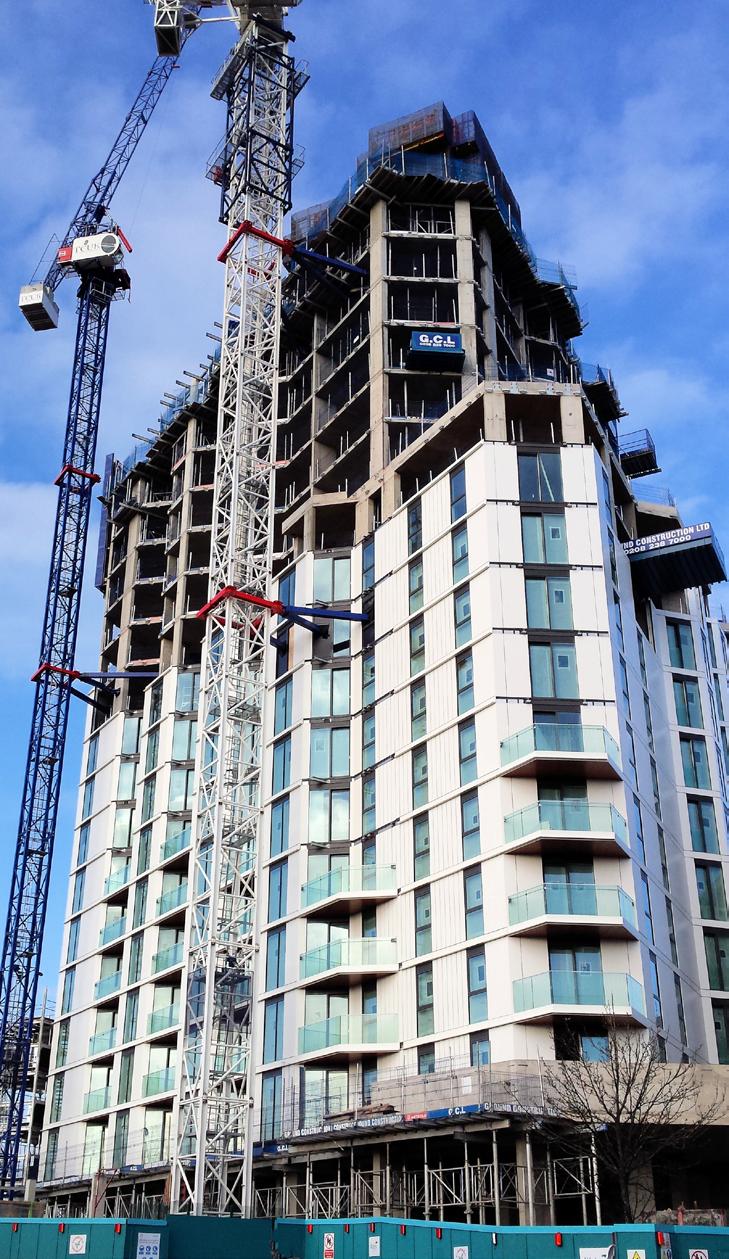
14 minute read
Buildings & Architecture
Schöck Bole prevents punching shear problems at Tottenham Hale Tower
Flat slab construction carries with it the inevitable risk of punching failure. When loads in the stress areas are increased, careful thought has to be given to criteria such as the quality of the concrete, additional reinforcement content, even enlarging the column heads.
Advertisement
These options are neither time efficient nor cost effective, and rarely solve the problem to an acceptable performance level. In addressing any potential problems of punching shear at the major new Anthology Hale Works tower needed to be cost-effective, easyto-install and certainly dependable.
