
12 minute read
Özen İplik sews success
by istmag
Özen produces sewing threads, which are designed according to the technical requirements of companies at home and abroad and are approved with quality certificates and standards.
Founded in 1972, ÖZEN İPLİK, an İstanbul-based company has become a leading firm in the industrial sewing yarn at home and abroad.
Advertisement
The company produces sewing yarns at international standards for different sectors, mainly technical textile, furniture, home textile, leather goods, automotive, and denim thanks to its investments in the recent years. We asked the details of their
success story to Engin Kalkan, a company partner at Özen İplik. Full text of the exclusive interview follows:
Could you give us some information about your products and current product groups? Our company produces synthetic (polyester and nylon) and cotton sewing threads, as well as many products such as bonded, elastic, antistatic, waterproof, water repellent, non-flammable (aramid), knitted (oil-freesemi-wax-waxed) according to sectoral needs. In addition to sewing threads, we started to produce solvent-based adhesives for our customers in the furniture and bedding industry developing Vera chemicals in January 1, 2020.
What are the main features of your products?
We produce the sewing threads which are designed according to the technical requirement of companies in Turkey and in the world and it is approved with quality certificates and standards. Regarding this purpose, we continue to develop VERA adhesives that we started to produce.
Why should the companies who are producing mattresses and serving in the sleep products industry prefer Özen İplik products? Can you tell us about your sales and after sales services? We provide the requirements of our customers with the fast production possibility and the special production planning regarding minimum price and maximum quality and shipping the orders by being produced and shipped as block. With our technical support team, we aim to benefit the technical and quality infrastructure of the industry in R&D and P&D studies both for ourself and our customers.
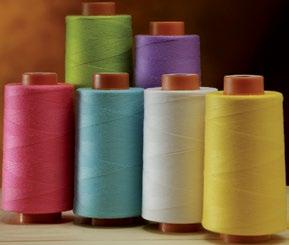
Could you tell us about your export map and the locations in your export target? We continue our exports to approximately 68 countries with the centers of our company in the United States of America, Russia and Europe.
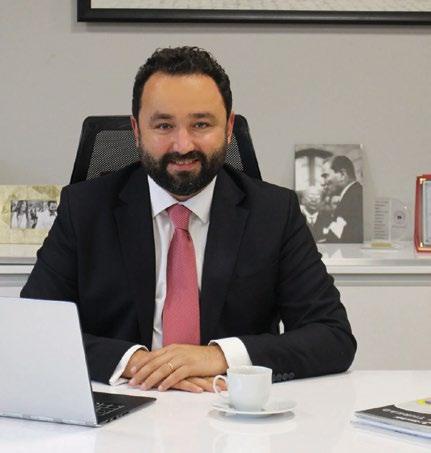
Engin Kalkan, a company partner at Özen İplik
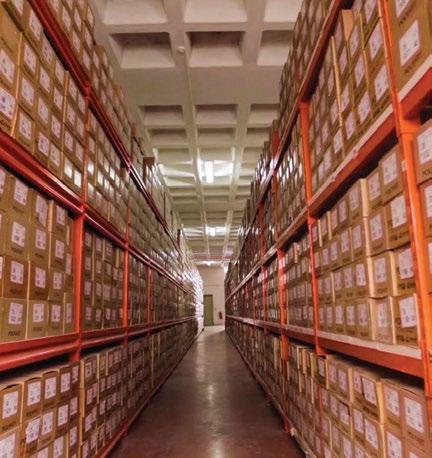
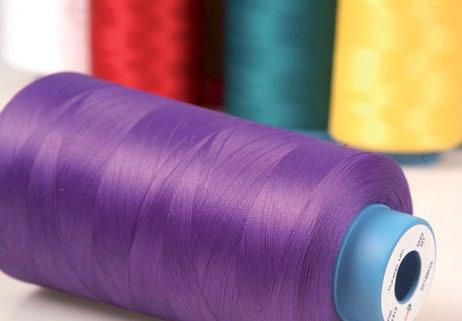
How did your domestic and international sales activities follow in 2020? Which product was more preferred in 2020? As well you know, the first quarter of this year was an unstable period due to the epidemic. All domestic and international fairs and customer visits were canceled. During this period, we never break contact with our customers and analyzed all their troubles and needs correctly. During this period, our company nonstop continued the production by taking all precautions. Although the movement in the market decreased in April and May, we achieved our production and sales targets in September. Additionally, due to the raw material and product
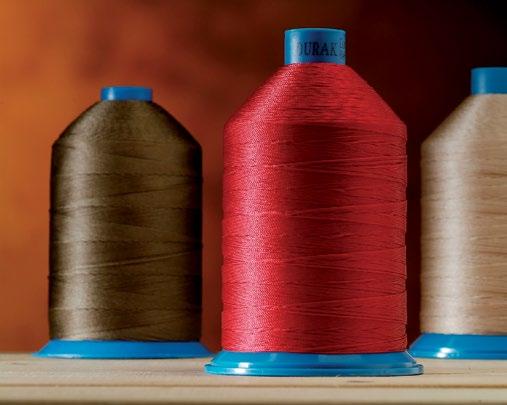
supply problems that occurred in the market during the pandemic process, our company continued to serve without interrupting any product supply with its strong structure. On the other hand, our products such as waterproof, antistatic and bonded sewing threads were in highly demanded which are produced during the pandemic process.
