
27 minute read
Bond It
Safe in the knowledge
Effective performance is everything when it comes to fire safety products. However, without knowing it, many of us could be making compromises when it comes to our choice of fire foams and fire rated silicones.
Advertisement
As a company that manufactures sealants, adhesives and other building chemicals, you might expect us to advocate increased awareness when it comes to choosing fire foams. But self-gain never has, and never will, be Bond It’s main motivation for urging greater consideration when it comes to these products. Instead we believe the building industry in the UK is affected by a serious issue with equally serious, and potentially life-threatening, implications. With lives at stake, and against a backdrop where we are all increasingly accountable for our work and where they have been a number of high profile examples of poor building practices contributing to the spread of fire, we see it as our responsibility to share our knowledge. The problem stems from the existence of too many different but similar sounding classification systems. This has created a degree of confusion which has left many in the sector at risk of inadvertently using fire foams with levels of performance that fall woefully short of the mark.
Not all fire foams are created equal
Years ago specifying a fire foam was a lot simpler and arguably safer than it is today. You had the choice of either a standard foam or a fire foam with both types available in either a gun or handheld form.
To benefit from its classification, fire foam had to comply with BS476 part 20. This meant it would act as a barrier to fire for 4 hours giving a building’s occupants vital time to escape. Then, with an influx of European foams into the UK came a proliferation of different standards. The most widespread was a German standard based on a sliding scale. This ranged from A1 (100% non-combustible) through to A2, B1, B2 and B3 with the latter offering the worst levels of performance. If the introduction of a whole new standard system and a large number of differing classifications didn’t serve to create enough confusion, the way of assessing the UK and European standards was also totally different. The UK standard meant a fire foam had to act as a barrier to prevent fire transferring from one room to another for a period of four hours. The German standard meanwhile was based on someone trying to ignite the foam itself - not a very realistic scenario.
Savings - but at what cost?
One of the most widely seen classifications people now find on fire foams is B2 and it’s not hard to understand why. B2 strikes a fine balance between offering some fire resistance and at a cost that won’t hurt budgets – or margins. However, in our opinion, B2 ‘fire’ foam’s performance is totally inadequate and we don’t think it should be sold as fire foam at all. Yes, there are savings and profits to be made, but at the end of the day, what price do you put on property or even more poignantly, on someone’s life? As we near the 4th anniversary of the Grenfell Tower fire, we are hoping lessons have been learnt.


Like most of our competitors, we react to market demand and do supply a B2 PU foam as part of our range. However, we are strict about this not being referred to as a “fire” foam and it is not marketing under this guise at all. We clearly state what the products performance characteristics are and what it is tested to.
Silicone sealants also play a big part in ensuring the integrity of fire resistant seals and joints. These are used in reestablishing the fire-rated integrity of a wall or floor assembly compromised by the inclusion or exclusion of a penetrant. Flames and smoke can spread through the smallest of gaps causing extreme damage to buildings and even human lives. Applying an intumescent sealant to linear joints, around pipes and between cables to close all the gaps and add fire resistance.
An intumescent seal slows down the burning process and does not contribute to spread of flames. Therefore, it can minimize the damage by protecting structures, giving fire fighters more time to arrive and take the fire under control as well as fireproofing escape routes allowing for efficient evacuation.
How does intumescent sealant work?
Intumescent seals are known as means of passive fire protection, but what is an intumescent sealant in practice? Also known as expansion sealant, intumescent sealant expands when it becomes exposed to extreme heat and can swell up to 40 times its original volume. The sealant increases in volume but decreases in density forming a char layer. The expanded sealant does not actually catch fire, but the char burns eventually, still much more slowly than most building materials. Depending on the product formulation, application and backing material, an intumescent sealant can be resistant to fire for up to 4 hours. Buildings require different levels of fire resistance depending on their size and whether they have a residential purpose.
Better safe than sorry
Of course, it would be remiss of Bond It to highlight an issue as grave as current fire foam classification and misclassification without proposing a solution. Thankfully, there is one - and it’s also fairly easy to implement.
In its simplest terms, our advice would in every circumstance if you need fire protection from your foams nothing less than B1 is really acceptable as a bare minimum standard and for silicones we would recommend a fire tested sealant. Look for the standards EN1366-4, EN1366-3, EN ISO 10140-2 and EN13501-2 on packs - which are proof that the foams and sealants will do their job and you can be safe in the knowledge that you’ve chosen a true fire foam or fire rated sealant that will leave people safe in their homes, offices and other buildings.
For more information on Bond Its Fire Rated products contact our Sales Office on 01422 315300 or visit www.bonditgroup.com.
