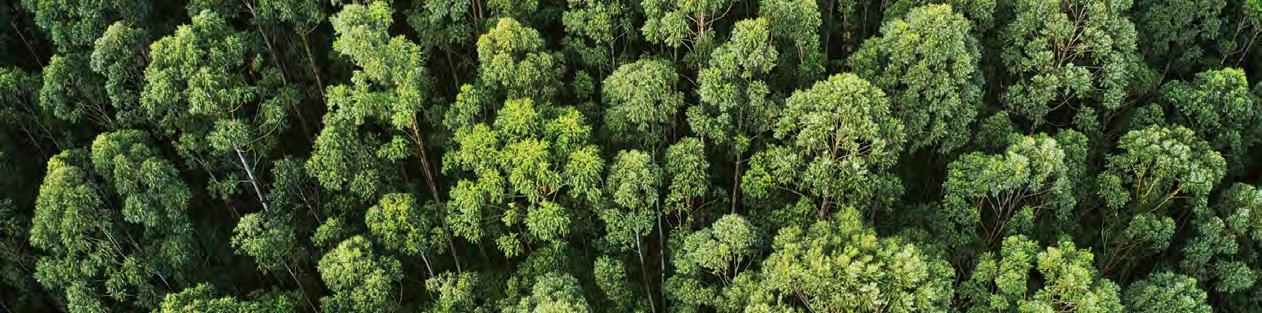
6 minute read
SUSTAINABILITY MATTERS: Safeguarding Sustainability
By Jessica McNaughton and Paul “Max” Le Pera
In this installment of the Sustainability Matters series, we arrive at a topic argued to be one of the most crucial aspects of our work in the fabrication industry: safety. Although it may appear disconnected from sustainability, it is critical. Safety transcends routine practices and accident prevention and extends its influence through procurement processes — even delving into the components of materials. Without the implementation of comprehensive safety measures, not only do you jeopardize the success of your business, but, more importantly, you endanger the well-being of your workforce. Sustainability means safeguarding the planet and its inhabitants; hence, safety is a paramount concern.
The Making of a Safe Facility
From the moment you acquired your workshop, secured your workspace and procured equipment, the safety of individuals occupying these areas and commanding these machines should have been a top priority. Ensuring the well-being of your employees necessitates establishing standard safety procedures, proper storage for blades and tools, protective personal equipment, eyewash stations and more. Equally vital is the presence of certified forklift operators and material handlers and the implementation of sound packaging and storage practices — all of which are instrumental in safeguarding your employees.
Within the confines of your facility, equipment must be safe to operate while sufficiently capable of carrying out the necessary tasks securely. Forklifts, overhead cranes, carts and appropriate tooling are indispensable for minimizing the physical strain on your employees. Safety equipment, including hard hats, gloves and other protective gear — notably respirators and masks for those exposed to airborne particles, discussed further below — are widely recognized as essential tools. Continuous and fundamental training on proper equipment operation is imperative to uphold safety standards.
Equipment continually evolves, becoming safer, more efficient and reducing downtime. For instance, transitioning from propane forklifts to electric alternatives can enhance safety by eliminating employee exposure to indoor fumes. Sustainable energy systems such as solar and water recapture mechanisms are pivotal to minimizing your facility’s environmental impact.
Some equipment manufacturers introduce safety features post-purchase. Remaining vigilant about equipment changes and upgrades can boost your bottom line and enhance your employees’ efficiency, potentially allowing you to accomplish more with fewer resources. Improved equipment handling and increased automation of equipmentrelated processes can curtail employee exposure to hazardous procedures. In addition, let’s not overlook the fact that safer, happier employees are typically more productive.
The Problem with Silica
Crystalline silica has taken a prominent position within the industry, becoming a focus of discussions, as industry associations and their partners are actively engaged in finding ways to effectively mitigate risk and impart knowledge regarding its inherent dangers, from the manufacturing process to installation. This ubiquitous material is found in an array of products, including concrete, masonry and luxury quartzites, where it presents hazards if not handled with care and appropriate equipment.
