
20 minute read
Zentia ceilings 17 Wieland Electric
Zentia ceilings rise to the challenge in Plymouth
Sloping ceilings at a Plymouth primary school feature Zentia products.
Advertisement
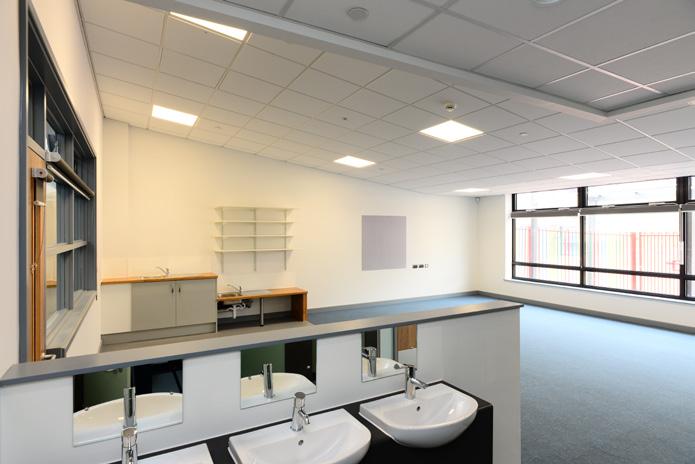
A new school for a new community in Plymouth has relied on ceiling solutions by leading UK manufacturer Zentia for delivering both form and function.
Some 1,200m2 of Zentia’s Perla OP 0.95 Tegular 600mm x 600mm tiles, which were the first mineral tile in the world to win Cradle to Cradle status, feature in the classrooms, offices, stores and communal areas at state-of-the-art Morley Meadows primary school.
Part of Persimmon Homes’ Saltram Meadows development in Plymstock, the £5.8 million primary school also features Zentia’s 100% humidity resistant Hydroboard 600mm x 600mm tiles with Prelude 24 non-corrosive grid in the kitchen, showers, toilets and changing areas.
Designed by Stride Treglown architects, and delivered by main contractor Halsall Construction, the two-form entry school accommodates 420 pupils, with part of it able to be cordoned off so it can be used by other community groups out of hours.
Specialist sub-contractor Vizion Interiors had a team of up to 10 on site for eight months, installing a total of 1,650m2 of the Zentia products on ceilings, that in the main part, unusually, sloped to degrees of 35® to mimic the sloping roof.
For form, the Perla OP 0.95 tile features a smooth, low-gloss monolithic visual with best-in-class fully painted edges for additional
Utility strikes and use of trenchless technology – using the bore hole created by removing the old pipe to install a replacement pipe
Simon Drain – CEO, Kobus
Utility strikes represent an ever-present threat to human life, yet, thousands occur each year in the UK, exposing workers to risks including electrocution and explosion. The issue is costly and disruptive as well as dangerous: with millions being subsequently spent rectifying the damage caused by ill-judged digging, not taking into account the environmental impact and at the very least, service delays to end customers.
There are over 12,000 works taking place every day across the UK, it is critical that we learn from near misses and lower consequence strikes to minimise the risk that workers are facing on a daily basis. The utility networks that run over our heads and below our feet extend to over 1.5 million km and are fundamental to daily life.
The Utility Strikes Damages Report, published by Utility Strike Avoidance Group (ASAG) found that over 2500 utility strikes took place across the UK in 2019, and that there is a necessary need for more robust survey practices to be put into place, and improved execution of works.
One organisation that exists to reduce this risk is Kobus which offers a trenchless technique for water and gas service pipe replacement.
Kobus technology uses the pathway of the existing service pipe thereby greatly minimises the risk of striking another utility, despite it being a trenchless method. If a pipe already exists, Kobus can use the bore hole created to install a new pipe as the old piping is removed, with a significantly less risk of damaging another utility.
Many leading global water companies and contractors have fully invested in Kobus technology, including Wessex Water and international operators in the US, Poland, and the Netherlands, after recognising the financial and safety benefits.
So, just how big an issue are pipe and cable strikes?
