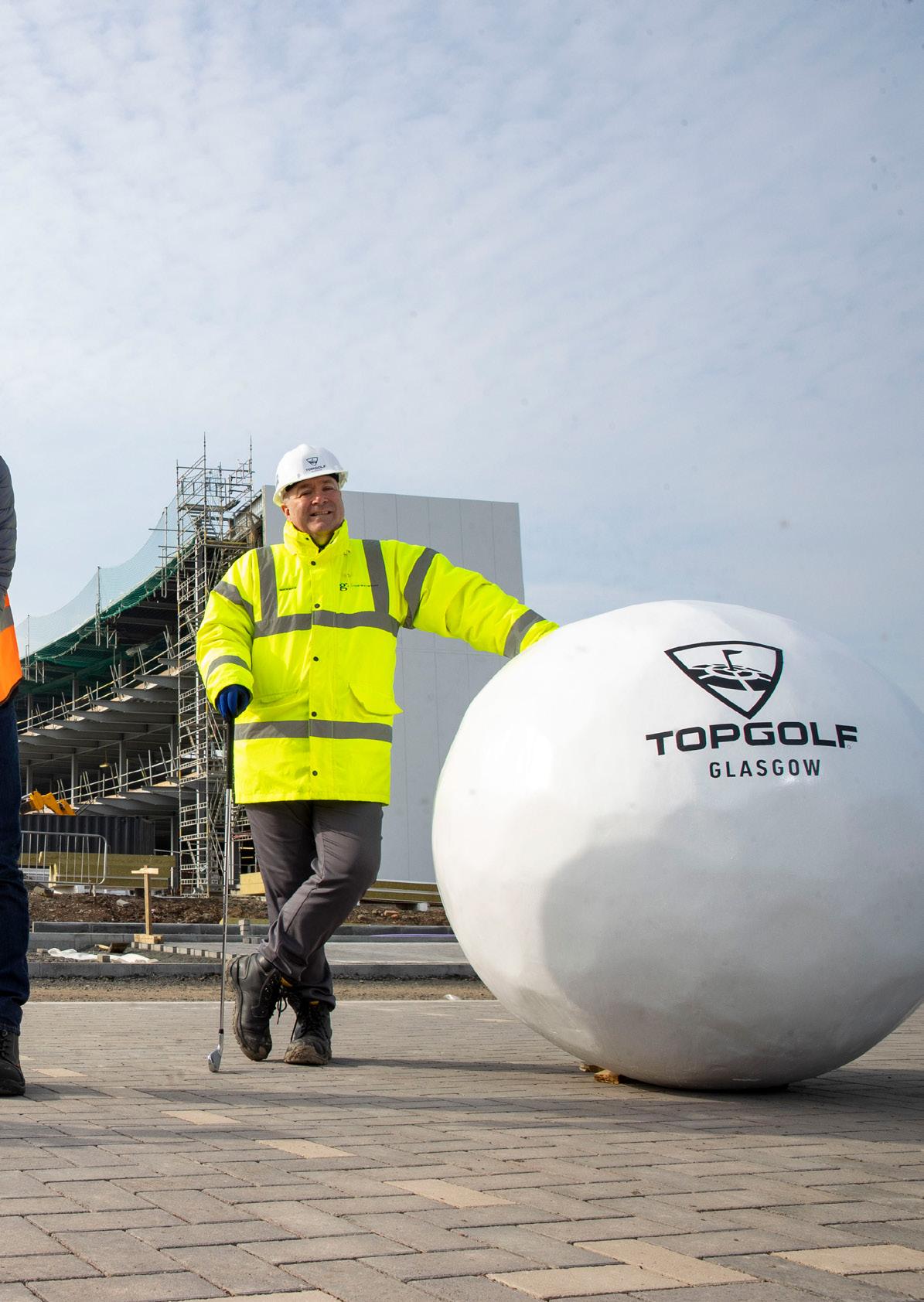
16 minute read
TopGOlf
works and it’s already starting to take shape. We’re on track for our launch at the end of this year and we’re looking forward to offering more sneak previews of what to expect very soon.”
Martin McKay, Executive Director of Regeneration at Clyde
Advertisement
Gateway said: “Clyde Gateway has worked with South Lanarkshire Council and Ashfield Land to attract investment into the site and we are thrilled to welcome Topgolf to the area.
“It is another multi-million-pound boost for Rutherglen, following the many new office and industrial buildings constructed in the last few years at Rutherglen Links Business Park and the hundreds of new jobs that it has attracted. The new jobs with Topgolf are a further economic boost for local communities and Clyde Gateway and South Lanarkshire Council are working to ensure local people have every opportunity to secure employment.
