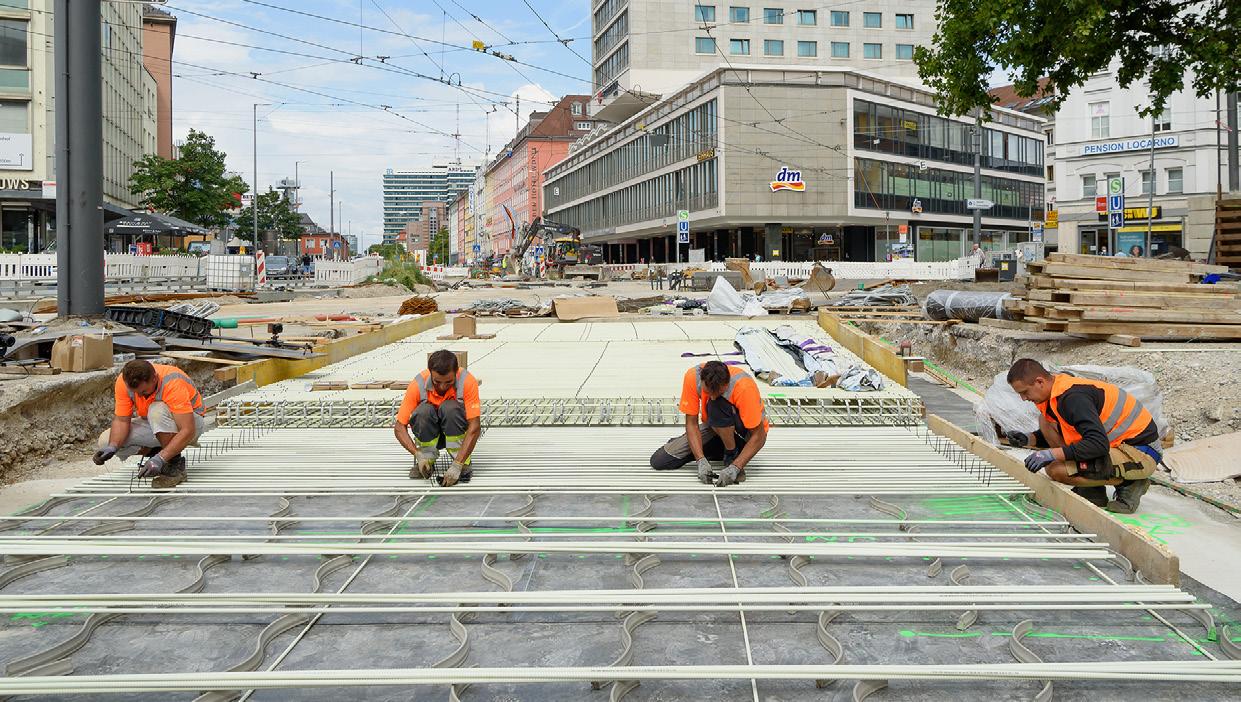
33 minute read
Schöck Combar
Work on the lower layer of the reinforcement. Photo: Moritz Bernoully
Schöck Combar ensures safer tram system and reduced noise
Advertisement
A great deal of investment is being made in the continued expansion of the Munich tram network in southern Germany. The latest construction work involves a thirdtrack being added just outside Munich Central Station. The use of Combar, the electrically non-conductive glass fibre reinforced polymer (GFRP) from Schöck, greatly reduces noise levels at crossovers; and unlike steel solutions, poses no threat of interference to sensitive electronic track control systems
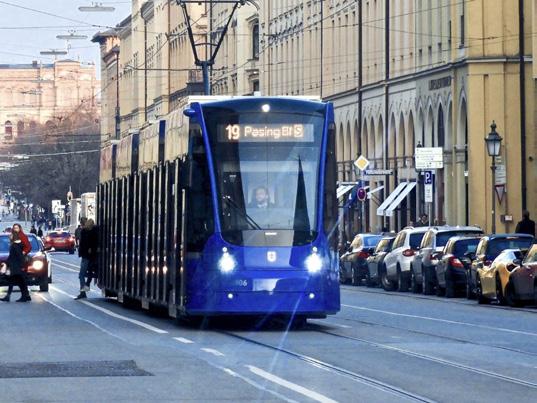
The Munich tram system is expected to transport in excess of 110m people this year and the rail section outside Munich Central Station is particularly busy. During rush hour, up to six trams can run through this double-track section every ten minutes and a third-track expansion is underway to help make operational running smoother and more flexible. Traditionally, the track support slabs involved would be reinforced with steel. However, this can create a safety problem with the sensor system of modern point-blocking circuits, which work by creating a resonant circuit in the area of the crossover. As a tram approaches the crossover, its large steel mass affects the resonant circuit, which is sensed by the track control system. If the carrier plate is reinforced using steel, this disturbs the resonant circuit in a similar way and may lead to interference in the pointblocking circuit – making it much more difficult for sensors to identify the presence of the tram, thereby putting safety at risk. Any such risk is avoided by
A typical tram in central Munich
using Schöck Combar reinforcing bars, as the glass fibre reinforced polymer solution is neither magnetic, nor electrically conductive.
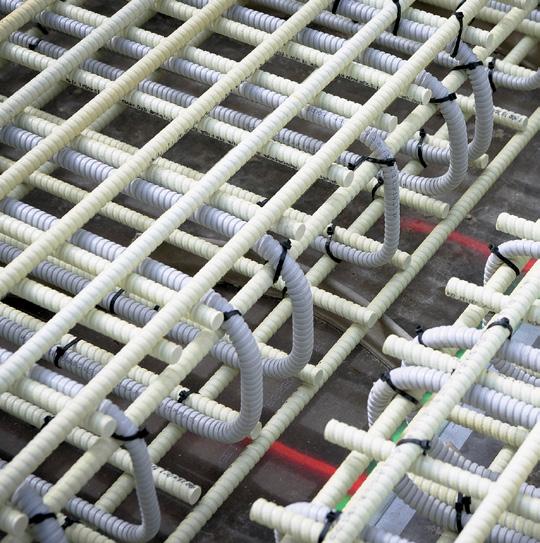
Cutting the Combar reinforcing bars to the correct length. Photo: Moritz Bernoully
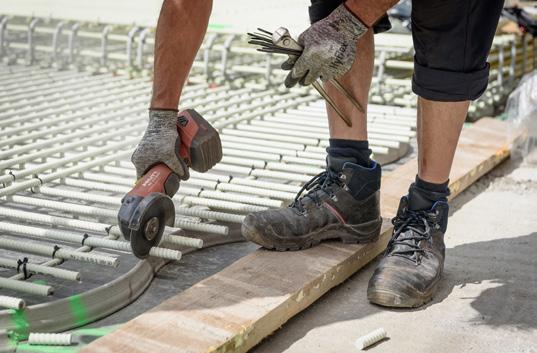
Operational safety and vibration reduction too
In additon to the improved operational safety at crossovers, the use of Schöck Combar also offers significant benefits in reducing noise and vibration as well. A welcome benefit, particularly for one of the largest department stores in Germany and also one of the most coveted large-scale properties in Munich’s city centre, which is located adjacent to this part of the track Mass-spring systems for these types of track typically consist of a rail carrier plate and a U-Trough shaped foundation of reinforced concrete. The two components being isolated to prevent mechanical vibration. However, because of the possible risk of local interference with the point-blocking sensors at the crossovers – and the fact that Combar has a tensile strength greater than steel – it was decided to incorporate the product in the mass-spring plates. Where Combar was installed in the area of the U-Trough and rail carrier plate, elastomer sheeting was used to completely isolate the carrier plate from its surroundings. The elastomer layer also served as lost formwork within the trough, where the Combar elements were installed crosswise, using cable ties and concrete, strength class C30/37, being poured in the respective section. Combar units have a smooth base and no sharp detailing, so there is no risk of them penetrating the elastomer layer and causing acoustic bridges. After the trough had cured, the carrier plate, also reinforced by Combar, was then poured using concrete of the same strength class. The construction section involved is around 1000 sq metres in total.
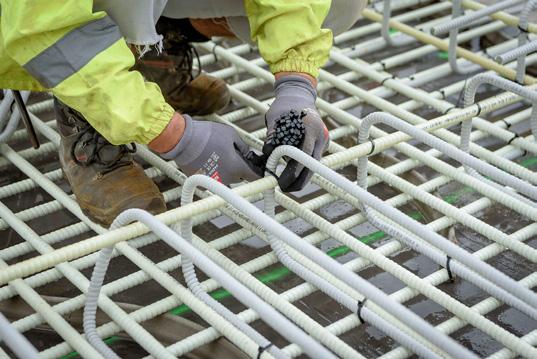
Close up of the floor slab reinforcement Photo: Moritz Bernoully
Superior performance
Historically, steel has been used as the most common reinforcement material in concrete construction. However, the material properties of steel rebar make it unsuitable for many applications. Conversely, since its initial introduction around fifteen years ago, Schöck Combar has gained ground in more and more markets, demonstrating its superiority as an alternative to steel. The unique structural and physical characteristics of the product are achieved by bundling high-strength glass fibres tightly together and pulling them through a closed chamber where they are impregnated with a synthetic resin. The lengths are then cut and the resultant product is a ribbed reinforcing bar made of corrosion resistant glass fibre reinforced polymer. It is significantly lighter than steel and is neither electrically or thermally conductive.
Exceptional versatility
Combar application examples include its easy machinability in tunnel construction, where boring machines used in shaft walls of tunnels, cannot drill through steel reinforced walls. With Combar the machine can cut directly through the head wall. In high voltage transformers and power plant reactors, inductive currents are generated within the reinforcing steel. The heat will affect the rebar strength if too close to the coils, but Combar remains unaffected. And its corrosion resistance – even from salt – is unrivalled when building bridge, marine and harbour constructions. Also, when it comes to onsite installation, handling Combar is effectively no different from conventional reinforcing steel, so no special user training is required.
For Combar enquiries, in the first instance visit www.schoeck.com
Trusted capability and single source for roof refurbishment wins through
Water leaking into the classrooms alerted the management team at Radford Primary Academy to the need to take action.
The major refurbishment, involving the upgrading of 14 roof areas, up to 40 years old, has had added benefits beyond making the buildings watertight. The improvement programme, managed by Barker Associates with support from Langley Waterproofing Systems Ltd, has meant the school has a better understanding of its estate condition, the ability to manage it going forward, and the potential for reduced energy bills as a result of insulation upgrade.
Barker Associates collated the application and implementation of two Condition Improvement Fund (CIF) bid applications, working closely with Langley Waterproofing Systems Ltd who provided supporting evidence and investigation into the condition of the existing roofs. This encompassed the CIF application from concept to completion, compiling a schedule of works, and then providing technical support from inception through to completion.