The underground utility infrastructure in the UK is vast and congested. Over four million excavations take place each year in Britain, and a 2017 industry survey shows that 44% of these took place with out a detailed examination for existing underground assets. With a lax approach being taken, the chances of strikes rise astronomically.
Taking a five-year period between 2013 and 2017 the rate of strikes rose by 668% from 162 to 1,244. Providing a headache for workers on the ground and local government officials responsible for the pipes and cables. Underground strikes between July and September last year jumped by a further 20% compared to 2019 with 2020 Q3 at 46% higher than the previous quarter.
The reason behind the upwards trend is hard to uncover. A survey released by the Energy Networks Association shows 93% of workers believe they operate safely whilst simultaneously 31% revealed they did not always check for underground cables before commencing the excavation.
Data from the Utility Strike Avoidance Group shows most strikes are caused by excavating machines. Furthermore, handheld tools such as pneumatic drills, shovels and crowbars also expose workers to avoidable danger.
There is an inherent risk involved with all pipes and cables. Whether they exist to distribute gas, electricity, water, cable TV, or sewage waste. Add individual property service lines to the mix and you are suddenly standing atop a variety of hazards which, thanks to oft times inaccurate historical maps can leave you in the dark.
Where does the solution lie? The ability to simultaneously pull decommissioned piping from the ground whilst installing new service pipes using the same bore path sounds like a dream. This is precisely what is on offer with Kobus’ Pipe Puller. old piping are removed from the ground avoiding a potential long-term degradation underground and added congestion. It is a trenchless, low-risk alternative that avoids much of the risks previously faced.
Better for the industry, better for the community

With the added mobility and efficiency of the pipe puller tool, work is faster and better for the environment as None of us truly enjoy having workers drilling outside the home. Loss of access, noisy machinery, potential damage to properties or gardens, there are many dangers involved and Ofwat and Ofgem are both increasingly challenging utility providers to improve their customer satisfaction when it comes to construction.
Community pressure for a more effective solution is just as strong as the need for the industry to innovate from within. Trenchless technologies are already a dominant feature of utility infrastructure maintenance. Needing just two small excavations disruption is minimised, roads can remain open and people are free to carry on with their lives.
On the industry side, Kobus is playing its part in driving towards Ofwat target of reducing leakage by 16% in this AMP period. Particularly because the pipe puller machinery removes rather than repairs which the industry is now embracing as the way to go.
Utility strikes are avoidable, preoperation mapping of existing utilities is the first step to a safer future, and a move away from moling towards the simultaneous pulling and laying of new pipes is the next step towards a future without strikes altogether.
Welcome back Matt
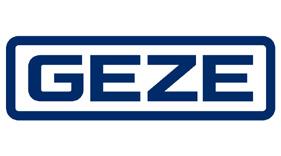
Matt will be responsible for assisting architects and specifiers with compliant solutions for all products in the GEZE range which includes automatic doors, window technology and manual overhead door controls.
In addition, he will produce detailed and risk assessed NBS specifications which are supported with BIM objects and present GEZE’s RIBA approved CPD to help architects and specifiers expand their knowledge.
Matt first joined GEZE in 2017 and after a spell outside the industry he returns to the company bringing with him extensive knowledge of entrance systems and automatic doors from his time as Automatic and Industrial door engineer and previous sales management experience. Said Matt ‘I am pleased to be back working with GEZE and their respected and varied product range, they have a strong brand and excellent reputation in the door industry. I look forward to working closely with architects and specifiers, creating strong collaborations with them and providing a quality service.’
Richard Richardson-Derry, National Specification Manager added ‘It’s great to be working with Matt again, he brings enthusiasm and extensive experience to the team. He will be an important part of the company’s continued growth.’
