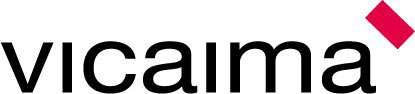
22 minute read
Editors Choice
Fresh ideas for Interior Doors in 2020
www.vicaima.com
Advertisement

Jobs in the Construction Industry
The construction industry is fast becoming a haven for individuals on the lookout for handsome paying jobs on construction sites.
There is no doubting the importance of the construction sector on the economic growth of any country.
If you are the type that loves constructing a fantastic masterpiece with your hands, then this article is for you. You can’t beat the feeling that comes with seeing how successful the work of your hands has become.
To put this into practice, how about we take a look at the top jobs available in the construction industry. Evaluate yourself, check for the job that fits your skills and expertise, then watch how you will conveniently find your way rising to the top.
• Project Engineer
If you know your onions in the engineering field and you are looking to get a job with the managerial position, then this job is for you. Here, you are tasked with supervising the engineering projects assigned to you.
Your ultimate aim is to make sure you go far and beyond expectations to deliver great results.
• Construction Estimator
A construction estimator is saddled with the responsibility of evaluating projects and providing near-to-accurate costs of executing a given project successfully. You are expected to pay attention to even the tiniest of details concerning a project.
• Journeyman Electrician
Someone looking to secure a job in this field is expected to have the technical know-how of installing and maintaining electrical systems both at home and commercial project sites.
You must take pleasure in finding the source of any problem an electrical system might be facing and at the same time, providing prompt solutions to such a problem.
• Construction
Superintendent
A construction superintendent plays an integral part in the execution of a project. As a superintendent, you have to be around to supervise any project given you, right from the onset to the end of the project.
Not only that, you must be accountable for all the activities that take place on the site. You are to ensure that the construction site is kept safe and secure.
• Pipe-fitter
To be the best fit for this job, you need to have gotten yourself immersed in the knowledge of some basic techniques. Basically, you will be working with metals a lot. It is then expected of you to use skills such as cutting, bending soldering and the likes, to shape your metals to your desired forms and shapes for construction sites.
In addition, you are expected to convey the pipes needed for construction to the appropriate sites and also install them.
• Plumber
