
17 minute read
Sustainability
Sustainability BLAH BLAH BLAH….
OF COURSE, WE NEED CONSTRUCTIVE DIALOGUE - BUT THEY’VE NOW HAD 30 YEARS OF BLAH, BLAH, BLAH, AND WHERE HAS THAT LED US? GRETA THUNBERG
Advertisement
There are those who talk and those who act. Action requires physical evidence of change and improvement, illustrated perfectly by a demonstration house already built at COP26 designed and constructed by a like-minded group of businesses to demonstrate how beautiful, affordable, healthy, and comfortable homes can be developed with minimal impact on the environment, throughout their lifecycle, using local materials and existing skills. The house delivers a 2030 compliant building today, in fact it goes beyond zero carbon. It’s not that it can’t be done but rather it isn’t being done. The context in which we build sheds some light on why we are likely to fall well short of our carbon targets.
Nearly all of the houses we build today involve construction techniques that are ill suited to meet the challenges of climate change. Alternatives exist, now is the time for action not words but can Government and industry change course quickly enough?
The overall form of the modern house as constructed by the mass house-builders has changed little in millennia. The essential elements of walls, pitched roofs, openings for light and doors have remained pretty constant.
Before the late 19th Century, home life, through modern eyes might have appeared basic or even grim. but people were resigned to their lot. Here, for example, is the Rev. Francis Kilvert describing his morning bath on Christmas Day of 1870:
‘It was an intense frost. I sat down in my bath upon a sheet of thick ice which broke in the middle into large pieces whilst sharp points and jagged edges stuck all around the sides of the tub like chevaux de frise1 , not particularly comforting to the naked thighs and loins, for the keen ice cut like broken glass.’
Soon however, living conditions changed for most people. The development of the house that followed shortly after Kilvert’s miserable experience, set the home to evolve from being just the simple and often cold shelter into what Le Corbusier provocatively called ‘the machine for living in.’
The late Victorian house was nearly crowded out with novelty objects. Many were trivial, but one product of wealth and industrialisation was set to change domestic life profoundly. The idea of warming and circulating air had recurred repeatedly since ancient times - usually only in places where
its exorbitant costs could be met. With central heating, middle-class Victorians could explore new ideas of comfort and leisure. They took off their thick coats and layers of fabric and slipped instead into something lighter and more comfortable. Welcome to the 20th Century.
Indoor temperatures steadily increased throughout the new Century as new concepts of lifestyle became possible. Even in the late 20th Century, homes continued to become warmer. In the year England last won the World Cup in 1966, the average temperature was 12 degrees C; Today, it is between 17 and 23 degrees C.
All was good just so long as fossil fuels kept flowing. But, unfortunately, cheap energy masked the problem to come: the system that paired space heating with traditional construction was the nexus through which the building envelope became environmentally compromised.
What became apparent and then important much later was that to operate with efficiency, warm air needed to be contained within the building envelope - but insulation and air-tightness were not features of traditional building. Until the late 19th Century and for many, far into the 20th, building occupants were warmed directly by open fires creating radiant heat. To be warm was to be in line with a fireplace or wearing a coat, whilst other provisions such as heavy curtains and wing-backed chairs limited cold drafts. Just so long as there was a fire in the hearth, leaking windows, flues, and simple 9-inch uninsulated walls and roofs were relatively unimportant.
