
12 minute read
A transformational year for Domino’s.
In announcing its full year results for the 52 weeks ended 26 December 2021, Domino’s Pizza Group Plc has reported continued strong momentum, with system sales of £1,499.1m, up 11.2%. Like-for-like system sales, excluding splits, up 10.9% (9.8% including splits).
Underlying like-for-like system sales (excluding the temporary benefi t of VAT) grew by 5.5%, 150 basis points higher than last year’s equivalent fi gure of +4.0% and underlying profi t before tax of £113.9m, was up £12.7m driven by strong underlying trading.
Statutory profi t after tax of £78.3m, up £38.6m due to signifi cantly reduced international losses with continued strong free cash fl ow of £104.6m (2020: £99.0m). Net debt of £199.7m, in-line with guidance, resulted in a net debt/underlying EBITDA leverage ratio of 1.54x.
There was additional £6.6m investment in a new Northern Ireland joint venture and £136m was returned to shareholders in FY21 through dividends and share buybacks and £14.3m of capex to support store growth.
A proposed fi nal dividend for FY21 of 6.8p per share is to be paid on 10 May 2022, resulting in a total dividend for FY21 of 9.8p per share, +7.7% vs. FY20.
Operational and strategic highlights included good growth in total orders, up 5.5% in the year. Delivery performed well, and collections continued to recover, growing sequentially each quarter. Collections fi nished the year at 87% of 2019 levels and there were excellent service standards with average delivery times of around 25 minutes, reported the brand. Now a truly digital-fi rst business with 91.2% of sales through digital channels, a new App launch now accounts for 42% of system sales (+2.2pts vs. 2020) 31 new stores were opened in the year with new stores trading ahead of expectations and on track to open at least 45 new stores in FY22. They had reached resolution with their world-class franchisees heralding a new era of collaboration and a fi rst national price campaign for several years launched in January 2022, with fi ve new stores opened in FY22 vs. one in the same period in FY21.
There had been a new integrated media campaign, ‘DominOh-Hoo-Hoo’, targeting families and friends reuniting post lockdown and followed by fi rst ever festive TV ad campaign, which resulted in order count growth ahead of expectations, they reported.
They had also continued to strengthen their leadership team with the appointment of a new chief marketing offi cer and operations director and a new people director. They had also opened their third UK supply chain centre in Cambuslang, Scotland and completed exit from all directly operated international markets allowing them to focus on the core UK and Ireland markets
They expect FY22 underlying EBITDA and EPS to be in line with current market expectations. Trading in the fi rst quarter has started well, aided by their fi rst national price campaign for several years, and made possible because of the resolution with our franchisees. Overall order count and customer acquisition continues to be positive, despite being up against a comparative quarter last year when there were strict lockdown restrictions in the UK.
Their fl exible and robust business model means they are well placed to adapt to changing market conditions and ongoing challenges related to infl ation and recruitment, they stated. As such, they continue to expect an acceleration in underlying system sales growth (excluding the benefi t of the reduced rate of VAT), largely driven by increased store openings and likefor-like growth due to the operating and capital investments associated with the franchisee resolution and continued implementation of our strategic plan. Commenting on the results, Dominic Paul, chief executive offi cer said: “This was a transformational year for Domino’s. Our performance continues to be strong, and we have made signifi cant progress against our strategic plan, all while delivering on our ambition to return excess capital to shareholders. None of this would have been possible without the hard work of our franchisees and my fantastic colleagues.
“There were two major milestones in the year. First, the launch of our new strategy, which is already delivering outstanding results and a better experience for our customers. Secondly, the resolution with our franchisees which has unlocked further potential within the system. Our franchisees are world class operators and the whole team is already embracing a new era of collaboration, with the system working together more closely than ever before.
“This year has started well, and we now have the right strategy and a strong senior team in place to continue to drive the business forward. We remain focussed on accelerating the sustainable growth of our system together, to deliver a better future through food people love.”