At the heart of Tottenham Hale, one of North London’s most diverse communities, Hale Village is a multi-award winning urban development. It already includes a mixture of private and affordable homes, student accommodation and a range of non-residential uses including a gym, supermarket, community centre and church. Hale Village has been voted one of the top 30 best regeneration projects in the UK and the most Innovative Affordable Housing Scheme. The last piece of land currently being developed is Anthology Hale Works Tower. This elegant 108 metre high, 32 storey tower offers 279 homes and over 12,000 sq ft of mixed commercial use. There is a selection of studios, one and two-bedroom homes with other features including a 24-hour concierge, resident’s sky lounge and garden, expansive landscaping and private balconies. The striking design of the tower will act as a landmark for Tottenham Hale and Hale Village, whilst simultaneously achieving the highest design and environmental standards.
The prevention of punching failure is critical though
With flat slab construction and the increasing trend for thinner slabs, there is the inevitable risk of punching failure around column heads.
So when loads in the stress areas are increased, consideration has to be given to issues such as the quality of the concrete, additional reinforcement content, even enlarging the column heads. These options are neither time efficient, or cost effective and rarely solve the problem to an acceptable performance level.
Construction at Anthology Hale involves a single-storey basement box, partly situated above a live London Underground tunnel and bordered on one side by Tottenham Hale station, and existing buildings to the other three sides. The 32 storey building has a jump-formed core and concrete frame, with the first six levels being acoustically separated from the basement structure, due to the adjacent London Underground line. First and foremost flat slab floor is an economical form of construction, but it offers other benefits as well. The minimisation of shuttering time for example, simplification of reinforcement work, ease of underslab work such as ducting and just as importantly, the optimum use of space. column heads. None of these options is necessarily time efficient or cost effective. They rarely solve the problem to an acceptable performance level either. So the ideal solution to resolving any potential problems of punching shear needs to be cost-effective, easy-to-install and certainly dependable.
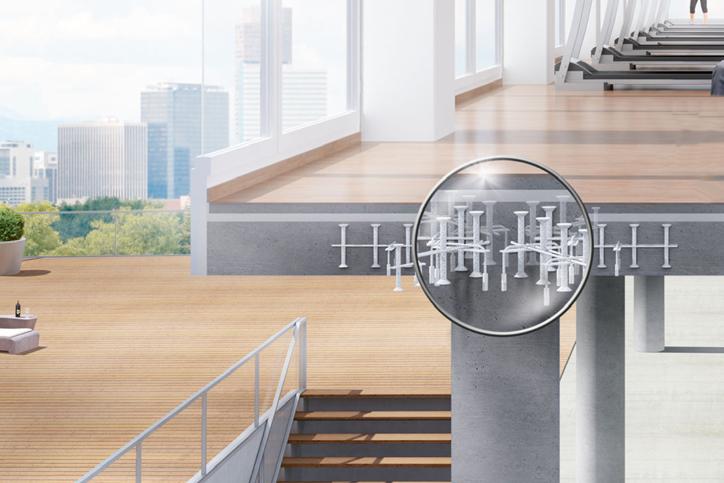
Increased shear force resistance of around 70%
However, with flat slab construction the risk of punching failure is always a critical issue. When increasing the loads in the stress areas, a great deal of consideration has to be given to variables such as the quality of the concrete itself, improving the reinforcement content and even enlarging the The reinforcement system used to prevent punching failure at Anthology Hale Works is the widely used Schöck Bole system. This reliable and trusted solution consists of double-headed studs and anchors, with spacing bars, which enable installation after the bottom reinforcement and before the top layer. Two spacer bars are welded to the vertical studs, which ensure the correct distance between uprights; and the forged stud heads guarantee a perfect finishing bond with the concrete. When compared with a typical stirrup reinforcement system, an increased shear force resistance of around 70% is achievable. It is a genuinely cost-effective and timesaving solution.