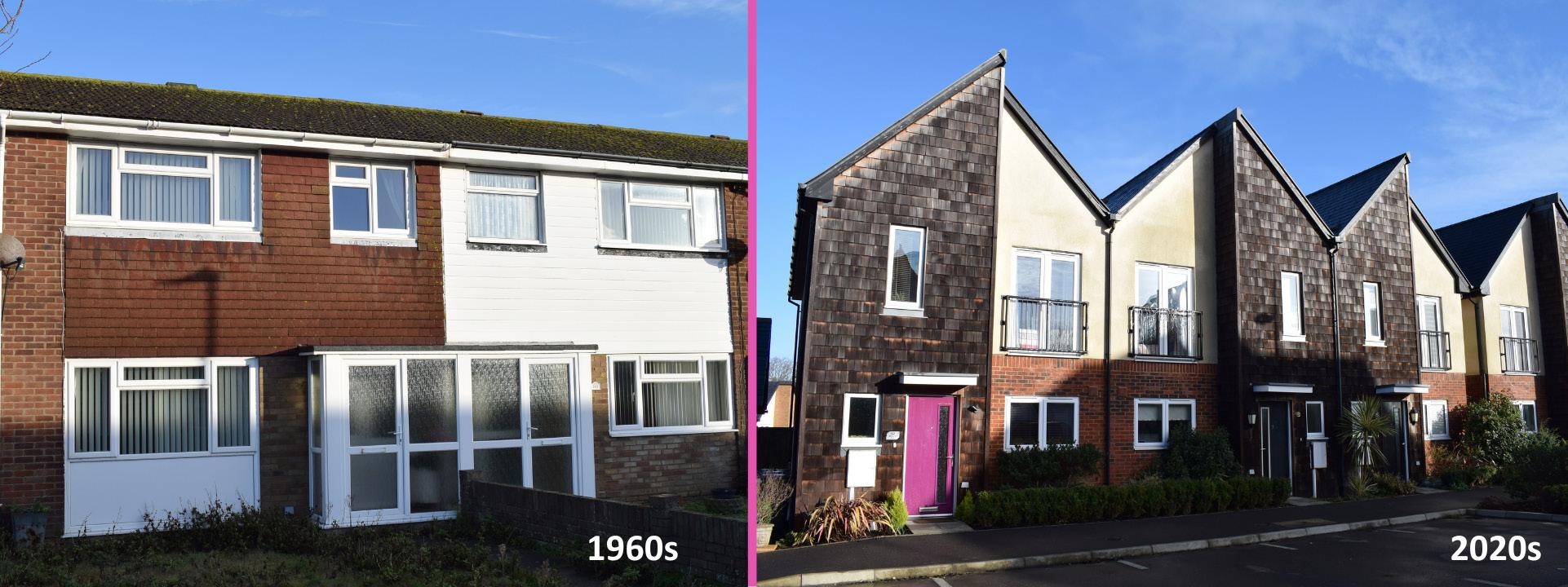
The curb on the limitless heat came in the early 1970s as the owners of the newly nationalised oil wells, particularly in the Middle East, learnt the political power of controlling supply to a beholden West. So oil taps were turned on and off and back on. Prices went up and up…… Cheap energy was history.
The Government intervened to tie down the amount of energy used in buildings. Through a succession of updates to what became ‘Part L’ , the Building Regulations imposed thermal performance standards on elements such as walls, windows, roofs and floors. Fuel poverty was kept at bay for most - but only just.
It wasn’t until 2002 that the first reference to Global Warming appeared in connection with the ‘Regs’. Making a stab at dealing with the threat, incremental degrees of application of performance standards increased to reduce carbon emissions up until the present day - but it has never been enough. ‘Part L’ has yet to achieve its potential to deliver energy-efficient buildings.
Whereas the Government has demurred at using its powers, the main obstacle to progress is how houses continue to be built using methods unchanged since before the 19th Century. The construction industry has never developed alternative building strategies that drive energy conservation. Instead, traditional building methods have been pushed well beyond their ability to deliver the necessary levels of performance. Even to meet current regulations, most houses need to be assembled using high degrees of accuracy and competence. Both are notoriously lacking - site skills levels are at their lowest in decades.
Still, the construction industry moves ahead, building hundreds of thousands of sub-performance houses a year using inadequate techniques backed by limp government standards. Continuing with this strategy is doing nothing to help avert the crisis, There needs to be a step-change.
The solution to energy loss and hence emissions has always been clear - by building walls, roofs and floors using materials and systems that inhibit heat transmission from inside to outside. Add appropriate ventilation, and it’s perfectly possible to build structures that use virtually no energy to keep them warm in winter and cool during increasingly warm summers - and keeps the air inside the house healthy for all to live in. Again, it’s a goal that is achievable using appropriate materials and technology. Higher than Government ambitions, standards like ‘Passivhaus’ exist outside the bigdeveloper ‘bubble’. What’s important is that these tested standards are available for adoption by Government - ‘ovenready’, as one B. Johnson might put it.
By offering different design strategies and materials matched to standards superior to those cited by Regulation, a growing number of smaller developers, architects and supporting supply chains already show how emissions can be neareliminated in new buildings. Getting to near-zero emissions is not rocket science - we just need a collective determination. Alarmingly, there’s more: if one existential emergency brought on by Climate Change were not enough, yet other environmental crises are bearing down. All man-made, they include fossil-fuel depletion, pollution, loss of biodiversity, deforestation, land degradation, water extraction, waste ……… the list goes on. The cost to the planet of our way of life is too much bear. There’s no wonder our children are betraying previously unknown levels of angst. According to the University of Bath, ‘Nearly six in 10 young people, aged 16 to 25, are very or highly apprehensive about climate change.
Outside of the mainstream, though, designers of sustainable buildings that meet the environmental challenge understand the impacts of the building process - not just how much energy is involved, but also where the materials come from and what procedures they have to go through before they arrive on a building site. Their buildings are designed to touch the earth ‘lightly’ so as not to compromise the future of succeeding generations.
