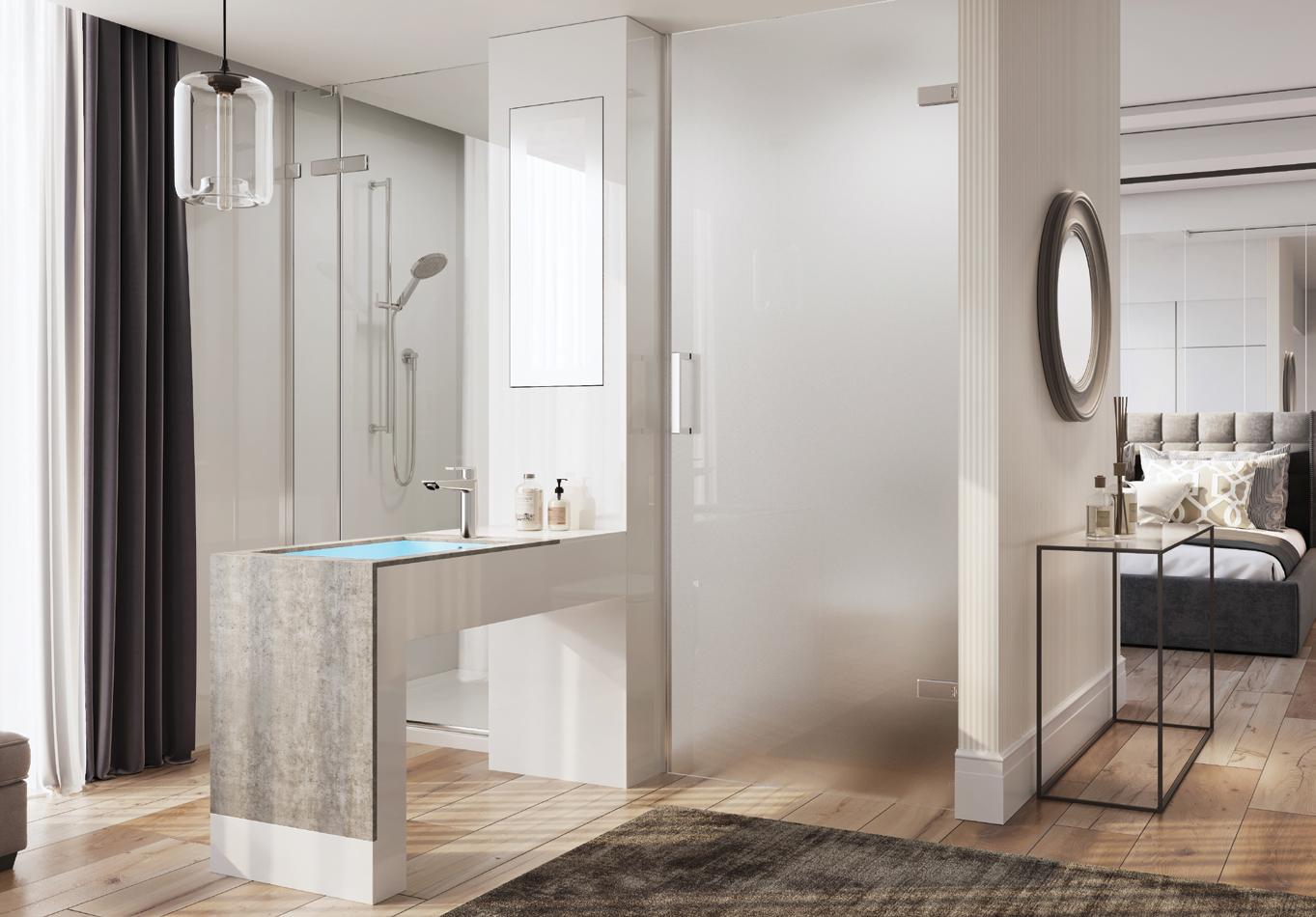
7 minute read
Sustainability
Hinged shower door with in-line panel and frosted hinged toilet door with chrome fittings. Solid surface illuminated basin unit with inset concrete effect panel and integrated mirror column.