For more information about GEZE UK’s comprehensive range of automatic and manual door and window control products visit www .geze.co.uk
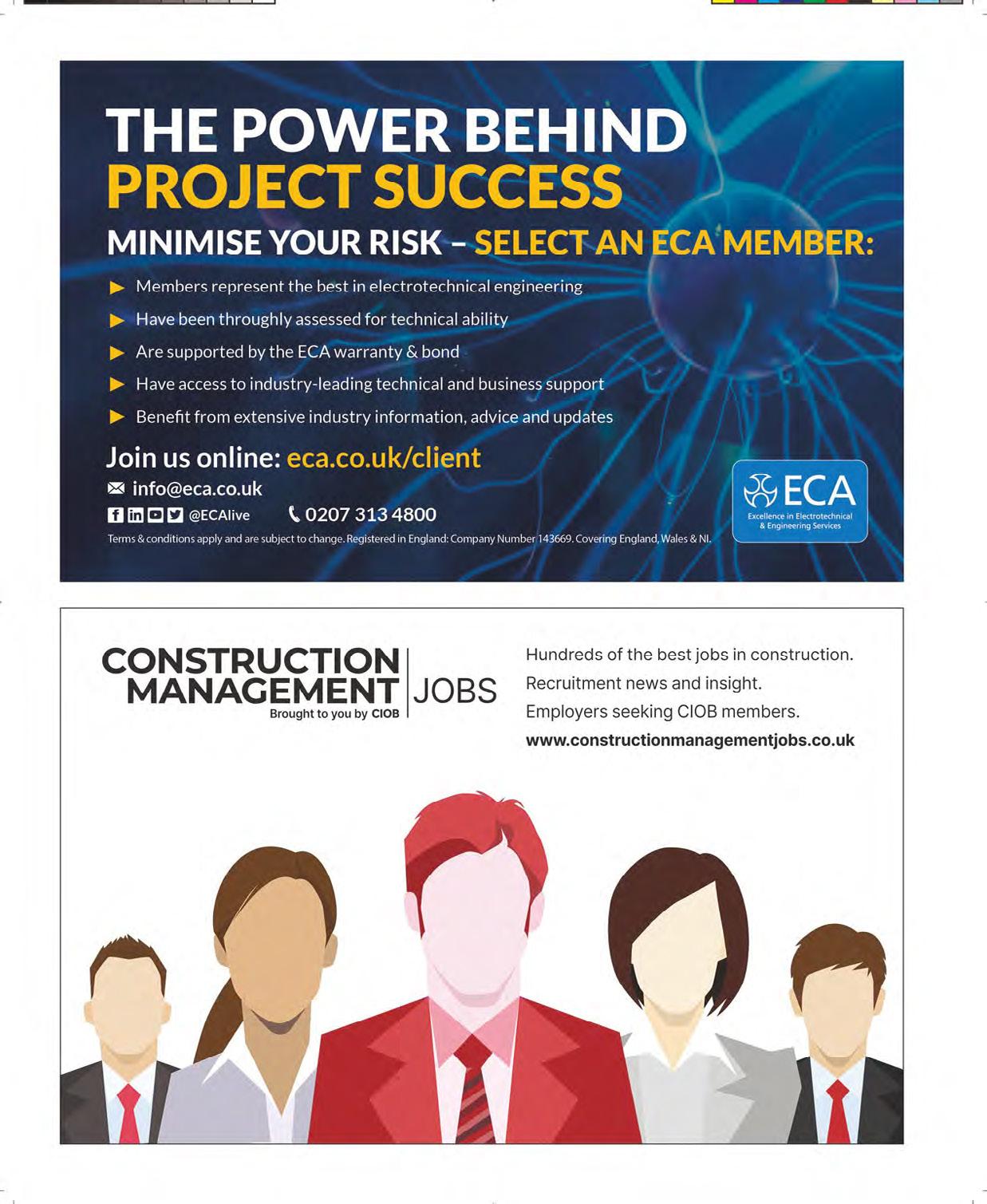
Gilberts helps create the right ambience at the Metquarter
Whether wanting American chicken and burgers to the delicacy of Asian cuisine, visitors to Liverpool’s newest and biggest food hall- GPO at Liverpool’s Metquarter- will be assured of a great atmosphere, thanks to the local air movement specialist with an international reputation, Gilberts.
