
12 minute read
Flooring Carpets

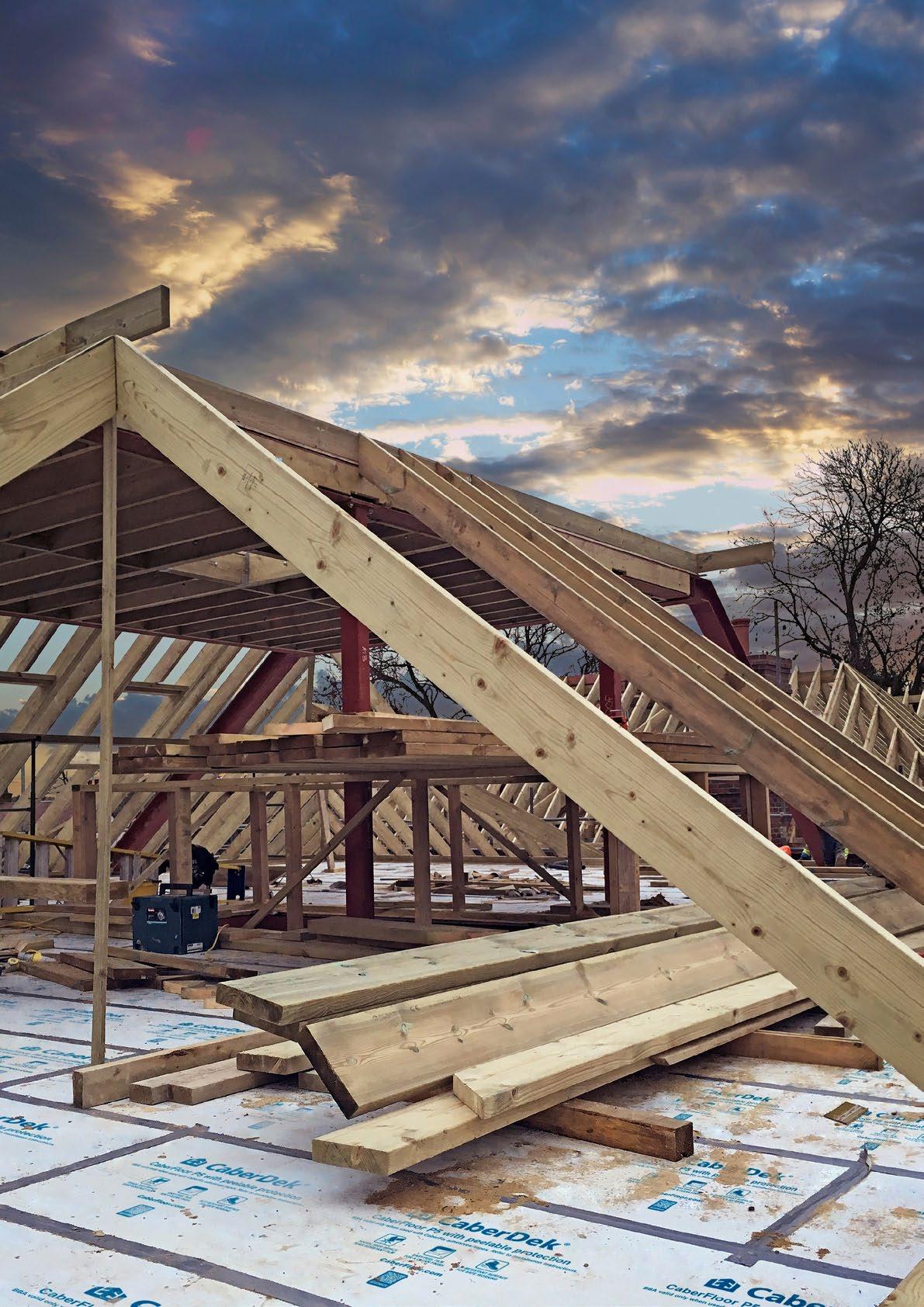
Advertisement
CABERDEK WEATHERPROOFS FLOORING WITH PROTECTIVE FILM
CaberDek, from West Fraser (Trading as Norbord), is ideally suited to the UK’s unpredictable climate, being that it combines the company’s market leading particleboard flooring with a tough, waterproof and slip-resistant film.
