
3 minute read
Custom Knives by Dan Bruce
from Move Up ~ Issue 28
by VAULTmedia
SHAPING NEW OPPORTUNITIES WITH CUSTOM KNIVES AND SHEATHS
By Talena Winters Photography by Virginia Moskalyk
Advertisement
k dan_bruce78@hotmail.com
m 780-835-3962 Dan Bruce, 64, takes pride in making knives people actually use. Eight years ago, he took a continuing education course about making knives. That was the beginning of a hobby that has grown into a passion.
Not only does Bruce make custom knives, he’s also made many of his own knife-making tools, often with plans he found on the internet. By early next year, he plans to complete a forge he’s started making—also by hand—so he can shape his own blades too.
CUSTOM KNIVES
Dan Bruce
Originally from Carmen, MB, he currently lives in Fairview with his wife, where he teaches at Grande Prairie Regional College Fairview Campus.
How did you get into making custom knives?
I took a course by George Roberts of Bandit Blades and built a knife from a blank blade that weekend. I fell in love with the craft. Of course, a hunting knife needs a sheath, so I started fooling around with leatherwork too.
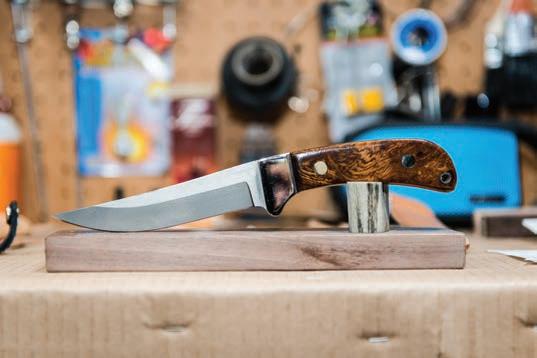
I bought five more blank blades from the same company. My wife encouraged me to take my custom knives to market, so I started selling them about two years later. When I finish the forge, I’ll be able to make the knives from scratch with raw materials. I work with a grinder I built, and I want to turn a log splitter into a hydraulic press to help with the work.
What about your process is important to you? I love the satisfaction of seeing what I started with become what I finish with.
For the knife handles, I start with a block of stabilized wood, epoxy them onto blanks and shape them to fit the hand. With some people, I’ve had them imprint their hand on Plasticine, so I can shape the handle to fit the hand. I make the basic shape with a Dremel tool, hand-file and then use a lot of hand-sanding to get the shape right. They get polished with a buffing wheel.
My sheaths are functional but plain, with no tooling. I hand-stitch all my sheaths with two needles and thread, and I block stitch. One of those takes me about four hours by the time I glue it, shape it, stitch it and dye it.
A knife handle can take as much as 12 hours. Right now, I’m working on a fancy dagger for my granddaughter with an ebony handle and nickel silver hand guard and pommel. I’ve probably got 30 hours into that one already.
Tell us a bit about what you make. I make various kinds of kitchen knives, filleting knives and hunting knives. I have a number of exotic woods I use to make the handles, like ebony, wenge wood, zebrawood, black walnut, bocote, ziricote and really hard woods like purpleheart and desert ironwood, which is one of the hardest woods in
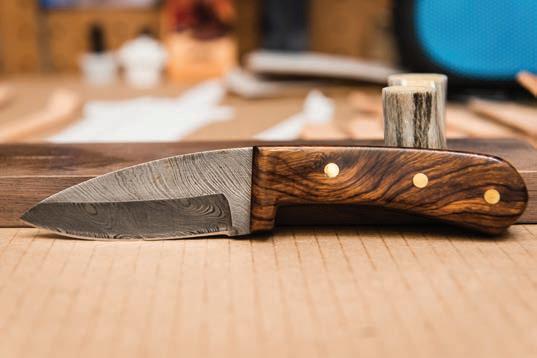
the world. A lot of them are South American and African woods, but the wood comes from all over. I use Jantz Supply blades and buy my leather from Tandy Leather.
A paring knife is about $40, and my top-end knife and sheath sets go for around $225.
For sheaths, I have a few different types of belt loops and clips. I’ve built shaped sheaths for folding blades, pocket knives and more. I’ve experimented with a few requests for people, making .22 rifle cases and even a key fob holder.
Where can people purchase your products? The best place to see photos of my work is my Facebook profile (Dan Bruce) under the albums labelled “Knives.” You could also call me at (780) 835-3962 or email at dan_bruce78@hotmail.com
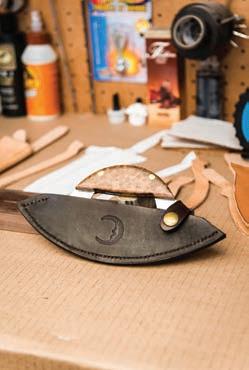