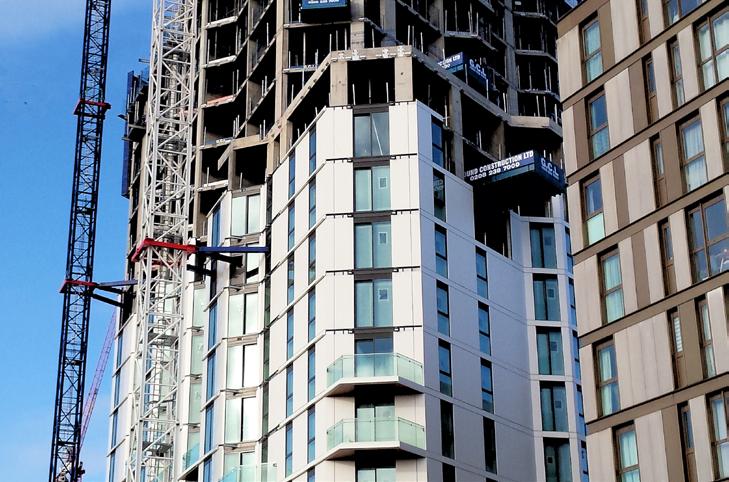
Other variants – plus Schöck design software too
In addition to the standard Bole solution, Schöck has developed three other punching shear reinforcement variants. The type U is a solution designed for installation before the lower mat; the type O is for installation after the top reinforcement layer; and the type F is designed for use in element slabs at prefabricating plants. The entire range is supplied ready for installation and provides a totally reliable solution to the problem of punching shear in flat slabs. There is downloadable user-friendly Schöck design software available too, which enables fast and simple dimensioning of the product to British Standards and the export of CAD drawings with dxf-format.
For further information on the Schöck Bole system contact the company on 01865 290 890 or visit www.schoeck.co.uk
The pioneering programme is now even easier for contractors to use.
The pioneer of ceiling recycling schemes, Armstrong Ceiling Solutions, has fine-tuned its awardwinning* programme to make it as simple and as accessible as possible.
It is now even easier for contractors to reduce their environmental impact and divert waste from landfill which also saves them money from the subsequent taxes as well as from skips and transportation costs.
All contractors are now required to do is simply take down the old Armstrong acoustic mineral ceiling tiles** and stack them on pallets. In partnership with the local distributor, Armstrong will arrange collection free of charge*** and the old tiles will be 100% recycled into new ceiling tiles at the company’s production facility in Gateshead.
The scheme for the UK and Ireland, which has been in place since 2003, enables Armstrong to minimise its impact on the environment by not only diverting its old products from landfill but also producing mineral ceiling tiles with even higher post-consumer recycled content, currently up to 82%.
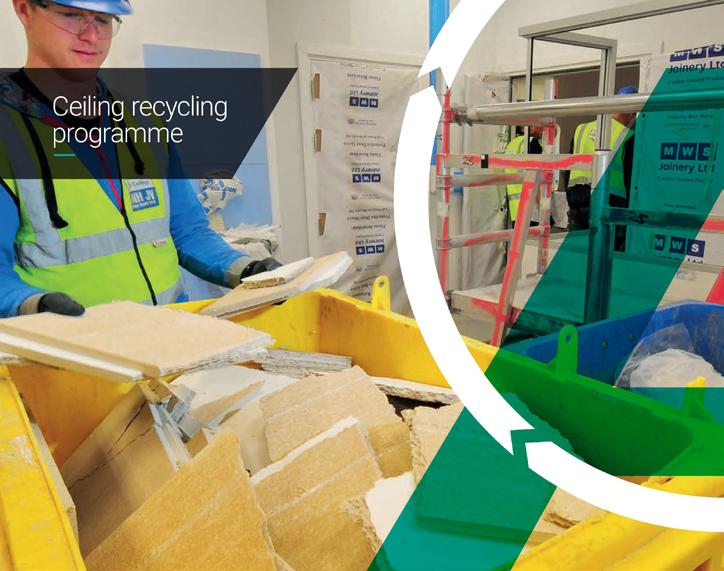
As well as the support it gets from distributors, Armstrong has also developed a “green” branch of its Omega network of approved subcontractors, specifically for those installers with proven recycling expertise .. and they claim that as well as saving them landfill tax it also makes then more attractive for main contractors to use.
