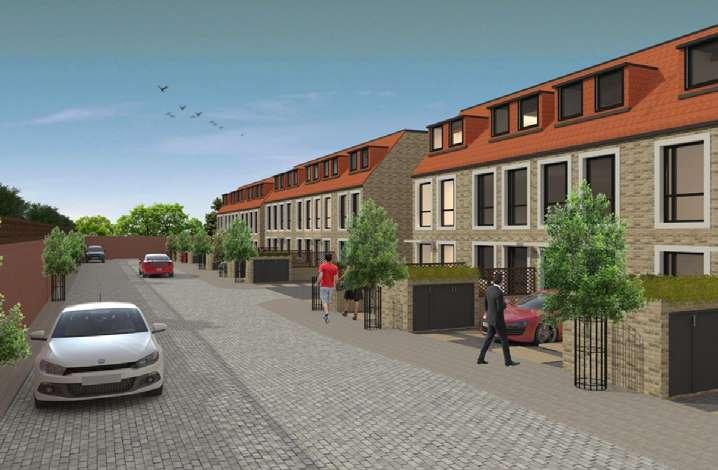
15 minute read
Industry News
Advertisement
Work will involve construction of 23 new private town houses in an area dominated by new apartment developments, The Bacon Lane scheme will be delivered in three completion phases, with the first homes due to be ready in late 2021. Each property at the private residential gated scheme will have gardens and off-street parking. The whole project is expected to complete by the Spring of 2022, with more than 100 construction and design specialists working on the build. Polyteck will be working alongside CG Architects for the build, Long and Partners for mechanical and electrical services, Hamptons for Quantity Surveying and Fox Greg for sales. Costas Polycarpou, development partner, Polyteck, said: “We are delighted to be able to start on this development.
“Not only does it provide much needed housing in the area, but it will also play an important role in creating jobs for many people who have been placed on furlough as a direct consequence of the economic fallout of the pandemic.”
Panasonic Increases UK Heat Pump Distribution as Nu-Heat joins its network
Panasonic has welcomed Nu-Heat to its distribution network for Aquarea Air Source Heat Pumps in the UK.
With installers seeing an increase in demand from homeowners for energy efficient sustainable heating, sales of air source heat pumps are set to grow as an alternative solution to conventional boilers. As the country’s most experienced integrated renewables and underfloor heating specialist, Nu-Heat’s team is well placed to fulfil the upsurge in demand for Panasonic’s range of Aquarea Airto-Water heat pumps and cloud based smart controllers. Brian Woodcock, Nu-Heat’s National Renewables Manager, comments, “With the market clearly moving towards renewable heat sources, we are seeing continuing strong growth for air source heat pumps right across the UK. With the addition of Panasonic’s Aquarea range offering great quality and reliability as well as an impressively wide range of capacities and capabilities, we are very excited to be able to offer our customers a complete package of heat pump and underfloor heating solutions to suit properties of almost any size.” knowledgeable team providing system design, support with MCS requirements and great customer service. This partnership with the team at Nu-Heat will provide installers with great opportunities to capitalise on increased consumer demand for energy-efficient heating solutions.” In a further bid to boost sales, Panasonic is also offering additional support as it extends its Green Install Cashback Scheme. Launched in October 2020, and running to 30 June 2021, the scheme provides qualifying installers with a cashback of £800 on the successful installation of five Aquarea heat pumps. A consumer scheme is also running - the Panasonic Green Homes Cashback scheme is for homeowners, who after satisfying the scheme conditions, can claim up to £600 cashback on the installation of an Aquarea heat pump unit*. These new Panasonic schemes are available throughout the UK and run in parallel, but independent of, the UK Government Green Homes Grant and offers additional cash incentives to both homeowners and renewables installers.
For more information, visit www.aircon.panasonic.eu or https://www.nu-heat.co.uk/
Jose Manuel Alves, UK Country Manager for Panasonic explains, “We welcome Nu-Heat to our team. Nu-Heat is well-established in the heating market and has a very
Bristan OPAC TMV3 Commercial Showers.