Are you planning fair attendance for 2021? Which fairs are you planning to attend in 2021? We currently plan to attend for the Texprocess and Interzum fairs in Germany in May and Intermob in Istanbul in October 2021. We will revise our plans according to the development of the process. Can you tell us about your domestic and international references where your products are used in the mattress and furniture sector? We are the approved supplier of many national and international brands that produce both domestically and abroad.
Do you have new investment and branding projects, can you give some information about them? In order to increase our sewing thread production capacity, the management decided to invest in additional buildings and machinery and the contracts were signed in September 2020 .In addition, we are continuing to set up facilities for HOTMELT, AEROSOL and water-based adhesives to further increase the sales of VERA brand solvent-based adhesives, which we started to produce at the beginning of 2020.In addition to our sewing thread products, we are trying to serve our customers with this group.
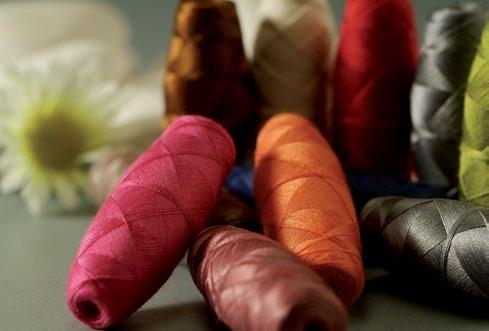
In the Covid-19 epidemic, which affected the whole world, economic activities were also changed along with social life. How has your sales operations changed during this period? How have your export markets and rates been affected? With Covid-19, our production and sales order had to be changed. Our company took very fast action and gave the necessary trainings to all personnel in the company without any delay and put all the measures into action. When we look globally, many sectors suffered from sales and finance problems and many sectors had an increase in production at the same time. Our company has analyzed this process in the market for 7 months and took the necessary measures. We hope that this process will end as soon as possible in our country and in the world and we can enter the normalization process.
Comfytex: “Increasing bed change trend due to Covid-19 caused an increase in our export demands”
Gözde Seven, Comfytex Research Development Chief, comments on their sales operations and export activities after Covid-19.
“As people stay at home for a longer time, the trend of renewing old items has become popular all over the world. While the interval to renewing the beds of people before the corona was 5-6 years, this has completely changed with the thought of the virus being settled. On the mattress fabric side of the bed sector, we are trying to manage our sales and density by directing our domestic and foreign market customers to make long-term plans. As a result of these increasing of our sales, our exporting statics showed us 80-90% range has led to growth and our shipment quantities have also increased. On the other hand, we and our customers are aware that everything planned can change day by day.

Because even if the business plans and management are done in the most correct way, the uncertainty of who will be quarantined or who will be infected the next day has become the reality of our lives, both for us and the shipping companies we work with. As a result, we are now struggling to manage our increasing sales in the best way, admitting the fact that everything planned can change at once. On the other hand, we constantly warn our customers to plan long-term purchases and to be prepared for disruptions that may occur.”
