
13 minute read
Best By Design
from Encore March 2023
How Landscape Forms' products & workplace make it a top company
BY ZINTA AISTARS
Posing next to a lime-colored trash can in Central Park isn’t exactly the typical photo opportunity a tourist to New York City might choose. But for Marjorie K. Simmons, chief executive officer of Landscape Forms Inc., it was the perfect shot. With sunglasses pushed back atop her head and hair pulled back in a ponytail, Simmons held an arm out over the trash can as her travel companion snapped the photo.
“It’s probably a typical photo for any Landscape Forms employee,” Simmons laughs. “We love spotting one of our own products when traveling — we’re all proud of what we do here.”
Simmons has been with the company since 2014. She was initially a board member and took the position of CEO in 2019, when Landscape Forms celebrated its 50th anniversary. A graduate of Michigan State University and Eli Broad College of Business, Simmons studied marketing, labor relations and communications at Purdue University. She was a CPA at Ernst & Young, went on to become chief financial officer and director of business development for an architectural design firm, and in 1998 co-founded DSA Architects in Berkley, Michigan. When DSA was acquired by SHW Group, a national design firm headquartered in Dallas, Simmons was appointed its chief executive officer, in 2010. And when Stantec acquired SHW Group in 2014, Simmons became senior vice president and business leader. Five years later, Simmons took on the CEO role at Landscape Forms.
Simmons, 59, is only the fourth CEO of the privately held Kalamazoo company, which has 600-plus employees and satellite businesses in Arizona and Minnesota. Seeking ‘the perfect trash can’
Landscape Forms was launched in 1969 by John Chipman Sr. According to his son, the company began in a barn as a seed taking root in boredom.
“My earliest memories of my dad at work go back to being in the barn behind the house, where he was making prototypes of a planter,” wrote John Chipman Jr. in a 50-year remembrance of the company history. “He was running Chipman Landscape at the time, but, as he said, he was bored and looking for what’s next. There began what he jokingly called the 'quest for the perfect trash can.'”
Creating what turned into the company’s first fiberglass planter and soon after that creating a line of wooden benches, and ultimately trash cans for outdoor use, Chipman Sr. had landed on a way to keep his employees gainfully employed during the winter.
Fifty-four years later, the company has 638 full-time employees building not only planters, benches and trash cans but high-enddesign site furniture, structures, accessories, bike racks, lighting and custom outdoor settings. The company is headquartered on 58 acres at 7800 E. Michigan Ave., just outside of Kalamazoo, and includes in its family of brands Kornegay Design, in Phoenix, Arizona, and Loll Designs, in Duluth, Minnesota. The company has sales representatives throughout North America, South America, the United Kingdom, Australia, the United Arab Emirates and Asia.
With clean, sleek, simple lines and classic designs, Landscape Forms products are easily recognizable, with benches, tables or trash cans, visible on most every street of downtown Kalamazoo, not to mention in cities and towns across the country and the globe.
“We have an internal design team and consider ourselves modern craft manufacturers,” Simmons says. “But we also work with international designers for a modern take on traditional products. Design is in our DNA. Our three core pillars are design, culture, craft.”
In 2005, Landscape Forms established its specialized Studio 431 arm for high-profile custom projects, designing unique outdoor settings to fit the needs of individual businesses, institutions and venues. Designers are matched to projects, creating one-of-a-kind branded environments.
“Landscape Forms is not an assembly-line manufacturer,” Simmons says. “We are low-volume but high-variety. You can order one chair or 50, and we will make it. We’ve earned more than 70 awards since 2010 for our designs.”
Taking pride in people
With equal pride in products and people, Simmons points to a poster placed prominently in the Landscape Forms lobby that illustrates the many factors that comprise a successful business, many of which are based on treating employees with respect.
“We’re incredibly proud to receive recognition as Michigan Manufacturer of the Year in 2020, but also Great Place to Work certification three years in a row — 2020, 2021, 2022,” she says. “We also earned top rankings on Fortune’s Best Workplaces in Manufacturing & Production over those three years as well as Veteran-Friendly Employer awards.”