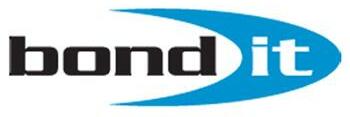
DECADES OF INNOVATION
in the palm of your hand
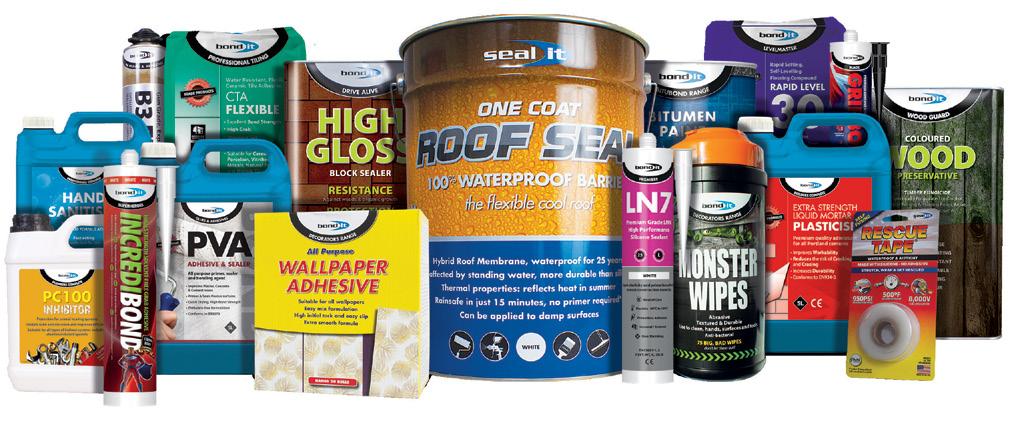
Head Office: Unit G16, River Bank Way, Lowfields Business Park, Elland, West Yorkshire HX5 9DN Tel: +44(0)1422 315300, Email: salesuk@bonditgroup.com, www.bonditgroup.com
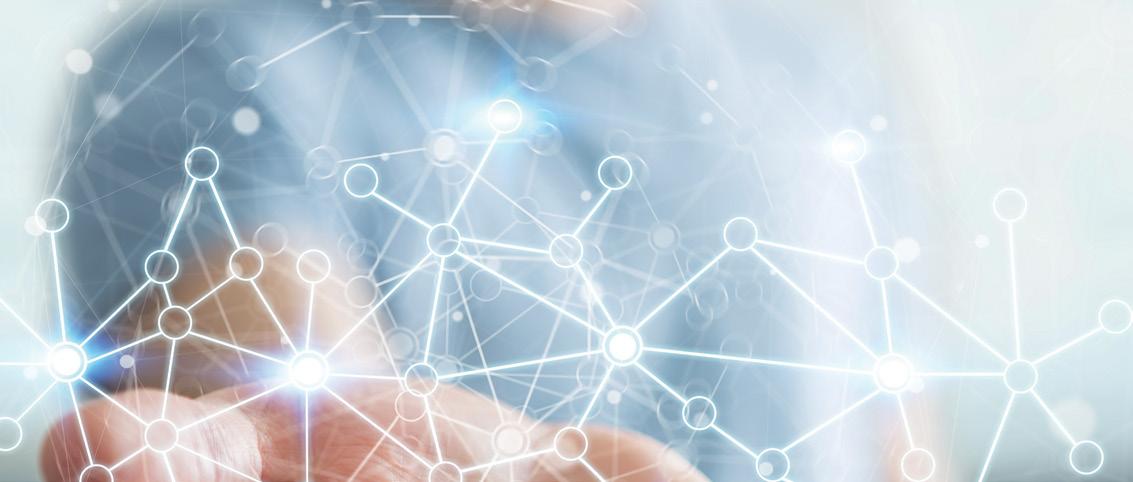
Carbon Neutral Buildings Today
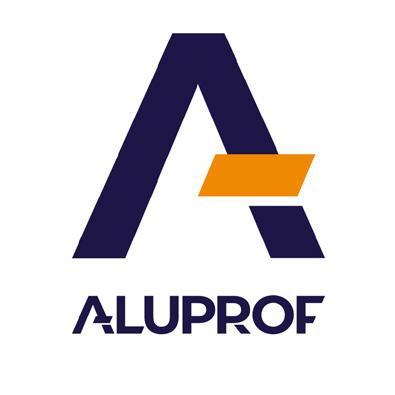
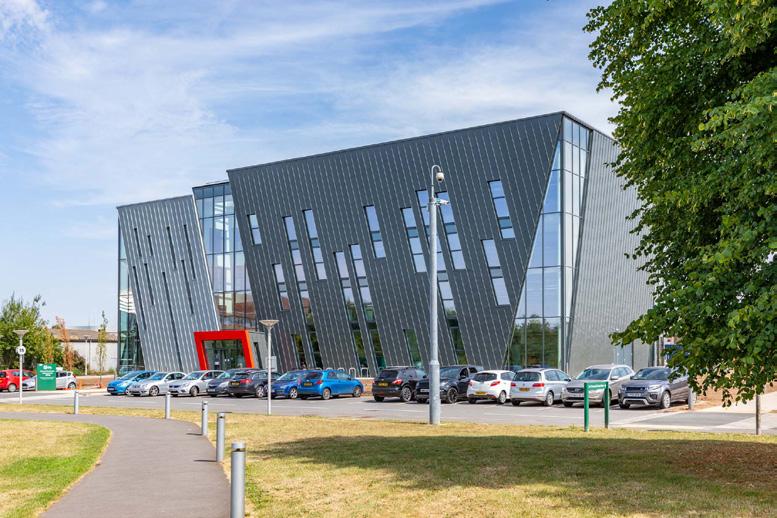
by Wojciech Brozyna - MD of Aluprof UK
There is a real benefit of living and working in a ‘Carbon Neutral’ home or office. Not only are the rising energy costs for space heating eliminated, but the living and working environment can actually be improved, which significantly reflects on our well-being. This is not a utopian vision of the future, we have had the ability to source sustainable materials and build this way for some years, but have chosen to remain with our traditional construction. Change is now urgently needed to enable sustainable living for everyone, it is captured in the Passivhaus concept, something that we should all be working towards.