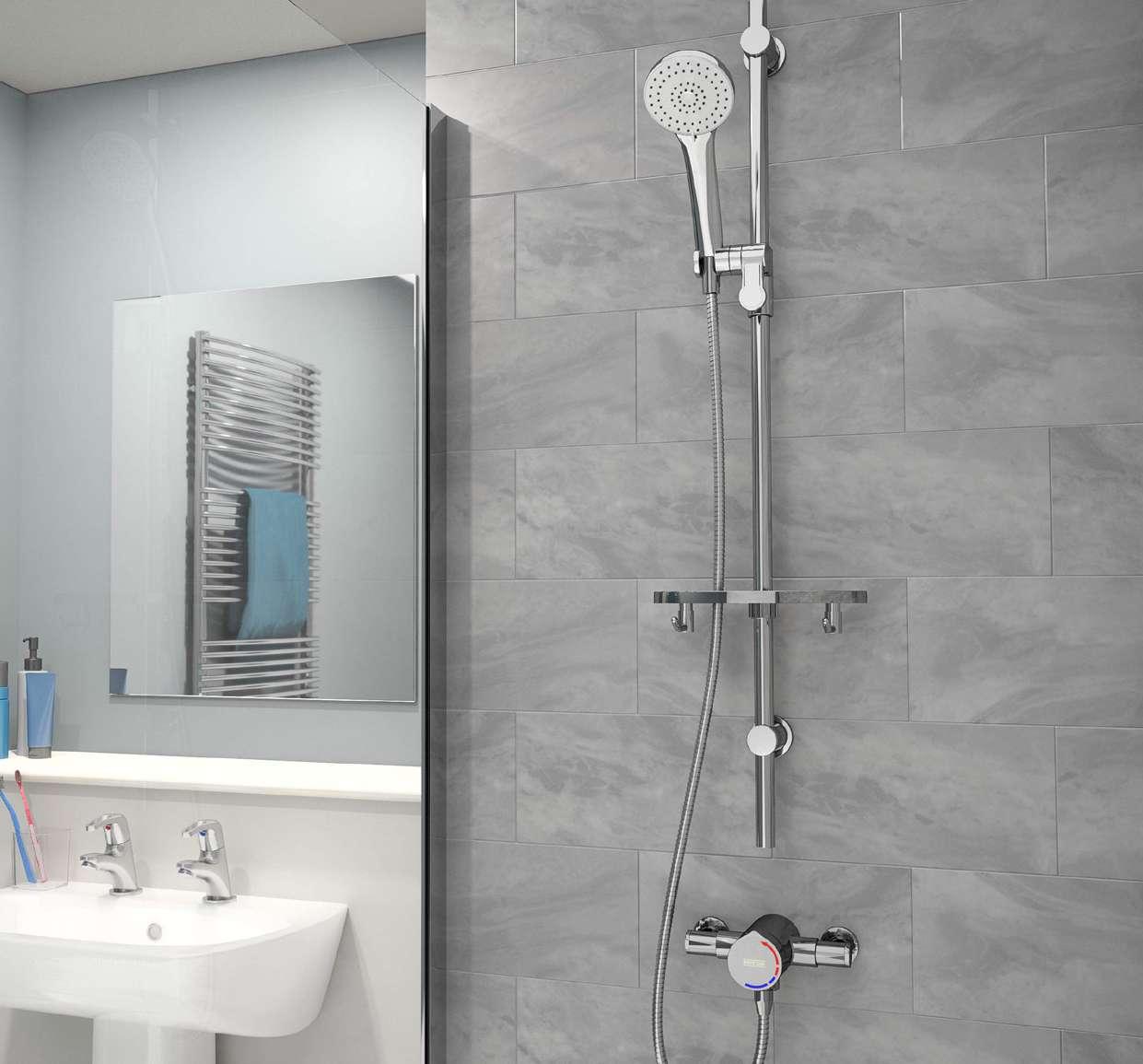
At Bristan we continually invest in new product development to ensure that our products excel in quality, safety and performance. That’s why we’ve recently improved our range of OPAC TMV3 Commercial Showers, designed with a host of new innovations to meet the needs of commercial sector environments.