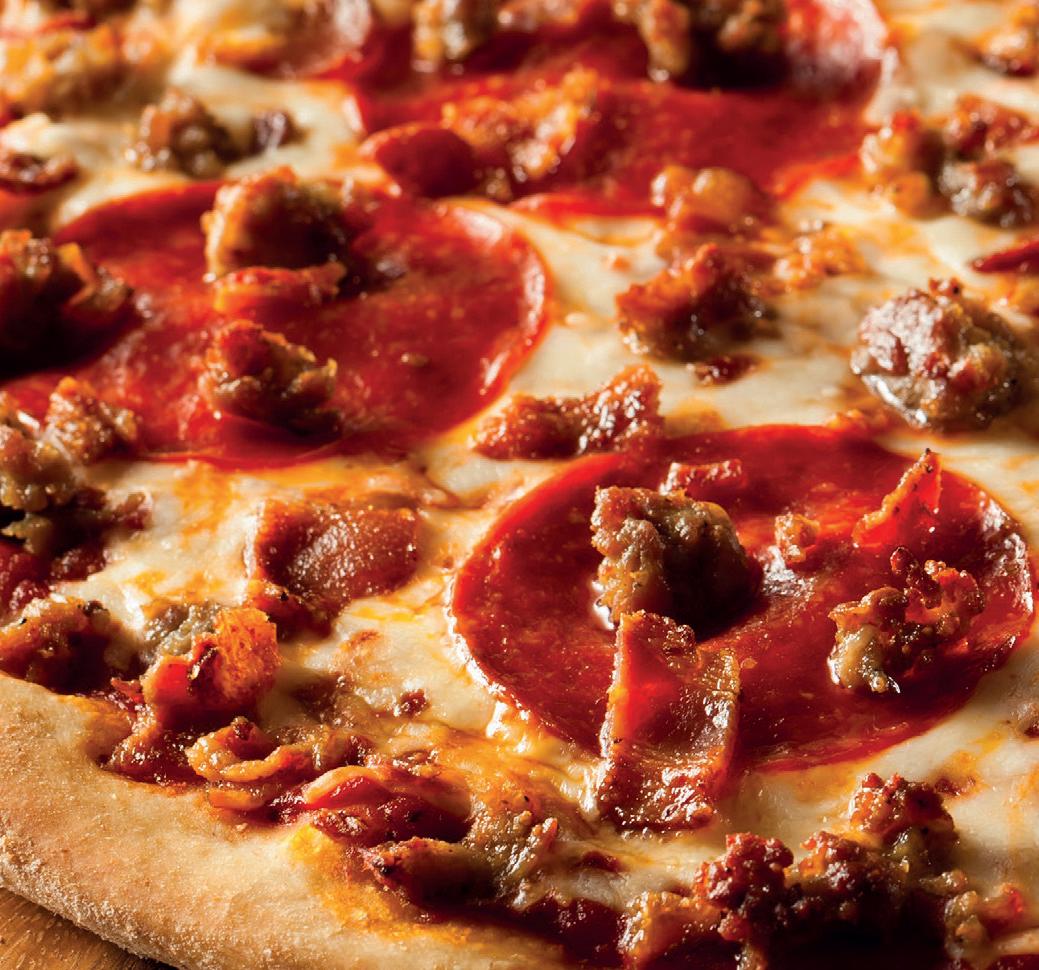
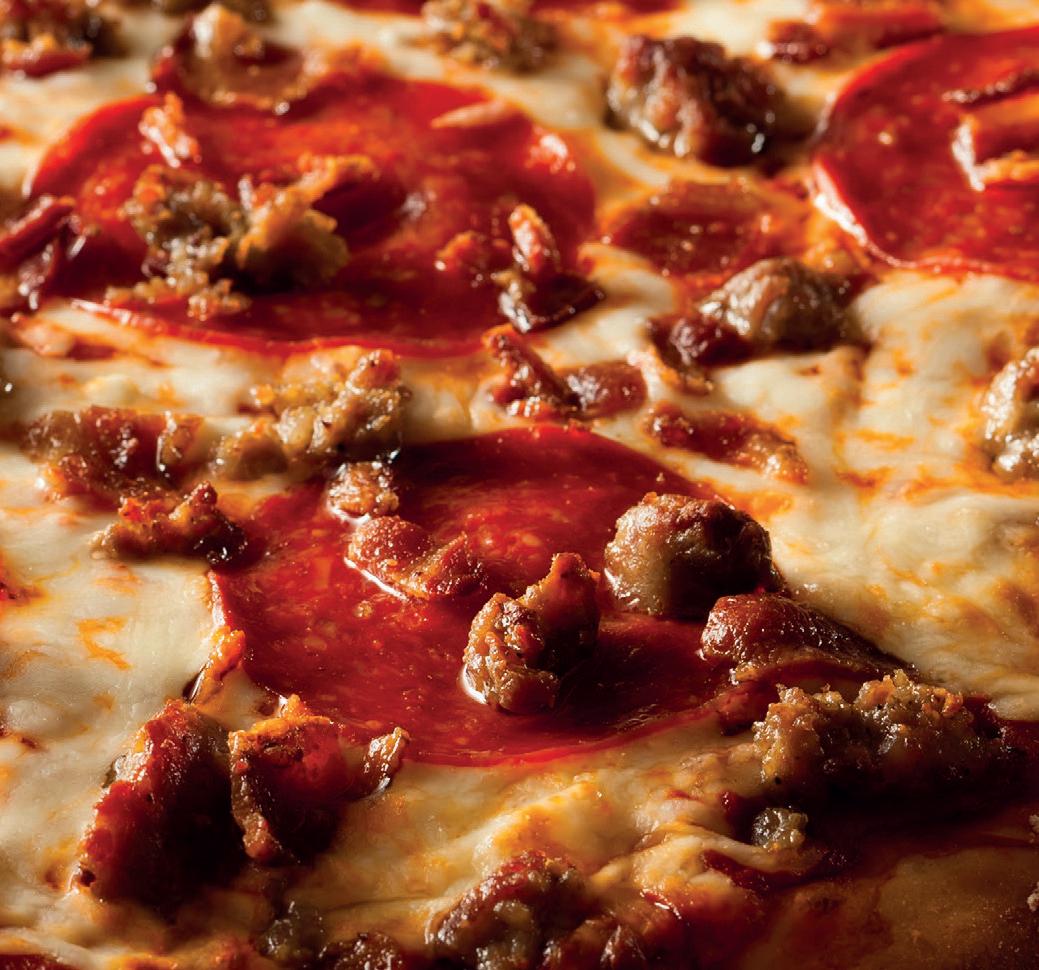
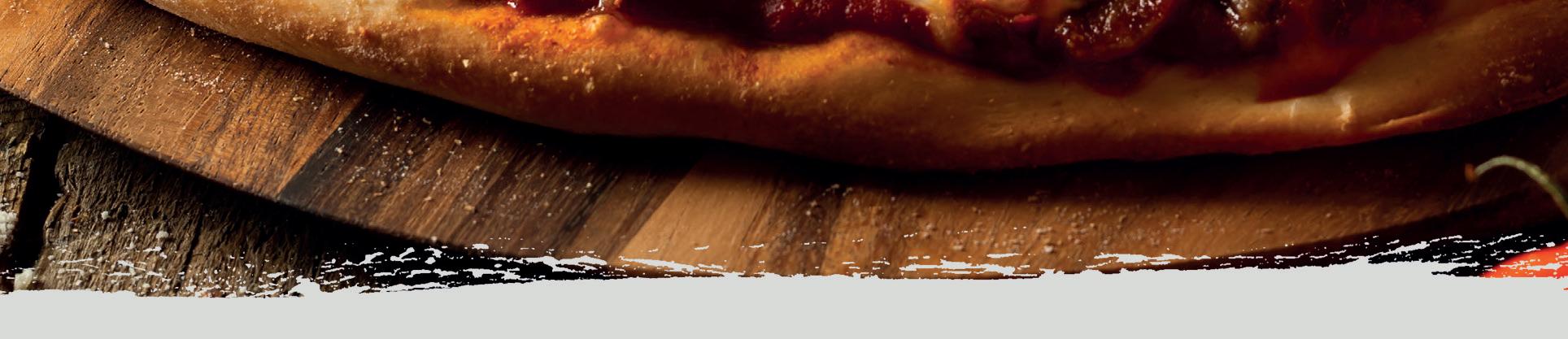

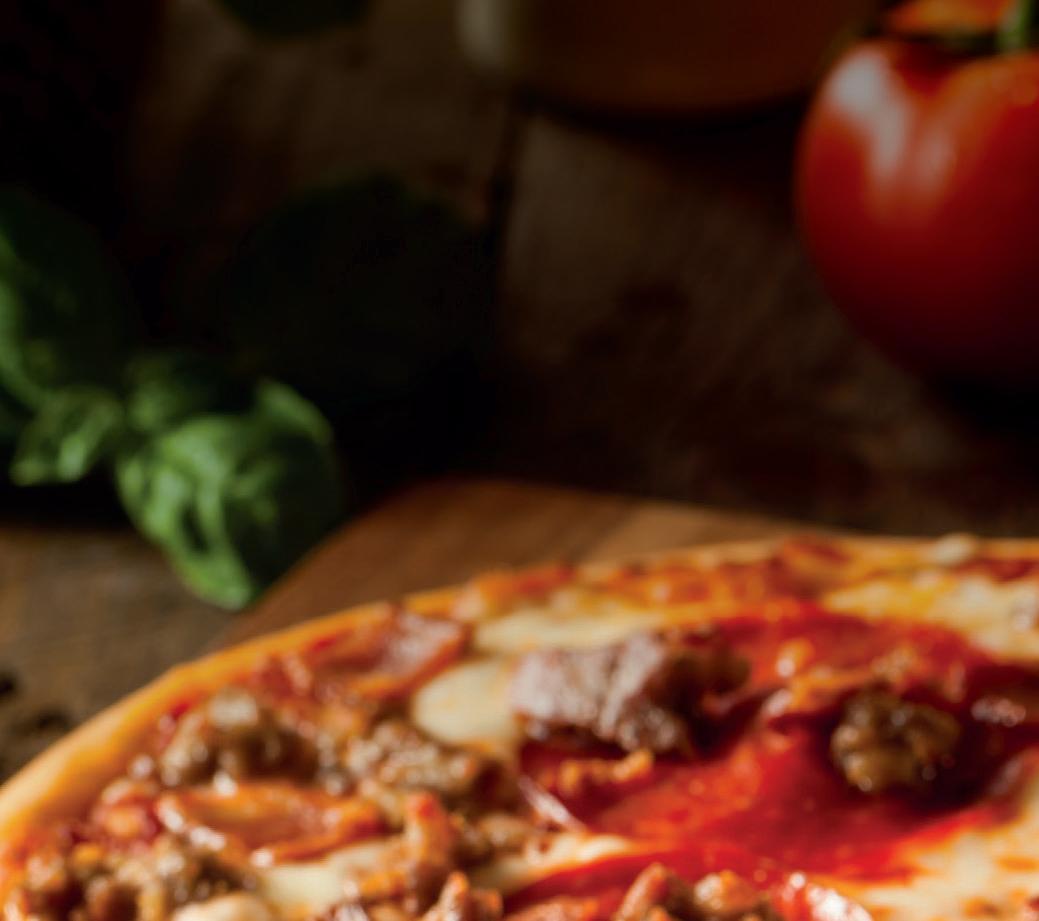
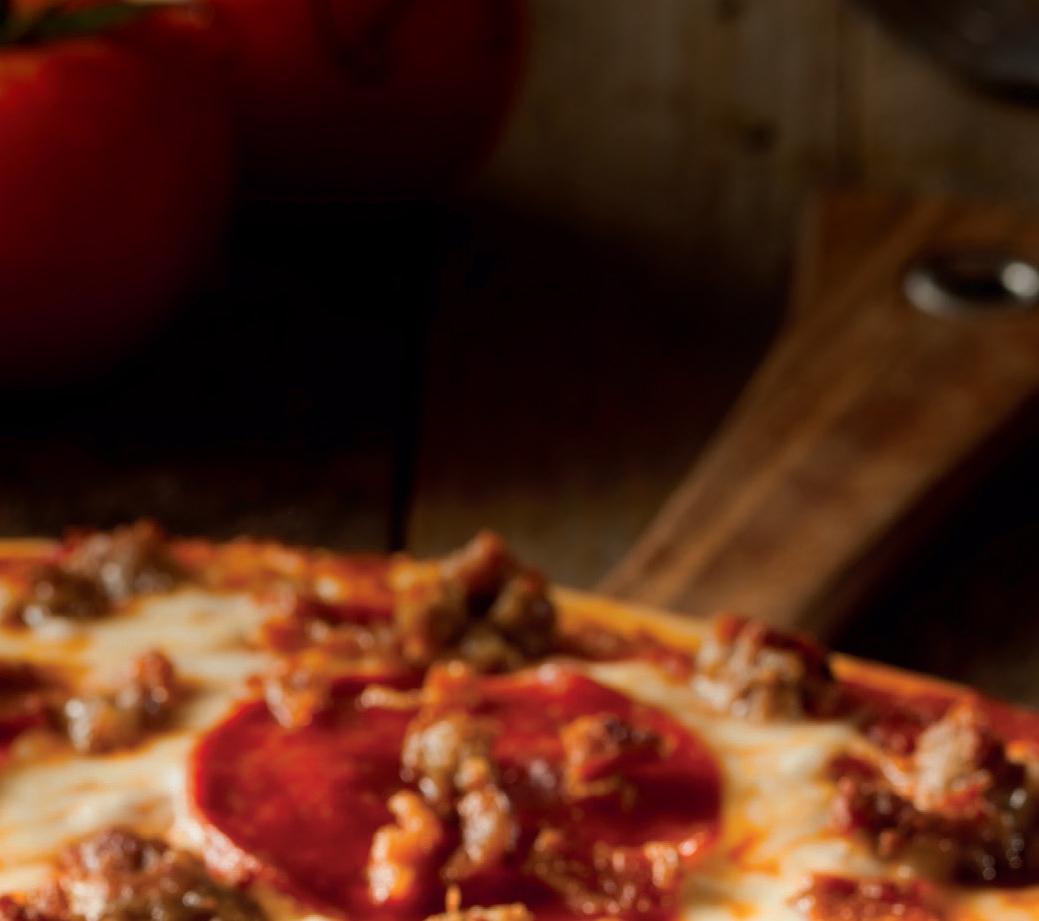
Consorzio del Parmigiano Reggiano partner in food-safe digital tracking technology
The Parmigiano Reggiano Consortium (Consorzio del Parmigiano Reggiano) has announced a partnership with Kaasmerk Matec (Kaasmerk) and p-Chip Corporation (p-Chip) to launch a line of food-safe and secure traceability digital labels for its Parmigiano Reggiano cheese wheels.
The new technology will deliver previously unseen levels of traceability, inventory tracking and control, product authentication, quality-assurance testing, product serialisation, and consumer safety.