Design strategies and materials
Low energy and low environmental impact buildings generally have in common basic design strategies and choice of materials:
Space heating consumes around 60% of a home’s total energy demand. The ‘Fabric first’ design strategy is based on the simple idea that reducing heat loss through the building fabric minimises the energy needed Timber frame house built using only natural materials, Picture courtesy Kithurst Homes Ltd. Construction NIPPS (naturally insulated passive panels), insulation blown wood fibre floc, Steico rigid wood fibre board sheathing. from the grid. When the Government is looking Passive standard ach 1.2 @50pa. 35,921kg of carbon sequestered. to replace gas boilers, reducing the need to generate heat from alternative technology and fuel sources will result in more accessible and cheaper solutions with fewer emissions.
Air-tightness - ‘Build tight - ventilate right
Build tight: A well-insulated building is nothing if warm air can leak uncontrollably from window and door openings or through flues and pipe penetrations in walls and roofs. Air-tightness is twin to insulation in the strategy of a low-energy building.

Ventilate right: High carbon dioxide levels, a build-up of toxins and mould from condensation are the unwelcome products of an ill-ventilated building. Traditionally trickle vents were built into the walls and windows. Vents could be opened by the occupants to let bad or steamy air out into the atmosphere. But whilst accepting that opening a window is almost a human right, using it to ventilate a room needs to be restricted if energy is to be conserved. So instead, there has evolved, mainly through the Passivhaus movement, advanced ventilation systems that keep the air fresh and warm. These extract foul air from interior spaces whilst pumping fresh air into the opposite direction - itself warmed by exchanging heat from the exhausted warm air.
The term ‘Operational energy’ expresses the amount of energy used to heat and power a building throughout its lifetime. ‘Embodied energy’ refers to the sum effect of all emissions attributed to all the materials, components and equipment during the building’s life cycle. This cycle encompasses extraction, manufacturing, transportation, construction, maintenance, and disposal of those materials.
Reducing the amount of embodied energy is an early part of the design strategy. The designer will calculate the quantity of energy used in supplying, maintaining, and disposing of each material specified. An obvious material to be minimised will be concrete. Cement production is the third-largest emitter of carbon dioxide globally, followed closely by steel and aluminium. If the quantity of those materials can be reduced or eliminated, then significant amounts of embodied energy can be reduced too.
It is no surprise that timber is at the top of the list of materials used by designers of sustainable buildings. This is because timber, along with other renewable materials such as hemp, cork and bamboo, actually absorbs carbon dioxide during its growth period. So ultimately requires very little energy to extract timber and transform it into roles such as structure, finishing, and cladding.
Préfabrication
One of the factors aggravating any chance of producing high performance, traditionally-built housing stock is the reliance on qualified site operatives. Skilled workers have always been wanted in the construction industry, but currently, with many trained workers returning to the EU, a skills vacuum leaves the industry desperately in need. Even guided by relatively benign building standards,
PH15. Akerman Road Social Housing. Picture courtesy of Passive House Homes Ltd. Certified passive house, build cost under £450/m². Construction timber frame, LVL, Steico I Joists, Steico wood fibre insulation, Unilin Vapourblock, lime render, sheep’s wool.
