
5 minute read
ABOUT THE GREASE
Dr. E Sayanna Chief Technology Officer, Siddharth Grease & Lubes Pvt Ltd
Lubricating grease is a vital engineering component of any and every moving machinery. Grease accounts for around 4% of the total lubricants, and around 80% of bearings are grease-lubricated. Grease lubrication has clear advantages over oil lubrication because of its semisolid nature; it does not leak easily, has excellent sealing properties, and protects bearing surfaces from corrosion. An added advantage of the semisolid nature of grease is that solid lubricants like molybdenum disulfide, graphite, polytetrafluoroethylene, etc., can be uniformly dispersed in grease. Its disadvantages are recirculation and filterability constraints and limited cooling ability.
Advertisement
The American Society for Testing and Materials (ASTM) defines lubricating grease as “A solid to a semi-fluid product of the dispersion of a thickening agent in a liquid lubricant. Other ingredients imparting special properties may be included.” As the definition indicates, the lubricating grease is composed of three components: oil, thickener, and additives. The base oil, thickener, and additive package are the components in grease formulations and, as such, exert considerable influence on the behavior of the grease. Adding the proper grease to your maintenance routine guarantees that your facility is operating at peak performance.
COMPLEX GREASES ARE MADE BY COMBINING CONVENTIONAL METALLIC SOAP WITH A COMPLEXING AGENT. SINCE LAST YEAR, THE MOST WIDELY USED GREASES HAVE BEEN LITHIUM AND LITHIUM COMPLEX GREASE BASED. STILL, THE INDUSTRY IS FORCED TO LOOK FOR ALTERNATIVES DUE TO THE UNPRECEDENTED AND OUTRAGEOUS LITHIUM PRICE ESCALATIONS.
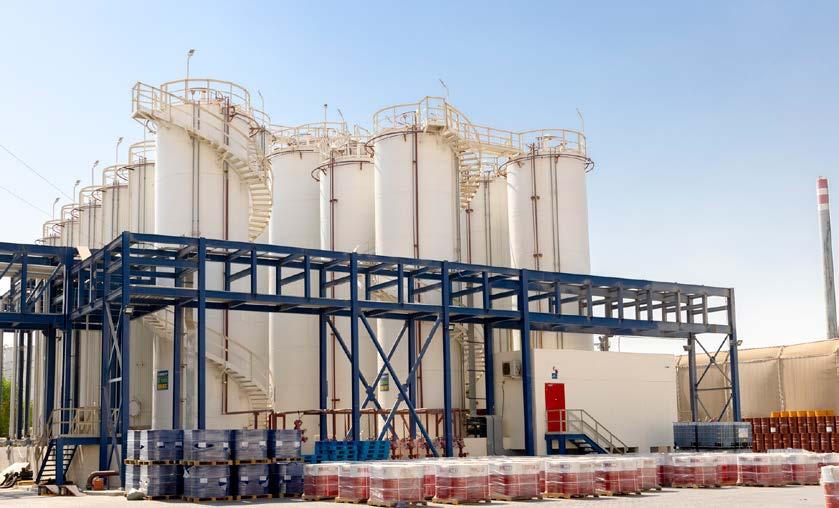
Over 90% of the thickeners used worldwide are soap-based, and thickeners are produced from an acid-base reaction. The primary thickener used in current grease is based on metallic soaps. These soaps include lithium, aluminum, clay, polyurea, sodium, calcium, and some mixed soaps. Complex thickener-type greases are high-performance products due to their improved thermo-mechanical properties. They are selected because of their high drop points and excellent loadcarrying abilities.