Langley’s roof condition survey found significant areas of concern. All the roofs were at the end of their useable life and had already been subject to extensive reactive liquid repairs. There were also potential structural issues related to the woodwool structural deck which, if saturated by water ingress, could result in roof collapse, alongside fragile Georgian wired glazed rooflights, with poor- or in some instances no- insulation, plus cladded upstands and overhangs that could pose a potential fire risk. Some areas of the insulation were saturated with water, rendering it inefficient. Alongside the flat roofing, there was trapezoidal corrugated cladding which was deteriorated. Langley designed solutions to refurbish all the roofs, and recommended the installation of its TA-30 Flat Roofing System; where possible, existing roof surfaces were to overlaid rather than stripped, reducing waste to landfill, and for optimum cost efficiency without impact on the new roof performance. Langley’s TA-30 system, part of the well-established Reinforced Bituminous Membrane range, is a premium quality, torch applied, high performance SBS elastomeric membrane warm roof system for flat or sloping roofs which carries a 30 year independently insured guarantee for both materials, design, workmanship and consequential loss. The trapezoidal cladding was addressed with a bespoke solution from Langley Structures, part of the Langley group of companies, using its warm roof striptiles (usually used to convert flat roofs to pitched). Its Approved Contractors Cambridge Flat Roofing Co Ltd undertook Phase 1, with Premier Roofing & Construction Ltd executing Phase 2, through competitive tendering.

Roofs 4,7,8,9 and 11 were refurbished under Phase 1, being deemed in most urgent need.
In each case, the defective existing BUR was removed to expose the deck below. Langley’s TA-30 system which includes PIR insulation was installed to bring the roofs up to current
U-values of 0.18W/m2K as roofs 4, 8 and 9 had no insulation at all, and the 20mm fibreboard on roofs 7 and 11 was wet.
To deal with the trapezoidal sections, Cambridge Flat Roofing stripped and removed the corrugated metal sheet to expose the timber below and renewed the wood as necessary. Insulation 140mm thick was fitted in between the rafters then battened and tiled with 1280mm x 415mm Langley roofing tiles. Details were flashed and abutted as required. Langley LG45 ventilation tiles were fitted to modify existing soil pipes. In Phase 2, Premier Roofing & Construction (PRC) addressed the remaining eight roofs of the main school and the roof of the tank room. Although the roofs over the main school premises were all insulated, they did not meet current Building Regulation requirements in regard to U-values. PRC prepared the existing roof to install the TA-30 system, then built up the new insulated roof, fitting flatboard insulation up to 120mm thick and tapering where necessary to correct falls and improve drainage, whilst achieving the desired 0.18W/ m2K U-value.
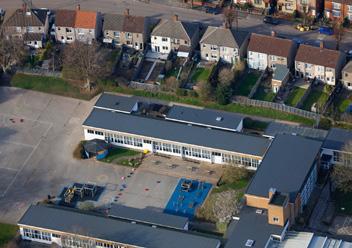
Said Langley’s Mike Preston, Regional Manager, “On such a large refurbishment it is taken as economical to use a single supplier to ensure continuity and give the school a ‘one stop shop’ to contact should any issues arise in the future. Langley as a group, with our Structures division, had the ability and capability to deliver that single source despite the variety of roof requirements to be addressed. It also provides the end client with cost certainty and compliance to Building Regulations across all roof areas.”
Added Barker Associates’ Project Surveyor David Mugliston, “We have an established long-term relationship with Langley. There is trust that they will deliver, even on such a complex and extensive project and return to rectify issues that could arise.
“The team at Radford Primary appreciated the logic in using a single source for its roofing refurbishment, that had the capability, in-house, to survey, advise then deliver the most efficient solution. Using Langley has enabled the school to upgrade its estate comparatively painlessly and have the peace of mind going forward that its roofs are now fully compliant for current Building Regulations, specifically Approved Documents B and L, and that the children in its care will be safe, dry and warm for the future.”
IS YOUR FLAT ROOF ESTATE... AN ASSET OR A LIABILITY?
The Government’s response to the Naylor Review acknowledged the importance of the collection of data to support strategic estate planning and stated:
reducing backlog maintenance not only provides a safer and higher quality estate but reduces running costs in the longer term.
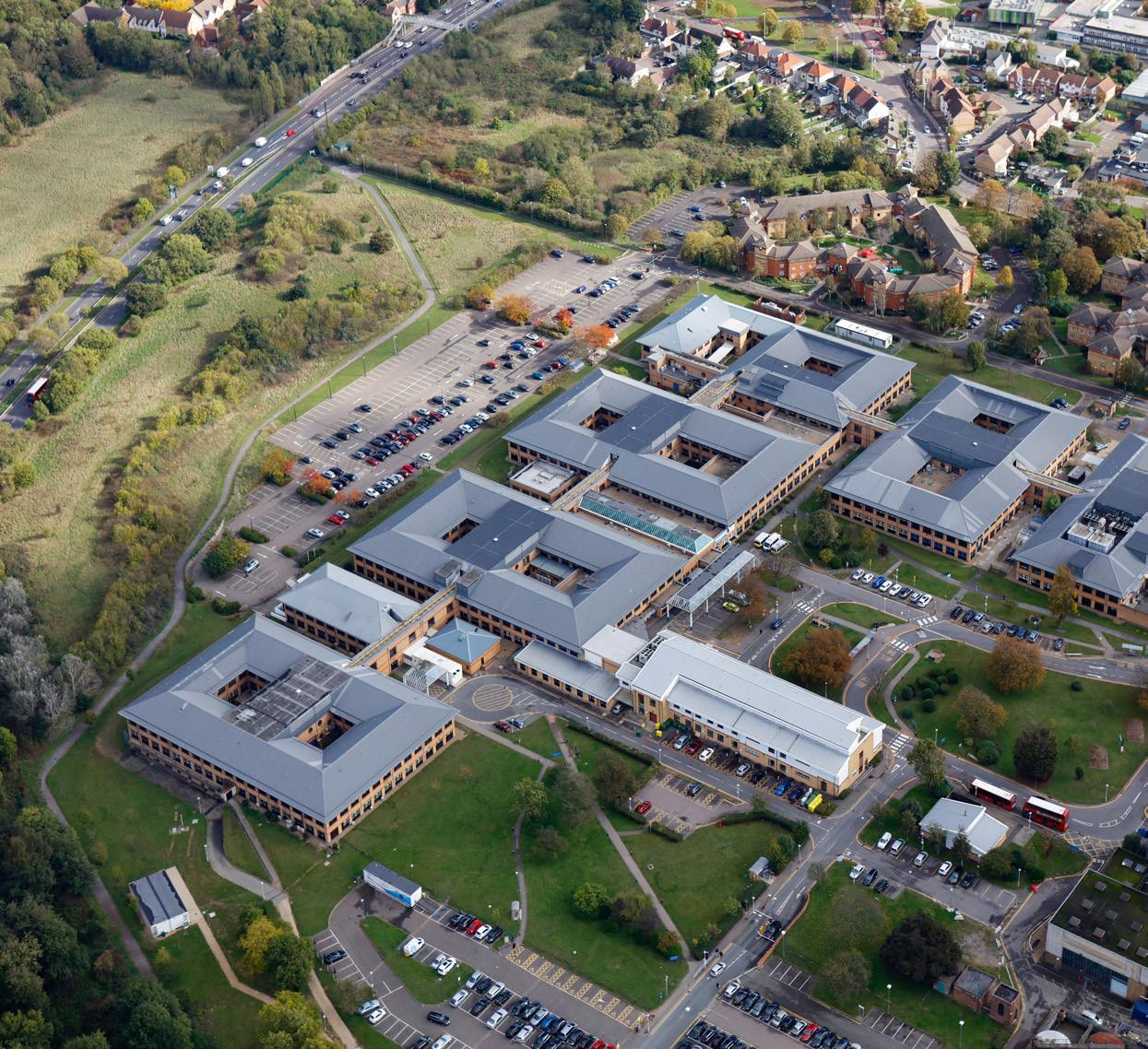
A roof is a significant ‘out-of-sight’ asset and when its condition is unknown, often issues can develop over time.
Easily accessible data is a crucial element in managing any estate. Without reliable data, any long-term strategic approach is unattainable and the management of the estate budget is rendered a purely reactive one. Langley provides a long-term approach by creating a full asset management plan for your flat roof estate by carrying out a comprehensive roof condition survey. The data gathered then supports preventative planning and cost-effective budget management, this is achieved by minimising the risk of sudden unexpected remedial expenditure. If work is required immediately, we are a trusted single-source of responsibility and handle every aspect of your project, from initial consultations and design, right through to final installation, after sales care and maintenance - for peace of mind.
We provide systems that are durable, guaranteed, safe and fully compliant with Building Regulations.
BOOK YOUR FREE ROOF CONDITION SURVEY TODAY
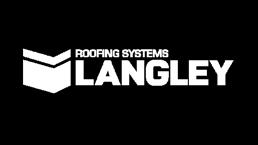
W: www.langley.co.uk E: enquiries@langley.co.uk T: 01327 704778
SUITABLE FOR ALL SECTORS DOWNLOAD THE WHITE PAPER HERE
HOW TO ENSURE A ROBUST AND SAFE FLAT ROOF SYSTEM SPECIFICATION

The White Paper, supported by Zurich, covers: Regulations, Broof(t4) classification, fire performance materials, the risk of non-compliance and specifying the correct system.
Why it’s time for a mental health revolution in construction
We all know the importance of workplace safety to the construction industry. Slips, trips and falls, working at height, noise protection and more mean that workers need to be welltrained, monitored and assessed to ensure their safety on the job.
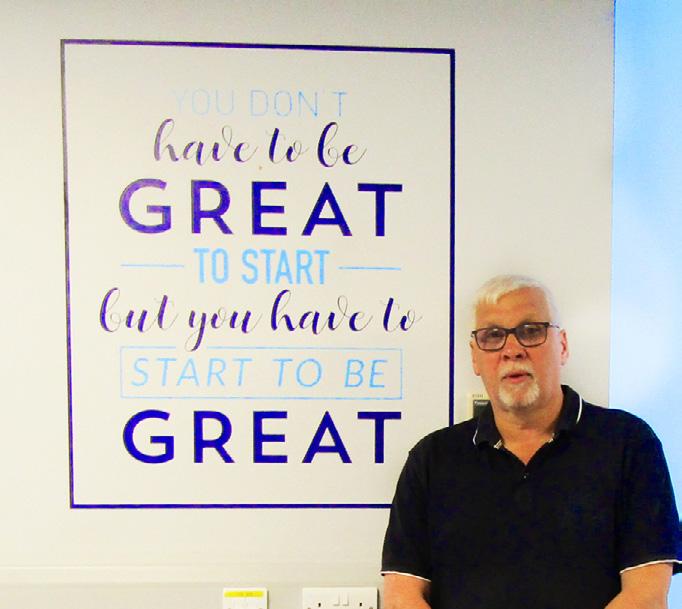
What you may not know is that more than 11x as many construction workers commit suicide each year than are killed in workplace accidents. Society’s attitudes towards mental health are slowly changing, but for construction, this is an emergency that demands a swift and powerful response.
While mental health is a societal issue, construction is particularly vulnerable due to being male-dominated, and often involving long periods away from home. The ‘macho’ culture can make people feel that they will be judged for speaking out, causing them to suffer in silence. These problems are exacerbated by the physical demands of construction. Injuries from heavy lifting, repetitive strains, loud machinery and other sources are common, and can be debilitating. It’s also not always financially stable, as shown by the recent bankruptcy and collapse of Carillion.