One must say this job is quite challenging. However, if you’ve acquired enough training on repairing and fixing water pipes for homes and buildings, you shouldn’t let this job pass you by. Plumbers are expected to identify and provide a solution to the leaks that may occur in pipes run for domestic purposes. Pipes run through sink drains, toilets and other domestic purposes often develop faults after a while. A plumber is expected to come in easily and put an end to any issue that may arise.
• Equipment Operator
Often time, some construction sites require the use of some heavy machinery. Equipment operators are charged with ensuring the safe use and proper care of the equipment in use.
Their services are commonly employed on sites where demolition or construction is to take place or sites where logging of wood is frequent.
Final Take
Getting a job in the construction industry is not as hard as it is made to be. Thankfully, Jobs is available to help you in your quest to search for the available jobs in the UK. Pay them a visit and secure that dream job in no time. Needless to say, make sure you’ve evaluated yourself according to your skills before applying for any job.
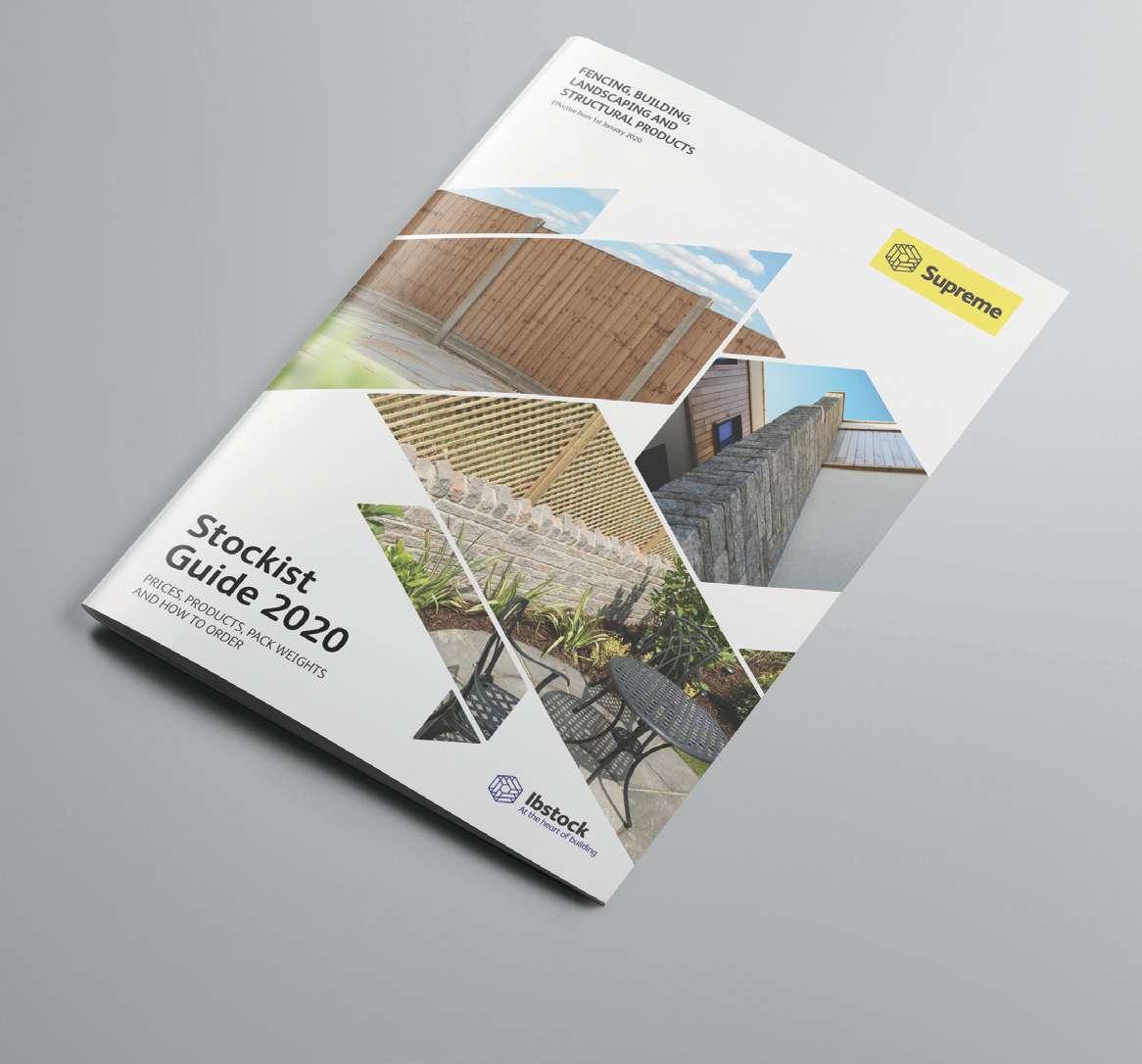
As part of its commitment to supporting the built environment, Supreme Concrete, the UK’s leading manufacturer of precast concrete products and fencing systems, has released its new stockist guide for 2020.
The easy to use brochure has been updated to incorporate the latest changes to its extensive product offering following the addition of Anderton Concrete’s building and fencing products into its portfolio. In addition to its updated product offering, the newly refreshed guide provides customers with a simple pricelist to help streamline the planning and specification stages.
Mark Swift, Director of Sales for Supreme Concrete, said: “Our latest stockist guide provides a handy catalogue for customers to refer to when selecting specific products for each project they are working on. This can be easily done through the guide’s simple breakdown of the products’ attributes, including colours, textures and pricing. “2019 has seen a fantastic increase to our product range, including the inclusion of pre-blended packs of high quality Shearstone Walling Stone, all of which can be found in our new stockist guide.” For further information on Supreme’s market leading offering, visit: www.supremeconcrete.co.uk or call 0333 999 2220
Tips for running a
Operating a greener fleet reduces carbon emissions whilst saving costs and improving productivity for businesses of all sizes, but organisations have different ways of “going green.”
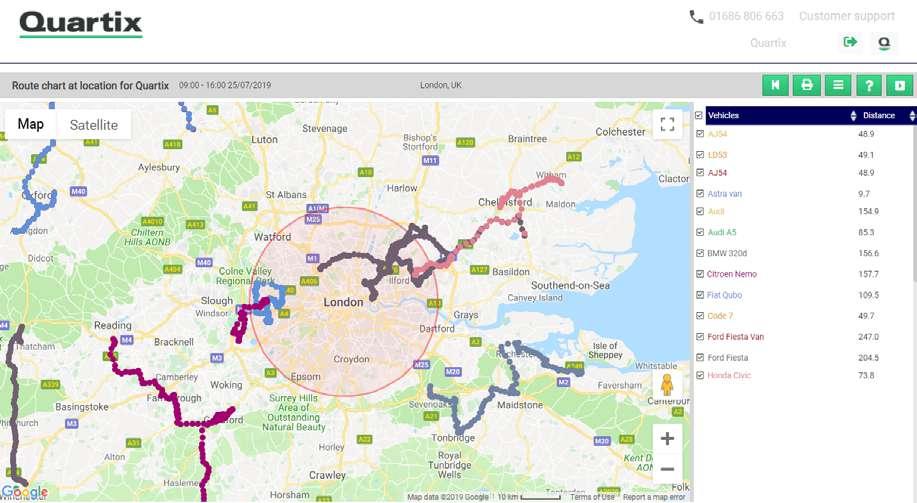
Some employ a vehicle tracking system to help them improve their carbon footprint. This comes with the added benefit of reports and tools that allow them to measure driver performance, a key factor in reducing overall emissions. Others rely on Eco-Driving, a style of driving behavior that can reduce fuel consumption and minimise vehicle maintenance which costs money and time.