Armstrong’s recycling programme for demolition, construction and renovation schemes has saved 15 million m2 of old ceiling tiles globally and diverted 61,000 tonnes of waste from landfill. And with 2,000m2 of recycled ceiling tiles equating to 7.6 tonnes of waste diverted from landfill, that is a 14,000 kWh saving on energy.
Projects have included the headquarters of main contractor Kier Construction, the temporary beach volleyball venue at Horse Guards Parade in London, and the Southern General Hospital in Glasgow.
A member of the UK Green Building Council, Armstrong also a partner in the Ceilings Sustainability Partnership, a working party of the AIS (Association of Interior Specialists) technical committee, which delivers on the actions within the Mineral Wool Ceiling Tile Resource Efficiency Action Plan (REAP). The REAP plan is intended to help the sector reduce the amount of mineral wool ceiling tiles going to landfill.
Armstrong recycling case studies also feature as WRAP exemplars, including Birmingham University Hospital where almost 43 tonnes of ceiling tiles were diverted from landfill and an estimated 19.5 tonnes of embodied CO2 were offset.
A new recycling programme leaflet, which has all the criteria information and steps to follow, is available CLICK HERE.

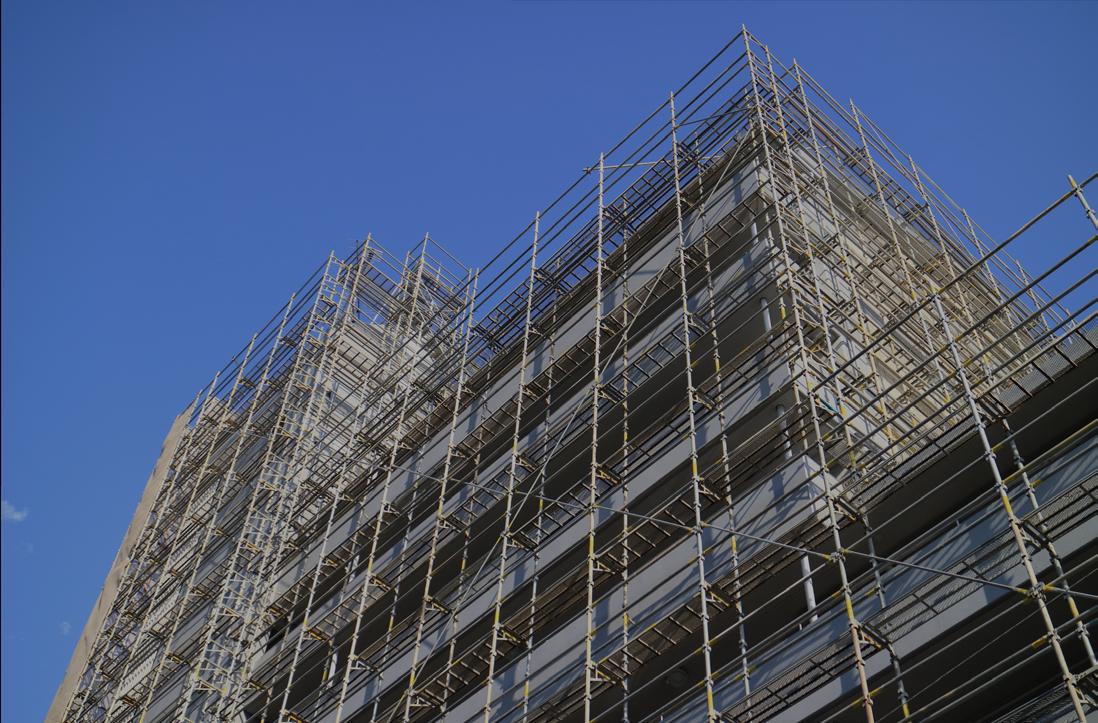
Scaffolding vs Platform Lifts: Which Should I Choose?