Even if you can hide your mental health issues, they can compromise safety by distracting people, putting everyone’s lives at risk. They also tend to lower people’s productivity, meaning there is a strong financial case for businesses to intervene, as well as a moral one.
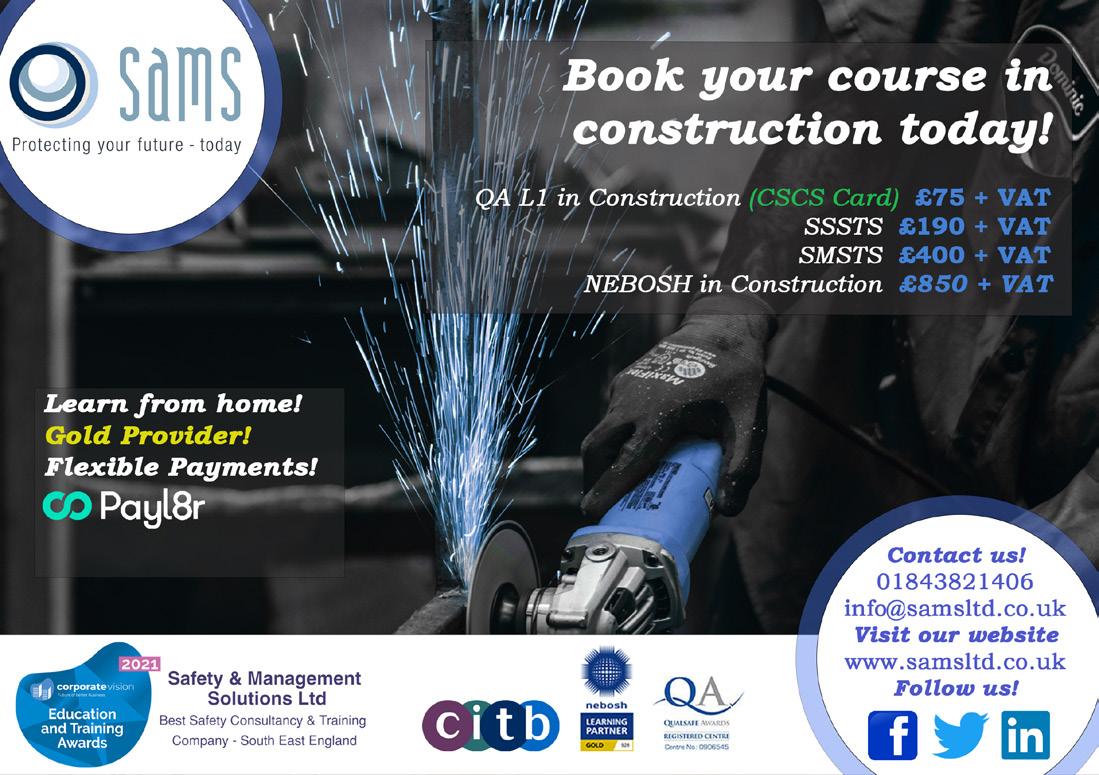
There has to be a recognition that mental health is as important to site safety as any other established physical risk factor. The most important step to achieving this is to make it clear to workers that you take mental health seriously, and invest in solutions to improve mental health in your workforce.
There are a range of ways to achieve this. The simplest and most effective is to provide mental health awareness training, teaching people the importance of good mental health and how to support their colleagues. This alone can break the stigma around mental health, and reinforce that it is something to be open about and not to shy away from.
From top to bottom, people should feel that they will be supported, and not be penalised for seeking help. This may require training for supervisors and business owners, as well as regular toolbox talks to reiterate the importance of good mental health and communication. The construction industry is at crisis point when it comes to mental health, but it isn’t too late to take action. What the industry needs now is for leaders to take responsibility and action rather than waiting for new legislation. By doing so, we can address the largest cause of deaths in construction - and make this a happier, healthier and more productive place to work.

At SAMS we offer remote Mental Health awareness courses therefore If anyone has any questions or would like to enquire then please contact us on: 01843821406 or email us at: info@samsltd.co.uk. Enquires for our Mental Health awareness courses can also be bought on our website.
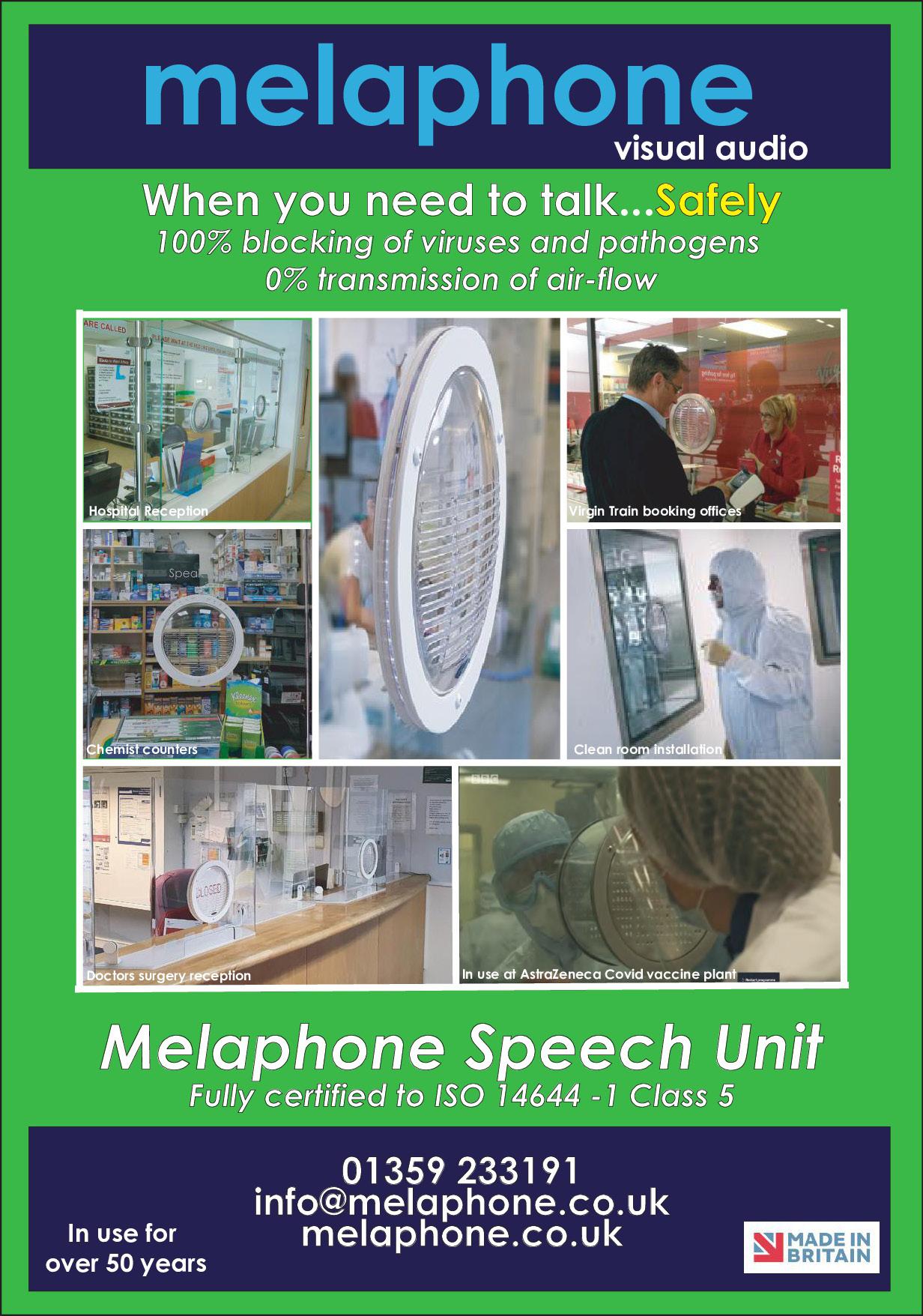

50 Year old product makes dramatic comeback to help beat the virus
When the Melaphone Speech Unit was
at British Rail stations, nobody could have predicted that half a century later it would suddenly be in such high demand.
The current Corona Virus Pandemic had created an urgent need for all protective equipment – both for personal use and in the working environment. This is the reason the Melaphone has come into its own again. Its unique design, with its resonating membrane and air-sealed constructions, make it the ideal device to install in any situation where face-to-face communication occurs. It not only offers protection from air-borne viruses and
through a screen. Its protective credentials
and designers for use in hospitals, laboratories and cleanrooms or anywhere hygiene is of paramount importance. It is a simple but really ingenious invention which requires no servicing, wiring or electrical supply. And it is very easy to keep clean and safe with an antiseptic wipe.
The Melaphone has now been built into the new Defender Virus Screens produced by the company and numerous doctors’ surgeries, medical centres, clinics and pharmacies in the UK have had these screens installed with considerable success and approval. The screens are individually made and every component is of the highest quality, giving a clean, sleek and professional appearance in any health-care environment.
The Melaphone is still available as a standalone unit for installation into walls, glass or plastic screens, windows or doors. I can easily
requires no special skill to install. The range has been expanded to meet the growing demand for the units. In addition to the original brushed aluminium model there is a stainless steel model, a white powder-coated aluminium model and the newest and highly successful Himacs acrylic-resin model, which is at a very popular price.
All of these models are available from stock and can be purchased from Melaphone VisAudio.
Even after 50 years, we’re proud to still be able to say ‘MADE IN THE UK’ at our London production facility.