The history of Passivhaus
As far back as 1982, American physicist William Shurcliff published a book “The Saunders-Shrewsbury House,” in which he describes the concepts of “superinsulation” and passive solar as “passive house.” In the late 1980s a passive house movement had emerged in North America, but, shortly after America lost its appetite for energy conservation and Germany picked up the reins. German physicist Wolfgang Feist refined the passive house concept to further improve efficiency and proposed a passive house concept with an annual heating demand of just 15 kilowatt-hours per square metre of floor area. Considered as the most rigorous standard in energy efficiency today, the Passivhaus-Institute, founded in Darmstadt in Germany in September 1996, continues to promote and control the Passivhaus standards. Today over twenty-nine thousand buildings have been certified according to the strict Passive House Institute certification criteria, representing a total floor area of almost twentyseven thousand square metres. In the UK we currently have over three hundred completed Passivhaus certified projects, with a further two hundred and twenty under construction.
Five key elements of Passivhaus
There are five key elements to understand about Passivhaus before starting to look at the technical requirements. First and foremost, Passivhaus is fundamentally about integrated design where the whole building team are involved at the outset. Whilst it may seem that Passivhaus is designed just for northern climates, the second key element is information about location, as well designed Passivhaus structure can now effectively be installed anywhere in the world. Orientation, the third key element, has a part to play in ensuring that solar heat gains are optimised. The fourth key element, is the building form, whilst a Passivhaus construction can take any form, physics confirms that with a convoluted shape, with a resulting greater surface area for a given space, will allow more heat loss. Finally, the fifth element is that of the construction system itself. Passivhaus is a fabric first approach and whilst any material can be utilised, the focus on airtightness and thermal insulation are paramount. Thermal bridges are to be avoided at all costs to maximise keeping the heat in, and of course, in certain climates and various times of the year, also keeping the heat out. It is the building fabric that does all the heavy work in Passivhaus design.
Included in the design is the crucial element of fresh outdoor air being circulated inside being warmed with an efficient heat recovery system, warm air going out heating up the cold air coming in, so that energy consumption is kept at a bare minimum. The best use of natural daylight, including some solar gain, further enhances the energy savings in this unique form of construction.
Design criteria
Designing high insulation wall elements can be relatively straightforward, but when these elements are perforated by windows and doors, robust detailing is needed to minimise thermal bridging and maximise air tightness. Window and door systems chosen must offer the highest levels of thermal insulation including the adoption of triple and quadruple glazing. Few systems meet these high performance characteristics, most are supplied from aluminium systems companies with wide, high performance thermal breaks. Aluprof, one Europes leading aluminium systems companies, offer a range of systems that can be specified by architects to meet the requirements of Passivhaus design.
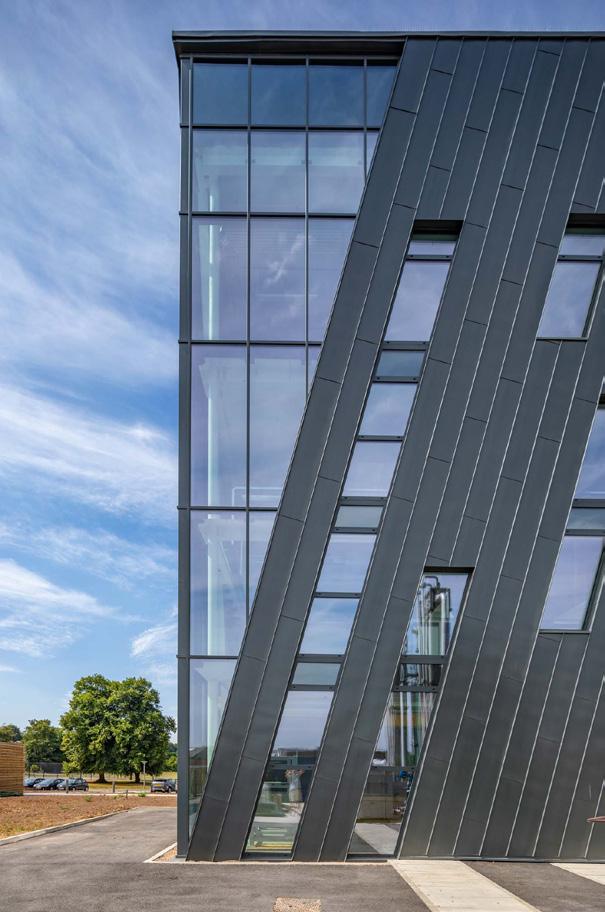
With Aluprof’s MB-104 system, both windows and doors can confidently be specified as the system has gained the Passivhaus Institute Darmstadt certification. The MB-104 Passive Aero has excellent thermal insulation performance for an openable window system with a Uw as low as 0.53 W// m2K and for a door a UD as low as 0.62 W//m2K. With glazing widths up to a class leading 81mm in thickness, the doors can also be assembled into panel doors as well as fully glazed. Passivhaus, by its name, suggests that the construction is just for dwellings. A recent project completed, the 2,500m2 research facility for the University of Nottingham, provides laboratory, office and support accommodation for the UK Government Energy Research Acceleration Initiative. The project is known as the ‘RAD’ Building (research acceleration and demonstration) on the Jubilee campus. The building was constructed by Robert Woodhead Construction of Nottingham and has been designed to achieve BREEAM Excellent and includes further extensive Passivhaus measures to reduce energy requirements. High performance window, curtain wall and door systems from Aluprof have been used throughout the building offering very high levels of insulation. Fabricator and installer, Commercial Systems International of Humberside, used MB-TT50 curtain wall and MB-104 windows from Aluprof which carry certification from Passivhaus. On completion the building has been extensively tested and has gained the coveted Passivhaus certification.
So why involve a systems provider?