Complex greases are made by combining conventional metallic soap with a complexing agent. Since last year, the most widely used greases have been lithium and lithium complex grease based. Still, the industry is forced to look for alternatives due to the unprecedented and outrageous lithium price escalations. The lithium crisis is basically due to the diversion of lithium usage more and more towards batteries for electric vehicles, etc. This has prompted new and innovative approaches and alternatives to grease research worldwide. India supplies the major soap thickener component, fat/fatty acids, to all the global grease makers; it solely depends on lithium imports for grease manufacture. Due to the skyrocketing price of lithium, formulators have been forced to think outside the box and look at non-lithium greases, as well as other thickeners being introduced. There has been a significant shift from lithium greases to non-lithium greases to help Indian customers meet their grease requirements within the operational budget before the lithium price spike. The scope for export of these greases has increased due to the performance credentials of some of the cheaper nonlithium greases innovated in India.
Non-soap thickeners are also gaining popularity in special applications such as high-temperature environments and specialty applications. Bentonite and silica aerogel are thickeners that do not melt at high temperatures.
Chemistry plays a key role in grease technology, and physicochemical process parameters are essential. The grease structure is the most important characteristic determining its stability under mechanical shear and stress. The type of open or pressure reactor, agitation, heating/cooling rate, process time, mode of thickener dispersion into the matrix, additives doping sequence, etc., are the major process parameters for the grease structureproperty relationship. Given the above, grease-making is conventionally considered an art and a science akin to household cooking. The advent of advanced, sophisticated process equipment is gradually shifting from art to science.
The global grease industry has very cohesive networking in the form of annual conferences, technical events, education courses, working groups, round-robin testing protocols, etc. The National Lubricating Grease Institute (NLGI) of the USA has been providing outstanding service to the grease industry since 1933. Balmer Lawrie & Co is the pioneering company that introduced grease in India and produced many grease technologists who are instrumental in spreading grease technology in India. Dr. A.K. Bhatnagar, a visionary and former Director (R&D) of Indian Oil Corporation Ltd., with his foresight, took the initiative of starting a Chapter of NLGI USA in 1997 by pooling the major lubricant and grease manufacturers.
The NLGI India Chapter organized its first grease Conference in 1999 at Nainital, the famous hill station in the Himalayas. Subsequent events were organized in exotic locations of the multicultural and picturesque Indian subcontinent.
NLGI India Chapter has decided to celebrate its 25th Conference as a memorable mega event by organizing it in a Metro City venue for the first time. To commemorate and recapitulate the entire journey of the NLGI India Chapter in the last 25 years, a Coffee Table Book is being brought out, which can be treasured by all the delegates as a precious souvenir of the Chapter.
It’s now over 25 years since the idea of an NLGI-India Chapter was conceived by folks a lot smarter than me but I was there at the beginning and what seemed impossible at one point to achieve has not only been achieved but excelled at over the years. It feels just like yesterday since NLGI India started working closely with NLGI headquarters, but this unique Chapter has been an essential part of our parent organization’s journey and success.
I must acknowledge that having come to almost all of the meetings, the NLGI-India Chapter members have set an exemplary standard for all of us with their dedication and excellence on how to conduct meetings, always exceeding the highest standards they set for themselves.
I am full of pride and joy on what was created initially in order to serve the grease industry locally and has since ballooned into a Conference that is a must attend for all global leaders in the grease industry. I salute everyone involved in the NLGI-India Chapter’s success. This year is the 25th anniversary year, and I wish to extend my heartiest best wishes and congratulations to everyone at NLGI India on this auspicious occasion.