Here are a few simple ways that you can run a greener fleet.
Improving driving styles
Monitoring driving style across your fleet can help you lower instances of speeding and reduce harsh braking and acceleration. If your system provides each of your drivers or vehicles with an overall score based on these three criteria, it’s easy to see where improvements need to be made, especially if the system displays the scores in a league-style table. Speed analysis reports let you see specific instances where a driver exceeded the speed limit or went above what’s considered a safe speed for that stretch of road. Improving your fleet’s driving style minimises CO2 emissions from your vehicles, helps save fuel and reduces the risk of accidents on the road, making your fleet safer and cheaper to run.

Tips for running a greener fleet
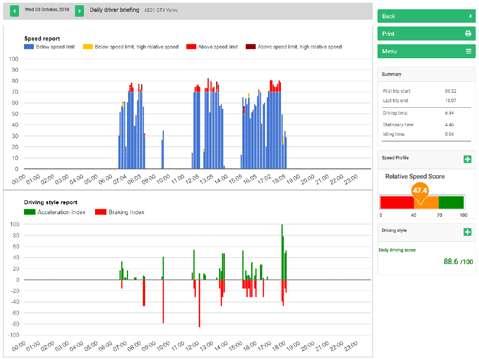
Trip reporting & route maps
Vehicle tracking shows you the total mileage for your fleet. Driving hours and idling times over a specified period are displayed in simple, easy to read reports, whether you need to see the data by driver or by vehicle. Acting on this insight can improve overall productivity and reduce employee overtime by up to 15%.
A good system shows you the routes your drivers are taking every day, letting you see where they overlap. Armed with this knowledge, you can streamline your drivers’ daily routines, eliminating unnecessary vehicle usage and the emissions that go with it.
Reducing idling times
Traffic is the number one source of idling, but live tracking with traffic information can help your drivers avoid areas of severe congestion, allowing them to take routes that will keep them moving. Instances where the engine is left running unnecessarily, for example when the vehicle is parked, can also be identified and corrected.
Knowing how your drivers are performing out on the roads can help you to decrease idling times by up to 30%. Identifying where your drivers can decrease idling not only saves fuel, it also reduces the emissions your vehicles are releasing into the atmosphere.
Eco-driving
Eco-driving, or energy-efficient driving, is a way of driving that reduces fuel consumption and CO2 emissions, while decreasing the risk of accidents. For companies who adopt eco-driving, it can lead to significant savings, both in terms of fuel use and vehicle maintenance. Embarking on an eco-driving initiative requires thought, planning, and awareness. The idea is for employees to drive smarter, better and to develop good driving practices. There are two points within a journey where simple actions will ensure that you and your employees are driving safely and efficiently.
When preparing for a trip and while on the trip, be sure to: Check your tyres – Check the pressure of your tyres at least once a month, and especially before long trips. Underinflated tyres increase rolling resistance, resulting in up to 5% more fuel consumption.
Avoid unnecessary loads – The heavier a vehicle is, the more fuel it consumes. Avoid carrying or storing unnecessary equipment in your vehicles; this can lead to higher energy consumption.
Check the overall condition of your vehicles – A poorly maintained vehicle can increase your fuel consumption. For example, a clogged air filter fills the engine with dirty air, leading to a loss in power from the internal combustion mixture. Regular maintenance of your fleet saves money on fuel and maintenance and extends the life of your vehicles.
Use air conditioning wisely – Limit its use to just periods of extreme heat and consider venting the vehicle before starting your journey. At lower speeds, open the vehicle’s windows instead of using air conditioning. However, at higher speeds, it’s more fuel efficient to use the air conditioning.
Avoid over-revving – To avoid overloading your engine, change gears around 2,500 rpm (2,000 rpm for a diesel vehicle). By using your engine optimally, you can reduce your fuel spend by a significant amount.