There has never been so much choice for trades people looking for equipment to help them work at height. And with the focus around health and safety more acute today than it has ever been, that is just as well.
Most of the options available can be broadly divided into two camps - scaffolding or mechanised platform lifts, which include scissor lifts, boom lifts, spider lifts and hybrid varieties. Scaffolding may be the traditional solution when it comes to working at height, but over the past couple of decades, the technology around lifting plant has developed significantly and soared in popularity (find out more here).
In recent years, a lot of the talk has been around platform lifts providing the better option for the modern construction worker. But is this really true? Let’s take a look at how the two options compare on three key criteria.
Ease of use
There is no doubt that scaffolding takes a considerable amount of time and effort just to get set up before you can start working. There are designs to be drawn up and/or compliance guides to follow, and putting up and taking down the scaffolding is a sizeable job in itself for a suitably qualified team.
Platform lifts, on the other hand, are much more straightforward. Instead of having to erect a structure from the ground up, you simply roll your plant into position and activate the lift. With so many different types of lift available these days,
there is an option for every type of job, from low level access to spider, boom and hybrid lifts that are not only capable of reaching considerable heights, they are also perfect for situations where scaffolding would be impractical.
In general terms, then, platform lifts save time and labour compared to scaffolding. And what really matters to businesses is, they tend to therefore work out more cost effective.
Safety
Claims are also made that platform lifts represent a safer option than scaffolding, based on the fact that they are designed to have very stable bases, aren’t prone to collapses or slippages in adverse weather and so on. But the key point here is that safety issues with scaffolding nearly always boil down to human error, whether that be incorrect installation or failure to inspect properly.
Scaffolding equipment hire is a highly specialised occupation that combines structural design expertise with a thorough focus on health and safety. The bottom line is, when designed and erected properly, scaffolding should be the equal of any plant lift in terms of stability and safety, and mistakes should not be made by certified contractors. It is often said that lifting platforms, especially spider and boom varieties, allow construction workers to reach those awkward places it is very difficult to access with scaffolding. But by the same token, a lifting platform only allows you access to one location at a time. There is mobility, but only in terms of getting down off the lift and moving the whole rig to a new position.
Scaffolding, by contrast, gives construction teams access to as large an interface as they like throughout a building at any one time. With scaffolding in place, it is easy to move from one position to another, to perform tasks in different areas. It is therefore no surprise that, while lifting platforms are ideal for quick, one-off tasks that can be completed by individuals or small teams, scaffolding remains the preference for larger-scale projects involving large work teams.
JPS Group provides a wide range of professional services to the buildings and construction trade, including scaffolding design and erection, tool and plant hire, environmental services and training. View
more here.

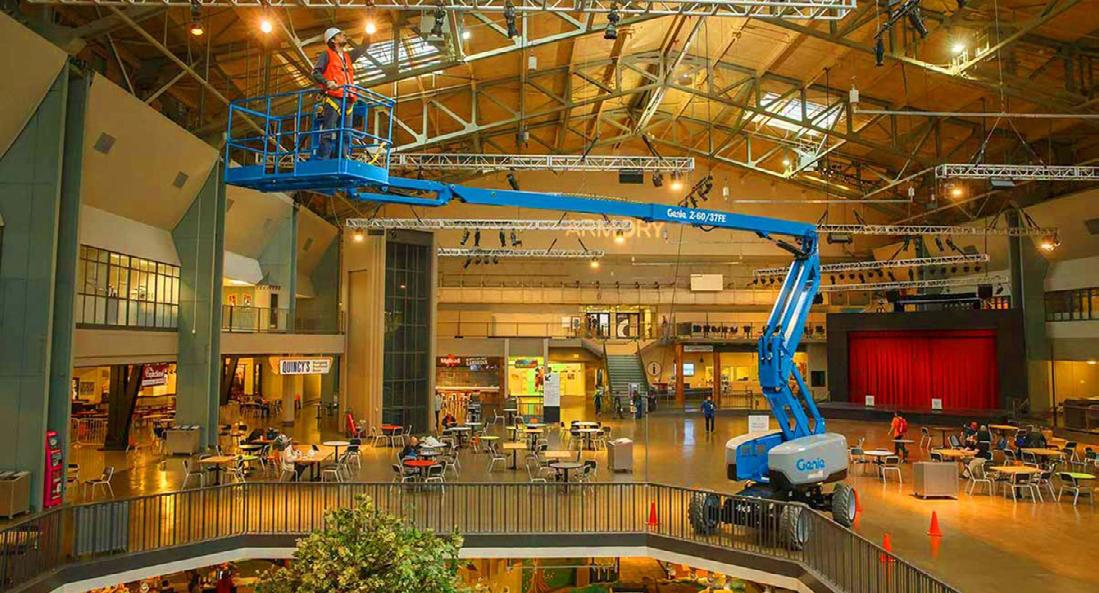
Gilberts louvres help double feed mill production capacity, safely
The safety of feed processing at the largest UK farmer-owned dairy co-operative is being protected via a patented ventilation design.