Compliant with BS EN312: part 5, CaberDek creates a safe working platform thanks to the waterproof, heavy-duty film, which is also resistant to the sudden impacts, puncture and tear risks to be encountered on any building site. It is recommended that CaberFix D4 adhesive is used for bonding flooring to joists, within tongue and groove joints and along the exposed perimeter edges of the floor. When applied in accordance with the instructions, CaberDek has full BBA approval for 42 days exposure.
For the eventual building occupant, CaberDek flooring more than meets the acoustic requirements of the Building Regulations: with tests on the CaberDek and CaberFix Pro flooring system having confirmed an impressive 44db sound reduction. Meanwhile the easy to peel film, once removed, leaves a clean and undamaged floor surface ready to accept a full range of floor finishes.
Measuring 600mm wide by 2400mm long, CaberDek is available through West Fraser distributors in an easy to install and familiar T&G format, making it the ideal choice for housebuilders or sub-contractors to ensure rapid installation, ready to face the toughest of conditions on site.
To find out more about West Fraser’s products for housebuilders, get in touch with Dan Clarke – email Daniel.Clarke@westfraser.com or download product brochures from the housebuilder page of the West Fraser website https://uk.westfraser.com/housebuilders/
For further information, call 01786 812 921 or visit https://uk.westfraser.com/
flooring & carpets WORLD’S ONLY SUSTAINABLE LUXURY CARPETS SHORTLISTED AT THIS YEAR’S THE INTERNATIONAL DESIGN & ARCHITECTURE AWARDS 2022
Luxury carpet brand SYLKA has been named as a finalist at this year’s International Design & Architecture Awards 2022 for its latest innovation, EcoSylk.
Launched earlier this year, this innovative new fibre system is crafted using sustainable yarns regenerated from recycled carpets that would otherwise end up in landfill.
Following a harrowing trip to the USA to see how millions of tonnes of used carpets are sent to landfills, the award-winning team behind SYLKA Carpets set about developing a ‘circular solution’ that would ensure that every carpet created not only comes from recycled fibres but that every carpet they produce are themselves fully recyclable.
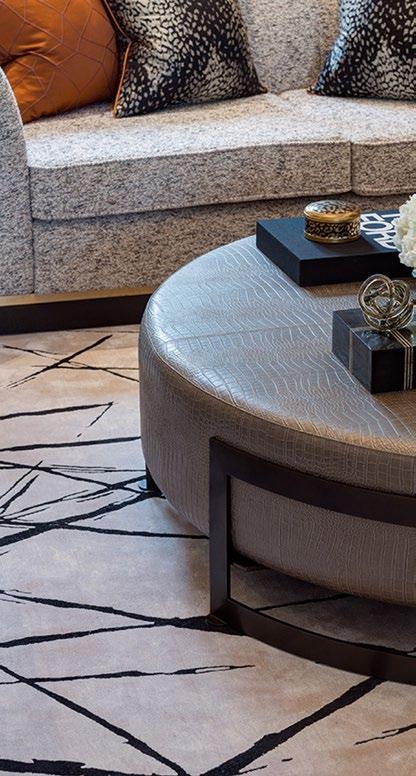
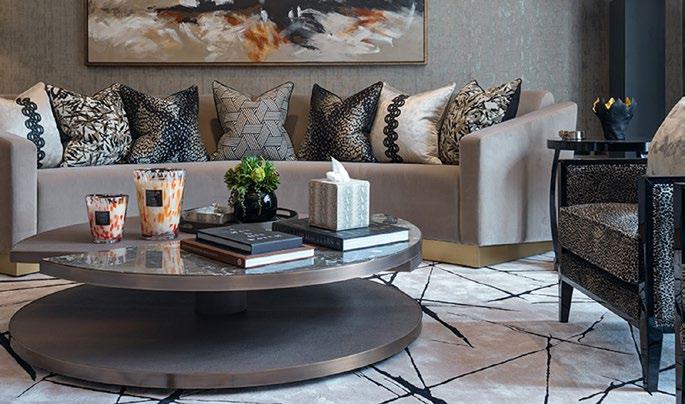
This new development now replaces its previous fibre, NuSilk, across all of SYLKA’s range of opulent carpets and rugs so that clients continue to enjoy some of the world’s best flooring while preventing thousands of tonnes of used carpets from going to landfill.
Judges at the International Design & Architecture Awards 2022 were impressed by SYLKA’s commitment to sustainability and have shortlisted them for the Flooring: Carpets/Rugs at this year’s awards.