With a new patented built-in thermal flush mechanism, the OPAC range is designed for easy infection control and anti-legionella regimes. What’s more, a new front mounted one-piece cartridge makes for simple servicing and commissioning.
And with TMV3 technology, you can rest assured that the highest level of safety and protection is guaranteed. There’s a variety of options to choose from to suit your specification requirements — all of which quality tested in our UKAS accredited in-house testing centre.
Discover the full range at the Bristan website.
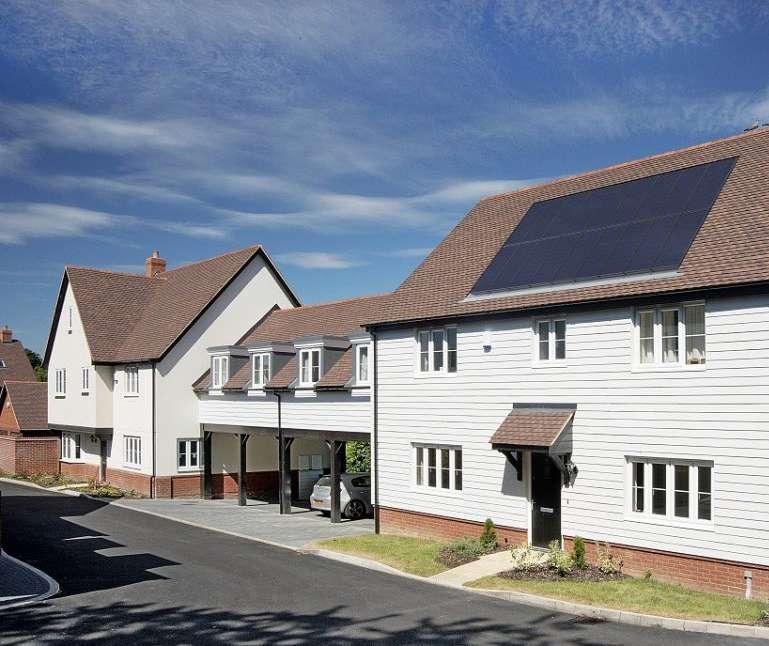
Need a full solar roof system… Marley have got you covered!
Marley’s pitched roof system, incorporating integrated solar panels, is a practical solution to the quality, time and sustainability challenges faced by specifiers. The full roof system offer means all roofing components can be sourced from one dedicated manufacturer and specifiers can benefit from technical knowledge, expertise and support, giving ultimate peace of mind that the roof specified is the one built.
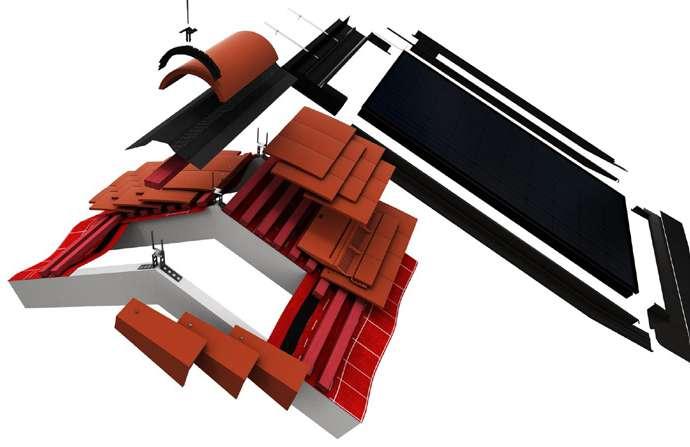
British Standards (BS 5534:2014 and BS 8612) for pitched roofing have become more stringent, so housebuilders must meet stricter fixing and quality requirements for all elements of a pitched roof.