RAJ SHAH Director, Koehler Instrument Company, USA
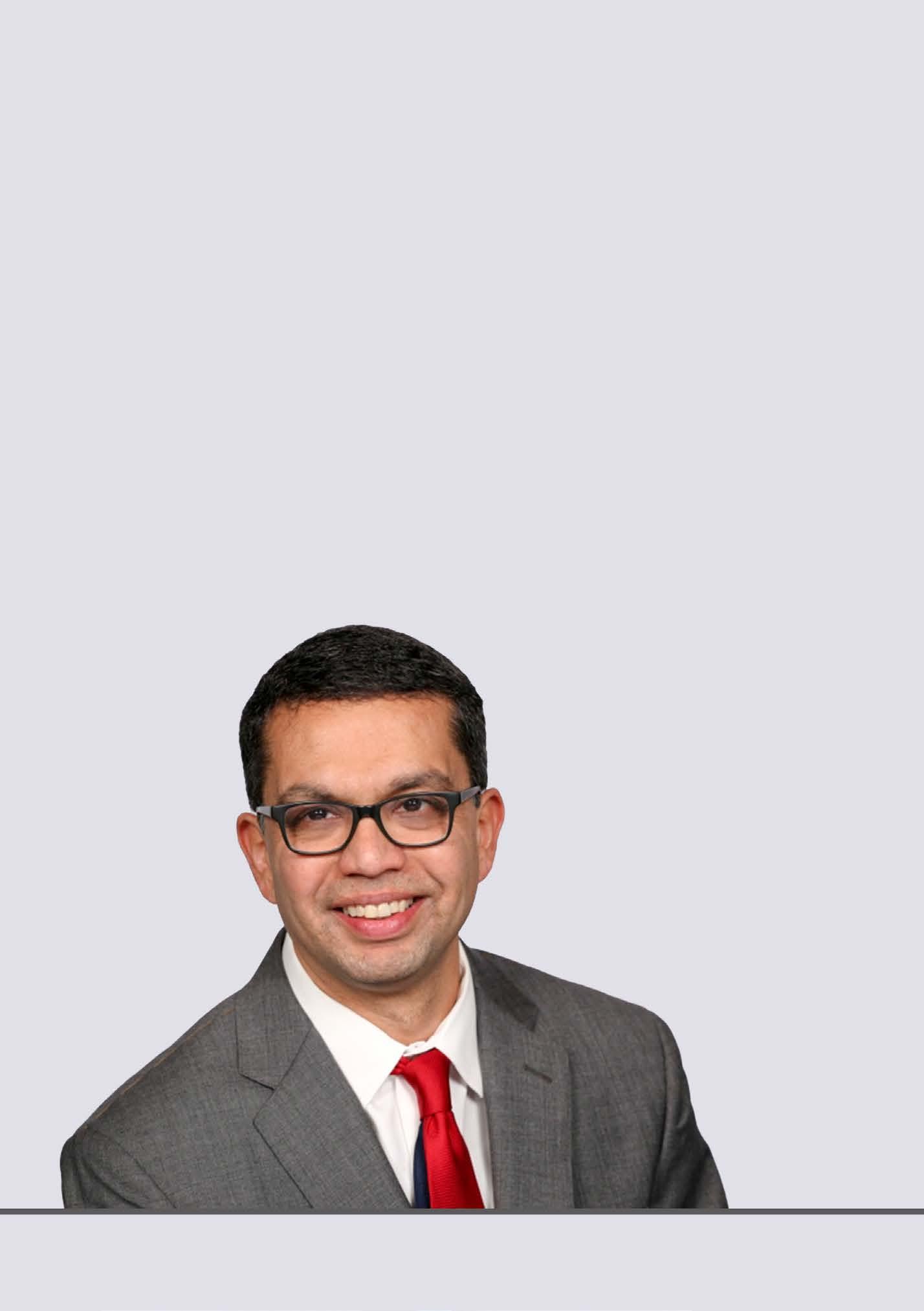
My First was the Second!
The Second lubricating grease conference was held in Goa, January 28-29, 2000, in which I had the privilege to participate for the first time, and since then in many more, very often by presenting technical papers.