At the design concept it is crucial that the right product is specified along with detailing to ensure that the building will meet Passivhaus standards. Aluprof can assist in product choice, often tailoring the system chosen to offer the best specification for its location. The tech team at Aluprof can also offering assistance in the reveal detailing, which will minimise any cold bridging in the interface between the building fabric and window system. Since setting up the Aluprof Office at the Business Design Centre in London, the company has rapidly grown their specification influence in the UK with their high performance architectural aluminium systems. Further expansion of the company’s’ headquarters in Altrincham now provides specifiers with meeting facilities and an extensive showroom of commercial systems to view. With overseas growth across Europe spreading into the Middle East and firm roots already in the East of the USA, the company is becoming a global player in facade supply.
Further information is available on the company’s website at aluprof.co.uk or direct from their UK office in Altrincham on 0161 941 4005.
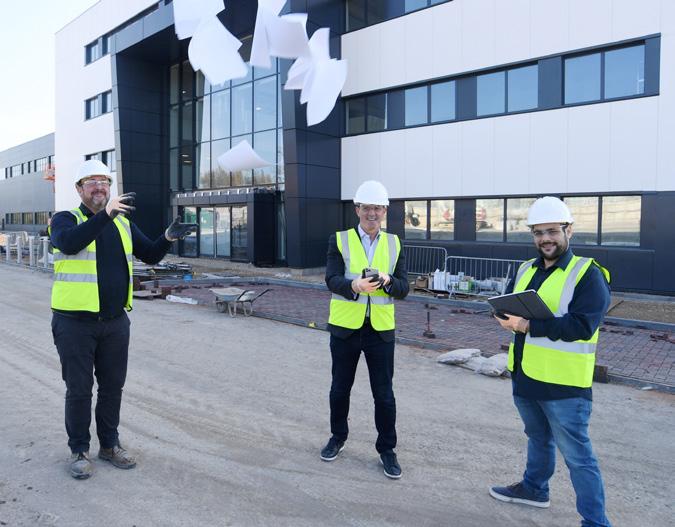
A smartphone app which allows construction companies to access and track all their compliance and safety paperwork in one place has been officially launched.
‘Under Construction’ – created by Coventry-based digital design company Apps Plus (the App division of Image+ Limited) – enables construction firms of any size to easily store, track and fill out key forms relating to their SHEQ (Safety, Health, Environment, Quality) requirements, such as SSOWs, operative certificates and risk assessments. ‘Under Construction’ – created by Coventry-based digital design company Apps Plus (the App division of Image+ Limited) – enables construction firms of any size to easily store, track and fill out key forms relating to their SHEQ (Safety, Health, Environment, Quality) requirements, such as SSOWs, operative certificates and risk assessments.
The app also allows site managers to streamline project management, allowing them to view updates on progress in real time when workers submit status reports. All documents can be shared with a firm’s principal contractor at any time, saving both parties having to put together the paperwork and travel between sites to assess it.
Notifications can also be sent to users alerting them to any issues, such as safety certificate expiration dates being sent to supervisors far enough in advance for them to address them.
Under Construction was refined by Apps Plus after Birmingham-based construction firm Gridlocked – which specialises in installing ceiling and partition systems in a wide variety of buildings - used the app for several months, and is now ready for the wider market to download and use.
Since using Under Construction, Gridlocked noticed a significant improvement across all its SHEQ responsibilities, operations, performance and evidential record keeping. Craig Buglass at Gridlocked said: “An app like this for construction companies like us has been long overdue in my opinion. “Construction is still one of the most dangerous sectors of employment in this country, so we are always looking to improve on how we process, control and manage risks associated with our specific trade.
“The Under Construction app comprehensively enhanced all our safety, health and wellbeing, quality and environmental aspect requirements and was all wrapped up in a user-friendly way. It’s fast, reliable and a pleasure to use.
From left: Craig Buglass, Alan Hartin, and Joao Matos (Image+)
“We have also been extremely impressed with the approach from the Image+ team to adapt this system to suit our every need.” When a firm downloads the app, it may not have all the forms it needs for a given project. Managers can send Image+ the forms it needs to use, and they will tailor the app to store and track those specific forms for that project. Alan Hartin, Managing Director at Image+, said: “Under Construction will be unique for each construction company that uses it. “Every site and project will be slightly different, so we handle the first step of tweaking the app for each user so the forms they need are included within it. far easier for managers to keep track of everything instead of filling out paperwork the oldfashioned way. “It gives peace of mind to construction managers that their SHEQ responsibilities are being taken care of, and it also saves time and money by giving them an easy way to share key paperwork with their principal contractors at any time. “We would encourage any construction firms looking to increase their efficiency to get in touch.”