Creating a greener fleet is a long-term commitment, but it won’t just be the environment seeing the benefit—your bottom line will see the difference, too. With ever increasing guidelines on emissions and fuel efficiency, having a good vehicle tracking system or a policy of eco-friendly driving will help your organisation get ahead of the curve.
About Quartix
The Quartix vehicle tracking system is installed in over 500,000 vehicles and helps more than 13,000 businesses cut costs and save on fuel every day. Providing commercial fleet tracking for cars, coaches and vans throughout France, the UK, US and Europe, the award-winning system offers a host of valuable features for fleet managers. Customer industries range from Construction, Security, Landscaping and everything in between. 43
The pioneering programme is now even easier for contractors to use.
The pioneer of ceiling recycling schemes, Armstrong Ceiling Solutions, has fine-tuned its awardwinning* programme to make it as simple and as accessible as possible.
It is now even easier for contractors to reduce their environmental impact and divert waste from landfill which also saves them money from the subsequent taxes as well as from skips and transportation costs.
All contractors are now required to do is simply take down the old Armstrong acoustic mineral ceiling tiles** and stack them on pallets. In partnership with the local distributor, Armstrong will arrange collection free of charge*** and the old tiles will be 100% recycled into new ceiling tiles at the company’s production facility in Gateshead.
The scheme for the UK and Ireland, which has been in place since 2003, enables Armstrong to minimise its impact on the environment by not only diverting its old products from landfill but also producing mineral ceiling tiles with even higher post-consumer recycled content, currently up to 82%.
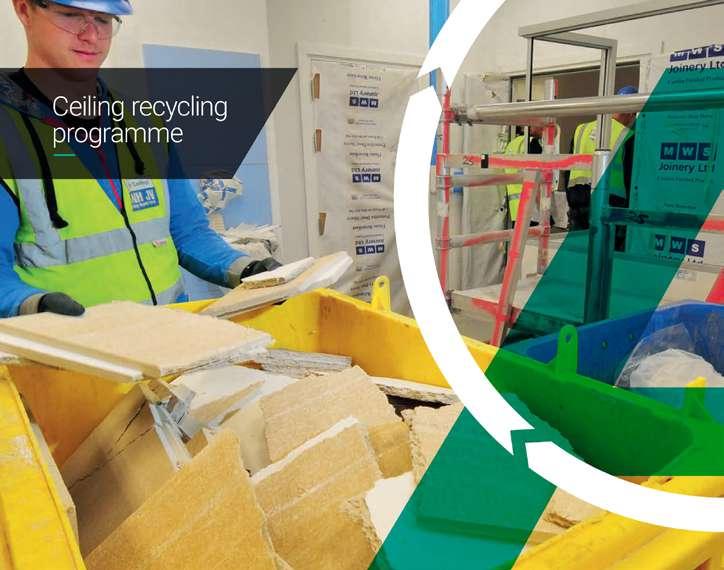
As well as the support it gets from distributors, Armstrong has also developed a “green” branch of its Omega network of approved subcontractors, specifically for those installers with proven recycling expertise .. and they claim that as well as saving them landfill tax it also makes then more attractive for main contractors to use.
Armstrong’s recycling programme for demolition, construction and renovation schemes has saved 15 million m2 of old ceiling tiles globally and diverted 61,000 tonnes of waste from landfill. And with 2,000m2 of recycled ceiling tiles equating to 7.6 tonnes of waste diverted from landfill, that is a 14,000 kWh saving on energy.
Projects have included the headquarters of main contractor Kier Construction, the temporary beach volleyball venue at Horse Guards Parade in London, and the Southern General Hospital in Glasgow.
A member of the UK Green Building Council, Armstrong also a partner in the Ceilings Sustainability Partnership, a working party of the AIS (Association of Interior Specialists) technical committee, which delivers on the actions within the Mineral Wool Ceiling Tile Resource Efficiency Action Plan (REAP). The REAP plan is intended to help the sector reduce the amount of mineral wool ceiling tiles going to landfill.
Armstrong recycling case studies also feature as WRAP exemplars, including Birmingham University Hospital where almost 43 tonnes of ceiling tiles were diverted from landfill and an estimated 19.5 tonnes of embodied CO2 were offset.
A new recycling programme leaflet, which has all the criteria information and steps to follow, is available CLICK HERE.
