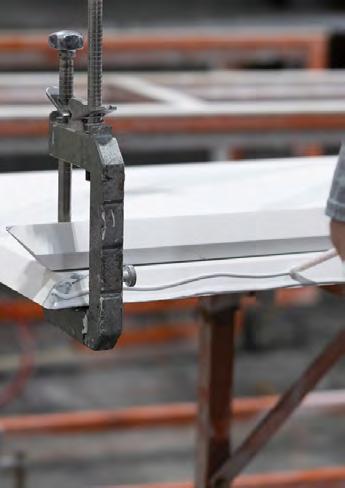
No drips or air pockets.
Every aspect of assembly has been tested, and in every case, the MMA cartridge-based adhesives provide a more consistent result, easier application, less waste and faster throughput.
Cartridge-Based Adhesives Are Cost-Effective.
Looking purely at volume, one might compare the cost per milliliter of a can of knife grade adhesive versus a cartridge of premixed adhesive and come to the incorrect conclusion that cartridge costs more.
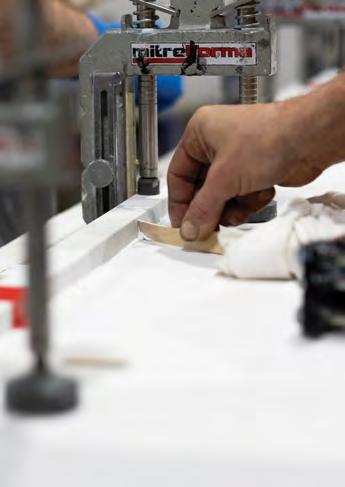
Easy to clean up with minimal waste.
Instead, considering the savings from mixing, curing time, quality, training, waste, and most importantly, safety, the postive impact of cartridge-based adhesives becomes more evident.