Roman has been designing and manufacturing showering solutions for over 35 years, and is home to the UK’s largest manufacturing plant. All Roman products are designed and created in Britain, offering the ultimate in quality, precision and craftsmanship
Advertisement
▪ UK Manufacturer
▪ Dedicated In-House Design Team ▪ Supplier to Major International Hotel Groups ▪ Bespoke Product Capability ▪ Experienced in Large Project Work ▪ Solid Surface Fabrication
▪ Products Exceed all Compliance Standards ▪ Global Manufacturer to over 60 International Markets
▪ Promotes Sustainability and Circular Economy
For more information please visit our website: www.roman-showers.com
Underfloor heating helps homeowners take back power on energy costs
Paul Simmonds, Digital Marketing Manager, Wunda Group
There’s a lot to be said about waking up on a cold morning and having warm tiles underneath your feet. The pleasure of not feeling any draughts or cold spots in your home as you get ready for the day is a luxury. However many people worry that these luxuries come at a price.
T
here is a growing concern that energy bills will skyrocket due to the increase of remote working. Energy bills are predicted to rise by 18% for home workers this winter, and heating experts, Wunda Group, want more people to consider the energy saving benefits of UFH.
How much energy does UFH use? Water based UFH, which runs through a series of pipes connected to a boiler, uses much less energy than central heating as it is designed to run at a lower temperature whilst providing a more comfortable level of heat. However, costs and efficiency will differ depending on construction, insulation, energy tariffs and how the heating is being controlled. For example, a room size of 40m² would cost around £900 per year to heat using electric UFH, whereas a water based UFH system would only cost about £180 per year.
UFH uses less energy than standard radiators, and is designed to be more efficient at circulating the heat around a home and running at a lower input temperature. Where a radiator may require the water to be heated to up to 90°C, UFH can function as low as 35℃. However, running costs depend on the quality of the insulation in a home, how high the temperature in the room needs to be and how often the heating is on. •34•
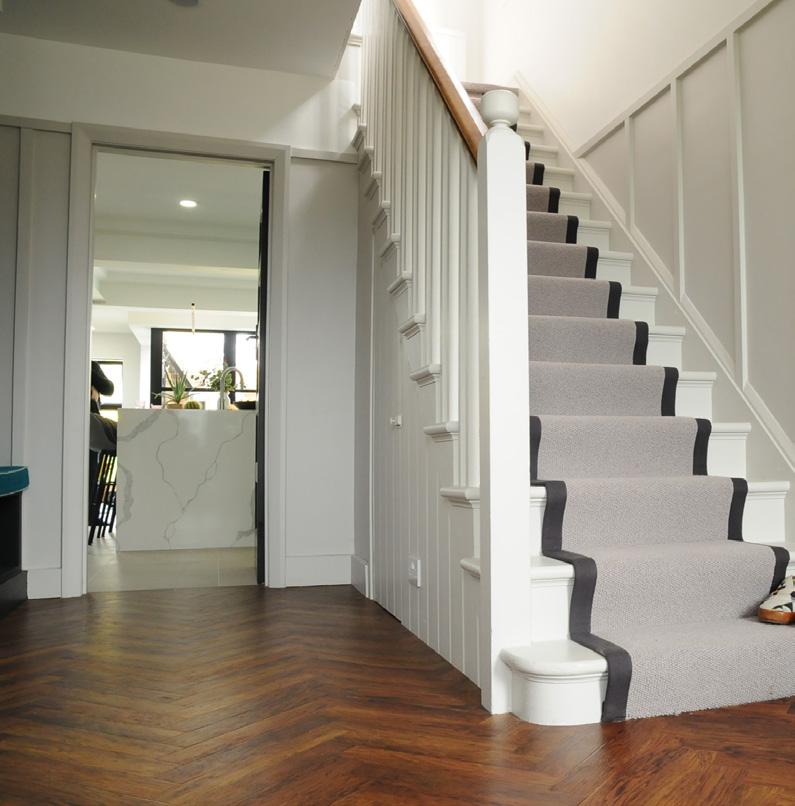
How to use underfloor heating efficiently Many guides and articles cover how to make sure your boiler is running efficiently, but using UFH effectively is not always covered. To keep the costs down over the winter, there are a few key things to consider:
• If you have a screed system use your thermostats setback feature - Heating screed from cold can be costly in time and energy, fortunately most thermostats feature a setback option, which allows you to set a “point of quick return” and if on those cold days the temperature drops below your setback, your screed floor heating can spring into action.