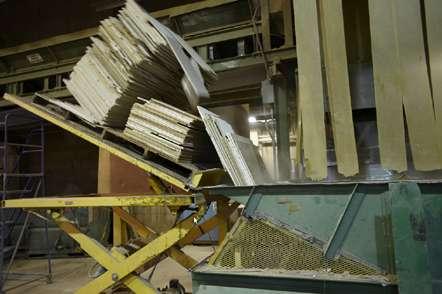
Wellbeing in the construction industry
Mental health and wellbeing are no longer corporate buzzwords. Businesses within the construction industry have a real duty to support the wellbeing of its staff. Not only does this foster a strong workplace culture, but can have a positive impact on business too. Happy staff are more productive, and more likely to stay loyal to their company (and, in turn, its customers).
Construction site workers are three times more likely to die by suicide when compared to the average male in the UK, showing the desperate need for more support in the industry. Construction professionals are exposed to long hours, demanding workloads, working away from home, financial uncertainty and physical strain. Some professionals feel high levels of responsibility and a general lack of support, which leads to mental health problems such as anxiety and depression. The environment is also still primarily male, perhaps reinforcing unhelpful male stereotypes leading to some being unwilling or feeling unable to talk about their struggles.
According to UK Construction Week stats, over half of construction professionals have suffered from mental health problems… and they believe their employer could do more to support them.
Though stats show that absenteeism is decreasing, presenteeism and leaveism is on the rise. This means that employees are coming to work ill, or using their annual leave entitlement when they’re working instead or should be off sick. For professionals in the construction industry this could be particularly dangerous, as mistakes can easily be made if someone isn’t fit to be at work. Employers should make sure that all members of staff, suppliers and contractors are able to take the time off they need to recover.
Stats from the Office for National Statistics show that employees take over for days off due to sickness each year, with many of these days off related to mental health problems.
Employers should prioritise improving wellbeing within the workplace. Healthy and happy employees are less likely to take time off work unless they are genuinely ill, in which case they should be entitled to rest and return to work when they are ready. In the long run, implementing a wellbeing programme can produce high ROI thanks to increased productivity, less sick days and higher employee retention rate. Stats show that over a third of construction workers have taken time off work due to mental health problems. If this number can be reduced thanks to an effective wellbeing programme, this can ultimately save businesses money. We Are Wellbeing is a strategic wellbeing partner that helps businesses develop a positive company culture where its employees can thrive. Part of the Romero Group, the complementary service offers businesses assistance developing and actioning a wellbeing programme. For those in the construction industry, this can help support staff through periods of stress. Where responsibility is high, hours are long and the pressure is on it’s important to be able to manage stress effectively and a wellbeing programme can help aid this. Physical health and safety is prioritised in the industry, and it’s high time employers now put the focus on mental health too. Nurturing an open-minded culture where team members are able to open up and talk about their struggles is just the start of building better wellbeing within the industry. To find out more about We Are Wellbeing, Romero Insurance Brokers’ recommended wellbeing partner, call 0113 281 8110 or visit www.romeroinsurance.co.uk.

Acoustics Academy by Quiet Mark. The new online building sector showcase for verified acoustic solutions
A new online platform has been launched to showcase verified acoustics solutions for the building sector.
Acoustics Academy is the latest development from Quiet Mark, the international award for quiet highperformance technology and solutions to unwanted noise.
The online showcase provides insight on verified acoustic products, materials and technologies for architects, designers, contractors, builddevelopers, specification-buyers and the wider building sector along with science-made simple commentary and installation insights.
It promises to simplify the complex world of sound design by comparing the most reliable and bestperforming products on the market. This is achieved through like-forlike comparisons and validation of products, which are organised into a directory for their performance, design, sustainability, suitability and costeffectiveness.
Acoustics Academy will also further educate on the complex technical details of acoustic design solutions, making them more easily accessible, better understood and higher priority, while encouraging design responsibility for health and well-being.
Developed in partnership with Quiet Mark’s expert acoustic teams including Anderson Acoustics, Head Acoustics and Intertek, Acoustics Academy uses leading sound measurement expertise to independently review all products equally and condense complex data to provide accessible market comparisons.
The platform includes every type of acoustic solution for all building application scenarios including; approved specialist Acoustic Glazing, Sound Barriers, Panels, Pumps, Acoustic Doors, Insulation, Commercial Ventilation, Acoustic Plasters and Surfaces and much more.


Example building application areas include, residential, commercial, industrial, schools, offices, healthcare, hospitals, restaurants and public spaces.
Poppy Szkiler, Founder and MD, Quiet Mark says: “Acoustics Academy is our new online platform to serve the Building sector by further equipping and empowering architects, designers and industry with expert-approved acoustic materials, products and solutions.