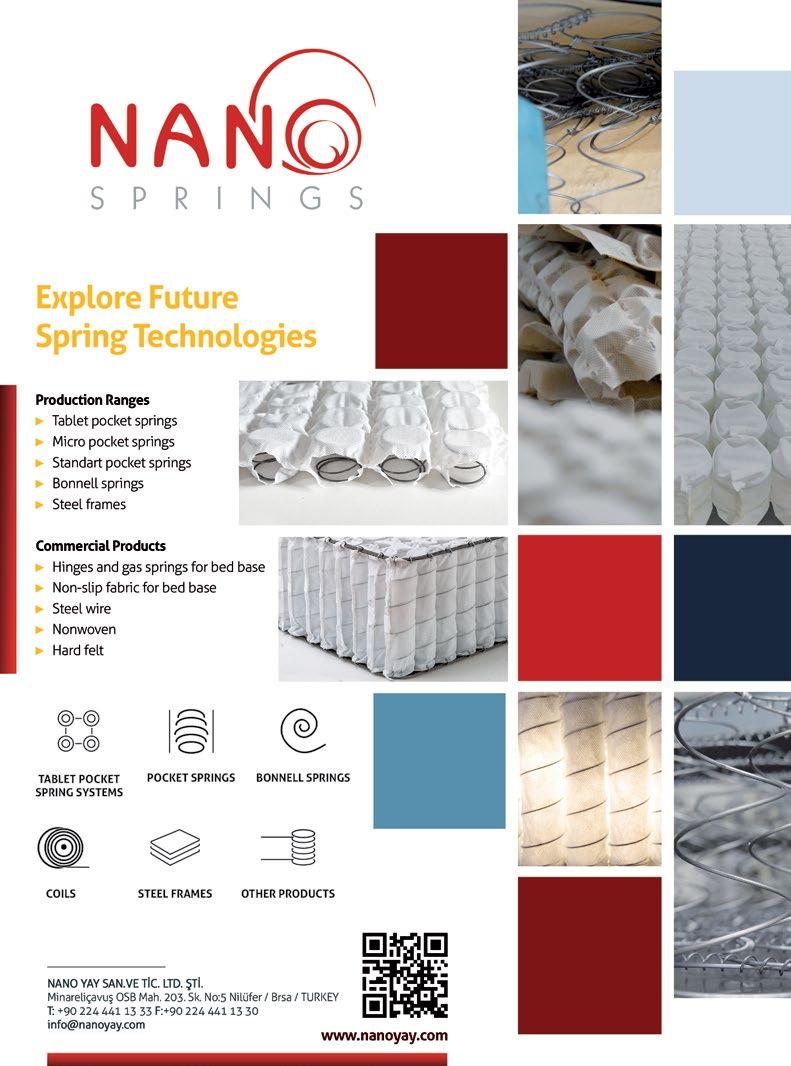
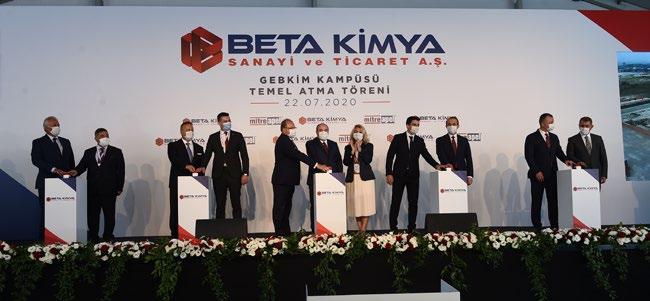
BETA Kimya adds value to the chemistry industry with its new production facility investment
BETA Kimya GEBKİM Campus, which is prepared to become the production base of high-tech new generation adhesives to be produced locally and nationally for the first time in the Turkish chemical industry with an investment value of 315 million TL, will provide employment for 500 people by operating with an annual production capacity of 150 thousand tons.
BETA Chemical Co. one of Turkey’s oldest chemical companies, laid the foundation of the largest adhesive and glue production facilities in Eastern Europe and the Middle East. The groundbreaking ceremony of BETA Kimya GEBKİM Campus was realized with the participation of T.C. Industry and Technology Minister Mustafa Varank, T.C. Trade Minister Ruhsar Pekcan, TIM President İsmail Gülle, BETA Kimya A.Ş. Chairman of the Board Adil Pelister and BETA Kimya A.Ş. General Manager Cihat Sayacı. BETA Kimya GEBKİM Campus, which is the new integrated production facility of BETA Kimya A.Ş., and fully compatible with digital transformation in the industry, and green building technology with LEED certification, will offer one hundred percent local and national innovative products for use in many strategic sectors such as automotive, defense and aviation.