Steve Farrell, Founder and Managing Director at SYLKA, said: “We are really proud of what we have achieved with EcoSylk. It is a considerable development for us and ensures that we are reducers rather than producers of waste.
“The sustainability of EcoSylk sets us apart from many other luxury flooring brands while ensuring that we retain the reputation for quality that has become synonymous with SYLKA.”
Having gained a place at these awards, SYLKA are now calling on the public to get behind them and support them in a public vote, which closes on Wednesday 21 September 2022 at 5pm BST.
To show your support please vote for them here.
SYLKA will find out whether its revolutionary EcoSylk development has won an award at a glamorous event at the JW Marriott Grosvenor House, London on Friday 23 September 2022
To find out more about SYLKA and its multi-awardwinning range of carpets and rugs, please visit www.sylkacarpets.com
MODULEO CELEBRATES 10TH ANNIVERSARY IN THE UK
Leading flooring brand, Moduleo, which has its UK headquarters in Derby, is celebrating 10 years of business in the UK.
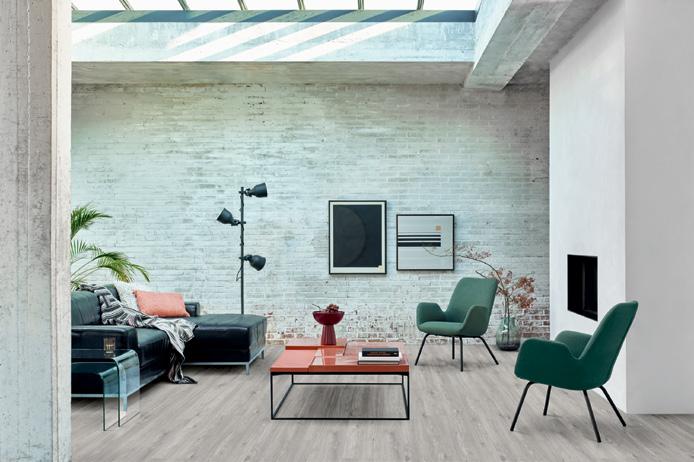
Part of the IVC Group, the world’s largest flooring producer, Moduleo first launched its collection of luxury vinyl floors in the UK in 2012 and the business has since grown from strength to strength.
Offering a diverse range of durable, stylish products, Moduleo has a number of collections available to UK customers, including Moduleo LayRed, Herringbone and Moods. Across its flooring portfolio, products come in a host of different designs and shades, from light to dark, in both wood and stone vinyl finishes.
David Bigland, managing director for Moduleo UK and Ireland, commented: “It’s fantastic for us to celebrate 10 years of Moduleo in the UK this year. Over the past decade the brand has grown extensively, and we now offer floors to suit all design tastes for each room of the home.
“This progress and development has been recognised in recent years and we’re proud to have received highly acclaimed accolades, such as a Red Dot Design Innovation Award for outstanding design quality and a German Design Award for innovation.”
Moduleo planks are manufactured in Belgium, completely free of phthalates. As part of the company’s sustainability strategy, the factory is equipped with three wind turbines and is cooled with water from the Scheldt River. Moduleo floors consist of up to 50% recycled material of verified origin and are themselves recyclable.
David continued: “Since our beginning, we’ve challenged ourselves constantly to produce high-quality flooring which moves with the times. 10 years on and our ambition is the same - we want to future proof the brand and make Moduleo the number one choice in the UK when it comes to luxury vinyl flooring.”
Recent studies into biophilic design suggest the positive benefits of interaction with nature in the home, and this is something the brand has embraced with its latest collections, producing flooring styles which compliment this approach to interior design. Moduleo styles are ideal for any modern space and come with a number of benefits such as scratch and stain resistance, warm underfoot and equipped to deal with water. The brand has 500 retailers across the UK which offer floors for every room.
For more information on Moduleo flooring, please visit www.moduleo.co.uk and to view styles across social media, visit the #MyModuleo hashtag.

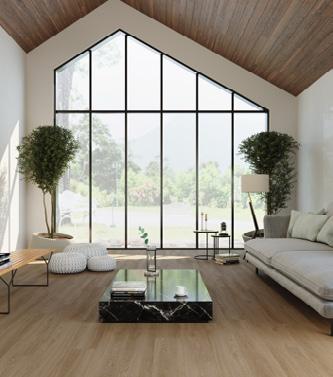

flooring & carpets HOW IS CABERFLOOR MADE?
