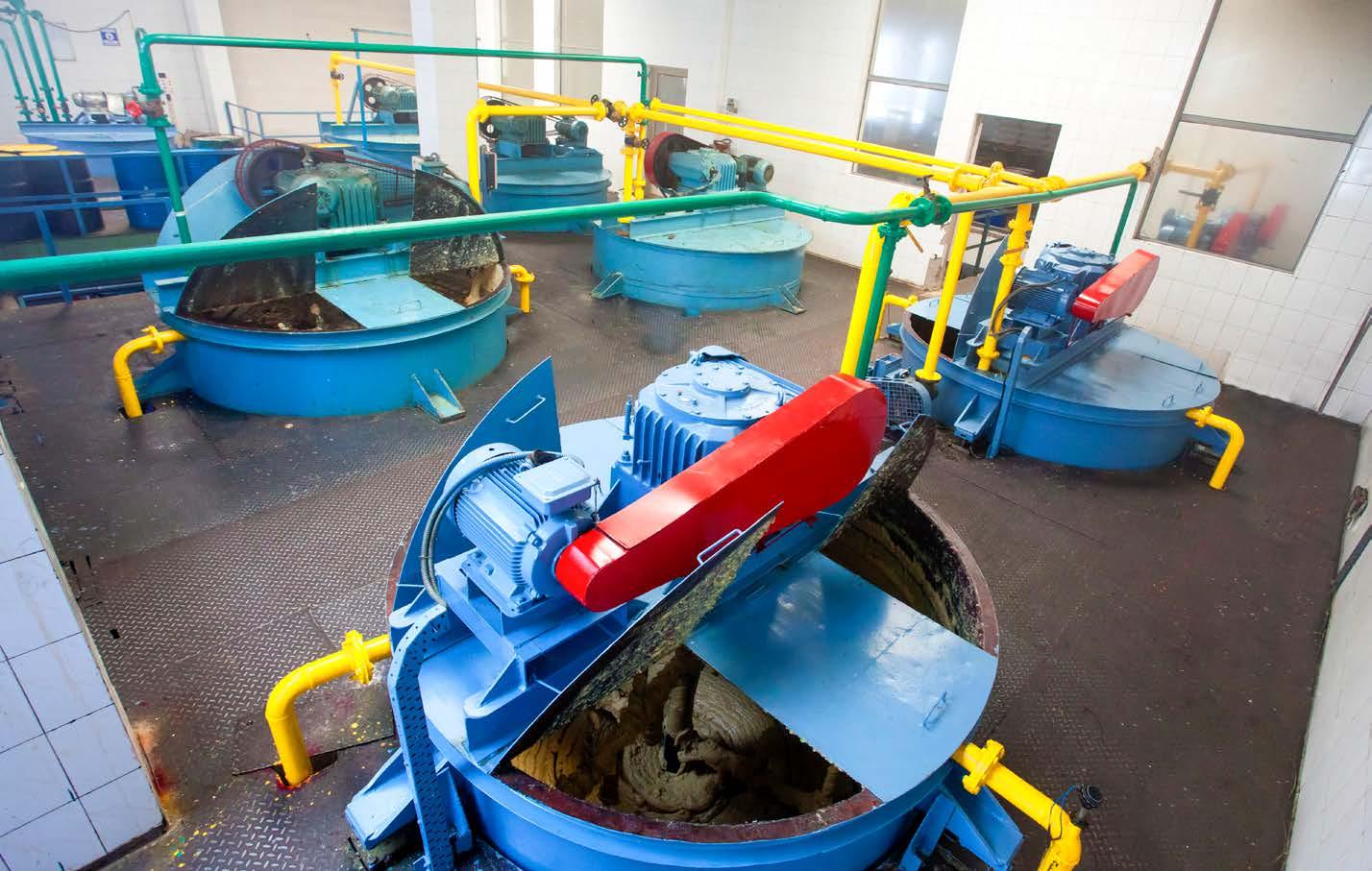
3 minute read
LUBRICATING GREASES INDIAN SCENARIO LUBRICATING GREASES INDIAN SCENARIO
The lubricating greases are composed of three components: oil, thickener, and additives. The base oil and the thickener are the major components in grease formulations. The thickener is often referred to as a sponge that holds the lubricant (base oil plus additives), which provides the lubrication.
Lubricating grease by and large has played a significant role in the advancement of modern industry. The history of lubricating grease goes back to the hoary past, may as old as beyond 1400 BC. The documented evidence indicates that the first use of grease perhaps has been in automotive industry in lubricating wheels of chariots etc. At that point of time, the concept of use of greases would have been based on vegetable oil-based products. The use of mineral oil-based products was triggered only after Colonel Drake drilled the first oil well in 1859. This revolutionized the total industrial sector. The use of lubricating grease in automotive and industrial sectors is quite substantial.