Anyone looking to download Under Construction can find it on the App Store or Google Play with more information at
www.underconstruction.co.uk
Alternatively, contact Image+ on 024 7683 4780
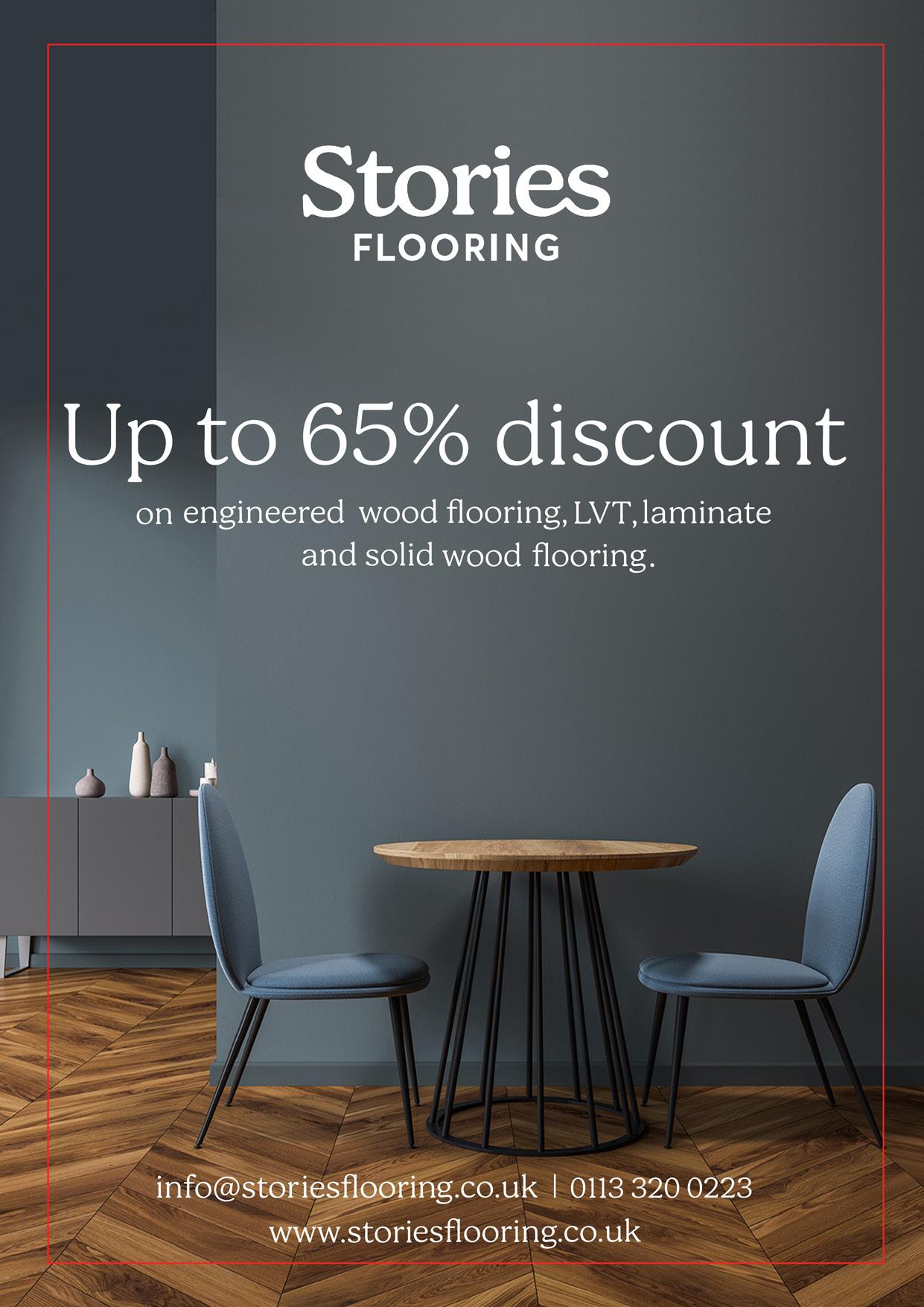
CUT COSTS, NOT CORNERS
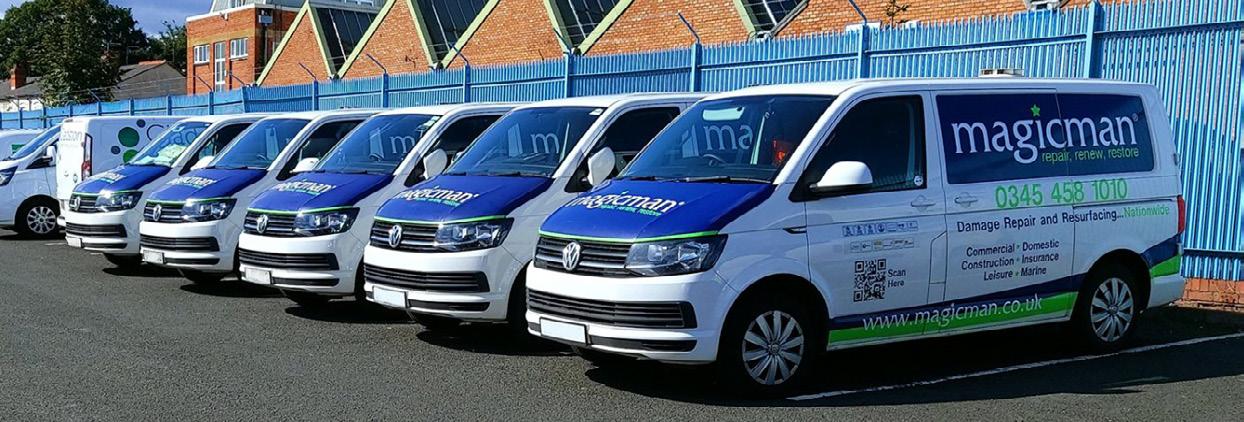
Your building project is near completion. You are feeling confident in your plans to mitigate risks that might derail your handover date. Yet one circumstance, snagging, is often an afterthought and under-budgeted despite being completely foreseeable. All because it takes place in the final phase of the building process. Accidental or so-called ‘unexpected’ damage is a normal part of the rough and tumble of the build and rectifying it is not only the responsibility of the builder but is essential to meet the expectations of your client. Only during the snagging inspection does the scale of remedies required become apparent as well as the urge to cut corners and rush repairs.
It is imperative that snagging issues are remedied promptly and to a standard that assists you to handover to client ‘defect free’. Your odds of achieving that successfully and without financial penalties are greatly enhanced by choosing the right supplier. Magicman has the skill sets, staff numbers and longevity to ensure you can book far in advance with full confidence. Each Magicman repair technician is trained to repair any form of damage to all hard surfaces. This includes accidental damage, wear and tear, vandalism, poor workmanship due to labour shortages or labour quality and perhaps unsurprisingly, the unsuccessful repairs of others. Our technicians arrive on site fully prepared. They carry with them all the kit necessary to carry out any and all repairs that our customers require. This includes multiple types of repairs to many different substrates within one booking, leading to greater time and cost efficiencies. Many contractors are simply unaware of the quality of restoration work achievable today and of the environmental benefits or repairing in-situ over sourcing and installing replacement. Smart operators utilise Magicman when carrying out refurbs in order to restore items that are perfectly serviceable but are showing their age. This allows their clients to divert cost saving to other areas and, by reducing waste, contribute to environmental targets.