“With the nearby Cuningar Loop Woodland Park undergoing major expansion, the arrival of Topgolf reinforces the emergence of this part of Clyde Gateway as an important leisure destination.”
Mike Shiel, Senior Manager, Global Investment at Scottish
Enterprise, said: “We’re delighted to have worked with our partners to bring Topgolf to Scotland.
Once complete, its state-of-the-art complex will build on the country’s golfing heritage and support the economic rejuvenation of the Clyde Gateway area.
“Our targeted approach to attracting international investment is intertwined with Scotland’s strengths and values. With the country deservedly recognised as the ‘Home of Golf’ this is definitely a development that plays to its strengths.”
Pauline Elliott, Head of Planning and Economic Development at South Lanarkshire Council, said:
“We are delighted that such a unique and innovative development will soon be opening its doors in South Lanarkshire.
“It will create jobs in the area for local people and will of course be a real boost to the Rutherglen economy, attracting visitors from across the central belt. We look forward to continuing to support this development with all the other partners.”
www.topgolf.com
Development: Residential Site: Blackhorse View, Walthamstow Housing Developer: Barratt Homes Supplier: Miers Construction Products
Completion Date: 2021 Titon Product: Titon FireSafe® Air Brick – Double Air Brick
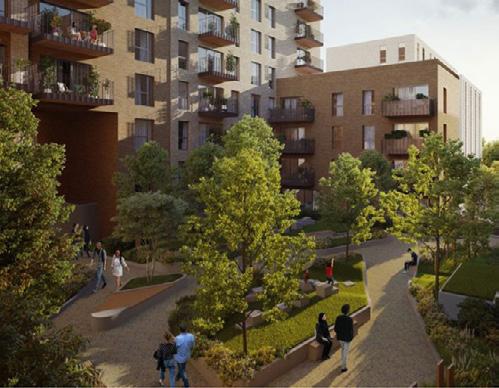
Titon Ventilation Systems new Fire Safe Air Brick® has recently been installed in the new Blackhorse View residential development.
Blackhorse View situated in Walthamstow is a brand new development from Barratt London of 350 new homes in East London. The development offers one, two and three bedroom apartments which includes a private outdoor area where residents will be able to enjoy the communal gardens. Miers Construction Products who have an expansive range of building products in their portfolio, supplied the Titon FireSafe® Air Brick to the Blackhorse View project.
The Titon FireSafe® Air Brick is a specialist product developed and manufactured by offering low resistance to airflow, but high resistance to fire as set out in Approved Document B (fire safety) volume 1: Dwellings, 2019 edition. Commenting on the partnership with Titon and Miers Construction Products, Laura French, Area Sales Manager stated: “Miers Construction Products required a solution that Titon was able to offer. The Titon FireSafe® Air Brick was developed following a tightness of construction standards following the tragedy of Grenfell. Laura continued to say “It’s been a pleasure working with Miers Construction Products and supporting their expert knowledge within the industry.”
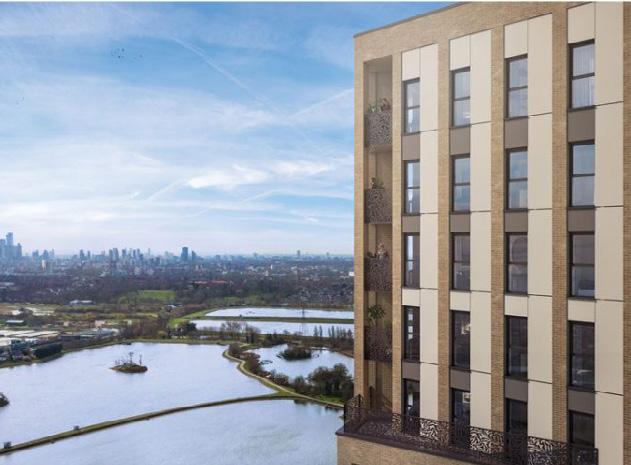
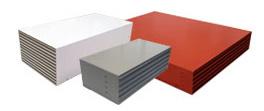
The Titon FireSafe® Air Brick is designed and tested to BS EN131412:2010 specifically for mechanical ventilation systems. Made from 1mm electrogalvanized sheet steel, fire class A1 ‘no contribution to fire’ and polyester powder coating meeting EN13501-1 classification A2-s1,d0. The Titon Titon FireSafe® Air Brick is ideal for fire safety applications.
Miers Construction Products Limited is an independent supplier of extensive products delivering from a number of locations across the UK.