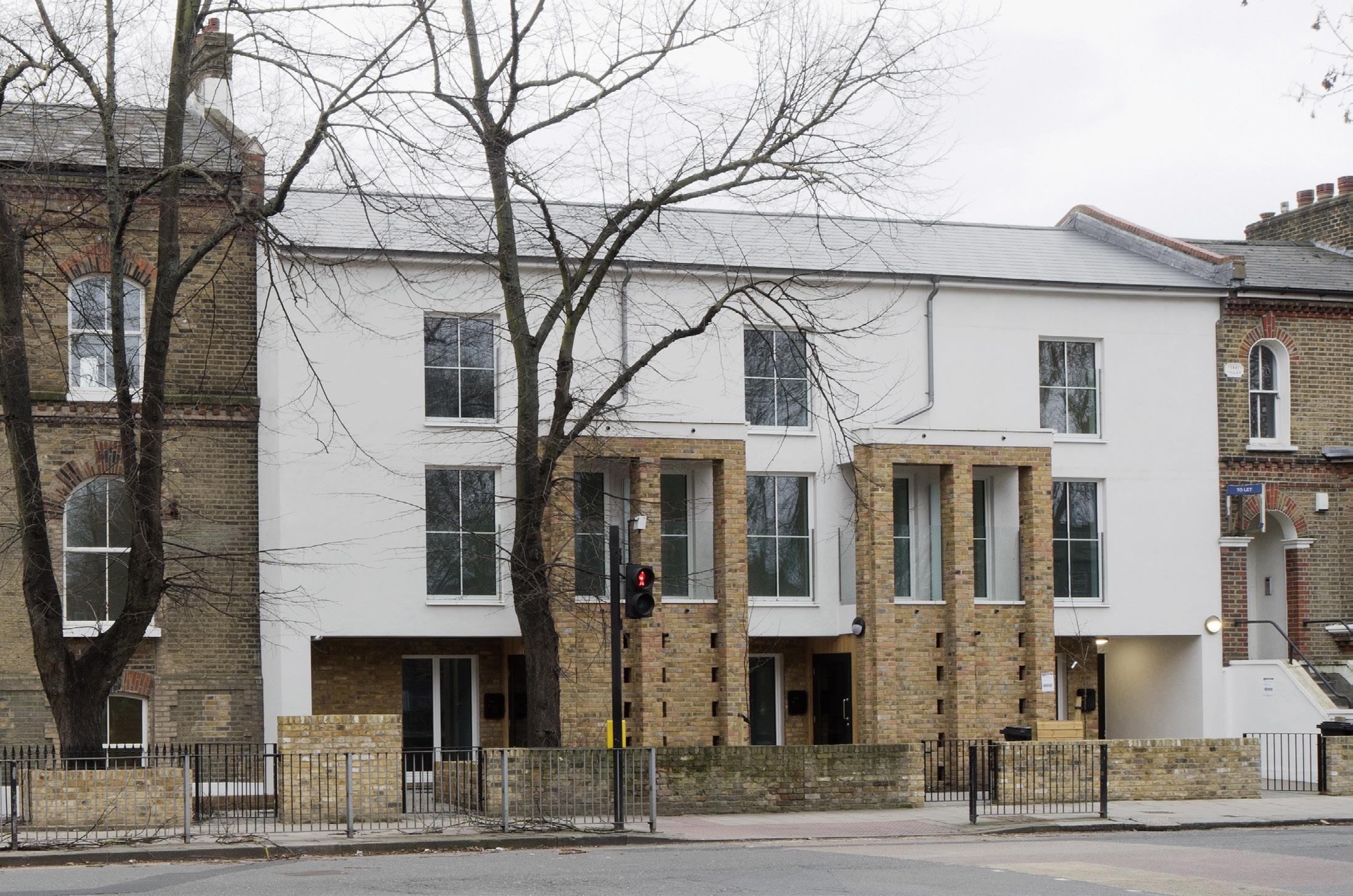
housebuilders can’t even run to stand still. With time running out to make the necessary reductions in emissions, most buildings will fail to meet the demand.
By moving most construction from the typically Somme-like conditions of the traditional British building site and into the warm, sheltered and closely monitored factory conditions, much higher levels of quality can be achieved. Assembling a kit of parts arriving on site is relatively risk-free and usually within the capabilities of a less-skilled workforce. The outcome is that most buildings can be built to higher standards of performance.
Try and tested alternatives to traditional construction.
Timber frame
The use of timber has been a significant feature of UK construction for centuries. In that time, its use as a structural frame has passed in and out of fashion. However, a substantial proportion of UK housing is built using timber frames within the traditional cavity wall format. Its advantages include that it is a well-understood, tried and tested and flexible building technology. Moreover, used appropriately, it can be impressively cost-effective. The COP26 House – built in central Glasgow to showcase zero carbon buildings during the COP26 event in November 2021 - is an example of a timber-framed building with the added benefits of prefabrication.
Cross Laminated Timber (CLT)
CLT is a relatively recent arrival on the UK construction scene. The system comprises timber laminations glued together and formed into prefabricated component panels such as walls, floors and roofs. Popular for some time in Germany and Austria, where timber is readily available, its introduction into the UK through low and high-rise buildings such as flats and schools has made significant inroads amongst the alternatives to traditional construction techniques.
Waugh Thistleton Architects are the leading exponents of CLT techniques, particularly in the application of high-rise housing around central London.
Similarly, a recent school building programme has also done much to open up the potential of CLT to enable large-span structures. Architects and engineers working with CLT include Fielden Clegg Bradley, Aberdeenshire Council, B&K Structures, Durban, Avanti Architects and Arup’s - amongst many others.
Prefabricated timber panels
Timber panels can act as structural elements in themselves. Good examples are manufactured by Eden Insulation. Their panels include structural elements clad externally with an insulation board and internally with a vapour barrier board. The whole is filled with recycled newsprint insulation. The panels are shipped from the factory and simply assembled on site. Already there are many buildings in Scotland and the north of England featuring their lowimpact panels - most meeting the demanding Passivhaus standard.