“Our buildings must evolve to embrace responsible sound-design to transform living spaces into harmonious soundscapes that deliver excellence in acoustic design and support our desire for quieter living. A property that has been designed acoustically creates a calm environment, reducing stress and supporting mental health.”
Quiet Mark confirmed sound measurement is complicated, saying It’s almost impossible to know how building or interior designs will sound if acoustics are not carefully considered with many foundational material elements involved.
Professionals often don’t know enough about which acoustic products are best to meet the bespoke needs that each building project requires or aware of the latest solutions available to suit their project budgets.
As a result, sound design can often be low on the list of priorities. Products and materials are selected without full understanding of their acoustic performance or the important installation and specification process to make them effective.
This leads to poor acoustics in buildings that do not support human health.
Quiet Mark also believe noise in our built environment can cause short and long-term health problems, including stress, sleep disturbance, increased risk of hypertension and cardiovascular disease, as well as hearing impairment. They say our bodies are not designed to cope with these constant intrusions and they take their toll. The World Health Organisation has defined noise pollution as the biggest threat to public health after air pollution.
As a result, the importance of acoustic design cannot be underestimated especially when open plan living means sound bounces around and quickly amplifies in the absence of absorbing surfaces. Building products and materials that are in harmony with nature are vital for calm living, working and leisure environments.
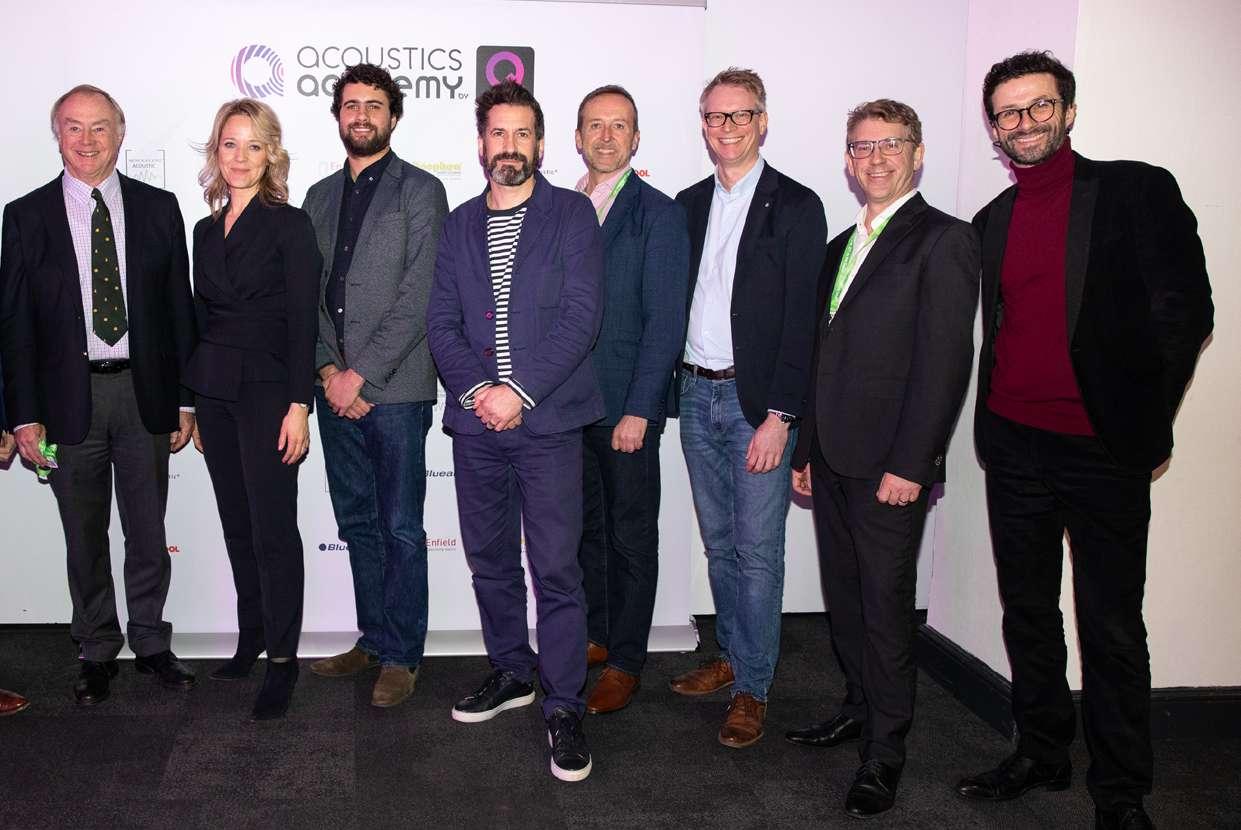
They believe a quiet environment is essential to help us recharge from the noise of modern life, including the constant mechanical soundtrack from road and air traffic, which creates an assault on our senses.