developer-update.co.uk
Recognising this challenge, Marley’s full pitched roof system includes all elements of a roof from an extensive range of roof tiles, including low pitch clay and concrete options down to 12.5°, integrated solar PV panels, JB Red battens, underlay, fittings, dry fix and ventilation. All of this is supported by a 15-year system warranty, a single point of liability, and the technical tools and expertise to ensure you get the finished roof your project needs As part of Marley’s ongoing commitment to supporting specifiers, they have launched an updated Roof Systems Specification Guide to support you with design and building regulation requirements. To request your copy, visit: marley.co.uk/specguide
Industry News 07 Social housing sector running out of time to meet sustainability targets, say industry experts
Nine in ten social housing construction professionals believe the sector is in urgent need of new government guidelines if it is going to successfully meet sustainability targets, new research has revealed.
In a survey of 150 decision makers, including architects, involved in the specification of building materials used for social housing developments, 88% agreed that the sector cannot wait for the pending Decarbonisation Fund and Decent Homes Standard review to define how it is going to become more sustainable – it needs this detail now. In addition, almost a third of architects (28%) said that the government is yet to adequately define what constitutes the design and build of a sufficiently sustainable home. The research by Wienerberger, a leading provider of wall, roof and landscaping innovations, explored several key social housing issues, including the housing shortage, sustainability and building quality. It found that the sector was in desperate need of support and guidance if it is to overcome the challenges it’s facing. This guidance was expected to be included in the Social Housing Whitepaper which was released late last year, but it failed to clarify a number of key details the sector was waiting on. When it came to when the sector would need guidance by, a quarter said that it was too late and that further detail was required in 2020 if it was going to adapt in time to meet the government’s sustainability targets. Over half (57%) of the architects surveyed believe that there is still time, but only if the government provides further guidance in the first half of this year. Not only must the UK build more sustainably, but it also needs to increase the rate at which new homes are built to reach the government’s target of 300,000 new homes by 2025. 56% of social housing experts said that, like with sustainability, significantly more guidance and support is required from the government if it’s to meet this target. As well as building greater volumes in a more environmentally friendly manner, the UK’s social housing stock needs to maintain a high standard of build quality. 71% of architects said that to improve standards without exceeding costs or being non-compliant the sector needs to improve how it collaborates and communicates so that it can share best practice methodologies, technologies and innovations. To better understand the standard that housing needs to meet, more than half (57%) of the architects Wienerberger questioned said that the pending review of the Decent Homes Standard must provide clarity on building quality. Wienerberger discussed its research findings with a panel of senior decisionmakers from across the social housing sector during a virtual roundtable. During the discussion, Michael Swiszczowski, Director at Chapman Taylor, shared his views: “While the targets are tough, if people think they’ve failed already then they might stop trying, so it’s important to keep going. As we’ve learnt, the government tends to follow the market and be reactive with its response. It’s the same with the sustainability agenda. We need to strike while the iron is hot and while people are passionate about it… I’d like to see this rise to the top of the public agenda again once we’re through the pandemic.” Tomasz Romaniewicz, Associate at Bond Bryan, added: “I think we’re miles away from meeting the government’s sustainability targets to be honest. It has to be viable for businesses and at the moment it often isn’t and the guidance is muddy – we need a clear and viable route to the destination.” For more information on Wienerberger and the solutions it offers, please visit: https://www.wienerberger.co.uk/
developer-update.co.uk
Rapid growth at Norwich-based glazing manufacturer, Norwich Aluminium Limited, has seen the company move to new 80% larger premises and employ five new staff as it continues to fly the flag for UK manufacturing in construction.
Norwich Aluminium was established six years ago by local man Alex Warren. Alex, who was working in the glazing industry at the time, spotted an opportunity to move into aluminium, a material which was growing in popularity for commercial and architectural glazing. By re-mortgaging his house, Alex set up the company in a unit on White Lodge Trading Estate in Norwich, next to other established brands such as Screwfix and SIG.