Hemp
Hemp is a crop better known for furnishing the Georgian Royal Navy with its ropes and, more recently, as a component of fat roll-ups. Hemp (without its intoxication element) is, in fact, a superbly flexible material that parts of the construction industry have invested in over the last 25 years. In buildings, hemp can be mixed with lime to produce Hempcrete, a plastic material that integrates in-situ with timber frames to form impressively insulated and airtight structures. Examples abound, with perhaps the best known being Kevin MacCloud’s ( of Grand Designs fame) 42 home development near Swindon. As part of their ‘Plan A’, M&S has also used the material extensively at their massive Chesire Oaks store.
COP26 Finished House, picture courtesy Roderick James
Aerated clay blocks
Popularly known as ‘Ziegel’ blocks, aerated clay blocks are a development of the humble brick. Blocks are larger individual components that are glued together. Think Lego. There is no need for a cavity because the blocks themselves are manufactured to include insulating air pockets.
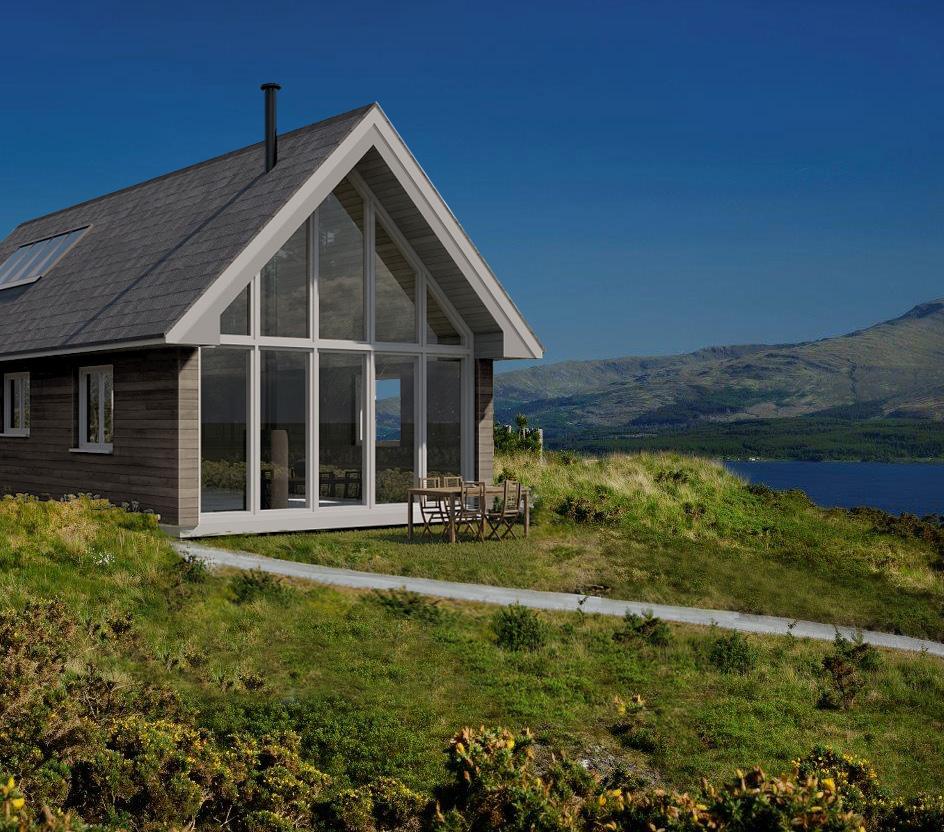
Clay blocks have been used for decades in Europe but are only just become popular in the UK. Lidl supermarkets are leading the charge by including the building technique in their new stores.
Straw
Straw is one of the most common byproducts of agriculture. It makes up half of the yield of cereal crops in the UK. As a result, it is available in massive quantities. Traditionally it is used as bedding, fuel and fodder. Historically though, much was simply burnt on the fields until 1992 when it was banned.
Strawbale building has been a way of constructing homes, particularly in the USA, since the 19th Century. However, its modern manifestation in the UK is proving its viability alongside other renewable building materials. Barbara Jones has been constructing straw bale buildings since the 1990s resulting in techniques tried and tested. Craig White and Modcell have also developed prefabricated panels made in ‘flying factories’ using a locally sourced straw to produce highperformance houses.