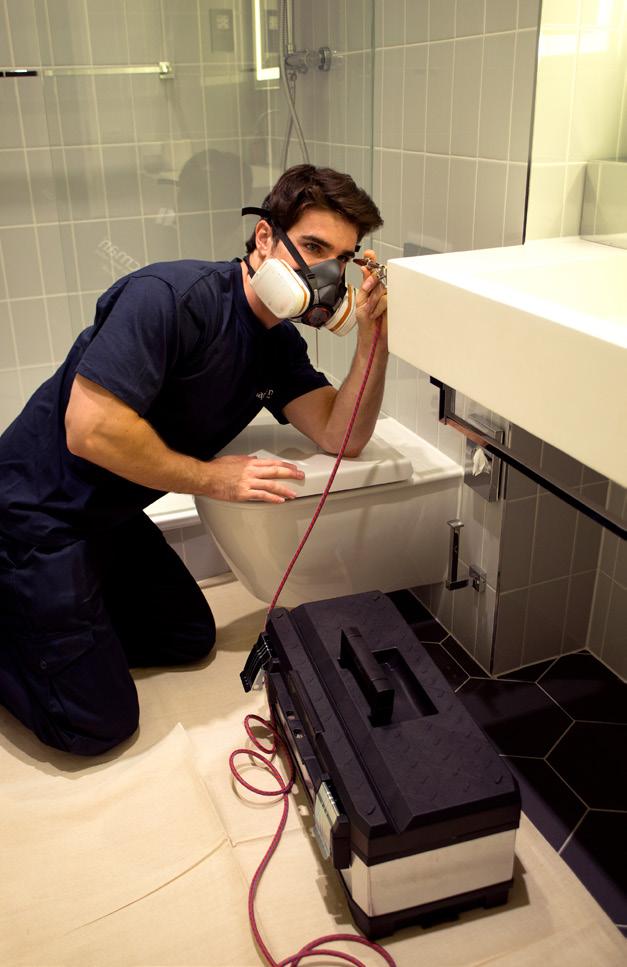
Magicman research and develop products to ensure their repairs are permanent and match not only the visible exterior but also the substrate of the items they restore. A truly sustainable solution.”
- Mark Henderson, CEO Magicman Group
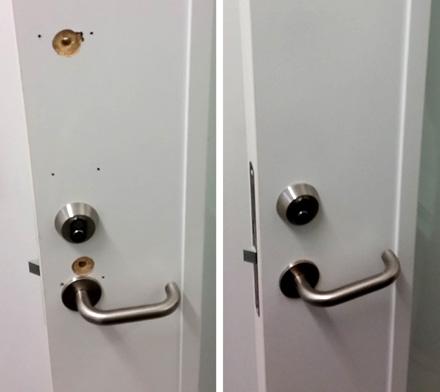
Above: before and after shots of door restoration by Magicman.
Early intervention and collaboration with Magicman means an end to rushed paperwork. Framework agreements between main and subcontractors are available on an annual basis.
Magicman invest in training, health and safety standards and fully audited certification including ISO 9001, 14001 and 45001. Other accreditations include Worksafe Contractor, Constructionline, CHAS, Safemark, Achilles and Builder’s Profile.
As the originator of on-site repairs almost 30 years ago, Magicman have had to create and develop their own training programme which is only open to future employees (conditional on a successful graduation from the course). Our programme prioritises the quality of repairs and health and safety standards as well as customer service, through an extensive 5 week course at our residential Training Academy in Sussex. Trainees learn all Magicman repair and restoration techniques to all hard surfaces including wood, laminate, uPVC, powdercoat, ceramics, vitreous china, marble, stone and brick. We teach perfect colour matching by eye and offer glass polishing as an additional service to remove scratches and graffiti. Early notification of surface colour and texture requirements such as RAL numbers means we can respond even faster.
For a no-obligation quote, please contact 0345 458 1010 or email your snagging list to enquiries@magicman.co.uk. Site visits are also available.
Gilberts is supporting Conlon Construction enabling Lancashire Constabulary to deliver facilities and services that are fit for purpose in line with changing laws.
The Blackpool ventilation manufacturer has supplied more than 300 air movement and control units for the refurbishment of Skelmersdale Police Station. The project follows Gilberts’ provision of similar for one of the Constabulary’s main Operating Centres two years ago. The Skelmersdale refurbishment is being undertaken by Conlon Construction supported by Pick Everard and James Mercer Group Mechanical Engineers. In addition to upgrading the façade, the interior is being remodelled and upgraded to create efficient, collaborative spaces appropriate for current and future policing requirements. As part of its works, James Mercer has installed Gilberts’ GSFE circular swirl diffusers and GECA eggcrate grilles at all levels throughout the building, to provide dedicated supply and extract airflow. The general air movement units are complimented by Gilberts’ Firegard FG2 and FG3 high velocity ductwork smoke and fire dampers and DUC fire dampers rated to deliver up to four hours’ protection against penetration of smoke and fire, managed by some 80 control modules.