Nicola Bertinelli, president of the Parmigiano Reggiano Consortium, commented: “As one of the world’s oldest and most famous cheeses, Parmigiano Reggiano is a symbol of high-quality Italian products. Since the Consortium was founded in 1934, we have aimed to convey the value of our product globally and distinguish it from similar-sounding products on the market that do not meet our strict requirements for production and area of origin. By being the fi rst to incorporate these secure digital labels onto our cheese wheels, we can continue to ensure consumer safety, bringing the traceability and authentication of our products to meet industry 4.0 technological targets.”
Since 2002, a casein label with a unique and sequential alphanumeric code is applied to each Parmigiano Reggiano cheese wheel but now p-Chip is launching a new line of secure, digital tracking labels for the industry, and the Parmigiano Reggiano Consortium is breaking new ground by embedding these p-Chip micro transponders into 2D codes, QR codes, and/or data-matrix codes. The result is an innovative, food-safe digital tag that takes CFPR’s food safety and security a step beyond the government requirement.
Kaasmerk Matec and p-Chip Corporation partnered to complete this innovation program for a p-Chip device integrated into casein label, an industry-standard, protein-based type of food/cheese identifi cation method. The innovation combines food-safe Casein labels with the p-Chip micro transponder—a blockchain crypto-anchor that creates a digital “twin” for physical items. This scannable new food tag is smaller than a grain of salt and highly durable, delivering next-generation visibility and traceability to the Parmigiano Reggiano Consortium.
Joe Wagner, CEO of p-Chip Corporation, commented: “We’re pleased to partner with a leading global brand as the Consorzio del Parmigiano Reggiano to bring world-class, disruptive tracing technology to the food industry. By integrating p-Chip micro transponders into casein tags, the Parmigiano Reggiano Consortium can better control its inventory and protect and diff erentiate its products against look and sound-alike brands and have access to unmatchable track-and-trace technology to protect itself in the case of recalls or other issues. I look forward to working with Consorzio del Parmigiano Reggiano as they realise the full potential this technology holds for their business.”
Over the past two years, the Parmigiano Reggiano Consortium has conducted extensive testing of the p-Chip/Kaasmerk Matec Casein label and approved the label’s technical use for the authentication and digital traceability of Parmigiano Reggiano cheese.