BZH COP26 House Construction Phase picture courtesy Roderick James Architects
The COP26 House
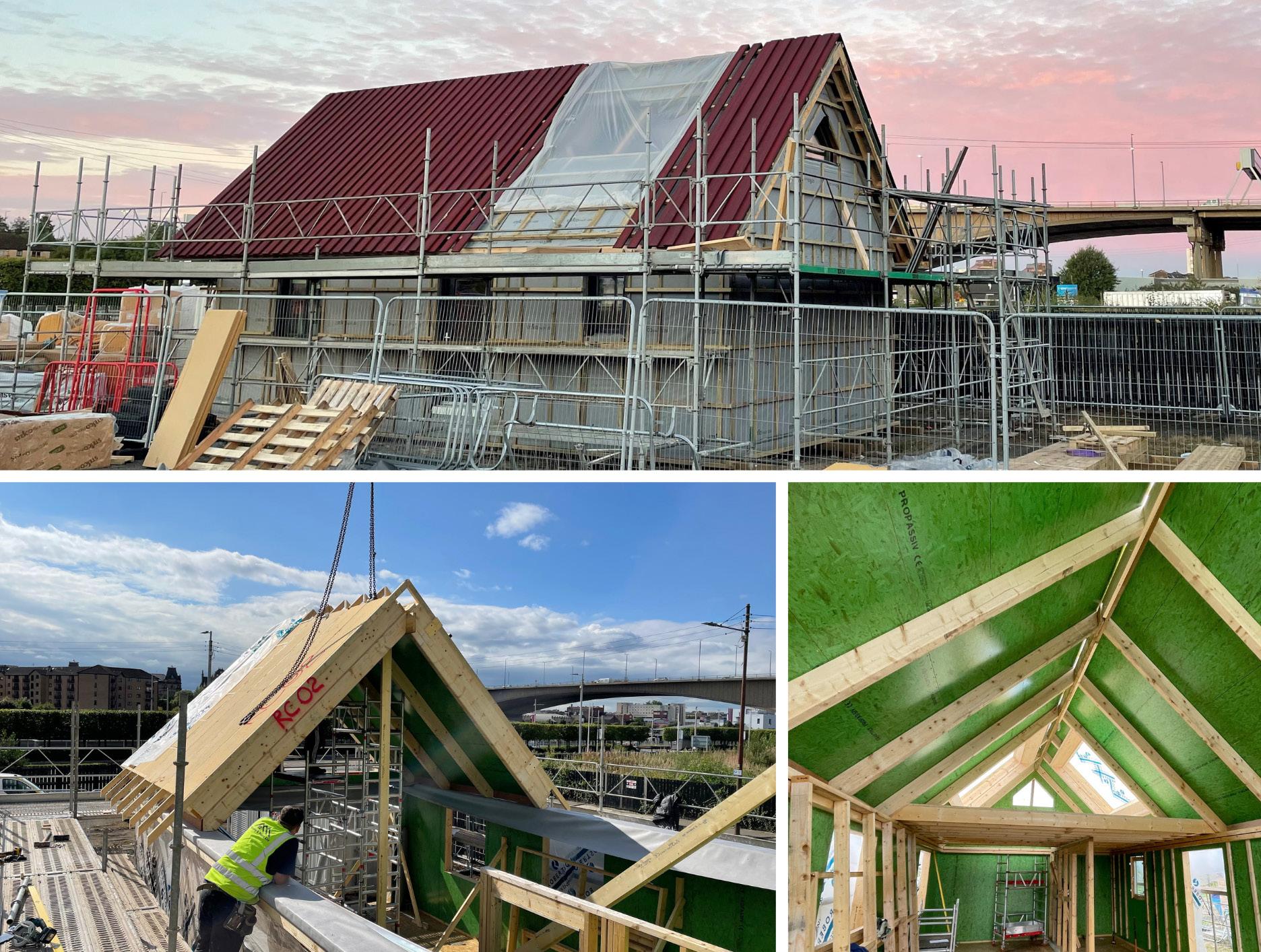
Architects
The COP26 House, designed by Roderick James Architects and currently erected close to the Glasgow Conference Centre which is hosting the UN Climate Conference, is a well-honed example of an low carbon house across its entire lifecycle. The design of the building follows the simple assembly prescription of the fabric-first concept but takes it further still. The house is distinguished by its extensive use of timber. The UK construction industry mainly imports timber from overseas to provide framing for otherwise brick-clad walls, floors and tile roofing. The COP26 House is timber-framed using homegrown Spruce but goes much further. The walls are clad in timber both inside and out; the roof is timber-boarded Scandinavian-style. Insulation derives from timber trimmings transformed into insulation boards and mats sandwiched into the walls and roof. The designers eschew plastic windows for high-performance timber-framed triple glazing. There is a determination to achieve a safe, non-toxic environment by avoiding where possible materials groups such as petrochemicals and other components that can emit toxic chemicals and gases either in their manufacture or use in the house.