Double deflection grilles from the Blackpool-based ventilation manufacturer have been fixed into the distinctive oval ducting running the length of the main food hall in the Metquarter. The grilles ensure a consistent flow of fresh air without draughts nor transfer of aromas from one zone to another from the 12 independent kitchens in the converted former General Post Office.
The strategy has been designed and installed by JD Engineering M&E contractor to the brief from development management company Queensberry and restauranteurs The Milestone Group.
The open plan 11,000 sq ft food hall with exposed building services limited available space into which to install the ventilation to ensure compliance with the diverse mix of needs.To balance ventilation, extraction and odour control requirements within the space constraints, JD Engineering proposed flat oval ducting to run the length of the retail area, with Gilberts GHV double deflection grilles strategically positioned along the sides. Adjustable blade dampers, fixed horizontally to the front and vertically to the rear of the grilles circulate the conditioned air. The design delivers 70% free ventilation area, deflecting incoming air vertically and horizontally to optimise rapid mixing and entrainment without draughts. The separate dishwash area is addressed via Gilberts GECA removeable core eggcrate grille. The WCs are served by Gilberts’ GX extract valves specifically designed for removing stale air from washrooms.
Explained a spokesperson for JD
Engineering, “Having 12 kitchens on one area, all providing very different styles of cuisine, was a challenge for the ventilation, to ensure the dining experience was pleasurable and not diluted by an influx of potentially conflicting aromas from other areas. The constraint in ceiling height added a further dimension to address. Gilberts’ grilles matched the requirements in terms of the requisite throw and air distribution we needed, and provided the quality and appearance requirements.”
Matt Bigland, Founder and Director
at The Milestone Group, added, “GPO will be a hub for Liverpool’s emerging food scene and will showcase the best in up-andcoming food and drink talent in the heart of Liverpool. It was critical therefore that we got the internal atmosphere right, and the ventilation has been a crucial component in creating a vibrant environment for diners.”
Founded 55 years ago, Gilberts is Britain’s leading independent air movement specialist, and is unique in its ability to develop components. Be it ‘mainstream’ or bespoke - entirely in-house, from initial design through tooling, production, testing and supply, at its 85,000 ft2 manufacturing facility. Its state of the art test centre, designed and built in-house, is one of the most technically advanced in the country.
CPA Installs Fall Protection at Aerospace Facility
Casper, Phillips & Associates Inc. (CPA) has designed and installed a bespoke fall protection system for a large commercial airplane supplier.
CPA was contracted to integrate it with 67 separate bridge cranes that vary in capacity from 34 tons to 40 tons and cover three million square feet. The galvanized chain-link (ASTM A392-07) installation allows crane operators and maintenance personnel to transition from a 90-ft.-high catwalk to crane bridge egress platforms without wearing personal protective equipment (PPE), which involved the timeconsuming process of attaching and disconnecting harnesses etc. Overall dimensions of the frames are 10 ft. 5 in. by 35 ft. 1 in.; the bridge girders are 12 ft. on center; and the chain link area is 7 ft. 6 in by 9 ft. 2 in.
Richard Phillips, mechanical engineer at CPA, said: “It was a
Before: This photo is taken from the factory (house) catwalks and is looking down to the bridge catwalk. There is a ladder from the bridge to the lower egress platform. voluntary upgrade. The bridge egress platforms were not previously equipped with fall protection. It’s not that the [safety] codes changed; the owner wanted to no longer require that workers be tied off. Maintenance personnel work at height to perform routine upkeep, such as greasing bearings, changing gearbox oil, and replacing the hoist wire rope. Crane operators access the bridges via catwalks and only use the egress platforms if the bridge or cab breaks down—or if there is an emergency.”
Phillips explained that the crane bridge spans vary between 100 ft. and 150 ft. Lift heights are all approximately 67 ft., he added. A low-weight solution was needed to not structurally impact the bridge and rail system. The CPA net frames offer the added benefit of allowing workers to see through them. A solid platform would have also been considered a working surface, which would have still required additional guarded edges for fall protection. The system was tested by dropping a 400-lb. sand bag from a height of 55 in.