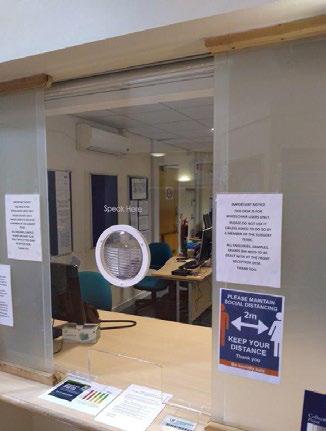
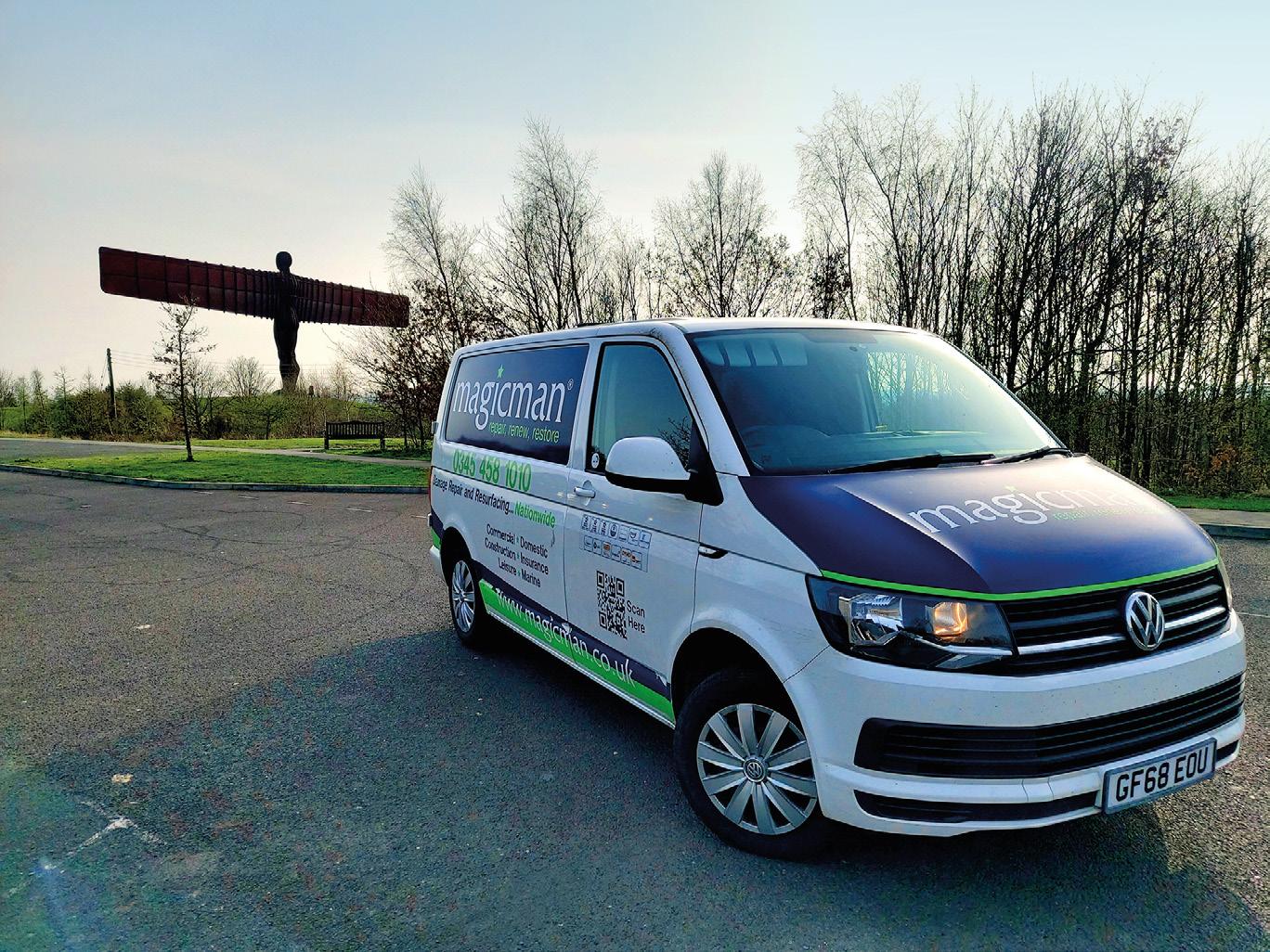
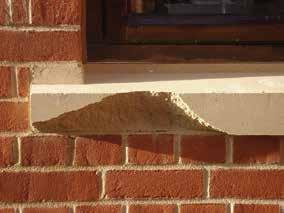
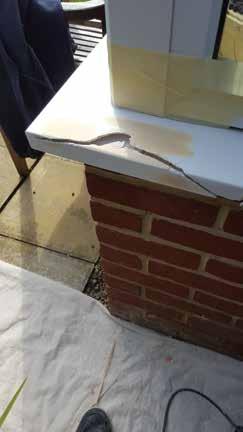


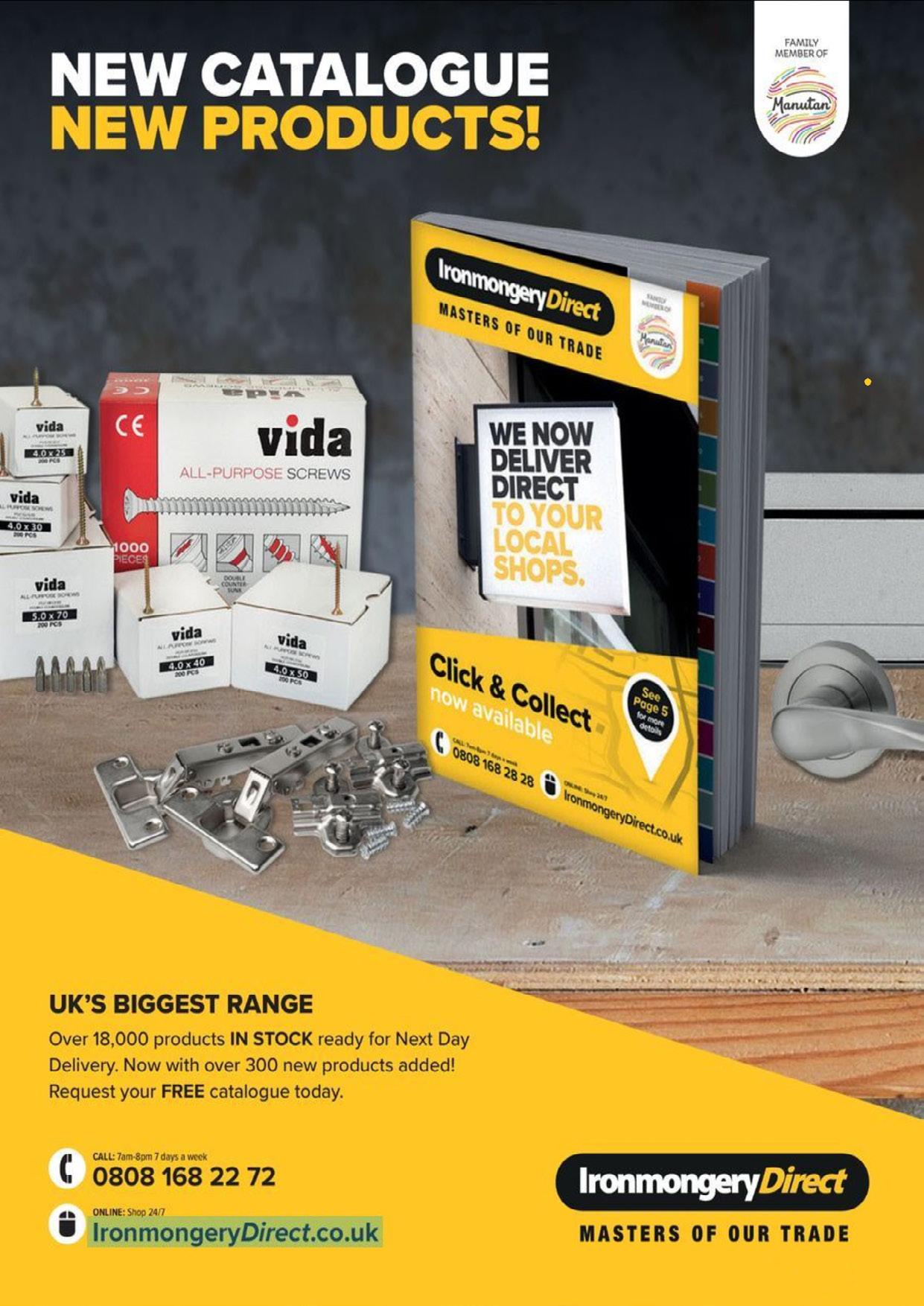

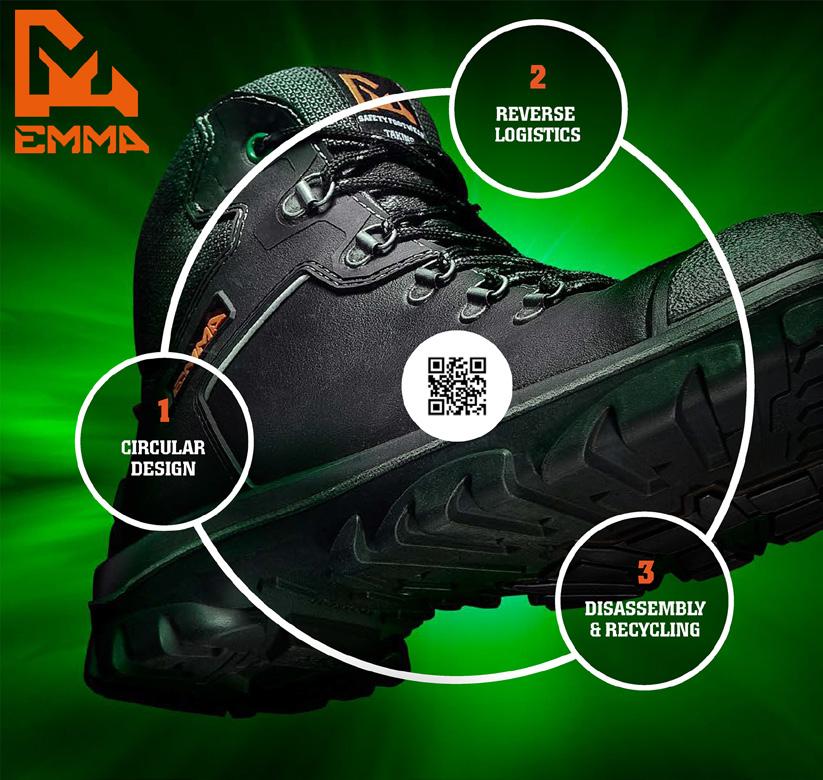
EMMA - Sustainably Responsible Safety Footwear
100% Circularity in Materials Technology to Improve Your Carbon Footprint.
EMMA will help you reduce your carbon footprint - by supplying Safety Footwear that’s completely made from a combination of recycled materials and materials that are recyclable. This ‘100% Circular’ footwear offering is changing the lifecycle of safety footwear as EMMA steps up to be an active part of individual and corporate sustainability programmes. Every product in the EMMA range is safe for the environment with a ‘100% ‘Circular’ manufacturing, usage-mapping and recycling process for every shoe and boot produced under the EMMA brand – the supply-chain partner that’s totally committed to sustainability and reducing waste.
For buyers and specifiers in all industry sectors including construction and manufacturing, logistics and warehousing, office and retail, hospitality and medical, EMMA safety footwear will make a doubleheaded contribution to their businesses – a value for money investment in workforce-wellbeing and a commitment to improving corporate social impact. Part of the Hultafors Group portfolio of marketleading PPE brands, EMMA complements the Solid Gear and Toe Guard safety footwear ranges by including all the Hultafors Group hallmarks of hitech designs that combine top quality materials for ultimate comfort, maximum safety and wellbeing at work.
To get more information on EMMA Safety Footwear, visit the website at www.emmasafetyfootwear.com, call the Snickers Helpline on 01484 854788 or email sales@hultaforsgroup.co.uk
Snickers Workwear = Comfort = Wellbeing and Improved Performance.

Snickers Workwear For Summer
Everyone wants to be cool, and comfortable at work this summer – and to do their bit for saving the planet. That’s why Snickers Workwear has integrated improved 37.5® fabric technology and ‘Verifiable Sustainability’ into its T- and Polo-shirts.
The new AllroundWork styles are made from highly functional waffle- structured 37.5® fabric for optimal ventilation, cooling and moisture transport to keep you feeling fresh for longer. And, with the aim of being at the forefront of sustainability in Workwear, the new lightweight Polo and T-shirts are made of 100% recycled polyester with a bio-based, anti-odour finish with a smooth texture and efficient moisture transport for great working comfort. They’ve all got street-smart body-mapping designs for an amazing fit, outstanding functionality and long-lasting comfort – all day, every day.