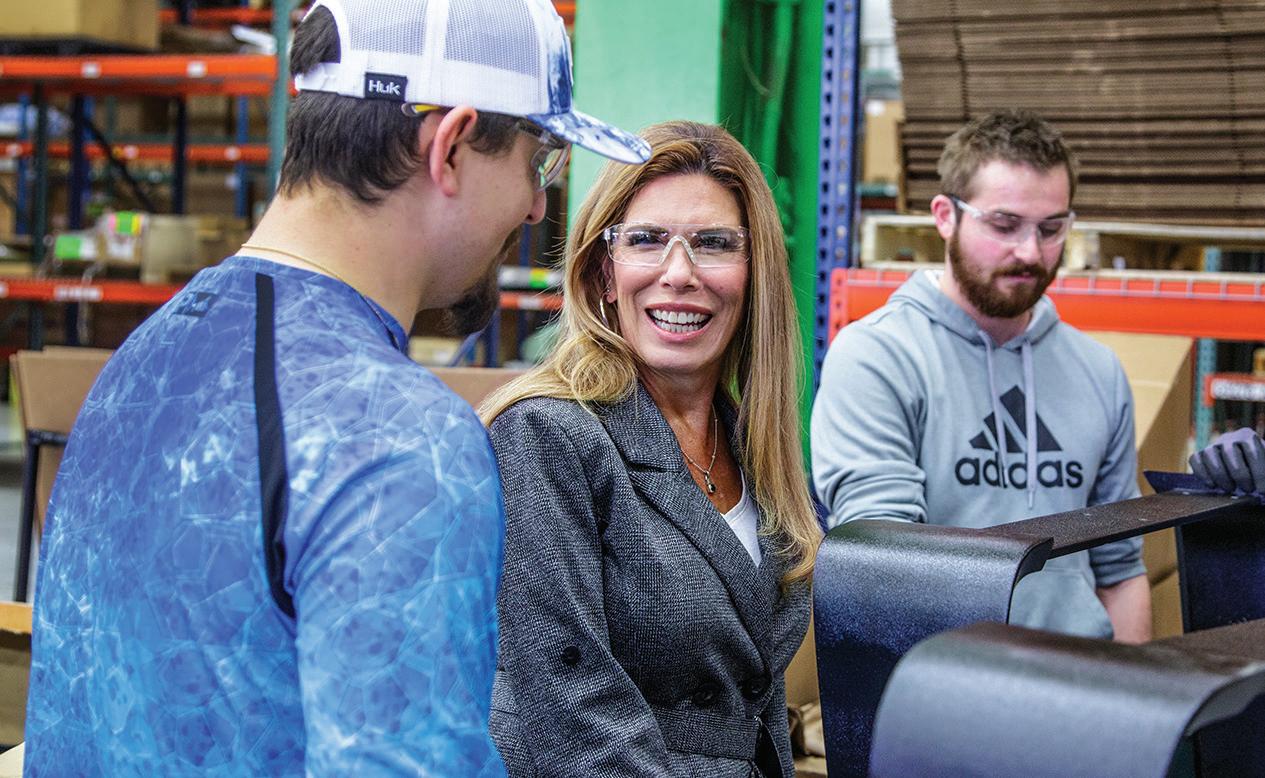
The poster highlights 215 new hires over the past year, increases in pay range for manufacturing positions, 72 special events to show appreciation for team members, and 35 internal promotions, among other bragging points.
“John Chipman Sr. didn’t only have innovative designs,” Simmons says. “He also believed that a successful company depended on how he treated people. Personal and professional development is part of who we were then and who we are today. But we also want our people to feel that we are having fun along the way with various events and family fests. We recently had a carnival with food trucks in our parking lot to include family that gathered about 900 people.”
In addition, individual team leaders come up with their own outings for their teams, including golf outings, axe throwing, pontoon boat rides — whatever comes to mind and builds camaraderie in and outside of the workplace.
“We encourage that, because when we have fun together, people create connections,” Simmons says. “Especially after the two years of the pandemic, when many of our people worked from home, we needed to connect again. Especially new hires needed that.”
Along with an element of fun, the company offers career development training programs, leadership programs and continued education, and it recently expanded parental leave for both parents.
“We’ve had 25 babies supported by our new parental leave program,” Simmons says. New parents, whether by birth or adoption, are eligible for up to 12 weeks’ leave, depending on the number of their years of employment with the company."
The company even provides pet insurance for those who feel their pets are their “fur babies.”