The factory was divided into two halves—the old and new part of the factory. The new area had a frame system that slipped in around the existing egress platforms, while the older half required the existing egress platforms to be removed and new platforms integrated into the net frame. The old half had much shorter bridge bumpers and the net frame was designed to overlap from an adjacent bridge so the bridges could still go bumperto-bumper. No two net frames
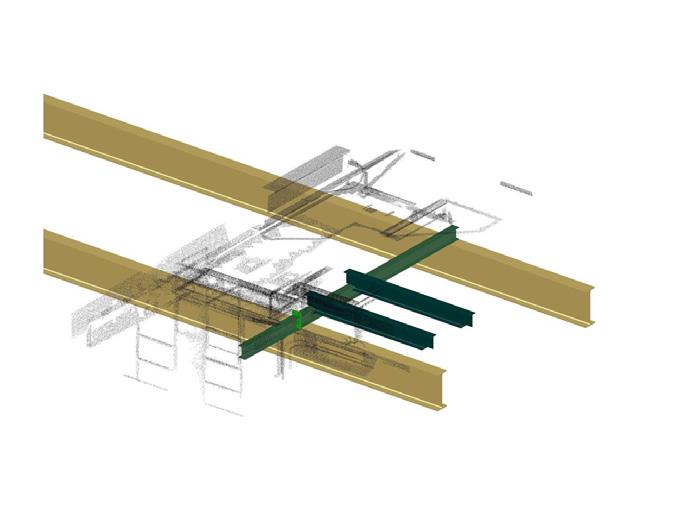
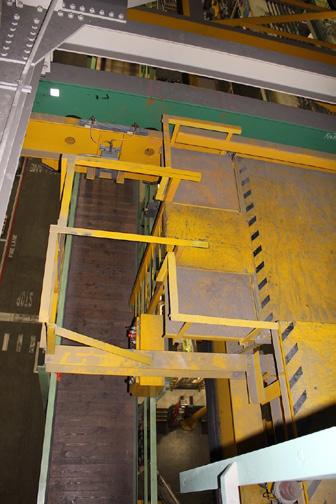
Cloud Data with Net and Frame: The point cloud data shows existing items. The net frame that goes around the egress platform is the new net frame.
across the factory were the same because conduit, junction boxes, lacing, and as-built egress locations varied from one bridge to another. The chain link to frame interface was consistent for all net frames.
3D scanning technology
Andrew Hanek, a civil engineer at CPA, said: “The project was unique because of the time constraints required to install the frame and no two bridges were alike. They all appear alike at first sight, but the location and orientation of limit switches etc. always changed. As-built conditions of things like the ladder and ladder cage changed or had angles mounted backwards. Space limitations were also a huge concern since the bridges still had to go bumper-to-bumper for picks and we had minimal clearance vertically with the roof truss system.”
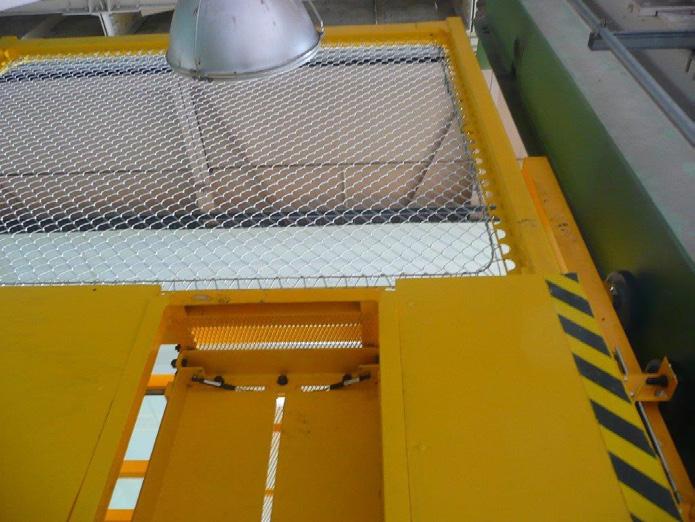
Many of these differences were either inadequately documented or not documented at all. CPA decided that the best path forward was to leverage handheld 3D scanning technology and scan all the cranes for these minor differences. CPA created a primary design that could be slightly modified to fit each crane without any costly interferences. As Phillips said, “A minute in the shop is worth five
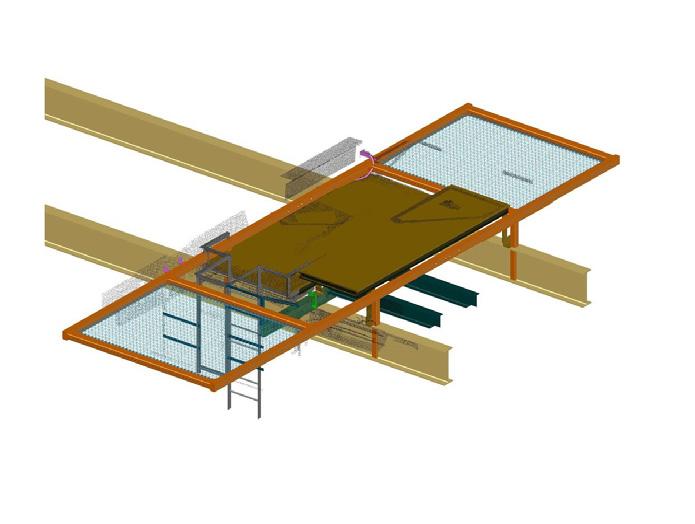
Installed: The installation allows crane operators and maintenance personnel to transition from a 90-ft.-high catwalk to crane bridge egress platforms without PPE.
Point Cloud Data: CPA decided to reference the point clouds to the bridge girder and assume that the 12-ft. on center spacing was precise.
minutes in the field so it was very important that everything dropped in and fit to minimize downtime.”