Gilberts’ GSFA circular swirl diffusers will rapidly deliver fresh air into all conditioned spaces. The omni-directional swirl effect discharge is projected horizontally for rapid entrainment and intermixing. Gilberts’ GECA eggcrate grilles extract the used air with 90 per centfree ventilation area. Gilberts’ Firegard curtain dampers feature bespoke angled locking ramps to ensure full blade closure to prevent the spread of flames through ductwork, providing a solid barrier to fire and smoke for up to four hours. Ductgard engineered smoke and fire dampers adjoin the fire barrier wall, and fully close automatically. In addition to manufacture, Gilberts has unrivalled technical support capability, including Computation Fluid Dynamics modelling software and a full inhouse test laboratory at its 95000 sq ft head office, backed up by a heritage spanning 60 years. Commented Michael Conlon, chairman of Conlon Construction: “The Constabulary is keen to promote the concept of Backing Lancashire. We concentrated on making use of the local supply chain, to ensure efficient use of resources, value for money and to ensure we deliver a lasting legacy beyond the build. Our focus has been to create a scheme that ensures Skelmersdale Police has the right working environment to provide a firstclass service to the public.” Cristina Marshall Head of Estates, Fleet and Facilities Management for Lancashire Constabulary added: “Our social value policy ensures that all resources are used wisely, whilst ensuring the efficient use of resources and delivery of value for money.” The station is due to reopen in late 2021.
Lotus School is a first in more ways than one….
The opening of the Lotus School in Blackpool is a first in more ways than one. It is the first purpose-built social environmental mental health school in the area. It is also the first in the area to be fitted with the first COVIDcompliant hybrid ventilation.
The £4.5m project, funded by the Department of Education’s Free Schools Funds for Special Education Provision, was commissioned through self-delivery by Blackpool Local Educational Partnership and Eric Wright Special Projects, to achieve better value than arranging out-of-area transport for pupils who need special educational support. The Lotus School can accommodate up to 48 pupils with specific needs, with a mix of main classrooms, a science laboratory, feed technology lab, art & design rooms, sports/main hall and sensory rooms, as well as a life skills flat.
The main teaching classrooms and sports hall are all aired using Gilberts (Blackpool) Ltd’s innovative MFS hybrid ventilation units, installed by Read & Errington. In total, 24no MFS 128 units have been fitted through the two-storey façade into the classrooms, with a further three MFS-V roof-mounted units to the sports/main hall. In addition to being the first stand-alone hybrid ventilation system designed, developed and manufactured in Britain (co-incidentally just up the road from Lotus School), Gilberts’ MFS is also the first of its type to be COVID-compliant as standard.
Since its launch, MFS has become the product of choice for ventilation in schools, combining natural ventilation with a heat exchanger to minimise energy wastage by extracting, via a low energy fan and mixing damper, the warmth from the ‘used’ internal air being exhausted and transferring it to the cooler fresh incoming air. By blending the incoming air, the low energy fan ensures an even distribution of airflow, with control over temperature and CO2 levels within, and maintenance of a comfortable internal environment for occupants.
MFS delivers 8l/s ventilation, exceeding as standard Government COVID requirements of 5l/s. As it is a standalone unit with no connections to other zones within the building, crosscontamination risk is almost eliminated.
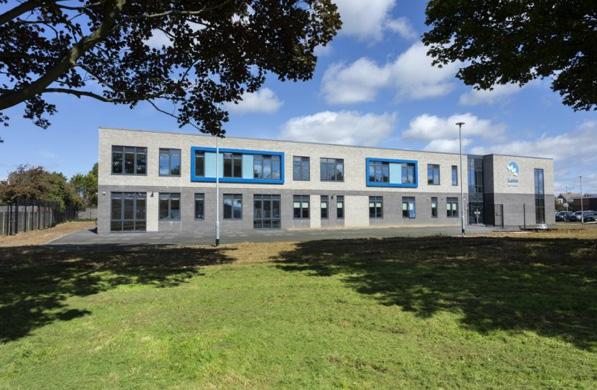
Each unit also achieves relevant modulation (often a consideration for pupils with special needs): its operational ‘noise’ is less than 30dbA, and it has been engineered to absorb external noise to keep within the classroom criteria required by Department of Education Building Bulletin.
MFS-V incorporates two MFS128 units placed vertically into a rooftop penthouse turret, with a shaft up to 1500mm2 ensuring effective ‘standalone’ ventilation of the space below. No additional ducting or plant is required. By routing the ventilation through the roof then internal spaces that have no external façade or that have a large open floor area can still be efficiently ventilated, be it via natural or hybrid principles.
Stephen Knowles, head of special projects at Eric Wright, observed, “As a commercially focussed business with a social purpose, involvement in the Lotus School was especially important to Eric Wright, as it means local children with special educational needs can be taught in their home town, in a safe, stable environment. We were also keen to use local suppliers as far as possible. That Gilberts is based in Blackpool, and had developed market-leading ventilation technology, it was logical to use its products and expertise on this project.”
Ful details of Gilberts’ MFS system can be found here. Alternatively, email sales@gilbertsblackpool.com or telephone 01253 766911.
