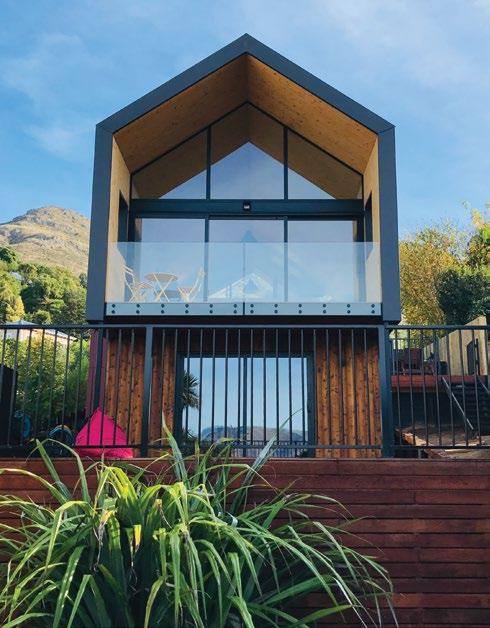
6 minute read
Make way for change
The days when sustainable house design was just a cosy, nice-to-have will soon be behind us. The government has flagged significant upcoming changes in its Building for climate change programme and other workstreams. It’s time for industry to start limbering up for the challenge to come.
The benefits of good sustainable design have been understood since the 1970s, but they are still far from standard in many houses in Aotearoa New Zealand. You don’t need to look hard to find new homes where the carbon footprint is enormous, the north-facing garage steals the winter sun, the large south-facing glazing makes for chilly nights, and the power bills are eyewatering.
The government says that the newly increased insulation requirements to comply with Building Code clause H1 Energy efficiency aim to reduce the energy needed to heat new homes by up to 40% compared with the previous requirements.
What’s coming?
What is on the horizon is much more substantial, including:
▶ new requirements to measure and put a cap on the whole-of-life embodied carbon emissions of new buildings
▶ an aim by MBIE to reduce building-related emissions by 0.9–1.65Mt CO₂-e (million tonnes of carbon dioxide equivalent) over 2022–25
In Brief
▷ New Zealand's Building for Climate Change program aims to reduce building-related emissions and improve thermal performance.
▷ Mid-size companies may face challenges in pursuing sustainable design without sufficient resources or shareholder pressure.
▷ Financial support is available for sustainable building initiatives, such as green loans and subsidies for meeting sustainability standards.
▶ new requirements that will improve the thermal performance of walls and window installation
▶ potentially, new requirements to prevent buildings from overheating.
The H1/AS1 schedule method of determining insulation needs will likely be withdrawn, and modelling will be required for either embodied carbon or energy use or potentially both.
Where do we stand today?
A lot of the progress on sustainability seems to be found among the largest and smallest companies. ‘The larger you are, the more you have a target on your back,’ Jeff Vickers of sustainability consultants thinkstep-anz told Build. He points to large players with overseas owners where some of the initiatives around sustainability are being driven by decisions made in overseas head offices. ‘The reality is that, if you are a large publicly listed company, then you have to act,’ he says.
‘At the same time, we are seeing a lot of great work among small companies, often still run by the founder who either has a personal ethos or passion for sustainability or who is developing environmentally friendly products.
‘It is often the mid-size companies that fall through the cracks – they don’t have the resources or the shareholder pressures to change the way they operate.’
Andrew Eagles of the New Zealand Green Building Council (NZGBC) says that ‘many people struggle to understand the scale of what we have to achieve’. He points to BRANZ/Massey University research that found newly constructed houses were responsible for five times more emissions than they should be if our houses are on track to reach a netzero goal by 2050.
Should the changes be led by clients or industry?
There is no doubt that some clients request sustainable buildings. BRANZ is hearing from around the country that a growing number of clients, including families looking to build a new house, are bringing up the topic of carbon footprints with their designer. But their limited technical knowledge means that the industry can’t sit back and let clients be the primary drivers for sustainability. ‘Encourage clients to use thermally broken window frames if you can,’ says Andrew Eagles. ‘Encourage heat pump water heating, efficient taps, LED lights.’