Varank: “A new breath to the chemical industry” Minister of Industry and Technology Mustafa Varank, in the speech at the groundbreaking ceremony of the Beta Kimya GEBKİM Campus in Gebze Chemistry Specialized Organized Industrial Zone (GEBKİM), said

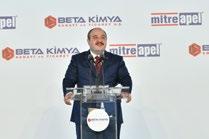
that they witnessed an exciting day for the real sector which continues its path without stopping even during the epidemic of the new type of corona virus (Covid-19). Stating that they are together to lay the foundations of the largest adhesive and glue production facility in the Middle East and Eastern Europe, Varank said “Beta Kimya GEBKİM Campus, which will come to life with an investment of 315 million liras, will make new employment opportunities for 500 citizens. From the first day of our visit to the Ministry with the appreciation of our President, we have demonstrated the vision of national technology and strong industry. We are concerned with developing new policies that will take this vision further with every step we take. We try to dominate the real sector in an approach that encourages localization and directs our companies to innovation. With BETA Kimya Inc.’s new integrated facility investment, the polyurethane reactive hot-melt adhesive products and different variants, so far imported, will begin to be produced in Turkey for the first time. Thus, an important input of the packaging, automotive, furniture, construction, defense and aviation industries will be procured domestically. In the medium term, an import of 120 million dollars will be prevented. After domestic needs are met, of course, the export potential will also be evaluated. When this factory goes into mass production, it will be one of the most modern production facilities in our country. I wish the BETA Kimya GEBKİM Campus investment, which will bring a new breath to our country’s industry and the chemical industry, and I congratulate everyone who contributed especially the BETA Chemistry Board and İKMİB President Adil Pelister.”
Pekcan: “Chemistry is the locomotive sector for Turkey” T.C. Trade Minister Ruhsar Pekcan, in her speech at the Beta Kimya GEBKİM Campus Groundbreaking Ceremony, by attending with video conferencing, said that she is pleased to be at the groundbreaking ceremony of an investment of strategic importance for the country. Minister Pekcan said “BETA Kimya Inc.’s investment in the new integrated production facility is really very important for Turkey.
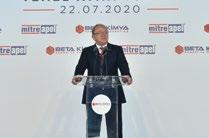
Because it coincides with our country’s high technology and high value added production and export strategy. Under the leadership of our President, we will take all necessary steps to bring our country to the level of high-income countries together with its political stability and effective management system, more technology, more value-added production and exports. BETA Chemistry GEBKİM Campus will make added value of Turkey’s production deficit and imported products and also will provide making exports to new markets. In our country, it will provide domestic input to many sectors such as automotive, construction and defense industry, and make employment for 500 people. I congratulate the BETA Kimya Family for their valuable investments and wish them good luck for our country.”
Pelister: “It is a product of our vision to make high added value” Stating that they will bring a new value to the chemical industry and Turkish industry with BETA Kimya Gebkim Campus, Adil Pelister, the chairman of the Board BETA Kimya Inc., said “As BETA Kimya, we have focused on growing, produc-
ing and always creating high added value for 34 years. With our Apel and Mitreapel brands, we have managed to become a large industry family that exports to 75 countries on 5 continents, with approximately 150 products in 9 different categories, from furniture to automotive, textile to construction and even to health with its COVID-19 pandemic. Today, BETA Kimya Gebkim Campus, which we have laid the foundation, is a product of our excitement to make high added value. Our new integrated facility, which will be commissioned with an investment value of 315 million TL with 100 % domestic and equity capital, will be the largest adhesive and glue production facility in the Middle East and Eastern Europe.”
Pelister: “We will take a step in 5 new products categories” Expressing that they will focus on domestic and innovative products for Turkey’s strategic sectors with BETA Kimya GEBKİM Campus, Adil Pelister said “With our new integrated facility that will have an annual production capacity of 150 thousand tons, we will employ 500 people and we will step into 5 new product categories with high added value. Our LEED-certified, eco-friendly green building production campus will be one of the most modern chemical facilities not only in our country but also in the nearby geography, as a giant integrated production facility built on a total of 50 thousand m2, with a closed area of 35 thousand m2. We take pride in signing one of the best examples of digital transformation in industry that our state and ministries expect from us, a step that will add value to our country and the chemical industry. With our new production facility, which
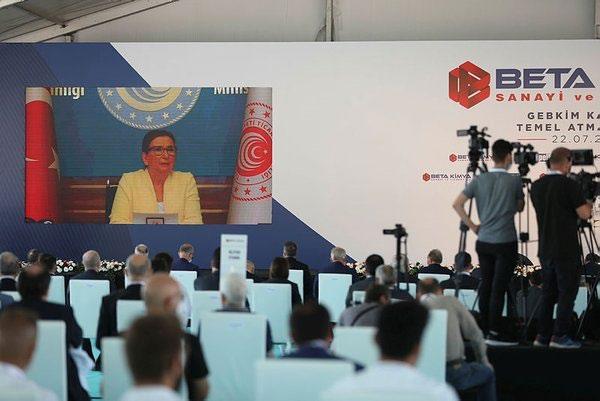
will be operational in the next year, we will be ready for the future digital production technologies. I wish it good for our chemical industry, country industry and our company.”