Turning down the volume on our lives allows quietness to restore and rebalance our physical and mental rhythms, recharging our energy and creating clarity of thought.
This is especially true for those with autism, dementia and people of any age with sensitive hearing who need help to find solutions to protect hearing and prevent hearing loss.
Quiet Mark, associated with the UK Noise Abatement Society charitable foundation (est.1959), has been leading the Quiet Revolution for over eight years. Quiet Mark engages directly with industry, manufacturers, consumers, retailers and influencers establishing noise-reduction and acoustic design as key considerations in product development.
Quiet Mark educates millions of consumers on the impact of noise in the home environment through new national retailer partnerships with Argos, ASDA, Currys Dixons, John Lewis, Very, Littlewoods and more, presenting a clear, easy way to identify quieter products.
Through its pioneering acoustic tests, and validation of manufacturers performance claims, Quiet Mark awards its distinctive Purple ‘Q’ Mark to products that are the quietest highperformance models in their category and noise reduction solutions to equip designers to build and design better buildings.
Quiet Mark
emailus@quietmark.com
Tel: 01273 823850 Quiet Mark: www.quietmark.com Acoustics Academy: www.quietmark.com/building/ building-sector
REGENERATED RESIDENTIAL ESTATE IN LONDON UTILISING LANGLEY’S FLAT TO PITCHED ROOF SOLUTION
Flat to Pitched roofing conversion is an excellent way of regenerating an estate or building by not only changing the roof of the building but, also extending its life expectancy and cost effectiveness of the building’s lifetime.
An example of a residential estate utilising this initiative was Enfield Council.
As part of a wide scale refurbishment project to improve the aesthetic outlook and services within the local area, Enfield Council employed Playle and Partners LLP who contracted ENGIE Regeneration. ENGIE partnered with Langley Structures to complete ten Flat to Pitched (FTP) roof conversions.
By implementing the FTP system, Enfield Council benefits from an improved aesthetic look of the buildings and an opportunity to make changes, including meeting modern building standards. Long-term maintenance of social housing roof assets is a key component of a council’s planning. Therefore, a durable pitched roof solution, reducing maintenance costs opposed to maintaining the existing flat roofing system was also beneficial.
Initially Langley compiled a comprehensive client specification which comprised of the following design work;
• Plan and evaluations. • Existing and proposed drawings for planning. • Roof cores to existing roof to determine the construction and assembly. • Dead load and wind calculations to determine fixing pattern and pull out resistance. • Final drawings for the client’s approval.
The four symmetrical ’L shaped’ roofs posed an initial challenge to design. This was due to the different depths of each roof segment, which meant a varying ridge height. Careful consideration was needed, and the decision was made to move the centre line of the ridge, having minimal impact on the aesthetic look of the buildings.
Once the design of the roofs was confirmed with the client, Langley created final drawings which incorporated four designs. Four of the buildings were made up of two blocks that were joined by a podium that incorporated garages, which in total included eight roofs. Located on Bowes Road, these buildings were all identical and were assigned one FTP system design that incorporated the L shaped roof and the smaller square roof. There was also another building on Bowes Road that had a different design alongside another independent building that was situated on Cross Roads. There were three architype designs altogether for the buildings with FTP conversions.