“Providing parental leave meant a lot to our employees,” Simmons says. “We found that too many women especially had to leave their jobs to take care of their kids, so it was important to work around that. We have also brought in flex time and hybrid work hours for those who are able to do their jobs at home but come into the office at other times. It’s one of the few positive outcomes of the pandemic. We learned that our employees are as productive working at home as at the office.”
Embracing the needs and perspectives of employees has become as important an aspect of how Landscape Forms is run as of how its products are designed and built. There’s an acronym for it: EPIC.
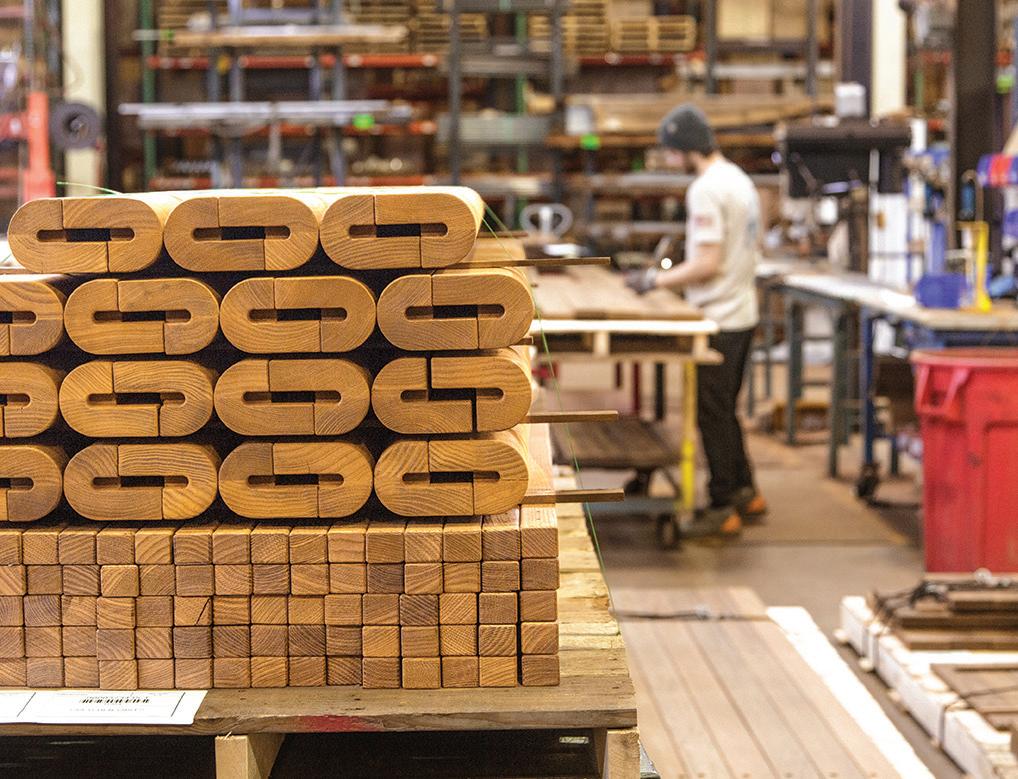
“EPIC stands for equity, participation, identity and competency,” Simmons explains. “Across the board, every decision we make here goes through that lens, with buy-in from everyone at Landscape Forms. From how and what we produce down to our fun events, everyone participates in the decision-making.”
Sharing the profits
Employees not only participate in decision-making but also reap the benefits. A Quest Bonus disburses a percentage of corporate profits on a quarterly basis to participating team members.
“That started with our founder,” Simmons says. “Everyone who generates a successful project has a share in that reward. It ties everyone together with a common purpose.”
Chipman Sr.'s desire to build a sense of shared success in his company has expanded over the years to bring the people who make up the company closer to the forefront.