The government is already moving the industry with its own actions, notably with Kāinga Ora committing to all its new homes being built to at least 6 Homestar standard (with 10 being the highest).
The cost challenge
At the large-scale end of the industry, there are cases where a more sustainable way of doing something is possible but just not financially viable. Jeff Vickers points to this being one of the big challenges for basic materials such as concrete or steel.
‘The big challenge is not that companies lack the will to act or lack the capital to make the investment required – it is just that the operational costs of a more sustainable manufacturing process are so much higher that you can’t make a business case for them.’
He uses the example of moving away from traditional ways of smelting steel to using hydrogen as a reductant, producing emissions of water rather than carbon dioxide. It has been shown to be technically feasible but hugely expensive. ‘If a company takes this path, but its competitors keep to the traditional approach, they’ll be stuffed by the competition because they have far higher operating costs.’
These sorts of moves are only likely to be made when enormous incentives make them financially feasible. Jeff Vickers says, that if a government opted to ‘crash the price of green electricity’, it would provide an incentive to produce hydrogen using electricity and elsewhere to shift processes currently using natural gas over to electricity.
Funding support available
At the lower level, there are a surprising number of potential sources of financial help for the industry and their clients. The ANZ Business Green Loan is one example, with a discounted interest rate for green buildings, sustainable land use and the like that is 150 basis points below the standard floating rate.
Other banks also have or have had offerings in this area. Kiwibank offers support for sustainability on a case-by-case basis, with lending rate discounts of around 50–100 basis points for commercial green buildings, residential buildings with at least an 8 Homestar standard and so on.
ASB had a Back My Build product that gave customers a $3,000 cash rebate if the house they built was 6 Homestar rated or higher – effectively subsidising the margin that building to this level costs.
Territorial authorities are also offering support. Wellington City Council has an Environmental and Performance Accessibility Fund that can support eligible projects for up to $500,000 (commercial developments) and up to $2 million (residential developments). In the residential category, for example, $15,000 per unit (self-contained residence) is available up to a maximum of $1 million for homes that reach a 7 Homestar rating.
Take to the tools
The government has clearly flagged that major changes are on the near horizon in the form of its Building for climate change programme. Computer modelling for things like energy use and carbon footprint will eventually be the norm for new buildings, including houses.
While much of the detail still must be worked out, there are already a host of tools that people can experiment with to see what it’s all about.
BRANZ has a cluster, including LCAQuick, which calculates the environmental impacts of any building designs, with a focus on homes and offices.
NZGBC has the Homestar Embodied Carbon Calculator tool – freely accessible on its website – which helps calculate the estimated carbon footprint of a dwelling.
Planning for a fast-moving future
‘One of the really important things for us is helping people prepare for the implementation of Building for climate change,’ Andrew Eagles says. ‘Change is going to happen at a faster rate in the future. We are keen to help people get up to speed now, building the skills and knowledge they will need before they have to use it. Our sector can be an agent for change, inspiring and helping people.
‘That should mean that, instead of alarm and the industry lobbying for delays in implementation, people can say “Yep, I know how to do that. I’ve got that”.’
by David Hindley Freelance Technical Writer
This article was first published in BRANZ Build magazine issue 193, December 2022 www.buildmagazine.co.nz
6 Steps Towards Sustainability
1. Use passive solar design to reduce the heating/cooling energy that building occupants would otherwise need to buy to stay warm or cool.
2. Think in terms of whole of life. For example, some materials may have slightly lower embodied carbon than others but need to be replaced two or three times over the life of a building. Another option with slightly higher embodied carbon at the start that doesn’t need replacing may be a better choice in the long run.
3. Ask your suppliers about more-sustainable products. For example, talk to your concrete supplier about providing concrete with supplementary cementitious materials, which can reduce the embodied carbon in concrete by 20% or more.
4. Minimise the building site waste that goes to landfill. Separate waste and recycle as much as possible.
5. Don’t buy or specify appliances that run on fossil fuels.
6. Use the tools and resources that are freely available to help you. BRANZ has the Level website and the carbon tools and calculators on the main BRANZ website. NZGBC also has good resources.