The bridges were scanned from the bridge and factory catwalks, a maintenance trolley for areas between the bridge girders, and the top of the egress platforms. The top of the platforms did not have a lot of unique features so stitching the point clouds across the platform did not give good results. CPA decided to reference the point clouds to the bridge girder and assume that the 12-ft. on center spacing was precise. This method, combined with photos, allowed CPA to identify all features of concern to work around.
The majority of point cloud scanning and data processing into 3D was performed by Hanek.
Installing the bespoke fall protection system
“The first few bridges were a learning curve,” Hanek acknowledged, “But the installation crew eventually got it down to the entire process for a single bridge being performed in a 12-hour window. Net frames were fabricated and staged ahead of time so they could be hoisted into place and installed. If needed, relocation of electrical conduit and junction boxes was performed prior to the frame installation. The short install time was a huge success since production was not able to lose bridges for days at a time. All work was performed between shifts and pick moves while the factory remained at full production.
The relevant safety code for the galvanized chain-link installation is Chapter 296-155 WAC Construction Work.
www.casperphillips.com
Yanmar Compact Equipment’s new premium red machines pave the way to a new era
Yanmar Compact Equipment has adopted an eye-catching Premium Red paint colour across all its machines globally.
Premium Red machines were first introduced onto the North American market in 2020, and this roll out sees Yanmar’s EMEA (Europe, Middle East, Africa), AOLA (Asia excl. Japan, Oceania, Latin America) and Japanese markets completing the metamorphosis. The new Premium Red paint colour brings Yanmar’s compact equipment in-line with Yanmar Group’s image.
“Our dealers and our customers really like the new colour,” commented Jeff Pate,
Sales Director, Yanmar Compact
Equipment North America. “Everyone feels that Premium Red attracts attention on the jobsite, and just as the quality and reliability of our products stand out from the competition, in a sea of yellow competitive machines in North America, our Premium Red colour stands out too.”
But this shift from the well-known Yanmar yellow is more than simply a cosmetic colour change. For Yanmar Compact Equipment, the symbolism of this change resonates on a deeper level.
“Yanmar Compact Equipment is on a journey of transformation,” explains CEO, Giuliano Parodi. “We aim to be a global leader in Compact Equipment and, with the help of our dealer partners, deliver sustainable business solutions for our customers and the societies in which they operate.