Endeavors to ban engineered stone have surfaced in Australia and the United States, particularly in California’s Los Angeles County. While the installed material is generally safe for end users, architects and designers are keen to ensure safety and sustainability from the initial extraction phase to the end of its useful life.
The extraction of crystalline silica, as well as its subsequent fabrication and polishing, entails inherent risks. Although guidelines and standards exist for proper management, recent audits have uncovered a concerning number of companies failing to adhere to these norms.
A steadfast commitment to safety necessitates establishing comprehensive procedures and continuously implementing educational and training programs. Given the rapid developments in sustainability and safety measures — particularly regarding crystalline silica abatement — companies must adopt a proactive stance rather than reacting to emerging challenges regarding equipment enhancements and procedural improvements. Safety, symbolized by hard hats and orange vests, is intertwined with sustainability, and dismissing either in the current state of our industry would be unwise.
The Innovation of Safer Materials
Prominent industry leaders have begun introducing new materials that remedy the silica problem. Notably, Lapitec from Breton, a pioneer in quartz production, emerged as an alternative to quartz, primarily due to its reduced crystalline silica content. Breton revealed the development of its BioQuartz technology, a new process line for engineered stone without any crystalline silica. The pace of innovation continues with Cosentino’s HybriQ technology, which has significantly reduced silica content in Silestone compositions, with the goal of reaching zero. Lapitec has transitioned its entire sintered stone production to be silica-free, while Caesarstone publicly expressed its intent to meet a crystalline silica content threshold of 40% or less.
Subsequently, Cosentino’s Dekton and Neolith and several other companies have introduced lower silica options for quartz countertops, including sintered and porcelain materials. More manufacturers are likely to follow suit.
The Future of Sustainability Through Safety
As we breached this rather large topic of safety at many levels here and placed it as a significant pillar within the domain of holistic sustainability, what survives now and poses the greatest stress on sustainable progress rests in three main areas: leadership, culture and commitment. Sustainability and employee safety remain intrinsically linked in this evolving landscape.
For example, while the risk of silicosis is not new information to most fabricators, the prominent reactivity to the health hazard is. For safety to become a truly viable and effective pillar of the sustainability paradigm, it must be championed — proactively. Although this is more of a moral, ethical and human respect issue, let’s address the elephant here quickly: Safety is not an expense; it is an investment.
That said, as a company systematically prioritizes safety and sustainability, the goal is to protect those who are contributing to your business’s success — those who put their futures at stake for your profits. They have every right to expect their safety to be taken seriously and championed. With leadership setting a high bar through intentional investment and demonstrated actions, we begin to see the development of a company culture around safety. Any positive investment into company culture will profoundly affect productivity and loyalty — a powerful synergy.
Safety starts at the top. It must be embraced as a core value to yield its efficacy. Fabrication company owners and managers have a decision to make every morning: “Are my people safe, and if not, where are the vulnerabilities?” Safety is something that is never too late to embrace, improve and champion. Investing in safety is a deep-rooted pillar of servant leadership, and the more that is invested in people and safety culture, the more fluid and sustainable the operation can be. Again, safety is not an expense; it is a wise and necessary investment.
Jessica McNaughton serves as president at CaraGreen, a provider of sustainable building materials, including many alternative surfacing materials. She has 20 years’ experience in sales, marketing, business development and strategy. Previously the director of sales and marketing at CaraGreen, Jessica has maintained her status as a LEED Accredited Professional since 2009 and she hosts a podcast, Build Green Live Green. She can be reached at jessica@caragreen.com.
Paul “Max” Le Pera is the president and founder of Proprietary Ventures, LLC, a boutique-style global firm devoted to researching, discovering and deploying disruptive and sustainably oriented proprietary products and technologies. He serves on the ISFA board of directors as vice president of standards. He can be reached at paul.l@proprietaryventures.com.