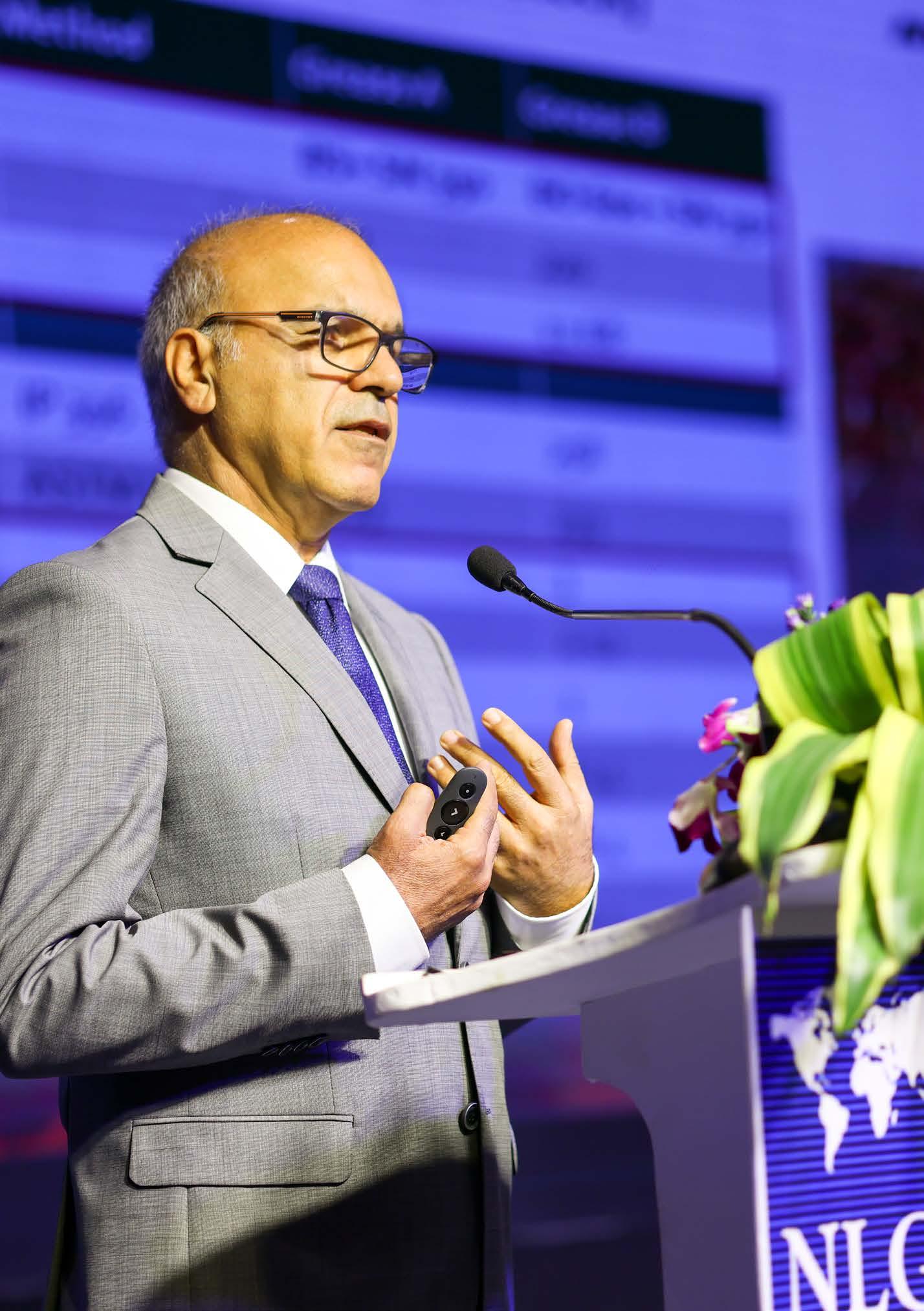
In my eyes, at year 2000, the NLGI-IC was a baby with some potential areas, but today it looks like a mature adult. We know that the success story, of the NLGIIC, is pure result of thousands of working hours by lots of dedicated fellows. Hence, my sincere gratitude to all these friends! This couldn’t be achieved if it wouldn’t be for your hard work.
On the personal level, thanks to all these events, I got the opportunities visiting numerous beautiful and historical places in India, learned from the presentations and discussions around, but ultimately its inevitable not being impressed by a tremendous hospitality and the rich culture that my Indian fellows introduced me to! Best wishes for the years ahead.
MEHDI FATHI-NAJAFI Nynas AB – Sweden