• Improve your home’s insulation - Insulation in the home works to keep the heat in and reduces the amount of warmth that escapes through the walls, windows and roof. Newer homes tend to be more environmentally friendly and are often well insulated, but older homes are likely less insulated
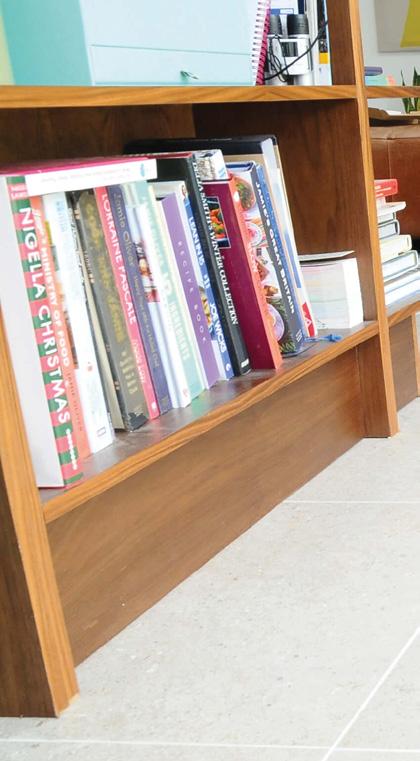
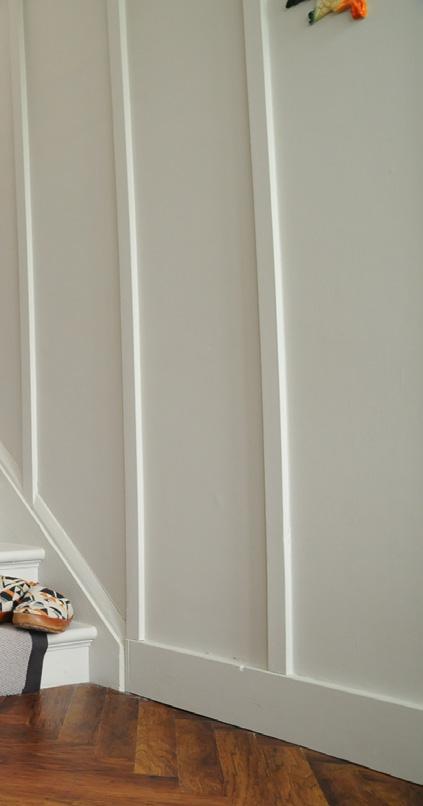
and will need upgrading. By using an EPS floor heating system that retro-fits, you could benefit from additional insulation in your floor just from installing the floor heating boards. Be sure to ask your supplier about any test insulation value in the floor heating fixings.
• Consider a future-proof boiler alternative - Heat pumps naturally complement UFH as they supply a cost effective and steady temperature for homes. Depending on your property and the amount of heat it loses, a ground source or air source heat pump will be recommended, but UFH can be used with most boiler alternatives.
• Only heat when it is actually needed - It is possible to save energy by not using UFH all the time in every room. It is a good idea to limit the heat in the rooms that are used the least. With today’s technology most
UFH systems allow users to zone various rooms. Just by turning the less frequently used rooms down to 16/17℃ is enough to make a difference to a home’s energy consumption. Wundatherm’s Rapid Response® system is incredibly easy to install, with no mess or drying time and is extremely durable, as well offering an increase in thermal insulation. The lightweight low-profile boards are just 16 or 20mm thick, heat up in minutes and are suitable for any floor finish including carpet, vinyl, Karndean, Amtico, laminate, wood, ceramic and stone tiles. Once installed, the floor heating pipe is laid into the preformed grooves in the boards and the system is ready for immediate use.