In a short video launched by West Fraser,trading as Norbord, the panel product specialist demonstrates how its sturdy CaberFloor is made at the huge Cowie facility near Stirling, Scotland. The video is available on West Fraser’s YouTube channel: https://www.youtube.com/watch?v=5yfo8ZyfBRg
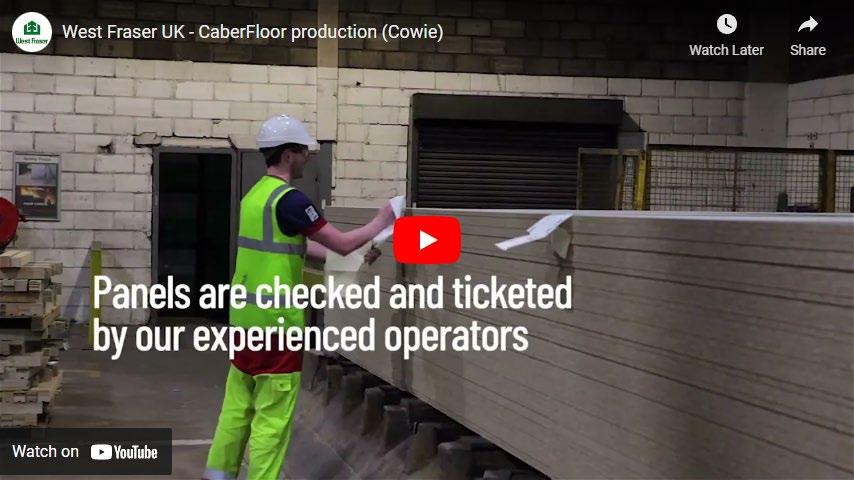
The 95-second, virtual ‘factory tour’ enables the viewer to appreciate the exacting processes required to produce the versatile and wellproven particleboard flooring panels. The cameras offer a panoramic view of the space-age interiors through to the highly automated plant: where dust and other pollutants are fully suppressed to create a healthy working environment for the handful of engineers and other staff who operate it.
At Cowie, CaberFloor begins life as a series of raw wood streams, carefully sieved and graded to the loadbearing panels’ precise specifications, while the fibres are dried to regulate their residual moisture content. Minutely regulated chemical treatments are used to facilitate the panels’ formation in layers on the production line and pressure applied to achieve the exact thickness. being mechanically sanded and precision cut to size. CaberFloor also features a machined tongue and groove interlock around all four sides to provide stability and minimise the need to support joints.
While the finished CaberFloor panels are carefully checked and labelled by experienced operators for distribution to merchant stockists and other customers, housebuilders and specifiers across the construction industry can be confident in the consistency of a precision made, fit-for-purpose product.
To find out more about West Fraser’s products for housebuilders, get in touch with Dan Clarke – email Daniel.Clarke@westfraser.com or download product brochures from the housebuilder page of the West Fraser website https://uk.westfraser.com/housebuilders/
Next, the panel blanks are cooled and cured on a slowly rotating carrier system, enhancing their longterm performance and durability, prior to them •16•
For further information, call 01786 812 921 or visit https://uk.westfraser.com/
CaberFloor production
Screening
Separates material by size
The wood is screened and sieved into different sizes
Nothing is wasted
All waste is recycled
Even the unwanted sawdust is re-used as fuel for the dryers The raw materials
Sawdust, wood chips, 70% recycled material
Different grades and sizes of wood are used to make particleboard Decontaminating
Raw materials are separated and washed
Cleaning removes any contamination
Drying
Reduces the moisture content
The wood is dried at 250-300˚C to remove the moisture leaving a humidity level of approximately 2% Ring fl aker
Shreds the wood chips into strands
48 knives rotating at 400rpm are accurate to 0.8mm
Blenders
Coat the strands with a mix of wax and resins
A mix of resins and wax are added to glue the wood together and give it strength Forming Line
Ensures the board’s consistent density
The wood is layered to controlled standards to ensure maximum strength
Quality Control
Panels are checked for quality at every stage
They’re date stamped and marked with quality certifi cations giving total traceability Continuous Press System
Heats and compresses the strands together
Accurate, constant pressure and temperature produces high quality board effi ciently Metal Detector
Removes any ferrous material
The mat is rejected if non-ferrous material is detected
Cooling
Star coolers reduce the boards’ temperature
The huge panels are cooled on two star coolers, 78 boards at a time Finishing Lines
Panels are cut to desired sizes
Tongue and groove edges and special fi nishes applied Warehousing
Stacks and packs boards for dispatch
Customers include distributors, merchants and manufacturers
industry news INTRODUCING STUDIO MOREN
Hospitality design specialist Dexter Moren Associates (DMA) is excited to announce a rebranding and change of name to Studio Moren. The rebrand reflects a further evolution of the studio and its collaborative approach to architecture, interior design and integrated hospitality solutions. The new name will be effective immediately.