Most significantly, the COP26 House meets the 2030 zero-carbon target right now. As befits such a lowenergy building, heating is carefully designed to drive down the annual bills to somewhere around £150 per annum. Technologies can be incorporated as appropriate – in the current house infra-red panels provide the space heating by heating objects and people directly, air source heat pumps, solar thermal and PV immersion heating could also be incorporated for space and water heating.
For the low energy usage achieved through high insulation and air-tightness standards in the house, it is a must to pair up with an efficient artificial ventilation system. Tried and tested is Mechanical Ventilation with Heat Recovery (MVHR) that, when applied to the whole building, can deliver fresh air whilst extracting foul air. The useful twist is the heat recovery element, which uses the exiting warm air to heat the cooler incoming air.
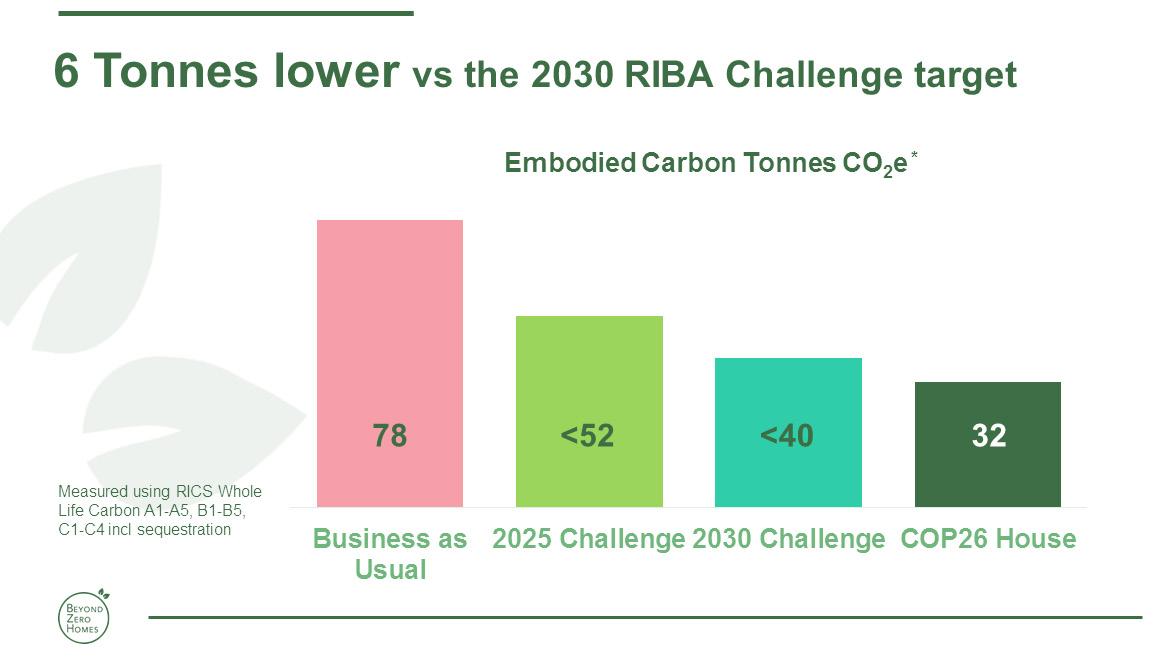
The single bedroom 65m2 COP26 House is just one of several design variations using the same zero carbon approach, with the largest currently a 4-bed semidetached version of 140 square metres.
The house is easy to build using the many off-site manufactured components as part of the design. The architects estimate that total build cost should be in the range of £1,800 for self-build up to £2,500 per square metre dependent on size, location, builder, and final finish specification.