Winus Sloot, managing director of Kaasmerk Matec, commented: “For more than 100 years, we’ve worked with artisan cheese producers to deliver casein cheesemarks that provide an invaluable level of protection for their recipes, helping to safeguard the passion and craftsmanship they bring to production of their cheeses. We are pleased to collaborate with p-Chip to develop this smart digital label that will track and trace the Parmigiano Reggiano Consortium’s bulk cheeses from start to fi nish, providing additional protection to both the Consortium as well as consumers, as the label is highly resistant to tampering.”
The new smart digital food labels will be added to 100,000 Parmigiano Reggiano bulk cheese wheels in the second quarter of 2022. This represents the fi nal phase of large-scale ‘testing’ before evaluating the possibility of extending this technology to the entire production of Parmigiano Reggiano.
Pasta Rapida launches in Ocado
In a hurry to make dinner but still want a mouthwatering meal made with authentic pasta from Italy?
This ultimate pressed-for-time pasta, claim its creators – Pasta Rapida - has now been brought to the UK by pesto company Sacla’. It is made by Rustichella in Abruzzo, Italy, a family business who’ve been making pasta since 1924, and is full of fl avour, cooking in just 90 seconds from the packet!
Thanks to the unique way it is produced, this spaghetti-type pasta cooks in less time than it takes to open the jar of your favourite sauce or grate the Parmesan, it is claimed. And it’s not precooked – it’s made with a special bronze die to create the clever shape that allows the pasta to cook so quickly, they point out, even telling you when it’s done, with the small slit along its length closing up (it costs £2 a packet).
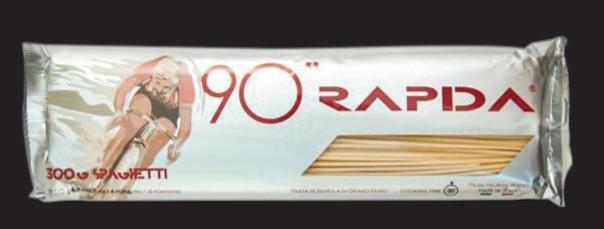
Princes becomes first Italian tomato processor to sign pre-harvest supply contracts
International food and drink group, Princes, says that it has delivered on its promise to sign tomato supply contracts well in advance of the 2022 harvest – becoming the first Italian tomato processor to establish agreements and commit to fair pricing that reflects the rising costs of production.
The group’s Italian tomato processing facility, Princes Industrie Alimentari (PIA) and popular Italian cooking brand, Napolina, are long-term advocates of conducting early negotiations to support the economic sustainability of the tomato supply chain and enhance the competitiveness of this strategic sector for Italy. Signing contracts in advance of harvest season is an important ethical practice which helps to enhance financial security among growers and their workers through the guarantee of fair and transparent pricing.
For 2022, PIA and Napolina have factored cost increases throughout the cultivation process into pricing for farmers across the Apulia region, who are also facing water shortage and supply chain disruption challenges. With industry-wide pricing negotiations yet to take place in southern Italy and agreements on hold in the north, the General Confederation of Italian Agriculture (Confagricoltura) has raised concerns about the future of the industry amid mounting pressures and market uncertainty.
Andy Hargraves, group director for Italian products, said: “One of the key challenges that many tomato producers face in southern Italy is not knowing what prices they will be paid until a few weeks before the harvest begins. At that point, if a grower has concerns for the profitability of their crop, the only costs that can be cut are in labour. This late contracting has been frequently cited by NGOs as a contributor to forced labour and human rights abuses, however it is a practice that still continues today.
“By signing contracts in advance, we are giving our growers more time to plan their investments for the harvest season, fostering financial stability and supporting the implementation of best practices and state-of-the-art technologies that help to enhance both social and environmental sustainability. We are also committed to ensuring producers receive a price for their tomatoes that reflects the actual costs of production, which continue to rise.
“The prices we’ve already agreed with our agricultural partners for 2022, which have been established in collaboration with the Department of Agricultural Sciences at the University of Foggia, guarantee a fair price for around 300 producers across 30 partner cooperatives. We believe this is an important catalyst for the growth of the entire Apulian tomato supply chain and will support its competitiveness throughout international markets, at a particularly turbulent time for the industry.”