How Hydroscand Reduce Costly Downtime Through Effective Hose Maintenance
Forklift trucks are an expensive asset to your company.
You invest in them because you need them to keep things moving. The last thing you want in your busy operation is for your FLT to be out of service. Downtime is expensive. Estimates on the cost of downtime range from £500 to £5,000 per hour depending on the size of your business.
The optimum way of reducing downtime caused by hydraulics hose failure is to carry out regular maintenance checks on your hoses. By doing this, you will replace your hoses when they have worn out, thereby not only increasing the life expectancy of your hose but saving time and money and decreasing the hours you are not able to use your forklift.
It is good practice at the start of each day to carry out daily inspections and visual checks of hydraulic hose lines. This way, you can minimise hose failures and call a technician quickly if there is a problem.
Forklift trucks are essential to keeping goods moving and our team have the experience and expertise to replace broken hoses quickly, minimising your downtime.
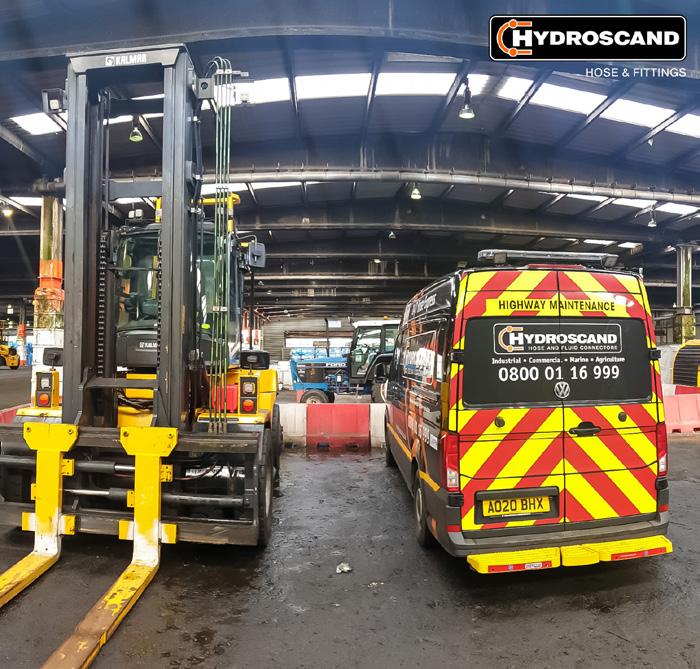
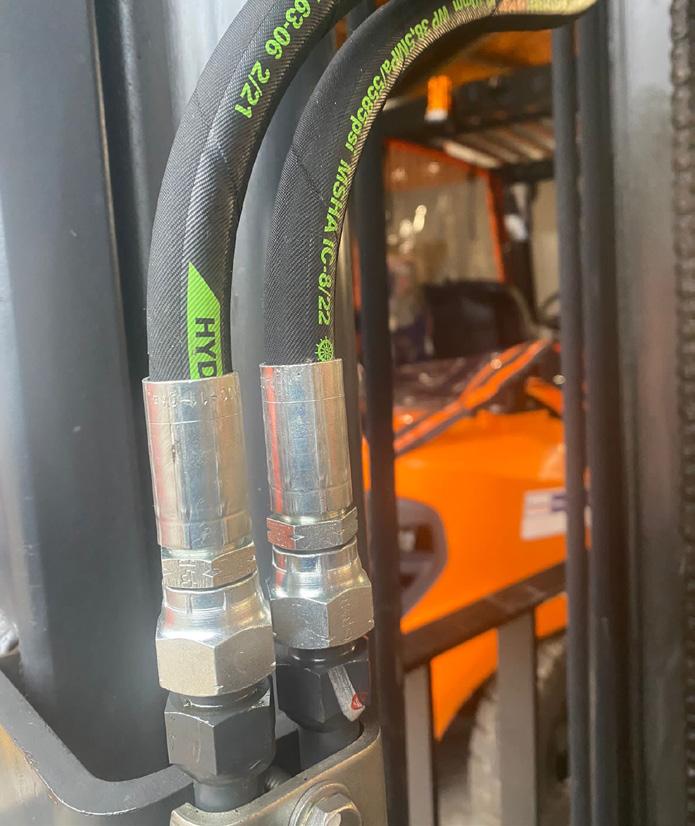
Jason Bray, HoseExpress Development Manager at
Hydroscand UK, explains: “Due to the design of forklift trucks hoses, especially on mast hydraulic hoses, are constantly under tension to enable the hoses to run smoothly over guide rollers and through clamps. Over time, due to the nature of how forklifts operate, these hoses can ‘stretch’ and ‘crack’ the outer cover of old hose assemblies. By doing daily visual checks this can be prevented by ensuring hoses are tensioned correctly.