Before progressing on with the steel framework for the FTP conversions, all six buildings had a minimum of one mains water tank on the existing system, the elimination of the mains water from the roofs made the tanks redundant. The decision was made to demolish the tanks, which meant
decontaminating them initially and then a highly stringent safety plan to remove the large concrete structures which posed a number of risks. Their removal meant that the roof’s pitch could be lower,
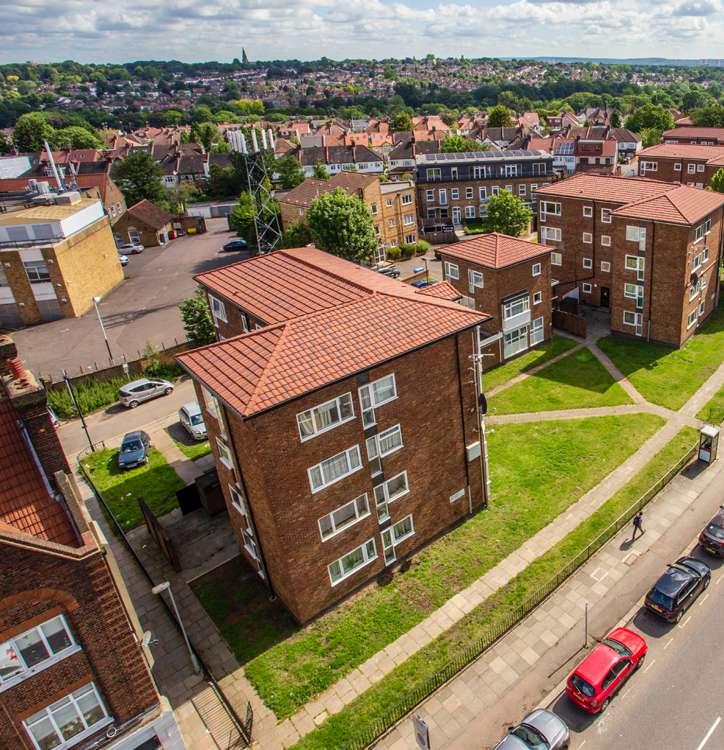
harmonised with surrounding buildings in the area and improving the aesthetic finish of the roofs.
The independent building on Bowes Road had existing elements within its flat roof that were initially problematic. Alongside the water tanks was a light well within the roof. It was a potential health and safety risk to those that require access to the newly constructed pitched roof void. This was overcome with hot rolled transfer steels designed by Langley to close off the light well. This allowed a reduction in height from which the ENGIE team of the FTP system were then able to work from.

Within the steel structure of the pitched roof, existing apertures were used to incorporate a new sun tube to allow natural light into the building and to maintain daylight savings—this was an opportunity to introduce a new automated passive smoke extract systems to the communal areas.
By using the existing apertures, it also meant reducing building and decorative works externally and internally for the client. This reduced
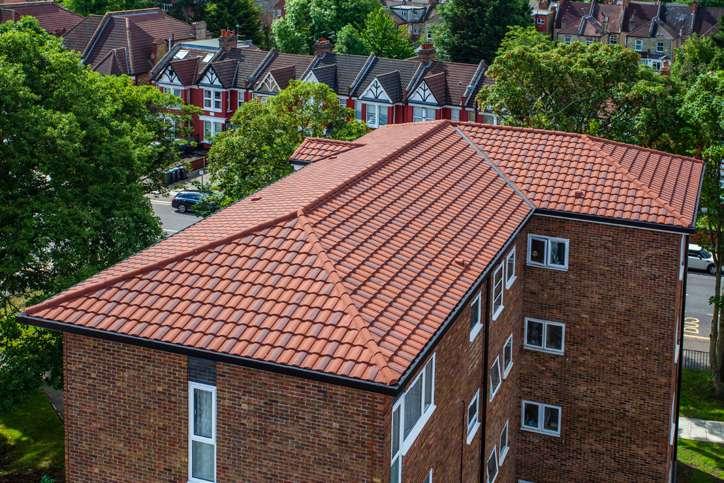
disturbance to residents living in the building which was occupied throughout the project.
A fire rated duct provided a sealed riser to the automated louvre mounted on a roof top kerb. The smoke louvre’s powder coated finish was matched with the predominate two-tone tile colour to reduce the visual impact on the roof-line.
As part of the wider refurbishment, Langley supported the refurbishment design of two buildings that had existing pitched felted roofs on Massey Close. After a comprehensive building and risk assessment, asbestos was removed at the verge and soffits and replaced with aluminium
components. The buildings were finished with Langley lightweight tiles, in keeping with the other refurbishments in the area. Sarah Primarolo, Architect at Playle & Parners LLP said ‘we have had a positive experience working with Langley on this project from design stages through to completion on site. The regular inspection correspondence and site progress photographs were particularly helpful’.
Chris Marlow, ENGIE Senior Quantity Surveyor said ‘ENGIE has, with the assistance of Langley, successfully delivered five, flat to pitch roof
conversions for our mutual client, the London Borough of Enfield on Bowes Road. From the inception of the scheme, the design team on behalf of Langley provided detailed design information and addressed any issues and obstacles with reasonable time-frames. Regular inspections and reports were carried out on site to ensure, in line with ENGIE management, that the required quality levels for the works were achieved.’
Once all the works were complete, Langley provided Enfield Council with their 20-year insurance backed guarantee that covers both materials and installation.
To find out more, we have a ‘Lightweight Structural Frames: Design and Installation Over Existing Flat Roofs’ online CPD Seminar available. To book contact enquiries@langley.co.uk Or visit,
www.langleystructures.co.uk
for more information about their services.