Over the past 30 years, Studio Moren has established a worldrenowned reputation as a leader in hospitality design, built on long-lasting client relationships that are testament to the creativity, collaborative spirit and expertise of the studio. Increasingly, as the influence of hospitality design has grown across the property spectrum, Studio Moren has found its hospitality experience much sought-after in other sectors including alternative and high-end residential, student, commercial and later living.
Partner led and co-owned, the studio remains equally focused on architecture and interior design, with the new name embracing both the quality of its service offer and reflecting the greater team collaboration and diversity.
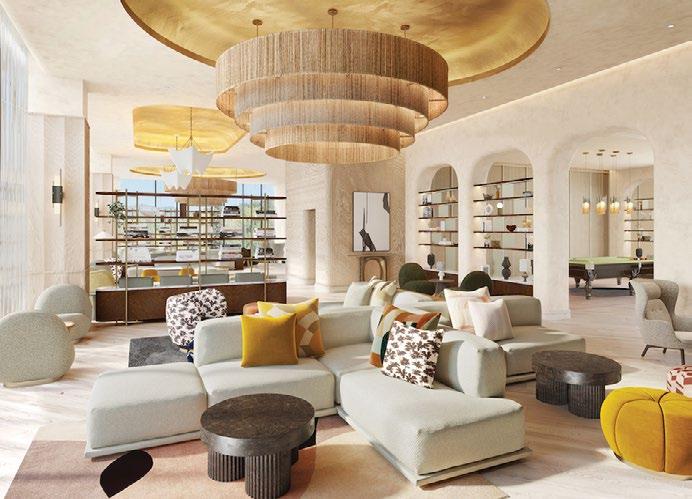
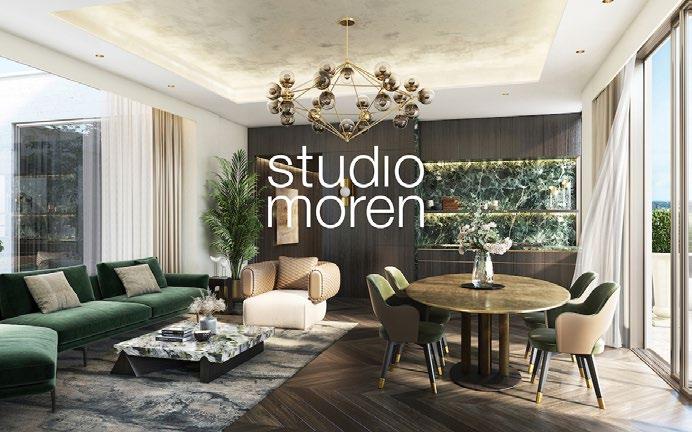
Founder and Partner, Dexter Moren, explains: “For some years the RIBA advised us we were too exposed to a single market and that worried me until I realised it was preferable to be a leader in one sector than master of none. The hotel specialisation has also enabled us to bring our expertise into the many sectors of student, co-living, co-working, later living and BTR projects where hospitality is now a primary focus.
“Today we are led by a management team of 17 who are also co-owners of the studio and together we have an impressive cumulative total of 243 years of working together. Everyone in our studio contributes and the combination of everyone’s individual brilliance creates a stand-out end product. In the spirit of inclusivity it seems time to evolve the name yet again to reflect our greater team and diversity and I am pleased to announce that from this point onwards we will be known as Studio Moren.”
Studio Moren is based in Camden, London, where its team of 70 architecture and interior design specialists work right across the hospitality spectrum and internationally, mainly Europe, Africa and the Middle East. In every location, Studio Moren creates places where people want to be.
Recent high-profile schemes for the studio include: The Westin London City, The Hotel Villa Pamphili Roma and 8-10 Great George Street, London. Current projects include a private and affordable housing scheme in Great Oakley, Essex, the conversion of a former London police station at 37 Wood Street into a luxury hotel, and an Autograph Collection hotel in Abastumani, Georgia.