“Our acquisitions of the past few years are now fully integrated into a harmonised, Yanmar CE way of working, with common processes and customer focus right across our enlarged product and services portfolio. For us, Premium Red sends out a clear signal that we are one company, with a clear product strategy. But our transformation goes far beyond our machines. Indeed, we are challenging the way we think and the way we work, to transform our products, our business, and our brand to create even more value for our customers.”
In product transformation, Yanmar CE is currently evaluating several alternative fuel and powertrain technologies and recently unveiled its first electric mini excavator prototype, the new SV17e. Proudly featuring the new Premium Red colour, the SV17e is aimed at customers in the European market in the 1.5 to 2.0 tonnes segment.
Director Channel and Brand
Development. “We have the ambition to be a leader, not only in machines but in the customer experience too and are working hard to get closer to our customers to identify new and innovative ways in which we can add value to them.”
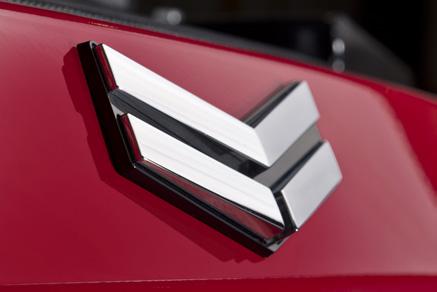
“Our prototype is significant because it demonstrates our capability to bring the quality and reliability of our highly respected conventional engine technology into the arena of electrification,”
explained Director Product Management EMEA, Cedric Durand.
In business transformation, Yanmar Compact Equipment is continuing to invest in manufacturing infrastructure and in expanding their global dealer network to increase the proximity to customers, reduce lead times and improve service. Closely linked to these investments is the focus on creating an amazing customer experience.
“Our move to Premium Red across our machines certainly signals a change and we are confident that our customers will start to see other changes too,”
explained Elsie De Nys, Global
The change to the new Premium Red also heralds a new confidence in the Yanmar Compact Equipment brand and coincides with the launch of its new tagline, ‘Together We Build’.
“Our aim, together with our dealer partners, is to build stronger relationships and create even greater customer value,” said CEO, Giuliano Parodi. “Together We Build’ really underlines our commitment to transforming Yanmar CE and, with the help of our dealers, to focus on creating a new and exciting experience for our customers.”
For Yanmar Compact Equipment, change is in the air and the fresh, new image of the Premium Red machines certainly reflects the optimism running through the business. This milestone moment is about shared goals and ambitions and about building a better future for everyone.
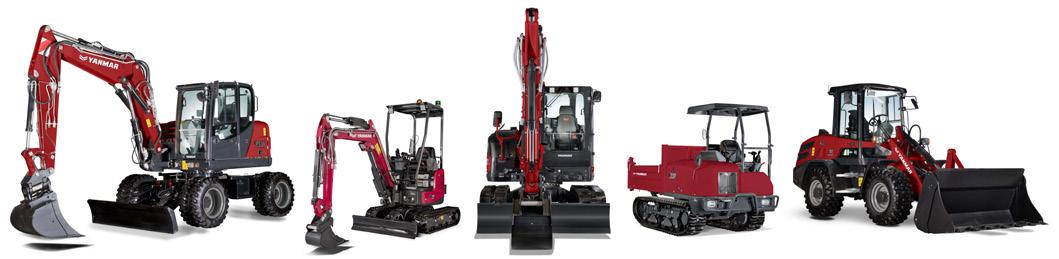
February 2022
First of its kind
made possible within the Bucket Bundie range.