Getting information on the Snickers’ Summer Workwear range is easy. You can call the Hultafors Group Helpline on 01484 854788. You can check out the website and download a digital catalogue at www.snickersworkwear.co.uk or email sales@hultaforsgroup.co.uk
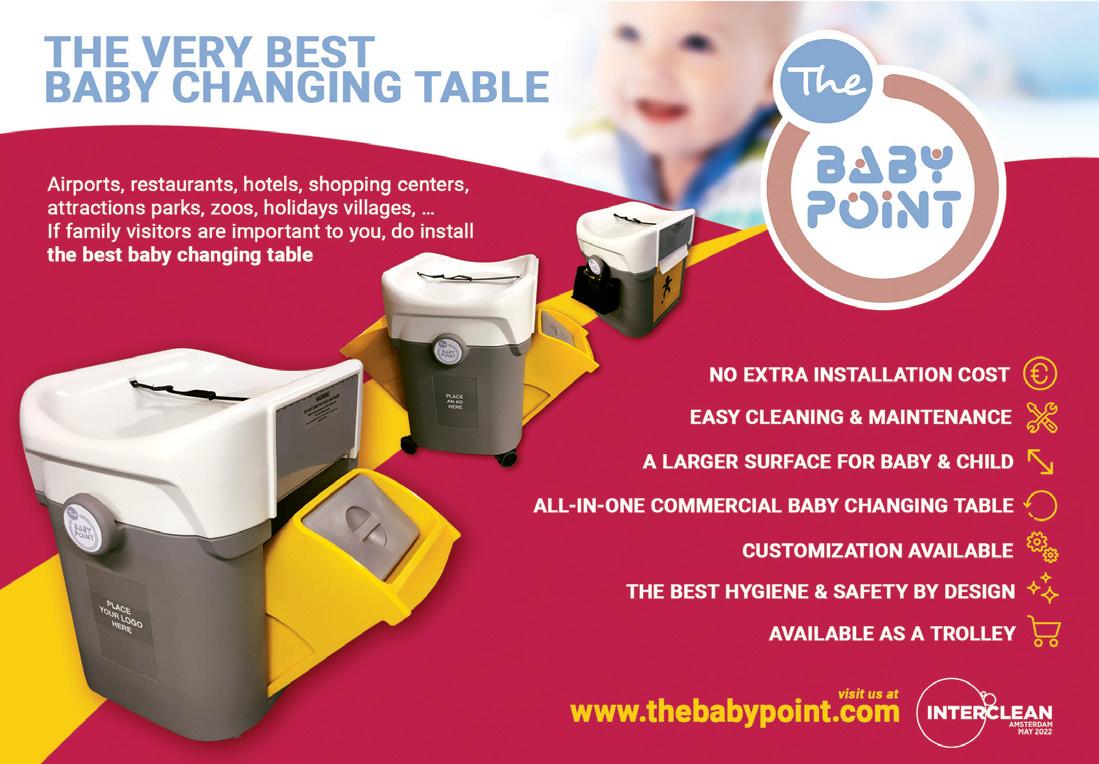

BT1 Ultimate Bathroom Sealant & Adhesive TRIBRID® Technology. Made in Britain
No More Mould or Fungal Growth
CT1 who lead the way in research and development have pioneered the latest technology for the building industry over the last 18 years. The first to introduce a hybrid sealant almost 18 years ago, pioneered the way forward with a new era of sealants. CT1 showed the industry that you only need one tube for most applications with the correct raw materials and formulation. This new technology presented itself in a tube CT1.
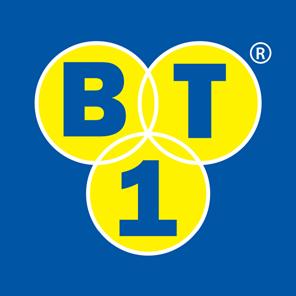
CT1 created a formulation with no solvents, allowing CT1 to perform under any difficult conditions, even under water. CT1 can guarantee that it will never shrink or crack, so it will not lose its bonding and sealing capabilities over time.
Realising that hybrid formulations would be soon dated with old technology, as demands increase in what we expect from products and with the building industry producing more complex builds. CT1 was proactive rather than re-active.
Introducing TRIBRID® technology. Another new era of sealants and adhesives. Now three times stronger, longer colour retention and elongation, TRIBRID® CT1 can’t be matched or compared to again for a long time. CT1’s technical field team also realised that in today’s current conditions people are demanding much cleaner environments and surface areas. Using the correct sealants and adhesives in installations and repairs is key keeping a surface area healthier. BT1- The Ultimate Bathroom Sealant and Adhesive was created as most sealants over time will allow bacterial and fungal growth. Some will grow quicker than others. The bathroom can be a contaminated area, with heat, fluids and lack of UV light. BT1 based on the revolutionary TRIBRID® formulation, was created to prevent fungal and bacteria growth happening over long periods of time.
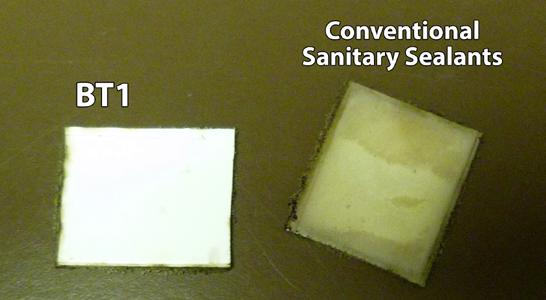
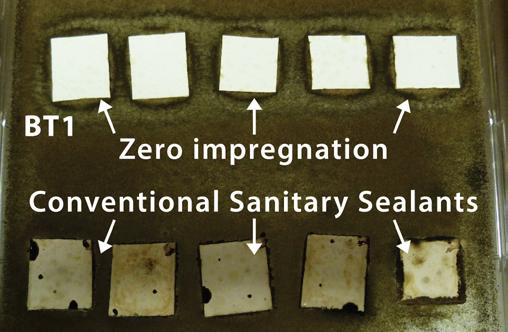
This unique formulation makes it impossible for bacteria or microbes to form on the surface, and with almost zero indoor emissions, makes this the heathiest choice for your home. But what became apparent after vigorous testing was that using BT1 would reduce the risk of MRSA, E. Coli and campylobacter. Reducing bacteria by 99.99% and being able to retain its clinically clean white appearance is now proving to be the only sealant and adhesive being used by Hospitals, Aged Care Facilities, Clinics, Schools, Universities and Public Buildings.
Solihull Hospital in Birmingham and Good Hope Hospital in Sutton to name a few have used and will only use BT1.
BT1 - which can also be used in kitchen installations, launched initially in The IPG Member Stores. The IPG is the largest and fastest growing membership group for plumbing, heating and bathroom specialists, wanted to add BT1 to their stock profile and give their members the latest technology for plumbing and installations.
Since the growth and reputation of BT1 and the important role it plays in keeping a healthier environment, Wickes stores, will now also be stocking BT1 nationwide.
Go to www.CT1.com and https://youtu.be/ kirVUrwWbaY
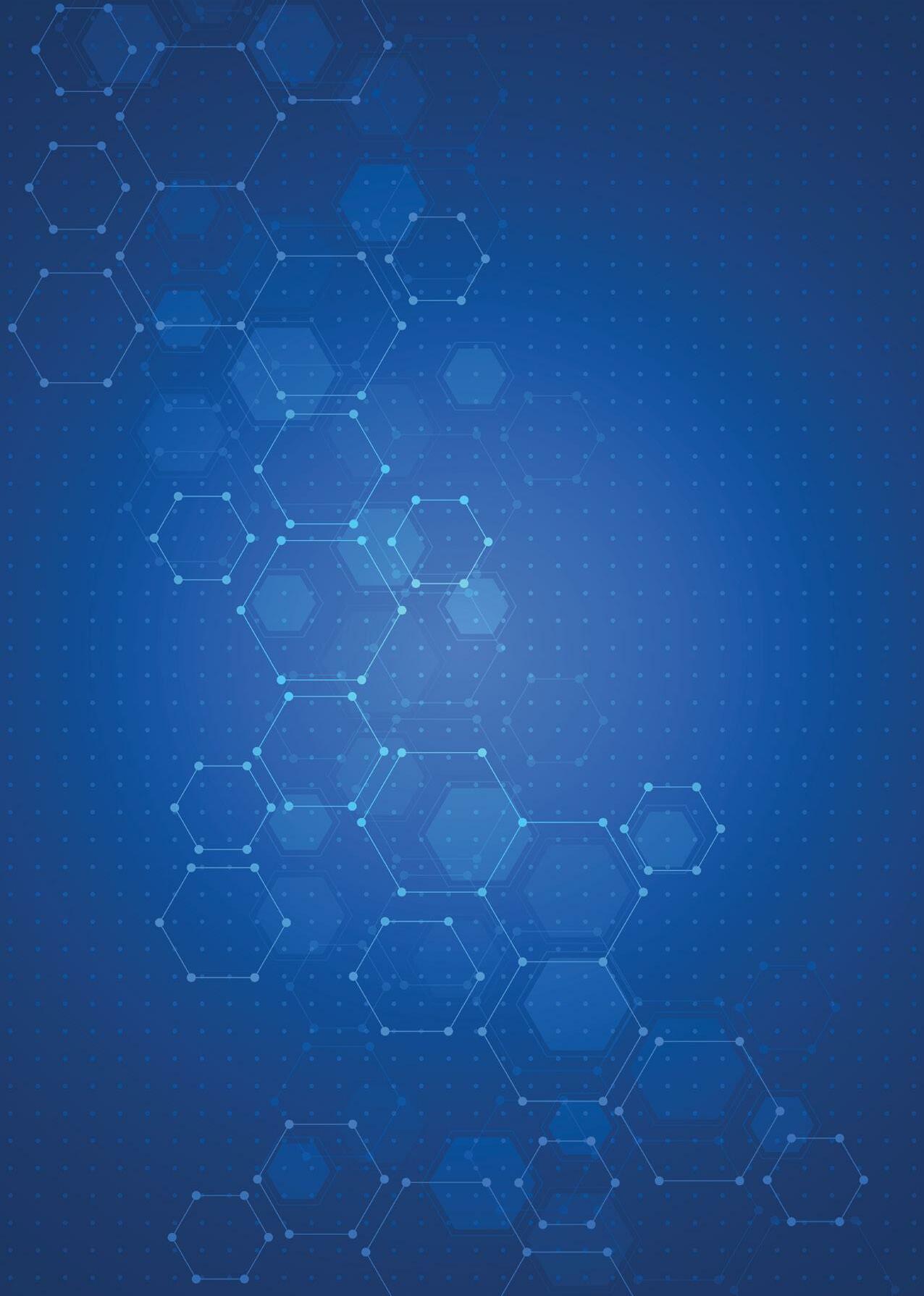


Artificial Plants & Trees for Businesses
Our master craftsmen construct each bespoke order with painstaking care and attention, to create an exceptionally ‘real’ artificial showpiece, and we offer bespoke solutions to suit the needs of your space, business and tastes.