United Feeds, part of the Dale Farm co-operative, has extended its mill at Dungannon, in Northern Ireland, to double its capacity. Central to the development, built by McKelvey Construction, is a new intake building to include eight rax material bins, plus an additional loading point and weighbridge, with 10 additional finished product bins for the company’s bespoke nutritional solutions for ruminant animals.
“It was crucial the ventilation was optimised, to meet the stringent health & safety, and fire, requirements necessary in such facilities, particularly above the weighbridge area,” explained
Daniel McCrory of McKelvey
Construction. “Health & safety is paramount to United Feeds, and the new building faced essential fire safety requirements. We had to provide good ventilation because of the potential for dust, yet avoid any potential risk of water ingress as this could damage the stored feed.”
Optimum ventilation to the weighbridge and finished product bins to maintain safety inside is achieved via three-sided, 33m long louvre screens on each of the two silo towers, created from Gilberts’ patented WH75 series high performance ventilation louvres.
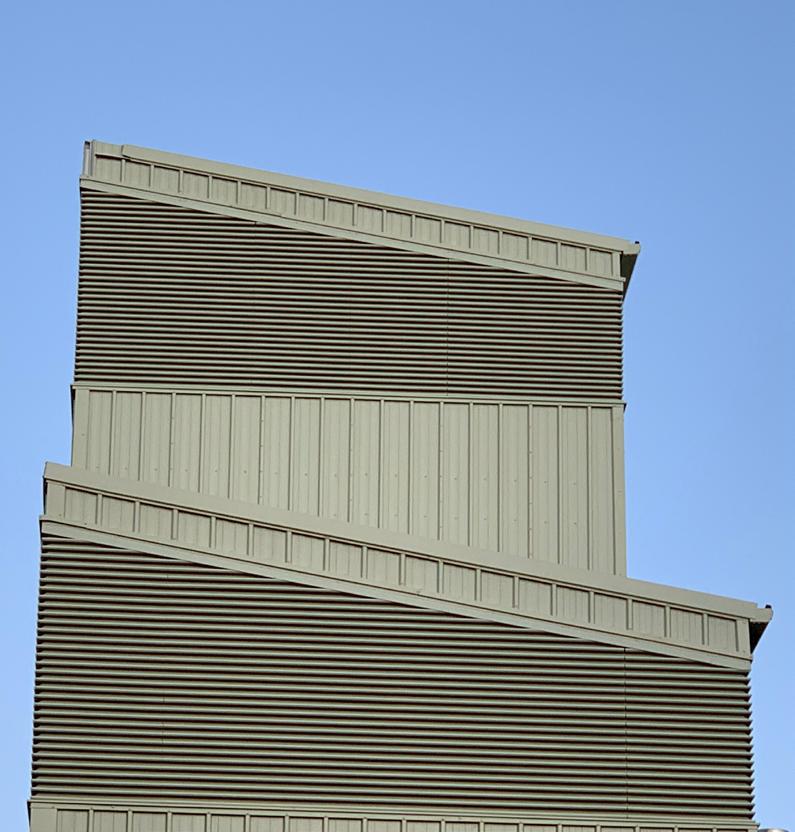
Each louvre façade was constructed on site, with each blade having to be cut to fit precisely to suit the raking head profile that graduated from 1.5m to 2.5m, and corners mitred for a flush fit.