- Diesel And AdBlue Bucket Bundie for J A Jackson
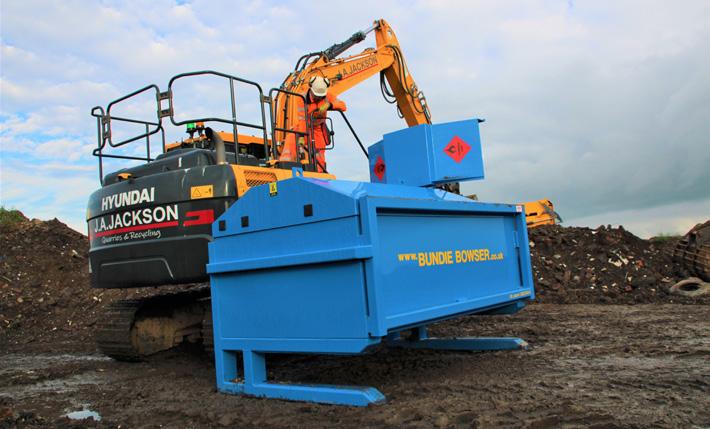
Established in 1967, J A Jackson Quarries & Recycling Ltd are a family run business who supply quarried and recycled aggregates. Providers of sustainable building materials, aggregates and ready-mix concrete, the company also provide domestic and commercial skip hire and have a fully licenced waste transfer station and facilities for inert tipping. J A Jackson operates a fleet of more than 20 tippers, artics, skip wagons and concrete mixers.
The company’s quarries in Preston,
Leyland and Lancaster are all within easy reach of the region’s motorway network making access and distribution as efficient and effective as possible.
J A Jackson have recently added the first combined Diesel / AdBlue
Bucket Bundie Fuel Bowser to their fleet provided by manufacturers,
Ace Plant.
Ace Plant, home of the ‘Bundie Bowser’ fuel storage range, are a plant hire and sales company based in Buckinghamshire who utilise their engineering roots to manufacture Fuel Storage Solutions and Dust Suppression equipment for hire and sale throughout the UK. Based on the same concept as the patented Bucket Bundie Fuel Bowser, Ace Plant’s Bucket Bundie Store was seen shortlisted in the Institute of Quarrying’s Excellence Awards in the knowledge and innovation category - a fantastic accolade for the ‘Bundie Bowser’ name.
Ace Plant have recently launched the first Bucket Bundie that is capable of carrying both Diesel and AdBlue at the same time. This capability can already be seen in Ace Plant’s static, site tow and road tow ranges but has finally been J A Jackson first found out about the Ace Plant Bucket Bundie Bowser after searching the internet about fuel bowsers. They liked the fact that the Bucket Bundie can be transported by existing site machinery without the need for a tractor. These units remove the need for lifting chains as well as the need for the operator to leave the safety of the machine’s cab to attach any chains. It features a patented bucket loading system with special slots above the support legs that allow a wheel loader operator to easily pick up and move the bowser using the machine’s front bucket. With the loader bucket crowded back, the Bucket Bundie is held securely for safe transport across rough ground – this combination works much better than a towed bowser which can be difficult to move and reverse – particularly on rough terrain. J A Jackson say that the Bucket Bundie will be a benefit to their business as the unit will result in “less risk of contamination and we no longer need to use the 5 gallon drums”. In turn, this also makes refuelling a faster and safer processes with less risk of spillage. The Bucket Bundie Bowser is available in three different capacities: 450L, 1000L & 2250L.
To find out more visit www.aceplant.co.uk or call 01908 562191.
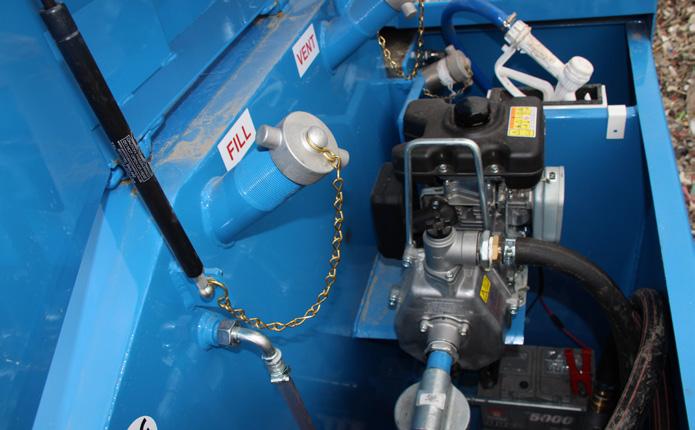