PIA and Napolina will also reward growers who supply particularly high-quality tomatoes this season, through the support of innovations such as agriculture 4.0 technologies – introduced in collaboration with group partners. This continues from last season, they report, when PIA paid €3.9 million to its agricultural partners, in addition to the base price, as a bonus for their contribution to the sustainability of the sector. This is just one element of PIA and Napolina’s ongoing efforts to tackle ethical trading and human rights issues across the southern Italian tomato supply chain, such as the Caporale (gangmaster) system. The Caporale’s control often has farreaching and negative impacts on the lives of workers, through illegal wages, poor working conditions, lack of contracts and forced labour. Labour in fields is not the only issue, with recent reports of fines imposed on tomato processors for illegal practices, including the adulteration of food products made with non-Italian tomatoes. The contract agreements follow the recent announcements of Princes’ new partnership with Oxfam Italy and expanded collaboration with leading Italian agricultural association, Coldiretti, to enhance the social, environmental, and economic value of the tomato supply chain. Through collaborations with partners like Coldiretti and Oxfam Italy, Napolina and PIA say that they are playing an important role in highlighting the positive changes that can be made to historical ways of working in Southern Italy. In the UK, consumers can see the origins of Napolina tomatoes via on pack Quick Response (QR) code technology, and PIA has been recognised by UK supermarkets for its work in addressing human rights issues in the Italian tomato supply chain. During the 2021 season, PIA processed over 200,000 tonnes of fresh tomatoes (+ 10% versus 2019) – and between July to September, hired over 1,500 workers (across agronomy, logistics, production, and quality control). At PIA’s Foggia plant - the largest tomato processing site in Europe – 100% of the processed tomatoes are of Apulian origin and all suppliers must hold Global G.A.P. GRASP or SA8000 certifications. In addition, all of PIA’s tomato growers must be enrolled on the ‘Rete De Lavoro’, a Ministry of Labour public register of businesses fully compliant with labour and human rights legislation and transparent payment of wages.
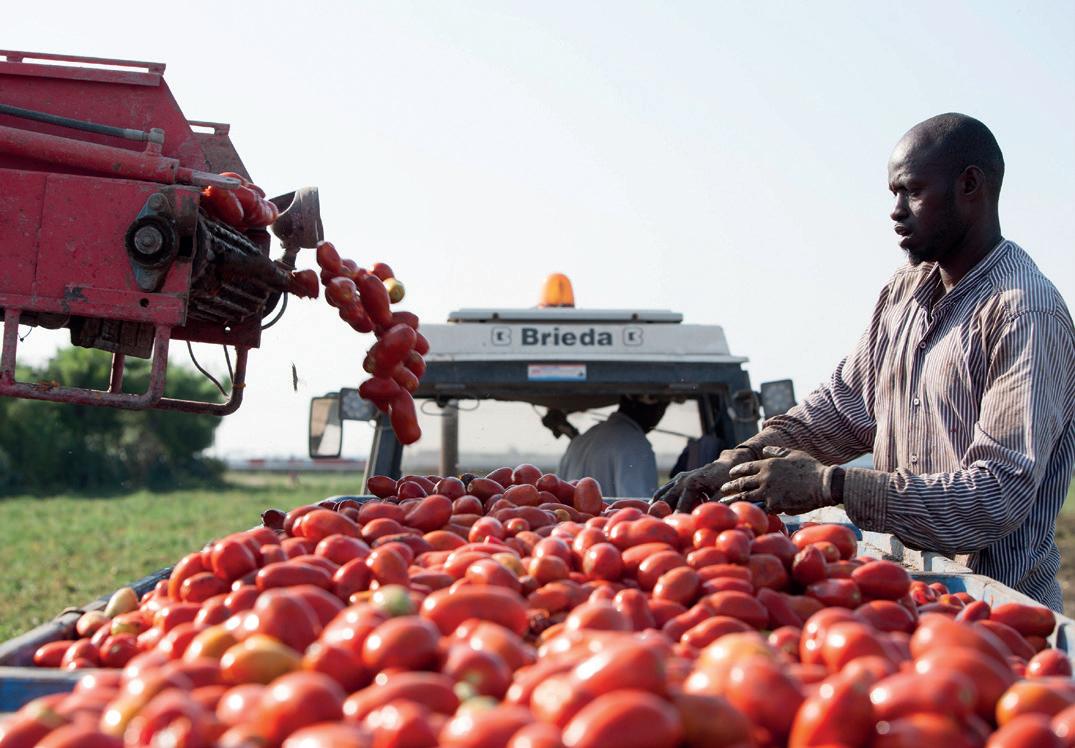