Alex explained: “Using my knowledge of the PVC-U market, I could see the growing opportunity in aluminium. I knew that if I wanted to take the leap, I had to react quickly to market trends and invest properly. The banks were not interested at the time, so I raised the funds myself to get going and set up a small manufacturing facility in Norwich. We started with just three staff.” In December 2020, they set up subsidiary company Norwich Aluminium Trade Supply, with a focus on manufacturing a quality aluminium product for other glazing companies that are involved in installation-only projects and looking for a reliable local supplier.
Today, Norwich Aluminium employs 30 full-time staff across the group. Having outgrown its premises, Alex has invested £340,000 to move to new 80% larger offices and a bespoke manufacturing facility on the same industrial estate. The offices have been designed, manufactured and installed by spatial designers and event agency Production Bureau and comprise workspace and meeting rooms, as well as a staff canteen. The manufacturing premises include new top-of-the-range equipment and work benches to allow an increase in production, as well as a better space for the staff, who have been key to the success of the business.
Alex Warren continued: “In 2020 alone we manufactured over £3 million of aluminium glazing products for customers across the country. We are targeting a 30% growth on that figure this year. While the UK construction and manufacturing industries continue to struggle, our future order book is looking very strong. We’re bucking the trend and still growing. We pride ourselves on quality and moving to these new premises will enable us to offer an even better service for our customers using the latest manufacturing facilities. We are looking forward to seeing what the future brings.”
For more information on Norwich Aluminium, visit www.norwichaluminium.co.uk and www.norwichtradesupply.co.uk