Added Daniel McRory, “The patented design of Gilberts’ WH75 louvres gave us the ventilation and weather protection performance we needed, in a system that could be tailored to the project’s precise tolerances.”
Gilberts’ WH75 Series of ventilation louvres deliver a Class A weather rating, with low pressure loss and at least 50% free airflow area. The innovative design of the louvre blades features an integrated channel to provide optimum efficiency in removal of water from the blade face, and subsequent discharge away from any façade opening.
The WH75 louvres are just part of Gilberts’ range of louvres, grilles and diffusers that have established it as Britain’s leading independent air movement specialist, with solutions for mechanical and natural ventilation in commercial applications.
Founded over five decades ago, Gilberts Blackpool is unique in its ability to develop components- whether ‘mainstream’ or bespoke - entirely in-house, from initial design through tooling, production, testing and supply, at its 95,000 ft2 manufacturing facility. Its state of the art test centre, designed and built in-house, is one of the most technically advanced in the country.
For further information:
Gilberts tel: 01253 766911 E: info@gilbertsblackpool.com
RSS delivered the below-the-hook equipment and services, and fellow Welsh company Davies Crane Hire Ltd. a 100t capacity Grove GMK4100L. The mobile crane was fitted with a 19.6t counterweight and operated with a boom length of 52m to meet Massey Cladding Solutions’ requirement for multiple lifts to raise its roofing products. Neil Davies, of Davies Crane Hire, said: “A 100t [capacity] crane was required because of the main boom length and we needed the capacity at the furthest working radius when we were situated close to the building. The lifting frame provided control and support as the roof sheets were being raised into position.” The equipment combined as 35m-long sheets were raised via 17 separate pick points to the top of the £29m secondary school in Neath Port Talbot. Construction of the school started last September and is due to be finished by March 2021. The beam was the centrepiece of the lift but also integral to its safe completion were shackles and a variety of slings. Jack Sleeman, health and safety coordinator / hire and sales at RSS, explained the rigging configuration, involving two 22m-long outermost wire rope slings and two 18m-long wire rope slings inside them. A 13m-long wire rope sling was rigged in the centre with a two-leg chain sling beneath it to utilise two pick points on the lifting beam. Six chain slings with shortening grabs completed connection to the lattice beam, while beneath it, 38 2t capacity allow bow shackles and 19 1t capacity, 4m-long synthetic slings were wrapped underneath the roofing sheets. Sleeman said: “It was a challenging job and we had to remain patient before completing it because of the stormy weather we have been experiencing; the lift was delayed for two weeks. Once the winds had calmed sufficiently, we were able to rig our beam and sling configuration beneath the hook of the crane.” Davies Crane Hire boasts a fleet of 45 mobile cranes, ranging in capacity from 8t to 400t. In addition to Groves, it also owns a variety of Liebherr, Terex and Tadano models. Combining with a fleet of specialised transport vehicles, it fulfills lifting and other contracts in a number of sectors including steel, petrochemical, wind, energy and infrastructure. Davies added: “Business has generally been good recently, but we have endured storms and high winds in the last three or four weeks that have made it too dangerous for cranes to operate. We look forward to normalised conditions as spring approaches.” The new school is due to open in September 2021.
Rope and Sling Beam for Welsh School Construction
Rope and Sling Specialists Ltd. (RSS) has provided a 2t capacity, 36m-long lattice beam and rigging gear for lifting roofing sheets at the Cefn Saeson School construction project in South Wales.