Whether you need simple plants and trees that don’t need tending to or you’re going for a full artificial landscape with turf, hedges and more, we have existing products and the capacity to create custom designs for any need and budget.
We’ll offer a no obligation quote to help you plan your projects and we can tailor our service to ‘fir’ your needs.
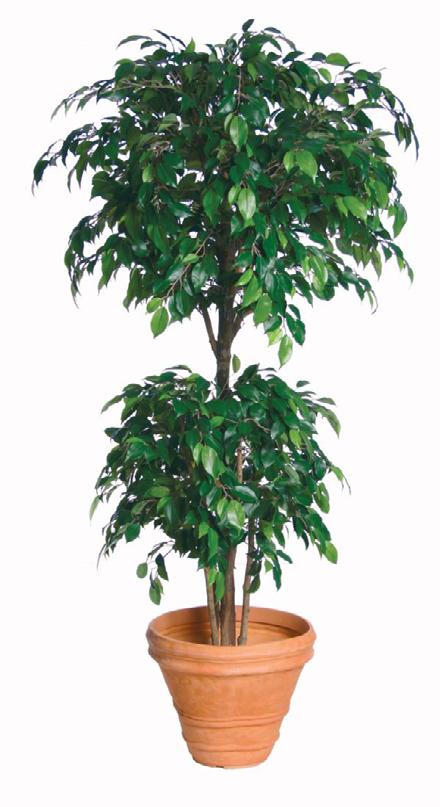

Full Support
Whatever your choices, we have the design experience and know-how needed to make you stand out. We can work with your design to make your premises look incredible, whatever the space and whatever the industry. We can even help you develop the design, drawing on years of experience.
Who Have We Supplied?
Major companies in many industries including ITV, BBC, Channels 4 and 5, Mulberry, Innocent Drinks, Monsoon, Bella Italia, Tescos, Big Brother, The Only Way is Essex, Coronation Street, Dancing on Ice, Park Resorts, Volkswagen, and more. centres, theme parks, colleges and schools, cruise ships, theatres… the list goes on! We have tens of thousands of satisfied customers in the UK, in Europe, and across the World.
We can provide offers for procurement managers and corporate buyers on bulk orders and for trade, to help you finalise your design. Our quotes are no obligation - so call us today. We look forward to working with you!
Get in Touch!
Call us today on 01524 858888 or email sales@justartificial.co.uk – Browse our Web Store online for our full stock range and more info on our bespoke solutions on offer.
We’ve also sold to house builders, zoos, hotels, restaurants, shopping
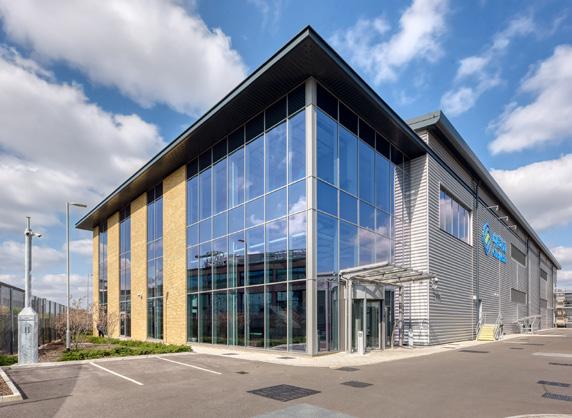
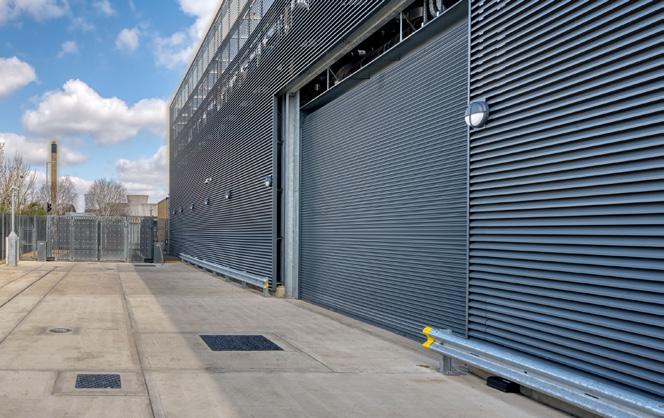
Concert has successfully delivered phases 1 and 2 of the first China Mobile data centre outside Asia
Construction consultancy Concert has completed phases 1 and 2 of a 10 megawatt data centre in Slough for telecommunications network China Mobile, the client’s first facility outside Asia.
Concert were appointed to look into the feasibility of the site before the decision was made to locate the data centre in Slough. The process included supporting the negotiations on the agreement for lease as part of the diligence team, and liaising closely with both the developer, China Mobile’s technical team and appointed design team to ensure the successful implementation of the scheme. The due diligence support included reviewing the lease’s technical documents, the landlord’s shell design and budgeting the tenant specific changes including introducing a mezzanine floor, to ensure the building was fit for China Mobile’s requirements at the market price. Concert also worked very closely with the client’s in-house procurement team in Asia to ensure that their specific procurement protocols were implemented. Daniel Wright, Director at Concert explains, “This was a gold standard for China Mobile Internatinal and we successfully achieved all of their KPIs, completing the design and delivery needed to support this client in a completely different market with different types of contracting arrangements.” Adds Jack Ke, Data Centre Manager, Europe, China Mobile International, “We were very pleased with the experience and performance of the Concert team. Their professionalism and expertise gave us confidence and we look forward to working with Concert again in the UK and other regions.”
www.weareconcert.com
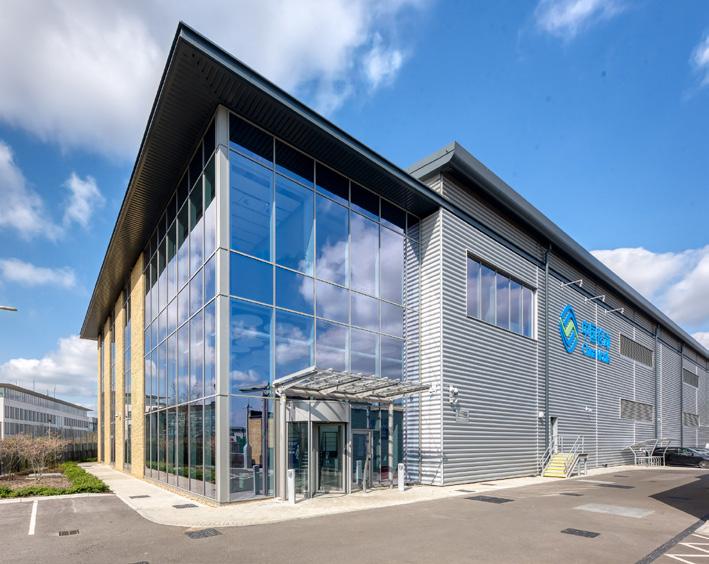
Steelworks up on second phase at St. Modwen Park Gatwick
St. Modwen Logistics is continuing to grow its portfolio with the commencement of steelworks for a new 64, 752 sq ft unit at St. Modwen Park Gatwick.
The unit forms part of the second phase of development at the site and is expected to be ready for occupation by mid-July 2021. Once complete, St. Modwen Park Gatwick – which has been designed to meet the growing demand for big box and urban warehouse space in the area – is expected to create around 75 jobs across the region. Strategically located adjacent to Junction 10 of the M23, serving both Gatwick and Crawley, St. Modwen Park Gatwick also offers easy access to the M25 and the south coast. The scheme is expected to help meet employment demand for the industrial and logistics sector across the region and has a gross development value of £31 million. David McGougan, Senior Development Manager at St. Modwen Logistics, said: “This second phase of development at St. Modwen Park Gatwick will cater for the significant market demand for schemes of this nature within the region. With such a prime location close to the neighbouring airport and with outstanding road transport links, we’re confident in pressing on with our development plans.” BNP Paribas Real Estate and DTRE are joint marketing agents for the site. Jake Huntley, Partner at DTRE, added: “The plans St. Modwen have in place will be sure to attract many high-quality businesses to the area. The location and quality of the proposed unit means St. Modwen Park Gatwick is likely to be a highly sought-after site and we anticipate significant demand for this second phase.” William Merrett of BNP Paribas Real Estate added: “The demand for logistics space in this region continues grow, so it is great to see St. Modwen working to meet that demand with a new, innovative, design led commercial unit.”
For more information on the scheme, visit: https://stmodwenlogistics.co.uk/property/st-modwen-park-gatwick/
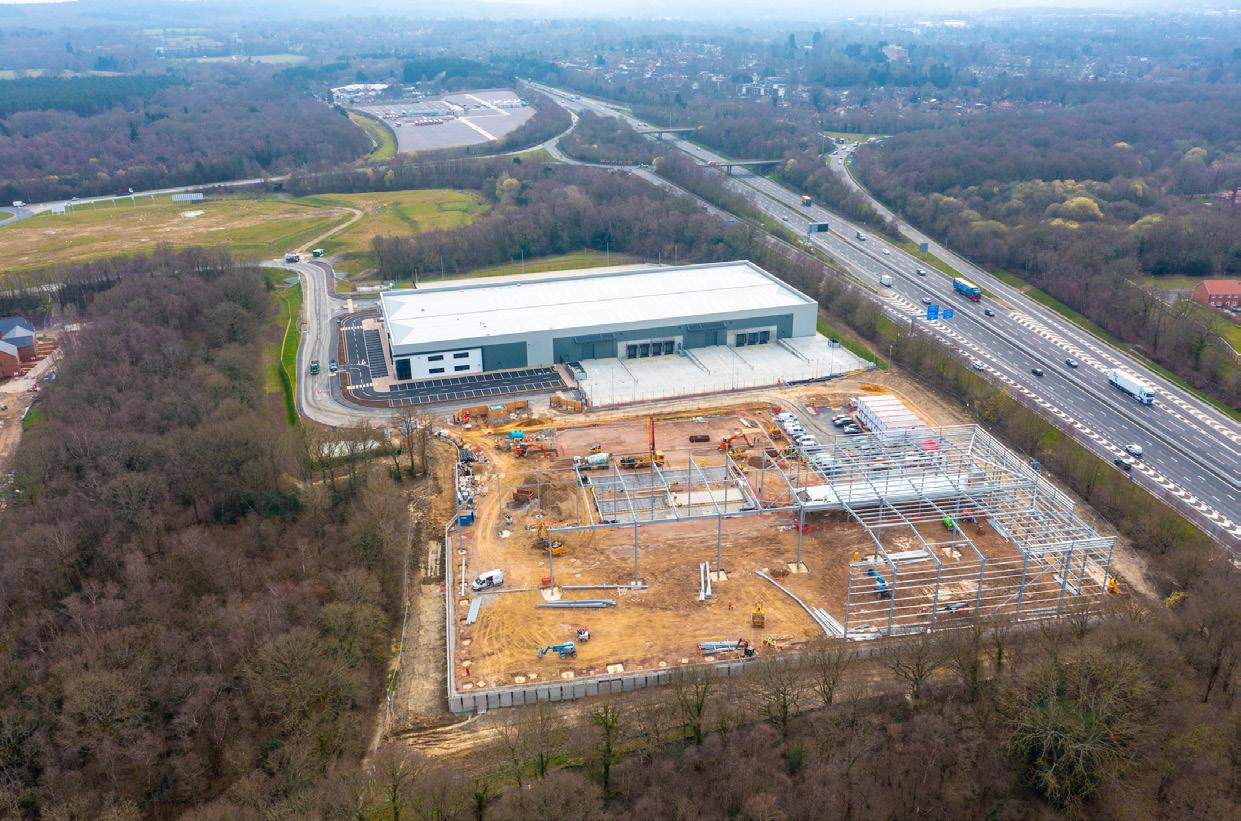
Bauer implements innovative lift cell method for “Postbyen” construction project in Copenhagen
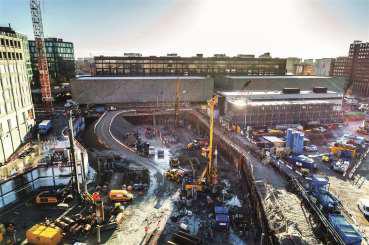
In the center of the Danish capital of Copenhagen, the new city area “Postbyen” is being constructed. The project includes commercial spaces, office buildings, hotel service apartments, retail as well as urban residences. To implement the construction project, BAUER Spezialtiefbau GmbH was commissioned by the owner Hercules Fundering on behalf of the general contractor KPC with the execution of the new and innovative lift cell method.