Wundatherm is totally future-proof and perfect to use with both boilers and future heat sources. With home heating accounting for 21% of our carbon footprint, homeowners must stop using fossil fuels to heat their homes in favour of sustainable green energy heating, in order for the UK to meet its climate change goals and get to net zero by 2050.
For further information on the Wundatherm UFH system or a free estimate, call 0800 083 2677, email plans@wundagroup.com or visit the website at www.wundagroup.com
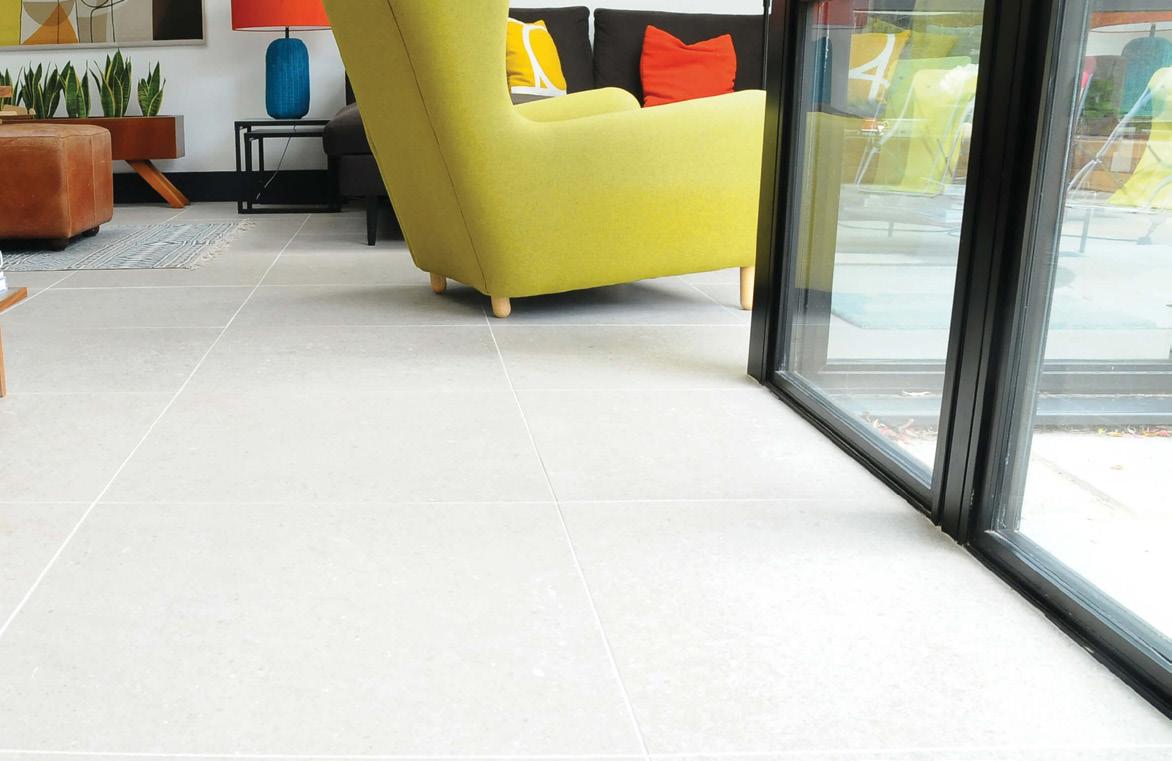
Heating & ventilation Domus Ventilation MVHR System Specified For Extensive Office-to-Apartment Conversion
Domus Ventilation’s HRX-aQ Mechanical Ventilation with Heat Recovery (MVHR) systems and Domus ducting are being installed into the striking No. 1 Thames Valley apartment complex in Bracknell, Berkshire. This extensive development sees the building converted from offices to 130 single bedroom apartments laid out in two wings with floor-to-ceiling windows.
A
s with most office to residential conversions, No. 1 Thames Valley has presented a number of challenges along the way, not the least the ventilation. Thankfully, Working Environments, which is responsible for the design, supply, installation and commissioning of the mechanical, public health and electrical services, has plenty of experience in this field. This has enabled them to meet these challenges, from ducting that needs to run through the building façade to trying to match the ventilation grilles with the terracotta tiles in place.