“Hydroscand mobile hydraulic engineers while on site replacing an old hose due to failure or hose fatigue, will ensure that all hoses are visually checked for fatigue and report findings to our customer. It is about understanding why hydraulic hose has failed and supplying a solution that can prevent this from happening again. This could be for various reasons. For example:
• General wear and tear • Original hose too long for the application required • Rubbing or ‘catching’ • Incorrect routing of original hose assembly”
Our mobile hose technicians have been called out on numerous occasions to replace side shift hoses, auxiliary hoses, and several high-pressure hydraulics hoses on Combi Lift drive circuits on forklift trucks for our customers.
Stuart Larkin, Mobile Hose
Technician at our Birmingham branch, attended a job where the customer needed a repair on a forklift. He replaced two side shift hoses and cleaned up the spilled hydraulic oil. He said: “I left the job with happy customers, ready to start their days work.”
Jason Bray said: “The Managing Director of a local company called me as the side shift hoses on their forklift truck had failed. I inspected the hoses and discovered the hoses had been incorrectly routed. I had a look at routing the hose assemblies differently and after turning valve adaptors 90 degrees, new hoses were now free from being caught. Sometimes the best solution is the simplest.”
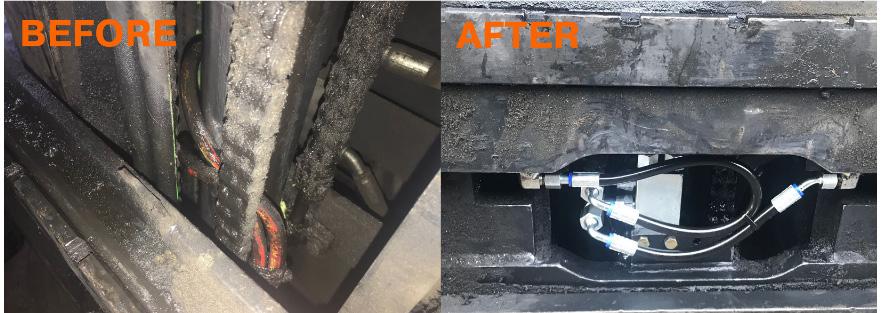
Josh Legg, Mobile Hose Technician
from our Southampton branch also replaced side shift hoses on a forklift. Josh said: “We always have our customers’ needs in mind, which helps to reduce their downtime and ensures they work efficiently.”
When Josh inspected the old hoses, he discovered they had failed. So, he wrapped plastic hose protection on the new hoses to avoid abrasion which made it better, as the old hoses were rubbing together. “The customer was very happy with the result.”
Craig George, one of our long-term
customers said: “There are hundreds of hoses that can fail on combi lifts. We use Hydroscand as they are a first-time fix. I will call Jason Bray and the job is done. I would never use anyone else apart from Hydroscand, and their prices are reasonable too. They have an electronic system, so, you can see what they have done and how they have done it.”
If you need our reliable and trusted hose technicians, call us on 0800 0116 999 or visit: www.hydroscand.co.uk/uk_en/
branches
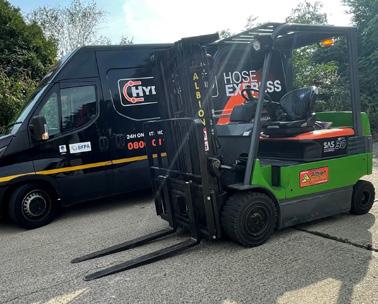
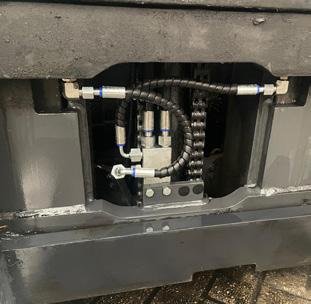
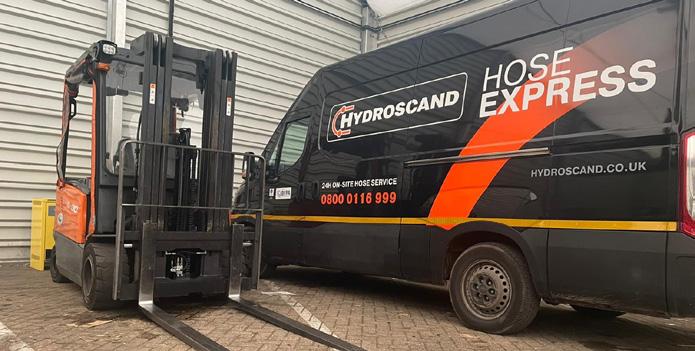
May 2022
First of its kind
made possible within the Bucket Bundie range.