“The BAUER lift cell is an in-house enhancement of the Bauer capsule press”,
explains Dr. Joerg Zimbelmann, Team Leader of the Geotechnics Division in the Structural Engineering Department. “The capsule press is used for force measurement and – where necessary – prestressing and strutting in excavation pits.” The strategic use of the BAUER lift cell makes it possible to anticipate the pile settlement during the construction of bored piles, which makes the lift cell an interesting solution for projects with a low permitted total settlement or low permitted differential settlements between adjacent piles.
The method is highly innovative: Before the installation of the pile reinforcement, the BAUER lift cell – a kind of hollow cushion made of stainless steel – is fastened to the bottom end of the reinforcement cage. Through hydraulic lines that are guided upwards out of the pile at the reinforcement cage and accordingly also encased in concrete, the lift
Above left: To implement the construction project “Postbyen”, BAUER Spezialtiefbau GmbH was commissioned with the execution of the new and innovative lift cell method.
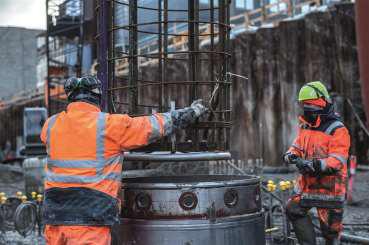
All images: © BAUER Group Above: The installation of the BAUER lift cells was carried out during the day, while injection work was carried out during the night shift to ensure completely vibrationless working conditions.
cell is initially filled with water under high pressure after the pile concrete has sufficiently hardened. This “expands” the lift cell and pretensions the pile shaft with respect to the pile base. The pressure used in this process is generally determined individually for each pile.
After a prescribed retention time for the hydraulic pressure, the lift cell is first entirely filled with a cement paste that has been tested to ensure its suitability until the planned quality is achieved. Then another injection is carried out so that after the cement paste has hardened, deformations of the lift cell are permanently excluded and the pile is fully pretensioned. “Depending on the project requirements, the lift cells are produced by our certified manufacturer with individually defined diameters and undergo a special quality inspection”, continues Dr. Zimbelmann.
To prepare for the “Postbyen” construction project, two BAUER lift cells were subjected to a load test at the Schrobenhausen location and loaded with a pressure of 120 bar – results of up to 150 bar were achieved in earlier projects. Overall, the work of Bauer Spezialtiefbau in Copenhagen included the delivery, installation and injection of a total of 101 Bauer lift cells, of which 35 had a diameter of 1,300 mm for large-diameter bored piles with a diameter of 1,500 mm, as well as 66 lift cells with a diameter of 1,000 mm for piles with a diameter of 1,180 mm. Bauer also provided a BAUER BG 36 V and the required drilling personnel as part of a contract extension. Apart from the extreme space constraints on the urban site, the sharp frost and very hard limestone in the subsoil above all posed challenges for the personnel as well as for the equipment. The installation of the BAUER lift cells was carried out during the day, while injection work was carried out during the night shift to ensure completely vibrationless working conditions. After an execution period from December 2020 to February 2021, Bauer was recently able to successfully conclude its part of the project.
The IPG
– supporting independent plumbing, heating, and bathroom stores
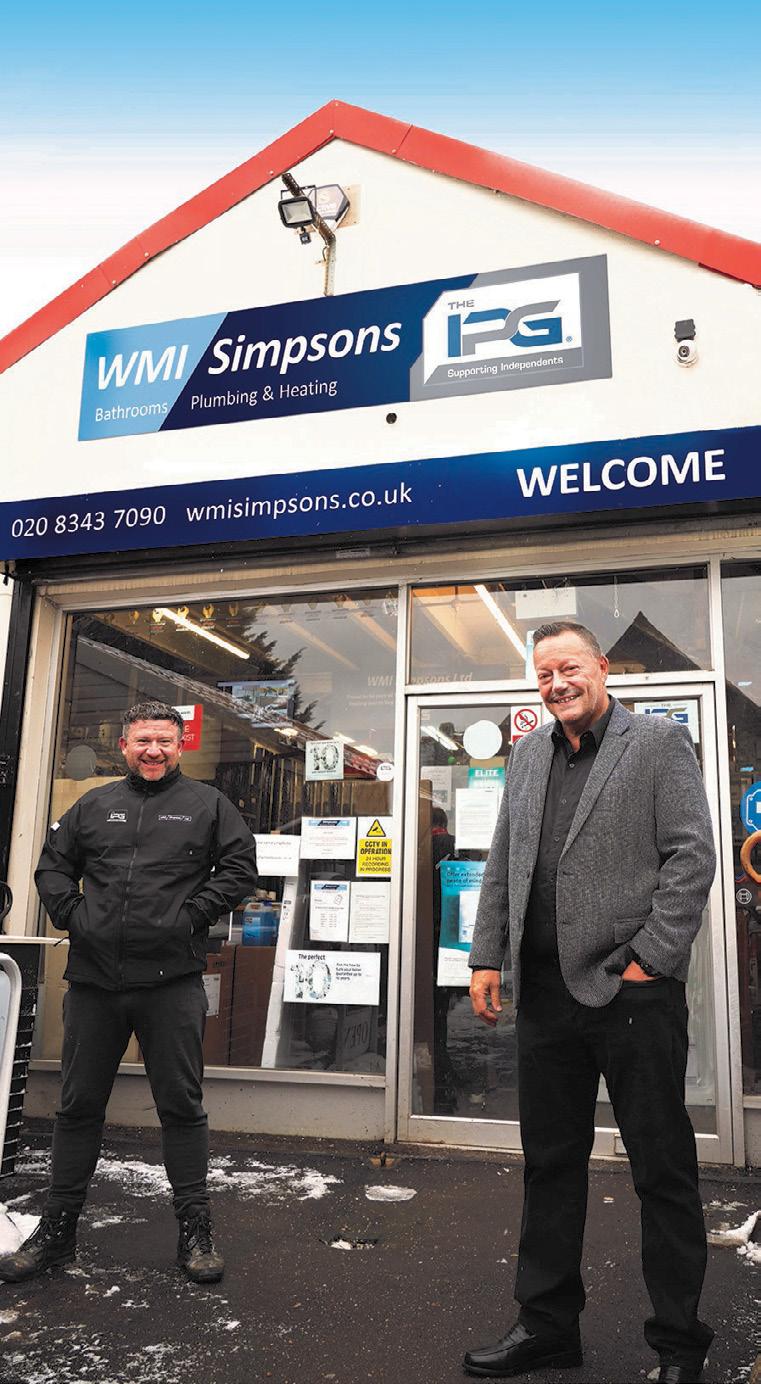
The last few months have been difficult for us all, but we have so many reasons to be optimistic.
At The IPG, we have witnessed first-hand the resilience of our members and suppliers - many have gone above and beyond to keep serving their customers.
When a business becomes part of The IPG and joins forces with other likeminded independents in the plumbing, heating, and bathroom sector, they can achieve economies of scale and have a voice that can compete with larger companies. Members benefit from each other’s success, by working together we succeed together. And, importantly, this collaborative approach enables IPG members to give their customers the opportunity to buy the best brands locally at great prices.
Some of The IPG members share their experience:
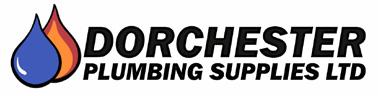
Dorchester Plumbing Supplies joined in October 2014 as they liked the idea of being part of a group which was specifically set up for the smaller independent business and liked the ‘stronger together’ ethos. Director, Steve Rolph said, “Working with The IPG gives us a voice that is heard a lot more clearly by our customers and a presence that is noticed. Being part of the group has given us the opportunity to work with suppliers and manufacturers that perhaps would not have opened their doors to us otherwise”.
WMI Simpsons situated in Finchley, London, joined in 2015. As a familyrun supplier of heating and bathroom products, Justin Protheroe, Sales Director was impressed with the passion the group demonstrated towards the independents. Recently, one of his customers commented on a favourable price that Justin was able to offer him saying that “it’s a better price than I can buy it elsewhere”, Justin
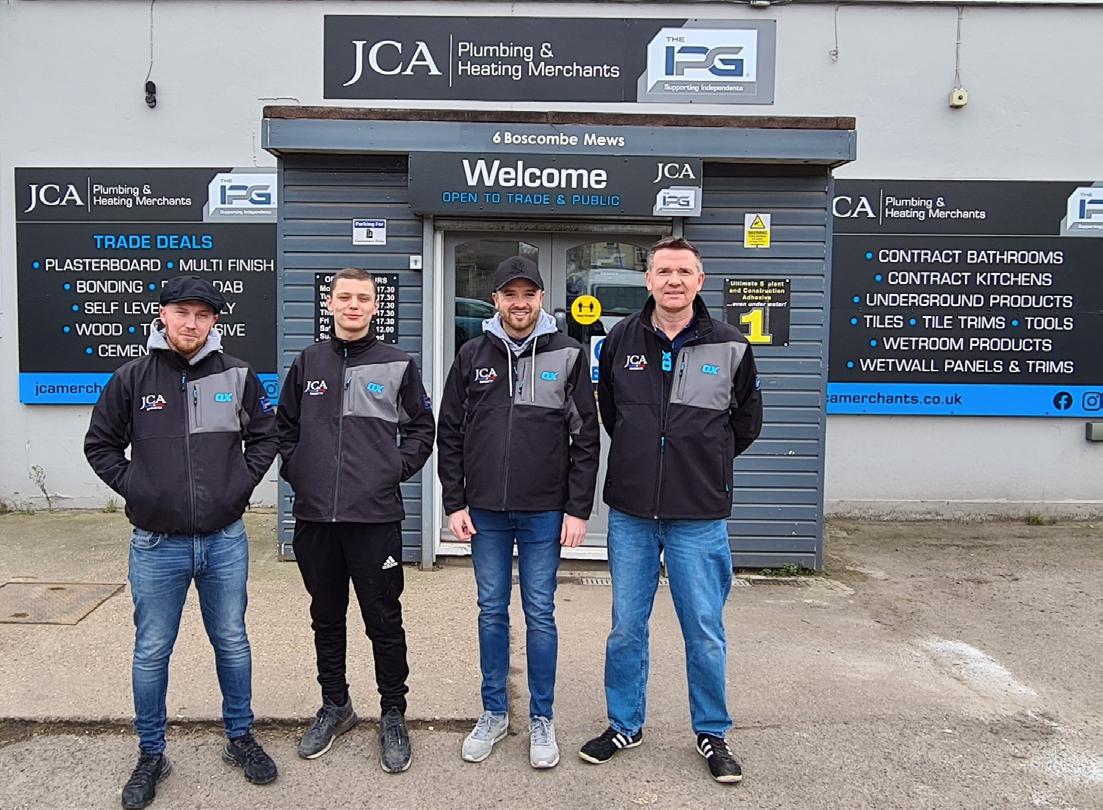
responded that it was because he was part of The IPG, who negotiate with suppliers on behalf of all their members to get favourable prices that he can pass on.