Through realising the COP26 House in Glasgow, the architects have indeed demonstrated they can set out to match ‘...design and materials in a way that showcases that low carbon housing, made from ecologically responsible materials, can - and should - be beautiful, comfortable and affordable. Thanks to Ecomerchant for contributing this piece. Ecomerchant are a key partner of the COP26 House as a supplier of natural, carbon friendly and sustainable building materials www.ecomerchant.co.uk More on the Beyond Zero Homes COP26 House at www.beyondzerohomes.co.uk More on Steico wood fibre insulation, I Joists and LVL at www.steico.com
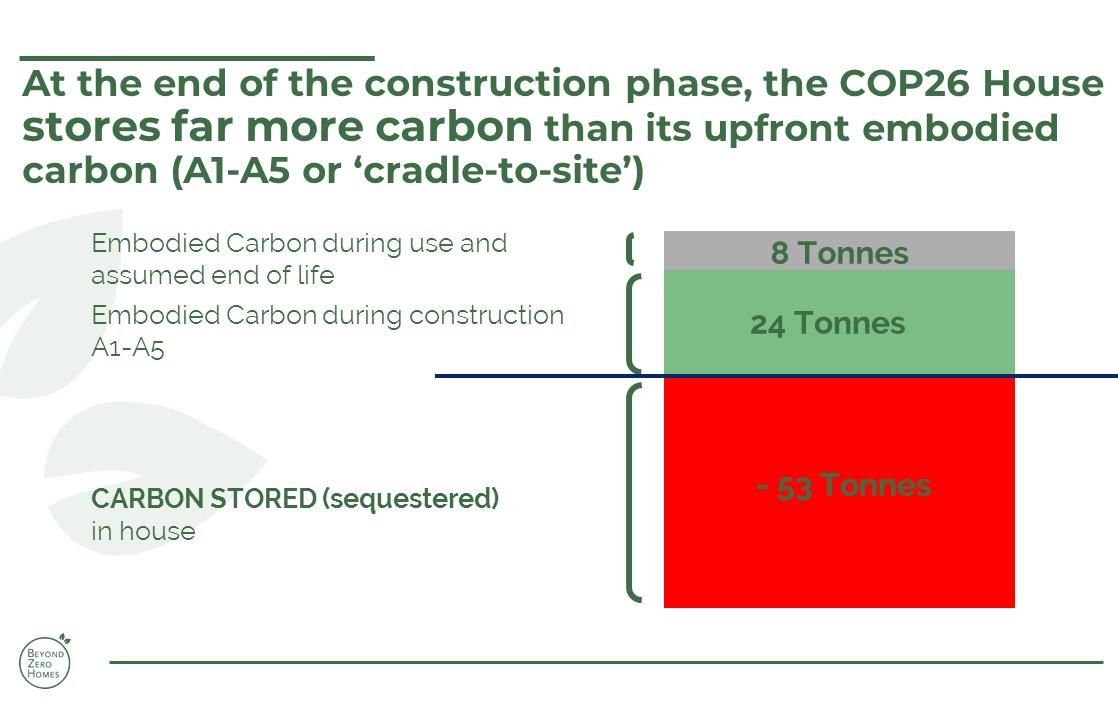

Four Stop Platform Lift for historic Old Portsmouth
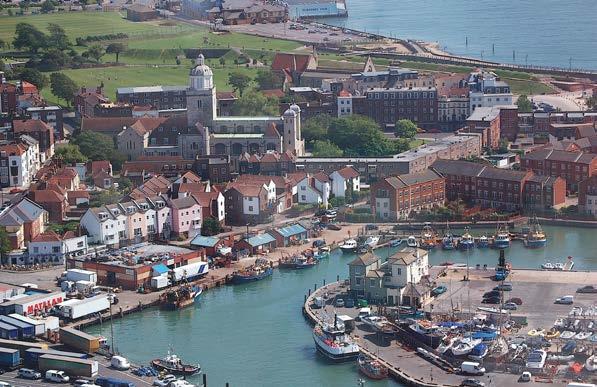
We’ve just fitted our Home Lift in a historic property overlooking the harbour in Old Portsmouth.
Old Portsmouth is the area of Portsmouth which was covered by the original medieval town of Portsmouth. It is steeped in history, and contains many historic buildings including Portsmouth Cathedral and Portsmouth Point.
Our client was a resident of a rare, historic four storey property overlooking the harbour and the Solent. They were in need of a lift to enable access to all floors of the property, and contacted the lift experts at Invalifts for a solution.
After an initial site survey, Invalifts recommended and installed their Home platform lift, with a custom footprint of 910mm x 870mm optimising the available space.
The Home Lift was the perfect solution, as a quiet and efficient platform lift, with a capacity of 250Kg. The carriage controls are clear and easy to operate whilst the aluminium handrail located just below the carriage push button enhances the feeling of Swedish quality and design. The home lift was installed with glazed 800mm wide landing doors at every level.
The client was thrilled with the quick and hassle-free installation and now has easy access to all of the floors of their property. If you would like to know more about our platform lifts or other access solutions, please contact the Invalifts team on 0845 468 2543 or alternatively, email sales@invalifts.com •60•
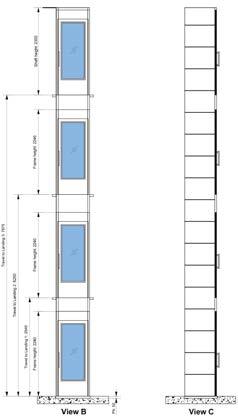