Advertisement
As per ASTM D 288 (American Society for Testing and Materials), the lubricating grease can be defined as “A solid to semifluid product of dispersion of a thickening agent in liquid lubricant. Other ingredients imparting special properties may be included”.
Lubricating greases basically consist of base oil (7095%), thickener (3 - 30%) plus performance additives (0 – 10%). Both base oils as well as thickeners influence the properties of lubricating grease. Performance additives are used to boost the certain desired properties of greases.
Indian Grease Scenario
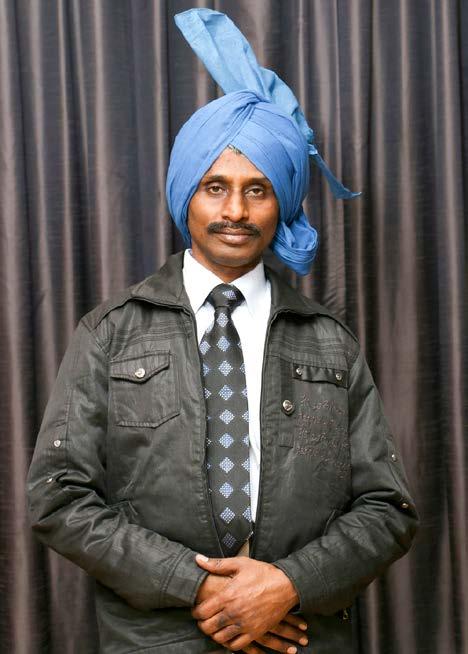
Indian Grease Market: Grease Consumption %
45% Automotive 55% Industrial
As per our estimate Indian grease market is around 150 TMT in organized and unorganized sectors. The thickener wise breakup is – Lithium 70%, Lithium Complex 5.1%, Sodium 3.5%, Non-Soap (Polyurea and Clay Based) 1.5%, Aluminium and Aluminium Complex 2.5%, Calcium, Calcium Complex and others 14.9% and Calcium Sulphonate 2.5%.
Thickener-wise breakup at elevated temperatures, thus requiring a frequent relube interval.
Additives: Additives can play several roles in lubricating grease. It is used from 0 - 10% by wt. in grease composition. These primarily include enhancing the existing desirable properties, suppressing the existing undesirable properties, and imparting new properties. The most common additives are oxidation and rust inhibitors, extreme pressure, antiwear, and friction-reducing agents. Friction modifier, such as molybdenum disulfide (Moly) or graphite is used in greases to reduce friction and wear without adverse chemical reactions to the metal surfaces during heavy loading and slow speeds in boundary lubrication conditions.
Greases are most often used instead of liquid lubricants when it is required to stay in place, particularly where frequent re-lubrication may not be feasible. As such, satisfactory performance of the grease requires the following functions:
• To provide reduced friction and wear on contact surfaces
• To act as a seal to prevent ingress of contaminants
Grease Composition: The lubricating greases are composed of three components: oil, thickener, and additives.
Base Oil: The base oil may be either mineral oil or synthetic fluid and it constitutes 70-95% by wt of the grease composition. Most grease produced today use mineral oil as their fluid components. In temperature extremes (low or high), a grease that utilizes a synthetic base oil will provide better stability.
Thickener: The thickener (3 -30% by wt) in combination with the selected lubricant, will produce the solid to semifluid structure. The primary type of thickener used in current grease is metallic soap. These soaps include lithium, aluminum, sodium, and calcium.
The complex thickener-type greases are used because of their high dropping points and excellent load-carrying abilities. Complex greases are made by combining the conventional metallic soap with a complexing agent.
Non-soap thickeners, such as Bentonite and silica aerogel are used for high-temperature applications, and they do not melt at high temperatures. The non-thickener may be able to withstand the high temperatures, but the used base oil oxidizes quickly
• Withstand a certain amount of contamination without suffering performance deterioration
• Resist leakage or throw-off from the surface to be lubricated
• Prevent rust and corrosion
• Resist structural deterioration during prolonged use
• Acts as carrier for solid lubricants
However, as greases are essentially “semi-solid” in nature, they will not provide the same degree of cooling or cleaning as provided by liquid lubricants. There are many different lubrication requirements and demands placed on greases such as operating temperatures – high or low or wide range, must function under various speeds – slow to extremely fast, varying amount of loads and should act as sealant to environmental contaminants.
Modern grease’s ability to meet these critical requirements generally depends on following key characteristics such as:
Consistency
Shear Stability
Oil Separation
The degree to which the grease resist deformation under the application of force
The ability of the grease to resist changes in consistency during mechanical working
The ability of the grease to release oil in controlled manner, ensuring proper lubrication