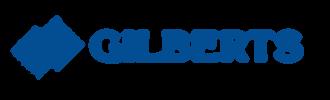
Mental Health Awareness Week:
Mark Nixon, Senior Health, Safety and Wellbeing Consultant and Trainer at Arco Professional Safety Services, Shares Three Key Areas of Focus for Positive Mental Health and Wellbeing in the Workplace
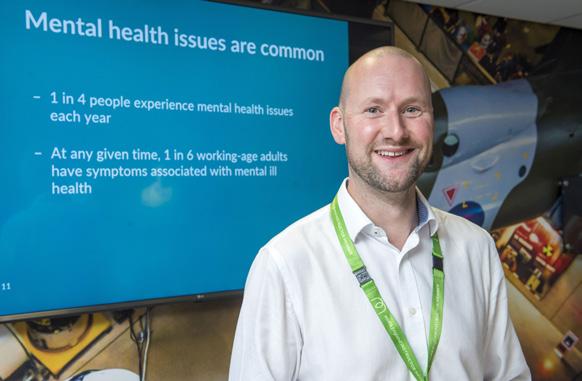
Ihave been a passionate Occupational Health and Safety Professional since 1995, but something changed five years ago. I was fortunate enough to be able to prevent a young individual from committing suicide. On hearing the phrase “you saved my life”, I made a commitment to improving my knowledge around the wellbeing and mental health of the people I work with every day and the employees in my clients’ organisations. I now deliver
Arco Professional Safety Services suite of courses to clients and instruct the MHFA Two Day Adult Mental
Health First Aid course. The feedback for these courses is breathtakingly positive; quite simply, the courses change lives and save lives.
Mental distress across the nation is at an all-time high compared to pre-pandemic levels. As individuals face grief, forced isolation, an economic slump and unfamiliar ways of working, we can help organisations make the decisions that will strengthen, rather than harm, an already vulnerable workforce. Beyond the human cost, better mental health support in the workplace can save UK businesses up to £8 billion per year. There are three key areas that demand organisations’ attention to support and improve mental health and wellbeing in the workplace: the business, the managers and the individuals.
The Business
The ‘Hierarchy of Controls’ is an approach to risk reduction that has become entrenched in the Occupational Health and Safety (OHS) sector. It aims to provide a consistent structure for managing safety, ensuring effective control measures are put in place to eliminate or reduce workplace hazards. However, mental wellbeing is one of the only areas of health and safety where the ‘hierarchy of control’ does not apply. At Arco Professional Safety Services, we have developed an alternative hierarchy that better suits the aims, problems and solutions in this critical area. Key principles include: • Prevention is better than cure. Recovery takes far longer than prevention and the costs to individuals’ livelihoods and businesses are far greater
• Failing to maintain health and wellbeing increases the likelihood of poorer mental health
• Enhancing and maintaining overall health and wellbeing increases the likelihood of better mental health
The Managers
How much stress a team faces is dependent on factors such as resource availability, workload, corporate culture and the strength of their support system. Managers are ideally placed to help handle employee stress as they have a greater understanding of the people in their team, their roles and the stress risk factors. In as little as one day, we can help managers acquire the knowledge and confidence to manage mental wellbeing proactively. We recommend a tenpoint action plan that can help managers support their teams more effectively. Key actions include: • Carry out Stress Risk Assessments based on the Health & Safety Executive’s (HSE) Stress
Management Standards (HSG218) to establish and resolve the causes of stress in the workplace
and use the HSE’s ‘Talking Toolkit’ to engage with individuals about the topic and make reasonable adjustments
• For non-work-related stress, managers can use a coaching approach (ask rather than tell) to help employees identify what is causing their stress, why it’s stressful to them, how they can tackle it and where they can go for help and support
• Managers can encourage employees to complete a
Wellness Action Plan (WAP), which can be used to promote wellness in already healthy employees and help those suffering or returning from a mental illhealth absence
The Individuals
There are many ways for individuals to manage stress, from guided breathing to decrease stress hormones and lower blood pressure, to understanding the importance of positive psychology. We teach recognised models such as PERMA as part of our mental health training courses to help achieve positive mental wellbeing. PERMA can help increase wellbeing by encouraging individuals to focus on living meaningfully, establishing supportive relationships, accomplishing goals and being fully engaged with life. Another key aspect of positive psychology is resilience, defined as the ability to cope with and recover from adversity.
Individual resilience will differ from person to person and throughout a person’s lifetime. It is not a fixed trait; it can be taught and developed over time with experience. Dr Lucy Hone, researcher and resilience expert, outlines three key traits of resilient people:
• Resilient people understand that bad things
happen to everyone
Every life will come with ups and downs and understanding this is critical to a balanced response to fortune and tragedy
• Resilient people can focus their attention skilfully
Being able to view a situation ‘as-it-is but not worse than it is,’ is a vital skill for resilience and mental wellbeing. In addition to the things that may not be going so well, individuals can focus their attention on extracting the positives, otherwise termed as ‘benefit finding’. We recommend individuals ask themselves,
‘what has gone well today and what is still right with me, others and the world?’
• Resilient people ask if what they are doing is
‘helping or harming?’
We encourage individuals to identify their unhelpful thoughts, self-talk and behaviours and choose more helpful, realistic and empowering alternatives Ultimately, mental health is not only a major issue in the workplace, but a major opportunity to take stock and ensure we are doing everything we can to protect the wellbeing of our colleagues. Five years ago, a near-tragedy cemented my belief that with the right support in place, positive mental health and wellbeing can be achieved and sustained.

Mark Nixon is a Senior Health, Safety and Wellbeing Consultant and Trainer at Arco Professional Safety Services. Arco Professional Safety Services offers specialist courses including Mental Health First Aid, Mental Wellbeing Awareness and Stress and Mental Wellbeing for Managers. Its highly experienced trainers can help build bespoke programmes to meet client needs, whether that means delivering training on the client’s site or at one of its national safety centres. The expert in safety can also provide training online via its specialist video conference service developed during the COVID-19 pandemic to ensure businesses can continue training while maintaining social distancing.
For more information on the mental health and wellbeing training courses available, visit the dedicated course finder at Arco Professional Safety Services.
Alternatively, to contact Arco Professional Safety Services call 0330 390 0822 or email info@arcoservices.co.uk.
23