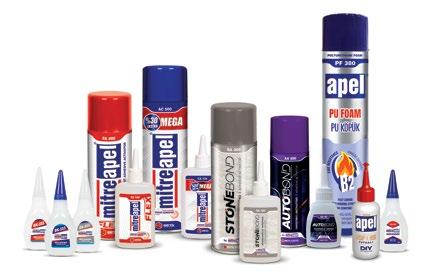
Sayacı: “We will produce new generation pur hotmelt adhesives for the first time” Stating that they are among Turkey’s 250 companies that invest most in R & D and always focus on innovative products, Cihat Sayacı, General Manager of BETA Kimya Inc. said “With our BETA Kimya GEBKİM Campus, we are signing a modern integrated production facility project that is of great importance for the Turkish chemical industry and fully complies with the principles of digital transformation. As BETA Kimya, we have gained power from R&D and innovation for 34 years and we are committed to developing high-tech products. We are also signing an important investment move for R&D in our new integrated facility. We are preparing to grow our innovation base, which has an R&D Center Certificate and consists of all Turkish engineers, exactly 7 times here. With a R&D team of 50 people, we will step into new MS technology adhesives terminated with silane and PUR Hot-melt products that we will produce for the first time completely locally. We will carry BETA Kimya to the future with new generation innovative products that we will develop specifically for the automotive, packaging, building and furniture sectors as well as nationally strategically important sectors such as defense and avia- tion.”

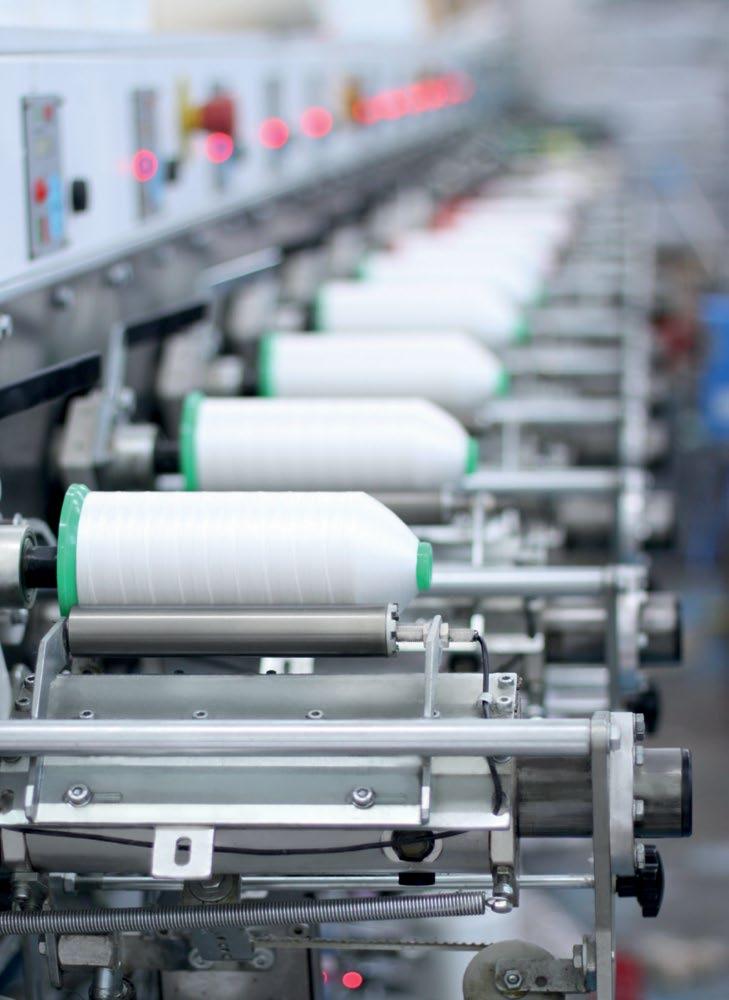