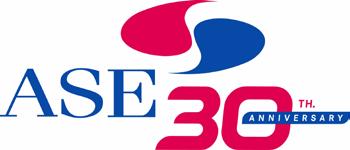
ASE Plumbing & Heating Supplies based in Ludlow is a wellestablished family-run and owned business that first opened its doors in 1988. Director, Adam Pearce, explains how the group has played a major part in its success story. “Over the past seven years, we have benefitted from several group strategies and initiatives, such as networking opportunities, marketing ideas and joint campaigns. The financial and business support provided has been second to none. The group has also helped improve our online presence by providing us with a website that is easy to update from the IPG portal and is well supported by suppliers with offers and banners. The profile of the independent merchant has been raised massively thanks to the group. The scale and strength that can be achieved together has only been highlighted through being a member.”
A new member in 2020, Howard Slowley from JCA Plumbing, and Heating Merchants based in Southend on Sea (pictured above) was attracted by the support the membership group could offer his business. Howard wanted to be “all in” on the marketing initiatives available from the start. He believes that this will benefit his business and his competitive offering to his customers saying: “I am positive about the future now I am a member of The IPG. The group has already supported my business in creating a new brand identity, new store signage and we are working together on a dual branded website, as our relationship develops, the only way is up.”
The IPG members have unique advantages that cannot always be found in larger operations, they have exceptional product knowledge, are willing to go that extra mile to support their customers, can offer the best brands at great prices and most importantly, they understand that together we are stronger!

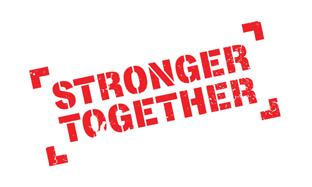
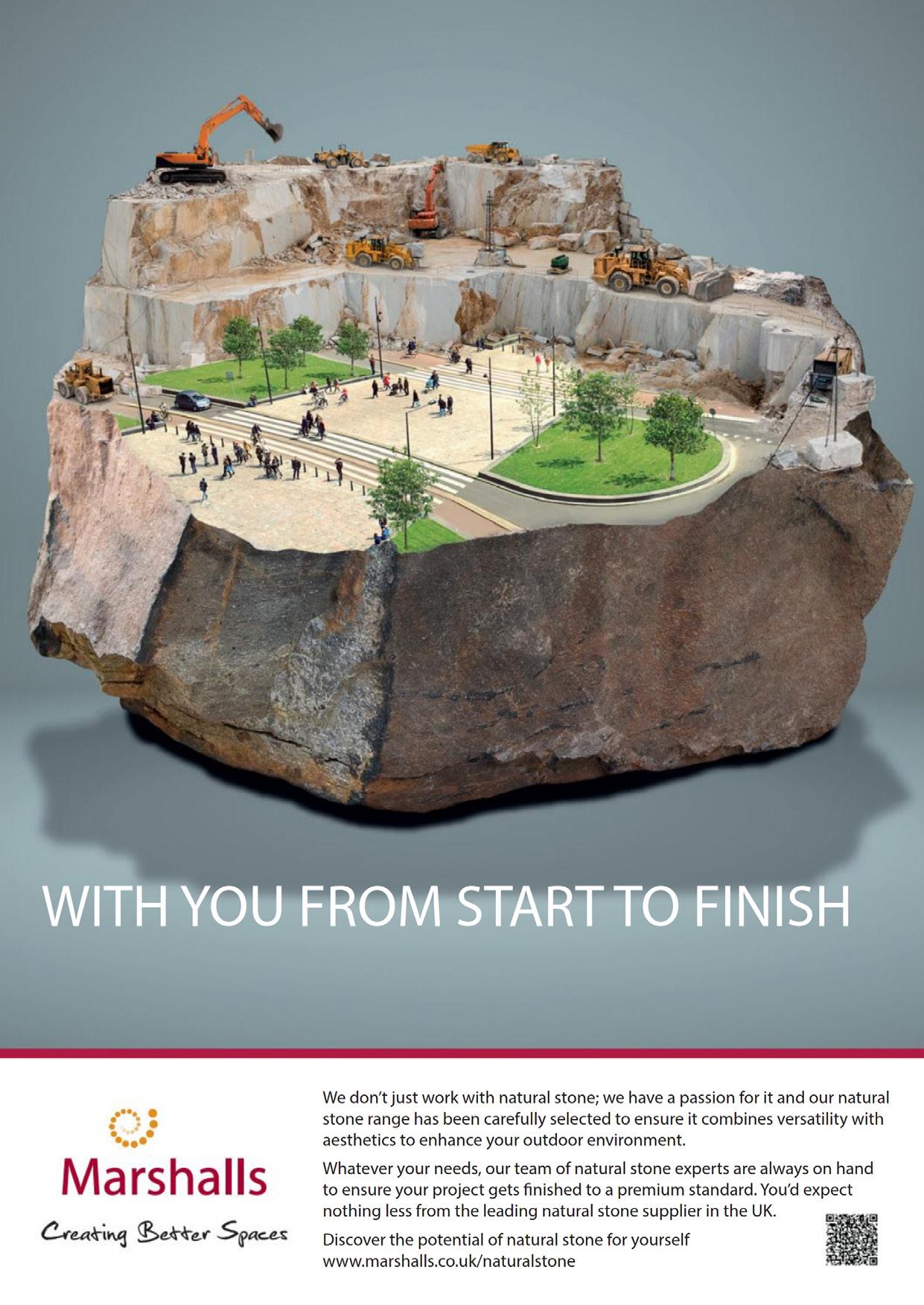
The Best Type of Flooring for Home Offices
When the coronavirus pandemic forced the UK into lockdown, millions of employees were forced to work from home. Now, as the pandemic eases, many businesses are considering allowing their employees to work remotely full time.
To work effectively at home, having a dedicated office space is essential. Those looking to create the perfect office environment need to pay attention to its design, as well as comfort. The type of flooring you choose plays an important role in the overall ambience of the office. So, which types of flooring are best for home offices?
The key factors to focus on when choosing home office flooring, are comfort, style, durability, and noise. The floor should be comfortable, enhance the visual appeal of the space, and be able to withstand caster chair use. Carpets are a popular choice for those looking to add comfort and warmth to the space. It is the quietest option, perfect for upstairs offices. Carpet tiles are easier to handle and install, and they typically provide a longer-lasting design than carpet rolls. Another durable option is vinyl. Customers have a great choice of luxury vinyl floors, each boasting a stylish, durable design. Vinyl floors are comfortable, easy to maintain, and they tend to have a long lifespan. These floors are also highly resistant against dents and scratches. They can also withstand a lot of foot traffic, making them ideal for busy home offices. Those looking to create a formal, impressive home office space should consider hardwood flooring. While expensive, this type of flooring provides outstanding aesthetics. It is tough too, though it will require a lot more maintenance than other flooring types. For a cheaper alternative, consider laminate flooring. Many laminate floors come with a hardwood design, yet they also offer increased practicality. When selecting the best type of flooring for the home office, it is important to consider how the room will be used. Will there be a lot of foot traffic and do you want to install it with underfloor heating? These are just a couple of questions you should ask before choosing the right office flooring for the home. Stories Flooring supplies a wide range of home office flooring at up to 65% off RRP. Customers can also request free samples to help them decide which floor best suits their chosen space. Stories Flooring, Unit 2 Wortley Business Park, Amberley Road, Leeds, LS12 4BD Phone: 01133200223
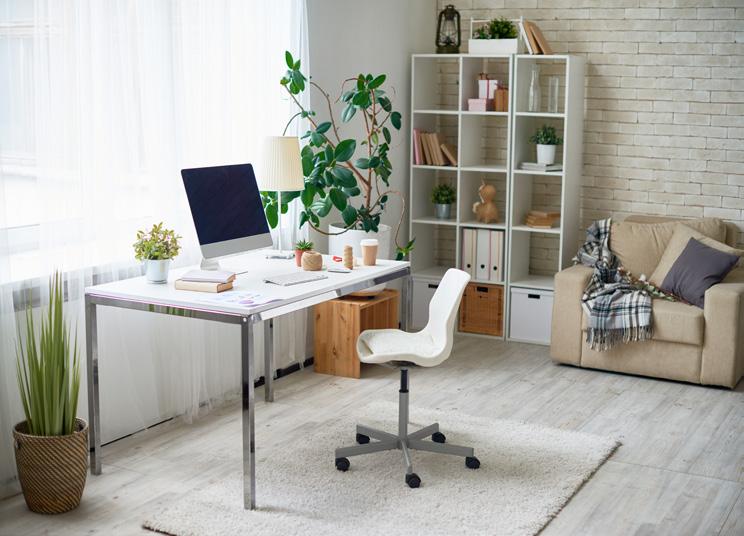
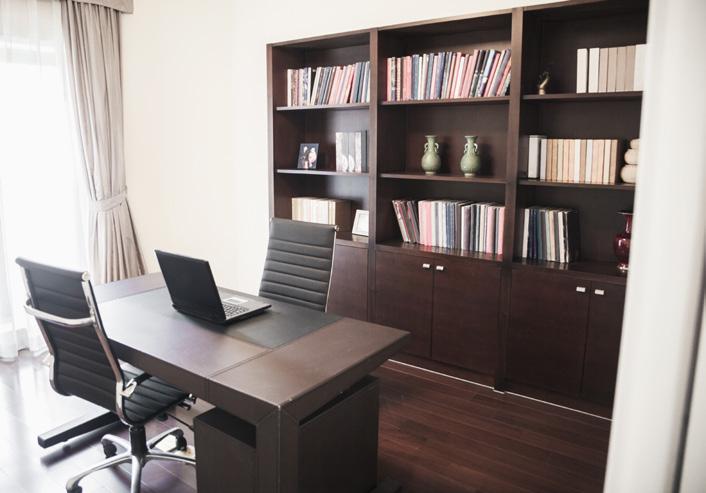