As part of the evolution of the Studio Moren brand a new and dynamic website will be launched in October.
industry news POWDERTECH SANDSTORM FINISH FEATURED AT PERRY BARR STATION,
BIRMINGHAM Powdertech Corby used its Evolution Sandstorm finish to powder coat the sides of a large planter outside Perry Barr railway station, Birmingham. Re-development of the railway station was part of a £30.9 million project which also included the bus interchange The entire project was finished on time, and within budget, ready for the Commonwealth Games 2022 hosted by Birmingham.
Perry Bar railway station became a key visitor destination, situated close to Alexander Stadium, home of the opening and closing ceremony as well as athletics events. “We can now say that Powdertech Corby put in an appearance of sorts, at the highly successful Commonwealth Games 2022” said Richard Besant, Director, Powdertech.
Client: Galliford Try, RAAFT. Architect: Glancy Nicholls
Update of the station buildings themselves followed the popular trend for the appearance of rusted metal, providing a contemporary industrial look. “Powdertech’s Sandstorm finish complemented the main building perfectly,” said Richard Besant. “The finish has high durability and colour stability. Providing a very natural appearance of rust with subtle variation in tone, the overall effect is a pleasing consistency of shade. Cleaning and maintenance will be very straightforward, requiring just a 6-monthly wash with water.”
Powdertech coated over 100 mild steel panels and post-brackets some weighing over 100kg which were joined together internally to form the large planter.
www.powdertechcorby.co.uk
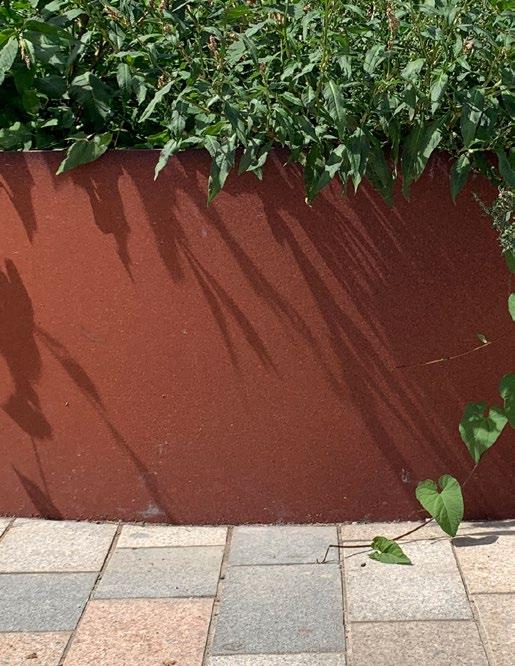
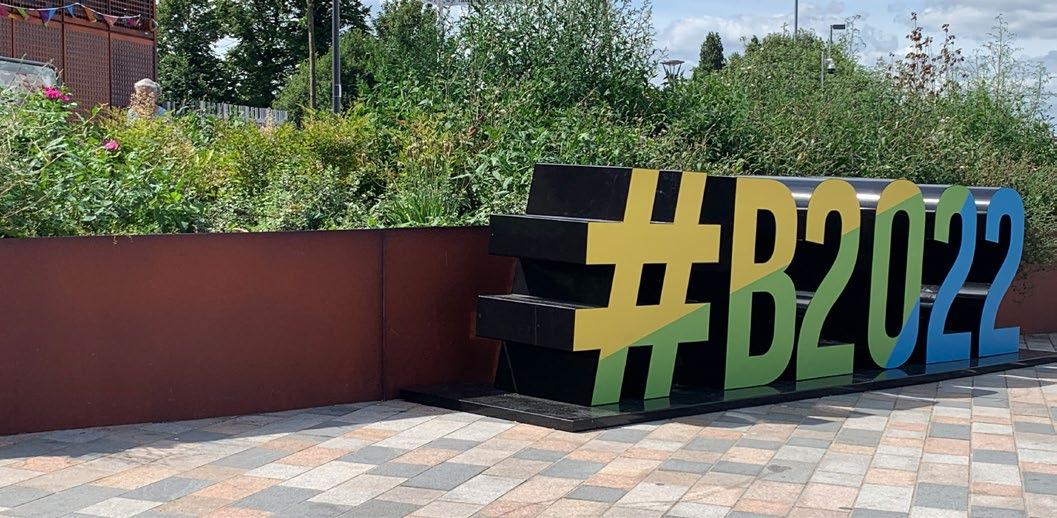