- Diesel And AdBlue Bucket Bundie for J A Jackson
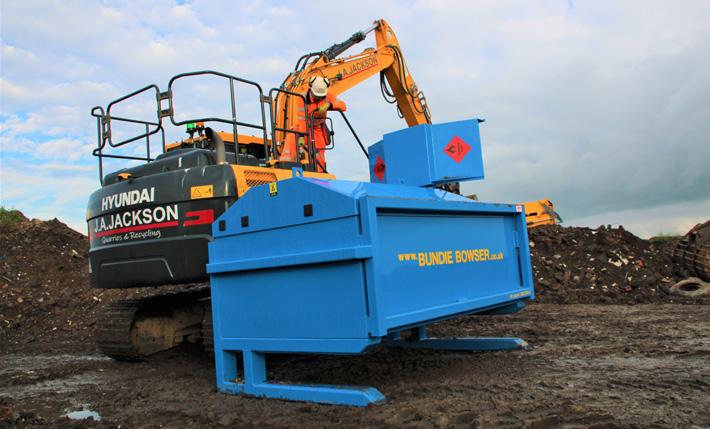
Established in 1967, J A Jackson Quarries & Recycling Ltd are a family run business who supply quarried and recycled aggregates. Providers of sustainable building materials, aggregates and ready-mix concrete, the company also provide domestic and commercial skip hire and have a fully licenced waste transfer station and facilities for inert tipping. J A Jackson operates a fleet of more than 20 tippers, artics, skip wagons and concrete mixers.
The company’s quarries in Preston,
Leyland and Lancaster are all within easy reach of the region’s motorway network making access and distribution as efficient and effective as possible.
J A Jackson have recently added the first combined Diesel / AdBlue
Bucket Bundie Fuel Bowser to their fleet provided by manufacturers,
Ace Plant.
Ace Plant, home of the ‘Bundie Bowser’ fuel storage range, are a plant hire and sales company based in Buckinghamshire who utilise their engineering roots to manufacture Fuel Storage Solutions and Dust Suppression equipment for hire and sale throughout the UK. Based on the same concept as the patented Bucket Bundie Fuel Bowser, Ace Plant’s Bucket Bundie Store was seen shortlisted in the Institute of Quarrying’s Excellence Awards in the knowledge and innovation category - a fantastic accolade for the ‘Bundie Bowser’ name.
Ace Plant have recently launched the first Bucket Bundie that is capable of carrying both Diesel and AdBlue at the same time. This capability can already be seen in Ace Plant’s static, site tow and road tow ranges but has finally been J A Jackson first found out about the Ace Plant Bucket Bundie Bowser after searching the internet about fuel bowsers. They liked the fact that the Bucket Bundie can be transported by existing site machinery without the need for a tractor. These units remove the need for lifting chains as well as the need for the operator to leave the safety of the machine’s cab to attach any chains. It features a patented bucket loading system with special slots above the support legs that allow a wheel loader operator to easily pick up and move the bowser using the machine’s front bucket. With the loader bucket crowded back, the Bucket Bundie is held securely for safe transport across rough ground – this combination works much better than a towed bowser which can be difficult to move and reverse – particularly on rough terrain. J A Jackson say that the Bucket Bundie will be a benefit to their business as the unit will result in “less risk of contamination and we no longer need to use the 5 gallon drums”. In turn, this also makes refuelling a faster and safer processes with less risk of spillage. The Bucket Bundie Bowser is available in three different capacities: 450L, 1000L & 2250L.
To find out more visit www.aceplant.co.uk or call 01908 562191.
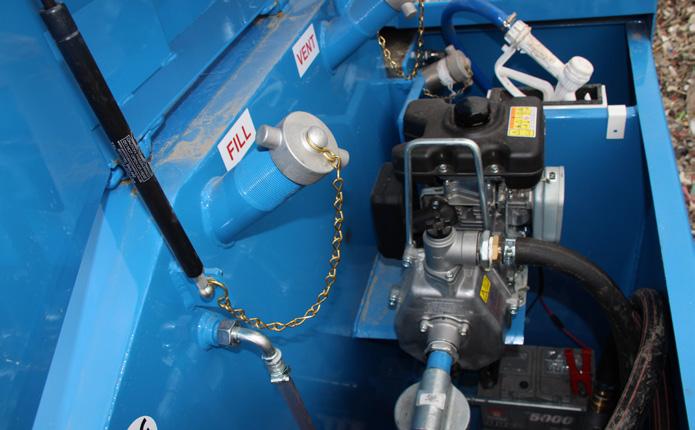
Build your own cleanroom with Guardtech’s revolutionary new Isopod Configurator tool
Controlled environment innovators unveil exciting online software allowing users to create a bespoke rapid-assembly cleanroom
THE GUARDTECH GROUP have unveiled a revolutionary new online tool which allows users to configure their very own cleanroom.