Working Environments specified the Domus Ventilation HRX-aQ for this demanding project as the MVHR system was readily able to provide the level of indoor air quality required. Other factors that were taken into consideration were the pricing and cost-efficiency, plus the level of support provided by Domus Ventilation.
The HRX-aQ MVHR system is ideally suited to No. 1 Thames Valley as it intelligently manages air conditions for maximum homeowner comfort. This is achieved through advanced AMIE (Air Management for Indoor Environments) technology including features such as digital humidity control, automated summer bypass and accurate system balancing.
Unlike conventional humidity sensors, the HRX-aQ enables occupants to have direct control over managing the humidity levels in their home to suit personal comfort levels. By accurately measuring air humidity, the HRX-aQ’s extract speed automatically changes from background to boost as the level of humidity increases, thereby providing optimal ventilation performance.
The HRX-aQ features advanced bypass control, programmable by occupants based on time and temperature. In standard mode the MVHR units work by warming fresh air drawn into the building using the heat from waste stale air extracted from the kitchen and wet rooms. In conjunction with multiple time controlled bypass options (night time free cooling), the HRX-aQ also detects when air temperature reaches a preset level and intelligently activates the bypass mechanism allowing in cooler, fresh and filtered air.
Working Environments has installed the HRX-aQ units at No. 1 Thames Valley within each apartment’s bathroom in the ceiling void, with the MVHR controller located in the utility cupboard. This is the first time the company has used HRX-aQ and, according to Robert Druce, Project Manager at Working Environments, they have found the units very easy to install, further assisted by the online training provided by Domus Ventilation.
Measuring just 199mm in depth and weighing from just 7.9kg, the HRX-aQ is compact and light enough to be easily installed in the most restrictive of ceiling voids. It can be simply designed-in with a straight in-and-out duct run and, in the case of No. 1 Thames Valley, is directly fitted to Domus 204x60mm Supertube rigid ducting for an air-tight connection, minimising pressure drops virtually eliminating air leakage. Its offset duct connections also mean that any duct crossover is much more straightforward. The accumulation of HRX-aQ’s quick and simple installation features make for one of the lowest install costs of any MVHR in the market today.
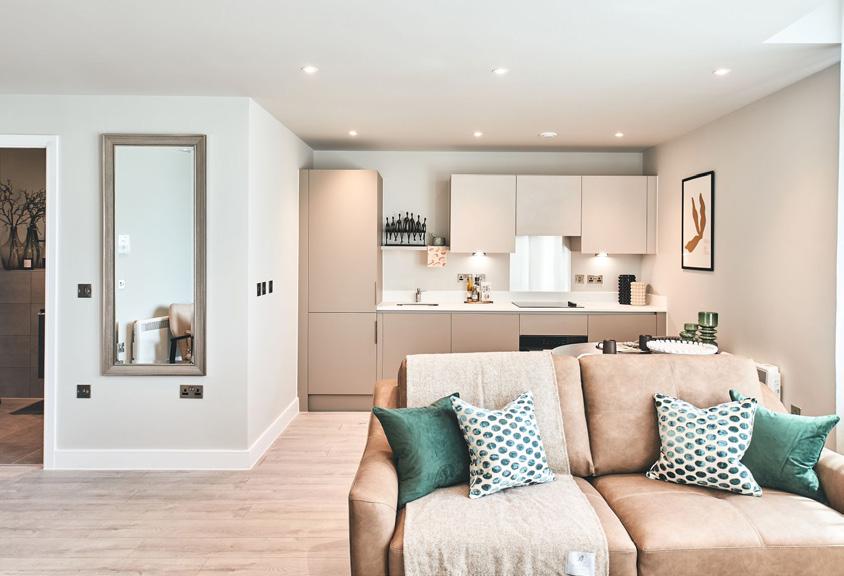
For further information on the Domus Ventilation HRX-aQ range of MVHR appliances, please go to www.domusventilation.co.uk or call on 03443 715523.