Norwich Aluminium manufactures glazing for domestic and commercial projects. It recently completed glazing for new wards at the Norfolk & Norwich Hospital, some of which are currently being used as emergency COVID-19 wards. The company has worked on hundreds of projects across the country, ranging from new and existing schools and shop fronts to home renovations and commercial offices. Norwich Aluminium is very proud of the foothold gained in the local Norwich area and neighbouring counties, working on some high profile and stand-out architectural buildings. Recent projects have seen the company diversify and move further afield, reaching from Brighton to Edinburgh, to work with retained clients.

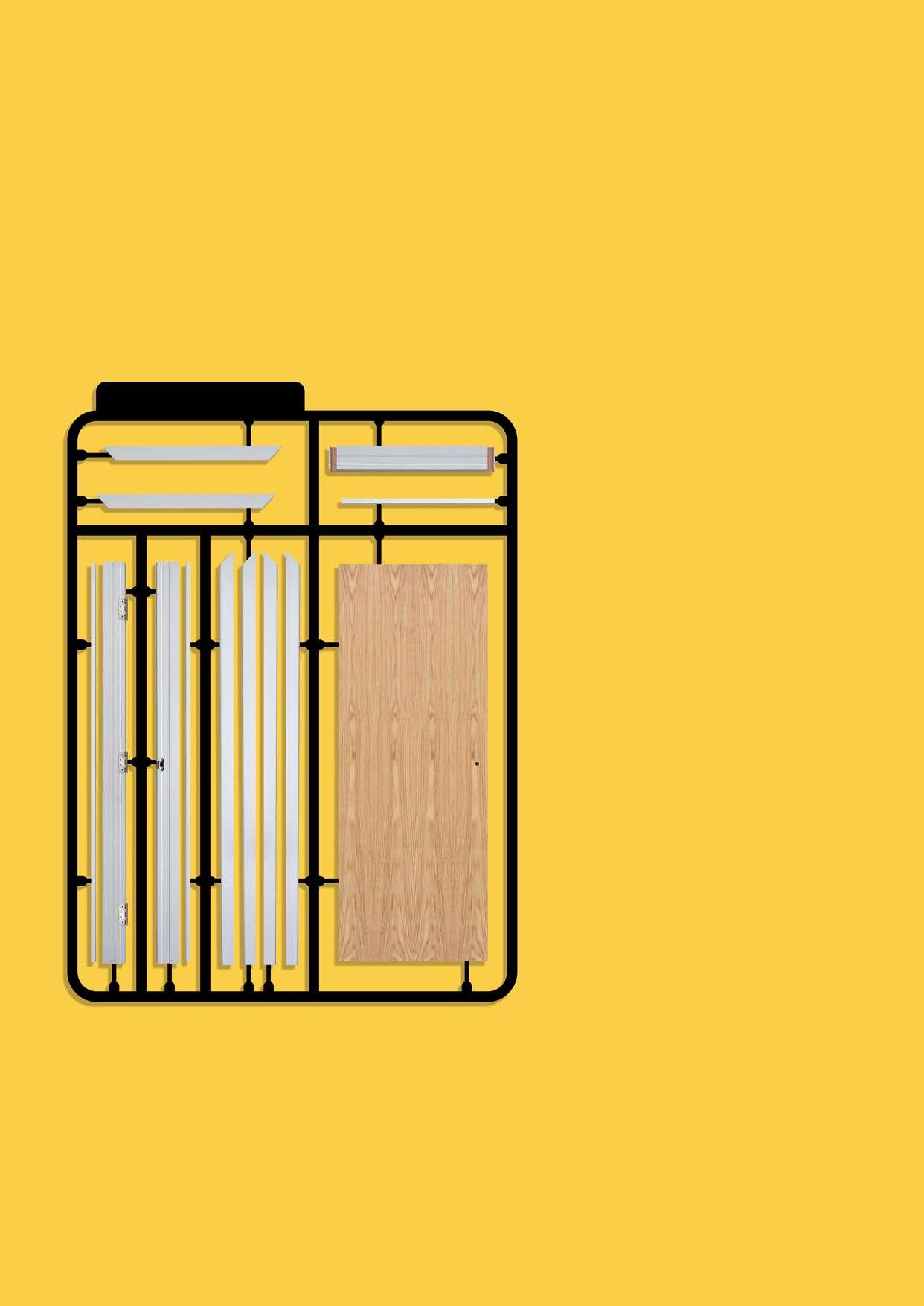
10
UK Conformity Assessment and What You Need to Know
By Wojciech Brozyna - MD of Aluprof UK
Since the beginning of 2021 the UK now sits outside of the European Economic Area (EEA) complete with a late brokered ‘deal’ which helps businesses trade without tariffs between the EEA and the UK.
Despite the increased levels of paperwork required for such imports and exports, it is ‘almost business as usual’. Over the last few years conformity with legislation and standards present in Europe has been a prerequisite for producing and selling any goods within the EEA, either produced in the EEA or from overseas. Known as ‘CE’ marking, it is applicable equally to the manufacture and sale of a paper clip to a curtain wall facade.
So what is a ‘CE’ mark? A CE mark indicates conformity with a harmonised product standard, and assures the user that the product is classified to the relevant essential characteristics, within Annex ZA, for the member state whose market it is placed on. Construction products are different to say medical devices for CE marking as regulations differ.
So now that we have left the EEA, what now?
The UK has set up its own conformity marking known as the ‘UKCA’ mark. Broadly the same as the current CE marking the new UKCA mark will allow the UK to begin to adjust its conformity standards to suit UK businesses and the UK’s legislative requirements in the longer term. As far as timing is concerned, CE marking is still fully accepted in the UK this year, but all companies manufacturing and selling in the UK must have UKCA marking on their products by the end of 2021. Importantly for Aluprof UK, we will comply with the new UKCA marking and are
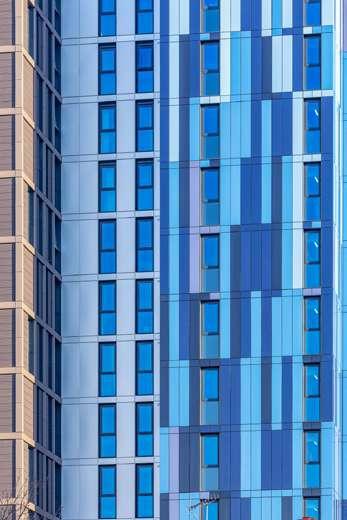

already scheduling our products for conformity with UK ‘approved bodies’ this year.
