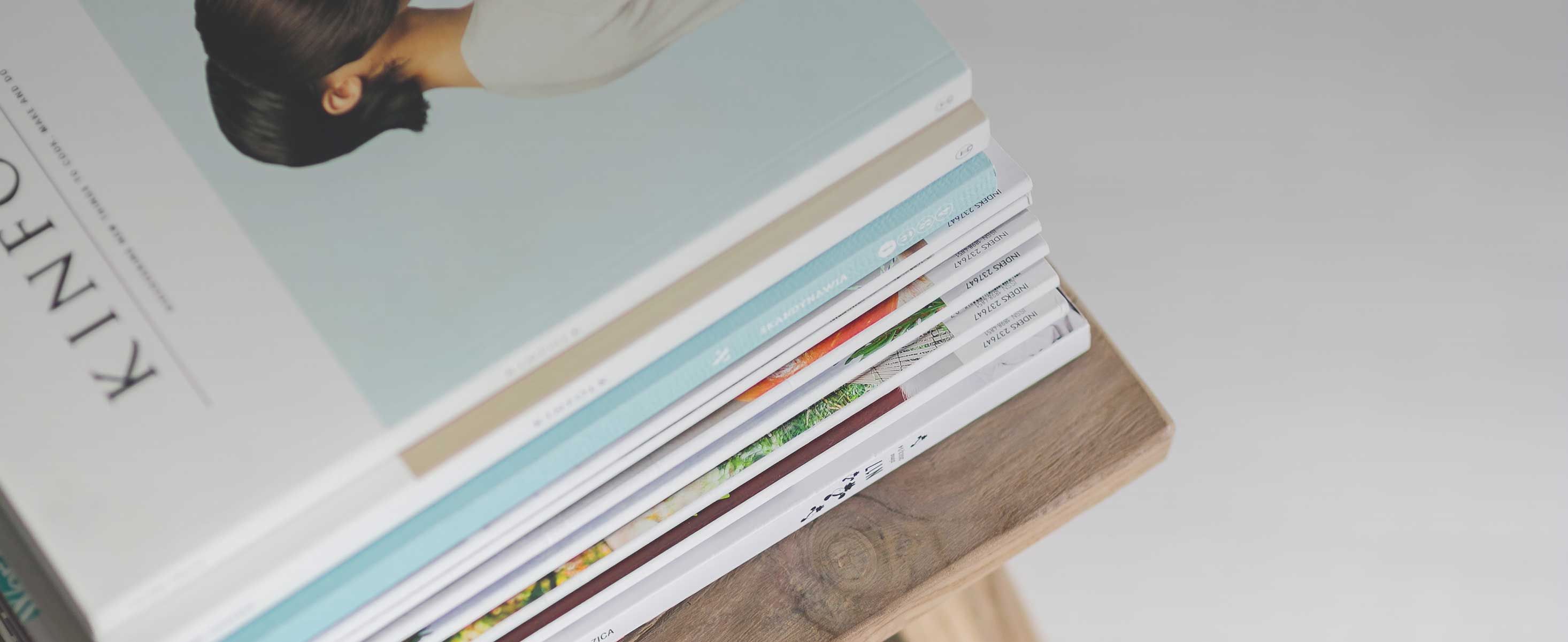
2 minute read
Design smarter for cost-neutral, low-carbon homes
MBIE-backed research finds low-carbon buildings can be built at no additional cost if clever design choices are made.
To reach our climate goals, Aotearoa New Zealand, needs to build houses with smaller carbon footprints. MBIE’s Building for Climate Change (BfCC) programme proposes new regulatory requirements to cap both operational and embodied carbon in new buildings.
Can carbon savings be made without increased costs?
While there’s no doubt that energy-efficient buildings are cheaper to heat and cool, MBIE wanted to know if low-carbon buildings would come at a cost premium at the initial construction stage.
It commissioned thinkstep-anz, engineering consultancy Mott MacDonald and quantity surveyors Prendos to investigate if it is possible to achieve BfCC’s proposed carbon savings without increasing the upfront cost of construction.
Looking at more than 20,000 unique combinations of locally available building elements for residential homes, the research found that reducing the carbon from building materials will typically come at a higher upfront cost.
However, an opportunity exists to reduce or eliminate this additional cost by optimising the building’s design.
Impact of lightweight building design
Lightweight building design often equals low embodied carbon design. The widespread use of lightweight timber framing and lightweight cladding materials throughout New Zealand means that our homes have a lower-carbon starting point and less potential to reduce embodied carbon than many other countries.
Reductions in carbon footprint per square metre are, therefore, likely to be incremental rather than radical step changes.
Smart design will keep costs down
While homes with lower embodied carbon were typically more expensive, there was significant variation in building costs for the same level of decarbonisation.
Without changes to building design, reducing the upfront carbon footprint of the reference building selected for this study by 30–40% was achievable through the choice of currently available building elements. However, these reductions come at a price premium of 5–10% per square metre of floor area on average.
The study also showed that, through optimising the design, savings of up to 36% in upfront carbon and 12% in whole-of-life embodied carbon compared with the reference building were possible for no additional upfront cost.
Strategies to reduce upfront cost and carbon
The study found there is no silver bullet to reduce operational carbon, embodied carbon and upfront cost simultaneously. One effective strategy to reduce embodied carbon was to substitute a concrete slab for a suspended timber floor, but this had trade-offs in operational energy performance and upfront cost in some cases.
The construction industry has an important role to play in implementing tools that identify optimal outcomes at the building level. Designers and builders should work with suppliers and demand low-embodied-carbon building systems (such as floors and windows) with equal or better thermal performance than existing systems.
by Jeff Vickers Technical Director, thinkstep-anz
Parameters of study
Reference building
The study used a single reference building from the LCAQuick library as the basis for analysis. It is a single-level detached home with a gross floor area of 218 m² and an internal living area of 170 m². It has 4 bedrooms, 2 bathrooms, 2 living areas, a kitchen and laundry and an internal garage.
Calculating carbon and cost
The study modelled operational energy/ carbon and embodied carbon for the reference building with different levels of thermal performance and material combinations.
Modelling was done at system level – floors, roofs, walls and windows – rather than material level. Operational energy modelling was done in IES in accordance with NZS 4218:2009 Thermal insulation – Housing and small buildings. Embodied carbon values come from BRANZ’s CO₂RE v2.0 with additional modelling in LCAQuick v3.5.
Overall, 22,032 unique combinations of building elements were considered:
• 6 roof options
• 7 envelope wall options
• 6 internal wall options
• 12 floor options
• 3 window options.
There were also regional scenarios for operational energy/carbon modelling in Auckland, Wellington and Christchurch.
Definitions
Operational carbon – carbon emissions from energy and water used in the building during its operational life.
Embodied carbon – emissions from the building’s materials and products, the construction process, construction waste disposal, maintenance and refurbishment throughout the building’s life and disposal at the end of the building’s life.
The report Cost-neutral, low-carbon residential construction is available at www.thinkstep-anz