Image: The crane and rigging gear combined as 35m-long sheets were raised.
19
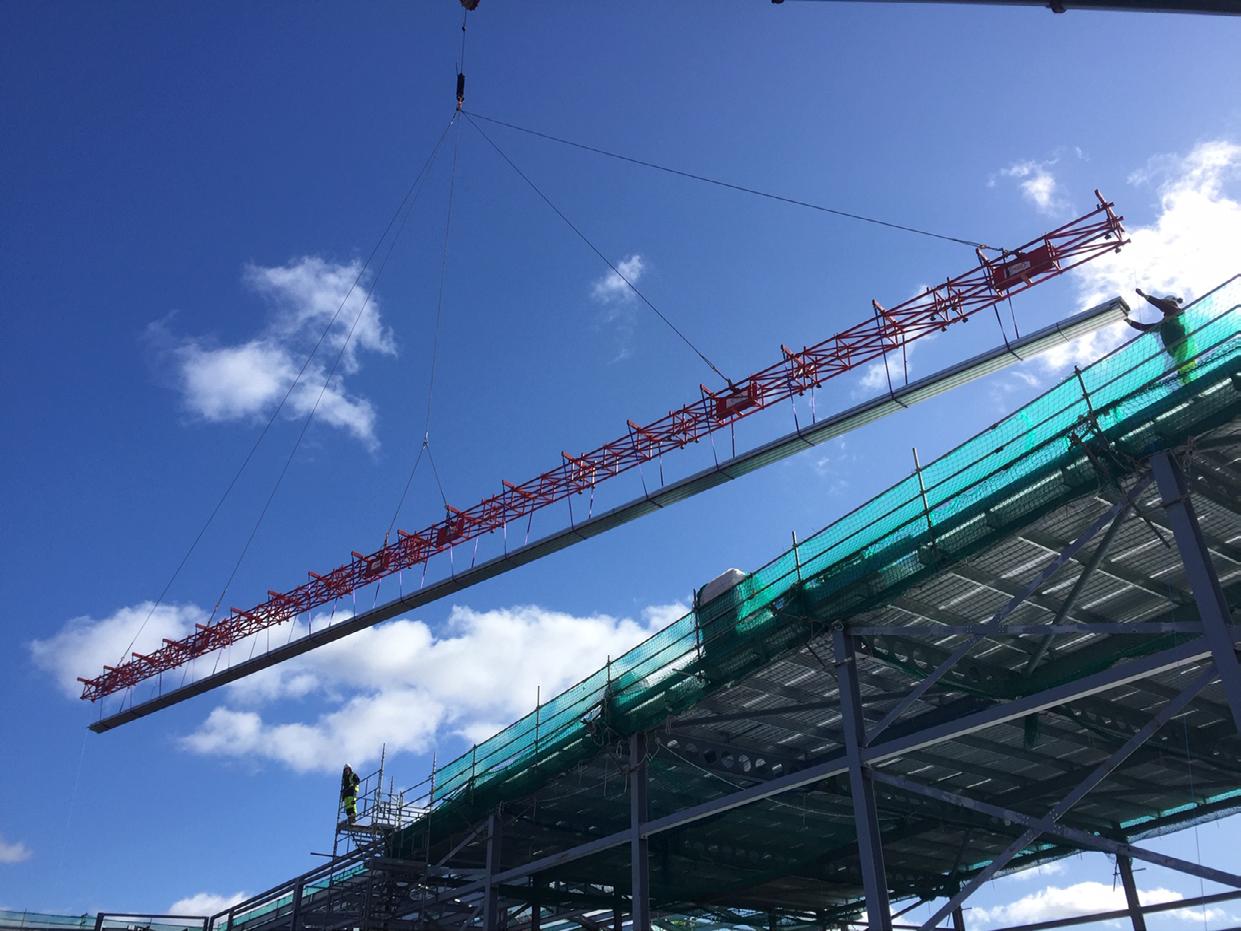