
4 minute read
Improve Workplace Safety and Productivity with Overhead Cranes
By Paul Hershberger
When most people think of a crane, they think of the giant cranes used to build skyscrapers or other tall structures. But have you considered that cranes can help lift heavy objects inside a building? These types of cranes are called overhead cranes. They’re used in many industries to move heavy loads safely and efficiently.
Advertisement
Many manufacturers and fabricators have a workspace that is holding back production. Overhead cranes can transform any workspace by improving efficiency and reducing worker fatigue. While there is an initial investment upfront, an overhead crane will help your company save costs in the long run and increase profitability.
So how do overhead cranes promote workplace safety without hindering productivity?
Overhead cranes are an efficient way of moving heavy objects from one area in a workplace to another. They are made up of a bridge that spans the work area, and a hoist that travels the length of the bridge. This hoist is the muscle and does all the heavy lifting. Overhead cranes can often lift .25 to 2 tons, so you’ll be able to move heavy loads with ease. For fabricators, it means they can easily move slabs and other heavy materials.
Moving heavy material in the shop takes a lot of manpower. It’s manual labor that adds to worker fatigue and downtime in production. Workers’ safety is put at risk by having to carry loads by hand or use a forklift, and forklift accidents are all too common. Regardless, a forklift doesn’t carry loads as steadily and safely as an overhead crane, and it can take a lot of time to navigate a forklift from one area to another in a busy shop. It often takes two men and a forklift to do the work of a single workstation crane.
Overhead cranes require one operator, thus reducing the required manpower. Cranes can be operated remotely with a wireless radio control, making it easy to lift a heavy load with the push of a button. Workers won’t have to hunt down a forklift; they can just pick up a radio and get to work. While only powered cranes can be controlled with a radio, most overhead crane manufacturers have this option.
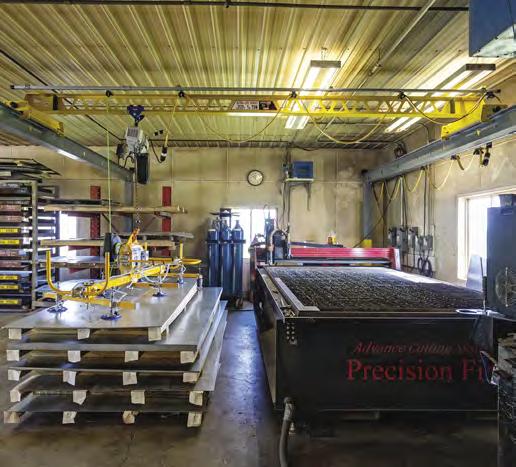
J.R.’s Metal uses a workstation crane for a specific process. This process is using a vacuum lifter to lift and move metal sheets onto a machine to be cut.
Many fabricators see the value in the investment of an overhead crane. Most overhead cranes are more affordable than you might think. It is an upfront investment that will save you costs down the road. A 10-by-15-foot, half-ton workstation crane costs less than $8,000 while a new forklift could cost two to three times more. While a forklift will need to be replaced after 10,000 to 12,000 hours, an overhead crane will not need to be replaced if proper inspections and maintenance are performed. Annual inspections for some cranes can cost as little as $200 per year.
“Our operators love the ease of use [of a workstation crane] and the enclosed festoon system is pretty great as well,” says Paul Jochim, a plant manager for a piping solution company. “The columns are very substantial compared to other systems that we’ve bought.”
Overhead cranes come in several different types so you will be able to get the appropriate one for your workspace. Motorized cranes are more expensive than manually operated cranes and depending on the workspace, the manual crane may be the better option. 1. Bridge cranes: These are the most typical overhead cranes for material handling needs. They consist of a bridge that is supported by a runway. 2. Workstation cranes: These are the most
lightweight and economical option and can be installed in any workspace. These types usually handle fast, lightweight materials. 3. Jib cranes: This option makes it easy to hand off materials from one workstation to another because they rotate 360 degrees. 4. Gantry cranes: This type of crane is smaller and usually moves on wheels. It allows you to physically move the crane to different work areas.
Overhead cranes can cover a single workstation or several workstations, allowing loads to easily move from one area to another. You can add multiple bridges or hoists, so your workspace will be configured to maximize productivity. There are specific attachments that can be added to customize based on the task. One crane attachment, the horizontal slab lifter, has two jaws that clamp down on a slab. The attachment allows for easy lifting of a slab so fabricators can move it to the next production area.
You can also get a crane system as an assembly kit that you can install yourself, and you can be up and running in as little as two days’ time. A typical assembly kit includes four column posts, two runway beams, a rolling bridge, a hoist, a trolley, and electrical components (if motorized). Cranes are typically mounted onto a concrete floor. A crane manufacturer will work with you to provide drawings to ensure that your crane will fit in your space.
When it comes to looking at efficiencies and profitability, an overhead crane could be just the thing that takes your shop to the next level.
Paul Hershberger is the Vice President of Sales for PWI. PWI has over 40 years of experience building overhead cranes that promote workplace safety and efficiency. For more information on how PWI can help you employ overhead cranes in your workflow, contact info@pwiworks.com or visit pwiworks.com.