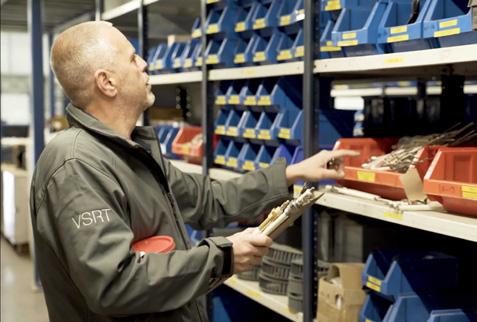
3 minute read
The Key to Keeping Your Boiler Plant Operational

In this article, Fulton’s Leigh Bryan looks at the strategies available to lessen the impact of boiler plant downtime and breakdowns and considers the impact of national and global supply chain issues.
Advertisement
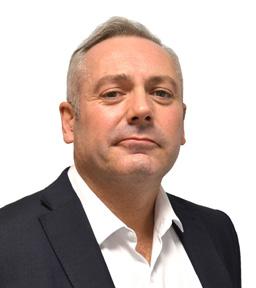
Ask any engineer what the ideal steam boiler setup is to cover breakdowns and scheduled maintenance and they’ll tell you it’s simple, employ an N+1 (spare boiler) strategy, where you always have one boiler available as a spare to operate as backup.
However, this is not always practical. Common reasons include footprint issues, where there just isn’t enough room available to fit the extra equipment into the plantroom; or a financial decision when, by tying up capital in a ‘spare’ piece of equipment, those funds could be used elsewhere in the business.
Whatever the reason and no matter how well the boilers are maintained, the likelihood is that at some point there will be an occasion where a boiler breaks down. It could be a perishable item such as a gasket or sight glass that fails, or other components incorporated into the boiler pressure vessel including level probes or steam/water valves. Of course, good, accurate water treatment and correct load matching to the boiler help prevent failures that occur from corrosion or erosion, but they cannot be completely prevented.
Then there are the wear and tear items including motors and their actuators or switch gear; manual and automatic valves where packings and seals will gradually perish; ignition probes and ionisation rods that eventually burn away; and reactive components such as UV cells that degrade with time.
And let’s not forget recent global supply chain issues, which have seen almost all products impacted by extended lead times, with some not just increasing by days, but weeks or even months. It is therefore worth taking into consideration the spares kept on site, as supply of the most basic components are also being affected and may not be available exstock or at short notice.
So where does this all leave the customer? In an ideal world – supported by the Original Equipment Manufacturer – while companies including Fulton are doing their best to hold relevant stock, they are still like everyone else, subject to delays in obtaining raw materials and parts to replenish their own stock levels.
Even if items are held in stock, there is the delay in getting it to the customer, which generally means a lead time of 24h hours on an overnight delivery and sometimes 48h to remote locations. So even if you only consider the timeframe from the point of diagnosis of a known fault, to the part or parts arriving at your facility and being installed, these delays to production, or temporary closures of facilities due to steam being unavailable for the processes, are costing facilities dearly in downtime and lost production for the sake of a relevant spare part.
So, if you’re not operating an N+1 strategy and don’t have that spare boiler in place, holding your own spares is of vital importance to ensure overall equipment and process efficiency.
At Fulton, we help clients make that informed decision. With our product and industry knowledge, we produce full spares lists for our own heat transfer solutions and even those of other OEM steam boilers, but rather than leave it there, we identify components that are considered ‘highly-recommended’ due to a higher risk of failure or long lead times. We simplify this further with a traffic light system that highlights, from green to red, the criticality of a particular spare part. By keeping it simple yet effective, it allows our clients to make informed decisions, selecting the most relevant equipment for their site held spares and working on a package to suit their budget.
On those occasions where clients look at the risk and possible financial implications and chooses to hold a full spares package, Fulton recognises that everyone is in the same current global economic situation together and acknowledges our client’s foresight by providing good discounts to lessen the fiscal impact to their business.
There really is only one way we all come out of this economic squeeze in one piece, and that’s by working together. Maybe it’s time to re-evaluate the N+1 philosophy, and to recognise Fulton can be that +1 to your boilers and your business.
For further information please visit www.fulton.co.uk.