The award-winning Suffolk-based company have continued their recent trend of developing innovative cleanroom solutions with the software, which gives potential controlled environment clients the chance to select the different structural, mechanical and electrical components in their own bespoke Isopod Rapid Cleanroom.
After choosing between a Hardwall, Softwall or Hybrid base model, users can select the unit’s size, frame material, flooring swatch and glazing, as well the ISO class, lighting level, environmental control and environmental monitoring set-up.
The Isopod Configurator even allows users to fit out their cleanroom with a range of furniture & equipment options and then book both installation and validation through Guardtech’s team of experienced Installation Engineers – all with just a few clicks of a mouse!
This innovative tool will take what can be a complicated and confusing process and streamline it for Guardtech’s contented customer base. Forward-thinking Commercial Director Mark Wheeler first came up with the idea of developing the Configurator as he wanted to make the cleanroombuying sales process as smooth as possible for future clients.
“I’m delighted to launch our Isopod Configurator,” he said. “We spend a lot of time thinking about new ways to make our customer journeys as straightforward, simple and enjoyable as possible. We realise how important it is to put our clients’ needs at the heart of everything we do – and this new tool is just another step towards us offering the complete cleanroom package.”
You can access the Isopod Configurator directly via www.isopod.org.uk or by visiting www.guardtechgroup.com – and Mr Wheeler is urging anyone interested in potentially buying a new cleanroom to check it out.
“We encourage a lot of our customers to sketch out the type of cleanroom they think they need,” he added, “but this tool is a neat and effective way to quickly visualise their concept, see what they could be getting and decide whether or not it does the job they require.
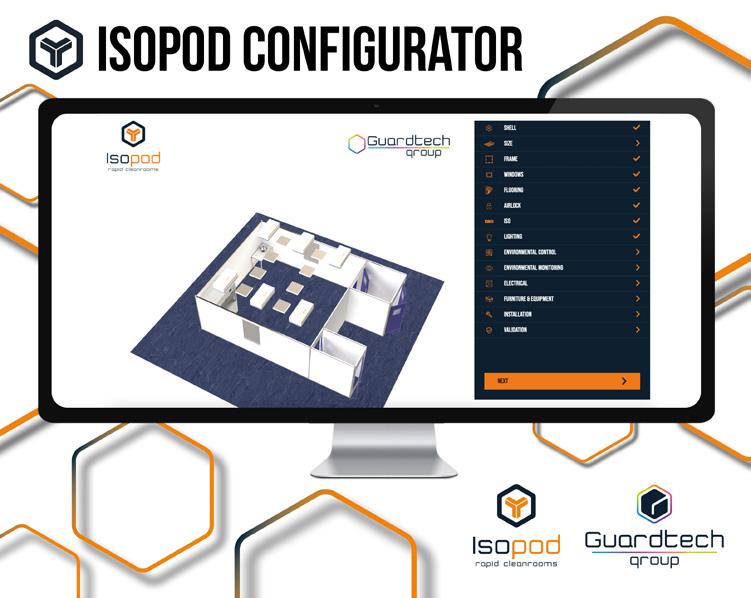
“Even if you’re looking for a controlled environment on a grander scale, I’d recommend trying out our Configurator first, as it will just help to give you a bit of insight into the key considerations of your build.
“We can then work with you to determine whether or not Isopod is the solution for you, or if a Guardtech Cleanrooms modular build or Cleanroom Solutions turnkey package might be more appropriate.”
For more information on the Guardtech Group, visit www.guardtechgroup.com, email sales@guardtech.com or call 0330 113 0303.
Waterloo’s Collaborative Approach Supports New British Motorcycle Marque, Solihull
An iconic British motorcycle marque has moved into its new production facility at Solar Park in Solihull, with air distribution products supplied by Waterloo Air Products.