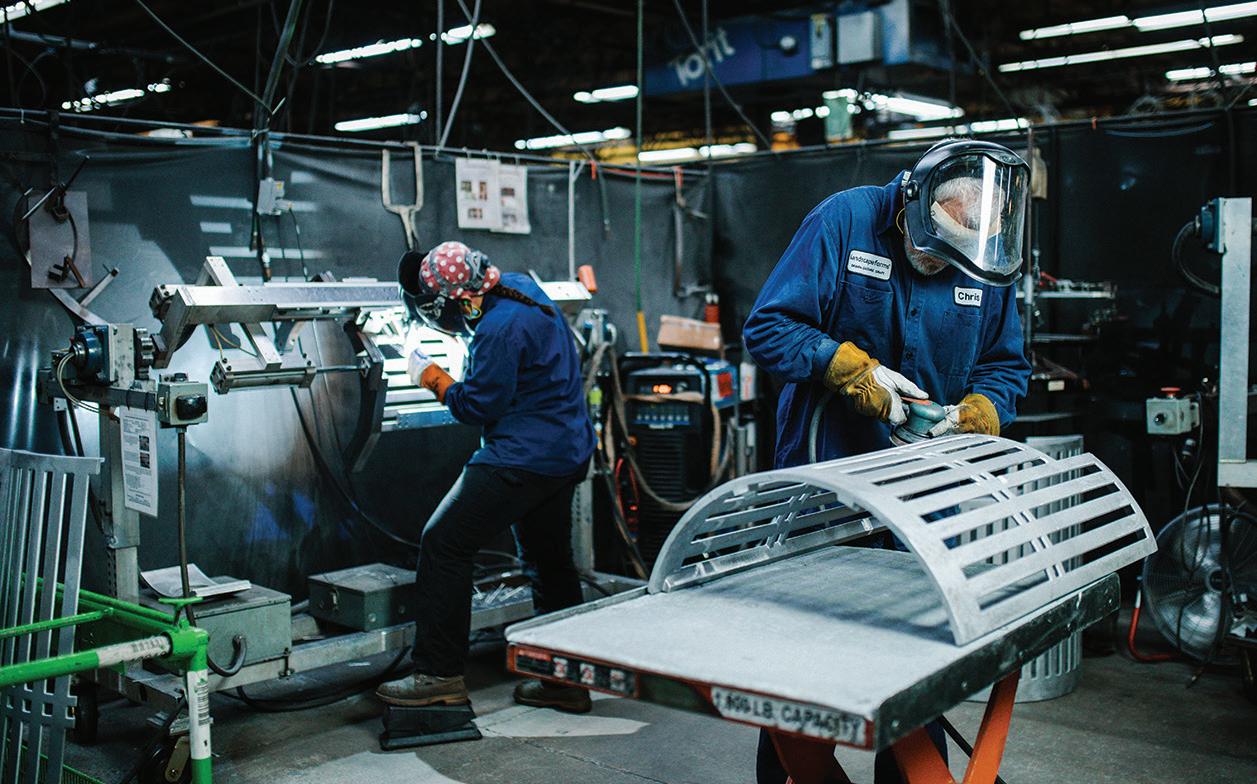
“When he retired, he wanted active management to have ownership of the company,” Simmons says. “Managers, directors — almost 50 people who work here — are now part-owners of Landscape Forms. None of the Chipman family are owners any longer, although John Chipman Jr. does sit on our board. It’s very motivating to have that ownership in what we do. Our board of directors too consists mostly of external members to avoid conflict of interest. That’s unique for a privately owned company. We get the expertise of our board members without their day-to-day involvement in our activities.”
Another point of pride for Simmons has been bringing women into leadership positions and onto the company's board of directors. Landscape Forms has joined hands with WxLa, an advocacy initiative created in 2018 to encourage and lead efforts toward equality in the profession, championing women leaders in landscape architecture.
“There’s me as CEO,” Simmons says with a smile, “and our CFO is a woman. Quite a few of our directors and other key positions have been filled by women. But it is more than just about women. Landscape Forms has been working hard on our DEI program — diversity, equity, and inclusion — with the goal of achieving a vision of a just and diverse community in our industry.”
In 2021, Landscape Forms established its Diversity, Equity, and Inclusion Scholarship. The scholarship is open to undergraduate landscape architecture students who are Black, Indigenous, or People of Color (BIPOC) and currently enrolled in an accredited landscape architecture program in the U.S. or Canada. Candidates must demonstrate financial need, academic aptitude and commitment to the discipline of landscape architecture.
Landscape Forms also partners with the Landscape Architecture Foundation to offer annual scholarships for distinguished undergraduate landscape architecture students.