Now a note of caution, we often use Great Britain, the United Kingdom and the British Isles interchangeably, but this is not correct. ‘Great Britain’ consists of England, Scotland and Wales, the ‘United Kingdom’ consists of ‘Great Britain’ and ‘Northern Ireland’. The ‘British Isles’, consists of the ‘United Kingdom’ and ‘Ireland’, plus numerous smaller island groups, which include the Hebrides, the Shetland Islands, the Orkney Islands, the Isles of Scilly, and the Isle of Man.
In Northern Ireland, matters get a little more complicated as manufacturers there have their own UK(NI) mark to comply with which must be used alongside the CE marking. Whilst Great Britain will accept the UK(NI)+CE marked products known as ‘unfettered access’, products manufactured in Northern Ireland only need to carry the CE mark if they are to be sold solely in the EEA. Part of the reason for the difference in Northern Ireland is that whilst Northern Ireland sits within the EEA, from the 1st January 2021, it is now outside the EU Customs Union. It must be reiterated that for products manufactured and sold in Northern Ireland, they must always carry both the CE mark and the UK(NI).
It is also important to remember that a separate Declaration of Performance/Conformity (DoP) must be provided for each UKCA, UK(NI) and CE mark. Whilst at the moment these will broadly be the same, it is likely that with changes to legislation here and in the EEA over time, these will begin to differ. It has also been confirmed that both CE and UKCA marks can be used together on products as long as they are separate and are clearly visible. As the UK ‘approved bodies’ move to offer UKCA marking, CE marking ‘approved bodies’ for products to be sold in the EEA, can only be provided by an EU based ‘approved body’.
Whilst new conformity marks are being introduced, UKCA and UK(NI), nothing else changes at this time regarding the products that require labelling. The marking convention and conformity continues for construction products as it has done for CE marking for the last few years.

So what does this mean for supply of goods from the EEA to our customers in the British Isles and in particular, products imported by Aluprof?
As a European manufacturer, we will continue with CE marking which will confirm with the requirements for Ireland and Northern Ireland, for Great Britain (England, Scotland and Wales) all our products can continue to be used with CE marking in 2021 are being lodged with a UK ‘approved body’ to ensure they can carry UKCA compliance markings.
There is also one caveat to the conformity marking, that is the marking is only applied at the time of manufacture, so there could be products manufactured in 2021 in compliance with CE marking that may enter the Great Britain market in early 2022. At this point we begin to get into some of the grey areas of compliance and the government is still working out some of the detail. What is known is that for our customers who manufacture our systems into products that go on site, you will need to demonstrate compliance with the new UKCA marking from the 1st January 2022. As ever with our loyal customers in the British Isles, we are on-hand at Aluprof to give any of our customers guidance on the compliance and marking convention.
With the company Project Office at the Business Design Centre in London, Aluprof has rapidly grown their specification influence in the UK with their high performance architectural aluminium systems. With overseas growth across Europe spreading into the Middle East and firm roots already in the East of the USA, the company is becoming a global player in facade supply. Further information is available on the company’s website at aluprof. co.uk or direct from their UK office in Altrincham on 0161 941 4005.
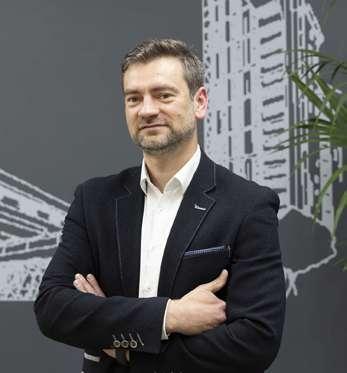