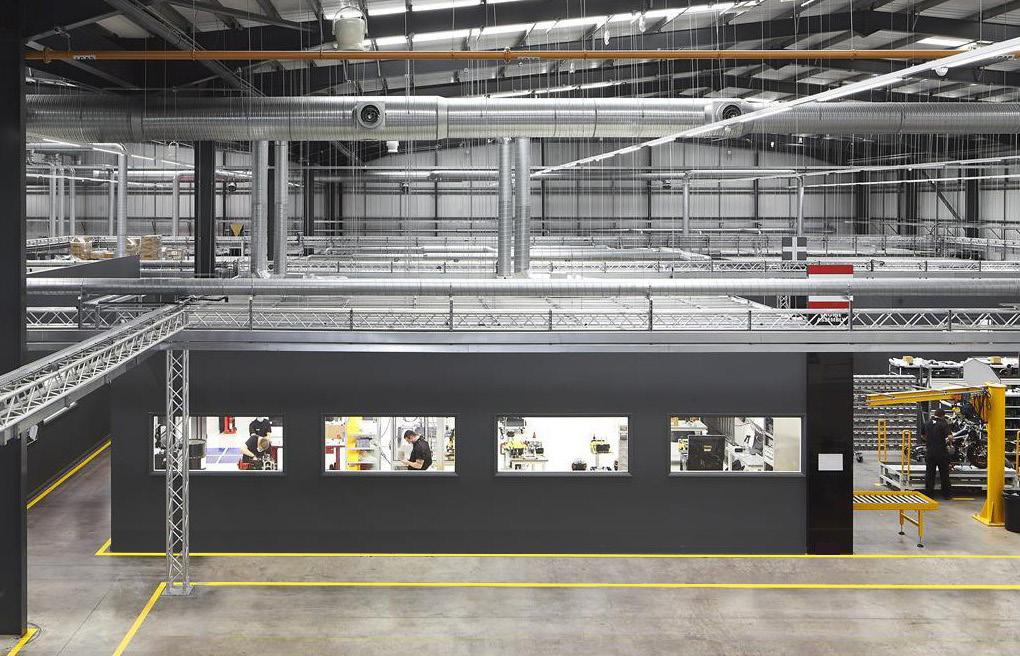
Speed was of the essence with this project in more ways than one, with a turnaround time of only two months from tendering to completion. Working with contractor Aldridge Air Conditioning, Waterloo was chosen to supply a range of diffusers to suit the differing requirements of the main manufacturing floor, engineering and testing rooms, office space and the customer-facing reception area. Converting the former distribution centre into both a manufacturing floor and office space required an air distribution system designed to create a healthy environment for both machinery and people. At the same time, the aesthetics of the products used were a vital consideration to reflect the brand and provide the perfect backdrop for the luxury motorbikes. Waterloo’s extensive range of products and ability to respond quickly to ongoing adjustments to the design provided the agility and flexibility required for this type of refurbishment project. The air distribution system for the manufacturing floor where the motorcycles are hand-built has been fitted with Waterloo’s RWH High-Flo Jet Diffusers. These models are designed to handle high air flow rates and provide relatively long throws, making them particularly suitable for this kind of large open space. The innovative reversible and rotatable core design of the RHW diffuser allows for the air jet to be adjusted for both pattern and deflection for increased flexibility of application. Adjoining the manufacturing floor are a range of smaller offices used for engineering design and testing. These workspaces have been designed with exposed services, a factor which presents specific product requirements for both appearance and performance. Waterloo’s solution for this application was the Circular Plate Vane Swirl Diffuser (SDVC) which was supplied with a powder-coated finish to match the exposed duct work. For the main offices, which are served by a local heat recovery unit, Waterloo specified a Square Plate Vane Swirl Diffuser (SDVS) which could be mounted within the gridded or plasterboard ceilings. Waterloo’s Vane Swirl Diffusers are designed for these kind of office areas where rapid mixing of air supply is required in rooms of ceiling height between 2.6m and 4m. Commenting on the suitability of Waterloo’s products for this refurbishment, Glynn Taylor, Project Engineer at Aldridge Air Conditioning, said: “Product design and versatility is not the only reason why we chose to work with Waterloo for this project; equally important is the excellent working relationship that we have with the team. We know we can rely on Waterloo to support us every step of the way with technical queries and ongoing customer service after the project has been completed.” Waterloo is proud to be associated with a moment in British automotive manufacturing history.