Caring for the planet
It would seem a natural outgrowth of creating outdoor landscapes that Landscape Forms would also have a strong concern about sustainability and the environmental impact of producing its products.
“And that’s true,” Simmons says. “A passion for environmentalism has been a part of this company from its foundation. Since 2008, we have partnered with 1% for the Planet, a global organization that works with businesses and individuals to support environmental nonprofits. They connect companies like ours with other nonprofits to help create a more sustainable world."
The company takes a hard look at its carbon imprint, with consideration of energy use, pollution reduction, resource conservation, recycling, transportation and waste elimination. Metrics are maintained for energy, water, carbon and material usage, with the goal of constant improvement. Steel and aluminum are imported mostly from mills and plants within a 150-mile radius.

Of 200 products Landscape Forms makes, 85 percent are produced from post-consumer or post-industrial recycled materials. All lighting within the company's buildings has been converted to more-efficient LED. And nearly 600 tons of waste produced during manufacturing processes in 2020 was recycled.

Training apprentices
As a crucial part of being a responsible member of the community, Landscape Forms maintains extensive community outreach, especially in the realm of education.
“Education has a profound impact on our lives,” says Simmons. “We bring students here as interns, as apprentices, working with schools such as Western Michigan University and Comstock schools to identify and develop emerging leaders. We also work with the community colleges, Michigan Career & Technical Institute, Allegan County Area Technical and Education Center, and many others.”
As Tony Ide, manufacturing group leader and coordinator, leads the way into the production area of Landscape Forms for a closer look at where the magic happens, he tells of his personal gratitude for the company's approach to developing future leaders.
“I came here from out of the military eight years ago,” he says. “I learned welding at Landscape Forms — something that was completely new to me. We have had the Welding Academy here since 2011, and we have some of the best welders in all Southwest Michigan come out of here. We train people on the job with paid apprenticeships, and most of them we retain while others in the industry try to take them away.”
Ide grins, waves at one of the welders, and continues: “Our team goes out to schools to talk to students about our program. We go to Kalamazoo, Van Buren, Constantine, Allegan, and we talk to young people about the opportunities here. We offer 10- and 14week certification. It’s an opportunity to get into the trades with work-based learning, up to 20 hours per week. Most of them stay after they complete the program.”
Landscape Forms also works with engineering students at WMU to sponsor projects, pairing engineers with engineering students and faculty members. As students learn by doing, guided by professionals through real-world challenges, many remain in the pipeline and take advantage of employment opportunities at Landscape Forms.
“With our fast growth, we are always hiring,” Ide says. “We take note of the students working here who are highly engaged and select them for training into leadership positions. I was a material coordinator for a couple of years before I was brought onto the metals team, a year later to manufacturing process leader, and a year after that to the position I am in now. Hard work gets rewarded.”
Keeping ‘an aggressive pace’
Ide strolls the floor, greeting and checking in on workers as shifts change; one shift ends at 4:30 p.m. and the floor goes silent for a while, but new teams arrive at 7 p.m.
“It’s important to stay on top of the market,” he says. “That’s the 800-pound gorilla. We produce nine to 13 new products a year, and that’s an aggressive pace in the industry. We keep adding to our portfolio.”
Ide stops to examine a weld in a large planter. To the uneducated eye, it appears to be sufficient, but Ide shakes his head. This one won’t make it out the door, he says. Every weld must be smooth and even and perfect.
Perfection and innovation are everyday goals on the floor and in the office.
“Our goal is to double the size of the company every six years,” Simmons says.
Part of that ambitious growth, Simmons says, is through acquisitions, but those are made as carefully as any other part of the business is conducted, if not more so — as perfect as a solid weld.
“It’s a robust and intentional process,” she says. “For an acquisition, they must fit us. It is the first of five points we consider. The fit of their vision — do they believe in craftsmanship? Their size, because resources are limited, and we don’t want to bet the farm. We look at strategic fit — what can we do with this acquisition (and) how will it benefit us? We look at cultural fit — how well we are aligned? And, finally, we look at the finances — will this make us profitable in the long run?”
Another acquisition is expected this year, Simmons says.
“Success breeds complacency,” she says, “and you don’t want to get lazy about what you are doing here. It’s grow or die or someone else is going to eat your lunch. If you work at Landscape Forms, change better be OK with you. Continuous improvement is in our DNA.”