West Fraser Commits To GHG Emissions Reductions Through SBTi Process
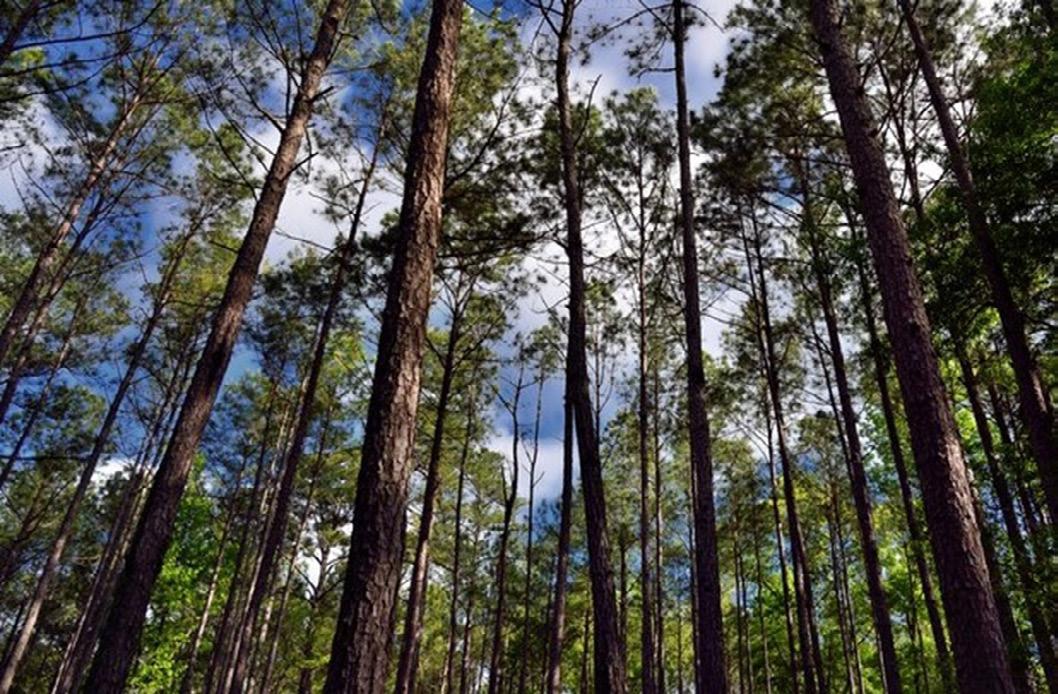
West Fraser has announced a commitment to set science-based targets to achieve near-term greenhouse gas (“GHG”) reductions across all its operations located in the United States, Canada, United Kingdom and Europe
As the world’s largest producer of lumber and oriented strand board (“OSB”) and a leading manufacturer of other engineered wood and forest products, joining the Science Based Targets Initiative (“SBTi”) demonstrates the Company’s commitment to sustainability leadership and contribution to global climate action. SBTi helps companies to set emission reduction targets in line with climate science and Paris Agreement goals. It promotes best practice in science-based target setting and independently assesses companies’ targets. To accelerate corporate climate action, SBTi is focused on significant reductions in global emissions before 2030 and achieving net-zero emissions before 2050.
“Committing to science-based targets through our SBTi pledge is a natural next step for West Fraser,” said Ray Ferris, President & CEO, West Fraser. “By committing to reduce emissions in line with climate science and align with the Paris Agreement goals by 2030, we are building on our solid legacy of sustainability performance of our products while enhancing the social, environmental and economic benefit in the communities in which we operate.” West Fraser has set the following specific GHG reduction targets: • Reduce direct emissions under West Fraser’s operational control, Scope 1 GHG emissions, and indirect emissions from purchased energy, Scope 2
GHG emissions, by 46.2% by 2030 from a 2019 base year. These reductions are in line with a scenario which limits global temperature increases to 1.5°C, compared to pre-industrial levels. • Reduce all other indirect emissions within West Fraser’s value chain, Scope 3 GHG emissions by 25% by 2030 from a 2020 base year. Scope 3 GHG reductions align with a scenario which limits global temperature increases to well-below 2°C, compared to pre-industrial levels. To achieve these goals West Fraser will expend capital and adapt some operating practices, which will have broad benefits that improve our business. The Company’s capital plans from 2022 forward include projects that will make reducing GHG emissions a priority. It is expected the average annual capital expenditures on GHG reduction projects to be approximately $50 million and fit within the overall capital budget going forward. West Fraser anticipates investing at least $400 million before 2030 to achieve our targets. The SBTi process is initiated with a letter of commitment and provides a period of two years to develop targets for SBTi validation prior to organizational communication and disclosure.
About Science Based Targets Initiative The Science Based Targets initiative (“SBTi”) is a global body enabling businesses and financial institutions to set ambitious emissions reductions targets in line with the latest climate science. For more information about SBTi, visit: sciencebasedtargets.org